E‑BOOK Wykonywanie i naprawa pomocy wzrokowych
MEP.03. Wykonywanie i naprawa pomocy wzrokowych - Technik Optyk 325302
Urządzenia do naprawy i wykonywania okularów
E‑BOOK
Proces powstawania okularów korekcyjnych
Proces powstawania okularów korekcyjnych rozpoczyna się w salonie optycznym. To moment, w którym klient wybiera oprawki, a optometrysta wykonuje pomiary skali wady wzroku pacjenta i wystawia receptę na okulary.
Recepta stanowi podstawową dokumentację potrzebną do wykonania okularów i zawiera wszystkie ważne parametry, jakie powinny spełnić tworzone przez optyka okulary.
Recepta optyczna powinna zawierać identyfikację pacjenta oraz informacje o wszystkich wartościach niezbędnych do przygotowania odpowiednich soczewek okularowych:
sfery,
cylindra,
osi,
rozstawu źrenic.
Na recepcie mogą również pojawić się bardziej specjalistyczne oznaczenia, wskazujące na konieczność korygowania rzadziej spotykanych zaburzeń, np. addycja, pryzmat i baza pryzmatu, wysokość montażowa lub zalecane soczewki.
Nawet gdy recepta jest kompletna, często wymaga uzupełnienia o dodatkowe informacje, takie jak: wysokości środków w oprawce, rodzaje soczewek, wymagany kąt pantoskopowy, kolor czy intensywność zabarwienia soczewek. Do recepty dołącza się wówczas zlecenie wykonania okularów. Można też wszystkie informacje, te z recepty i te dodatkowe, zebrać w całość i zapisać w formularzu zlecenia. Warto stosować własny formularz zlecenia zawierający pełny zakres informacji w celu zmniejszenia ryzyka popełnienia błędu przy wykonywaniu okularów na podstawie kilku dokumentów.
Na podstawie recepty lub zlecenia optyk zamawia soczewki u producenta lub dystrybutora. Gdy te zostaną dostarczone, optyk dostosowuje je do potrzeb klienta i wybranych przez niego oprawek.
Rozpoczynając prace nad okularami, trzeba zwrócić uwagę na to, że optyk ma do czynienia z zestawem często zawierającym bardzo małe elementy, które łatwo zgubić lub pomylić z komponentami należącymi do innych zestawów. Warto zadbać o wyodrębnione pole pracy. Optycy często korzystają w tym celu ze specjalnie do tego przeznaczonych tac. Obowiązuje tu zasada: jedna taca zawiera zestaw potrzebny do stworzenia jednej pary okularów i nic poza tym. Na tacy powinny się zatem znaleźć: zlecenie lub recepta, oprawa i soczewki okularowe.
Na tym etapie pracy zadaniem optyka jest zamontowanie soczewek w oprawach i dostosowanie okularów do potrzeb klienta według zapisów recepty lub zlecenia.
Na początku optyk wyznacza w soczewkach środki optyczne, a w soczewkach cylindrycznych do korekcji astygmatyzmu (cylindrycznych) również osie cylindra. Optyk wykonuje to zadanie na urządzeniu zwanym dioptromierzem. W dioptromierzu znajduje się tusz, który jest nanoszony na soczewkę. Pozwala to na bardzo dokładne wyznaczenie parametrów korekcji dostosowanej do określonego pacjenta.
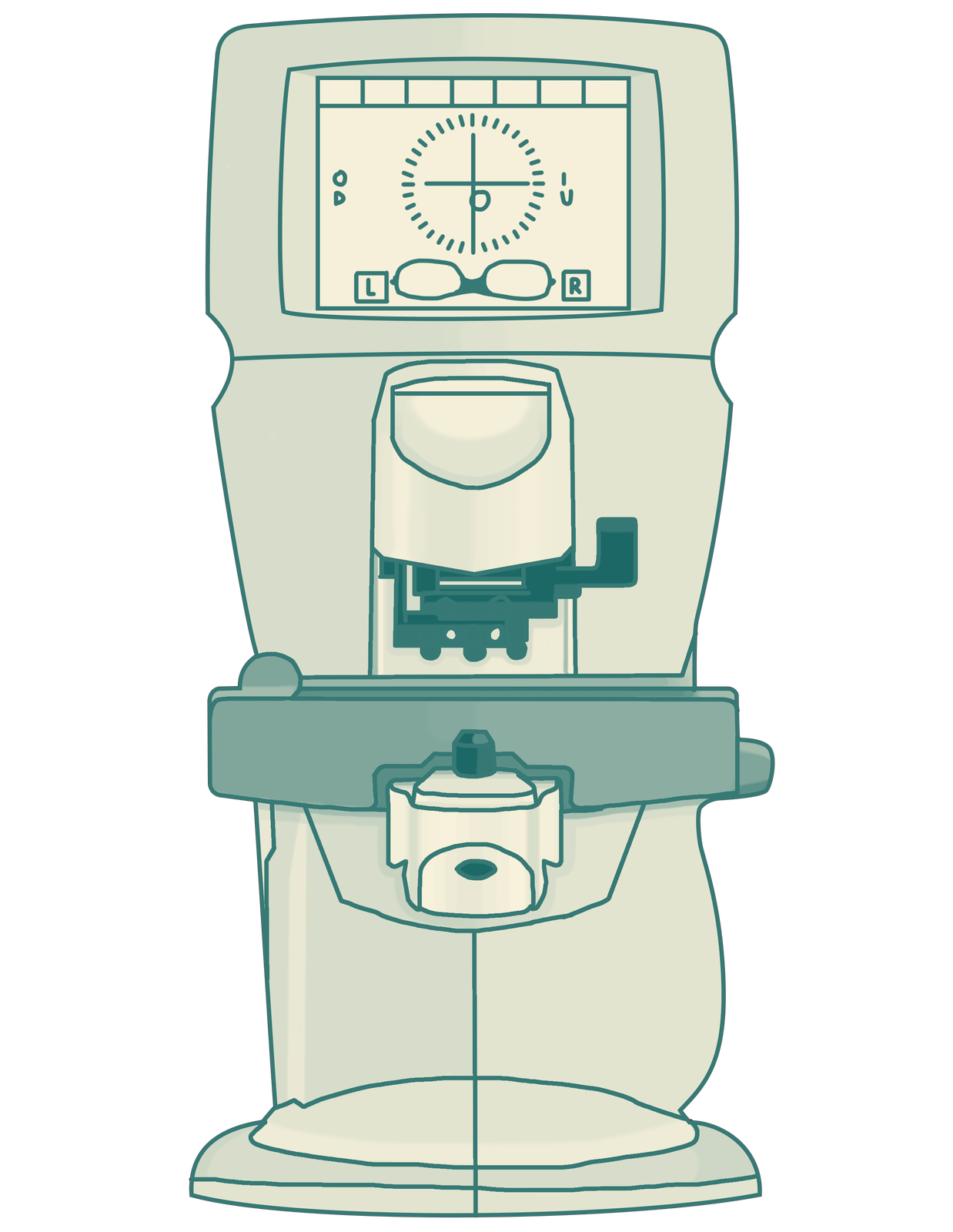
Tak opisaną soczewkę optyk przenosi do centroskopu. Centroskop pozwala przykleić na środku optycznym soczewki specjalne blokery, które utrzymują soczewkę dokładnie w wyznaczonych wcześniej parametrach. Blokery zapobiegają niepożądanemu przesuwaniu się soczewki w automacie szlifierskim.
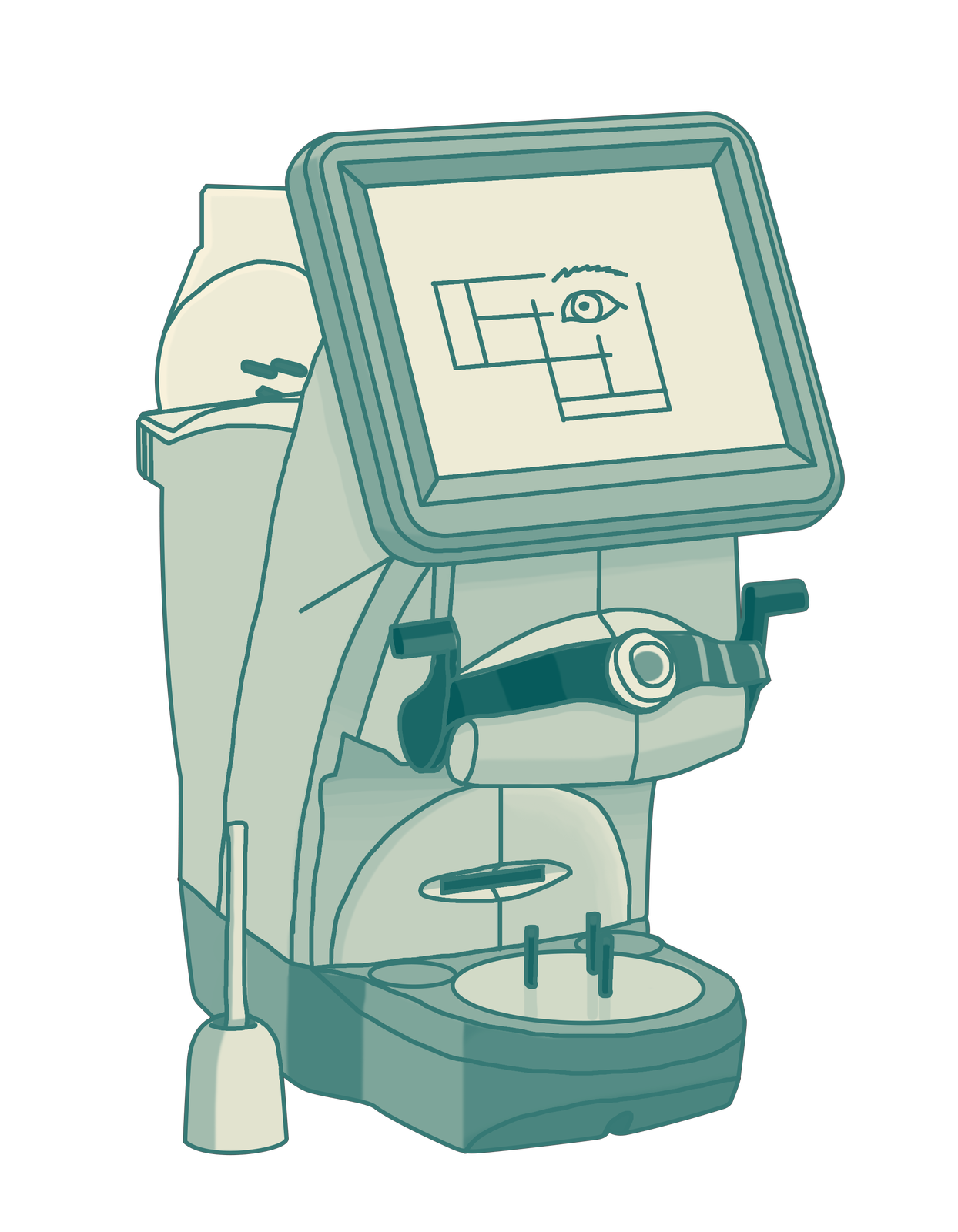
Automat szlifierski zazwyczaj wyposażony jest w skaner, który odczytuje z oprawy jej kształt, krzywiznę i rozstaw. Optyk wprowadza do urządzenia dane, takie jak: rozstaw źrenic pacjenta oraz wysokość montażu. Na tej podstawie skaner oblicza optymalne wymagania do precyzyjnego dopasowania soczewek w zadanej oprawie dla danego pacjenta. Kiedy wypunktowana soczewka oraz zeskanowana oprawa znajdą się w automacie szlifierskim, rozpoczyna się proces obróbki soczewek okularowych. Automat zawsze najpierw szlifuje soczewkę prawą, a następnie powtarza ten proces dla soczewki lewej.
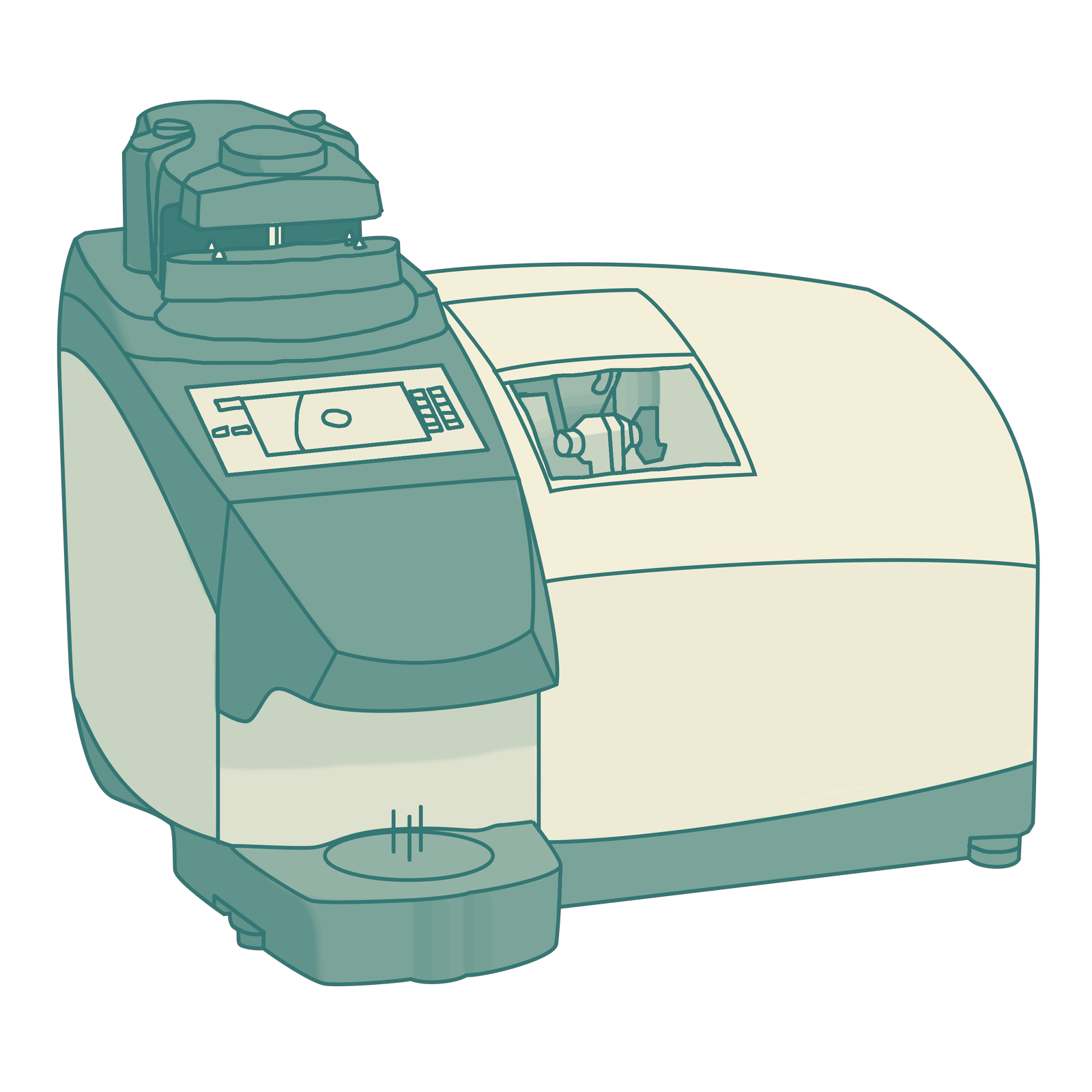
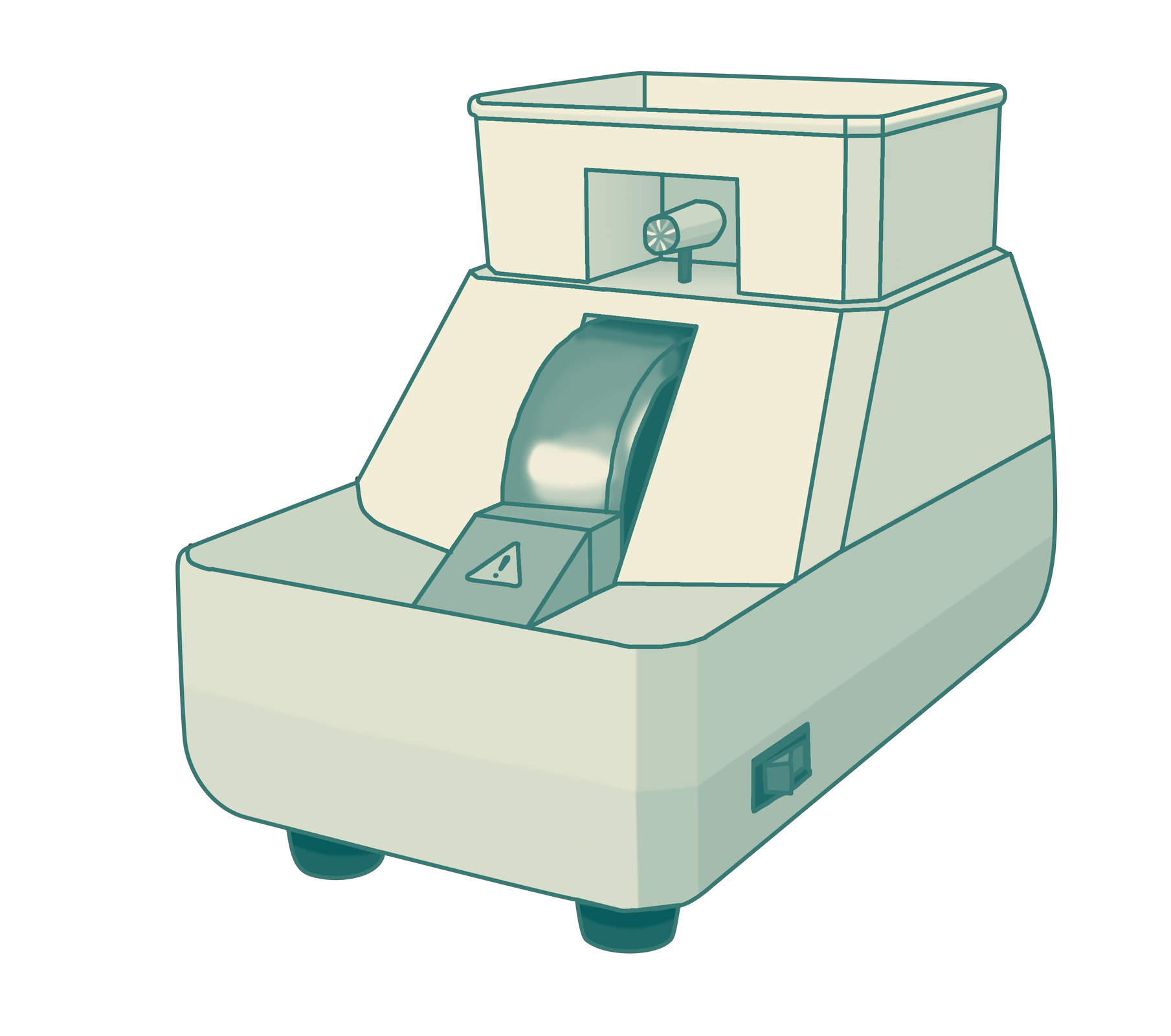
Podczas procesu szlifowania skanowana jest również soczewka. Mierzona jest jej grubość, krzywizna oraz kilka innych parametrów.
Automat szlifierski jest wyposażony w kilka tarcz. Są one dostosowane do obróbki soczewek wykonanych z różnych materiałów i montowanych do różnych typów oprawek. Inny rowek wykonywany jest w soczewce do oprawy pełnej metalowej lub z tworzywa, a inny w soczewce do oprawy niepełnej typu „żyłka”. Soczewki montowane do oprawy bezramkowej typu „patent” nie są rowkowane.
Optyk przez cały czas nadzoruje proces szlifowania.
Soczewka po kilku minutach przyjmuje kształt wprowadzonego do automatu szablonu.
Optyk musi sprawdzić, czy wielkość soczewki jest odpowiednia, a kształt zgodny z oprawą. Trzeba też upewnić się, czy na brzegach soczewki nie powstały mikroodpryski lub inne uszkodzenia. Warto przeszlifować gotowe soczewki ręcznie na tarczy piaskowej, co pozwoli załamać ich brzegi i zapobiegnie powstawaniu odprysków.
Soczewki po oszlifowaniu i załamaniu krawędzi powinny zostać sprawdzone pod kątem jakości szlifowania. Optyk musi je dokładnie obejrzeć, by stwierdzić, że na ich brzegach nie ma wyszczerbień, faseta jest wykonana prawidłowo na całym obwodzie, a soczewka ma kształt i wymiar odpowiedni do zamocowania w oprawie.
Po skorygowaniu ewentualnych błędów można zająć się osadzeniem soczewek w oprawie okularów.
Zamontowanie wyszlifowanych soczewek w oprawie metalowej nie jest trudne. Wystarczy wpasować soczewkę w rowek oprawy i przy użyciu odpowiednich wkrętaków i śrubek zamknąć ją w metalowej ramce.
Nieco trudniej jest zamontować soczewki w oprawie niepełnej typu „żyłka”. W tym przypadku należy dopasowaną soczewkę umieścić delikatnie w rowku oprawy (zazwyczaj rowek znajduje się w górnej ramie oprawy, ale nie zawsze), następnie delikatnie, korzystając ze wstążki, wsunąć specjalną żyłkę w rowek soczewki.
Osadzenie soczewki w oprawie z tworzywa wymaga nieco większej wprawy. Ten proces odbywa się poprzez nagrzanie oprawy do odpowiedniej temperatury i zwiększenie plastyczności materiału, co pozwala na wciśnięcie soczewki w oprawę. Jeżeli oprawa zostanie zbyt mocno nagrzana, to ulegnie odkształceniu lub stopieniu. Jeśli jednak oprawa będzie niewystarczająco ogrzana, to może pęknąć podczas osadzania w niej soczewki lub może wyszczerbić soczewkę.
Najtrudniejsze jest montowanie soczewek w oprawie bezramkowej typu „patent”. Wymaga to ogromnej wprawy i precyzji. Po odpowiednim wyszlifowaniu i sfazowaniu soczewki oraz wypolerowaniu jej krawędzi należy w ściśle określonych miejscach soczewki wykonać otwory. Otwory te muszą być idealnie symetryczne i dopasowane do kształtu oraz parametrów mostka i zauszników. Następnie przy pomocy dedykowanych do tego celu wkrętaków przykręca się soczewkę i zabezpiecza odpowiednimi nakładkami, żeby zniwelować ewentualne naprężenia. Okulary w oprawkach typu „patent” są niezwykle delikatne i przy dopasowywaniu ich do twarzy klienta należy wykazać się umiejętnościami, które zapobiegną ewentualnym ich uszkodzeniom.
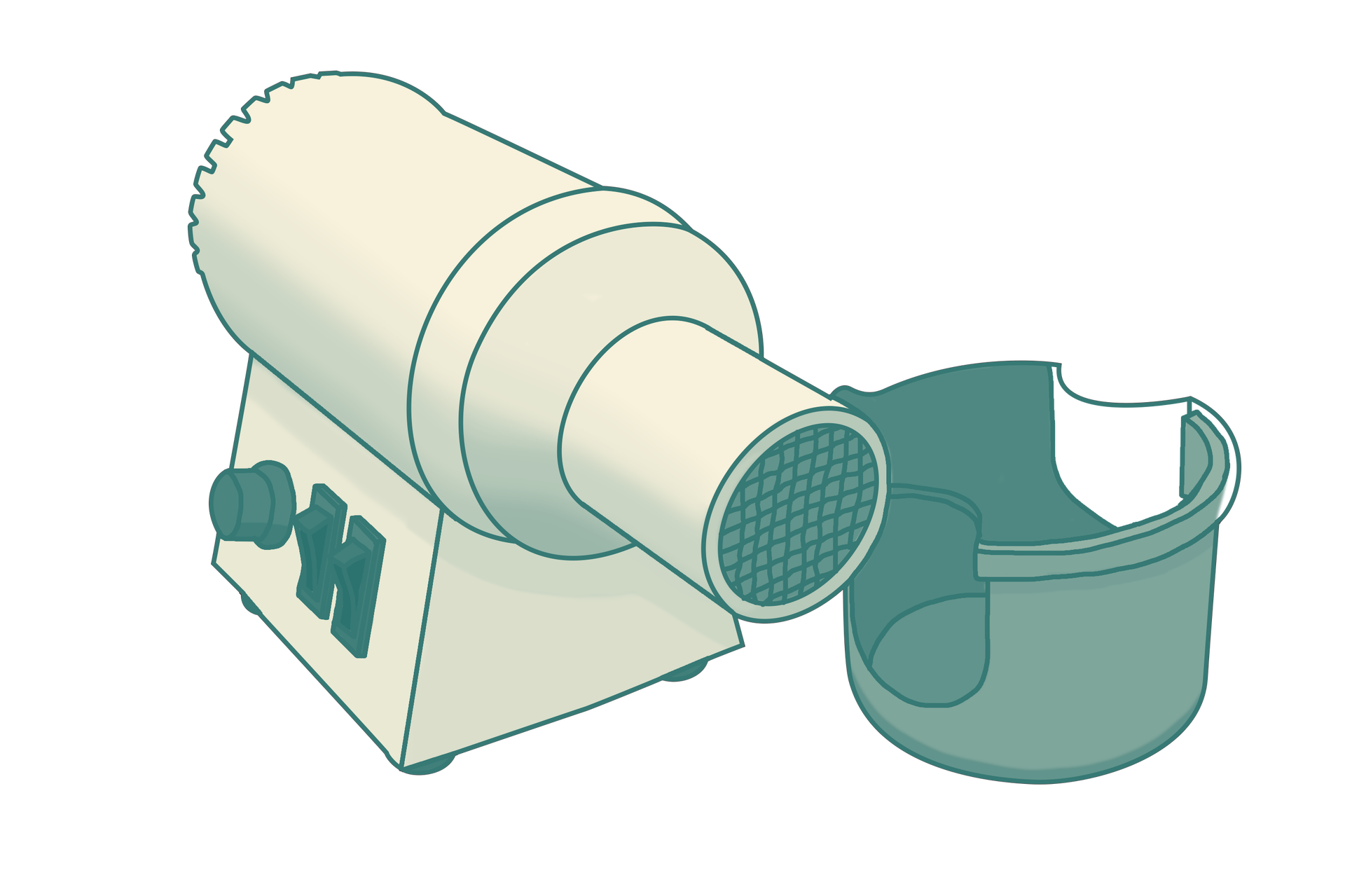
Po zakończeniu procesu tworzenia okularów gotowy produkt przechodzi testy poprawności wykonania. Na tym etapie optyk sprawdza kształt oprawy poddanej w czasie montażu dużym naprężeniom, a także weryfikuje, czy zauszniki są równe, a tarcze odpowiednio ustawione. W razie konieczności optyk reguluje oprawę lub osie soczewek cylindrycznych. Sprawdza je też pod kątem poprawności parametrów optycznych i zgodności z danymi z recepty.
Jeżeli wszystko się zgadza, okulary są czyszczone i po dopasowaniu do kształtu głowy klienta wydane są do użytkowania.