E‑book Obudowa konstrukcji dachowej w systemach suchej zabudowy od A do Z
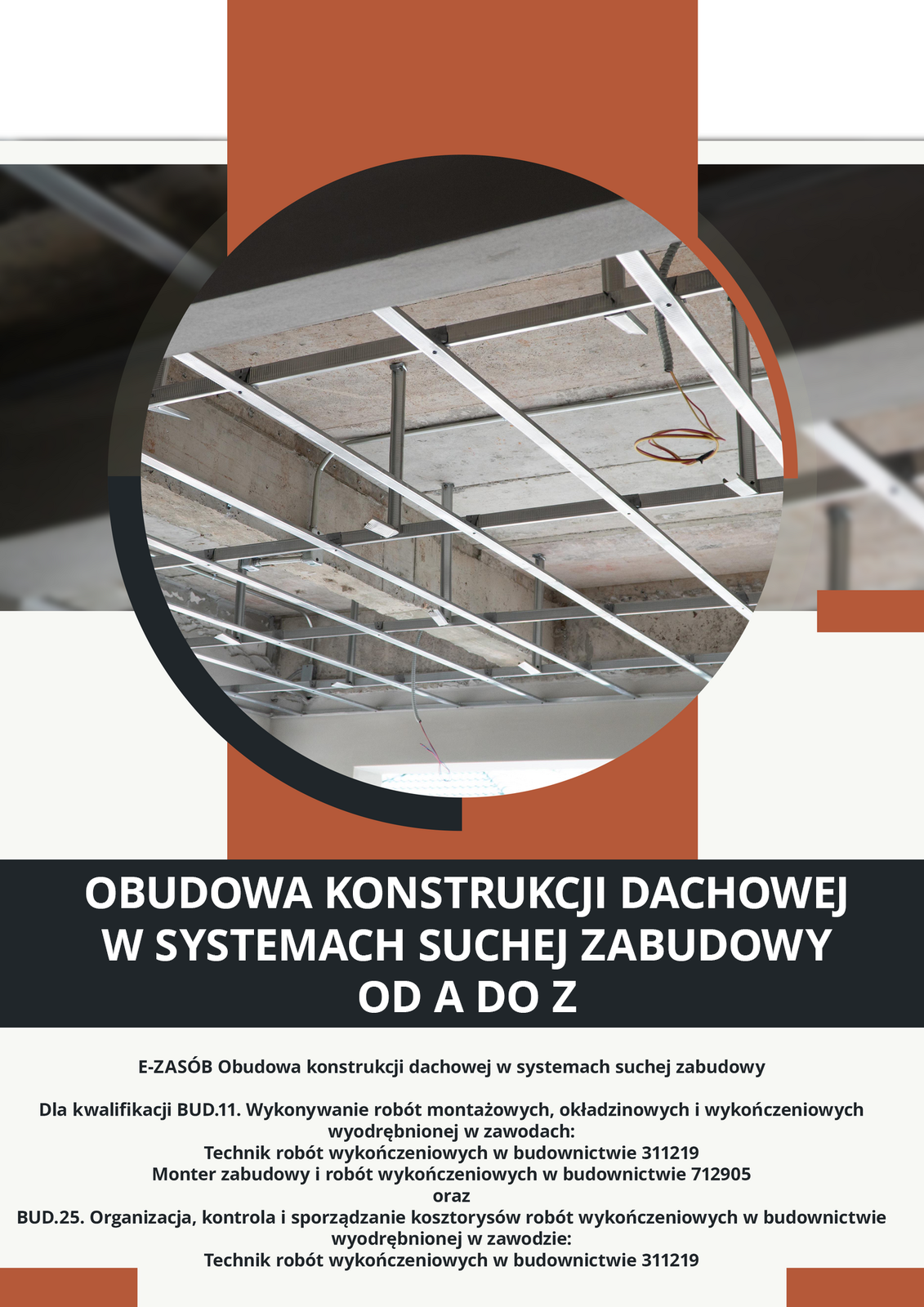
E‑BOOK Obudowa konstrukcji dachowej w systemach suchej zabudowy od A do Z
Spis treści:
1. System suchej zabudowy1. System suchej zabudowy
2. Materiały do robót w systemach suchej zabudowy2. Materiały do robót w systemach suchej zabudowy
2.1. Płyty kartonowo‑gipsowe2.1. Płyty kartonowo‑gipsowe
2.2. Profile systemowe2.2. Profile systemowe
2.3. Łączniki stosowane w systemach suchej zabudowy2.3. Łączniki stosowane w systemach suchej zabudowy
2.4. Masy szpachlowe2.4. Masy szpachlowe
2.5. Taśmy2.5. Taśmy
2.6. Tynki gipsowe2.6. Tynki gipsowe
2.7. Wełna mineralna2.7. Wełna mineralna
2.8. Akcesoria i elementy mocujące2.8. Akcesoria i elementy mocujące
3. Narzędzia do prac w technologii suchej zabudowy3. Narzędzia do prac w technologii suchej zabudowy
4. Ogólne wymogi prowadzenia robót4. Ogólne wymogi prowadzenia robót
5. Obudowa dachu w systemach suchej zabudowy5. Obudowa dachu w systemach suchej zabudowy
6. Etapy wykonywania obudowy konstrukcji dachu w systemach suchej zabudowy6. Etapy wykonywania obudowy konstrukcji dachu w systemach suchej zabudowy
6.1. Trasowanie6.1. Trasowanie
6.2. Montowanie profili stalowych6.2. Montowanie profili stalowych
6.3. Mocowanie folii paroizolacyjnej6.3. Mocowanie folii paroizolacyjnej
6.4. Montaż płyt gipsowo‑kartonowych6.4. Montaż płyt gipsowo‑kartonowych
6.5. Obróbka okien dachowych6.5. Obróbka okien dachowych
6.6. Spoinowanie i wykańczanie powierzchni płyt6.6. Spoinowanie i wykańczanie powierzchni płyt
6.7. Ocena efektu końcowego prac w systemach suchej zabudowy6.7. Ocena efektu końcowego prac w systemach suchej zabudowy
6.8. Zasady wykonywania poszczególnych elementów obudowy konstrukcji dachu6.8. Zasady wykonywania poszczególnych elementów obudowy konstrukcji dachu
7. Spis ilustracji7. Spis ilustracji
8. Bibliografia8. Bibliografia
1. System suchej zabudowy
System suchej zabudowy to system umożliwiający budowę ścian działowych, licowanie ścian wewnętrznych, zabudowę poddaszy oraz sufitów podwieszanych. Na system ten składa się skompletowany i zamontowany zestaw wyrobów: systemowych profili stalowych, płyt gipsowo‑kartonowych, systemowych taśm uszczelniających, systemowych mas szpachlowych, elementów mocujących i akcesoriów. Choć najpopularniejszym elementem systemów suchej zabudowy są płyty gipsowo‑kartonowe, to do określonych zastosowań można stosować również inne rodzaje płyt budowlanych, np. płyty gipsowo‑włóknowe, płyty cementowe, płyty drewnopochodne, np. OSB lub MFP. Obecnie na rynku budowlanym dostępne są kompletne rozwiązania systemowe – przetestowane i certyfikowane w zakresie odporności ogniowej, wytrzymałości oraz izolacji akustycznej.
System suchej zabudowy daje duże możliwości w kreowaniu przestrzeni – budowaniu ścian działowych, zabudowy skosów poddasza, obudowy pionów instalacyjnych, wykonywaniu sufitów podwieszanych. Płyty gipsowo‑kartonowe można docinać i profilować w taki sposób, by można było nimi obudować niemal każdą przestrzeń.
Konstrukcje wykonywane w systemie suchej zabudowy mają wiele zalet. Są lekkie i szybkie w montażu przy zachowaniu wysokich parametrów termoizolacyjnych, ogniochronnych i akustycznych.
Aby elementy budowlane wykonane w technologii suchej zabudowy, np. obudowa konstrukcji dachów, funkcjonowały bezawaryjnie, ich parametry i wykonanie powinny zostać prawidłowo określone i opisane w projekcie budowlanym. Istotne znaczenie ma typ zastosowanych profili, grubość blachy, z której zostały wykonane, wymiary zewnętrzne, jakość powierzchni.
Powrót do spisu treściPowrót do spisu treści
2. Materiały do robót w systemach suchej zabudowy
Powrót do spisu treściPowrót do spisu treści
2.1 Płyty gipsowo‑kartonowe
Płyta gipsowo‑kartonowa składa się z rdzenia gipsowego oraz kartonu pokrywającego obustronnie warstwę gipsu, który jest poddawany modyfikacjom za pomocą dodatków wpływających na jego wiązanie oraz gęstość. Karton przejmuje naprężenia rozciągające powstałe przy zginaniu płyty. Dzięki dodaniu do warstwy gipsu włókna szklanego oraz substancji hydrofobowych płyty zyskują dodatkowe właściwości – zmniejszoną chłonność wilgoci oraz podwyższoną odporność na działanie ognia.
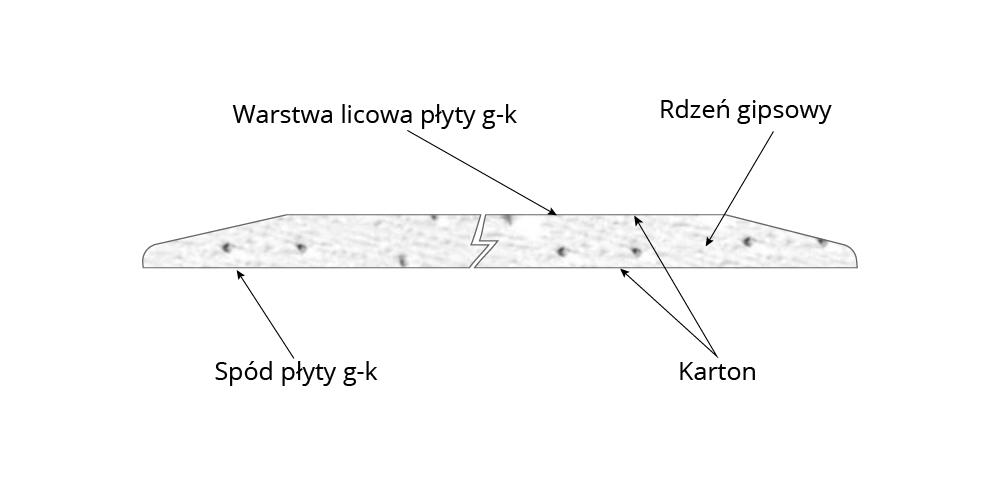
Wymagania dotyczące płyt gipsowo‑kartonowych zostały ujęte w Polskiej Normie PN‑EN 520+A1: 2012. Płyty te produkowane są w następujących wymiarach:
grubość – 6,5; 9,5; 12,5; 15,0; 18,0 mm;
szerokość – 600; 625; 900; 1200 i 1250 mm;
długość – od 2000 do 4000 mm oraz inna.
Rodzaje płyt gipsowo‑kartonowych:
Typ A – płyta standardowa, budowlana, przeznaczona do pomieszczeń o wilgotności względnej nieprzekraczającej 70%;
Typ H2 – płyta impregnowana o podwyższonej odporności na działanie wilgoci, przeznaczona do pomieszczeń o wilgotności względnej nieprzekraczającej 70% lub nawet 85% – jednak czas działania podwyższonej wilgotności nie powinien być dłuższy niż 10 godzin na dobę; rdzeń płyty H2 został wzmocniony środkami hydrofobowymi, dzięki czemu jej nasiąkliwość wynosi do 10%; wyróżnikiem tego rodzaju płyt jest zielony karton umieszczony po stronie licowej;
Typ F – płyta ogniochronna, stosowana do budowy przegród klasyfikowanych pod względem odporności ogniowej; dodatek włókien szklanych poprawia spójność rdzenia gipsowego podczas działania wysokich temperatur; można ją stosować w pomieszczeniach, w których wilgotność względna nie przekracza 70%; płyty tego rodzaju są różowe lub szare z czerwonymi oznaczeniami;
Typ DF – płyta ognioochronna o właściwościach płyty typu F charakteryzująca się kontrolowaną gęstością rdzenia gipsowego – minimum 800 kg/m3 i 10 kg/m2 przy grubości 12,5 mm; płyty tego typu wykańczane są od strony licowej kartonem w kolorze różowym;
Typ FH2 – płyta wodo- i ognioochronna, posiada właściwości płyty typu F i H2;
Typ DFH2 – płyta wodo- i ognioochronna o właściwościach płyt typu DF oraz H2.
Innym rodzajem płyt są płyty gipsowo‑włóknowe, do których produkcji wykorzystuje się rozdrobnioną celulozę i wypełniacze, spoiwem jest gips naturalny lub syntetyczny. Płyty tego rodzaju mają jednorodną strukturę, co pozwala na łatwiejszy montaż i obróbkę.
Rodzaje krawędzi płyt g‑k:
KS – spłaszczone krawędzie umożliwiające ukrycie styków, łączenia wykonywane są za pomocą taśmy zbrojącej i systemowych mas szpachlowych;
NS – rodzaj krawędzi KS o mniejszym kącie spłaszczenia;
PRO – rodzaj krawędzi KS z niskim równoległym przekrojem spłaszczenia;
KPOS – krawędź półokrągła spłaszczona; wymaga szpachlowania styków; do łączenia płyt stosuje się systemowe masy szpachlowe z taśmą zbrojącą lub masami szpachlowymi przeznaczonymi do spoinowania bez taśmy;
KP – krawędzie proste; płyty łączone są na styk bez szpachlowania.
krawędzie cięte – wykonywane poprzez przycinanie fabrycznych płyt g‑k, wymagają sfazowania łączonych krawędzi pod kątem 45°.
Przedstawione rodzaje krawędzi płyt gipsowo‑kartonowych również zostały ujęte w Polskiej Normie PN‑EN 520+A1: 2012.
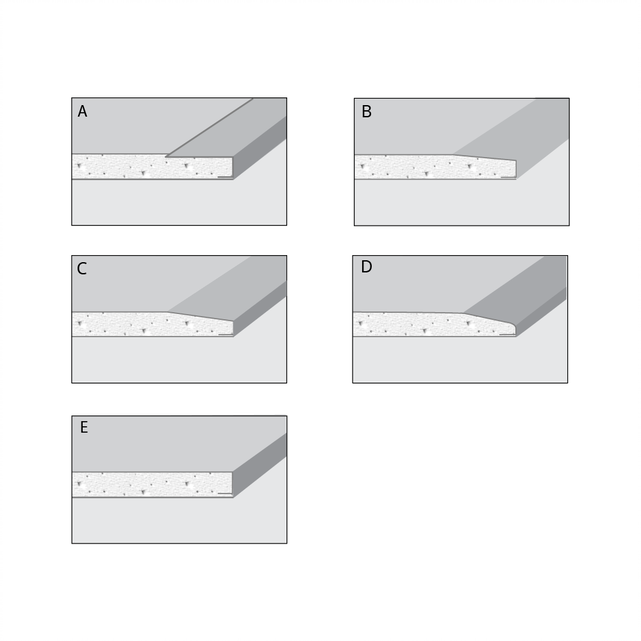
Płyty gipsowo‑kartonowe powinny być magazynowane w pomieszczeniach zamkniętych lub zadaszonych.
Powrót do spisu treściPowrót do spisu treści
2.2 Profile systemowe
Do wykonania odpowiedniej konstrukcji (rusztu) należy użyć systemowych profili stalowych, wykonanych z zabezpieczonej antykorozyjnie blachy stalowej (np. ocynkowanej), profilowanej na zimno. Profile systemowe produkowane są w oparciu o wymagania zawarte w normie PN‑EN 14195:2015‑02 – Elementy szkieletowej konstrukcji metalowej do stosowania z płytami gipsowo‑kartonowym lub w obowiązujących aprobatach technicznych.
Profile systemowe dzielą się na trzy grupy:
1. profile ścienne przeznaczone do wykonywania konstrukcji lekkich szkieletowych ścian działowych, okładzin ściennych i przedścianek (grubość nominalna blachy stalowej profili ściennych i sufitowych wynosi 0,6 mm lub 0,55 mm, z tolerancją określoną przez dostawcę systemu),
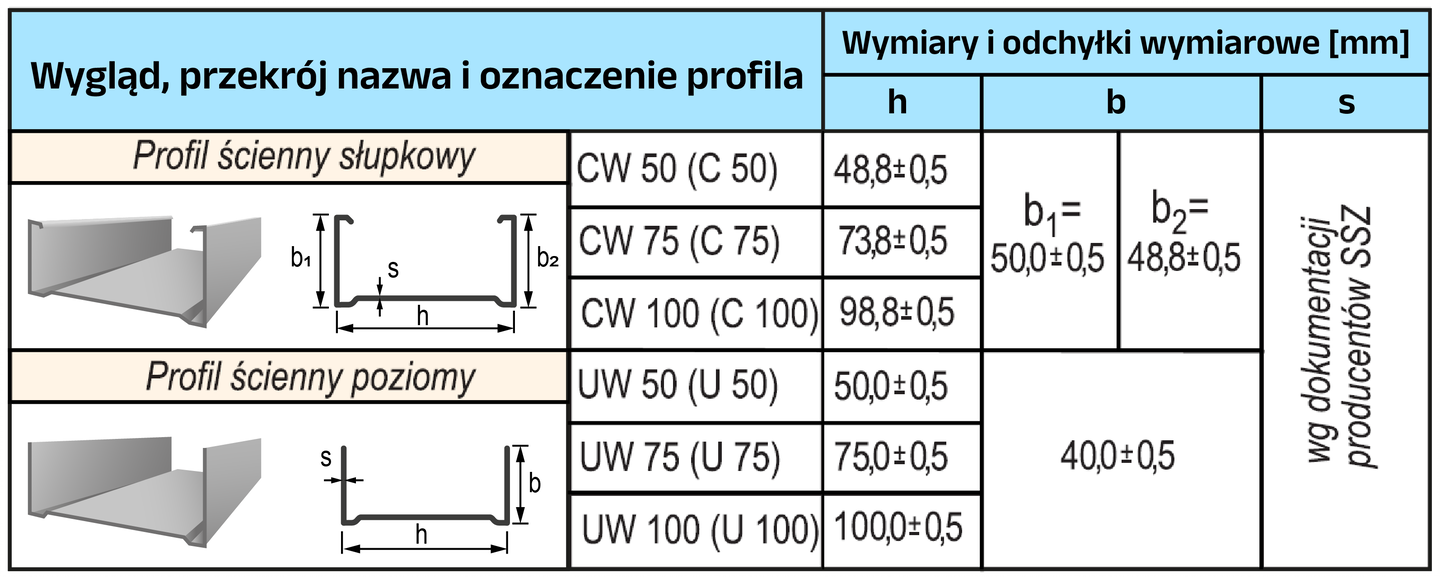
Tabela 1. Profile stalowe ścienne (h – wysokość profi u – szerokość środka ceownika, b – szerokość półek ceownika – w profilach CW (C) szerokości półek nie są jednakowe, s – grubość blachy).
2. profile ościeżnicowe przeznaczone do osadzania drzwi w ścianach działowych oraz do wykonywania wzmocnień rusztu ścian w nietypowych rozwiązaniach (wykonane z blachy stalowej o grubości co najmniej 1,8 mm; stosowanie profili o grubości nominalnej 0,5 mm wymaga opracowania odrębnego projektu technicznego uwzględniającego mniejszą sztywność profili).
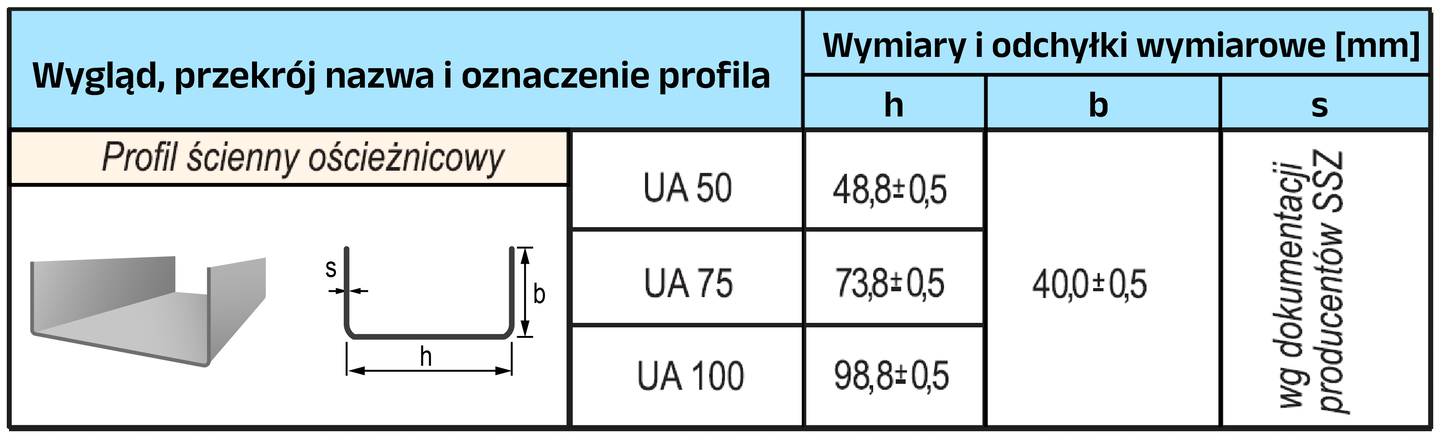
3. profile sufitowe do wykonywania konstrukcji sufitów podwieszanych oraz okładzin ściennych, sufitowych i zabudowy poddaszy (grubość nominalna blachy stalowej profili ściennych i sufitowych wynosi 0,6 mm lub 0,55 mm, z tolerancją określoną przez dostawcę systemu),
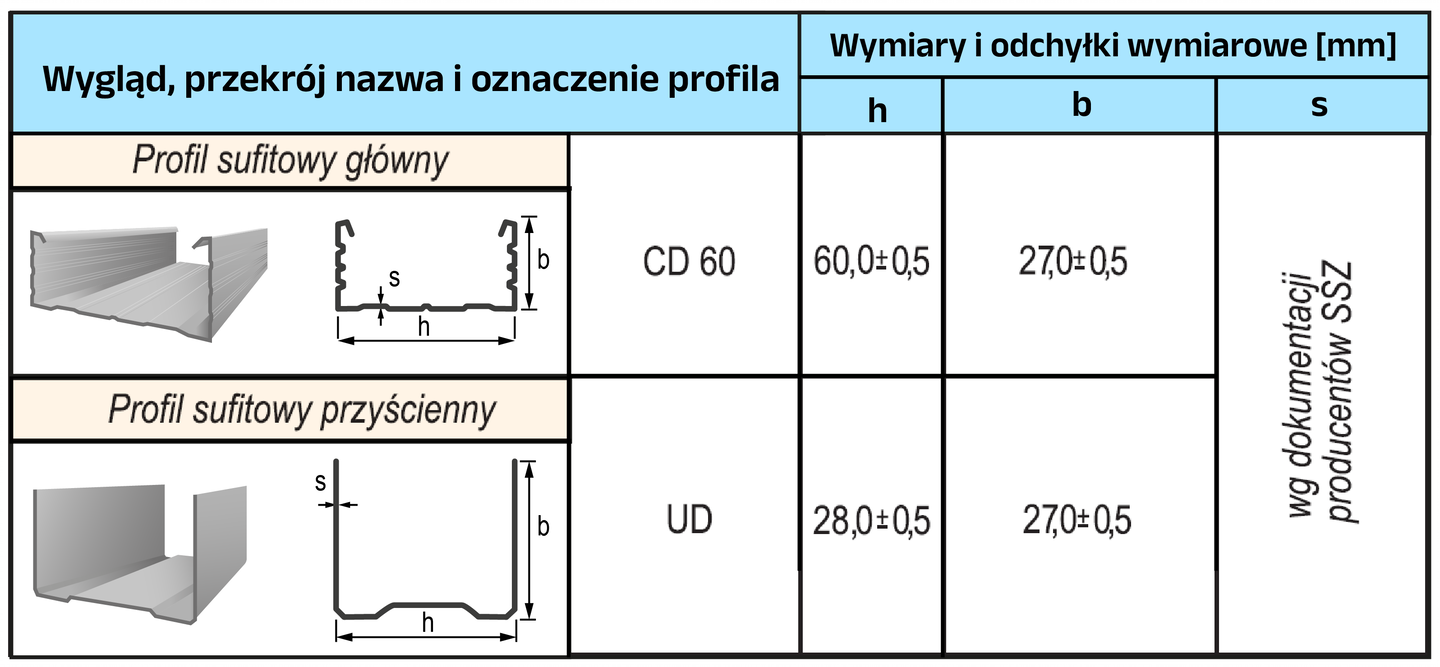
Zastosowanie niesystemowych profili ze zbyt cienkiej blachy prowadzi do utraty gwarancji systemowej w kontekście rozwiązania konstrukcyjnego oraz utraty zdefiniowanych parametrów technicznych (odporność ogniowa, izolacyjność akustyczna i wytrzymałość mechaniczna).
Profile specjalne:
profil kapeluszowy pozwala na wykonywanie elementów dekoracyjnych, zabudowy poddaszy, okładzin sufitowych lub okładzin ściennych; zastosowanie tego rodzaju profilu pozwala na wykonanie zabudowy o grubości ok 30 mm;
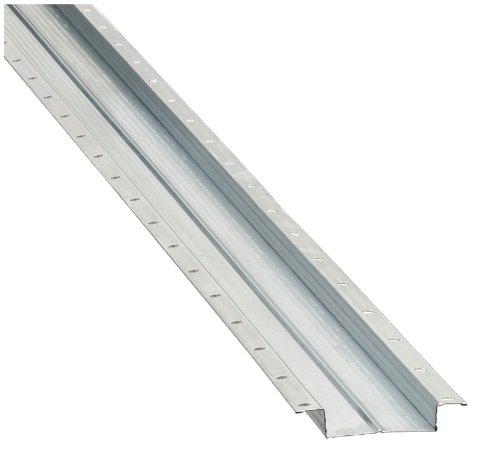
profil uniwersalny FLEX przeznaczony jest do stosowania w narożach wklęsłych i wypukłych;
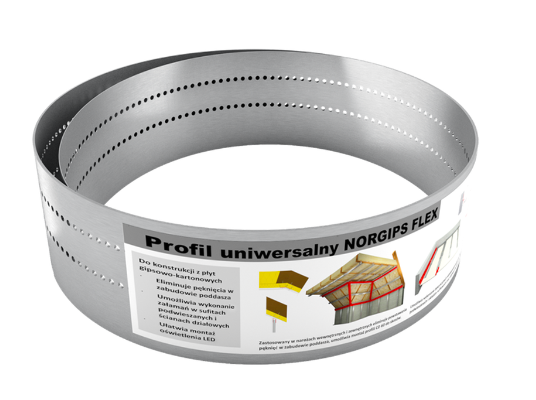
profil V stosowany jest w zabudowie poddaszy, zapobiega powstawaniu pęknięć i zarysowań w miejscach łączenia się płaszczyzn płyt g‑k (np. skosów z sufitami lub ścianami); mocowany jest poprzez środnik do skrajnych profili UD 60, które stanowią konstrukcję pierwszej płaszczyzny poddasza;
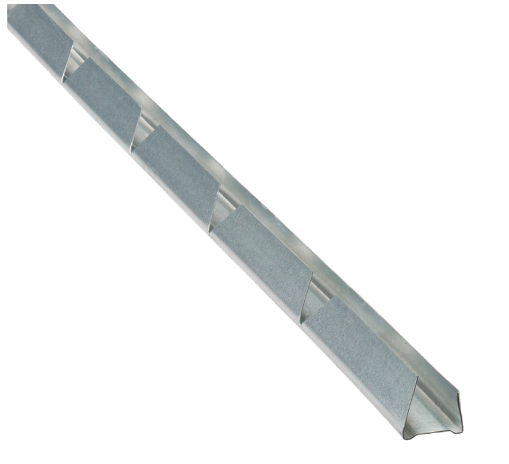
profil narożnikowy umożliwia estetyczne wykończenie i zabezpieczenie przed pękaniem oraz uszkodzeniami narożników obudowy okien dachowych lub w innych miejscach.
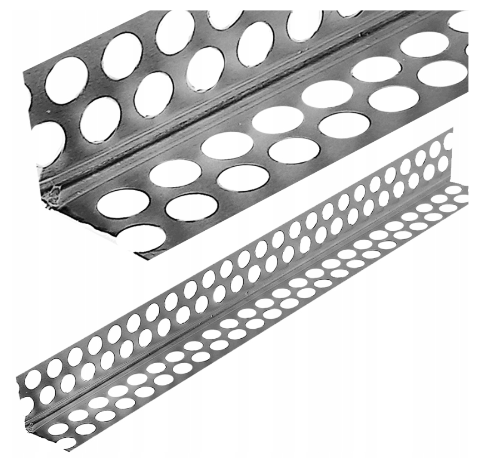
Powrót do spisu treściPowrót do spisu treści
2.4 Masy szpachlowe
Połączenia płyt g‑k, uzupełnianie ubytków oraz wygładzanie powierzchni ścian i sufitów wykonuje się przy użyciu mas szpachlowych. Mają one formę gotowych do użycia mas lub proszku wymagającego połączenia z wodą w odpowiednich proporcjach. Do spoinowania konstrukcyjnego i ostatecznego połączeń pomiędzy płytami gipsowo‑kartonowymi oraz do wypełniania uszczelnień obwodowych na połączeniu ściany lub sufitu z konstrukcją budynku służą systemowe masy szpachlowe.
Masy te produkowane są w oparciu o wymagania zawarte w normie PN‑EN 13963:2014‑10 – Materiały do spoinowania płyt gipsowo‑kartonowych.
Wyróżniamy cztery typy mas szpachlowych:
– masę szpachlową konstrukcyjną – stosowaną do spoinowania płyt g‑k z taśmą zbrojącą;
– masę szpachlową finiszową (wykończeniową) – stosowaną do wykańczania powierzchni płyt g‑k i ich połączeń;
– masę szpachlową dwufunkcyjną (konstrukcyjną i finiszową) – stosowaną zarówno do łączenia płyt g‑k, jak również do wykańczania ich powierzchni oraz połączeń;
– masę szpachlową konstrukcyjną do stosowania bez taśmy zbrojącej do krawędzi KPOS.
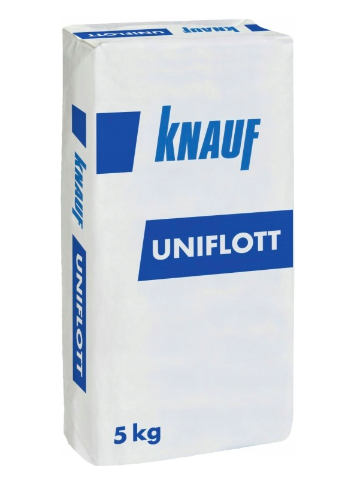
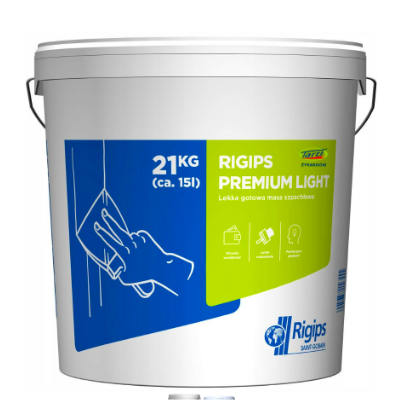
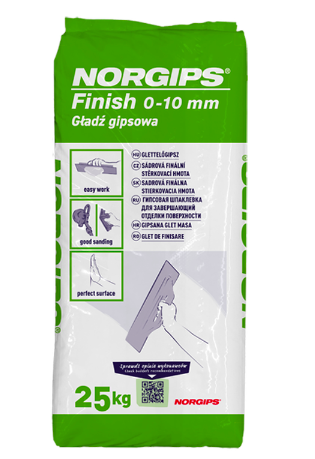
Powrót do spisu treściPowrót do spisu treści
2.5 Taśmy do wzmacniania połączeń płyt
Szpachlowanie połączeń między płytami gipsowo‑kartonowymi, tj. krawędzi ciętych, wykonywane jest z zastosowaniem taśm spoinowych, które zapobiegają powstawaniu pęknięć w miejscach łączenia płyt. Taśmy wykorzystuje się do wzmacniania połączeń pionowych i poziomych, a także narożników u styku prostopadłych płyt oraz styku ścian ze skosami lub sufitem.
Istnieje kilka rodzajów materiałów zbrojących: taśmy papierowe, flizelinowe, siatki z włókna szklanego lub taśmy kompozytowe typu tuff‑tape. Taśma papierowa stanowi materiał kompatybilny z wierzchnią warstwą płyty i przewidziana jest do zatopienia w masie szpachlowej w miejscu łączenia spoiny. Przed zatopieniem jej w masie szpachlowej, należy ją zwilżyć. Taśma flizelinowa powstaje ze sprasowanych ze sobą włókien szklanych i nie jest tak wytrzymała jak taśma papierowa. Kolejnym materiałem zbrojącym są siatki z włókna szklanego, zapewniające trwałość łączenia w przypadku działania sił rozciągających wzdłuż wątku lub osnowy płyt. Taśmy tuff‑tape powstają z kopolimeru etylenu i octanu winylu, bawełny, wełny oraz kleju lateksowego. Stosowane są nie tylko do łączenia płyt, ale także do maskowania pęknięć powstałych na ścianach lub sufitach oraz do naprawy połączeń, które uległy zniszczeniu.
Taśmy papierowe, flizelinowe oraz tuff‑tape wymagają przynajmniej dwóch warstw masy szpachlowej, wstępnej, na którą nakłada się taśmę, oraz warstwę nakładaną na taśmę. W przypadku siatek zbrojących masę szpachlową nakłada się na przyklejoną warstwę zbrojącą.
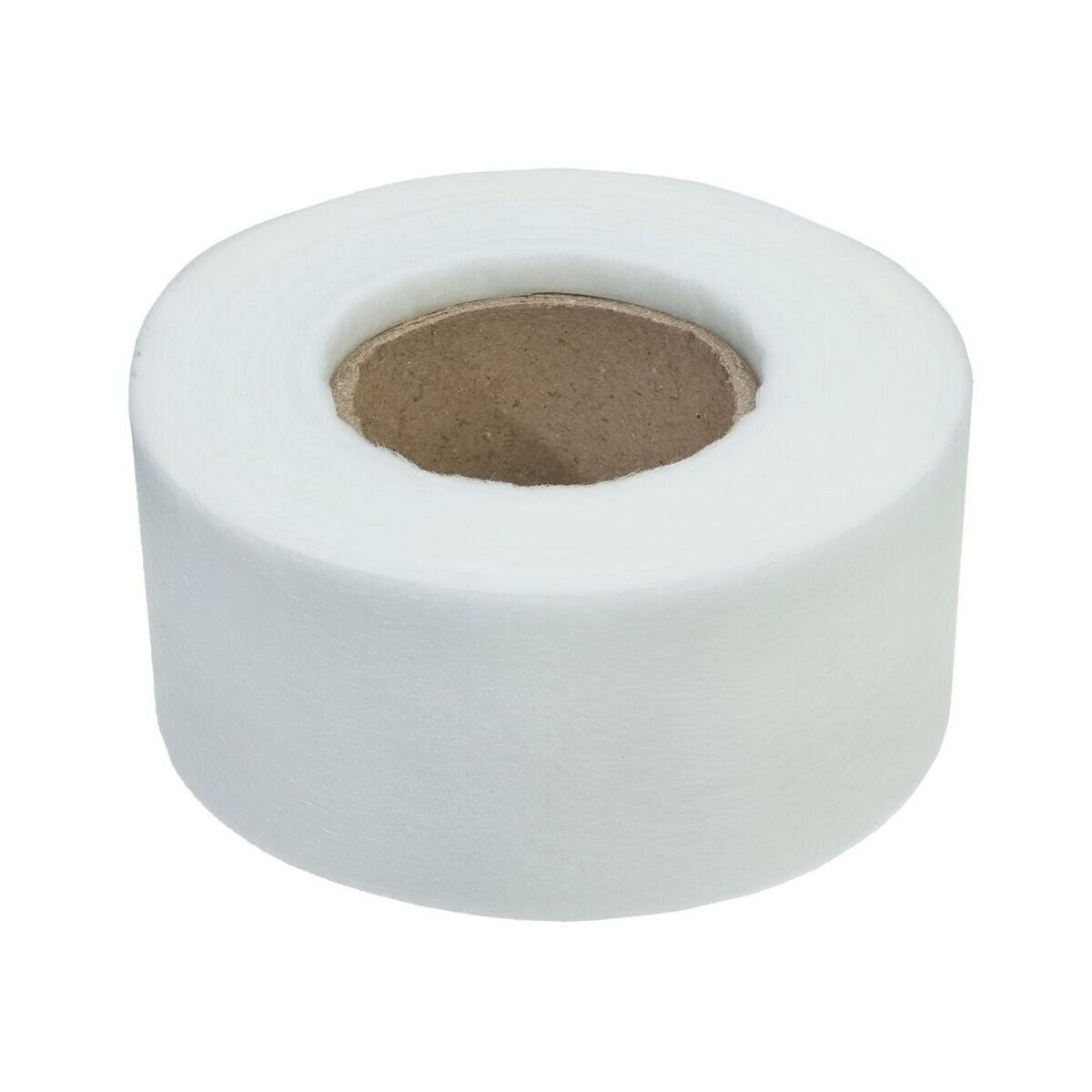
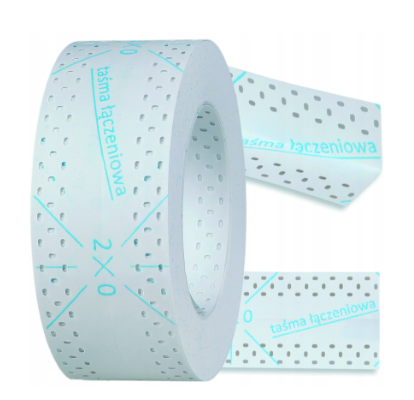
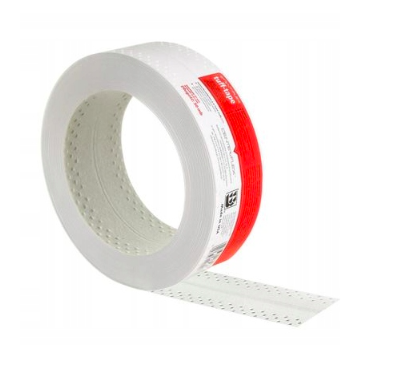
Powrót do spisu treściPowrót do spisu treści
2.6 Tynki gipsowe
Tynki gipsowe stosowane są do wykonywania wypraw tynkarskich w pomieszczeniach zamkniętych. Zapewniają gładszą powierzchnię niż tynki cementowo‑wapienne, dlatego często stosowane są do wykańczania ścian i sufitów. Głównymi składnikami tynków gipsowych są: wysokiej jakości gips, kruszywo kalibrowane (średnica do 1,2 mm), uszlachetniające dodatki, np. plastyfikatory i opóźniacze wiązania.
Tynki te dostępne są pod postacią suchych mieszanek wymagających połączenia z wodą lub gotowych mas i past.
Tynki gipsowe są wykonywane w dwóch technologiach:
– tynki maszynowe, produkowane na budowach przy zastosowaniu specjalnych agregatów tynkarskich,
– tynki ręczne, preferowane przy wykonawstwie prac remontowych z niewielkimi powierzchniami do otynkowania (np. do 50 m2).
Tynk gipsowy jest określany mianem tynku „ciepłego”.
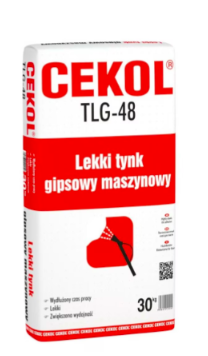
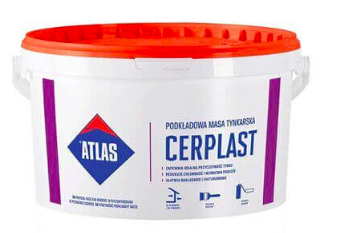
Powrót do spisu treściPowrót do spisu treści
2.7 Wełna mineralna
W systemach suchej zabudowy ważnym elementem jest warstwa izolacyjna umieszczana pomiędzy płytami w konstrukcji ścian działowych, w sufitach podwieszanych oraz w konstrukcjach obudowy poddaszy. Jej zadaniem jest izolacja termiczna i akustyczna. Materiałem, z którego wykonuje się warstwę izolacyjną najczęściej jest wełna mineralna, charakteryzująca się niskim współczynnikiem przewodzenia ciepła, niepalnością, ogniochronnością oraz znakomitymi właściwościami pochłaniania dźwięków. Wełna mineralna jest materiałem wytrzymałym mechanicznie, sprężystym, wodoodpornym, paroprzepuszczalnym oraz zachowującym stałość wymiarów i kształtów, jest także materiałem o wysokiej odporności biologicznej i chemicznej.
Wełna mineralna może być produkowana z bazaltu, gabra, dolomitu lub kruszyw wapiennych za pomocą wytapiania w temperaturze przekraczającej 1400 stopni Celsjusza – jest to wełna skalna. Inną odmianą wełny mineralnej jest wełna szklana, która powstaje w podobny sposób z piasku kwarcowego i drobno potłuczonego szkła. Włókna łączy się lepiszczem, formuje, prasuje i przycina na określony wymiar. 60% surowców znajdujących się w tych materiałach może pochodzić z recyklingu. Parametrem określającym izolacyjność cieplną wełny mineralnej jest współczynnik przewodzenia ciepła – im niższa jego wartość, tym lepsza izolacja termiczna. W przypadku wełny mineralnej współczynnik ten może wynosić już nawet 0,031 W/mK.
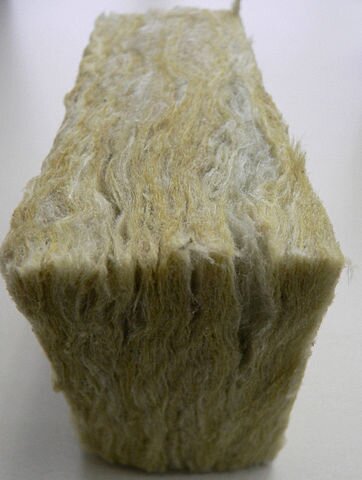
2.8 Akcesoria i elementy mocujące
Wśród akcesoriów wykorzystywanych w systemach suchej zabudowy, należy wymienić:
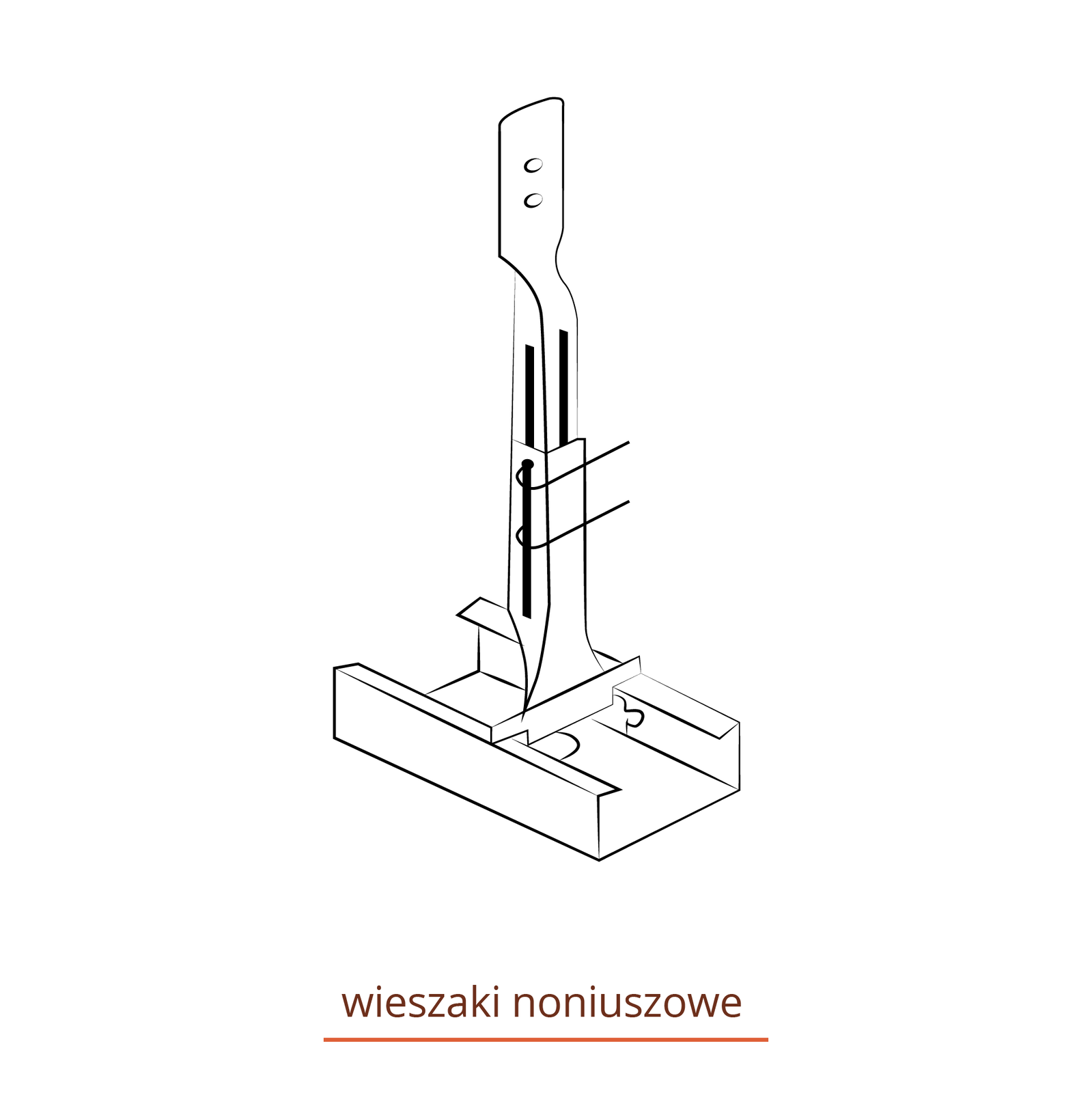
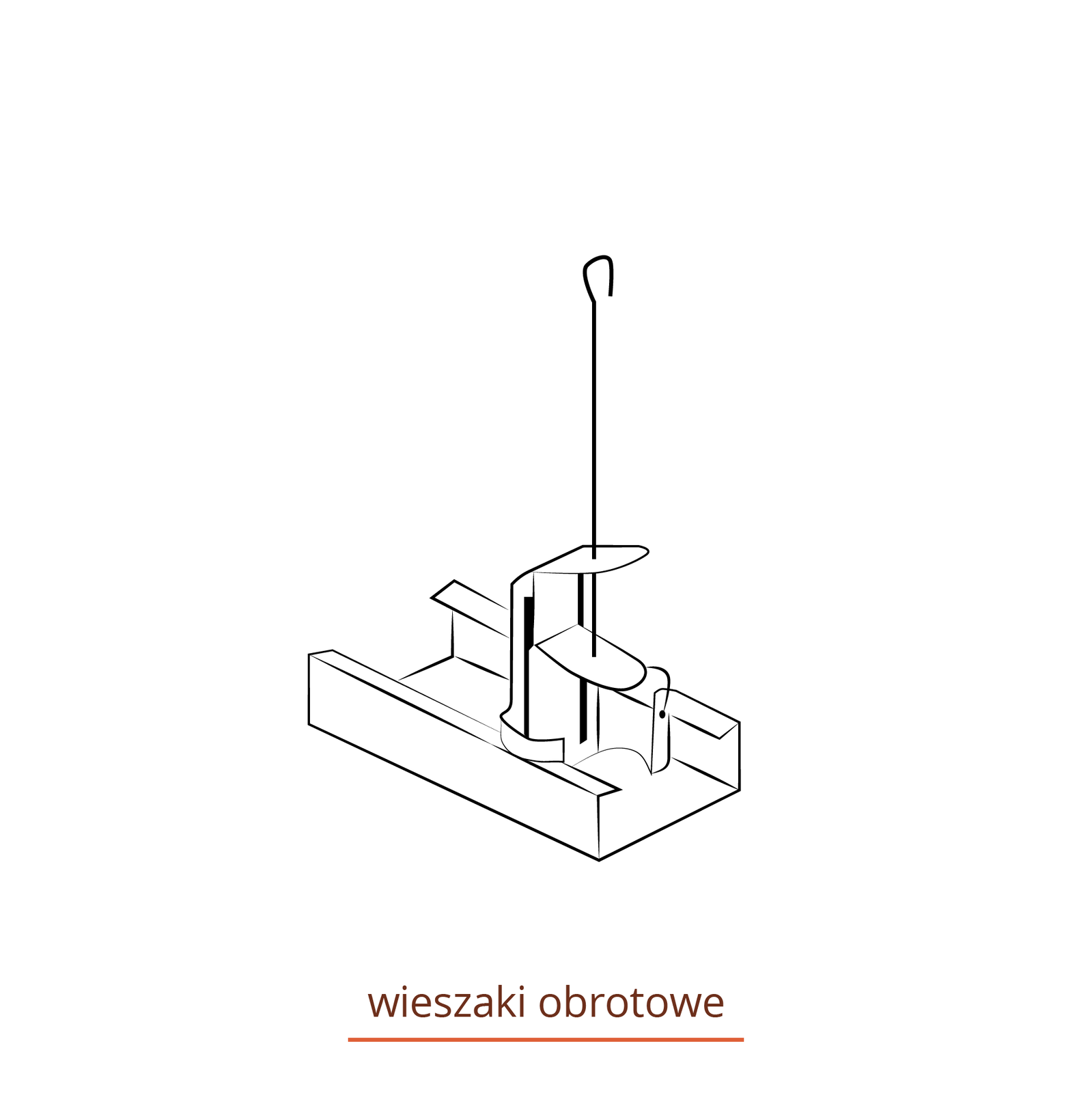
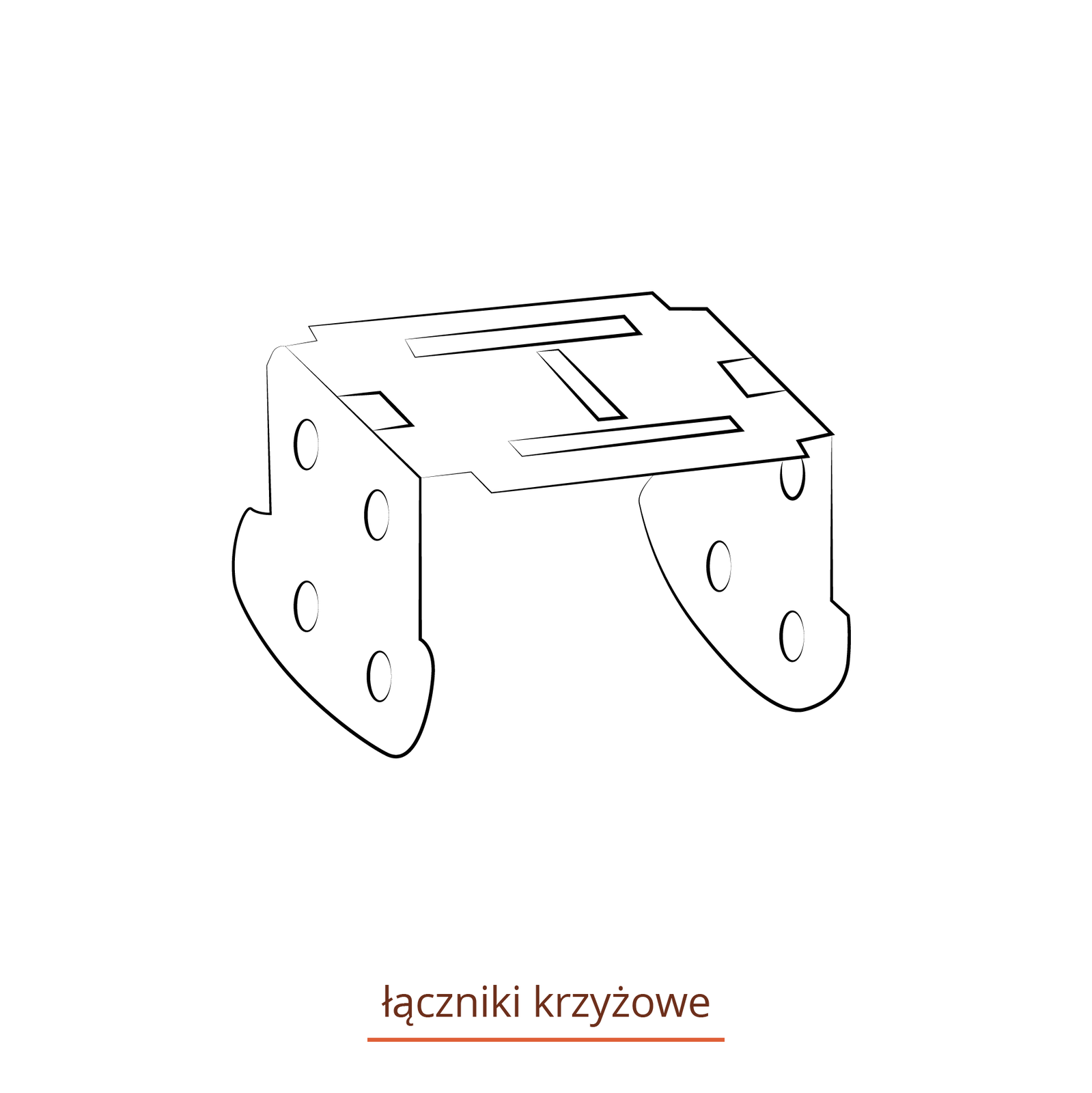
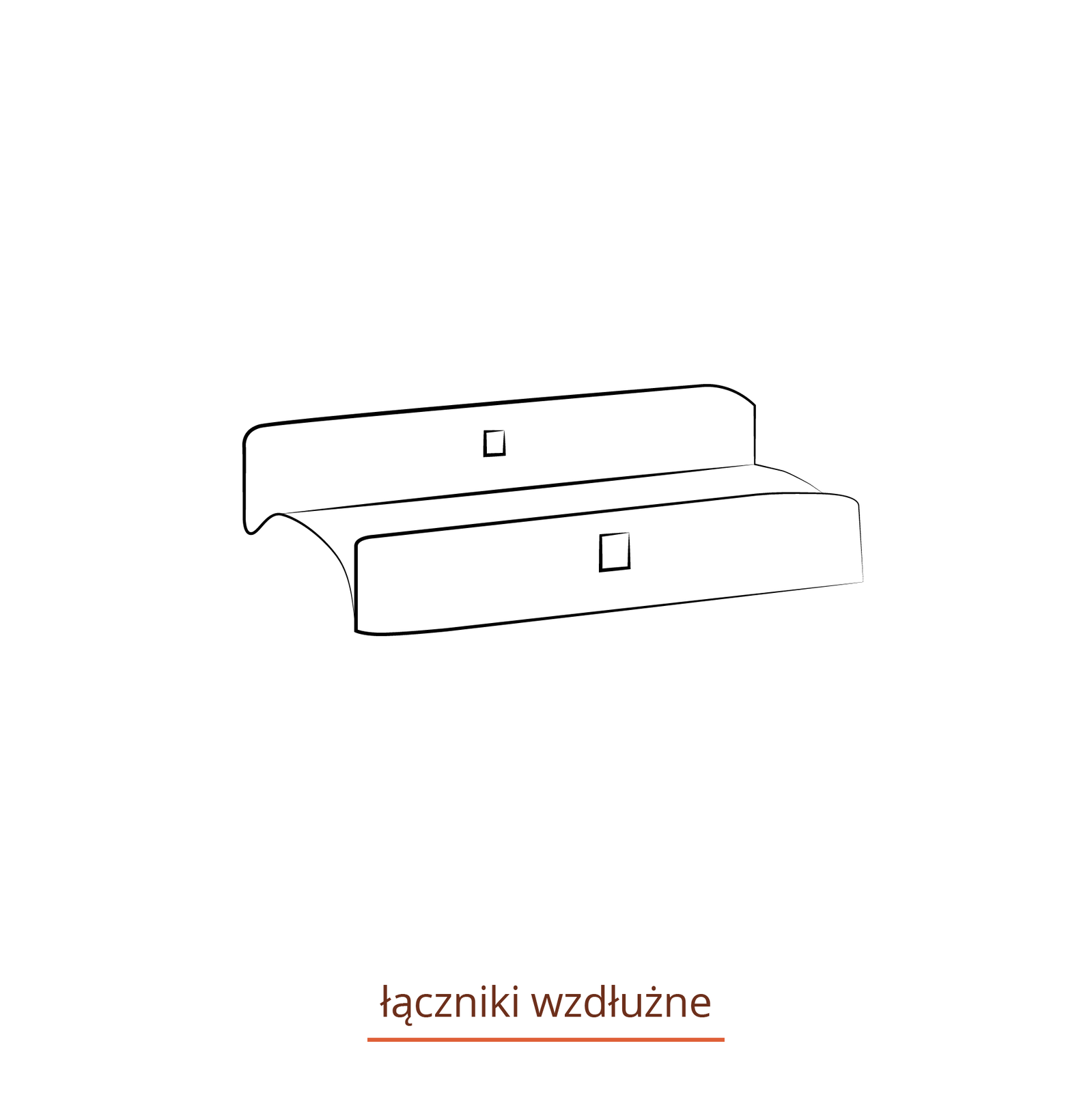
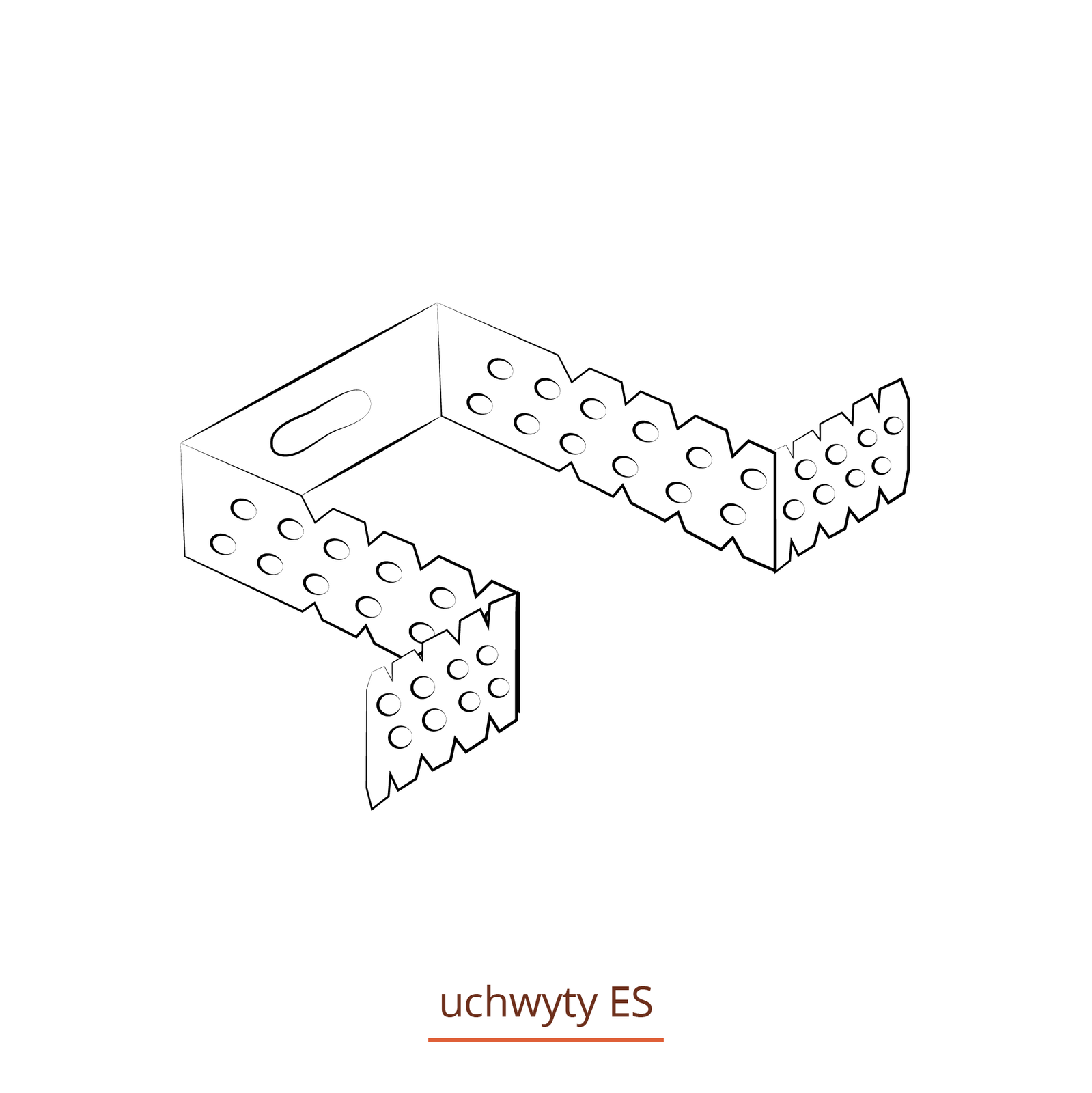
Elementy mocujące używane w systemach suchej zabudowy to:
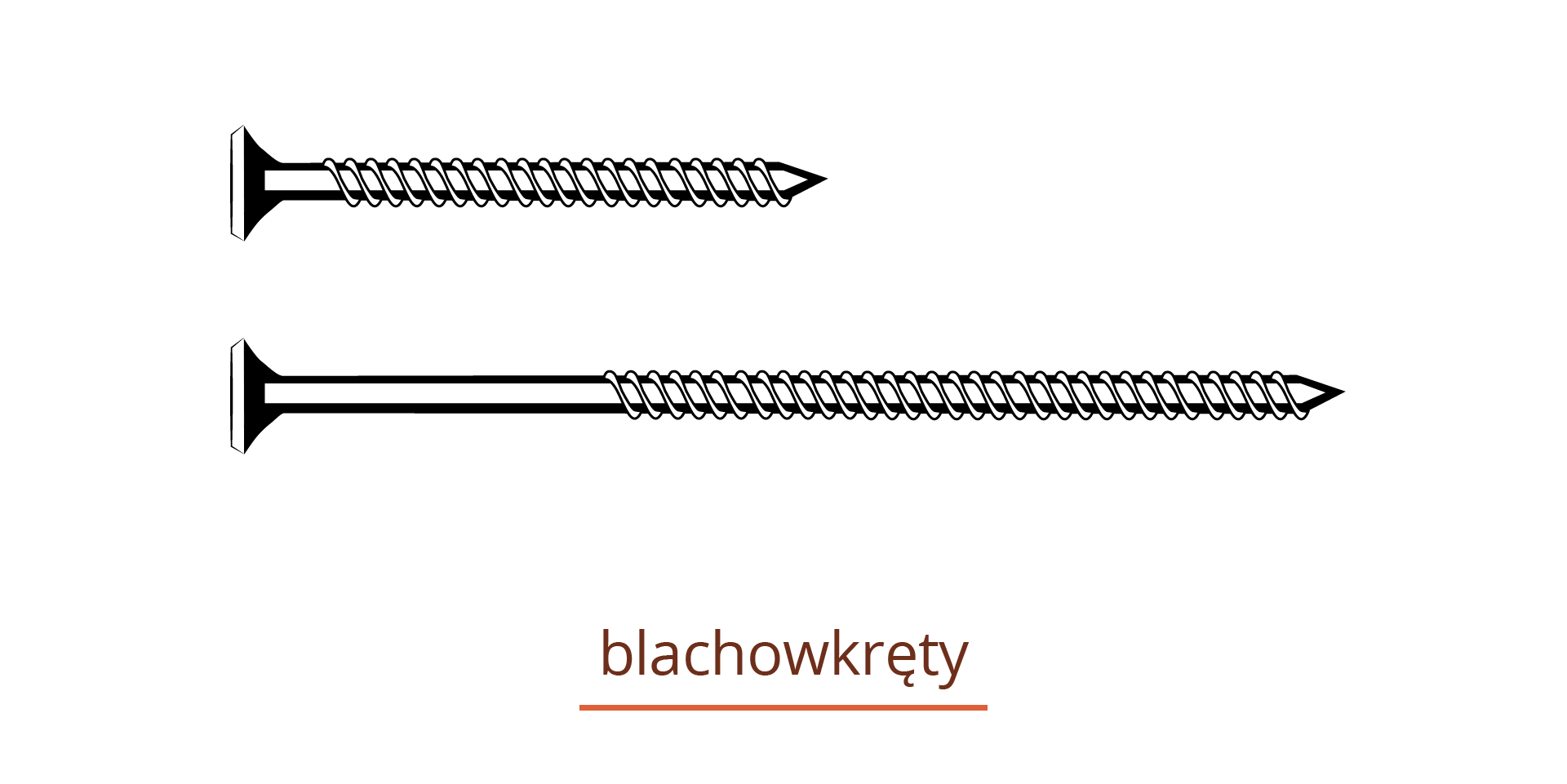
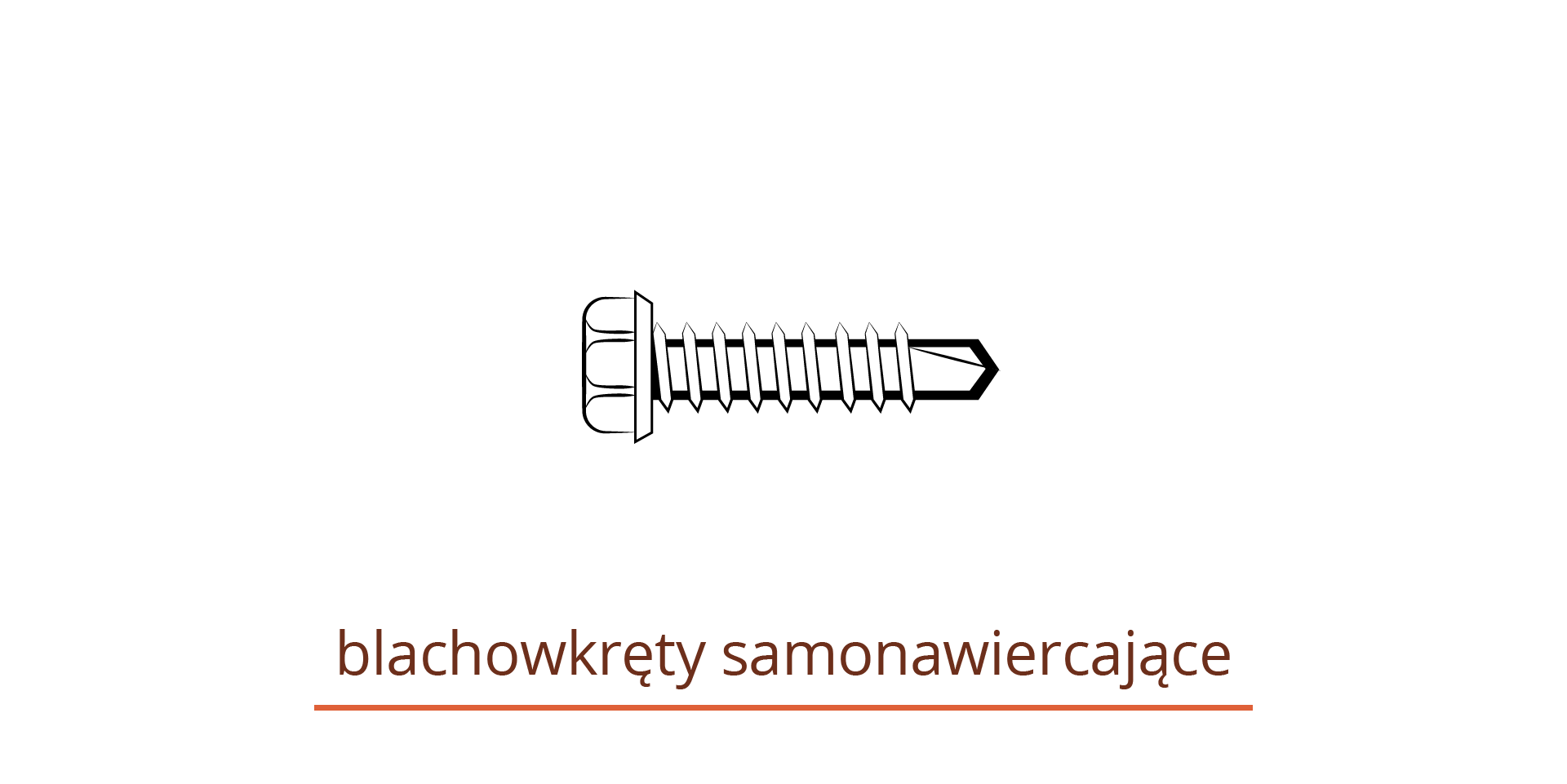
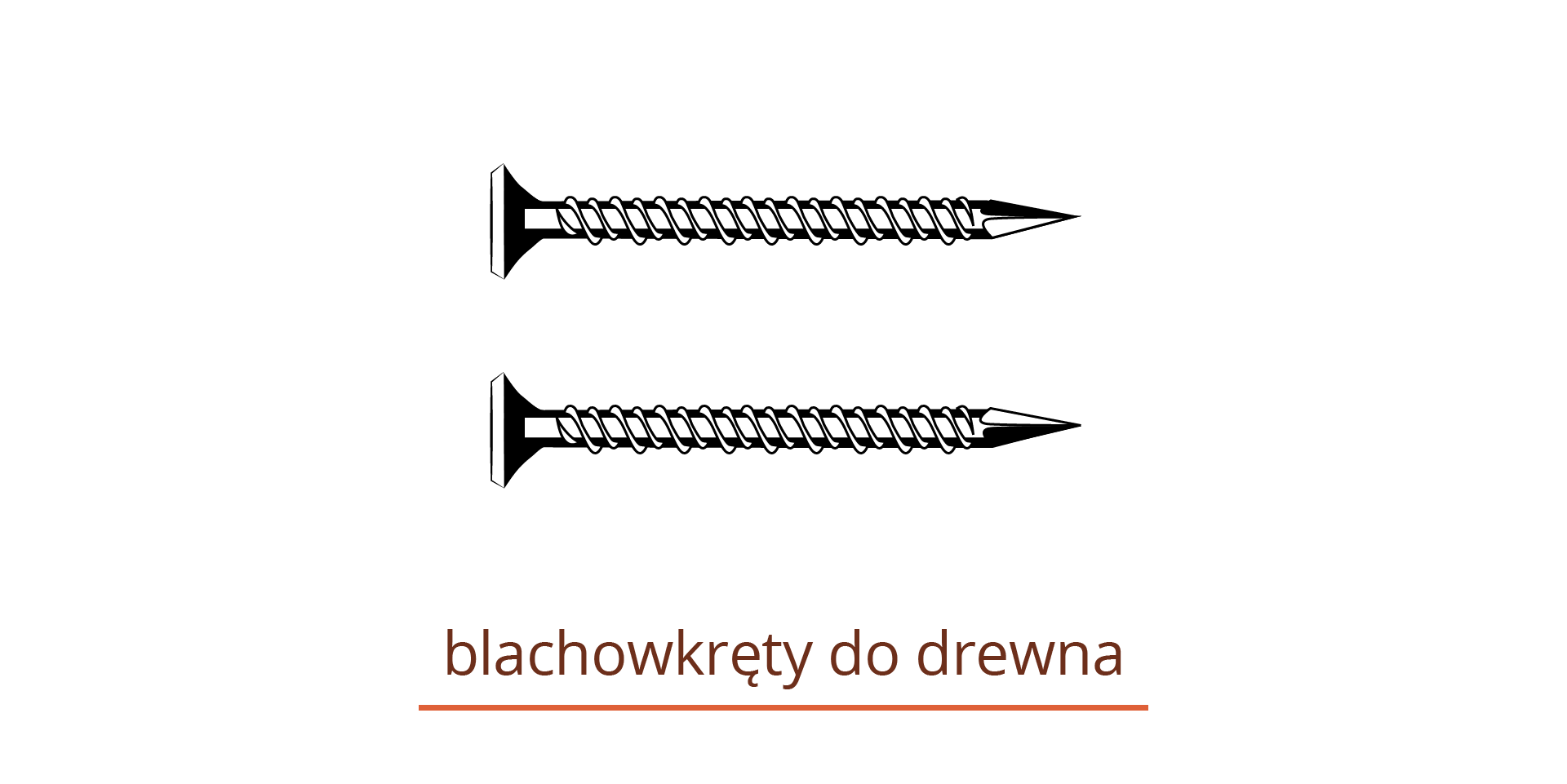
Powrót do spisu treściPowrót do spisu treści
3. Narzędzia do prac w technologii suchej zabudowy
a) Narzędzia do cięcia płyt gipsowo‑kartonowych:
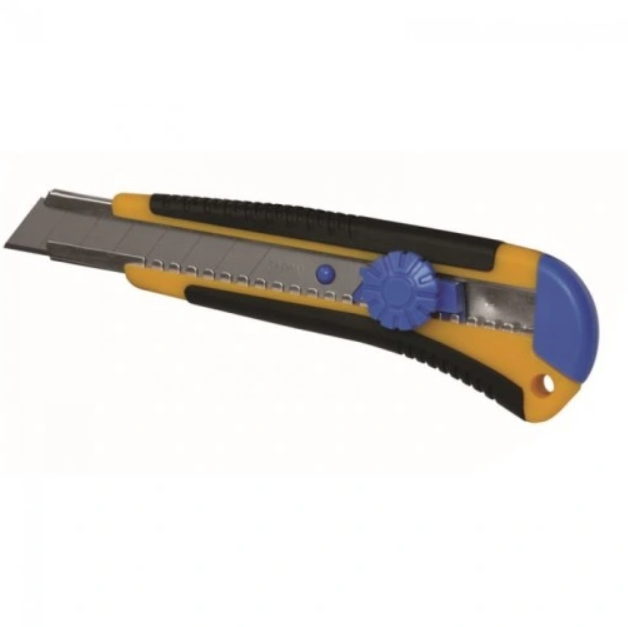
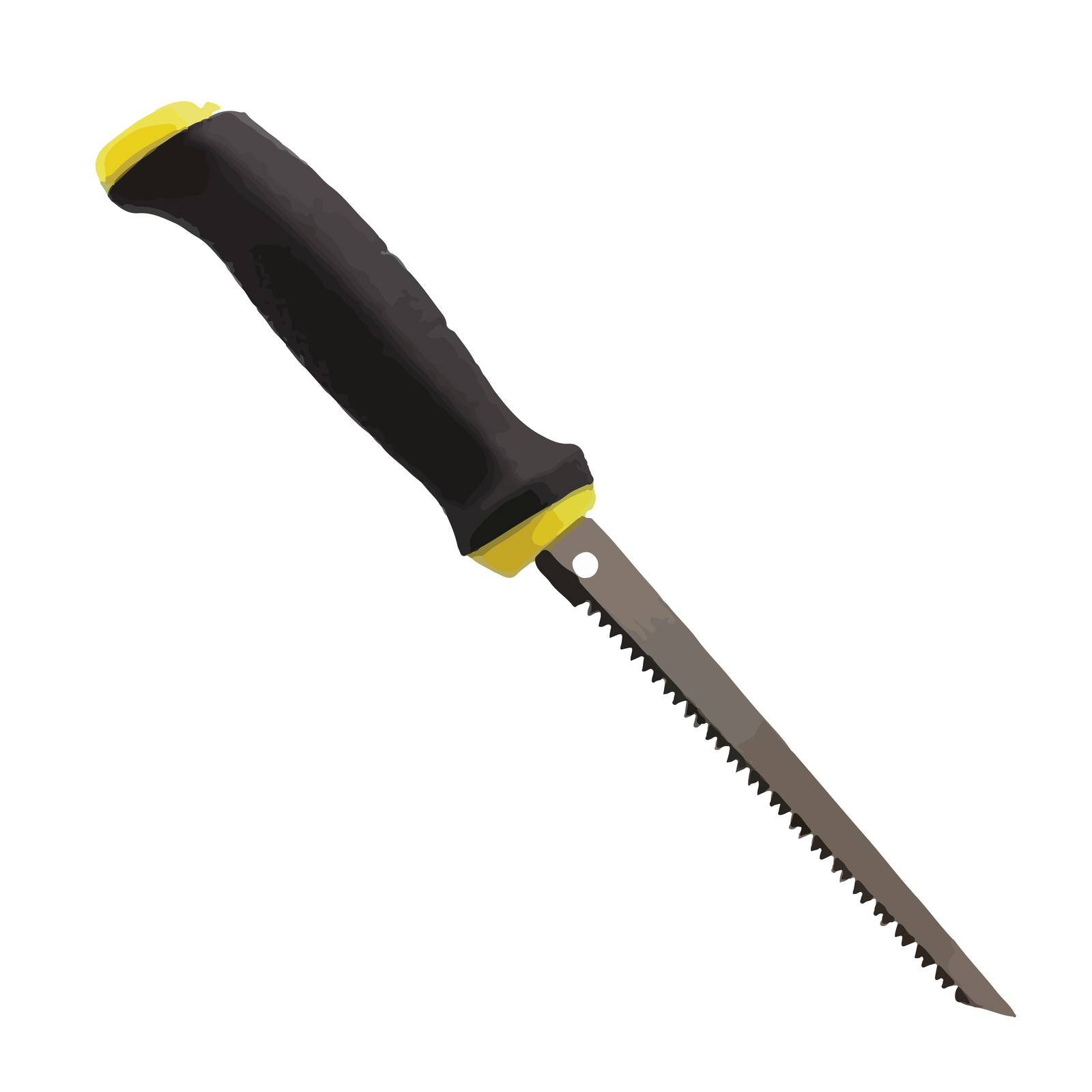
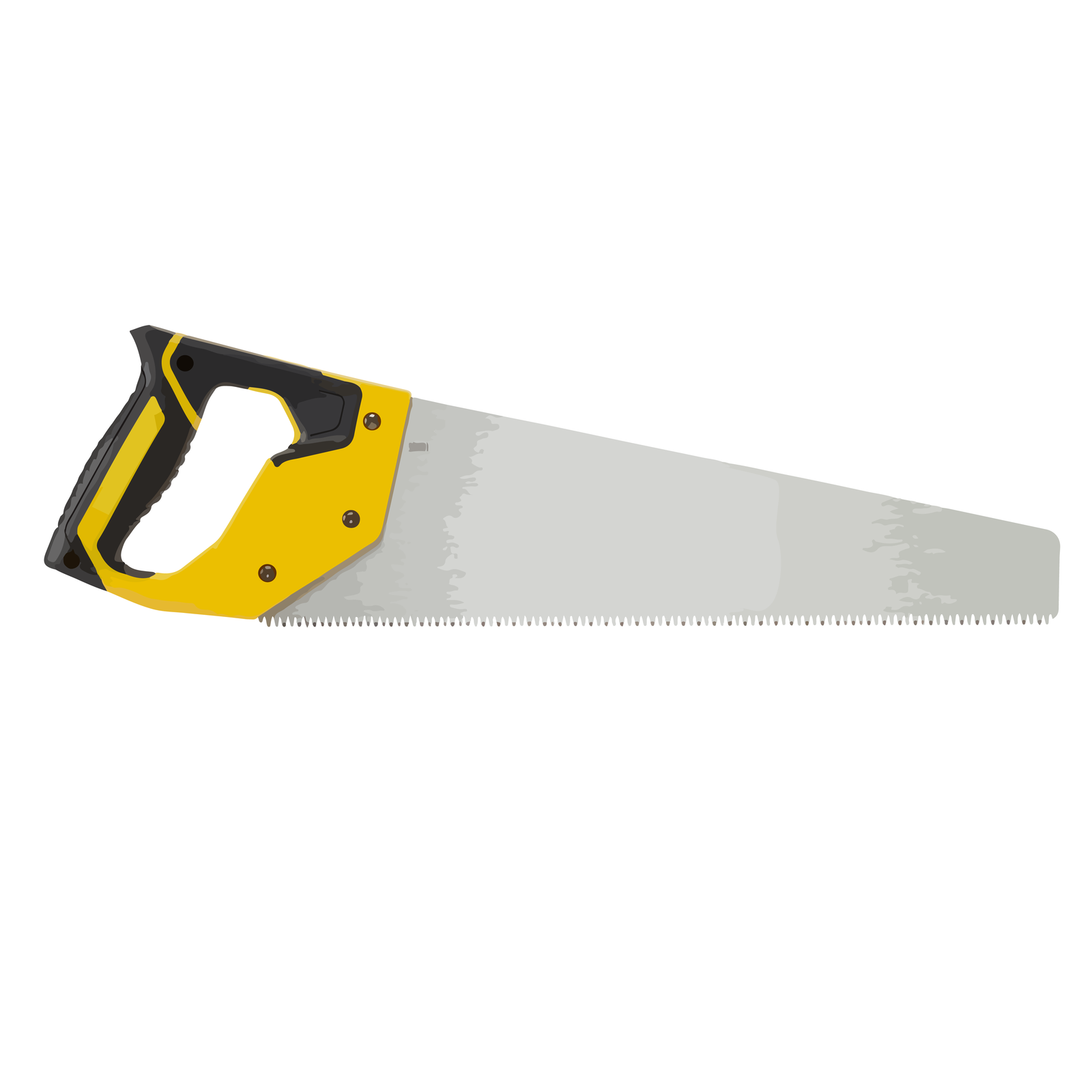
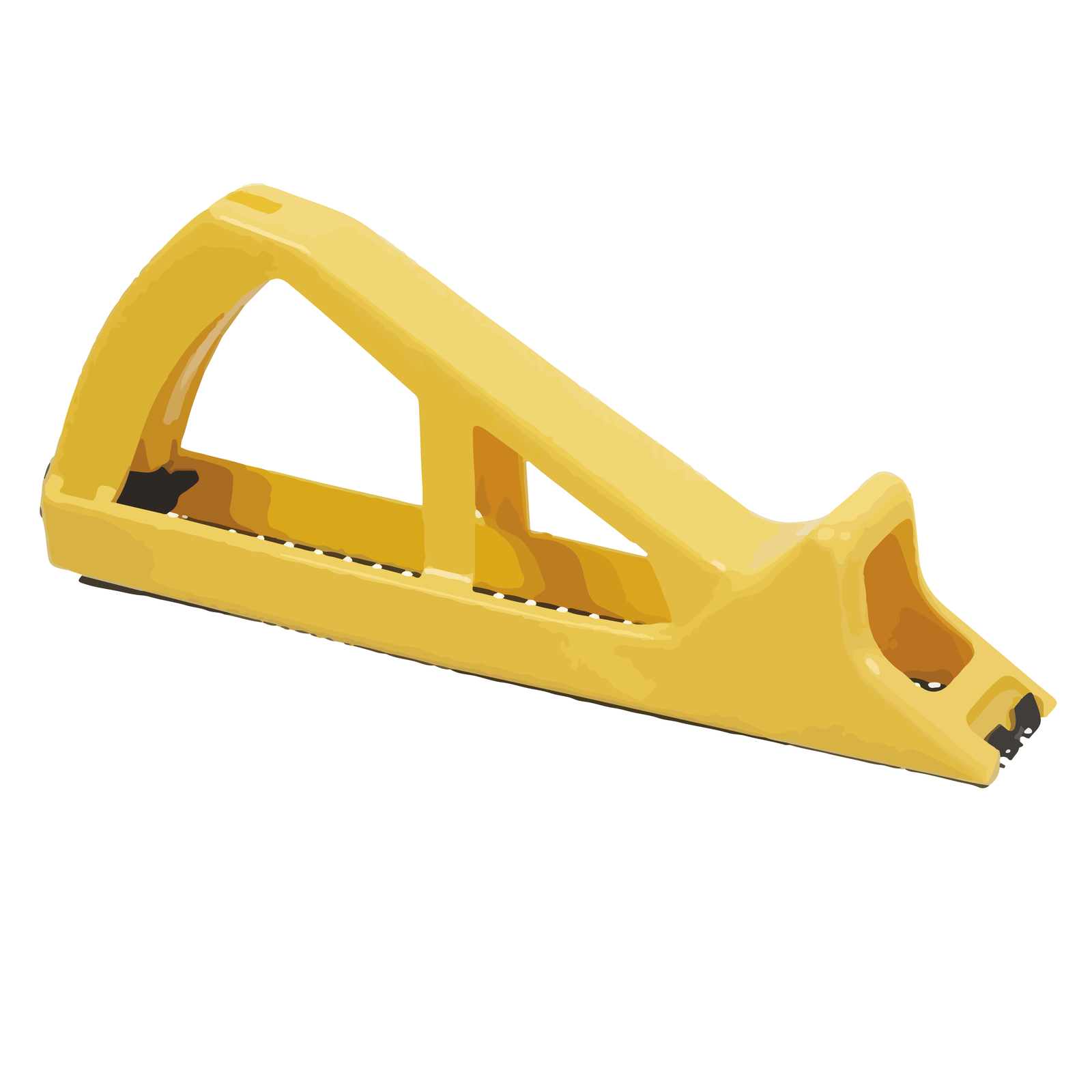
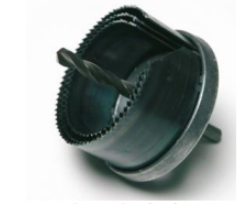
b) Narzędzia do mieszania mas szpachlowych i kleju gipsowego:
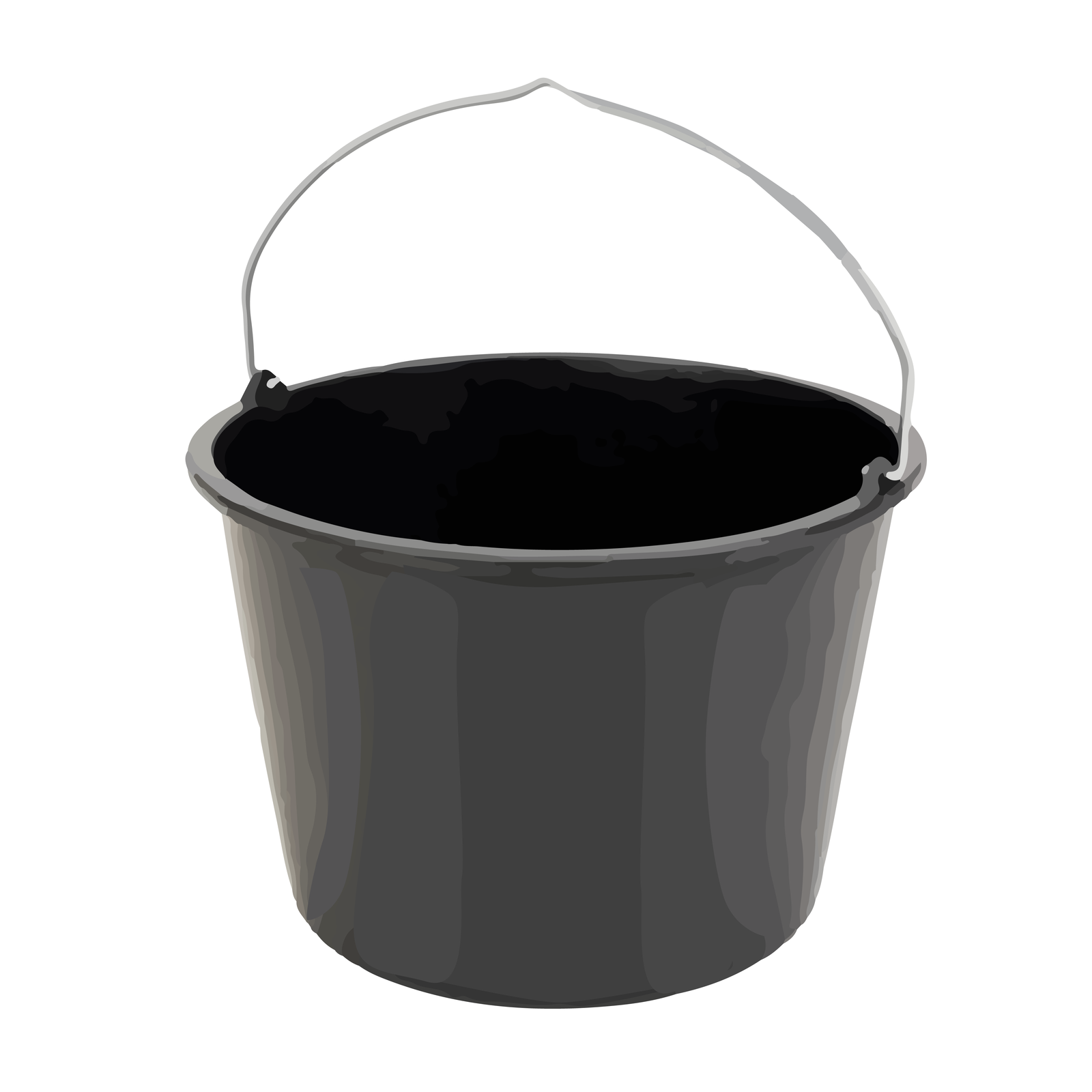
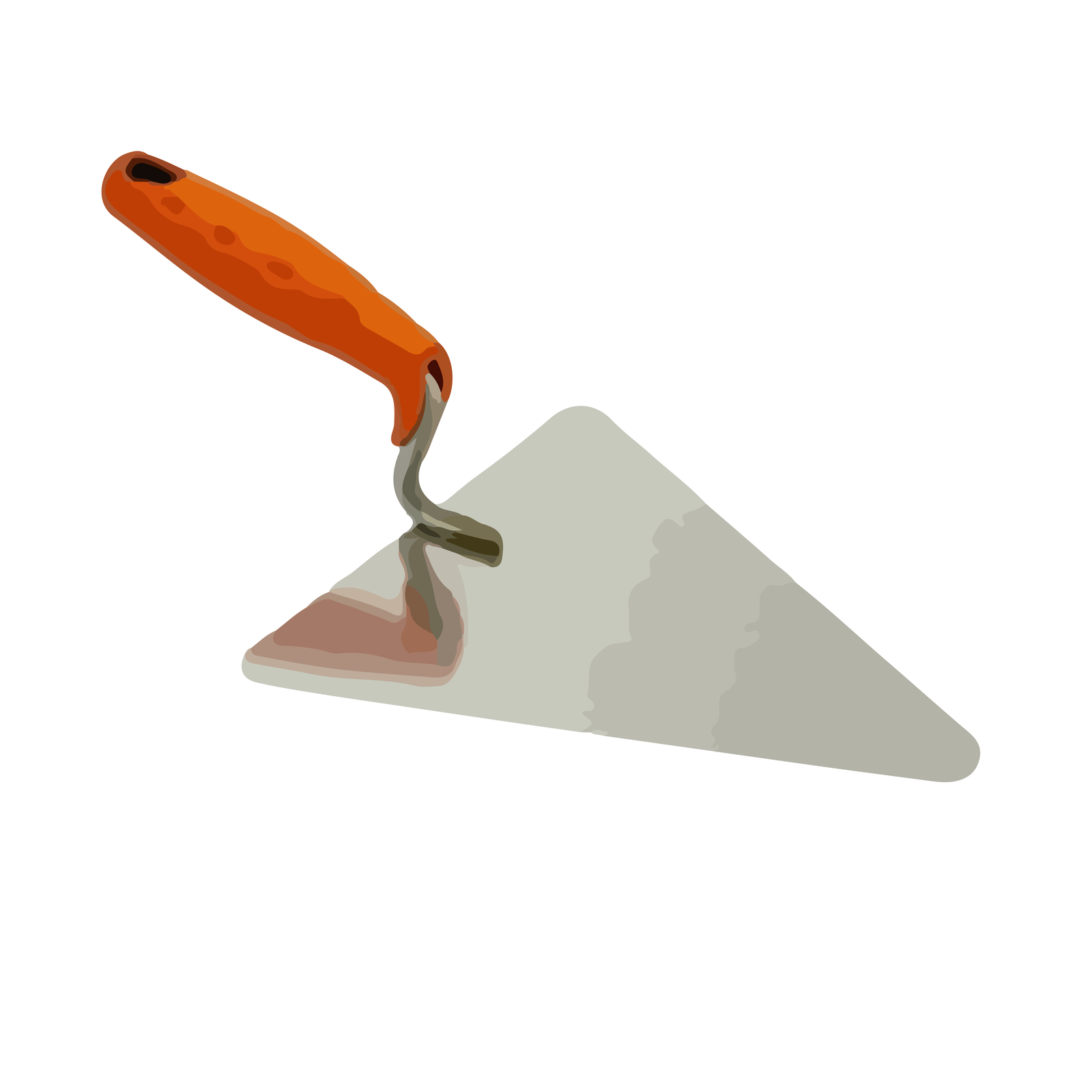

c) Sprzęt kontrolno‑pomiarowy:
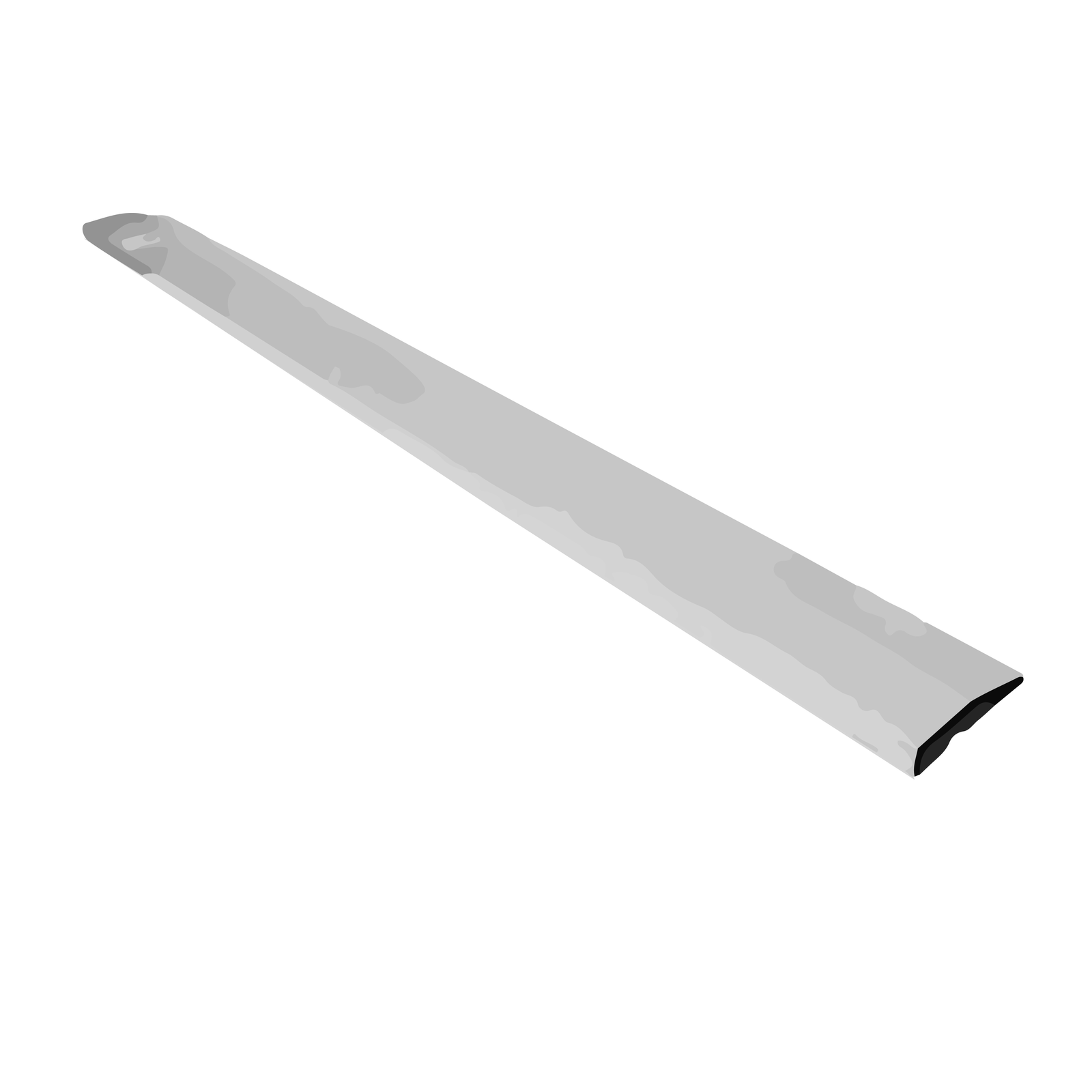
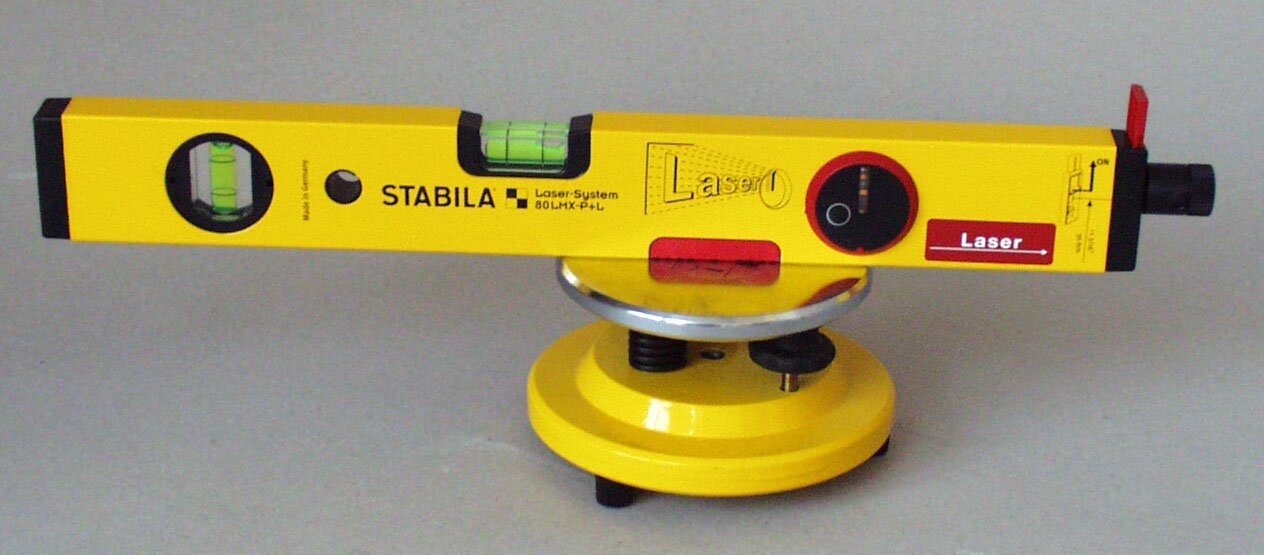
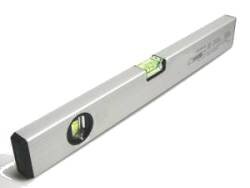
d) Narzędzia do mocowania płyt:
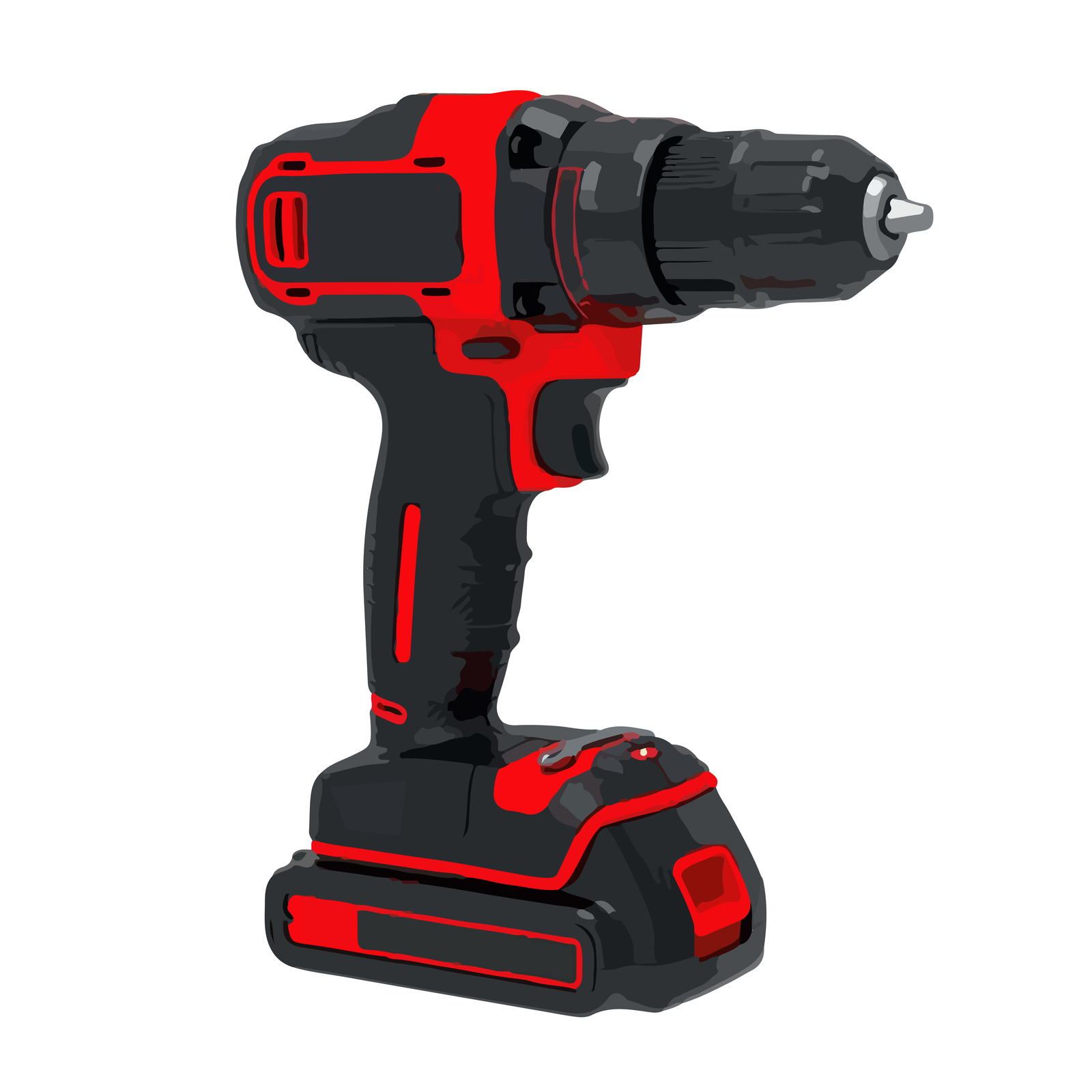
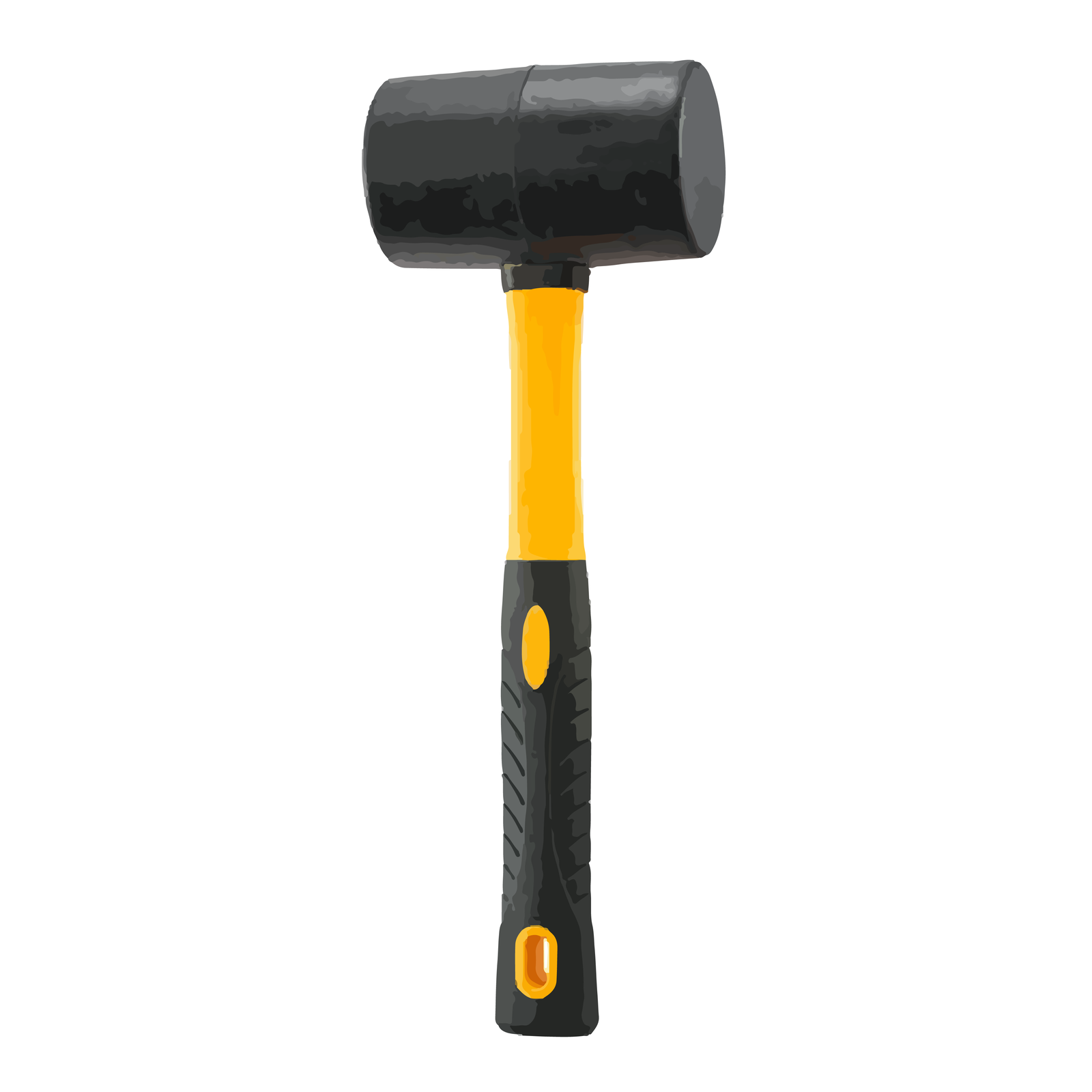
e) Narzędzia do spoinowania połączeń oraz wykańczania powierzchni płyt gipsowo‑kartonowych:
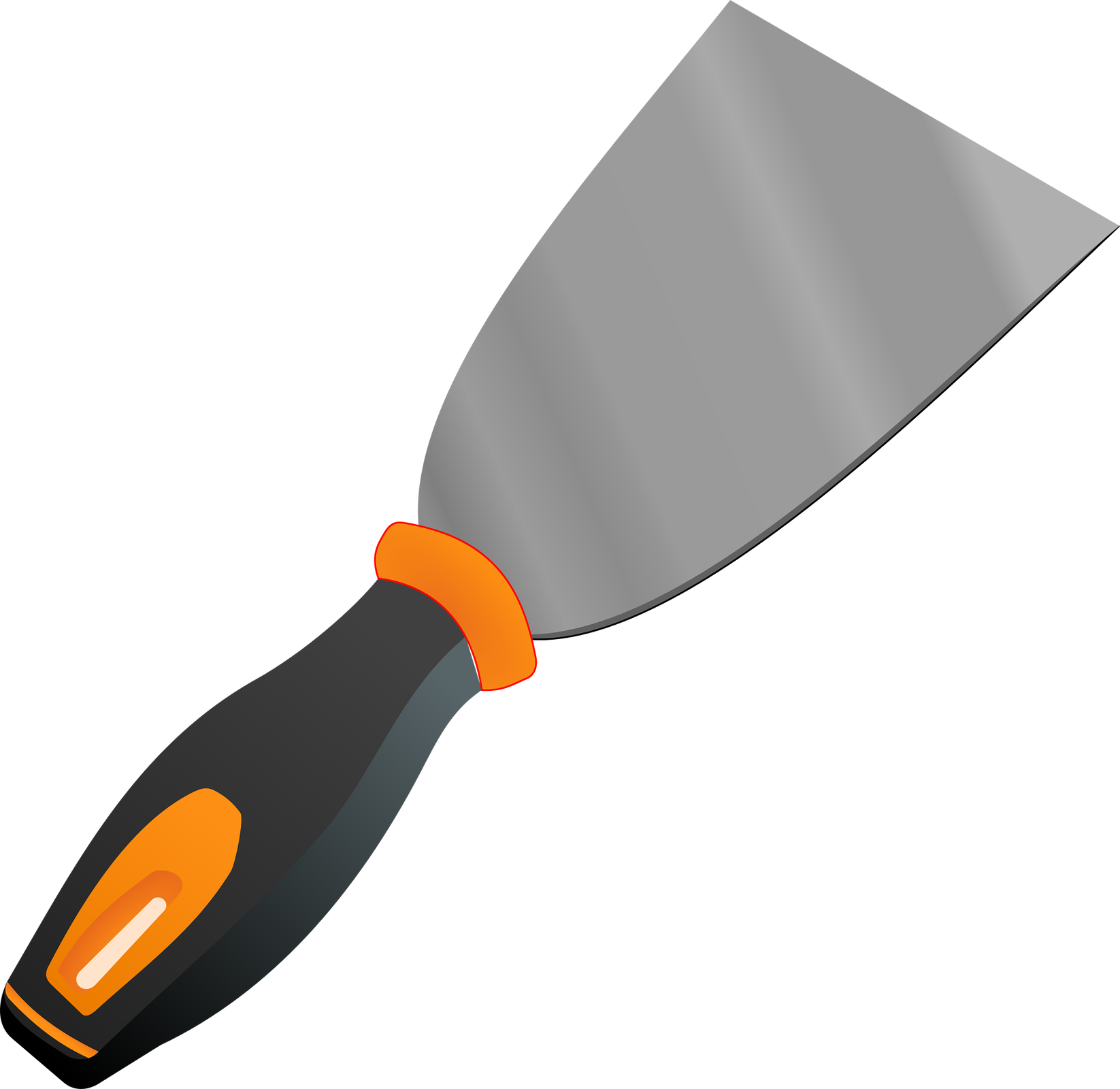
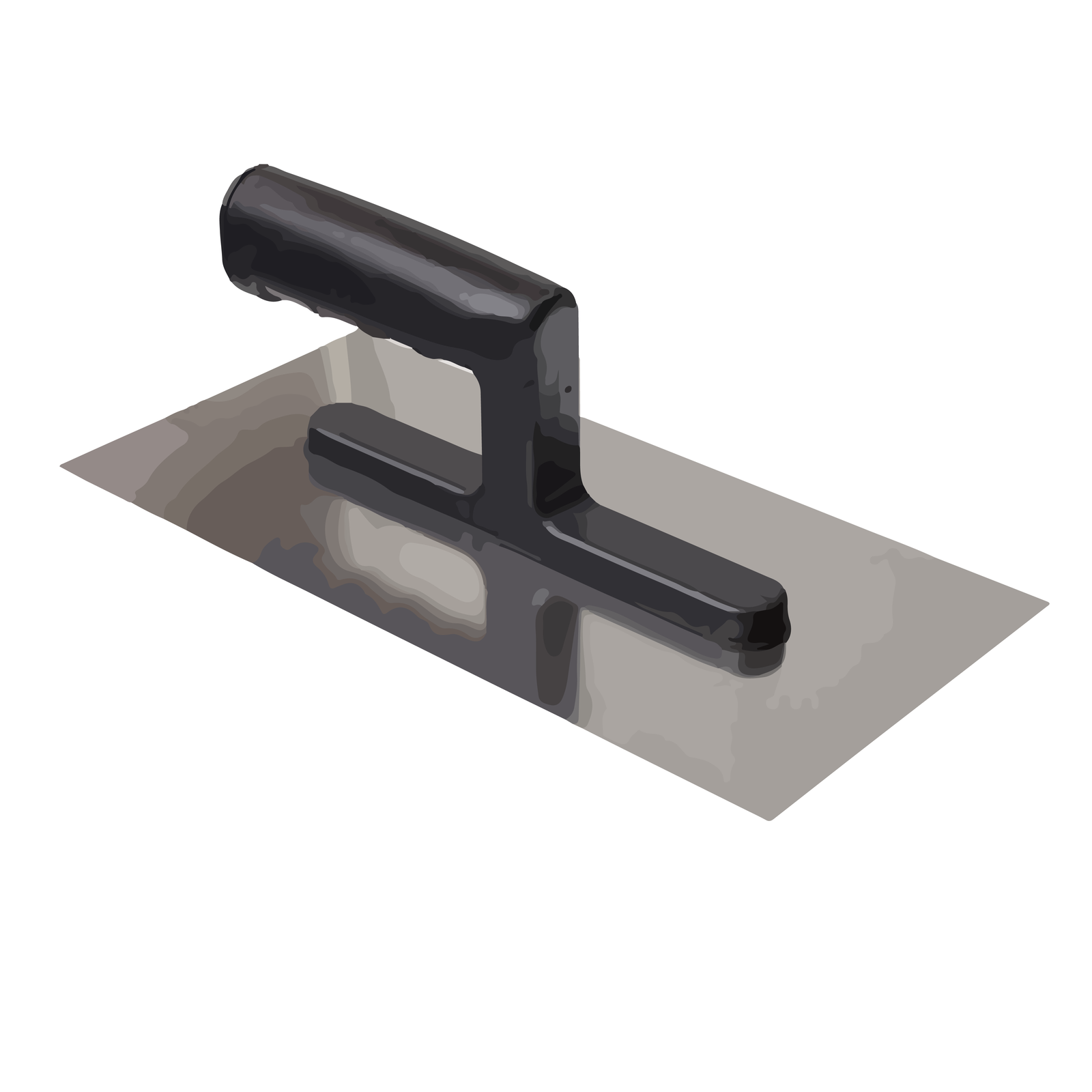
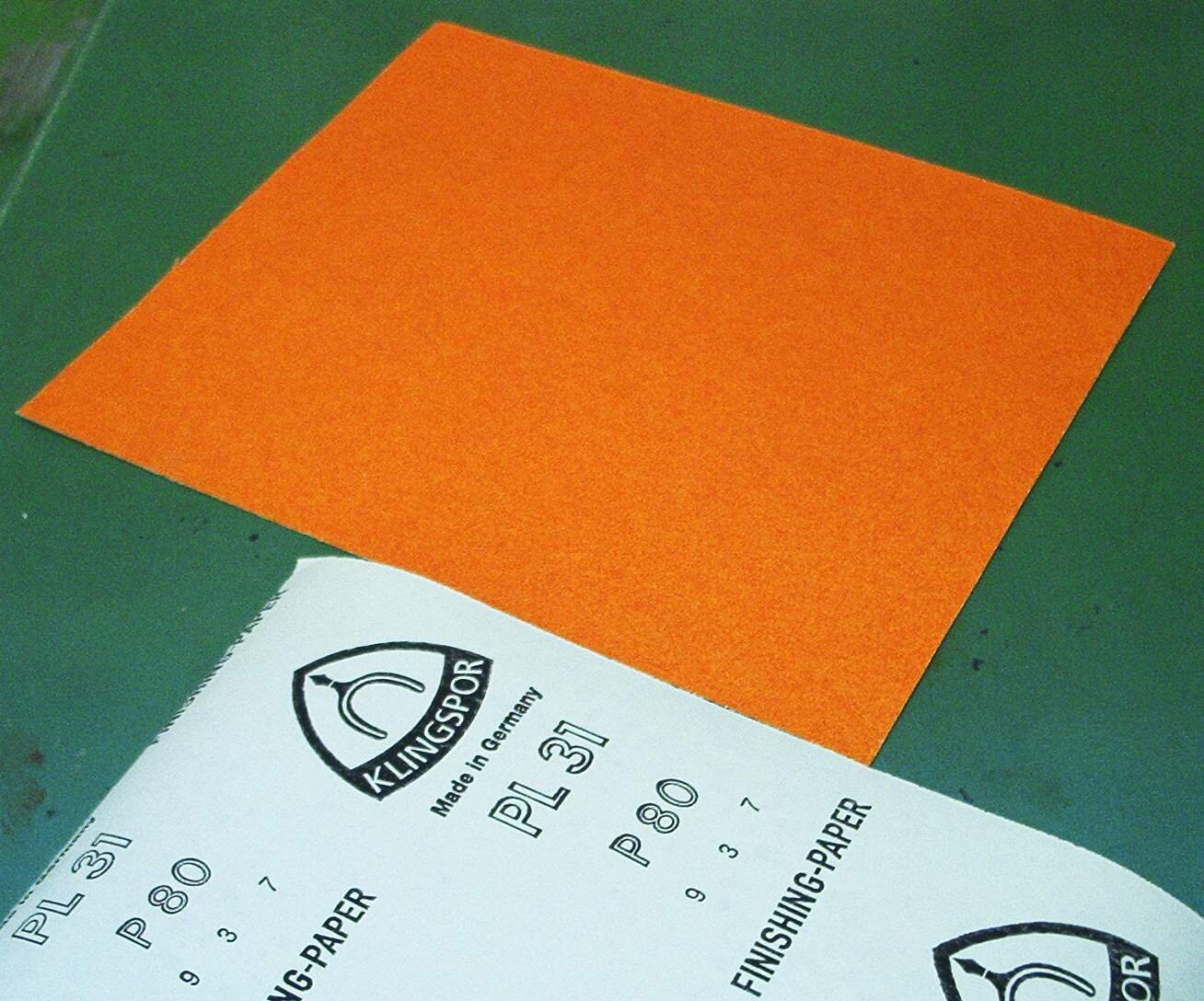
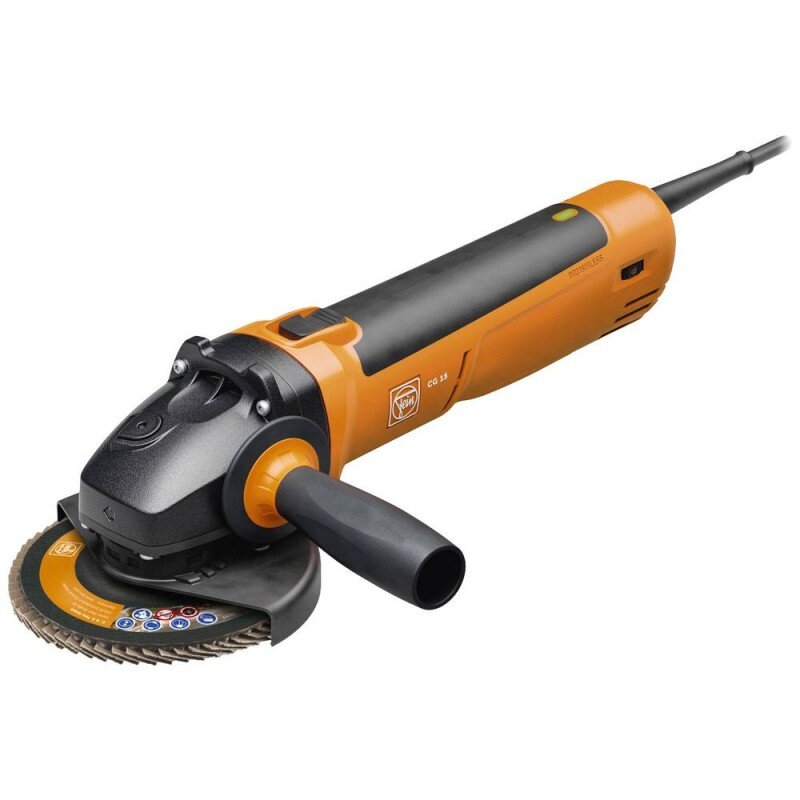
f) Narzędzia do formowania profili:
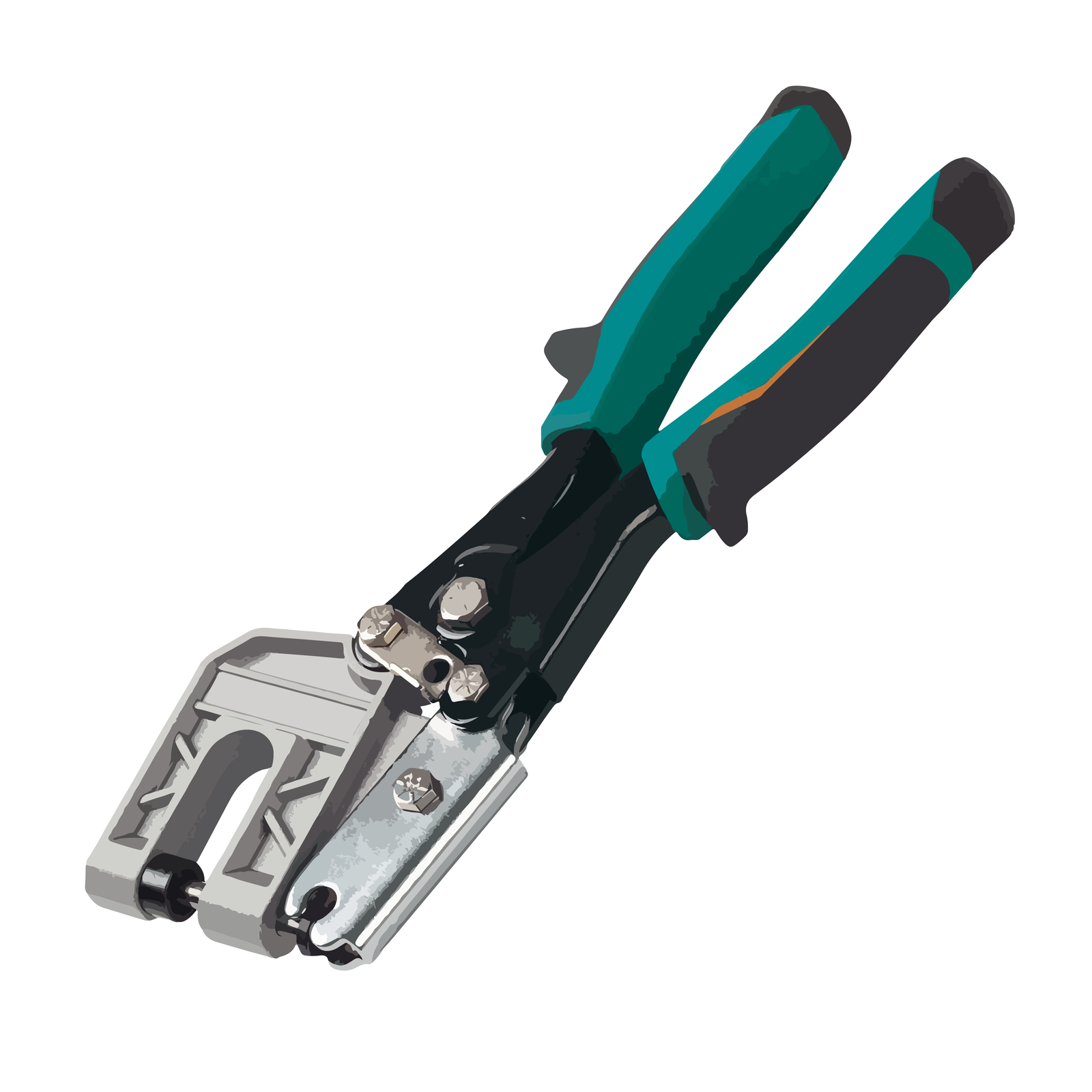

g) Narzędzia dodatkowe:
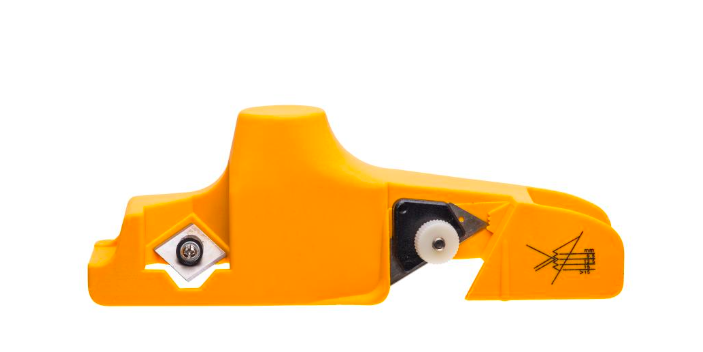
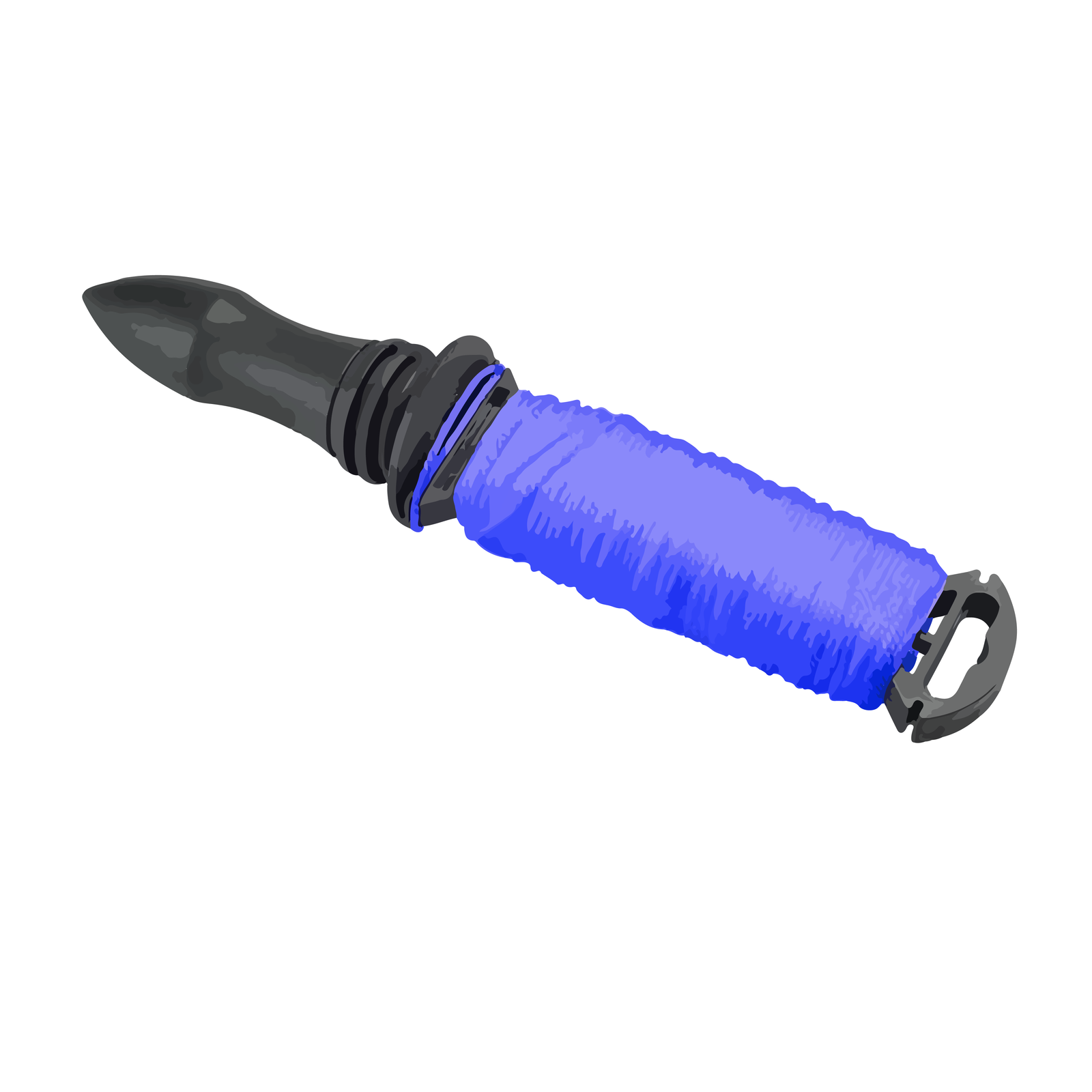
Powrót do spisu treściPowrót do spisu treści
4. Ogólne wymogi prowadzenia robót
Rozpoczęcie robót z wykorzystaniem płyt gipsowo‑kartonowych jest możliwe dopiero wówczas, gdy została zamontowana stolarka okienna oraz zakończono wszystkie prace „mokre” (wraz z wylewkami). Prace powinny być prowadzone w temperaturze nie niższej niż 10°C, co oznacza, że w okresie zimowym budynek, w którym wykonywane są roboty montażowe, powinien być ogrzewany. Ponadto istotna jest konieczność utrzymania stałej wilgotności względnej powietrza nieprzekraczającej 70%.
System do zabudowy powinien obejmować wszystkie elementy: płyty gipsowo‑kartonowe, profile, wieszaki, uchwyty, wkręty, masy gipsowe i taśmy zbrojące.
Powrót do spisu treściPowrót do spisu treści
5. Obudowa dachu w systemach suchej zabudowy
Systemy suchej zabudowy umożliwiają obudowę konstrukcji dachu i zaaranżowanie pomieszczeń na poddaszu na potrzeby mieszkalne. Jak już wcześniej wspomniano, na ten system składają się:
konstrukcja z profili aluminiowych,
zestaw płyt gipsowo‑kartonowych,
systemowych taśm uszczelniających,
systemowych mas szpachlowych,
elementów mocujących i akcesoriów,
a także warstwa termoizolacyjna, np. z wełny mineralnej.
Producenci systemów suchej zabudowy oferują kompletne rozwiązania. Aby prawidłowo wykonać obudowę w tej technologii, należy kierować się instrukcjami poprawnego wykonania. Dzięki nim zabudowa zapewni odpowiednią izolacyjność termiczną, akustyczną, bezpieczeństwo pożarowe i estetykę.
Powrót do spisu treściPowrót do spisu treści
6. Etapy wykonywania obudowy konstrukcji dachu w systemach suchej zabudowy
Powrót do spisu treściPowrót do spisu treści
6.1 Trasowanie
Pierwszą czynnością podczas wykonywania zabudowy poddasza jest wyznaczenie linii zabudowy. Można do tego wykorzystać poziomicę laserową. Przebieg okładziny wyznacza się na ścianach szczytowych i kolankowych.
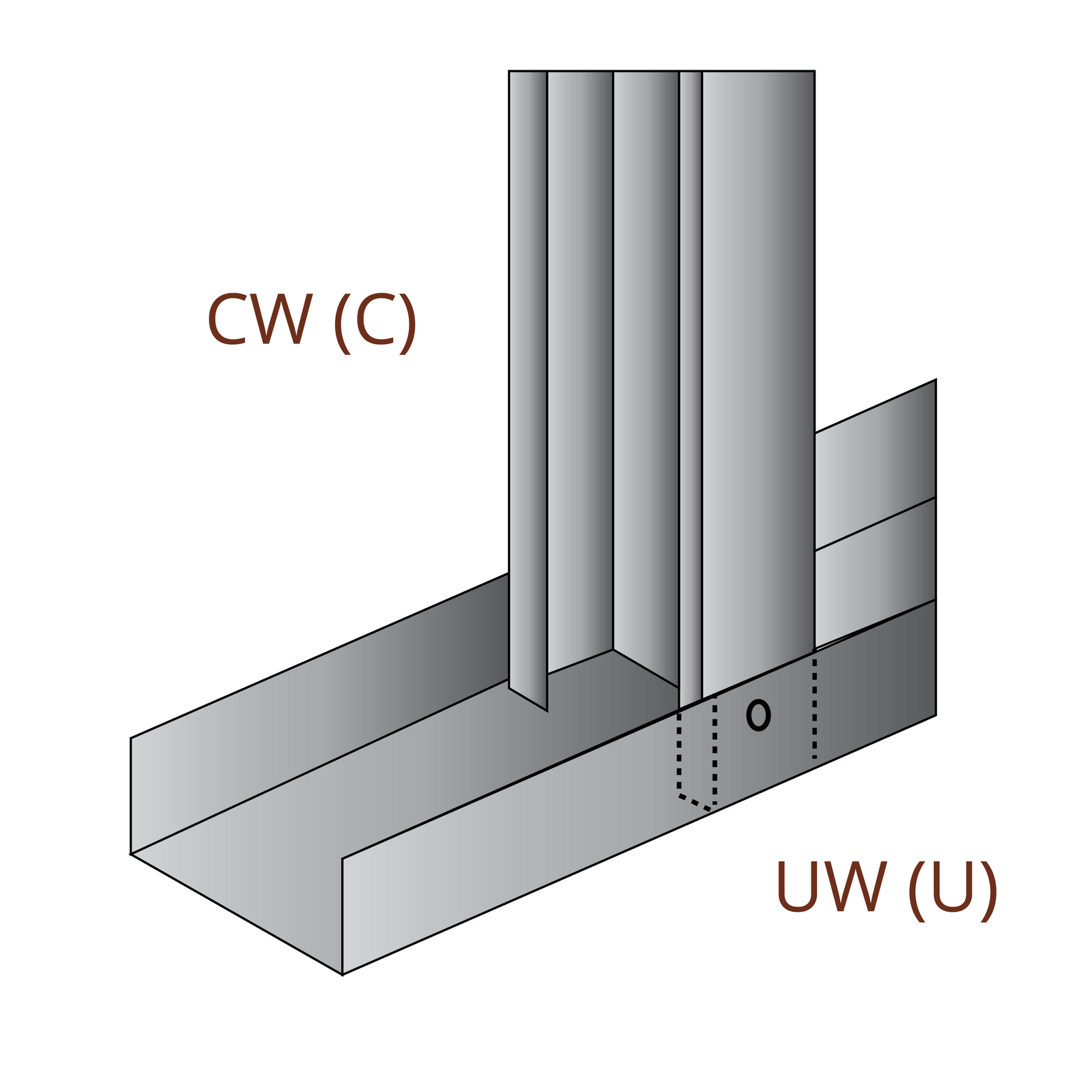
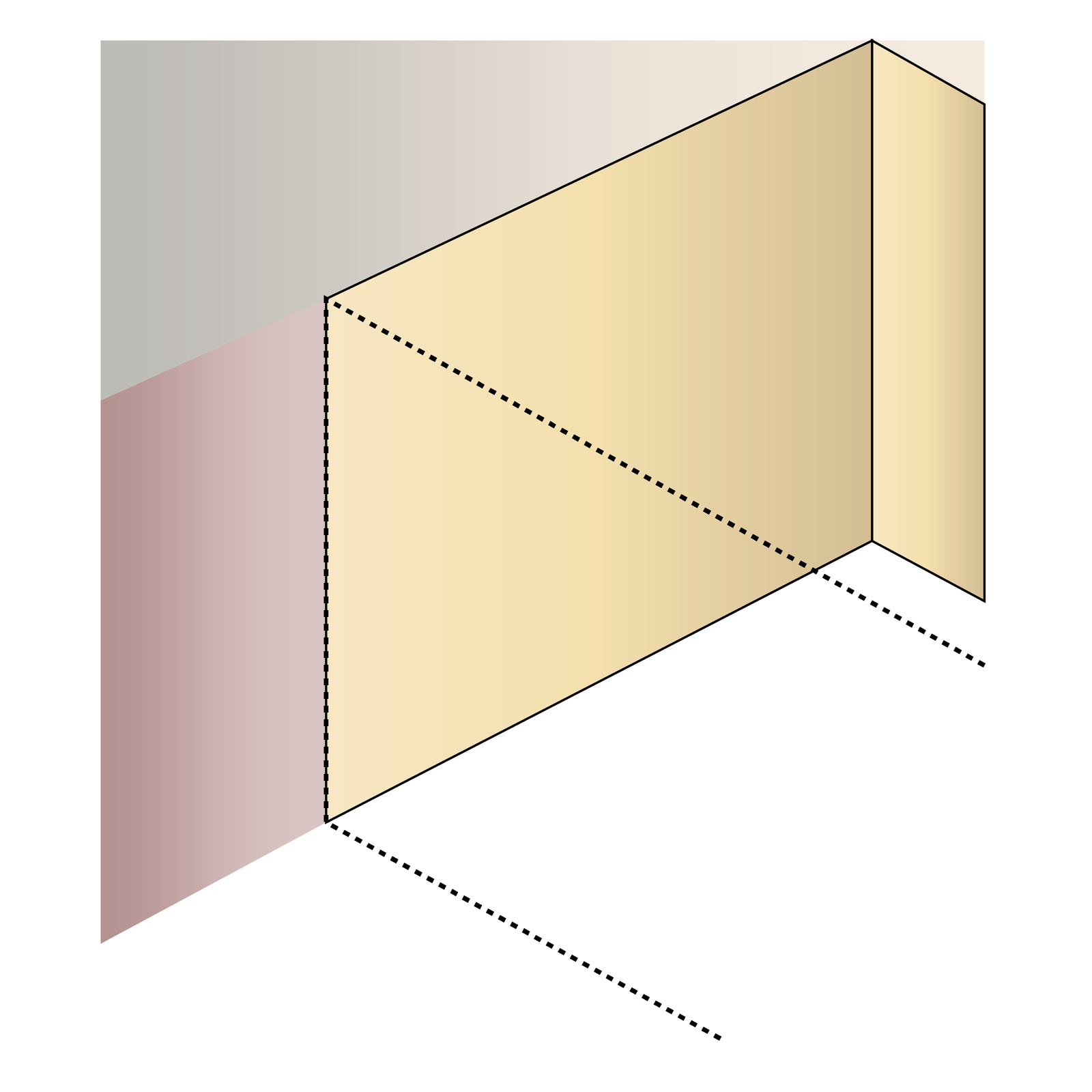
Aby prawidłowo wyznaczyć płaszczyznę skosu, należy zadbać o zachowanie równoległości krawędzi załamania między nim a sufitem i ścianką kolankową. Na ściance wyznaczana jest linia pozioma, będącą jednocześnie krawędzią skosu i ścianki. Na jednym końcu sufitu zaznaczane jest miejsce przyszłego przecięcia się sufitu i skosu; przenoszenie tego punktu na podłogę wykonywane jest za pomocą pionu, następnie mierzona jest jego odległość od ścianki kolankowej. Ta sama odległość odmierzana jest po drugiej stronie pomieszczenia. Pion pozwala znaleźć na suficie drugi punkt określający linie krawędzi; odznacza się go sznurem z proszkiem znacznikowym.
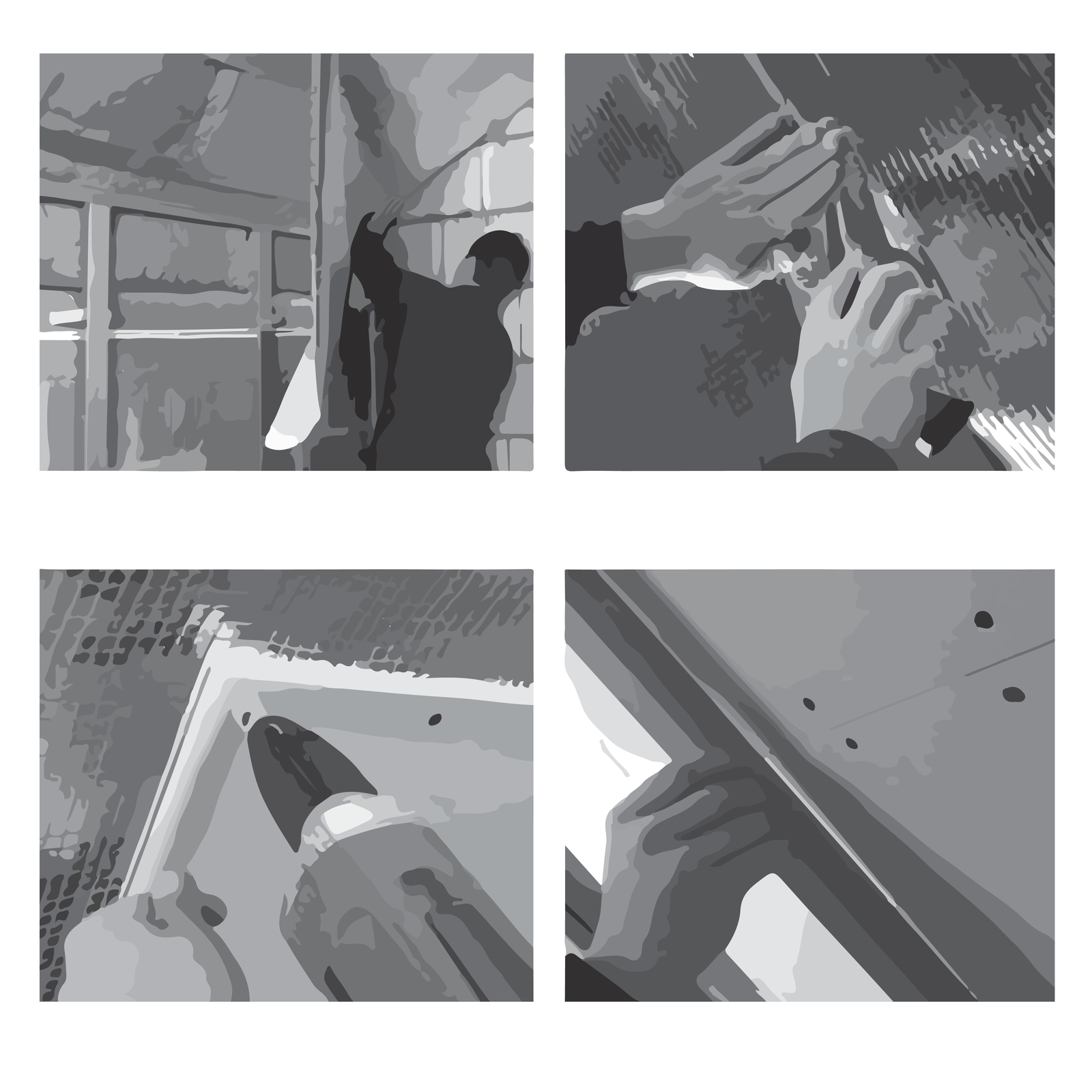
Powrót do spisu treściPowrót do spisu treści
6.2 Montowanie profili stalowych
Kolejnym etapem, kluczowym w systemach suchej zabudowy dachu, jest montowanie profili stalowych. Profilowanie zapewnia solidną podstawę dla kolejnych warstw konstrukcyjnych, umożliwiając precyzyjne i stabilne osadzenie pozostałych elementów.
Po pierwsze należy określić rozstaw i orientację profili stalowych zgodnie z projektowaniem konstrukcji dachu. Następnie należy bezpośrednio przytwierdzić profile do krokwi za pomocą odpowiednich elementów mocujących.
Profile nośne CD montuje się do uchwytów systemowych ES za pomocą blachowkrętów.
Na ścianach szczytowych stosuje się profile przyścienne UD. Profile nośne montuje się w rozstawie 40 cm prostopadle do belek konstrukcji dachowej.
Powrót do spisu treściPowrót do spisu treści
6.3 Mocowanie izolacji (wełny mineralnej i folii paroizolacyjnej)
Wełna mineralna to najczęściej stosowany materiał izolacyjny na poddaszach. Jest sprężysta, więc da się ją dobrze ułożyć między krokwiami, dzięki czemu można uniknąć powstawania mostków termicznych. Poza izolacją cieplną, wełna bardzo dobrze sprawdza się jako izolator akustyczny.
Wełnę mineralną docina się z zapasem (około 2 cm więcej niż rzeczywista odległość między belkami), aby uniknąć mostków termicznych. Do cięcia wełny powinno się używać specjalnego noża, dzięki któremu jej krawędzie nie zostaną poszarpane. W przypadku problemów z zamocowaniem wełny, można wykonać ze sznurka ruszt, w celu jej przytrzymania.
Wadą wełny mineralnej jest mała odporność na wilgoć. Dlatego warto ją zabezpieczyć folią paroizolacyjną.
Zastosowanie folii paroizolacyjnej odgrywa istotną rolę w utrzymaniu prawidłowego bilansu wilgotności w konstrukcji dachu. Zapobiega to skraplaniu pary wodnej wewnątrz konstrukcji, co może prowadzić do poważnych problemów z wilgocią.
Folię tę mocuje się po zamontowaniu wypoziomowanej konstrukcji stalowej. W pierwszej kolejności rozwija się ją i rozmieszcza na powierzchni konstrukcji dachu. Następnie przytwierdza się ją do profili stalowych za pomocą dwustronnej taśmy klejącej, na łączeniach przykleja się ją na zakładkę, tak aby warstwy folii zachodziły na siebie.
Powrót do spisu treściPowrót do spisu treści
6.4 Montaż płyt gipsowo‑kartonowych
Płyty gipsowo‑kartonowe są głównym materiałem wykończeniowym w systemach suchej zabudowy dachu. Montaż wymaga precyzji, aby uzyskać gładką i trwałą powierzchnię.
Płyty gipsowo‑kartonowe można dociąć, zarysowując je przy użyciu noża z wymiennym ostrzem (od strony lica), a następnie przełamując i przecinając karton z drugiej strony. Cięcie powinno się odbywać na płaskiej i stabilnej powierzchni.
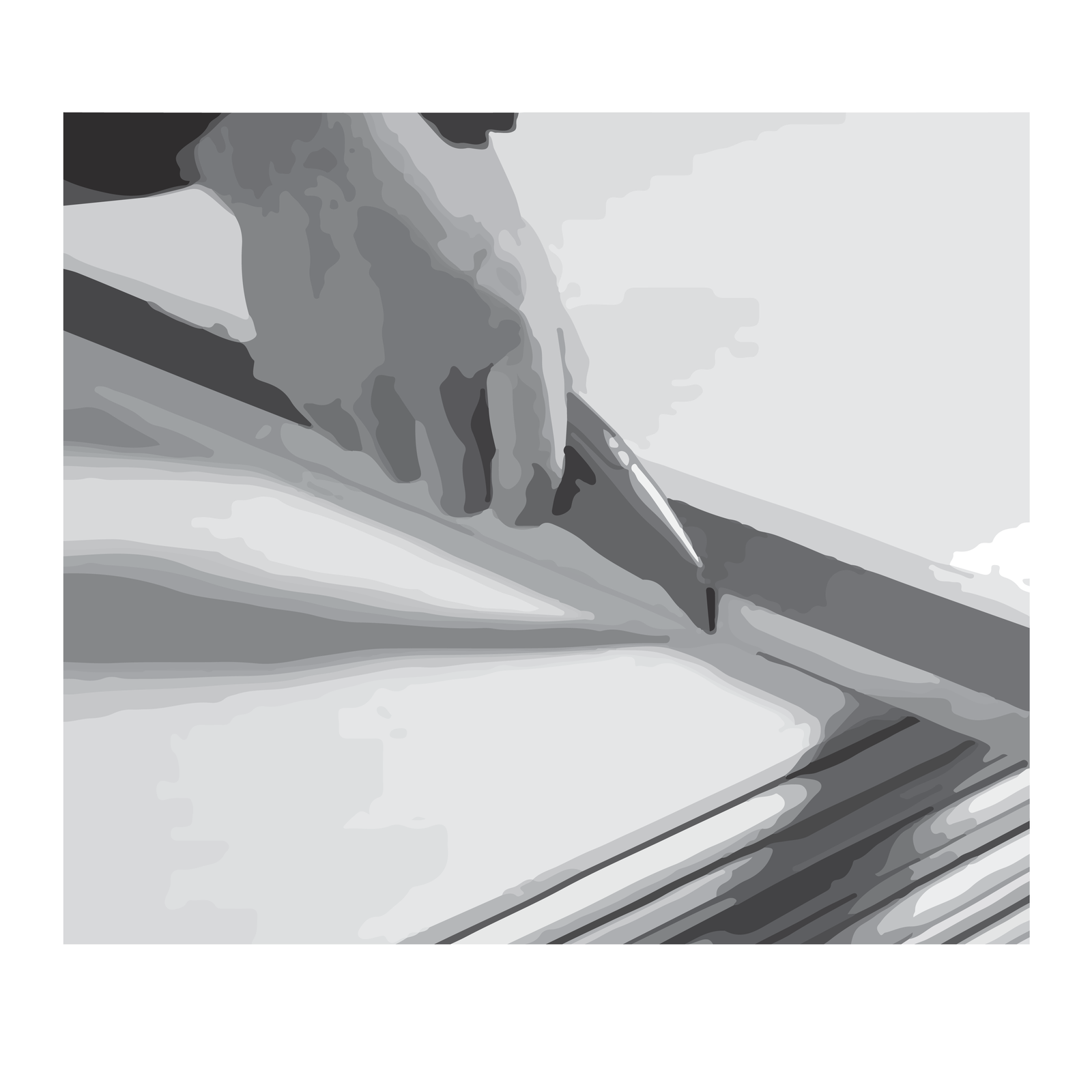
Jeśli zachodzi potrzeba wycięcia otworów (np. na gniazda sieciowe) należy użyć otwornicy lub wyrzynarki.
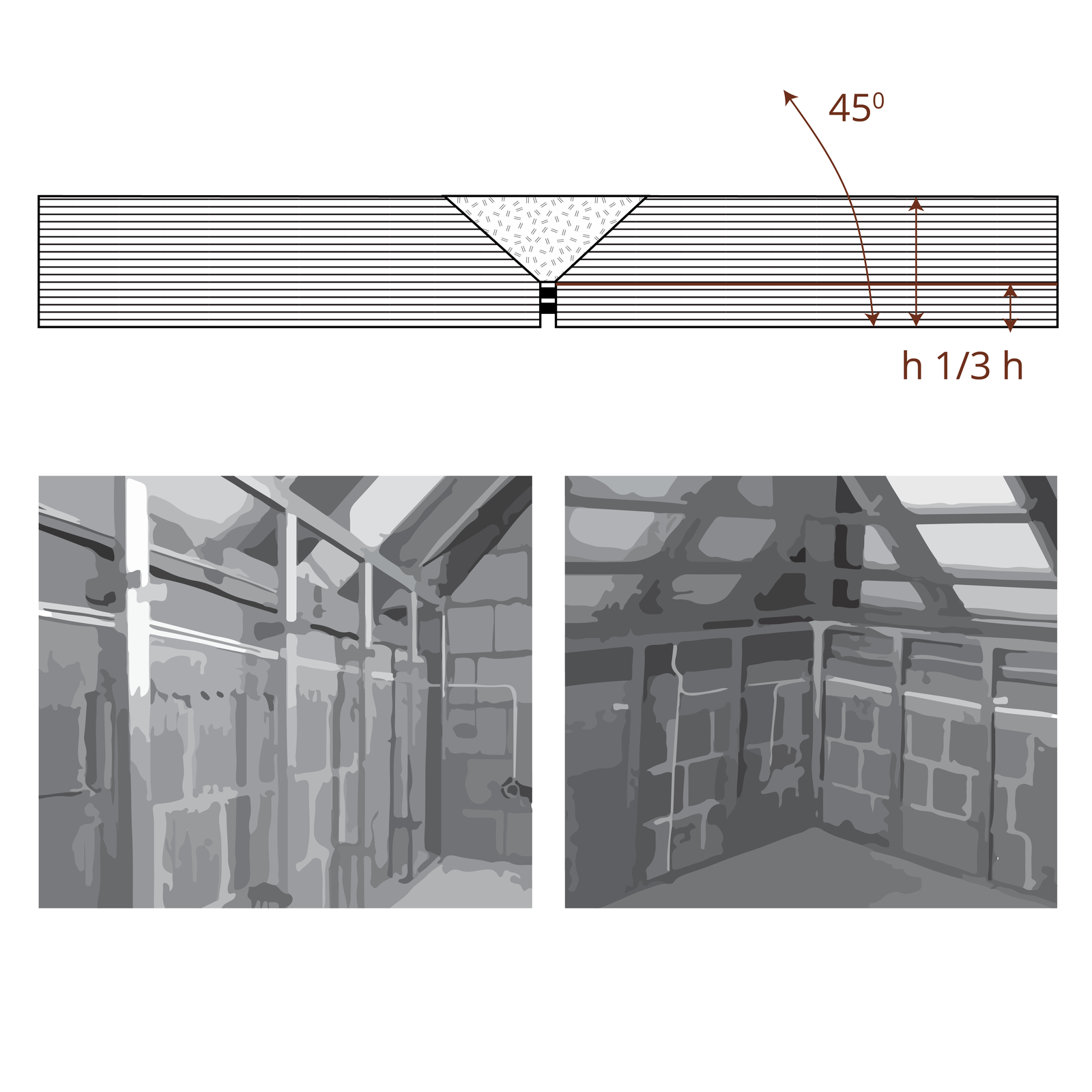
W dalszej kolejności cięte krawędzie należy sfazować (dociąć ich krawędzie pod skosem), używając struga do krawędzi. Sfazowanie krawędzi płyty pod kątem 45 stopni (do około dwóch trzecich grubości płyty) pozwala stworzenie bruzdy, w której następnie można umieścić gips szpachlowy. Płyty gipsowo‑kartonowe układa się prostopadle do profili montażowych i przykręca do nich za pomocą systemowych wkrętów do gipsu. Rozstaw wkrętów w poszyciach jednowarstwowych oraz w zewnętrznych warstwach poszyć wielowarstwowych powinien wynosić maksymalnie 17 cm. Z kolei maksymalny rozstaw wkrętów w wewnętrznych warstwach poszyć wielowarstwowych nie powinien przekraczać 40 cm.
Płyty należy odpowiednio rozmieścić, uwzględniając konstrukcję dachu oraz planowane otwory (np. okna dachowe). Następnie przytwierdza się je, stosując jedno z kilku dostępnych rozwiązań.
Montaż płyt na konstrukcji z łat drewnianych. Rozwiązanie to nie jest często wybierane, gdyż wysokość krokwi jest często mniejsza niż grubość materiału izolacyjnego, co powoduje, że całość konstrukcji musi być opuszczona na uchwytach. W przypadku wyboru tego rozwiązania, można zastosować jedną lub dwie warstwy poszycia. Przy poszyciu pojedynczym (12,5 mm) właściwy rozstaw łat to 40 cm (ułożenie poziome, równoległe do rusztu). W przypadku poszycia podwójnego (2 x 12,5 mm) prawidłowy rozstaw łat to 60 cm (przy ułożeniu poziomym, równoległym do rusztu) i 75 cm (przy ułożeniu pionowym prostopadłym do rusztu). Przekrój łat drewnianych jest uzależniony od grubości poszycia, a także od rozstawu krokwi dachowych, do których przymocowuje się ruszt:
50 x 30 mm w przypadku poszycia pojedynczego i rozstawie krokwi co 85 cm,
60 x 50 mm w przypadku poszycia pojedynczego i rozstawie krokwi co 120 cm,
60 x 40 mm w przypadku poszycia podwójnego i rozstawu krokwi co 85 cm,
60 x 50 mm w przypadku poszycia podwójnego i rozstawu krokwi co 100 cm.
Montaż płyt na profilach kapeluszowych. Profile te są montowane bezpośrednio do drewnianych belek przy użyciu wkrętów. Ich grubość wynosi 15 mm. Rozstaw między profilami w przypadku wyboru omawianego rozwiązania wynosi od 5 do 6 cm. Profile te są zwykle stosowane w przypadku niewielkiego odchylenia krokwi od linii prostej. Rozwiązanie to jest właściwe w przypadku małych pomieszczeń.
Montaż na profilach CD i wieszakach bezpośrednich lub typu klick. W przypadku wyboru tego rozwiązania profile CD montuje się na wieszakach bezpośrednich lub wieszakach typu klick zamocowanych do elementów więźby. Jeśli płyty są ułożone wzdłuż względem profili to maksymalny rozstaw profili wynosi 4 cm. W przypadku zaś ułożenia poprzecznego maksymalny rozstaw to 5 cm.
Montaż na profilach CD i wieszakach kotwowych do poddaszy. Wieszak kotwowy (zwany inaczej wieszakiem grzybkowym) to profilowany płaskownik o długości 15 cm. Przykręca się go przy użyciu wkrętów do boku belki. Można umieścić go na różnych jej wysokościach, co daje możliwość skorygowania ewentualnych nierówności poddasza. Zarówno przy poprzecznym jak i podłużnym ułożeniu płyt maksymalny rozstaw dla tych profili wynosi 40 cm. Zastosowanie długich wieszaków daje możliwość umieszczenia w zabudowie dodatkowej izolacji (nawet 10 cm).
Montaż na profilach CD i wieszakach ES. Wieszak ES jest perforowanym płaskownikiem wygiętym w kształt litery U. Montuje się go od spodu belki lub krokwi za pomocą wkrętów. Profil do wieszaka przytwierdza się przy użyciu wkrętów do metalu. Te części wieszaka, które wystają ponad profil należy odgiąć na boki, tak aby nie stanowiły przeszkody przy montowaniu płyt gipsowo kartonowych. Przy tym rozwiązaniu, niezależnie od ułożenia płyt względem profili (poprzecznego lub podłużnego), maksymalny rozstaw profili wynosi 40 cm. Jest to rozwiązanie właściwe, gdy grubość izolacji między krokwiami jest większa od wysokości belek.
Płyty gipsowo‑kartonowe są montowane z przesunięciem styków w taki sposób, aby spoiny kolejnych płyt były przesunięte względem siebie co najmniej o 40 cm. Nie tworzy się spoin krzyżowych.
Powrót do spisu treściPowrót do spisu treści
6.5 Obróbka okien dachowych
Obróbka okien dachowych jest etapem, który wpływa na szczelność i funkcjonalność konstrukcji. Prawidłowe osadzenie okien zapewnia optymalne warunki oświetleniowe i wentylacyjne.
W pierwszej kolejności należy wyznaczyć tzw. glify, a więc płaszczyzny boczne, które łączą okno z powierzchnią zabudowy. Glify mogą być prostopadłe do płaszczyzny okna bądź rozchodzić się pod kątem do wewnątrz pomieszczenia.
Od strony wewnętrznej poziome powierzchnie wnęki okiennej z płyt gipsowo‑kartonowych wykonuje się tak, by wnętrze było jak najlepiej doświetlone. Oznacza to, poziomą lub rozwartą górną obróbkę okna połaciowego oraz pionową obróbkę dolną. Obróbki boczne najczęściej są prostopadłe do okna.
Jeden ze sposobów obróbki okna połaciowego polega na wykorzystaniu stalowych profili UD i CD, z których wykonuje się stelaż służący do zabudowy okna. Do profili przykręca się następnie płyty gipsowo‑kartonowe. Górną krawędź profili należy ustawić w sposób równoległy do podłogi, natomiast dolną w sposób prostopadły. Boczne płaszczyzny powinny być poprowadzone prostopadle do okna.
Ułatwienie w obróbce okien połaciowych stanowi zastosowanie gotowej konstrukcji ze stalowych profili, którą można kupić razem z samym oknem. Taki stelaż systemowy złożony jest z kilku elementów połączonych za pomocą wkrętów. Można go dopasować do zdecydowanej większości okien połaciowych. Zastosowanie tego rozwiązania daje możliwość ułożenia grubej warstwy izolacji termicznej. Ponadto, warto podkreślić, że stelaże dostępne są w komplecie z folią paroizolacyjną we właściwym rozmiarze.
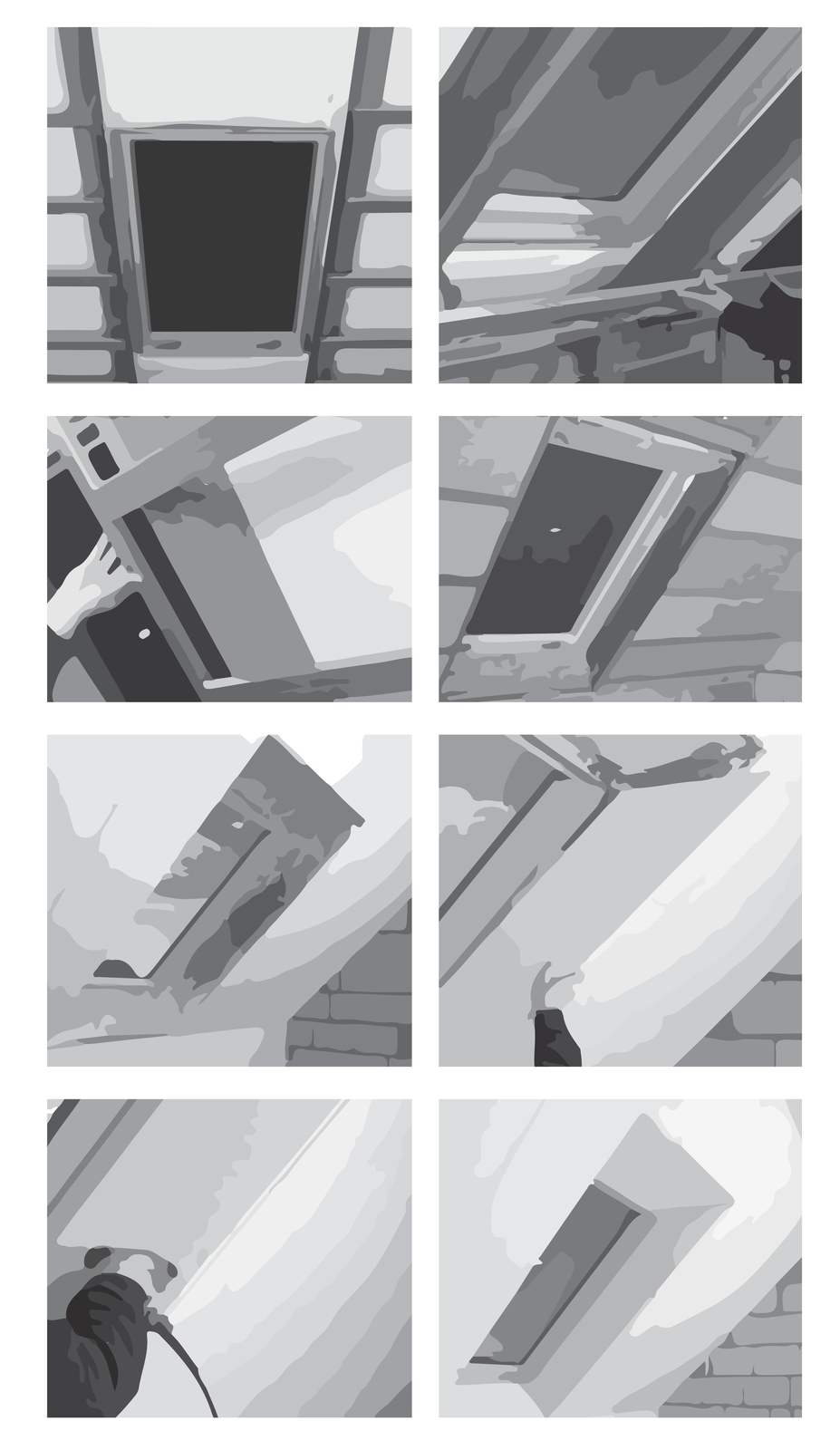
Powrót do spisu treściPowrót do spisu treści
6.6 Spoinowanie i wykańczanie powierzchni płyt
Spoinowanie płyt gipsowo‑kartonowych to proces eliminowania widocznych szwów i nierówności, w celu nadania powierzchni estetycznego i jednolitego wyglądu. Aby taki wygląd uzyskać należy zamaskować spoiny oraz łby wkrętów i uzupełnić ubytki oraz uszkodzenia krawędzi płyt. W tym celu używa się masy szpachlowej. Z kolei dla zabezpieczenia spoiny na stosuje się taśmy zbrojące.
Do spoinowania można użyć kilku rodzajów taśm zbrojących:
- papierową – wykonaną z włókna celulozowego o gładkiej powierzchni, taśma charakteryzuje się szorstką powierzchnią z jednej strony (do umieszczenia na płycie) i gładszą z drugiej; spoinowanie przy jej użyciu daje spoinie wyższą odporność mechaniczną niż inne techniki;
- samoprzylepną siateczkową z włókna szklanego, która pozwala najprościej i najszybciej wzmocnić łączenia; stworzona jest z siatki z włókien mineralnych z przylepną powierzchnią, którą można przykleić bezpośrednio do powierzchni płyt; dzięki temu w przypadku zastosowania tego rodzaju taśmy nie jest konieczne stosowanie podkładu (wymaganego przy użyciu taśmy papierowej); wytrzymałość tej taśmy jest jednak niższa niż łącza spoinowanego z wykorzystaniem taśmy papierowej,
- z włókna szklanego (fizeliny), którą stosuje się głównie na złączach płyt pokrytych włókniną z włókna szklanego; czasem jednak również na płytach o powierzchni tekturowej.
Do wyboru są również różne masy do spoinowania:
masa szpachlowa konstrukcyjna do stosowania z taśmą zbrojącą,
masa szpachlowa finiszowa,
dwufunkcyjna masa szpachlowa (konstrukcyjna i finiszowa),
masa konstrukcyjna do stosowania bez taśm zbrojących (do krawędzi KPOS).
Przed wykonaniem spoiny należy oczyścić powierzchnię z kurzu i pyłu.
Następnie masę szpachlową należy rozprowadzić poprzecznie do linii styku płyt. Masa powinna szczelnie wypełnić całą szczelinę. Kolejny krok to rozprowadzenie i wygładzenie masy szpachlowej na całej długości spoiny (najlepiej jednym ruchem). Kolejne warstwy szpachli umożliwiają osiągnięcie idealnie gładkiej powierzchni. Następnie precyzyjnie szlifuje się powierzchnię, aby uzyskać doskonały poziom wykończenia.
Poniżej opisano etapy prac, które należy wykonać podczas spoinowania różnych typów krawędzi:
Krawędzie typu NS i PRO. Na łączeniu wymienionych typów krawędzi należy przykleić samoprzylepną taśmę zbrojącą z włókna szklanego, a w następnej kolejności zaszpachlować łączenie jedną lub dwiema warstwami systemowej, konstrukcyjnej masy szpachlowej.
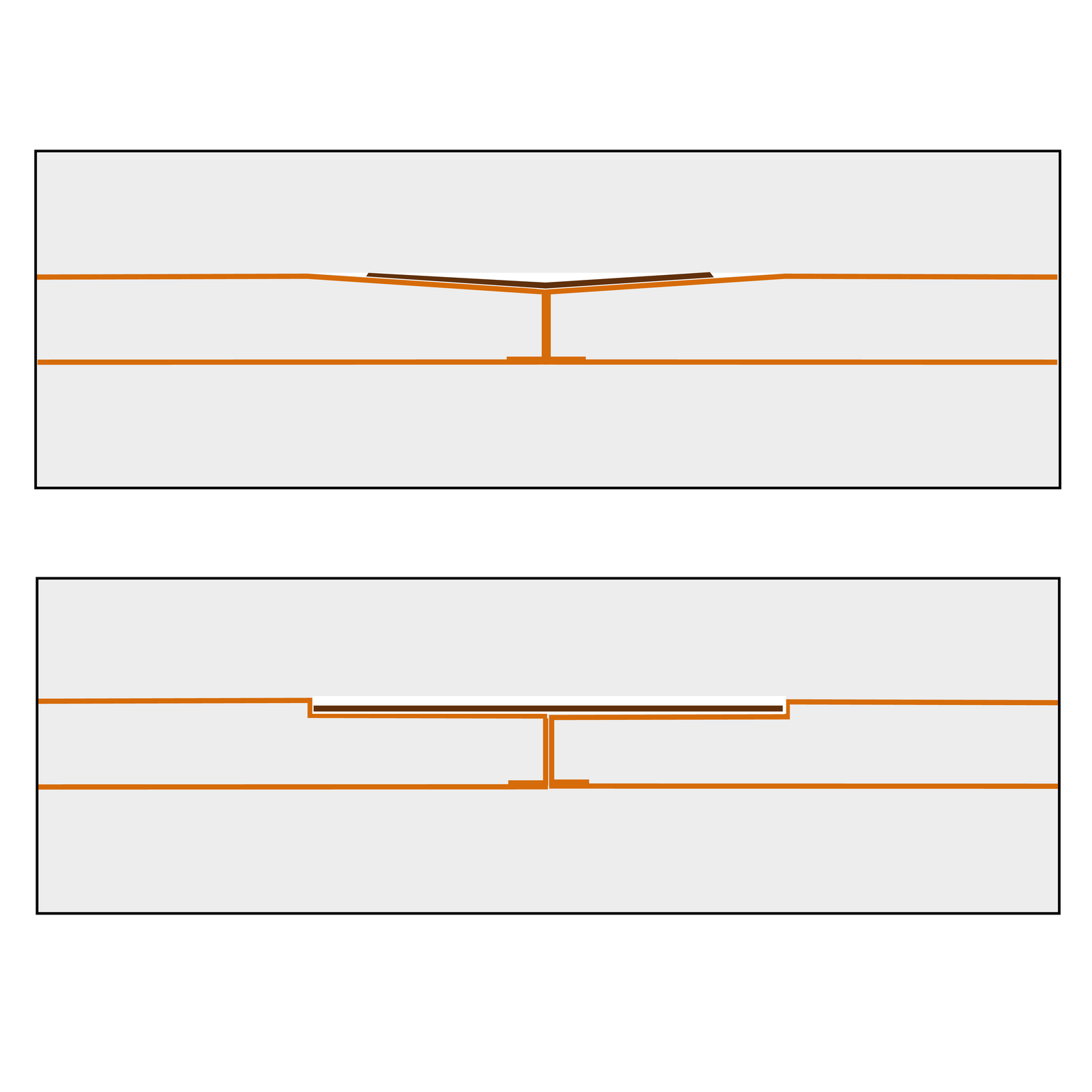
Przy zastosowaniu taśmy papierowej lub fizelinowej w pierwszym kroku należy nanieść warstwę systemowej konstrukcyjnej masy szpachlowej na łączeniu krawędzi płyt, w następnie wtopić w tę masę taśmę zbrojącą. Gdy warstwa masy z wklejoną taśmą wyschnie, należy zaszpachlować łączenie jedną lub dwiema warstwami konstrukcyjnej masy szpachlowej.
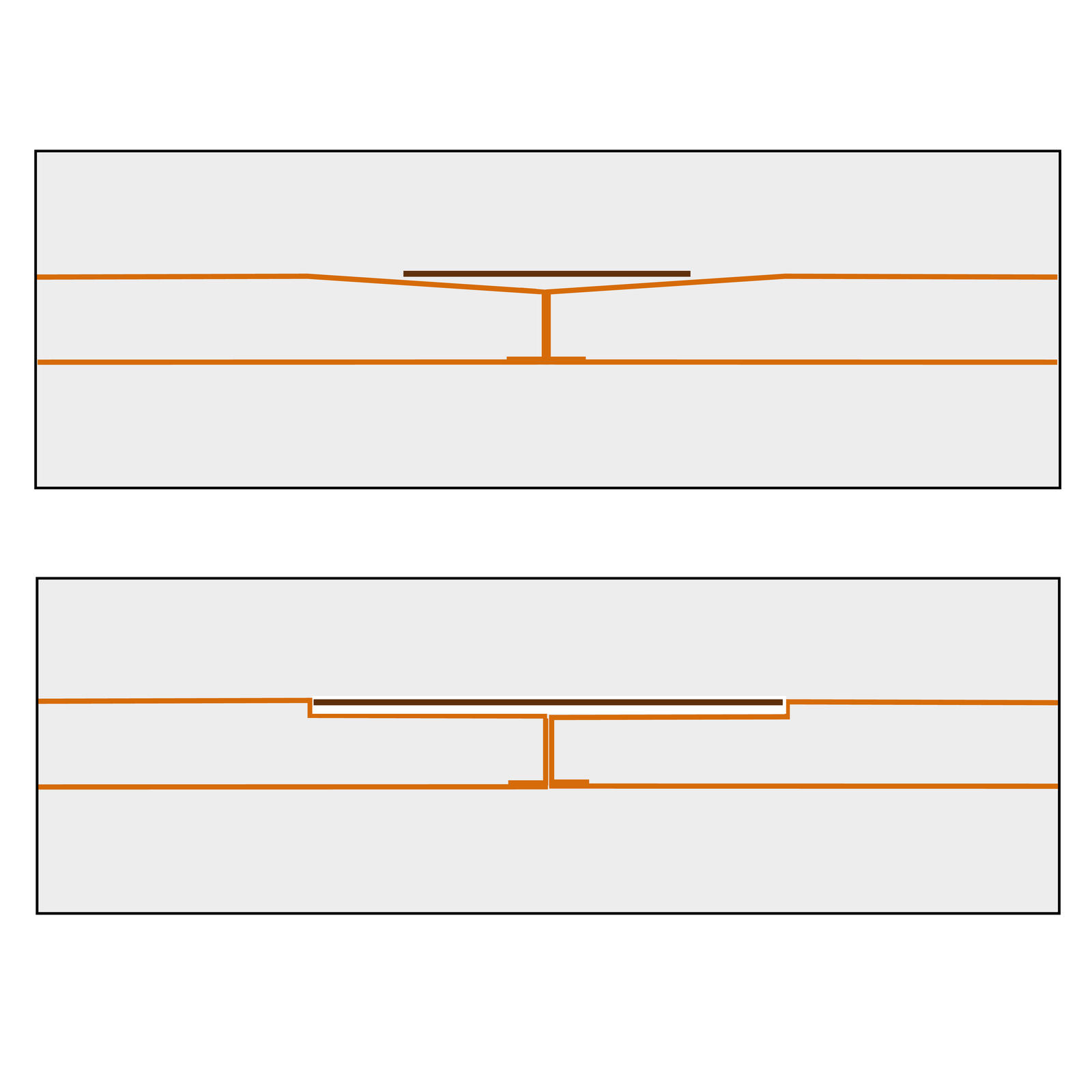
W zależności od tego, jaki ma być ostateczny poziom szpachlowania (szerzej w punkcie 6.7) na spoinę można dodatkowo nanieść warstwę systemowej finiszowej masy szpachlowej.
Krawędzie typu KS. W przypadku tego typu krawędzi, należy nanieść na łączenie warstwę konstrukcyjnej masy szpachlowej, następnie wtopić w nią taśmę zbrojącą (papierową lub fizelinową), a po wyschnięciu nałożyć jedną lub dwie kolejne warstwy systemowej masy szpachlowej. Podobnie jak w przypadku krawędzi omawianych powyżej, w zależności od ostatecznego poziomu szpachlowania, spoinę można pokryć dodatkowo systemową finiszową masą szpachlową.
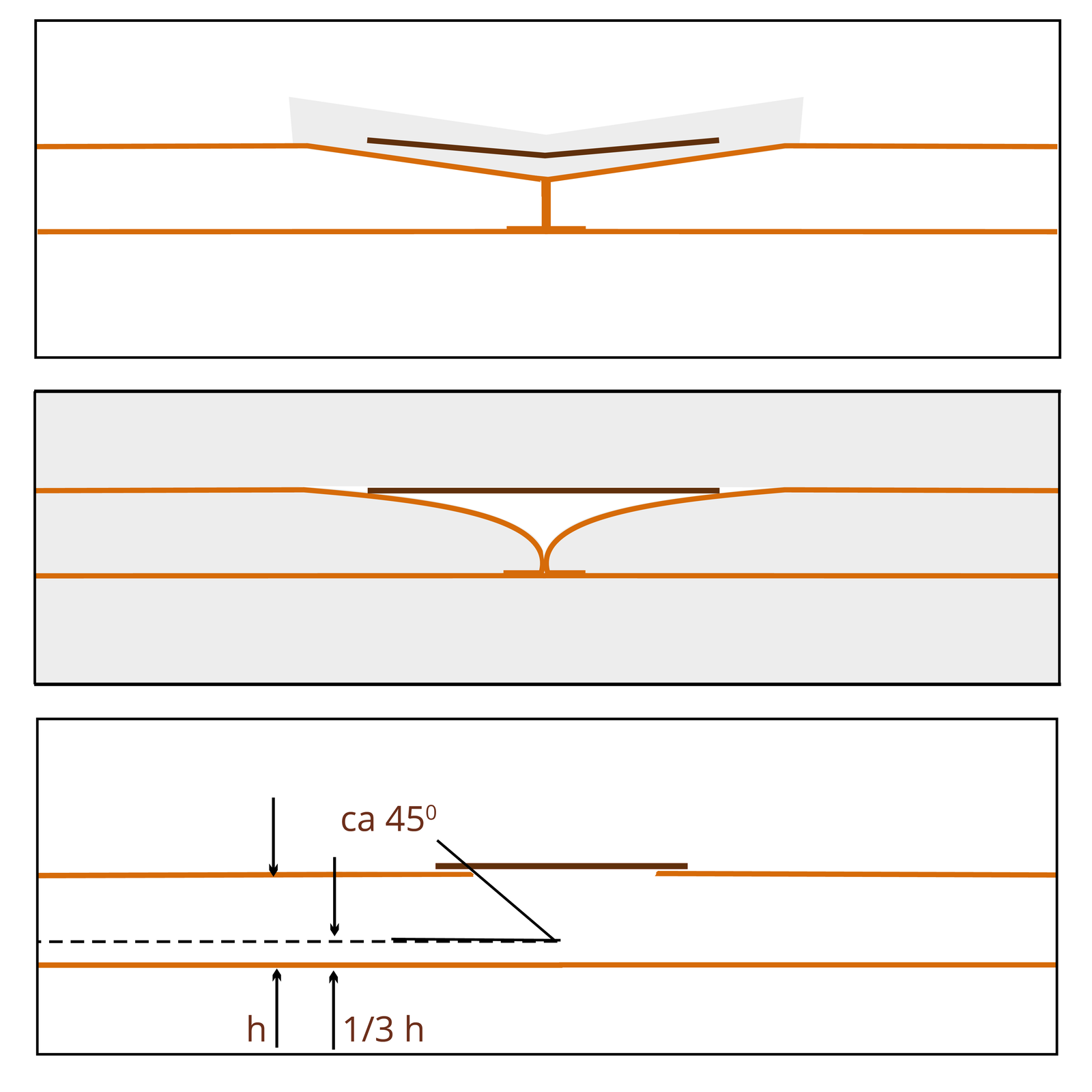
Krawędzie typu KPOS. Na łączeniach tego typu krawędzi, stosując dowolny rodzaj taśmy zbrojącej należy na łączenie nanieść warstwę systemowej konstrukcyjnej masy szpachlowej, a następnie wtopić w nią taśmę. Po wyschnięciu należy zaszpachlować łączenie dwiema kolejnymi warstwami konstrukcyjnej masy szpachlowej.
W przypadku stosowania płyt z typ rodzajem krawędzi (KPOS) można również zdecydować się na szpachlowanie bez taśm zbrojących. Należy wówczas użyć specjalnej systemowej konstrukcyjnej masy szpachlowej przeznaczonej do szpachlowania bez taśmy zbrojącej. W takim przypadku należy położyć dwie lub trzy warstwy wspomnianej masy szpachlowej.
Tak jak w przypadkach opisanych powyżej, zależnie od ostatecznego poziomu szpachlowania, na spoinę można dodatkowo nałożyć warstwę finiszowej masy szpachlowej.
Krawędzie poprzeczne (fabryczne lub cięte). Na tego typu łączeniach należy stosować taśmy zbrojące. W pierwszą warstwę systemowej konstrukcyjnej masy szpachlowej należy zatopić taśmę, a następnie - po wyschnięciu - zaszpachlować ponownie jedną warstwą systemowej konstrukcyjnej masy szpachlowej. Gdy i ta warstwa wyschnie należy zastosować na spoinę masę finiszową, nakładając ją na szerokości około 20‑30 cm z każdej strony, aby zniwelować zgrubienia.
Połączenia ślizgowe wykonuje się na łączeniu płyty gipsowo‑kartonowej ze ścianą monolityczną. Dobrze wykonany montaż pozwala uniknąć pęknięć. W połączeniu ślizgowym korzysta się ze specjalnej taśmy, dzięki której masa szpachlowa nie łączy się w sposób trwały ze ścianą. Między zaszpachlowaną płytą i ścianą pozostaje szczelina, która umożliwia ruch w miejscu połączenia. W efekcie otrzymujemy połączenie bez nieestetycznych pęknięć i uszkodzeń. Użycie tej metody pozwala na uniknięcie powstania niekontrolowanych pęknięć.
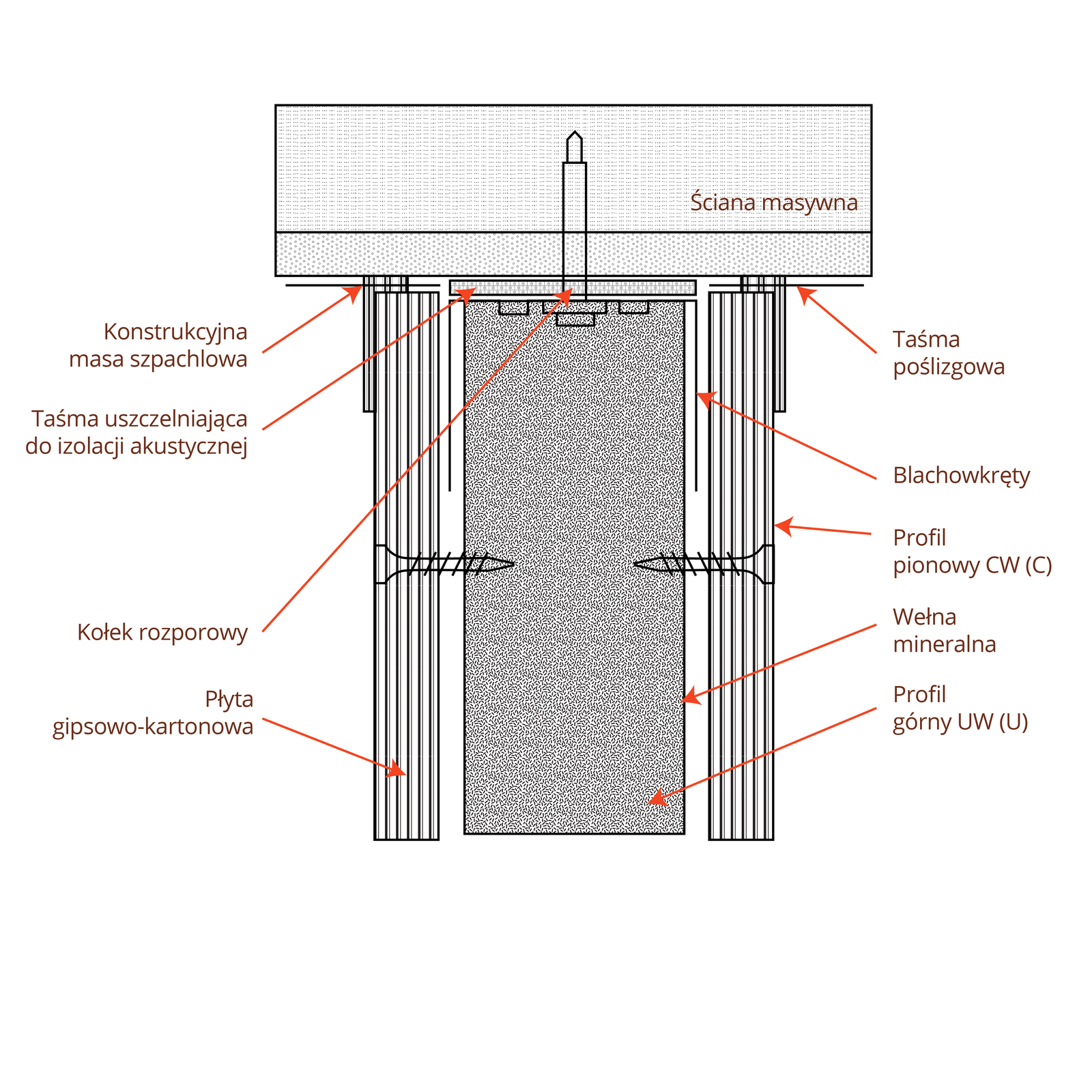
Dokładne szpachlowanie gipsowe jest kluczowe dla uzyskania równomiernej powierzchni. Odpowiednie poziomowanie eliminuje wszelkie nierówności i przygotowuje konstrukcję do malowania.
Aby skatalogować jakość wykończenia w systemie suchej zabudowy przyjmuje się cztery poziomy jakości szpachlowania powierzchni. Polski standard branżowy odpowiada klasyfikacji europejskiej (Quality Level) i wyróżnia cztery poziomy szpachlowania.
Poziom Szpachlowania Gipsowego PSG 1 (Quality Level 1 - Q1). Poziom ten dotyczy takich powierzchni wykonanych z płyt gipsowo‑kartonowych, dla których nie ma wymagań estetycznych (np. pomieszczeń technicznych lub tymczasowych albo podłoża przygotowywanego pod płytki ceramiczne lub panele). Przy tym poziomie niezbędne jest szpachlowanie podstawowe (na które składa się wykonanie spoinowania połączeń płyt i pokrycie masą szpachlową elementów mocujących i wykończeniowych).
Przy użyciu płyt typu NS i PRO szpachlowanie na pierwszym poziomie zakłada by przy krawędziach płyt była przyklejona taśma zbrojąca z włókna szklanego zaszpachlowana jedną lub dwiema warstwami systemowej konstrukcyjnej masy szpachlowej.
Przy zastosowaniu płyt o krawędziach KS i użyciu taśmy zbrojącej, na połączeniach krawędzi powinna być naniesiona warstwa systemowej konstrukcyjnej masy szpachlowej, w którą należy wtopić taśmę zbrojącą. Następnie, po wyschnięciu, połączenie powinno być ponownie zaszpachlowane warstwą wspomnianej masy szpachlowej.
W przypadku użycia płyt typu KPOS można zastosować metodę opisaną wyżej dla płyt o krawędziach KS lub zdecydować się na szpachlowanie bez użycia taśmy zbrojącej. W takim przypadku do spoinowania należy użyć specjalnej systemowej, konstrukcyjnej masy szpachlowej i powtórzyć szpachlowanie dwukrotnie lub trzykrotnie.
Poziom Szpachlowania Gipsowego PSG 2 (Quality Level 2 - Q2). Szpachlowanie na tym poziomie zawiera w sobie szpachlowanie podstawowe (PSG 1) oraz dodatkowo szpachlowanie systemowymi masami szpachlowymi (konstrukcyjną oraz finiszową) do uzyskania płynnego przejścia powierzchni spoiny z powierzchnią płyty gipsowo‑kartonowej. Przy tym poziomie nie mogą występować zagłębienia i rysy po użyciu narzędzi. Jeśli to konieczne, należy wyszlifować szpachlowane powierzchnie. Poziom ten jest odpowiedni dla przygotowania powierzchni, na których mają się znaleźć tapety, farby strukturalne lub tynki ozdobne.
Poziom Szpachlowania Gipsowego PSG 3 (Quality Level 3 - Q3). Szpachlowanie na tym poziomie zawiera w sobie szpachlowanie PSG 2 oraz szpachlowanie całej powierzchni masami systemowymi, szpachlami lub gładziami, dzięki którym powierzchnia zostanie wyrównana, mikropory zamknięte a tekstura ujednolicona. W tym poziomie grubość nakładanej warstwy z reguły nie przekracza 1 mm. Powyższy efekt można osiągnąć dzięki użyciu pac stalowych charakteryzujących się wypolerowaną powierzchnią roboczą i idealnie prostymi krawędziami. Nierówności powinny zostać zeszlifowane siatką ścierną lub papierem o ziarnistości 200.
Poziom Szpachlowania Gipsowego PSG 4 (Quality Level 4 - Q4). Ten poziom zakłada nałożenie na całą powierzchnię tynku cienkowarstwowego albo gładzi gipsowej. Oprócz wygładzenia czasem występuje konieczność wypolerowania całej warstwy. Powierzchnię o tym poziomie szpachlowania można malować farbami matowymi lub pokrywać grubymi tapetami.
Dzięki dokładnemu przygotowaniu krawędzi ciętych płyt gipsowo‑kartonowych jesteśmy w stanie zapewnić konstrukcji trwałość i estetyczny wygląd. Pierwszy krok polega na pozbyciu się ostrych krawędzi poprzez szlifowanie, drugi zaś na ochronie krawędzi i usunięciu widocznych szwów.
Obróbka naroży polega na osadzeniu listew narożnych w celu ochrony naroży konstrukcji. Następnie naroża wykańcza się w celu uzyskania estetycznego efektu. Ten krok zapewnia estetyczny wygląd konstrukcji, a jednocześnie chroni narożniki przed uszkodzeniami mechanicznymi.
Do zbrojenia spoin w narożach wewnętrznych można użyć taśmy papierowej. Taśma papierowa ma wzdłużne przetłoczenia umożliwiające łatwe zagięcie. Proces szpachlowania wygląda podobnie jak w przypadku krawędzi ciętych. Należy więc kolejno:
odpylić narożnik,
następnie nanieść w narożnik konstrukcyjną masę szpachlową plackami w rozstawie nie większym niż 10 cm,
wcisnąć w narożnik taśmę papierową i dokładnie docisnąć przy pomocy szpachelki do naroży wewnętrznych,
po wyschnięciu masy szpachlowej nanieść następną warstwę masy, po wyschnięciu kolejnej warstwy - przeszlifować naroże.
Do obróbki naroży zewnętrznych wykorzystuje się aluminiowe narożniki perforowane. Narożnik powinien być wklejony na masę szpachlową. Kolejne etapy montażu narożników ochronnych (aluminiowych) przedstawiają się następująco:
oczyścić cięte krawędzie płyt z pyłu,
nanieść masę szpachlową na naroże plackami w rozstawie nie większym niż 10 cm,
wcisnąć i ustawić (wypoziomować) narożnik na narożu ściany (przykleić),
wyrównać wyciśniętą masę i uzupełnić tak, by cały narożnik pokryć masą szpachlową po obu stronach,
po wyschnięciu uzupełnić miejsca skurczu masą szpachlową, zaszpachlować na większą szerokość,
zgrubienie w narożu rozprowadzić masą fi niszową na szerokości 30 – 40 cm.
Szpachlowanie łbów wkrętów ma na celu ukrycie śladów mocowania i uzyskanie jednolitej powierzchni.
Na początek przykrywa się łby wkrętów za pomocą odpowiedniej masy szpachlowej, następnie wykańcza się je szlifując, aby uzyskać gładką powierzchnię.
Powrót do spisu treściPowrót do spisu treści
6.7 Ocena efektu końcowego prac w systemach suchej zabudowy
Po zakończeniu prac przeprowadza się ocenę efektu końcowego, sprawdzając estetykę, trwałość i funkcjonalność konstrukcji.
Kluczowe elementy oceny to jakość wykończenia, solidność konstrukcji oraz zgodność z projektem. Ocenia się więc gładkość, równość oraz estetykę powierzchni; to, czy konstrukcja jest stabilna i wytrzymała; a także porównuje efekt końcowy z założeniami projektowymi.
Powrót do spisu treściPowrót do spisu treści
6.8 Zasady wykonywania poszczególnych elementów obudowy konstrukcji dachu
Obudowa ścianki kolankowej
Ścianką kolankową nazywamy pionową konstrukcję ściany, zlokalizowaną najczęściej pod skosem dachu. Wyznacza ona granicę między kondygnacją użytkową a skosem dachowym. Wykonanie zabudowy ścianki kolankowej obejmuje postawienie konstrukcji, która oddziela tę przestrzeń, tworząc przy tym izolację termiczną i akustyczną. Poniżej zostały opisane poszczególne czynności, składające się na wykonanie zabudowy ścianki kolankowej.
Dolny profil UD należy przykręcić do podłogi, profile boczne do murowanych ścian szczytowych lub działowych, natomiast profil górny trzeba przymocować do krokwi.
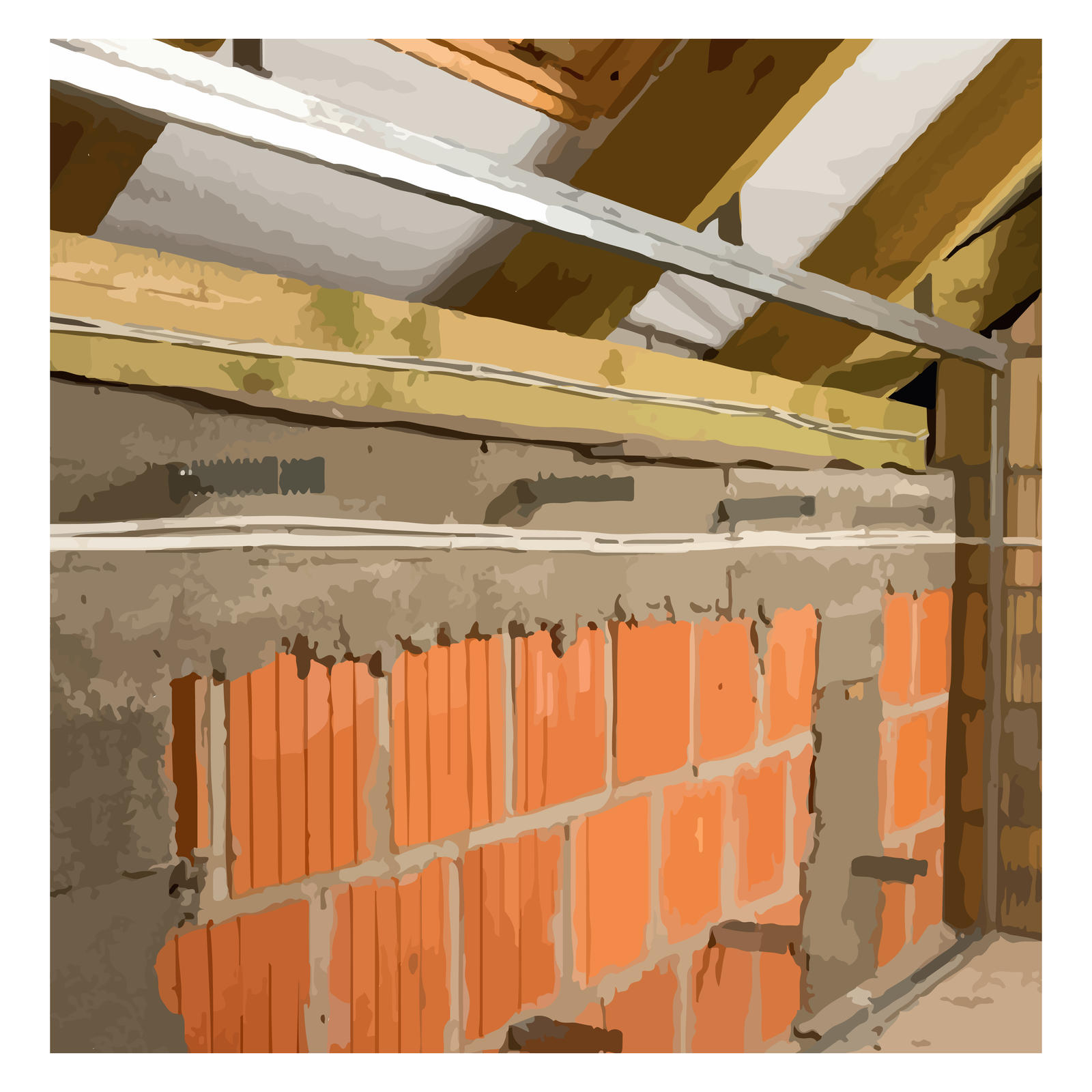
Zanim przystąpimy do montażu kolejnych elementów metalowego rusztu warto sprawdzić, czy profile przykręcone na jego obwodzie zachowują pion i poziom.
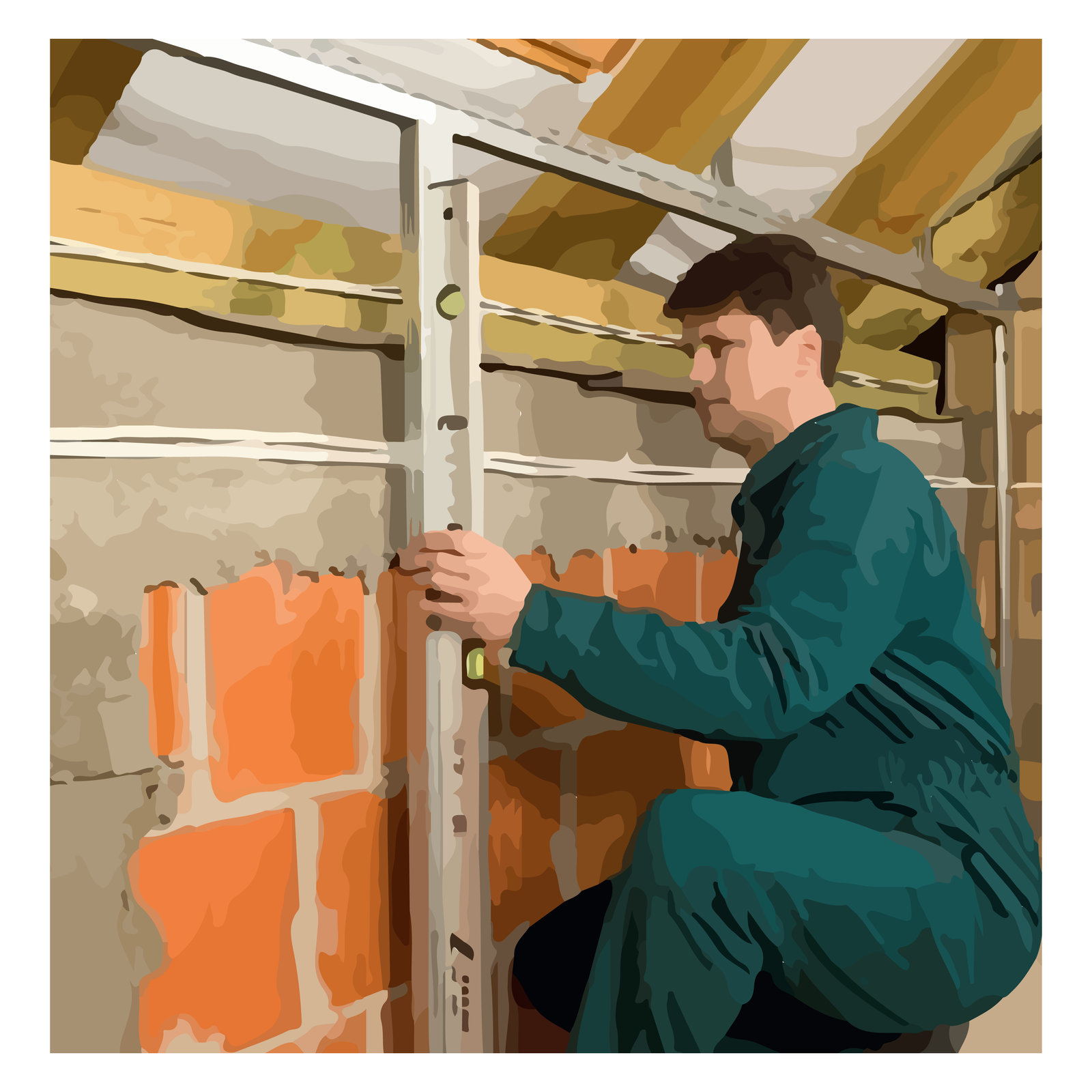
Kolejny krok, to przykręcenie do ściany kolankowej łączników ES w rozstawie od 40 do 60 cm. Następnie do profili UD należy wstawić pionowo profile CD i zamocować je do łączników ES.
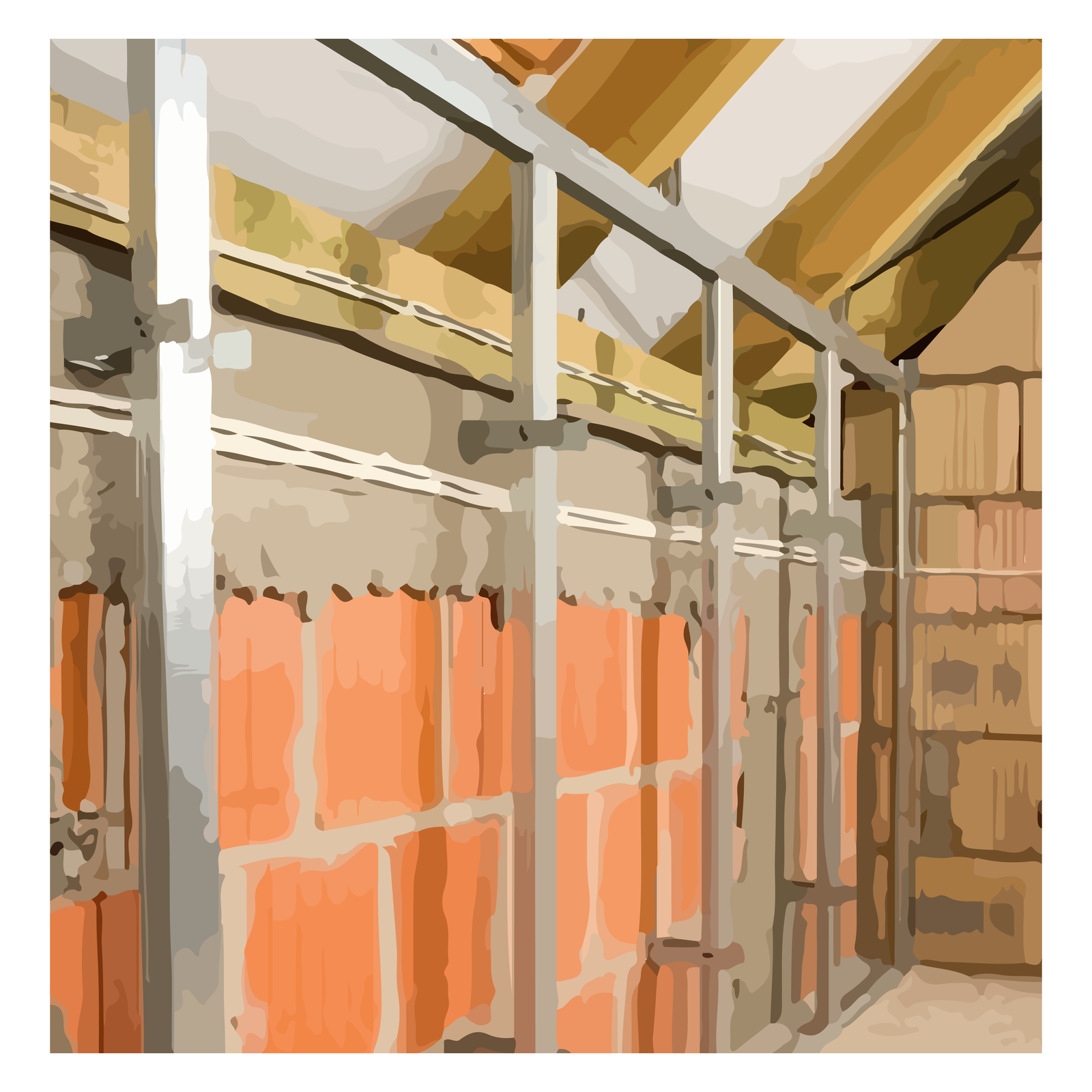
Następnie można przystąpić do montażu płyt gipsowo‑kartonowych i ich wykończenia. Styk obudowy skosu i ścianki kolankowej obrazuje poniższa grafika:
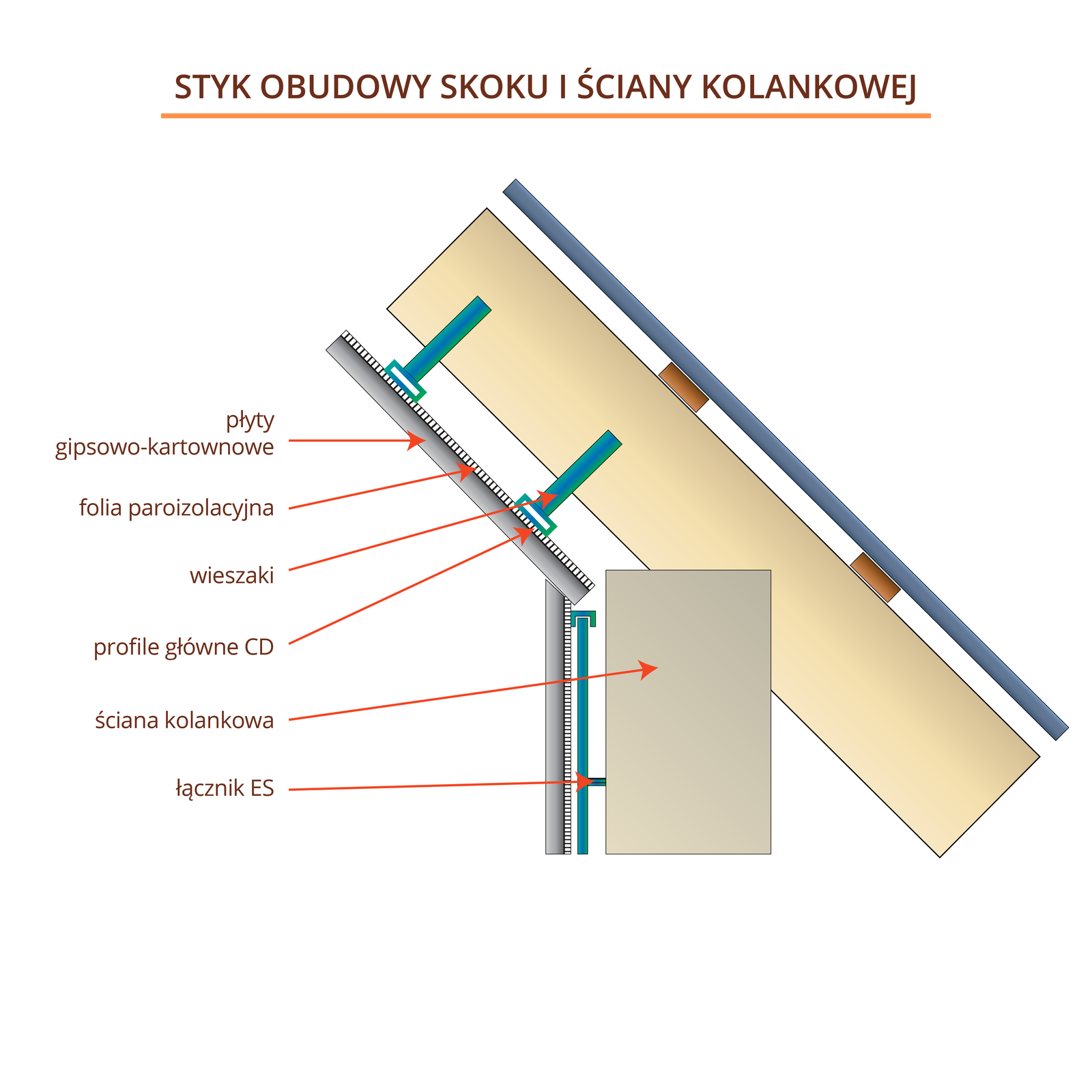
Obudowa skosu połaciowego
Ruszt, do którego przytwierdza się płyty gipsowo‑kartonowe powstaje z wieszaków kotwowych, a także profili CD i UD. Zadaniem wieszaków jest ograniczenie wpływu odkształceń więźby dachowej na obudowę skosu. To do wieszaków montuje się następnie profile CD i UD.
Wieszaki kotwowe, które mogą mieć długość od 15 cm do nawet 27 cm pozwalają skorygować nierówności więźby dachowej. Należy je przytwierdzić dwoma lub trzema wkrętami o długości co najmniej 35 mm do boku każdej krokwi, jętki lub kleszczy. Ramiona wieszaków powinny się stykać z bokiem elementu więźby na długości co najmniej 3 cm. Do wieszaków są mocowane profile.
Ruszt tworzą profile CD i UD. W pierwszej kolejności powinny być zamontowane profile UD, w które następnie wsuwa się profile CD w rozstawie wynoszącym maksymalnie 40 cm. Przed przytwierdzeniem płyt należy zamontować izolację oraz upewnić się, że płaszczyzny wyznaczone przez ruszt są równe.
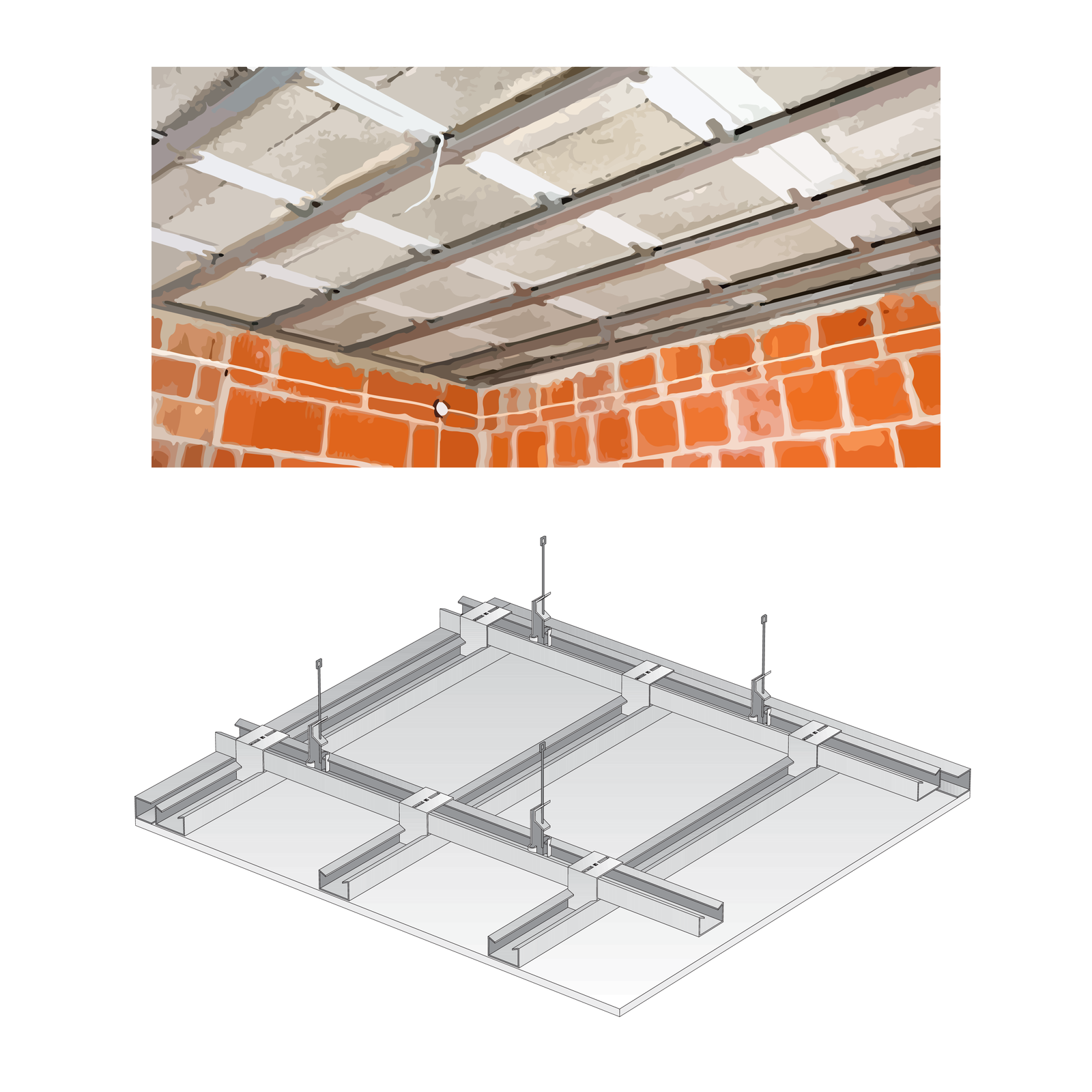
Płyty gipsowo‑kartonowe są szczególnie narażone na naprężenia i uszkodzenia w miejscach, styku się ze ścianami działowymi, szczytowymi, a także z kominami oraz sufitami podwieszonymi. W związku z tym wzdłuż takich styków stosuje się połączenie ślizgowe.
Obudowa sufitu podwieszanego
Wykonanie obudowy sufitu podwieszanego pozwala na ukrycie instalacji elektrycznych, wentylacyjnych czy klimatyzacyjnych pod płytami gipsowo‑kartonowymi.
Obudowę sufitów podwieszanych wykonuje się z wykorzystaniem profili przyściennych U30 i nośnych CD60 oraz łączników i wieszaków.
Zabudowę wykonuje się w następujących etapach. Do ścian po obwodzie sufitu należy przytwierdzić profile przyścienne. Profile CD wsuwa się do profili U30 w rozstawie 40 cm. W ten sposób powstaje ruszt. Jeśli szerokość sufitu jest większa od długości profili można zastosować specjalne łączniki.
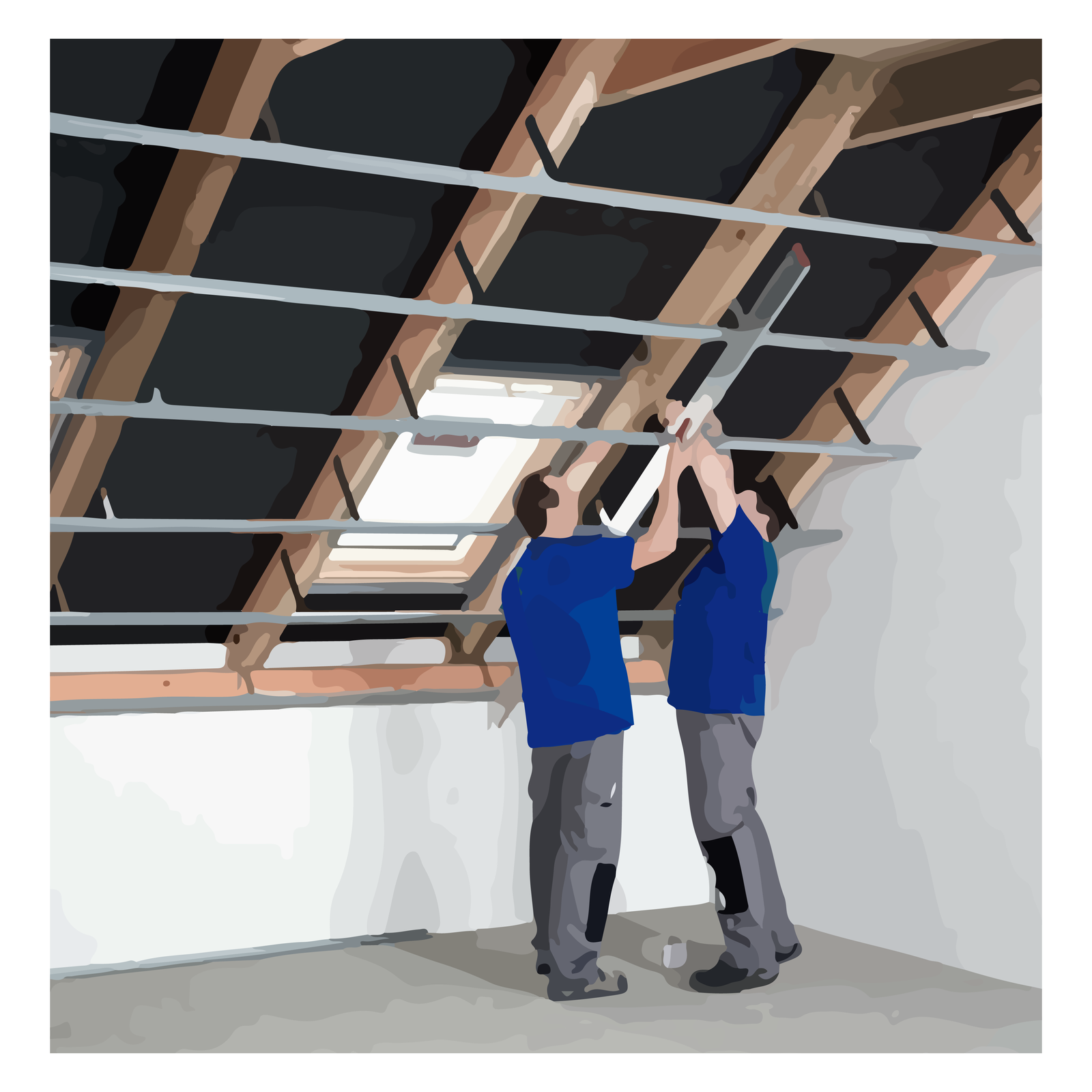
Wykonując sufit podwieszany na większych powierzchniach warto zdecydować się n ruszt dwuwarstwowy, krzyżowy. Jest on wzmocniony profilami umieszczonymi w poprzek rusztu podstawowego w rozstawie jednego metra oraz spięty specjalnymi łącznikami krzyżowymi. Na metr kwadratowy powierzchni powinien przypadać co najmniej jeden wieszak (regulowany drutowy, noniuszowy lub sztywny). Wieszaki regulowane i noniuszowe pomagają w poziomowaniu sufitu.
Zasady i sposoby wyznaczania płaszczyzn ościeży
7. Spis ilustracji
Rys. 1. Przekrój płyty gipsowo‑kartonowej
Rys. 2. Typy krawędzi: A – PRO, B – NS, C – KS, D – KPOS, E – KP
Rys. 3. Wygląd, nazwa i oznaczenie profili
Rys. 4. Profil kapeluszowy
Rys. 5. Profil uniwersalny FLEX
Rys. 6. Profil V
Rys. 7. Profil narożnikowy
Rys. 8. Masa szpachlowa do łączenia płyt gipsowo‑kartonowych bez użycia taśmy
Rys. 9. Gotowa masa szpachlowa do wstępnego i finiszowego szpachlowania połączeń płyt g‑k z zastosowaniem taśmy zbrojącej
Rys. 10. Gładź gipsowa do szpachlowania połączeń płyt gipsowo‑kartonowych i cienkowarstwowego szpachlowania podłoży mineralnych
Rys. 11. Taśma fizelinowa
Rys. 12. Taśma papierowa
Rys. 13. Taśma tuff‑tape
Rys. 14. Tynk gipsowy maszynowy
Rys. 15. Masa tynkarska gipsowa
Rys. 16. Wełna mineralna
Rys. 17. Wieszaki noniuszowe
Rys. 18. Wieszaki obrotowe
Rys. 19. Łączniki krzyżowe
Rys. 20. Łączniki wzdłużne
Rys. 21. Uchwyty ES
Rys. 22. Blachowkręty
Rys. 23. Blachowkręty samonawiercające
Rys. 24. Wkręty do drewna
Rys. 25. Nóż z wymiennym ostrzem
Rys. 26. Piła otwornica
Rys. 27. Piła płatnica
Rys. 28. Tarnik do płyt
Rys. 29. Otwornica do płyt
Rys. 30. Wiadro do mieszania
Rys. 31. Kielnia do mieszania ręcznego
Rys. 32. Mieszadło elektryczne
Rys. 33. Łata
Rys. 34. Poziomica laserowa
Rys. 35. Poziomica tradycyjna
Rys. 36. Wkrętarka z regulacją głębokości wkręcania
Rys. 37. Młotek gumowy
Rys. 38. Szpachelka
Rys. 39. Paca metalowa
Rys. 40. Papier ścierny
Rys. 41. Szlifierka
Rys. 42. Zaciskarka do profili
Rys. 43. Gilotyna do profili
Rys. 44. Strug kątowy
Rys. 45. Sznur murarski (do trasowania)
Rys. 46. Montowanie profili stalowych
Rys. 47. Montowanie profili stalowych
Rys. 48. Mocowanie folii paroizolacyjnej
Rys. 49. Docinanie
Rys. 50. Fazowanie
Rys. 51. Obróbka okien dachowych
Rys. 52. Krawędzie typu NS i PRO
Rys. 53. Taśma papierowa lub fizelinowa
Rys. 54. Krawędzie typu KS, krawędzie typu KPOS oraz krawędzie poprzeczne
Rys. 55. Połączenia ślizgowe
Rys. 56. Profile na obwodzie ścianki
Rys. 57. Sprawdzenie pionu i poziomu
Rys. 58. Łączniki ES, profile CD
Rys. 59. Styk skosu i ścianki kolankowej
Rys. 60. Obudowa sufitu podwieszanego
Rys. 61. Sprawdzenie płaszczyzny wyznaczonej przez ruszt
Powrót do spisu treściPowrót do spisu treści
8. Bibliografia
Kaczkowska A., Sucha zabudowa wnętrz, KaBe, Krosno 2015.
Kusina A., Machnik M.: Wykonywanie robót montażowych, okładzinowych i wykończeniowych, Część 1, WSiP, Warszawa 2018.
Maj T., Organizacja i technologia robót wykończeniowych, WSiP, Warszawa 2019.
Rogalski P., Szczepański W., Systemy suchej zabudowy wnętrz, Polskie Stowarzyszenie Gipsu, Warszawa 2015 .
Powrót do spisu treściPowrót do spisu treści