Eksploatacja maszyn i urządzeń do przygotowania mas formierskich i mas rdzeniowych
MTL.02. Eksploatacja maszyn i urządzeń odlewniczych - Operator maszyn i urządzeń odlewniczych 812107, Technik odlewnik 311705
Zasady oceny stanu technicznego elementów maszyn i urządzeń
SCHEMAT INTERAKTYWNY
Spis treści
Wstęp - Metody obserwacji prostejWstęp - Metody obserwacji prostej
Parametry stanuParametry stanu
Przegląd technicznyPrzegląd techniczny
Klasy stanu technicznego urządzeńKlasy stanu technicznego urządzeń
Szczelność maszynSzczelność maszyn
DTR (dokumentacja techniczno - ruchowa}DTR (dokumentacja techniczno - ruchowa}
Cykl remontowyCykl remontowy
Procedura usunięcia uszkodzeniaProcedura usunięcia uszkodzenia
Przykład harmonogramu smarowania i konserwacji mieszarko‑nasypywarkiPrzykład harmonogramu smarowania i konserwacji mieszarko‑nasypywarki
Jedną z częściej spotykanych metod diagnozowania maszyn i urządzeń jest metoda obserwacji prostej, wykorzystująca zmysły człowieka – wzrok, słuch, dotyk i węch. Metoda ta wymaga dużego doświadczenia pracownika i nienagannej znajomości danego urządzenia.
Grafika interaktywna przedstawia wyjaśnienie metod obserwacji prostej. Na samej górze schematu znajduje się prostokąt z napisem „Metoda obserwacji prostej”, od którego w dół odchodzą trzy proste linie, do kolejnych grup prostokątów. Przy każdym prostokącie znajduje się okrąg z cyferką, po której nacisnięciu pojawia się definicja albo objasnienie pojęcia.
Pierwsza grupa zawiera cztery prostokąty umieszczone kolejno pod sobą, oddzielone kropkowaną, pomarańczowa linią. Pojęcia w tych prostokątach oraz ich definicje to kolejno od góry:
1 - Kontrola wzrokowa: brak definicji
2 - wskazania przyrządów kontrolno‑pomiarowych: na przykład termometru, wskaźnika poziomu cieczy roboczej, manometru, obrotomierza, amperomierza
3 - wibracje: drgania, silne jednorazowe wstrząsy, wstrząsy powtarzające się
4 - przecieki zewnętrzne: przecieki oleju, smarów, wody lub chłodziwa widoczne na zewnątrz obudowy, siłownika, lub jakiegokolwiek elementu maszyny
Druga grupa zawiera cztery prostokąty umieszczone kolejno pod sobą, oddzielone kropkowaną, pomarańczową linią. Pojęcia w tych prostokątach to kolejno od góry:
1 - Kontrola dotykowa: brak definicji
2 - temperatura: ogrzana, ciepła obudowa np. silnika
3 - wibracje: drgania, silne jednorazowe wstrząsy, wstrząsy powtarzające się, cykliczne, wyczuwalne przy dotyku
4 - przecieki: włożenie ręki (przy wyłączonym zasilaniu) do elementu maszyny, sprawdzenie w miejscu niedostępnym dla wzroku lub sondy, wyczucie smaru, oleju, płynu
Trzecia grupa zawiera trzy prostokąty umieszczone kolejno pod sobą, oddzielone kropkowaną, pomarańczową linią. Pojęcia w tych prostokątach to kolejno od góry:
1 - Kontrola słuchowa: brak definicji
2 - zewnętrzne hałasy mechaniczne: generowany przez maszynę i jest słyszalny na zewnątrz jej obudowy, może być przekazywany do otoczenia i wpływać na otoczenie pracy oraz na osoby wokół maszyny
3 - wewnętrzne hałasy mechaniczne: odnosi się do dźwięków generowanych wewnątrz maszyny lub jej podzespołów, które nie są bezpośrednio słyszalne na zewnątrz
Do każdego podpunktu przyporządkowano również nagrania audio, przedstawiające treść zagadnienia.
Grafika interaktywna przedstawia wyjaśnienie rodzajów parametrów stanu. Na samej górze schematu znajduje się pomarańczowy prostokąt z napisem „Parametry stanu”, od którego w dół odchodzą trzy proste linie, do kolejnych grup prostokątów. Pierwszy od góry prostokąt w każdej grupie jest największy. Przy każdym prostokącie znajduje się okrąg z cyferką, po której nacisnięciu pojawia się definicja albo objasnienie pojęcia. Przy górnym prostokącie również jest okrąg, po którego naciśnięciu pojawia się definicja: parametry stanu maszyn to mierzalne cechy, które pozwalają ocenić i monitorować stan techniczny maszyny.
Pierwsza grupa zawiera pięć niebieskich prostokątów umieszczonych kolejno pod sobą. Od pierwszego prostokątu, z jego boku wychodzi linia prosto w dół, od której wychodzą pojedyncze cztery linie na bok do kolejnych prostokoątów. Pojęcia w tych prostokątach oraz ich definicje to kolejno od góry:
Fizyczne: dotyczą one właściwości fizycznych maszyny i jej działania
Temperatura: pomiar temperatury maszyny może wskazywać na przegrzewanie się lub niedostateczne chłodzenie, co może prowadzić do uszkodzeń
Wibracje: pomiar wibracji może służyć do wykrywania nieprawidłowości w ruchu maszyny, takich jak luz w łożyskach, nierówności w układzie napędowym itp.
Ciśnienie: pomiar ciśnienia może być stosowany w przypadku maszyn hydraulicznych lub pneumatycznych do monitorowania sprawności i wydajności systemu
Przepływ: pomiar przepływu może być używany w przypadku maszyn związanych z płynami, takich jak pompy, chłodnice, aby ocenić przepływ mediów roboczych
Druga grupa zawiera cztery żółte prostokąty umieszczone kolejno pod sobą. Od pierwszego prostokątu, z jego boku wychodzi linia prosto w dół, od której wychodzą pojedyncze trzy linie na bok do kolejnych prostokoątów. Pojęcia w tych prostokątach oraz ich definicje to kolejno od góry:
Chemiczne: dotyczą one składu chemicznego i właściwości mediów używanych w maszynach lub powstałych w wyniku procesu eksploatacji maszyny
Poziom pH: pomiar poziomu pH może być stosowany w przypadku maszyn, które korzystają z substancji chemicznych, aby ocenić ich odpowiednią jakość lub określić potrzebę konserwacji lub regeneracji
Stężenie substancji: pomiar stężenia substancji chemicznych może być używany do monitorowania ilości i jakości używanych mediów roboczych lub identyfikowania zanieczyszczeń
Analiza płynu: analiza płynów takich jak oleje lub chłodziwa oraz smary, takie jak pomiar zawartości metali, kwasowości czy obecność cząstek, może dostarczyć informacji o zużyciu maszyny, obecności zanieczyszczeń lub potrzebie wymiany płynów eksploatacyjnych
Trzecia grupa zawiera cztery zielone prostokąty umieszczone kolejno pod sobą. Od pierwszego prostokątu, z jego boku wychodzi linia prosto w dół, od której wychodzą pojedyncze trzy linie na bok do kolejnych prostokoątów. Pojęcia w tych prostokątach oraz ich definicje to kolejno od góry:
Geometryczne: dotyczą one pomiaru i analizy wymiarów, kształtu i geometrii elementów maszyny
Odległość: pomiar odległości między elementami maszyny może być używany do sprawdzania luzów, odkształceń czy nieprawidłowości w montażu
Kąt: pomiar kątów między elementami może być używany do kontroli poprawności ustawień czy nieprawidłowości w geometrii maszyny jak i również odpowiedniego ustawienia maszyn względem siebie wzdłuż całej linii produkcyjnej
Geometria powierzchni: można wykonywać pomiary geometryczne powierzchni elementów maszyny, takie jak gładkość, liniowość, równoległość, pionowość, prostopadłość itd. aby ocenić ich dokładność i zgodność z wymaganiami technicznymi
Do każdego podpunktu przyporządkowano również nagrania audio, przedstawiające treść zagadnienia.
Powrót do spisu treściPowrót do spisu treści
Przegląd techniczny
a) mechaniczne — naprężenia statyczne, pełzanie, zmęczenie, pitting, zużycie cierne;
b) chemiczne — korozja metali, starzenie gumy, farb, izolacji, butwienie drewna;
c) elektryczne — elektro-korozja;
d) cieplne — nadtapianie, intensyfikacja przebiegu zjawisk.
Rozróżniamy następujące sposoby usuwania uszkodzeń:
– wyłączenie i zastąpienie uszkodzonego elementu jego sprawnym rezerwowym odpowiednikiem; gdy uszkodzony element nie może by zastąpiony sprawnym, dopuszcza się wyłączenie go z eksploatacji (po odpowiednim zabezpieczeniu) i użytkowanie obiektu z ograniczoną wydajnością.
– wyłączenie i naprawa uszkodzonego elementu obiektu.
opis alternatywny
, 2. Przyczyny powstawania uszkodzeń Występujący w elementach maszyn rodzaj niszczenia jest zależny od wielu czynników, które można podzielić na:
a) geometryczne (kształt, chropowatość, błędy kształtu itp.);
b) kinematyczne (rodzaj ruchu, prędkość itp.);
c) dynamiczne (rodzaj obciążenia, siła obciążająca, nacisk jednostkowy itp.);
d) materiałowe (materiał warstwy wierzchniej, jakość smarowania itp.);
e) środowiskowe (wilgotność, powinowactwo chemiczne itp.);
f) cieplne (temperatura, odprowadzenie ciepła itp.).
Główne przyczyny powstawania uszkodzeń maszyn i urządzeń klasyfikuje się następująco:
a) konstrukcyjne — uszkodzenia powstałe wskutek błędów projektowania i konstruowania obiektu, najczęściej przy nie uwzględnieniu obciążeń ekstremalnych, tzn. wartości, które w istotny sposób przekraczają obciążenia nominalne, prowadząc wprost do uszkodzeń.
b) produkcyjne (technologiczne) — uszkodzenia powstałe wskutek błędów i niedokładności procesów technologicznych (brak tolerancji wymiarów, gładkości powierzchni, obróbki termicznej itp.) lub wad materiałów elementów obiektu.
c) eksploatacyjne — uszkodzenia powstałe w wyniku nie przestrzegania obowiązujących zasad eksploatacji lub na skutek oddziaływań czynników zewnętrznych nieprzewidzianych dla warunków użytkowania danego obiektu, co prowadzi do osłabienia i przedwczesnego zużycia i osiągnięć stanu granicznego.
d) starzeniowe i zużyciowe — zawsze towarzyszące eksploatacji obiektów i będące rezultatem nieodwracalnych zmian, prowadzących do pogorszenia wytrzymałości i zdolności współdziałania poszczególnych elementów.
, 3. Zużycie maszyn Zużycie maszyny to trwałe niepożądane zmiany jej stanu, występujące podczas eksploatacji. Procesy zużyciowe maszyny związane są z przetwarzaniem energii w pracę mechaniczną i towarzyszącymi im siłami, którymi oddziaływują na siebie elementy maszyny.
Jako podstawowe rodzaje zużycia wyróżnia się:
a) zużycie ścierne (bez i z warstwą ścierną, strumieniowo ścierne i w ośrodku sypkim);
b) zużycie adhezyjne (bez głębokiego wyrywania i z głębokim wyrywaniem);
c) zużycie plastyczne (w warstwie wierzchniej i w całej masie);
d) zużycie zmęczeniowe;
e) zużycie korozyjne (metali i niemetali);
f) zużycie erozyjne (hydroerozja, erozja gazowa, elektroerozja);
g) zużycie kawitacyjne (kawitacja przepływowa, kawitacja falowa);
h) zużycie cieplne (metali, niemetali)., 4. Hałas i drgania Każde urządzenie ma określony zakres hałasu i drgań podczas pracy. Przekroczenie zalecanych poziomów może powodować spadek komfortu pracy przy/na urządzeniu lub prowadzić do jego awarii i uszkodzenia. Oprzyrządowanie pomiarowe do celów mierzenia hałasu maszyn i urządzeń powinno zawierać mikrofony, kable, osłonę przeciwwietrzną i filtry, które powinny spełniać wytyczne dla przyrządu klasy dokładności. Badając emisję hałasu należy ją rozpatrzyć we wszystkich możliwych stadiach procesu.
Każda pracująca maszyna generuje charakterystyczny dla siebie rodzaj drgań i wibracji. Jeśli energia drgań zaczyna przekraczać ustalone limity, może to oznaczać, że maszyna jest źle wyważona, doszło do poluzowania części, zużycia łożysk lub uszkodzenia innego elementu. Odpowiednio wczesne wykrycie nieprawidłowości będzie miało kluczowe znaczenie dla zapewnienia nieprzerwanej pracy parku maszynowego. Do pomiaru drgań maszyny stosuje się wibrometry.
Powstanie wibracji i drgań podczas pracy maszyny mogą być spowodowane:
- powstaniem luzów w mocowaniach
- brakiem dokładności w montażu urządzeń
- uszkodzeniem łożyska
- złym wyważeniem elementów obrotowych
- zużyciem materiałów, 5. Dotyczy także mycia i czyszczenia układów smarowania i chłodzenia oraz wymianę olejów lub innych środków smarnych, 6. Dotyczy części takich jak: łożyska, sprzęgła i czopy wałów, przekładnie zębate, łańcuchy napędowe, pędnie, urządzenia cierne, armatura, przewody elektryczne, izolacja maszyn elektrycznych, 7. Sprawdzenie i regulacja odbywają się zgodnie z ustaloną dla nich klasą dokładności., 8. Do tego etapu wykorzystuje się odpowiednie, ściśle określone przyrządy pomiarowo-kontrolne., 9. Pomiary luzów można wykonać m. in. za pomocą szczelinomierzy. Szczelinomierze najczęściej są stosowane do regulacji luzu zaworowego silnika spalinowego, a także podczas montażu maszyn do pomiaru luzów między powierzchniami współpracujących ze sobą części maszyn.
opis alternatywny, 10. sprawdzenie czystości maszyn, częstotliwości i jakości smarowania mechanizmów i połączeń oraz ich regulacji, działania mechanizmów, stanu osłon ochrony i ogólnego bezpieczeństwa pracy
Schemat interaktywny przedstawia informacje na temat przebiegu przeglądu technicznego. Wyznacza poszczególne etapy oraz ich definicje. Składa się z zielonego koła z napisem „Przegląd techniczny” obok którego znajdują się dwa małe kółka, które po naciśnięciu pokazują poniższe dwie definicje:
Uszkodzenie lub zniszczenie obiektu technicznego następuje pod wpływem przenoszonej przez niego energii. Zależnie od tego, jaki rodzaj energii dominuje w danych warunkach, przyczyny uszkodzeń elementów można podzielić na następujące grupy: mechaniczne — naprężenia statyczne, pełzanie, zmęczenie, pitting, zużycie cierne; chemiczne — korozja metali, starzenie gumy, farb, izolacji, butwienie drewna; elektryczne — elektro‑korozja; cieplne — nadtapianie, intensyfikacja przebiegu zjawisk. Rozróżniamy następujące sposoby usuwania uszkodzeń: wyłączenie i zastąpienie uszkodzonego elementu jego sprawnym rezerwowym odpowiednikiem; gdy uszkodzony element nie może by zastąpiony sprawnym, dopuszcza się wyłączenie go z eksploatacji (po odpowiednim zabezpieczeniu) i użytkowanie obiektu z ograniczoną wydajnością. Wyłączenie i naprawa uszkodzonego elementu obiektu.
Występujący w elementach maszyn rodzaj niszczenia jest zależny od wielu czynników, które można podzielić na: geometryczne (kształt, chropowatość, błędy kształtu itp.); kinematyczne (rodzaj ruchu, prędkość itp.); dynamiczne (rodzaj obciążenia, siła obciążająca, nacisk jednostkowy itp.); materiałowe (materiał warstwy wierzchniej, jakość smarowania itp.); środowiskowe (wilgotność, powinowactwo chemiczne itp.); cieplne (temperatura, odprowadzenie ciepła itp.). Główne przyczyny powstawania uszkodzeń maszyn i urządzeń klasyfikuje się następująco; konstrukcyjne — uszkodzenia powstałe wskutek błędów projektowania i konstruowania obiektu, najczęściej przy nie uwzględnieniu obciążeń ekstremalnych, tzn. wartości, które w istotny sposób przekraczają obciążenia nominalne, prowadząc wprost do uszkodzeń produkcyjne (technologiczne) — uszkodzenia powstałe wskutek błędów i niedokładności procesów technologicznych (brak tolerancji wymiarów, gładkości powierzchni, obróbki termicznej itp.) lub wad materiałów elementów obiektu. Eksploatacyjne — uszkodzenia powstałe w wyniku nie przestrzegania obowiązujących zasad eksploatacji lub na skutek oddziaływań czynników zewnętrznych nieprzewidzianych dla warunków użytkowania danego obiektu, co prowadzi do osłabienia i przedwczesnego zużycia i osiągnięć stanu granicznego. Starzeniowe i zużyciowe — zawsze towarzyszące eksploatacji obiektów i będące rezultatem nieodwracalnych zmian, prowadzących do pogorszenia wytrzymałości i zdolności współdziałania poszczególnych elementów.
Od zielonego koła, w prawo poprowadzona jest pozioma linia, prowadząca do kolejnej, pionowej. Pionowa linia ma również 12 odgałęzień w prawo, do jasnoniebieskich prostokątów z różnymi pojęciami i kółeczkami, po których naciśnięciu pojawia się definicja. Pojęcia i definicje to:
Określanie stopnia zużycia i czasów pracy zespołów i części: Podczas przeglądu technicznego maszyn przemysłowych istotne jest określenie stopnia zużycia różnych komponentów i elementów oraz analiza czasów pracy. Pozwala to ocenić stan techniczny maszyny oraz przewidzieć konieczność naprawy, konserwacji lub wymiany poszczególnych części. Metody określania stopnia zużycia i czasów pracy obejmują: 1. Wizualna ocena - Analiza widocznych śladów zużycia, takich jak ścieranie, korozja, pęknięcia, luzy czy uszkodzenia powierzchni. 2. Pomiar grubości lub średnicy - Mierzenie grubości lub średnicy elementów poddanych zużyciu, np. przez ścieranie lub korozję. 3. Badanie zużycia powierzchni - Wykonywanie badań zużycia powierzchni, takich jak profilometria, w celu pomiaru głębokości śladów zużycia, wytarć lub korozji. 4. Analiza czasów pracy - Analiza rejestrowanych czasów pracy maszyny, uwzględniając parametry takie jak czas pracy całkowity, czas pracy pod obciążeniem oraz czas pracy w różnych trybach działania. 5. Badanie zużycia oleju lub płynu roboczego - Przeprowadzenie analizy oleju lub płynu roboczego w celu oceny stopnia zanieczyszczenia, utlenienia lub degradacji. Odczyty tych parametrów mogą wskazywać na stopień zużycia.
Sprawdzenie i pomiar zespołów dławicowych, styków i zespołów uszczelniających: Zużycie maszyny to trwałe niepożądane zmiany jej stanu, występujące podczas eksploatacji. Procesy zużyciowe maszyny związane są z przetwarzaniem energii w pracę mechaniczną i towarzyszącymi im siłami, którymi oddziaływują na siebie elementy maszyny. Jako podstawowe rodzaje zużycia wyróżnia się: zużycie ścierne (bez i z warstwą ścierną, strumieniowo ścierne i w ośrodku sypkim); zużycie adhezyjne (bez głębokiego wyrywania i z głębokim wyrywaniem); zużycie plastyczne (w warstwie wierzchniej i w całej masie); zużycie zmęczeniowe; zużycie korozyjne (metali i niemetali); zużycie erozyjne (hydroerozja, erozja gazowa, elektroerozja); zużycie kawitacyjne (kawitacja przepływowa, kawitacja falowa); zużycie cieplne (metali, niemetali).
Wyważenie urządzeń napędowych maszyny lub urządzenia technologicznego: Każde urządzenie ma określony zakres hałasu i drgań podczas pracy. Przekroczenie zalecanych poziomów może powodować spadek komfortu pracy przy/na urządzeniu lub prowadzić do jego awarii i uszkodzenia. Oprzyrządowanie pomiarowe do celów mierzenia hałasu maszyn i urządzeń powinno zawierać mikrofony, kable, osłonę przeciwwietrzną i filtry, które powinny spełniać wytyczne dla przyrządu klasy dokładności. Badając emisję hałasu należy ją rozpatrzyć we wszystkich możliwych stadiach procesu. Każda pracująca maszyna generuje charakterystyczny dla siebie rodzaj drgań i wibracji. Jeśli energia drgań zaczyna przekraczać ustalone limity, może to oznaczać, że maszyna jest źle wyważona, doszło do poluzowania części, zużycia łożysk lub uszkodzenia innego elementu. Odpowiednio wczesne wykrycie nieprawidłowości będzie miało kluczowe znaczenie dla zapewnienia nieprzerwanej pracy parku maszynowego. Do pomiaru drgań maszyny stosuje się wibrometry. Powstanie wibracji i drgań podczas pracy maszyny mogą być spowodowane: powstaniem luzów w mocowaniach brakiem dokładności w montażu urządzeń uszkodzeniem łożyska złym wyważeniem elementów obrotowych zużyciem materiałów.
Czyszczenie i mycie poszczególnych elementów maszyny lub urządzenia: W celu zapewnienia odpowiedniej pracy urządzenia, niektóre obszary i elementy należy utrzymywać we względnej czystości. Na szczególną uwagę zasługują powierzchnie ślizgowe, tłoki cylindrów, powierzchnie jezdne i cierne. Na wymienionych obszarach nie może znajdywać się żaden piach ani pył, gdyż może je porysować i uszkodzić.
Przegląd i badanie danych elementów: Dotyczy części takich jak: łożyska, sprzęgła czopy wałów, przekładnie zębate, łańcuchy napędowe, pędnie, urządzenia cierne, armatura, przewody elektryczne, izolacja maszyn elektrycznych.
Sprawdzenie i wyregulowanie dokładności pracy maszyny: W celu zapewnienia równej, dokładnej i powtarzalnej pracy maszyny, należy przeprowadzać odpowiednie kontrole i stosowne regulacje jej parametrów technicznych oraz elementów wykonawczych.
Sprawdzenie osi maszyn i urządzeń technologicznych: Sprawdzenie i regulacja odbywają się zgodnie z ustaloną dla nich klasą dokładności. Sprawdzenie wykonuje się za pomocą niwelatorów, urządzeń geodezyjnych, poziomic laserowych lub maszynowych, sznurków z obciążeniem.
Wykonanie pomiarów luzów: Pomiary luzów można wykonać m. in. za pomocą szczelinomierzy. Szczelinomierze najczęściej są stosowane do regulacji luzu zaworowego silnika spalinowego, a także podczas montażu maszyn do pomiaru luzów między powierzchniami współpracujących ze sobą części maszyn.
Częściowy demontaż maszyny lub urządzenia: Częściowy demontaż przeprowadza się czasami w celu umożliwienia dotarcia do elementów maszyny, które były wcześniej niemożliwe do obserwacji, konserwacji lub wymiany. Czynność tę wykonuje się również w celu sprawdzenia jej stanu, czyszczenia lub kalibracji, ale w innym miejscu niż w którym pracuje ona na co dzień. Może to wynikać ze skomplikowania części lub potrzeby przeglądu za pomocą niedostępnych na miejscu urządzeniach.
Sprawdzenie działania przyrządów pomiarowo‑kontrolnych i urządzeń regulacyjnych: Podczas przeglądu technicznego maszynerii przemysłowej istotne jest sprawdzenie działania przyrządów pomiarowo‑kontrolnych i urządzeń regulacyjnych. Oto kilka przykładów takich urządzeń i czynności, które można przeprowadzić podczas przeglądu: 1. Termometry i czujniki temperatury - sprawdzenie poprawności odczytu temperatury przez termometry i czujniki temperatury. Odczyty należy porównać z innymi sprawdzonymi termometrami lub skorzystać z wzorców temperatury, jeśli są dostępne. 2. Manometry i czujniki ciśnienia - Należy zweryfikować działanie manometrów i czujników ciśnienia, porównując ich odczyty z odczytami wzorcowymi lub innymi sprawdzonymi urządzeniami pomiarowymi. 3. Wskaźniki poziomu - Należy sprawdzić, czy wskaźniki poziomu (np. dla cieczy, paliwa, oleju) pokazują poprawne wartości. Można to zweryfikować to na podstawie innych wskaźników, poziomomierzy lub poprzez fizyczne pomiary poziomu substancji w zbiornikach 4. Regulatory temperatury i ciśnienia - Testowane są urządzenia regulacyjne, takie jak regulatory temperatury i ciśnienia. Istotne jest upewnienie się, że działają poprawnie i utrzymują wartości na odpowiednich poziomach. 5. Weryfikacja urządzeń kontrolno‑pomiarowych - sprawdzane jest działanie wszelkich innych urządzeń kontrolno‑pomiarowych, które są istotne dla bezpiecznej i prawidłowej pracy maszyn. Może to obejmować czujniki położenia, czujniki prędkości, czujniki wibracji, czujniki przepływu itp. Podczas przeglądu technicznego ważne jest również zapisanie wyników pomiarów i odczytów, aby móc porównać je z przyszłymi przeglądami i zidentyfikować ewentualne zmiany lub problemy w funkcjonowaniu maszyn. Jeśli zostaną wykryte jakiekolwiek nieprawidłowości, konieczne może być skonsultowanie się z odpowiednimi specjalistami w celu naprawy lub kalibracji urządzeń.
Usuwanie drobnych uszkodzeń: Dokręcanie, wymiana uszkodzonych śrub nie związanych z krytyczną konstrukcją maszyny, czyli np. poprawianie łączeń tabliczek i przycisków. Zamalowywanie zarysowań, wymiana filtrów, pasków napędowych, wymiana oleju, chłodziwa
Wykonanie wszystkich czynności wchodzących w zakres obsługi codziennej: Sprawdzenie czystości maszyn, częstotliwości i jakości smarowania mechanizmów i połączeń oraz ich regulacji, działania mechanizmów, stanu osłon ochrony i ogólnego bezpieczeństwa pracy.
Do każdego podpunktu przyporządkowano również nagrania audio, przedstawiające treść zagadnienia.
Wyniki weryfikacji i ustalenia zakresu napraw zapisywane są w protokole przeglądu technicznego. Poniżej dostępny do pobrania przykładowy wzór protokołu przeglądu.
Powrót do spisu treściPowrót do spisu treści
Klasy stanu technicznego urządzeń
Grafika interaktywna przedstawia schemat klas i stanów technicznych urządzeń przemysłowych. Można go podzielić na dwie połowy - górną i dolną. Każda z nich składa się z umieszczonego po lewej koła, w którego środku znajduje się pojęcie nadrzędne. Od tego koła w prawo wyprowadzone są linie, stanowiące ramiona, które doprowadzone są do prostokątów z pojęciami. Obok prostokątów umieszczone są małe okręgi, które po kliknięciu pokazują definicję pojęcia.
Górna połowa składa się z żółtego koła z pojęciem „Klasy stanów technicznych urządzeń”, a pojęcia znajdujące się w umieszczonych na prawo czterech zielonych prostokątach i ich definicje to:
Niesprawności technicznej: ze stanem niesprawności technicznej mamy styczność, gdy parametry struktury urządzenia przekraczają wartości dopuszczalne - w tym stanie urządzenie w nie jest w stanie w bezpieczny sposób spełniać wszystkich funkcji założonych w trakcie konstruowania
Sprawności technicznej: ze stanem sprawności technicznej mamy styczność, gdy żaden z parametrów struktury urządzenia nie przekracza wartości dopuszczalnej - w tym stanie urządzenie w bezpieczny sposób spełnia wszystkie założone przy konstruowaniu funkcje
Zdatności: obiekt znajduje się w stanie zdatności, jeżeli wartości wszystkich parametrów stanu znajdują się w dopuszczalnych granicach, czyli spełnia on określone wymagania
Niezdatności: obiekt znajduje się w stanie niezdatności, jeżeli wartość nawet jednego parametru lub cechy stanu wykracza poza dopuszczalne
Dolna połowa składa się z niebieskiego koła z pojęciem „Klasy stanów technicznych urządzeń”, a pojęcia znajdujące się w umieszczonych na prawo dwóch niebieskich prostokątach i ich definicje to:
Stan dopuszczalny: definiowany jest jak stan zagrożenia uszkodzenia obiektu
Sprawności częściowej zdatności: jest to taki stan obiektu, przy którym obiekt może wykonywać swoje zadania w ograniczonym zakresie, np. mniejsza prędkość, mniejsza siła pociągowa itp.
Do każdego podpunktu przyporządkowano również nagrania audio, przedstawiające treść zagadnienia.
Powrót do spisu treściPowrót do spisu treści
Szczelność maszyn
Szczelność maszyny określa kod IP. Składa się on z liter „IP”, dwóch cyfr charakterystycznych i opcjonalnie z dwóch liter – dodatkowej i uzupełniającej.
Grafika interaktywna przedstawia wyjaśnienie symboli kodu IP. W prawym górnym rogu znajduje się następujący kod: IP 2 3 C H. Od każdego z symboli odbiega żółta linia prowadząca do jego wyjaśnienia. Znajdują się one po prawej stronie grafiki.
Opisy symboli kodu:
IP to litery kodu, z języka angielskiego „Ingress Protection” - oznaczają stopień ochrony, dosłownie „Ochrona przed wejściem, dostaniem się do środka” .
Numer 2 to pierwsza cyfra charakterystyczna. Mniejszą czcionką w nawiasie zapisano tekst: „(cyfry od 0 do 6 lub litera „X”)”. Na żółtej linii umieszczony jest numer z rozwijalnym opisem: „stopień ochrony użytkownika przed dostępem do części niezabezpieczonych oraz odporność na penetrację ciał stałych”.
Numer 3 to druga cyfra charakterystyczna. Mniejszą czcionką w nawiasie zapisano tekst: „(cyfry od 0 do 8 lub litera „X”)”. Na żółtej linii umieszczony jest numer z rozwijalnym opisem: „stopień zabezpieczenia przed wnikaniem wody”.
Litera „C” to litera dodatkowa (nieobowiązująca). Mniejszą czcionką w nawiasie zapisano tekst: „(litery A, B, B, D)”. Na żółtej linii umieszczony jest numer z rozwijalnym opisem: „stopień ochrony uzytkownika przed dostępem do części niezabezpieczonych”.
Litera „H” to litera uzupełniająca (nieobowiązująca). Mniejszą czcionką w nawiasie zapisano tekst: „(litery H, M, S, W)”. Na żółtej linii umieszczony jest numer z rozwijalnym opisem: „ochrona w specyficznych przypadkach”.
Do każdego podpunktu przyporządkowano również nagrania audio, przedstawiające treść zagadnienia.
Powrót do spisu treściPowrót do spisu treści
DTR (dokumentacja techniczno – ruchowa)
Zakres przeglądu technicznego określa dla każdej maszyny lub urządzenia dokumentacja techniczno–ruchowa (DTR), która powinna zawierać:
Grafika interaktywna przedstawia zawartość dokumentacji techniczno‑ruchowej (DTR). Na środku znajduje się główny element w żółtym kółku, od którego odchodzą żółte linie prowadzące do zielonych ramek. Wewnątrz ramek znajdują się frazy napisane białą czcionką. Idąc od góry w kierunku ruchu wskazówek zegara, są to kolejno:
Treść w ramkach oraz ich definicje
dane techniczne maszyny: szczegółowa charakterystyka techniczna maszyny
instrukcja smarowania: jest to wykaz punktów smarowniczych (smarowniczek, powierzchni ślizgowych, jezdnych, ciernych) oraz rekomendowany przez producenta smar. Instrukcja zawiera również informacje na temat interwałów pomiędzy smarowaniami.
warunki gwarancji: oferowana przez producenta maszyny gwarancja, opisuje jej warunki i sposoby reklamacji
wykaz części zamiennych: wraz z rysunkami oraz oznaczeniami potrzebnymi do ich zamawiania. Są to elementy eksploatacyjne, przewidziane do wymiany po pewnym czasie.
instrukcja remontowa: zakresy remontów, normatywne przestoje remontowe, graniczne wymiary zużycia podstawowych części zamiennych, instrukcję technologiczną wykonania remontów, zestaw potrzebnych narzędzi, instrukcję przeglądów, wymagane wykwalifikowanie i przeszkolenie personelu, wymagane środki ochrony osobistej
instrukcja ustawiania maszyny: schematy podłączenia do sieci energetycznej, pneumatycznej lub hydraulicznej, zalecenia odnośnie położenia i pracy maszyny.
instrukcja montażu wraz z rysunkami technicznymi: podawana w przypadku gdy maszyna wymaga ciągłej wymiany pewnych elementów (np. narzędzi wykonawczych). Również gdy montaż wykonywany jest po stronie klienta a nie producenta maszyny. Znajdują się w niej również zalecenia odnośnie pracy i montażu, momentu i kolejności dokręcania śrub.
warunki techniczne odbioru nowej maszyny oraz po jej remoncie: podawane w celu ustalenia warunków odbioru przez klienta, potrzebne do przyszłych reklamacji i zasad BHP
instrukcja eksploatacji: ustala sposoby eksploatacji zatwierdzone przez producenta, informuje klienta o możliwościach maszyny, jej zastosowaniu i przeznaczeniu.
opis techniczny: przeznaczenie, budowa i działanie mechanizmów
instrukcja transportu wraz z rysunkami zamocowania: ustalone przez producenta dozwolone i zalecane sposoby transportu maszyny. Przydatna w przypadku dużego rozmiaru lub nieporęcznego kształtu maszyny. Wyznacza dozwolone punkty podparcia lub punkty do zawieszenia, do tego informuje o zaleceniach i wymaganiach odnośnie zabezpieczenia przed korozją, uszkodzeniami i zanieczyszczeniami (wilgoć, pył) maszyny podczas transportu.
instrukcja BHP związana z obsługą maszyny: ustalone przez producenta dozwolone i zalecane sposoby eksploatacji maszyny przez personel obsługi. Zawiera informacje dotyczące standardów użytkowania zgodne z normami. Określa wymagane środki ochrony osobistej i niedozwolone operacje podczas obsługi maszyny.
Do każdego podpunktu przyporządkowano również nagrania audio, przedstawiające treść zagadnienia.
Powrót do spisu treściPowrót do spisu treści
Cykl remontowy
Rozróżniamy obsługę techniczną jednokrotną - wykonuje się ją tylko raz, np. podczas wdrożenia urządzania do eksploatacji oraz wielokrotną.
Do najczęściej spotykanych obsług należą:
- obsługa codzienna (OC)
- obsługa okresowa (OO), nazywana także obsługą techniczną (OT)
- obsługa gwarancyjna (OG)
- zabezpieczająca (OZ)
- obsługa sezonowa (OS)
Obsługa sezonowa letnia - kontrola układu chłodzenia w związku z możliwą podwyższoną temperaturą otoczenia
Obsługa sezonowa zimowa - kontrola ocieplenia silnika maszyny, akumulatora, urządzeń grzejnych oraz urządzeń i materiałów przeciwślizgowych, 9. Remont kapitalny Zapewnia przywrócenie maszynie funkcjonalności pierwotnej. Obejmuje naprawę lub wymianę wszystkich zużytych części. Zwykle wiąże się z całkowitym demontażem maszyny.
Grafika interaktywna przedstawia cykl remontowy maszyn przemysłowych. Po lewej znajduje się piktogram przedstawiający żarówkę żarową. Po jej naciśnięciu pojawia się opis: Remonty służą do przywrócenia pierwotnej lub zbliżonej do pierwotnej wartości użytkowej maszyny lub urządzenia, natomiast przeglądy techniczne ją podtrzymują. Rozróżniamy obsługę techniczną jednokrotną - wykonuje się ją tylko raz, np. podczas wdrożenia urządzania do eksploatacji oraz wielokrotną. Do najczęściej spotykanych obsług należą: obsługa codzienna (OC) obsługa okresowa (OO), nazywana także obsługą techniczną (OT) obsługa gwarancyjna (OG) zabezpieczająca (OZ) obsługa sezonowa (OS).
Dalej na środku schematu znajduje się główny element w czarnym kółku, opisany „cykl remontowy”, od którego odchodzą żółte linie prowadzące do niebieskich ramek. Wewnątrz ramek znajdują się frazy napisane czarną czcionką. Idąc od góry w kierunku ruchu wskazówek zegara, są to kolejno:
Treść w ramkach oraz ich definicje:
OC: Powinna być wykonywana codziennie przed rozpoczęciem pracy oraz po jej zakończeniu, a także w przypadku zmiany roboczej maszyny. Obejmuje kontrolę podstawowych czynników, tj.: jakość smarowania mechanizmów i połączeń ruchomych, regulacja poluzowanych śrub i nakrętek itp., oświetlenie maszyny, osłony ochronne, zabezpieczenia. W przypadku stwierdzenia usterki należy niezwłocznie ją usunąć lub jeżeli nie jest to możliwe - wstrzymać jej pracę wraz z powiadomieniem przełożonego.
OO: nazywana też obsługą techniczną (OT), oznaczana kolejnymi numerami: OT–1, OT–2… Obejmuje czynności związane z regulacją zespołów i mechanizmów, usunięciem usterek i uszkodzeń, myciem i czyszczeniem, ustaleniem stopnia zużycia poszczególnych części i zespołów dla określenia szczegółowego zakresu naprawy.
RB: Obejmuje naprawę lub wymianę szybko zużywających się części. W zakres remontu bieżącego wchodzą również wszystkie czynności przeglądu technicznego.
RS: Obejmuje naprawę lub wymianę szybciej zużywających się części zespołów w celu zapewnienia prawidłowej eksploatacji maszyny lub urządzenia do następnego remontu średniego i kapitalnego. Remont średni obejmuje również wszystkie czynności remontu bieżącego.
OG: Obejmuje sprawdzenie stanu maszyny i należących do niej mechanizmów w okresie gwarancyjnym. Powinna być przeprowadzona przez autoryzowane jednostki lub producentów maszyn i urządzeń.
OZ: Obejmuje zabezpieczenie maszyny przed szkodliwymi czynnikami otoczenia (zabezpieczenia antykorozyjne). Wymaga sprawdzenia pokryć lakierniczych oraz w przypadku gdy istnieje taka konieczność - przywrócenia ich cech ochronnych i estetycznych.
OS: Jest wykonywana zgodnie z sezonowością wykorzystania maszyn lub w związku ze zmianą warunków pogodowych. Wymaga sprawdzenia stanu gotowości technicznej, a w razie potrzeby wymiany uszkodzonych części, smarów, odnowienia pokrycia ochronnego. Obsługa sezonowa letnia - kontrola układu chłodzenia w związku z możliwą podwyższoną temperaturą otoczenia Obsługa sezonowa zimowa - kontrola ocieplenia silnika maszyny, akumulatora, urządzeń grzejnych oraz urządzeń i materiałów przeciwślizgowych
RK: Zapewnia przywrócenie maszynie funkcjonalności pierwotnej. Obejmuje naprawę lub wymianę wszystkich zużytych części. Zwykle wiąże się z całkowitym demontażem maszyny.
Do każdego podpunktu przyporządkowano również nagrania audio, przedstawiające treść zagadnienia.
Powrót do spisu treściPowrót do spisu treści
Procedura usunięcia uszkodzenia
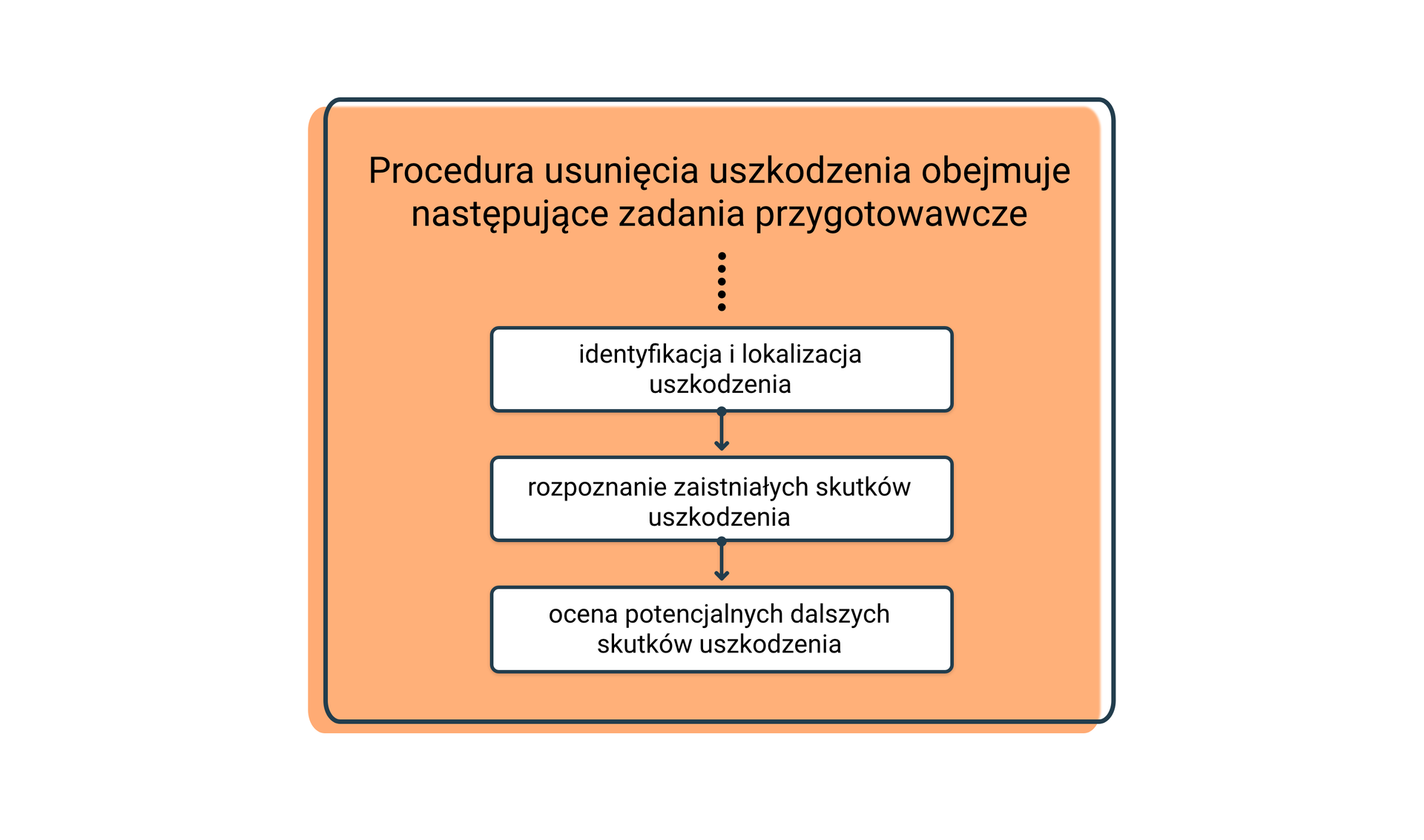
Powrót do spisu treściPowrót do spisu treści
Przykład harmonogramu smarowania i konserwacji mieszarko‑nasypywarki
W zależności od zużycia należy wykonać regulację lub wymianę łopatek, ślimaka transportowego i płyt osłonowych., 2. G/1000h oznacza kontrolę przekładni co 1000 godzin oraz ewentualne uzupełnienie oleju., 3. F/100h oznacza smarowanie uszczelki kołnierzowej smarem do łożysk tocznych w ilości 20-25 gram smaru, kontrola co 100 godzin pracy., 4. D/50-100h oznacza smarowanie koła zębatego wskazanym przez producenta lubrykantem w ilości 50-90 gram, kontrola co 50-100 godzin pracy., 5. Kontrola filtru spoiwa 50-100 godzin., 6. Kontrola filtru drobnego co 1000 godzin.
Przy każdym urządzeniu powinna znajdować się tabliczka z informacjami na temat przeglądu danej maszyny. Zawiera ona zakres przeglądów oraz czynności związanych z wymianą niezbędnych elementów maszyny umieszczonych na schemacie. Oznaczenie literowe oznacza element urządzenia, pod nią podany jest czas kontroli i ewentualnej wymiany zużytego elementu.
Grafika interaktywna przedstawia harmonogram smarowania i konserwacji mieszarko‑nasypywarki. Mieszarko‑nasypywarka przedstawiona jest schematycznie jako wysokie ramię z wysięgnikiem (po lewej stronie schematu), które umieszczone jest nad mieszarką (po prawej stronie schematu), czyli maszynie mieszającej za pomocą wałka ślimakowego. Dookoła schematu znajdują się prostokąty z różnymi pojęciami, od których poprowadzone są linie do konkretnych obszarów maszyny. Po prawej, na dole schematu znajduje się tabelka z trzema kolumnami: Miejscem smarowania; Lubrykantem; Ilością lubrykantu.
W opisanych wcześniej prostokątach, „dymkach” znajdują się pojęcia takie jak: F przez 100 ha, G przez 1000 ha, filtr drobny przez 1000 ha. Oznaczają one miejsce smarowania oraz interwały pomiędzy kontrolami. Przykładem jest F przez 100 ha - oznacza to, że miejsce oznaczone F, należy smarować co 100 godzin pracy maszyny.
Tabelka szczegółowo wyjaśnia czym są oznaczone miejsca, jaki powinien być użyty lubrykant oraz w jakiej ilości. Poniżej znajduje się lista wyjaśniająca zawartość tabelki. Pierwsze pojęcie to miejsce smarowania, drugie to lubrykant, a trzecie to ilość lubrykantu. Interwały podane są na rysunku w prostokątach:
F - Uszczelka kołnierzowa; Smar do łożysk tocznych; 20 do 25 gramów
D - Koło zębate; Mobilux EP2; 50 do 90 gramów
P - Łożysko baryłkowe; Mobilgear OGL 4 6 1; 30 do 40 gramów
O - olejarka sprężonego powietrza; Przeciwzatarciowy smar do łożysk; 130 gramów
G - przekładnia; Olej do przekładni; Ilość lubrykantu nie podana
Do każdego podpunktu przyporządkowano również nagrania audio, przedstawiające treść zagadnienia.