Maszyny i urządzenia- obsługa
MEC.03. Montaż i obsługa maszyn i urządzeń - Mechanik‑Monter maszyn i urządzeń, Technik mechanik
Maszyny i urządzenia - studium awarii
ATLAS INTERAKTYWNY
Spis treści
WstępWstęp
Niezawodność maszyn i urządzeńNiezawodność maszyn i urządzeń
Przyczyny zainteresowania niezawodnościąPrzyczyny zainteresowania niezawodnością
Sformułowanie poprawności funkcjonowania obiektuSformułowanie poprawności funkcjonowania obiektu
Miary niezawodności elementów nienaprawialnychMiary niezawodności elementów nienaprawialnych
Funkcja niezawodności i funkcja zawodnościFunkcja niezawodności i funkcja zawodności
Trwałość elementów nienaprawialnychTrwałość elementów nienaprawialnych
Intensywność i częstość uszkodzeńIntensywność i częstość uszkodzeń
Przykłady uszkodzeń maszyn i urządzeńPrzykłady uszkodzeń maszyn i urządzeń
Wstęp
W dzisiejszych czasach prawie wszystkie elementy maszyn są ze sobą wzajemnie powiązane. W związku z tym elementy te muszą być ciągle w optymalnej kondycji, aby nie doszło do ich uszkodzenia. Wiąże się to z koniecznością wykonywania regulowania, diagnozowania tych elementów oraz badania ich niezawodności.
Powrót do spisu treściPowrót do spisu treści
Niezawodność maszyn i urządzeń
Niezawodność jest to właściwość maszyn/urządzeń, która daje informacje na temat poprawności pracy oraz spełnienia wszystkich powierzonych funkcji i czynności, w okresie, w jakim miały pracować oraz w określonych warunkach eksploatacji. Podstawą do dopuszczenia danej maszyny/urządzenia jest ocena niezawodności.
Powrót do spisu treściPowrót do spisu treści
Przyczyny zainteresowania niezawodnością
Zagadnienie niezawodności maszyn od wielu lat jest jednym z podstawowych kryteriów oceny funkcjonalności urządzenia. Jest to spowodowane faktem, że nabywca oczekuje, aby pozyskana przez niego maszyna była dyspozycyjna, czyli gotowa do pracy o każdej porze. Współczesne maszyny posiadają wysoki wskaźnik dyspozycyjności. Osiągane jest to dzięki zastosowaniu dobrych materiałów, które są drogie, a to powoduje wzrost ceny maszyny. Kupując taką maszynę, każdy by chciał, aby pracowała przez bardzo długi czas bez napraw, lecz z powodu eksploatowania się części, jest to niemożliwe. Każda maszyna potrzebuje konserwacji, a aby być świadomym okresów w jakich należy je przeprowadzić, przeprowadza się analizy niezawodności, czyli prognozowanie ewentualnych uszkodzeń.
Powrót do spisu treściPowrót do spisu treści
Sformułowanie poprawności funkcjonowania obiektu
Poprawność funkcjonowania obiektu zależy od jego stanu. Stan zależy od przeszłości obiektu, a jego znajomość jest potrzebna do prognozowani zachowania obiektu w przyszłości. W celu określenia stanu maszyny wprowadzono określenia klasy stanów. Klasy te można podzielić na „klasę stanu zdatności” i „klasę stanu niezdatności”. Tak prosty podział pozwala jasno określić stan maszyny.
Aby móc powiedzieć, że maszyna znajduje się w stanie zdatności, należy ją skontrolować - czy wartości mierzonych parametrów lub cech stanu znajdują się w granicach wartości dopuszczalnych, czyli nie przekroczyły wartości granicznych. Natomiast, jeśli chociaż jeden parametr lub cecha znajdują się poza dopuszczalną granicą, to maszyna znajduje się w stanie niezdatności. Ze względu na potrzebę oceny możliwości realizacji zadań przez maszynę, wyróżniono dodatkowo zdatność funkcjonalną oraz zdatność zadaniową. Zdatność funkcjonalna oznacza, że maszyna jest zdolna do realizowania zadanej funkcji zgodnie z przeznaczeniem i zgodnie z założeniami dokumentacji normatywno‑technicznej. Natomiast zdatność zadaniowa mówi nam, że maszyna jest gotowa do realizacji zadań w wyznaczonych warunkach eksploatacji oraz przy wymuszeniach sterujących i zmiennych obciążeniach.
W celu określenia stanu maszyny należy wykonać badania diagnostyczne, czyli zespół czynności zawierających badania i wnioski diagnostyczne. Działania te powinny być odpowiednio zaplanowane, czyli powinny być określone elementy, które poddawane są kontroli, sposób badania oraz niezbędne przyrządy do wykonania badań. Badania różnią się od siebie sposobem realizacji, celem itp. Z tego powodu dokonano podziału.
Ze względu na cel kontroli wyróżniamy diagnozowanie użytkowe oraz diagnozowanie obsługowe. Diagnozowanie użytkowe ma na celu jakościowe lub ilościowe określenie zdatności obiektu do użycia. Natomiast, jeśli chodzi o diagnozowanie obsługowe, to jego celem jest lokalizacja uszkodzonego elementu i podanie przyczyny uszkodzenia, kontrola profilaktyczna, kontrola prognostyczna oraz samokontrola, czyli ocena stanu systemu diagnostycznego
Ze względu na warunki realizacji wyróżniamy:
kontrola aktywna (testowanie) – ocena stanu obiektu na podstawie obserwacji jego reakcji na zadane wymuszenia,
kontrola pasywna – ocena stanu obiektu bez oddziaływań zewnętrznych,
kontrola statyczna – ocena stanu obiektu w ustalonych warunkach,
kontrola dynamiczna – ocena stanu obiektu na podstawie obserwacji procesów przejściowych.
Ze względu na czas kontroli wyróżniamy:
kontrola ciągła – informacja uzyskiwana jest bez przerwy, w czasie pracy obiektu,
kontrola okresowa – diagnozy wypracowuje się we wcześniej ustalonym czasie,
kontrola bieżąca – rozpoczynana, losowo.
Do najczęściej stosowanych procesów diagnostycznych zaliczamy:
Kontrolę funkcjonalną,
Kontrolę stanu,
Lokalizację uszkodzeń.
Powrót do spisu treściPowrót do spisu treści
Miary niezawodności elementów nienaprawialnych
Elementy nienaprawialne są to części lub zespoły, których naprawa, w przypadku uszkodzenia, jest technicznie niemożliwa lub nieopłacalna. Parametrami opisującymi niezawodność tych elementów są: Oczekiwany resurs poprawnej pracy, czyli czas, w jakim element będzie pracował bez awarii. Pozwala on ocenić jakość konstrukcji i trwałość materiałów z jakich został zbudowany. Odchylenie standardowe resursu poprawnej pracy to miara rozproszona, charakteryzująca jakość technologii produkcji i jakość eksploatacji urządzeń.
Powrót do spisu treściPowrót do spisu treści
Funkcja niezawodności i funkcja zawodności
Uszkodzenia elementów posiadają głównie charakter losowy, a przewidzieć je można jedynie za pomocą odpowiednich rozkładów prawdopodobieństwa. Oczekiwany czas poprawnej pracy urządzeń można przedstawić za pomocą parametrów eksploatacyjnych, np. przebieg maszyny lub czas pracy. W takim przypadku parametry te będą oznaczać odpowiednio zmienne losowe (indywidualna miara pracy) (czas). Wykorzystując te dwie zmienne możemy stworzyć funkcję niezawodności oraz funkcję zawodności .
l - miara eksploatacji,
P(l) - prawdopodobieństwo wystąpienia awarii
Na wykresie przedstawiono funkcję malejącą oznaczoną kolorem czerwonym jako R od el oraz zieloną funkcję rosnącą F od el. Na osi pionowej znajduje się skala od zera do jeden, na poziomej od zera do małego el. Funkcja zawodności to prawdopodobieństwo wystąpienia uszkodzenia obiektu w przedziale miary eksploatacji od zera do małego el. Jest dystrybuantą miary eksploatacji i w sensie probabilistycznym oznacza prawdopodobieństwo tego, że zmienna losowa duże el ma wartość mniejszą od małego el takiego że R od małego el równe jest P od dużego el większego lub równego małemu el. Funkcja zawodności jest funkcją niemalejącą. Dla zwiększenia miary eksploatacji obiektu wzrasta prawdopodobieństwo jego uszkodzenia.
Funkcja niezawodności to prawdopodobieństwo niewystąpienia w przedziale miary eksploatacji od zera do małego el. Jest to dystrybuanta miary eksploatacji do jedności i w sensie probabilistycznym oznacza prawdopodobieństwo tego, że zmienna losowa duże elma wartość nie mniejszą od małego el takiego, że R od małego el równe jest P od dużego el większego lub równego małemu el. Funkcja niezawodności jest funkcją nierosnącą. Dla zwiększenia miary eksploatacji obiektu maleje prawdopodobieństwo jego nie uszkodzenia.
Powrót do spisu treściPowrót do spisu treści
Trwałość elementów nienaprawialnych
Trwałość elementów nienaprawialnych jest to oczekiwany czas, przez jaki element będzie pracował poprawnie i spełniał wszystkie funkcje w zdefiniowanych wcześniej warunkach eksploatacyjnych. Trwałość elementów opiera się przede wszystkim na prawdopodobnej liczbie cykli roboczych wykonanych przed rozpoczęciem wykazywania oznak zmęczenia. Po tym czasie występuje konieczność wymiany elementu. Mówiąc o trwałości elementów należy wspomnieć, że zmęczenie materiału jest zjawiskiem przebiegającym w sposób nieregularny. Oznacza to, że jeden element po przekroczeniu czasu pracy będzie nadawał się do użytku jeszcze przez jakiś czas a inny nie. Dzieje się tak, ponieważ trwałość określa na podstawie czasu pracy bez objawów zmęczenia przez 90% badanych elementów w określonych warunkach.
Na trwałość elementów wpływ mają najróżniejsze czynniki, a należą do nich:
Sposób przechowywania,
Sposób zabezpieczenia podczas transportu,
Sposób montażu,
Środowisko pracy,
Sposób serwisowa.
Powrót do spisu treściPowrót do spisu treści
Intensywność i częstość uszkodzeń
Intensywność uszkodzeń jest to prawdopodobieństwo wystąpienia uszkodzenia w ciągu jednostki czasu pracy w określonych warunkach. Określa się ją w sposób matematyczny, lecz nie da się odnaleźć dokładnej wartości, a jedyne wartość przybliżoną.
Jak już wspominaliśmy, intensywność uszkodzeń to prawdopodobieństwo wystąpienia uszkodzenia w przedziale czasu. Zapis funkcji intensywności uszkodzeń w sposób matematyczny wygląda następująco:
Pierwsze wykresu funkcji intensywności uszkodzeń to były krzywe siodłowe.
Patrząc na wykres można było stwierdzić, że podczas pierwszego okresu, uszkodzeń wczesnych, występowało dużo uszkodzeń, ale z upływem czasu ilość ta malała. Taki sposób przebiegu funkcji na początku był spowodowany słabym wykonaniem oraz wadliwością elementów. W drugim okresie, normalnej eksploatacji, liczba uszkodzeń jest stała. Uszkodzenia w tym okresie były spowodowane najczęściej przez przeciążenia oraz niepoprawną eksploatację. Trzeci okres to okres zużycia. Wzrost liczby uszkodzeń w tym okresie nie powinien dziwić. Uszkodzenia w tym okresie spowodowane były zmęczeniem elementów.
Obecnie, dzięki większej dokładności wykonania, wykres przybrał kształt krzywej grzbietowej.
Wykres funkcji intensywności uszkodzeń. Krzywa grzbietowa. Grzbiet to okres uszkodzeń wczesnych i, jak widać, w początkowych etapach eksploatacji one nie występują. Wady produkcyjne wychodzą dopiero później.
Powrót do spisu treściPowrót do spisu treści
Przykłady uszkodzeń maszyn i urządzeń
Jedną z wielu przyczyn powstawania uszkodzeń maszyn i urządzeń jest tarcie. Podczas tarcia o siebie elementów ruchomych, oprócz zjawisk cieplnych, występują procesy niszczące wierzchnią warstwę materiału i powstają ubytki materiału.
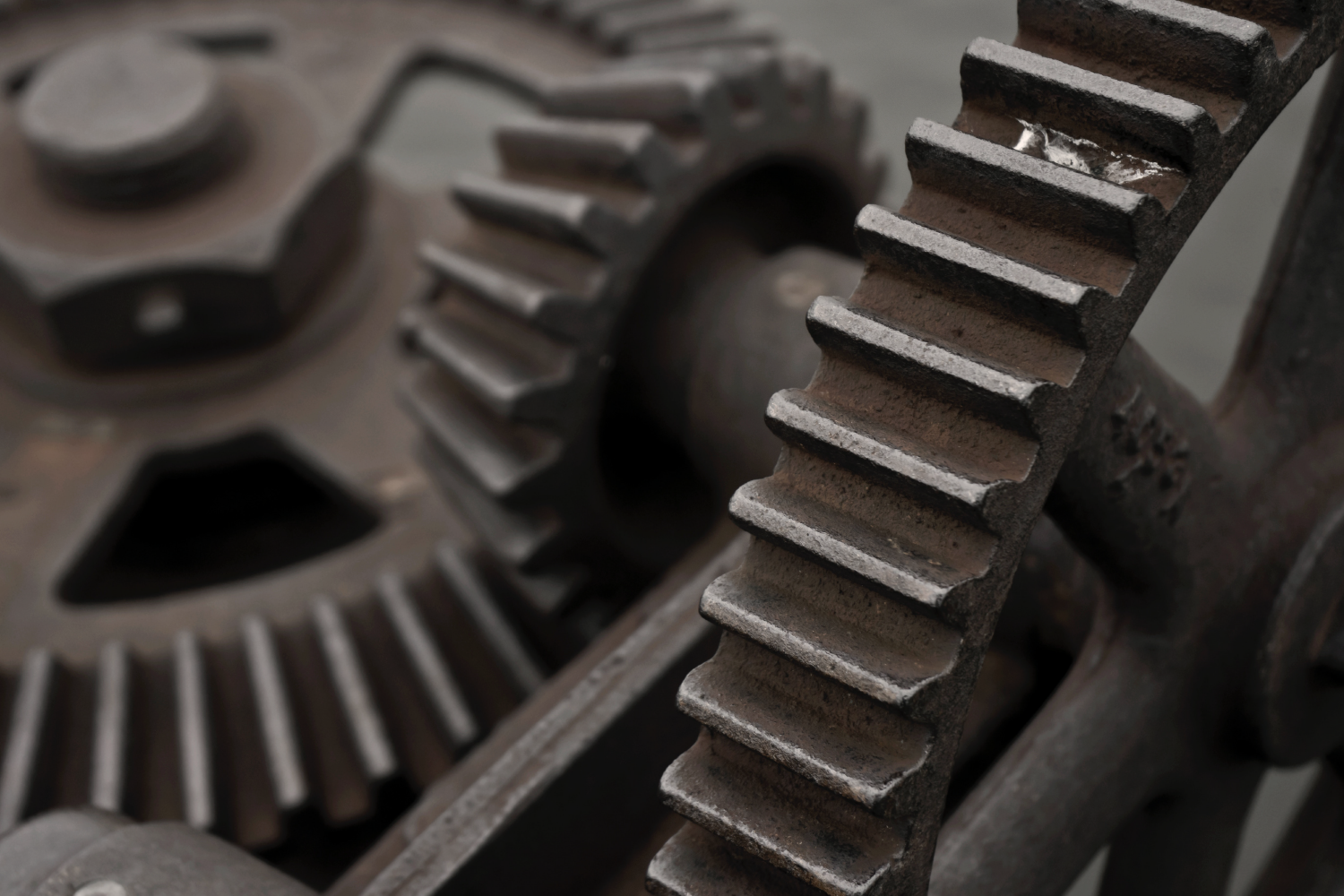
Następną przyczyną występowania usterek są wady materiału. Głównym powodem powstawania tych wad jest niewłaściwie przeprowadzony proces przygotowania materiału wyjściowego do produkcji oraz niewłaściwie przeprowadzony proces wstępnego kształtowania materiału. Wadami materiału mogą być:
Łuski,
Zmarszczki,
Pęknięcia,
Ubytki,
Rozdarcia,
Rozszczepienia,
Zawalcowania,
Wgnioty.
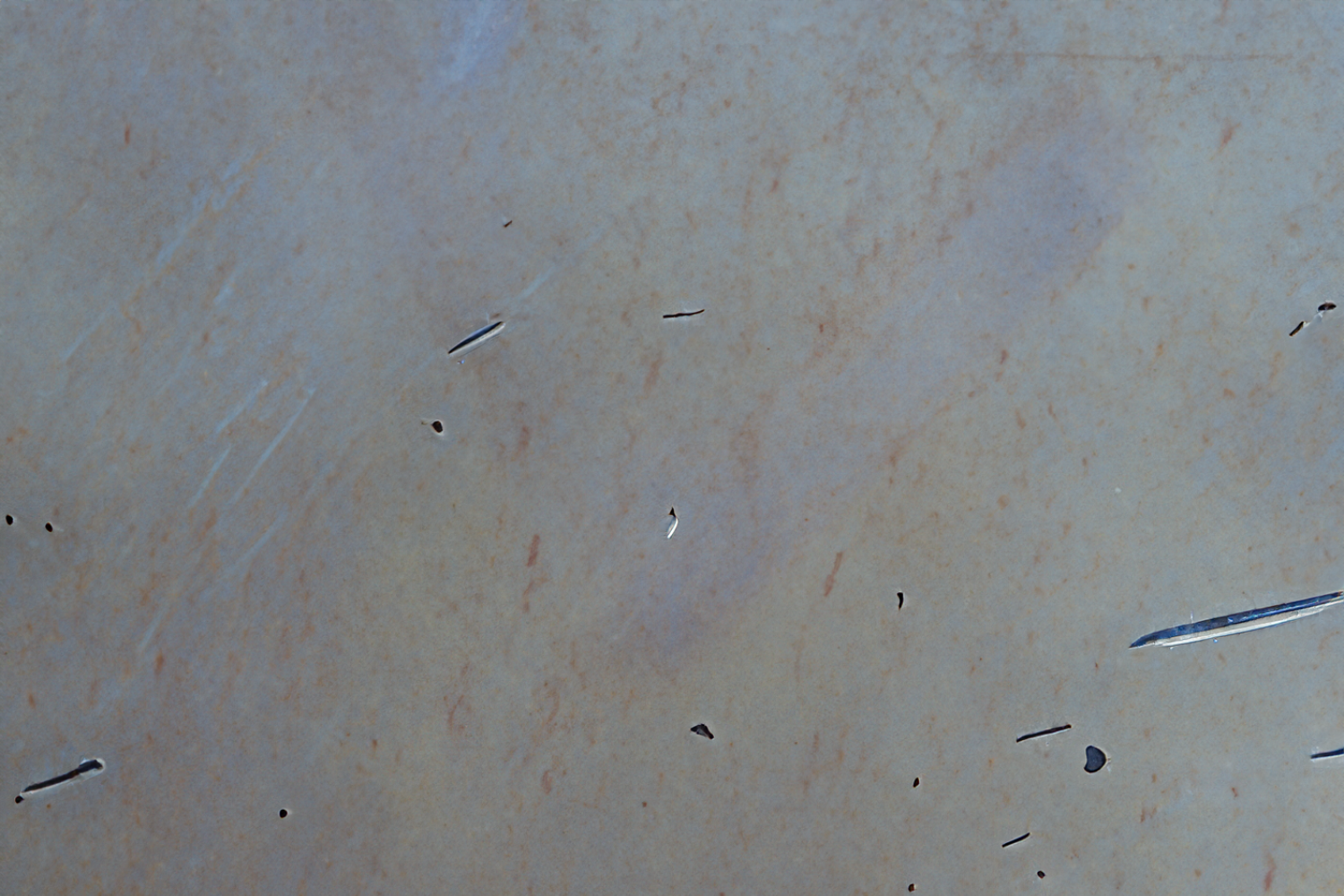
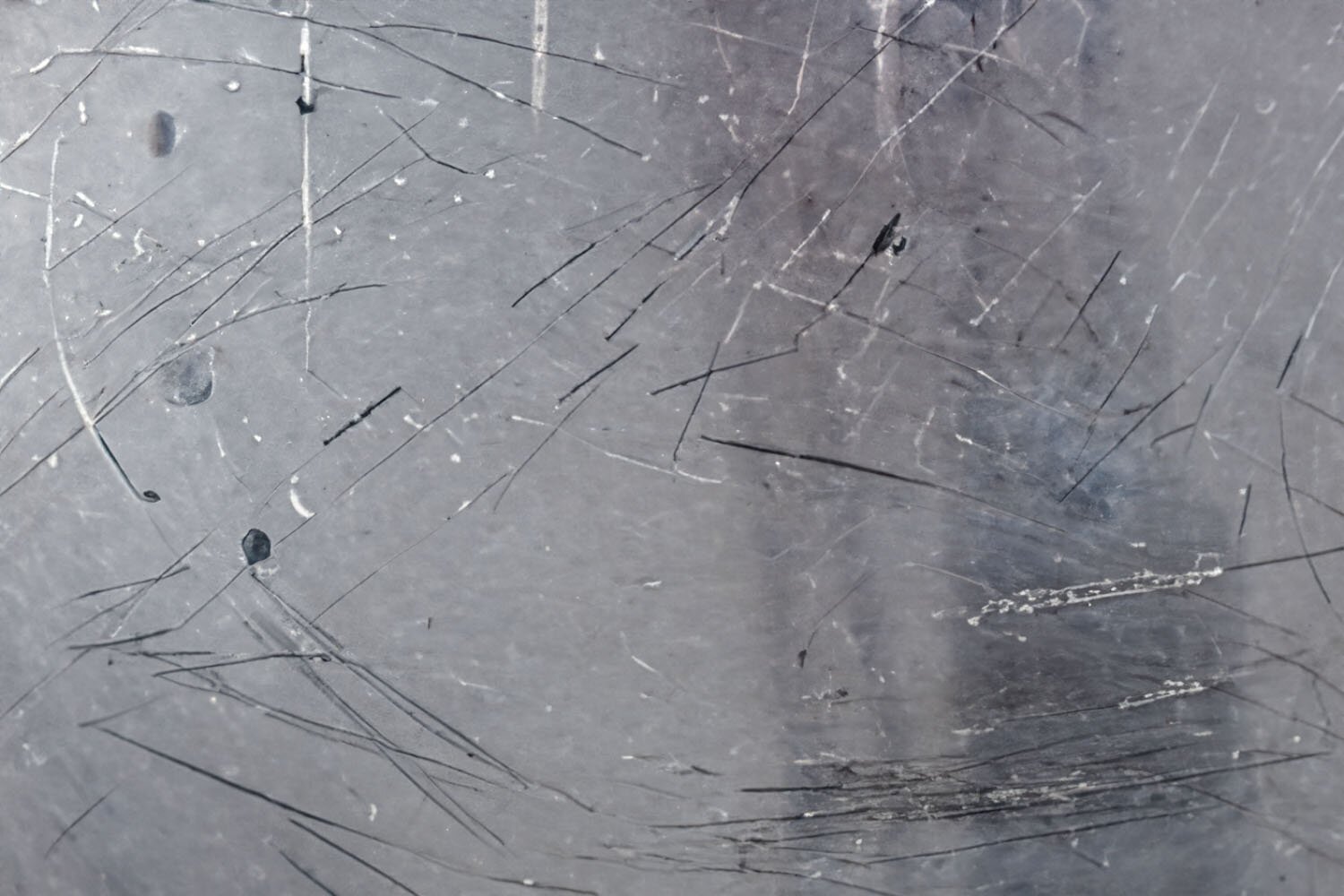
Kolejną przyczyną powstawania usterek jest zmęczenie materiału. Zmęczenie to proces powstawania i rozwoju uszkodzeń spowodowany przez długotrwałe obciążeniami części maszyn. Przykładowymi uszkodzeniami powstałymi w skutek zmęczenia materiału są:
Pęknięcia,
Zmiana geometryczna,
Zmiana właściwości fizycznych.
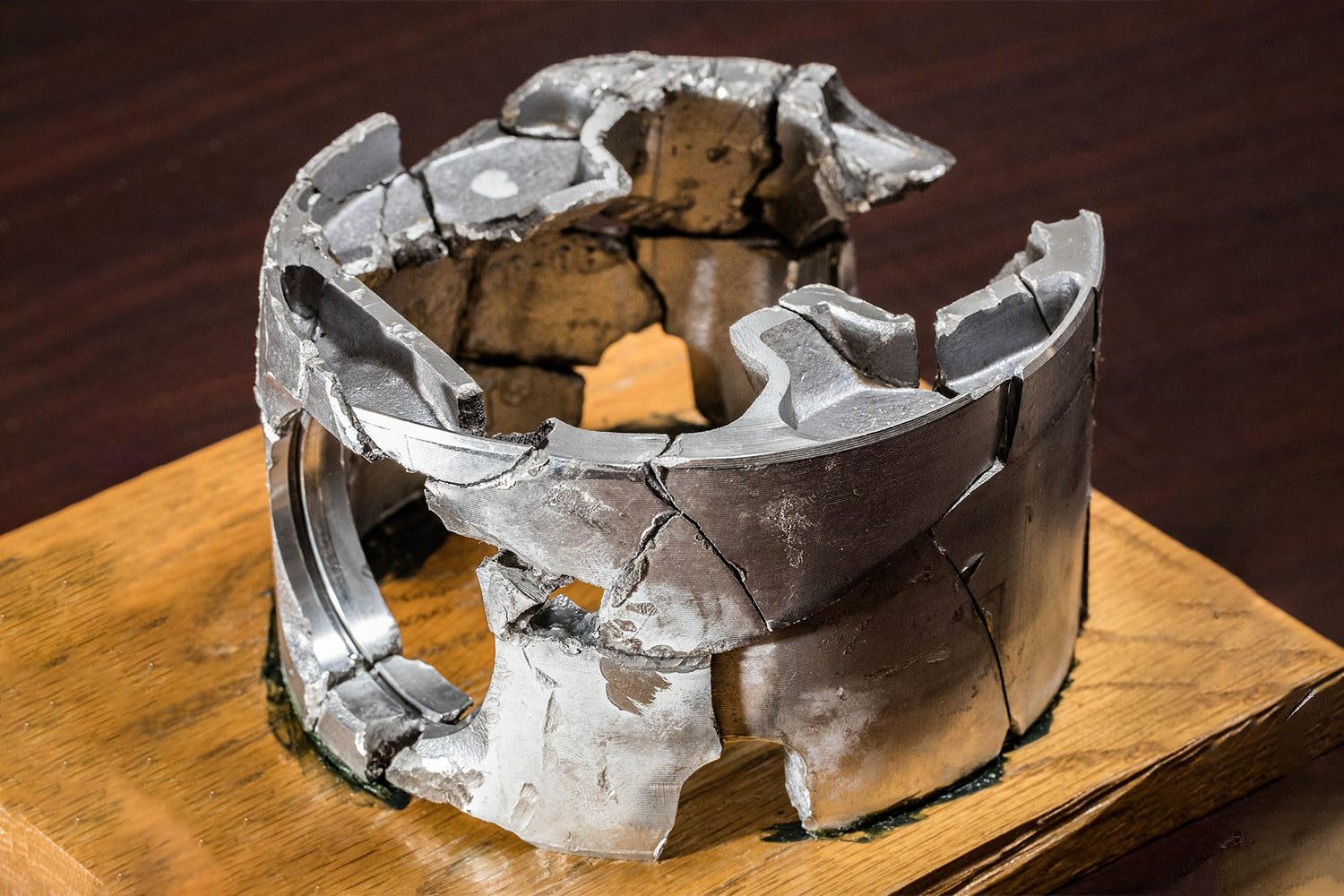
Niewłaściwy montaż również może prowadzić do poważniejszej usterki lub może sprawić, że maszyna w dalszym ciągu nie będzie zdolna zadaniowo. Przyczynami niewłaściwego montażu mogą być:
Brak odpowiedniej wiedzy,
Brak doświadczenia,
Niedokładność montera,
Rozkojarzenie montera.
Powrót do spisu treściPowrót do spisu treści