Montaż i obsługa prostych elementów maszyn i urządzeń
MEC.06. Montaż i obsługa prostych elementów maszyn i urządzeń - Pracownik pomocniczy mechanika 932916
Montaż i demontaż prostych elementów maszyn i urządzeń
ATLAS INTERAKTYWNY
Spis treści
Łożyska toczneŁożyska toczne
Łożyska ślizgoweŁożyska ślizgowe
Wały i osieWały i osie
Koła pasowe przekładni cięgnowejKoła pasowe przekładni cięgnowej
Koła zębate przekładni zębatychKoła zębate przekładni zębatych
Przekładnia ciernaPrzekładnia cierna
Połączenia rozłącznePołączenia rozłączne
Połączenia nierozłącznePołączenia nierozłączne
Pasowanie mieszanePasowanie mieszane
Napędy sterująceNapędy sterujące
Montaż i demontaż są niezwykle istotne w dziedzinie inżynierii maszynowej, wpływając na funkcjonowanie, trwałość i bezpieczeństwo maszyn. Poprawne łączenie elementów, zarówno prostych, jak i skomplikowanych, ma kluczowe znaczenie dla wydajności eksploatacyjnej. Montaż gwarantuje poprawne działanie, minimalizując tarcie i zwiększając żywotność. Łożyska toczne i ślizgowe są kluczowymi komponentami minimalizującymi opory i umożliwiającymi płynny ruch. Montaż wałów i osi jest kluczowy dla trwałych konstrukcji, wymagając dokładnego osadzenia i równomiernego obciążenia. Przekładnie przenoszą ruch i moment obrotowy, a montaż kół pasowych oraz zębatych wymaga precyzyjnego dopasowania. Montaż połączeń rozłącznych i nierozłącznych, takich jak spawanie, ma wpływ na trwałość konstrukcji. Montaż podzespołów łączy różne elementy, jak napędy czy układy hydrauliczne, wymagając precyzyjnych narzędzi i pomiarów dla kontroli jakości. Zrozumienie procesów montażu i demontażu jest kluczowe w projektowaniu, budowie i utrzymaniu maszyn.
Łożyska toczne
Łożyska toczne to elementy w maszynach umożliwiające przenoszenie obciążeń i ruchu w sposób efektywny i precyzyjny. Składają się one z dwóch głównych części: pierścienia zewnętrznego oraz wewnętrznego, między którymi znajdują się elementy toczne, takie jak kule lub wałeczki. Dzięki tym elementom, tarcie między poruszającymi się częściami jest znacznie zmniejszone, co umożliwia płynne obracanie się i przemieszczanie.
Montaż łożysk tocznych
Rozpoczyna się od przygotowania powierzchni czopa wału, gniazda łożyska oraz samego łożyska. Wymiarowość i kształt są dokładnie sprawdzane, a ewentualne błędy są eliminowane, aby zapewnić idealne dopasowanie. Podczas montażu, pierścienie łożyska są montowane, a elementy toczne, czyli kule lub wałeczki, są umieszczane w specjalnym koszyczku. W przypadku łożysk stożkowych kontroluje się dokładnie luz między elementami tocznymi, by spełnić wymogi konstrukcyjne. Stosuje się specjalne podkładki dystansowe, aby osiągnąć odpowiednią precyzję. W przypadku łożysk igiełkowych, które nie posiadają pierścieni zewnętrznych, stosuje się wałek montażowy. To narzędzie pozwala precyzyjnie umieścić cienkie wałeczki igiełkowe w łożysku. Dla łożysk stożkowych kluczowym etapem jest dokładne dociśnięcie nakrętek i ich delikatne odkręcenie, co ma istotne znaczenie dla prawidłowej pracy łożyska. Ważnym elementem jest także wybór odpowiednich uszczelnień, które dostarczają im odpowiednią ilość smaru lub oleju. Po zmontowaniu łożyska przeprowadza się test obrotowy, aby potwierdzić, że łożysko działa prawidłowo i nie występują żadne nieprawidłowości.
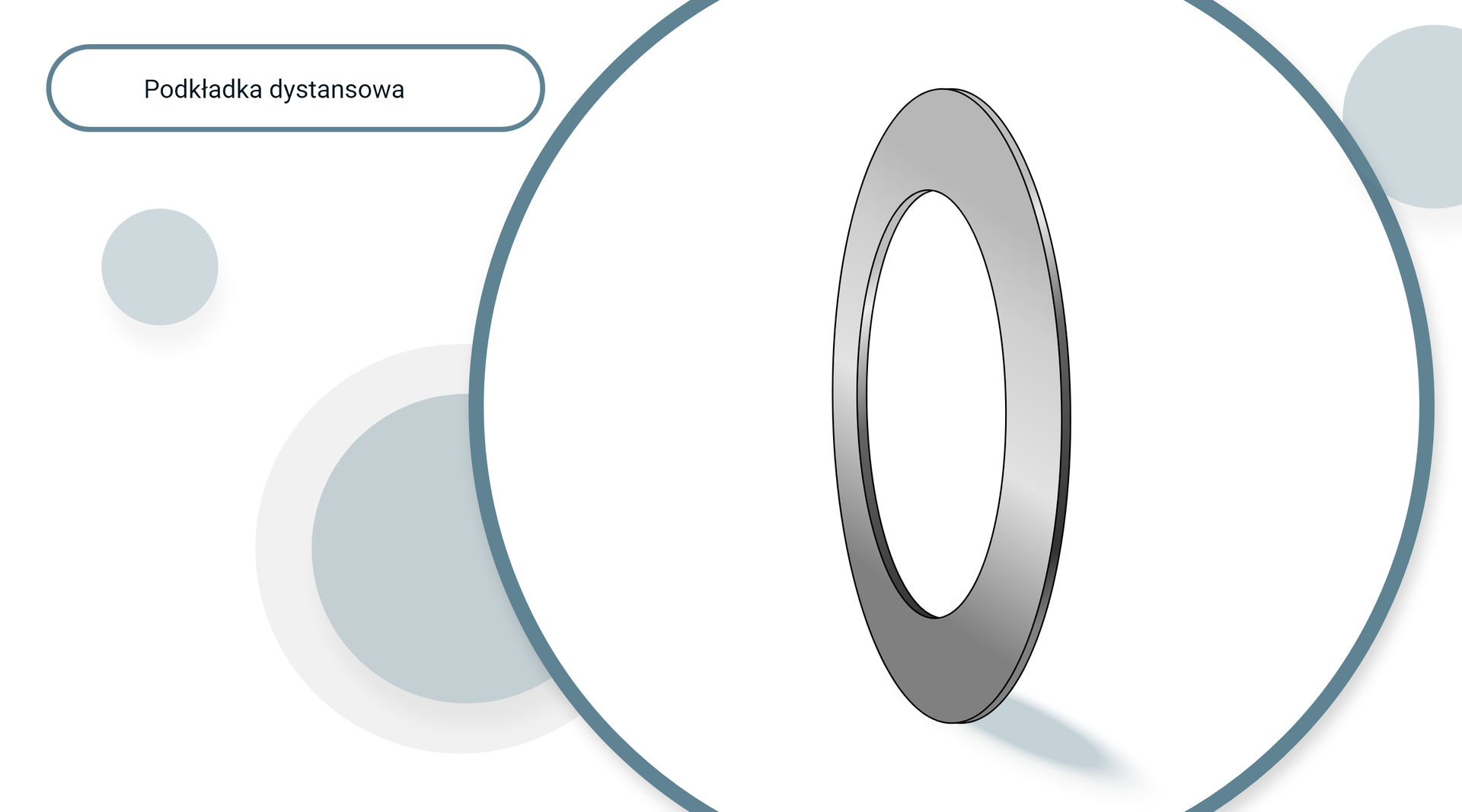
Demontaż łożysk tocznych
W przypadku ściągania łożysk stosuje się ściągacze lub prasy, które utrzymują współosiowość połączenia podczas oddzielania pierścieni łożyska od czopa wału i gniazda. Dla łożysk stożkowych kontrola luzu między elementami tocznymi podczas demontażu jest równie istotna, jak i podczas montażu.
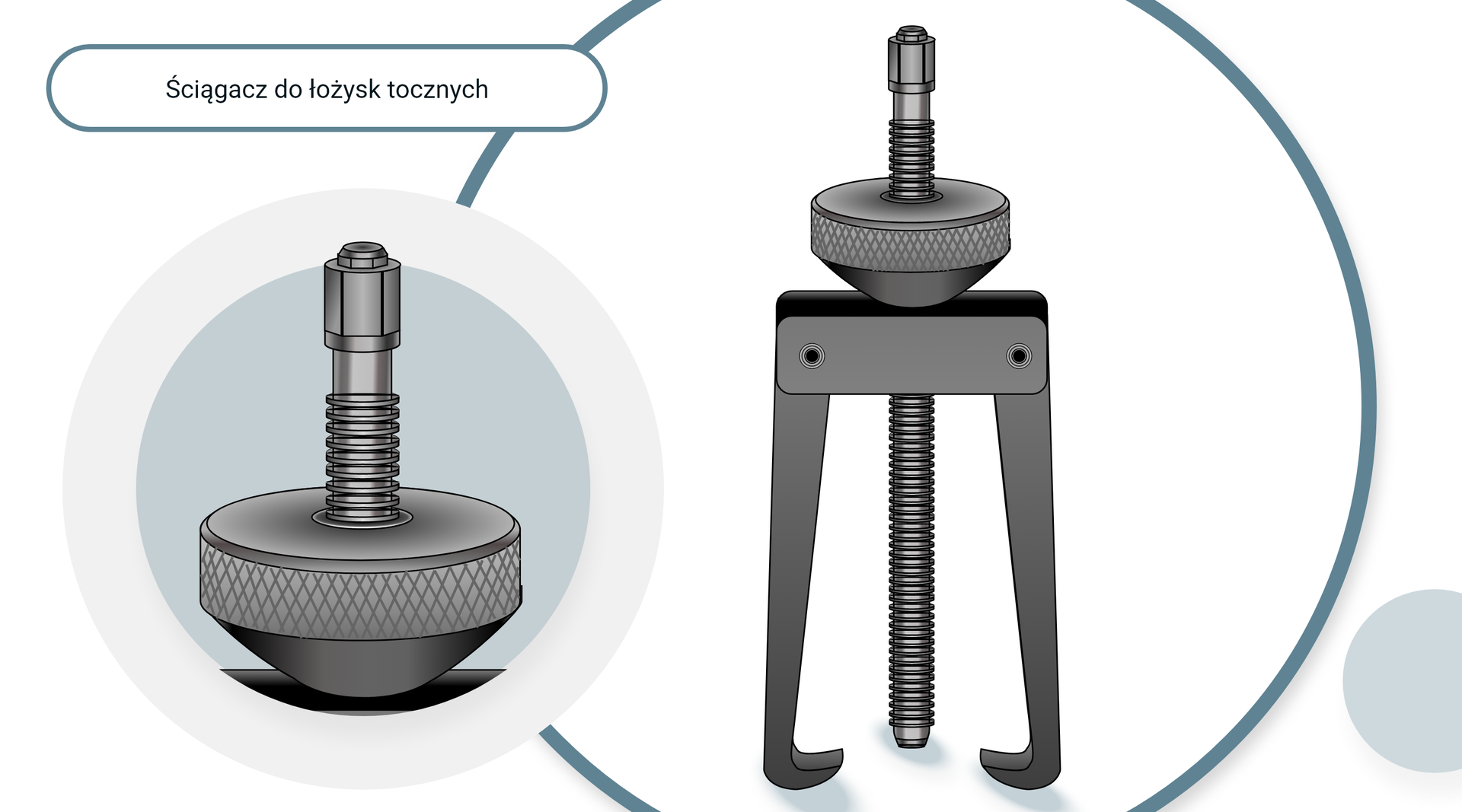
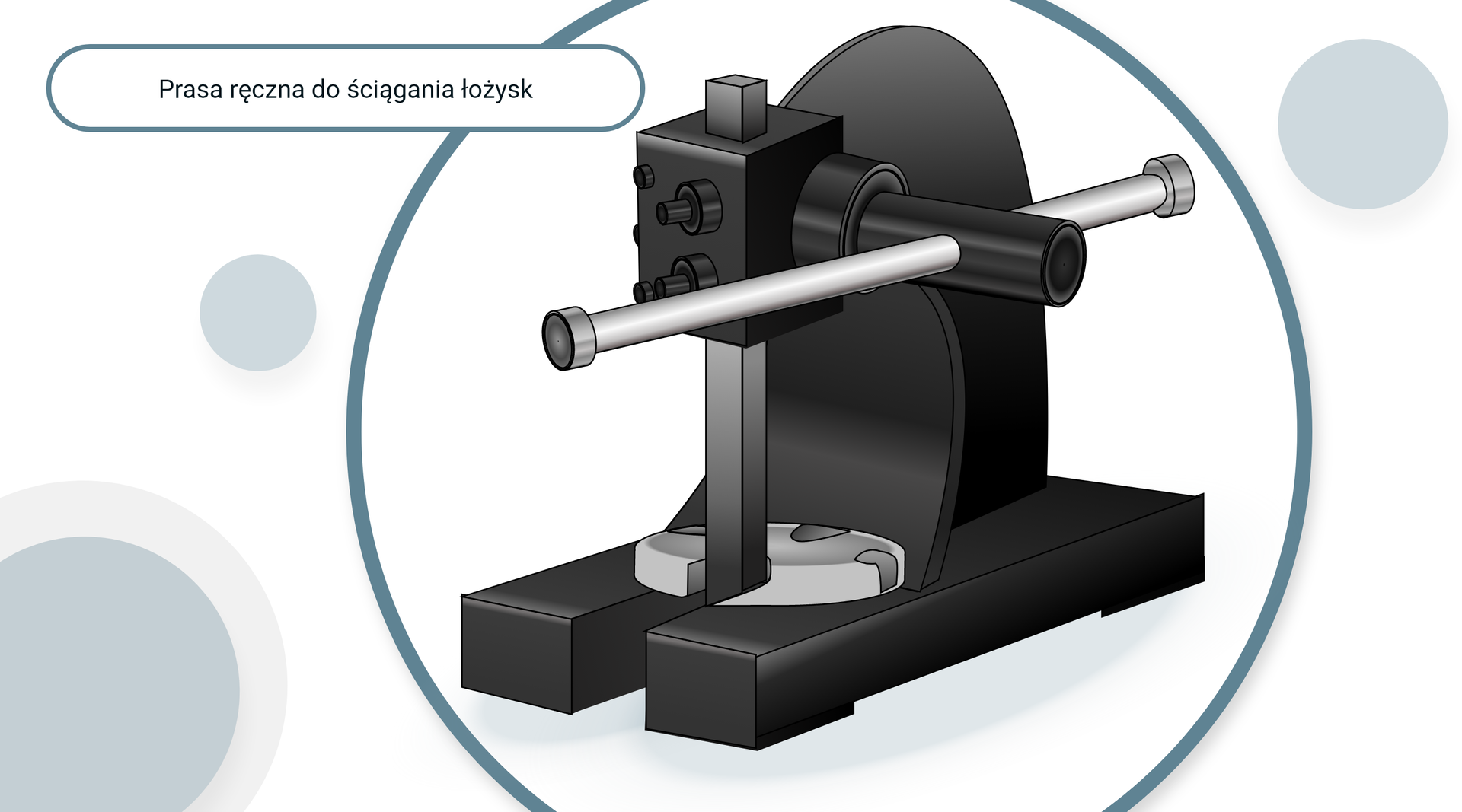
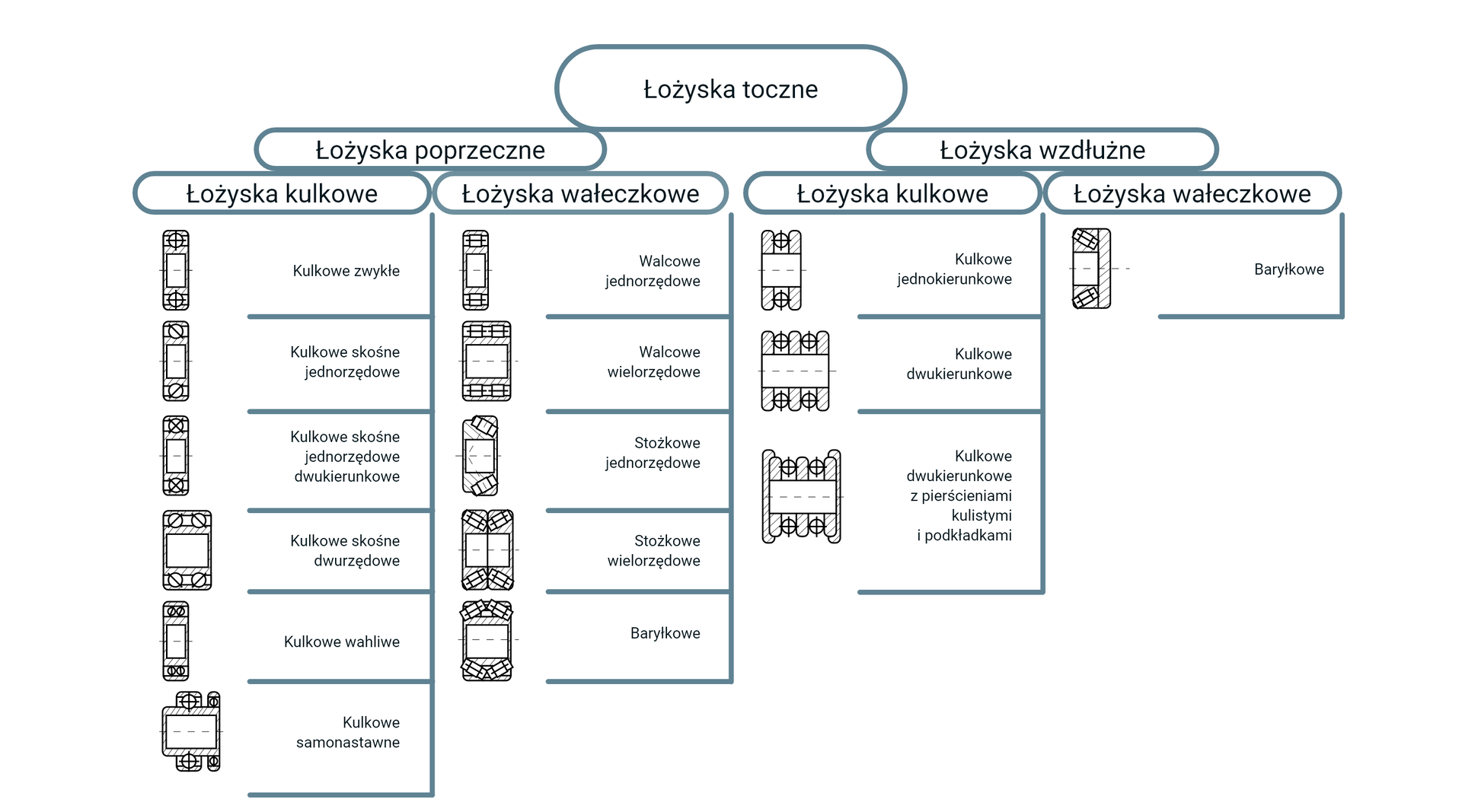

Powrót do spisu treściPowrót do spisu treści
Łożyska ślizgowe
Łożyska ślizgowe to elementy mechaniczne przenoszące ruch i obciążenia w mechanizmach, składające się z panewek i czopów lub sworzni.
Montaż łożysk ślizgowych
Składa się z kilku kroków: przygotowanie powierzchni panewek, czopów i korpusów, montaż panewek w gniazdach korpusów, kontrola odstępów między nimi, łączenie elementów korpusu, zabezpieczenie panewek oraz kontrola stanu powierzchni łożyskowych.
Demontaż łożysk ślizgowych
To proces odwrotny: usunięcie zabezpieczeń, stopniowe oddzielanie panewek od gniazd, kontrola stanu panewek i powierzchni łożyskowych oraz oczyszczenie panewek i gniazd. W obu przypadkach kluczowa jest precyzja w celu zapewnienia prawidłowego działania.
Montaż łożyska ślizgowego zamontowanego na wale wykorbionym
Dzielone łożyska ślizgowe to specyficzny rodzaj działający poprzez tarcie ślizgowe, bez elementów tocznych. Ich montaż na wał korbowy to proces obejmujący oczyszczenie panewek, połączenie podstawy i pokrywy śrubami, osadzenie panewek w gniazdach korpusu, dokręcenie śrub mocujących, kontrolę wymiarów i położenia gniazd łożyskowych oraz zabezpieczenie przed obracaniem się. Demontaż polega na odkręceniu śrub mocujących, usunięciu panewek z gniazd, czyszczeniu i kontroli wymiarów i kształtu gniazd oraz zabezpieczeniu otworów olejowych. Cały proces wymaga precyzji, by zapewnić prawidłowe działanie.
W galerii mediów przedstawiono podział łożysk ślizgowych. W ich skład wchodzą: akcesoria łożyskowe, elementy toczne, łożyska do klimatyzacji, łożyska igiełkowe, łożyska kulkowe samonastawne, łożyska baryłkowe, łożyska kulkowe skośne łożyska, kulkowe wahliwe, łożyska kulkowe wzdłużne, łożyska kulkowe zwykłe, łożyska stożkowe, łożyska walcowe, oprawy łożysk, tuleje ślizgowe i zespoły łożyskowe.
Na grafice interaktywnej przedstawiono elementy składowe łożysk ślizgowych. Tworzą one wypukły półokrąg, natomiast po montażu półokrąg. Po kliknięciu każdego z numerów pojawia się jego nazwa odczytywana przez lektora w nagraniu dźwiękowym.
Numer jeden. Gwint/śruba.
Numer dwa. Występy ustalające.
Numer trzy. Panewka.
Numer cztery. Wgłębienia w obudowie panewki.
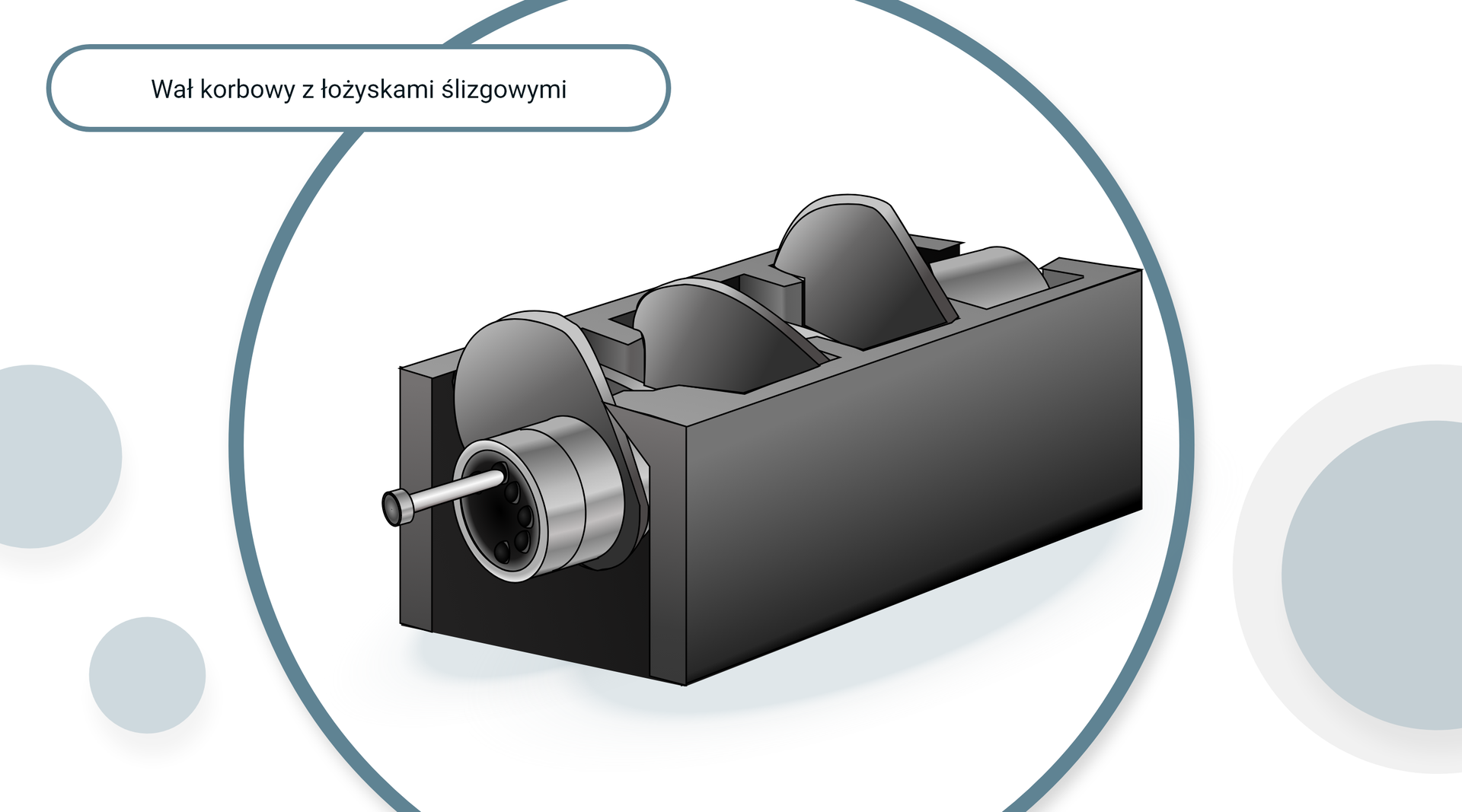
Powrót do spisu treściPowrót do spisu treści
Wały i osie
Montaż wałów i osi w maszynach jest niezwykle ważnym procesem, ponieważ te elementy pełnią istotną rolę w podtrzymywaniu i przekazywaniu ruchu obrotowego oraz wahadłowego. Osie stałe pozostają nieruchome, natomiast osie ruchome obracają się razem z elementami zamontowanymi na nich. W odróżnieniu od osi, wał zawsze jest w ruchu i przenosi momenty obrotowe.
Montaż wałów i osi
Należy zapewnić dokładne i właściwe położenie wałów oraz osi względem innych elementów maszyny. To istotne, aby zapewnić prawidłowe funkcjonowanie i współpracę pomiędzy elementami. Następnie, istotne jest zachowanie odpowiedniej powierzchni przylegania czopa wału do panewek oraz osadzenie osi w otworach. Poprawne luzy promieniowe i poosiowe są kluczowe dla minimalizacji tarcia. W procesie montażu wałów i osi konieczne jest przygotowanie powierzchni poprzez dokładne umycie i oczyszczenie czopów wałów oraz otworów osi. To zapewni lepsze połączenie. Mocowanie to kluczowy krok w procesie montażu. Metoda mocowania może różnić się w zależności od konkretnego przypadku — może to być dociskanie, zgrzewanie, a także wykorzystanie elementów takich jak śruby czy nakrętki. Ważne jest również, aby przeprowadzić testy obrotowe pozwalają zweryfikować, czy elementy pracują poprawnie i czy nie występują niepożądane efekty. W przypadku łączenia dwóch wałów warto sprawdzić współosiowość za pomocą narzędzi pomiarowych. Jest to szczególnie istotne, gdy wały są połączone przez sprzęgło. Należy korzystać z odpowiednich narzędzi, dbać o ergonomiczne warunki pracy i przestrzegać przepisów BHP.
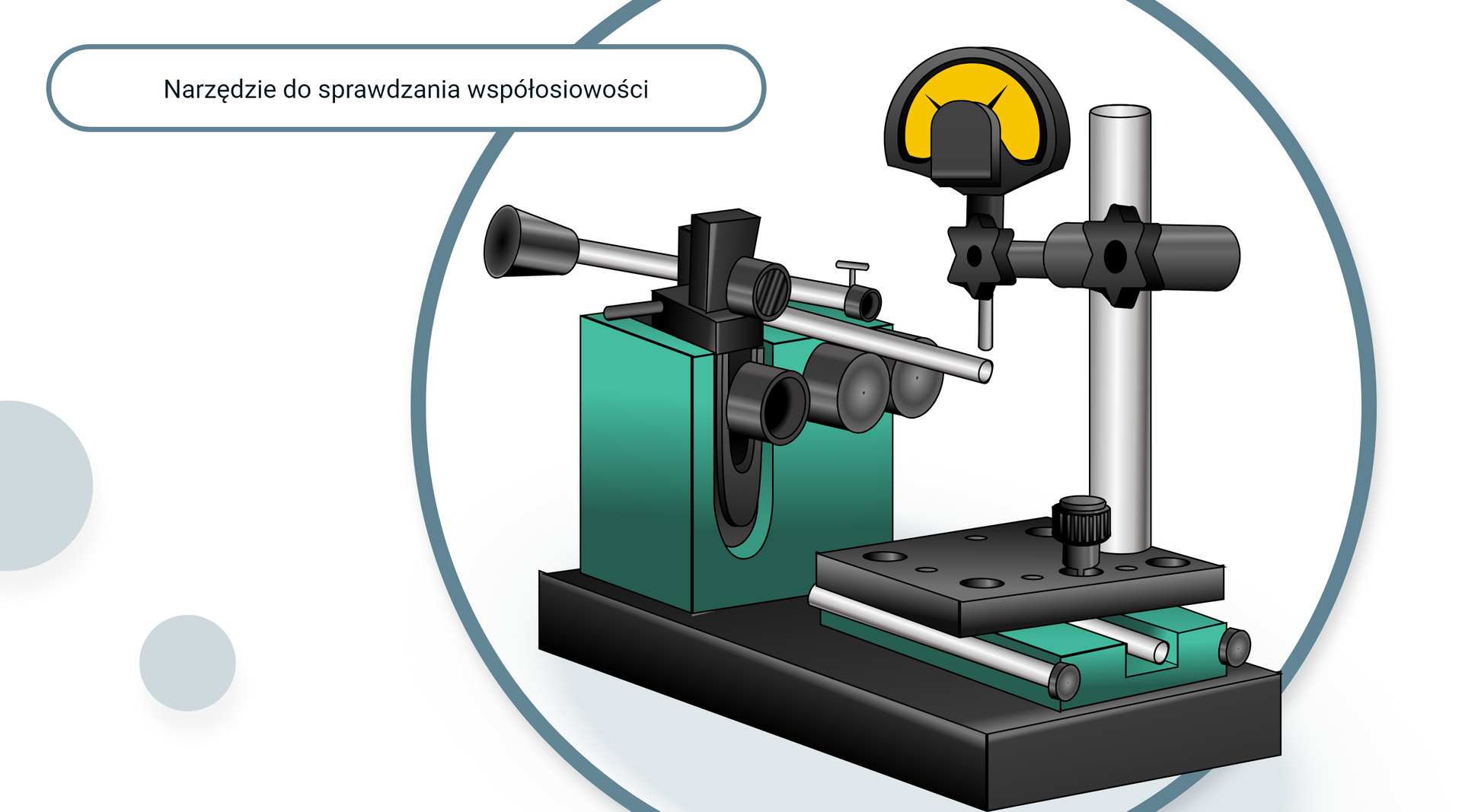
Czopy
Fragmenty osi lub wałów służące do osadzania różnych komponentów maszyn, takich jak łożyska. Istnieją dwie główne kategorie czopów: czopy ruchowe, które współpracują z obracającymi się elementami, oraz czopy spoczynkowe, które współpracują z elementami trwale zamocowanymi do wału lub osi. Czopy mogą znajdować się na końcu wału lub w jego środkowej części. Podział wałów według rodzaju czopów:
Wały kształtowe: Posiadają zmienny przekrój poprzeczny. Ich czopy mogą być ruchowe lub spoczynkowe w zależności od potrzeb.
Wały pełne: Nie posiadają otworu wzdłużnego. Czopy tych wałów mogą być ruchowe lub spoczynkowe, zależnie od ich funkcji.
Wały drążone: Posiadają otwór wzdłużny. Ich czopy zazwyczaj są ruchowe i umieszczone wewnątrz otworu, co pozwala na bardziej złożone zastosowania.
Wały proste: Osie są proste i nie wykazują krzywizny. Czopy wałów prostych mogą być ruchowe lub spoczynkowe, zależnie od współpracy z obracającymi się lub stałymi elementami.
Wały korbowe: Charakteryzują się krzywizną lub wypustami na powierzchni. Czopy tych wałów zazwyczaj są ruchowe, ponieważ są wykorzystywane do przekształcania ruchu postępowo‑zwrotnego na ruch obrotowy.
Wały dwupodporowe: Posiadają dwa punktowe podparcia, co zwiększa ich stabilność. Rodzaj czopów zależy od zastosowania, mogą być ruchowe lub spoczynkowe.
Wały wielopodporowe: Charakteryzują się wieloma punktowymi podparciami. Czopy tych wałów mogą być ruchowe lub spoczynkowe, w zależności od budowy i celu użytkowania.
Wały sztywne: Wykazują dużą sztywność, minimalne odkształcenia pod obciążeniem. Czopy wałów sztywnych przyjmują różne formy, dostosowane do wymagań konstrukcyjnych.
Wały podatne: Ulegają elastycznym odkształceniom, takim jak gięcie lub skręcanie. Rodzaj czopów zależy od elastyczności, a wały te mogą mieć czopy ruchowe lub spoczynkowe, zależnie od celu i elastyczności.
Na grafice znajduje się schemat sprawdzania położenia wałów. Istnieją 2 sposoby: pierwszy to sprawdzanie współosiowości wałów, a drugi to sprawdzanie położenia względem powierzchni podstawowych. Do obu pomiarów wykorzystuje się inne narzędzia.
Powrót do spisu treściPowrót do spisu treści
Koła pasowe przekładni cięgnowej
Przekładnie cięgnowe są mechanizmami wykorzystującymi ruch linearny lub obrotowy cięgien lub pasów do przenoszenia napędu między dwoma lub więcej elementami. Stosuje się je w celu zmiany prędkości obrotowej, kierunku ruchu, lub przenoszenia momentu obrotowego między różnymi elementami maszyn i urządzeń.
Montaż przekładni cięgnowej obejmuje umieszczenie elementów ruchomych, takich jak koła zębate i wałki, na odpowiednich osiach. Linki cięgnące są przytwierdzane do elementów ruchomych, z napięciem zapewniającym skuteczną transmisję ruchu. Montaż kończy się testami, które sprawdzają płynność ruchu i precyzję działania.
Demontaż przekładni cięgnowej — należy odczepić linki cięgnące i usunąć elementy ruchome, takie jak koła zębate, z odpowiednimi działaniami, takimi jak odkręcanie śrub. Jeśli przekładnia ma obudowę, trzeba ją otworzyć. Elementy mocujące są usuwane, a także inne komponenty pomocnicze. Elementy uszkodzone są demontowane, a po dokładnym oczyszczeniu i konserwacji można przystąpić do testów, aby upewnić się, że przekładnia działa zgodnie z oczekiwaniami.
Rodzaje kół pasowych wykorzystywanych w przekładniach cięgnowych:
Koła gładkie: Koła pasowe o całkowicie gładkiej powierzchni. Służą do przekazywania napędu przy pomocy naciągniętego pasa, który przylega do ich powierzchni. Wykorzystywane w prostych przekładniach cięgnowych, gdzie nie jest wymagane dokładne przenoszenie momentu obrotowego.
Koła z pojedynczym rowkiem: Posiadają jeden rowek na swojej powierzchni, do którego pas lub łańcuch jest naciągnięty. Wykorzystywane w wielu różnych aplikacjach, w których konieczne jest przekazywanie napędu, jak w wózkach widłowych czy przenośnikach taśmowych.
Koła wielorowkowe: Charakteryzują się posiadaniem kilku równoległych rowków na powierzchni. Pozwalają na przenoszenie większej ilości napędu lub zastosowanie różnych rodzajów pasów lub łańcuchów. Wykorzystywane w aplikacjach wymagających większej wydajności przekładni.
Koła zębate: Posiadają zęby na swojej powierzchni, które precyzyjnie wpasowują się w odpowiednie zęby pasa lub łańcucha. To rozwiązanie pozwala na dokładne przenoszenie momentu obrotowego i jest często wykorzystywane w przekładniach cięgnowych, gdzie istotne jest zachowanie stałego przełożenia, np. w maszynach tekstylnych czy drukarkach.
Powrót do spisu treściPowrót do spisu treści
Koła zębate przekładni zębatej
Koło zębate to element mechaniczny, który posiada wycięte, ściśle ukształtowane zęby, które wchodzą w interakcję z zębami innego koła zębatego lub przekładni zębatej. Kształt i układ zębów w kołach zębatych są projektowane tak, aby efektywnie przenosić moment obrotowy oraz ruch między elementami mechanicznymi. Koła zębate są niezbędne w układach przekładni, ponieważ umożliwiają zmianę prędkości obrotowej, kierunku ruchu oraz momentu obrotowego. Przekładnia zębata to rodzaj przekładni mechanicznej, gdzie ruch i moment obrotowy są przekazywane poprzez współdziałanie zębów na powierzchniach kół zębatych. Poszczególne zęby na kole zębatym łączą się z odpowiednimi zębami na innych kołach, tworząc łączność poprzez zazębianie.
Montaż przekładni zębatej to skomplikowany proces, który obejmuje umieszczanie osi wałków oraz montaż kół zębatych. Koła powinny być zamontowane prostopadle do osi wałków, a osie wałków powinny być równoległe. Wartość odległości między osiami powinna być dostosowana do średnic podziałowych kół zębatych. Podczas montażu, elementy są precyzyjnie dostosowywane i napięte, a testy są przeprowadzane w celu zapewnienia poprawnego ruchu i precyzji przekładania. Proces montażu zależy od rodzaju korpusu, typu łożysk oraz wymaga dokładnych pomiarów i dostosowań. Po montażu kół zębatych wykonuje się testy, takie jak sprawdzanie bicia promieniowego i czołowego kół zębatych, aby upewnić się o poprawności działania przekładni.
Demontaż przekładni zębatej wymaga odłączenia kół zębatych, odkręcenia osłon oraz usunięcia elementów mocujących. Następnie elementy ruchome, czyli koła zębate, są rozmontowywane, a cała procedura wymaga dokładności i uwagi.
Podział kół zębatych ze względu na rodzaj przekładni zębatej:
Koło zębate walcowe: To koło zębate, którego zęby są proste i znajdują się prostopadle do osi koła. Jest ono wytwarzane z wałka przy pomocy obróbki kształtowej lub obwiedniowej. Koła zębate walcowe są podstawowym elementem w przekładniach zębatych walcowych. Mogą mieć różne przeznaczenie, od zmiany prędkości, do zmiany kierunku obrotu lub przekazywania momentu obrotowego.
Koło zębate stożkowe: To koło zębate o zębach w kształcie stożka. Koła te są używane w przekładniach stożkowych, gdzie osie wałków napędzanego i napędzającego przecinają się pod kątem prostym. Przekładnie stożkowe pozwalają na przenoszenie napędu pod różnymi kątami. Koła zębate stożkowe są skonstruowane tak, aby przenosić duże obciążenia i pracować sprawnie oraz cicho.
Koło zębate ślimakowe: Koło to jest częścią przekładni ślimakowej. Przekładnie te składają się z koła ślimakowego (śruba ślimakowa) oraz koła zębatego (koło ślimakowe). Zęby koła zębatego łączą się liniowo z nawojem ślimaka. Dzięki tej konstrukcji, przekładnie ślimakowe są zdolne do przenoszenia dużych obciążeń i pozwalają na duże zmiany prędkości oraz momentu obrotowego.
Powrót do spisu treściPowrót do spisu treści
Przekładnia cierna
Przekładnia cierna to rodzaj przekładni mechanicznej, w której ruch i moment obrotowy przenoszone są poprzez połączenie cierne między dwoma elementami. W momencie dociskania tych elementów powstaje siła tarcia, która przenosi napęd. Działanie przekładni ciernych opiera się na współpracy zębów lub powierzchni elementów. Siła tarcia generowana między nimi przekazuje moment obrotowy. W skład przekładni ciernych wchodzą:
Koło cierne napędzane — przenosi ruch i moment obrotowy.
Koło cierne napędzające — odbiera ruch i moment, przekazując go dalej.
Siła docisku — dociska koła ciernego do siebie, tworząc połączenie cierne i umożliwiając przeniesienie napędu.
W porównaniu do innych przekładni mechanicznych mają większe reakcje łożyskowe oraz brak stałości przełożenia z powodu poślizgu.
Powrót do spisu treściPowrót do spisu treści
Połączenia rozłączne
Połączenia rozłączne to rodzaj mechanicznych połączeń, które umożliwiają chwilowe oddzielenie elementów lub ich części bez trwałego uszkodzenia. Wśród różnych rodzajów połączeń rozłącznych można wymienić:
Połączenia wciskowe — bezpośrednie łączenie dwóch elementów poprzez nacisk i tarciowe oddziaływanie między ich powierzchniami, bez użycia elementu pośredniczącego. Elementy są dopasowane tak, że wymiar wewnętrzny jednego jest większy od wymiaru zewnętrznego drugiego. Dzięki temu powstaje nacisk, który utrzymuje elementy w miejscu i przekazuje obciążenia. Przykład osadzenia za pomocą wcisku:
Podczas montażu łożyska tocznego kulkowego na wale prostym przez wciskanie, proces składa się z kilku etapów. Najpierw łożysko jest umieszczane na wale, a następnie przy użyciu młotka i tulei montażowej lub prasy, łożysko jest wprowadzane na wale. Młotek jest używany do wywierania delikatnych i równomiernych uderzeń w tuleję, która działa jako przewodnik, kierując łożysko na odpowiednią pozycję na wale. W przypadku dociskania w obudowie używa się specjalnej podkładki, by równomiernie rozprowadzić siłę. Jeśli pasowanie jest ciasne, łożysko można podgrzać, co ułatwia jego osadzenie na wale. Demontaż łożyska często polega na użyciu specjalnych narzędzi, takich jak ściągacze do łożysk. Istnieją zarówno mechaniczne, jak i hydrauliczne wersje ściągaczy. Alternatywnie, do demontażu łożysk używa się hydrauliki, w tym nakrętek hydraulicznych lub pomp hydraulicznych ze wtryskiwaczami oleju. W przypadku większych i cięższych łożysk gorący olej lub para są wykorzystywane do podgrzania i rozszerzenia łożyska, ułatwiając jego usunięcie z wału.
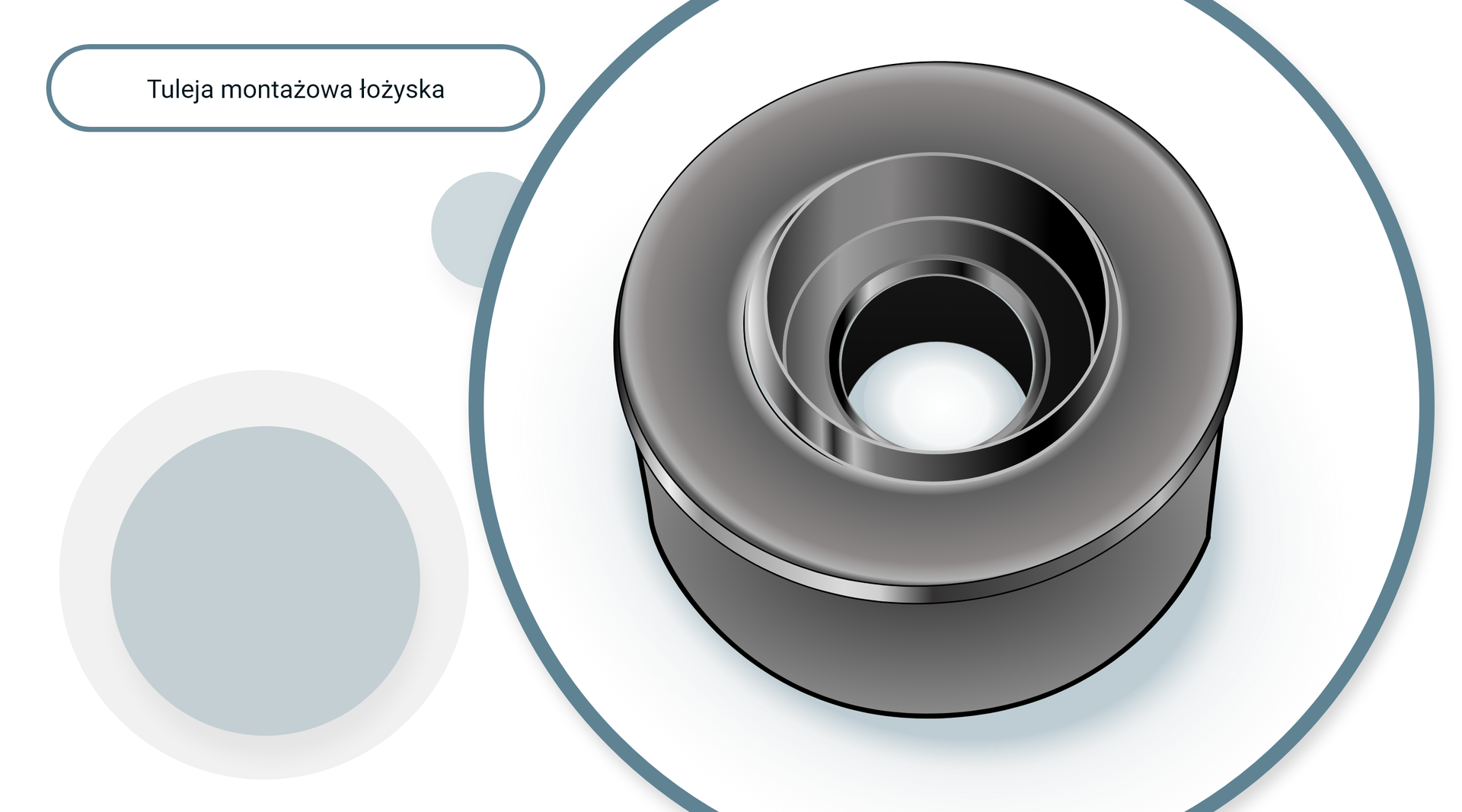
Połączenia wpustowe — rodzaj połączenia rozłącznego, które używane jest do łączenia piasty z wałem i zapobiegania względnemu obrotowi spowodowanemu momentem skręcającym. W tym połączeniu elementem pośredniczącym jest wpust, który jest umieszczany w rowku wpustowym na czopie wału i współpracuje z rowkiem w piaście. Przykładem takiego połączenia jest umieszczenie płaskiego koła pasowego przekładni otwartej na wale prostym. W procesie tym zarówno koło pasowe, jak i wał, są wyposażone w odpowiednie wycięcia — rowek na kole pasowym i gniazdo na wale. Precyzyjnie wykonany wpust jest następnie umieszczany w otworze wpustowym w kole pasowym, a po pewnym upewnieniu się o dokładnym położeniu, koło jest trwale mocowane za pomocą nakrętek oporowych lub tulei dystansowych. Aby dokonać demontażu, usuwa się zabezpieczenia i wyciąga wpust z rowka w kole pasowym, co pozwala na odłączenie koła pasowego od wału.
Na grafikach przedstawiono następujące elementy: koło pasowe płaskie połączone z wałem prostym wpustem pryzmatycznym, wpust pryzmatyczny, nakrętkę oporową i tuleję dystansową.
Innym przykładem jest połączenie koła zębatego czołowego o zębach prostych, w którym zęby poruszają się wzdłuż osi obrotu, tworząc linię ruchu. Montaż wpustów czółenkowych polega na przygotowaniu rowka w kole oraz gniazda na wale, które pasują do kształtu wpustu. Wpust czółenkowy jest delikatnie umieszczany w gnieździe na wale, na przykład poprzez subtelne uderzenia młotka lub przy użyciu prasy, z zachowaniem równoległości górnej powierzchni wpustu do powierzchni czopa w kole. Następnie wpust jest dociskany do rowka na kole, tworząc trwałe i precyzyjne połączenie między kołem a walem. W momencie demontażu koła zębatego używa się wyciągacza, by równomiernie wywierać siły i ułatwić odłączenie. Gdy koło stanie się luźne, może być delikatnie usunięte ręcznie, zachowując ostrożność, by uniknąć uszkodzeń. W widocznym i dostępnym wpustem czółenkowym można się posłużyć szczypcami lub śrubokrętem.
Na grafikach przedstawiono koło zębaty czołowe połączone z wałem prostym wpustem czółenkowym oraz zbliżenie na wpust czółenkowy, który budową przypomina połowę walca.
Istnieją trzy rodzaje wpustów:
Wpusty pryzmatyczne — charakteryzują się kształtem pryzmatu i są ciasno dopasowane do otaczających powierzchni. Stosowane do współpracy piasty z wałem oraz zapewnienia stabilności przed obrotem względnym.
Wpusty czopkowe — posiadają kształt przypominający wpust pryzmatyczny z walcowym wypustem na środku lub końcu. Służą do połączeń przesuwnych między piastą a wałem.
Wpusty czółenkowe — mają kształt odcinka koła i stosuje się je do połączeń piasty z wałem. Wykorzystywane w złączach walcowych i stożkowych.
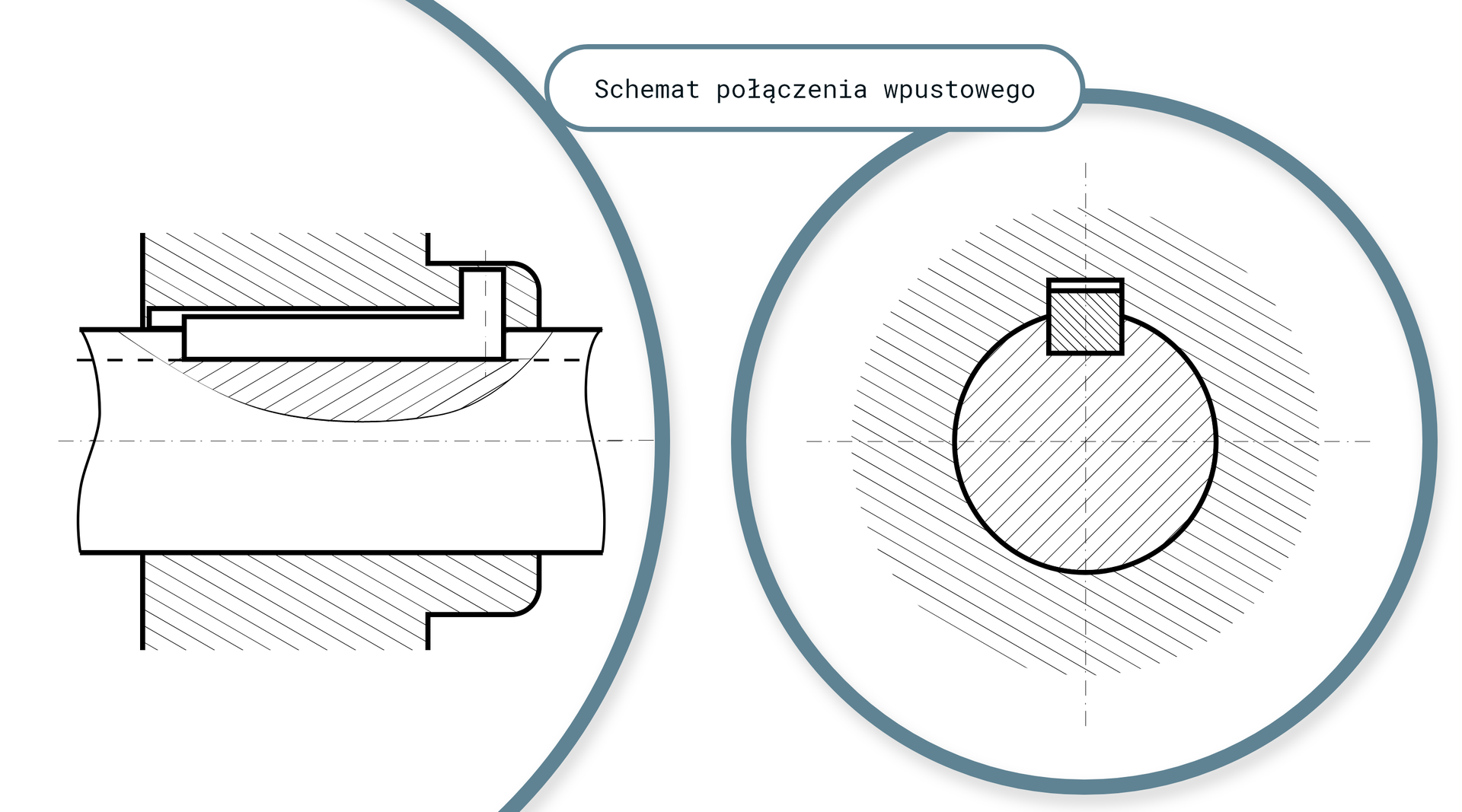
Połączenia wielowypustowe — sposób łączenia piasty z wałem poprzez wielowypust nacięty na wale. Zapewnia stabilność przed obrotem i umożliwia centrowanie elementów. Stosowane głównie w produkcji masowej znormalizowanymi liczbami wypustów, np. 6, 8. Połączenie wielowpustowe koła zębatego prostego na wał prosty: podczas montażu koła zębatego prostego na wał prosty, należy upewnić się, że liczba i kształt wypustów oraz wpustów na wałach i kołach zębatych są zgodne. Następnie umieszczamy koło zębate na wale tak, aby wypusty na wale idealnie pasowały do wpustów w kole zębatym. Korzystając z narzędzi montażowych, takich jak młotek i tuleja montażowa, delikatnie i równomiernie osadzamy koło zębate na wale, zapewniając solidne połączenie.
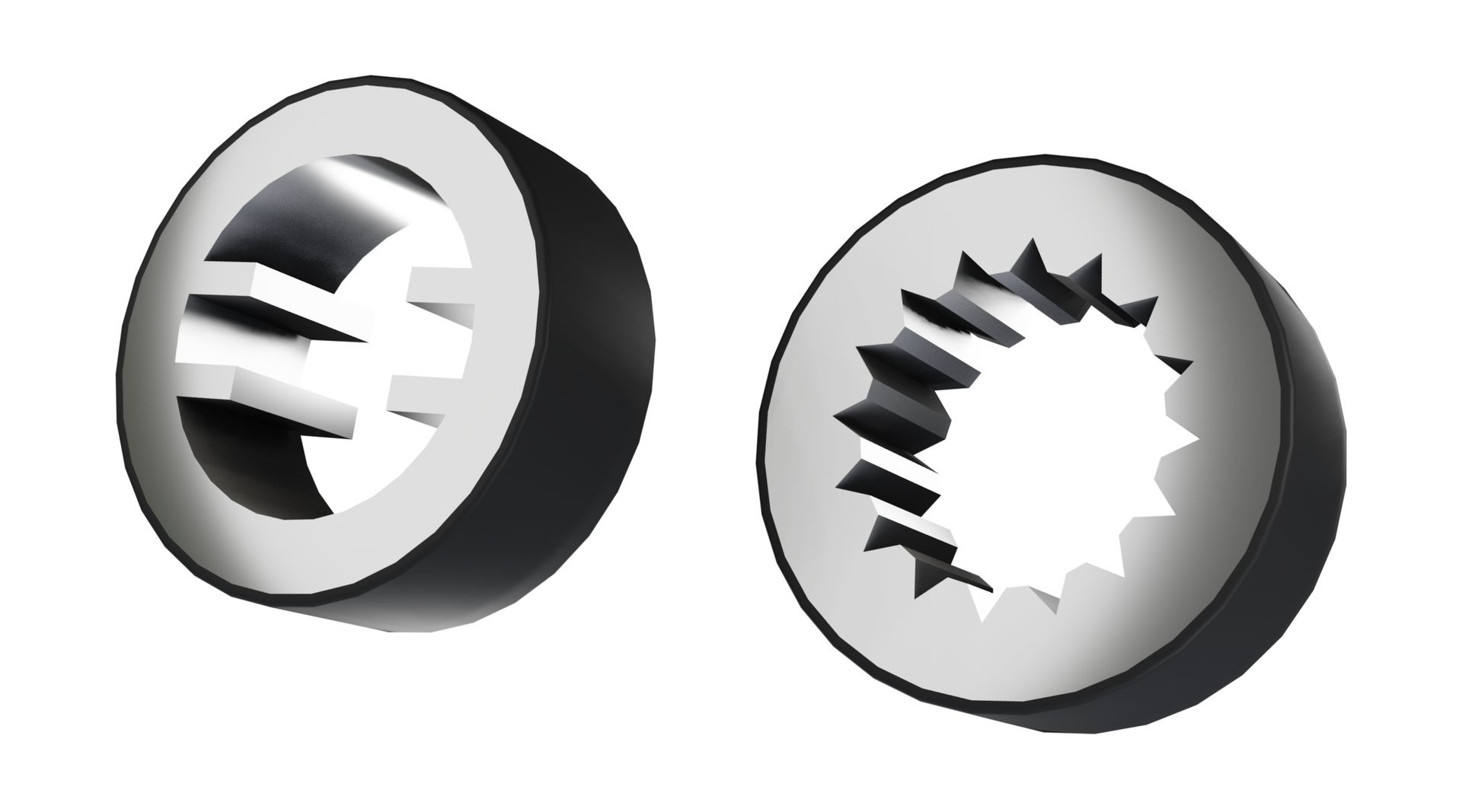
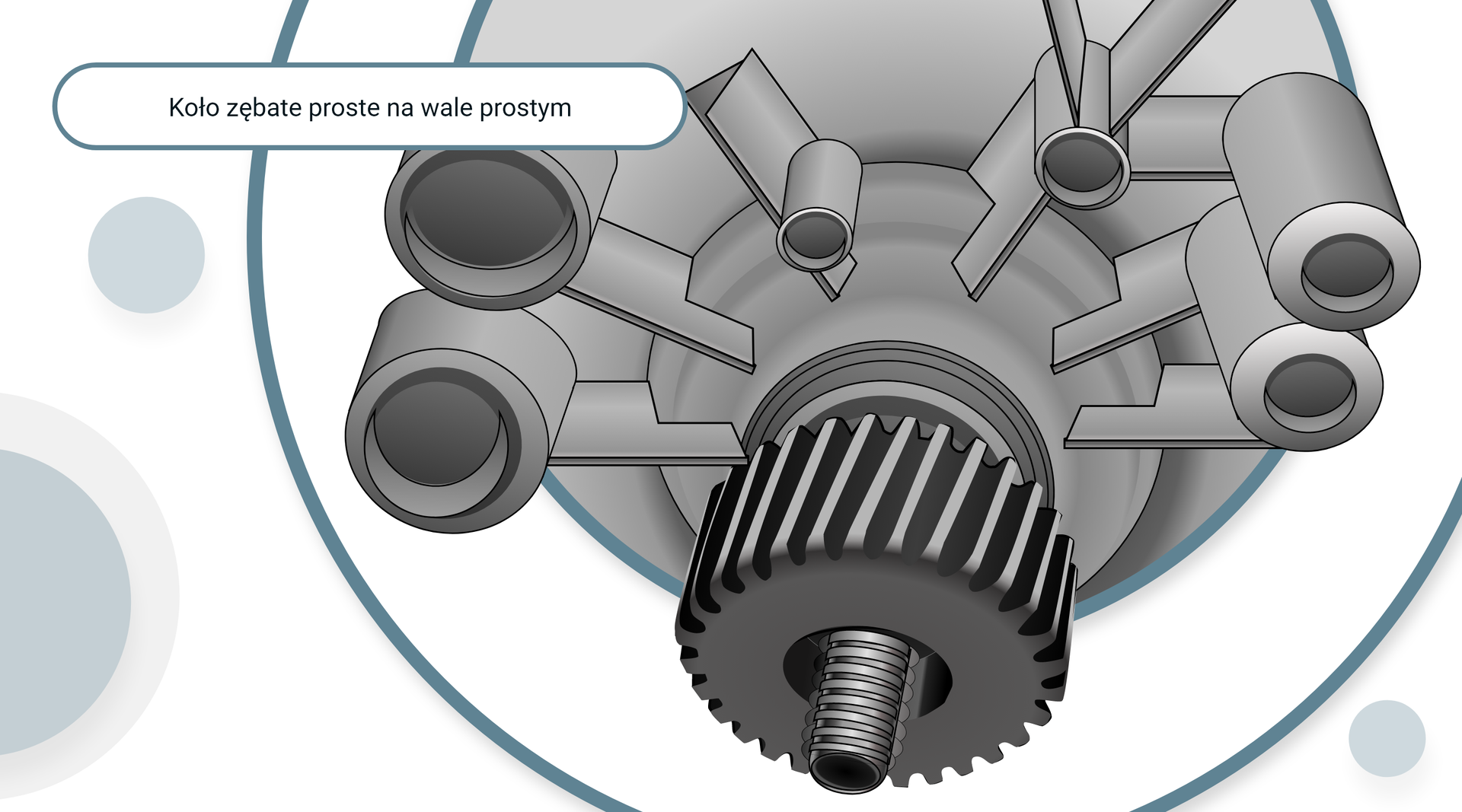
W przypadku montażu koła zębatego śrubowego na wał prosty również należy upewnić się, że wypusty i wpusty na wałach i kołach zębatych są zgodne. Umieszczamy koło zębate na wale w taki sposób, aby wypusty na wale pasowały precyzyjnie do wpustów w kole zębatym. Następnie wprowadzamy odpowiednie śruby przez otwory w kole zębatym i dokręcamy je. To zapewni stabilne połączenie między kołem a wałem.
Aby odłączyć koło zębate, które jest przymocowane na wale, w sytuacji, gdy koła zębate są naciągnięte na wale, należy ostrożnie wyjąć koło z wału. W niektórych sytuacjach, szczególnie gdy elementy są mocno osadzone, można skorzystać z narzędzi hydraulicznych, takich jak hydrauliczne odciągacze lub wyciągarki, które umożliwiają kontrolowane oddzielenie elementów od wału poprzez zastosowanie siły hydraulicznej. W przypadku kół zębatych śrubowych należy odkręcić wszystkie śruby, które mocują koło zębate na wale.
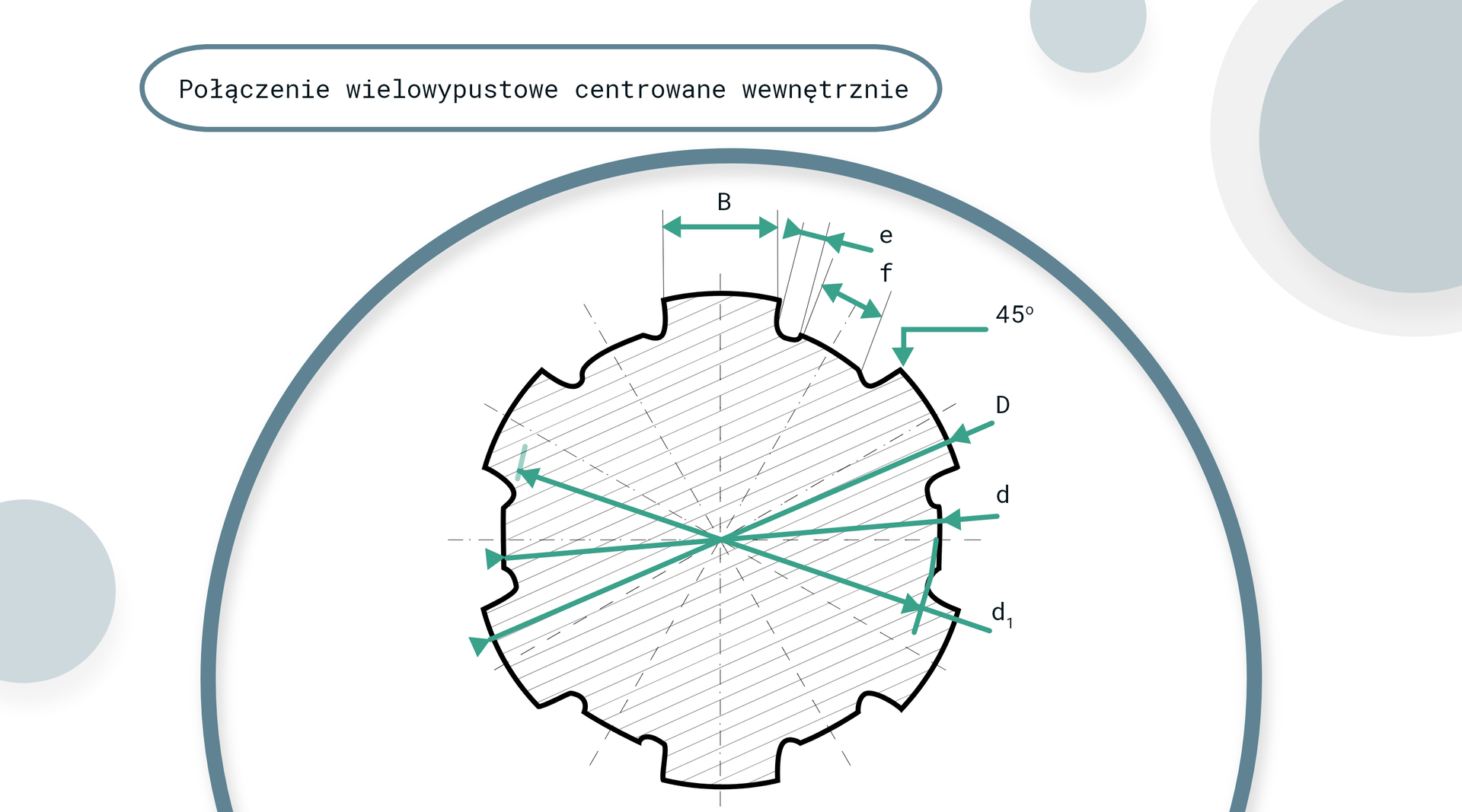
Wyróżnia się wielowypusty:
Wielowypust równoległy, prostokątny — charakteryzuje się liczbą zębów, średnicą głów i stóp oraz szerokością wpustu.
Wielowypust ewolwentowy — stosowany przy zmiennym momencie obrotowym.
Wielokarb (wieloklin) — ma profil trójkątny.
Połączenia klinowe
Rodzaj połączeń, w których klin jest elementem pośrednim. Dzielą się na klinowe wzdłużne (do osadzania piast na wałach) i klinowe poprzeczne (do łączenia elementów). Opierają się na spójności klina i siłach tarcia, umożliwiając trwałe mocowanie elementów na wałach.
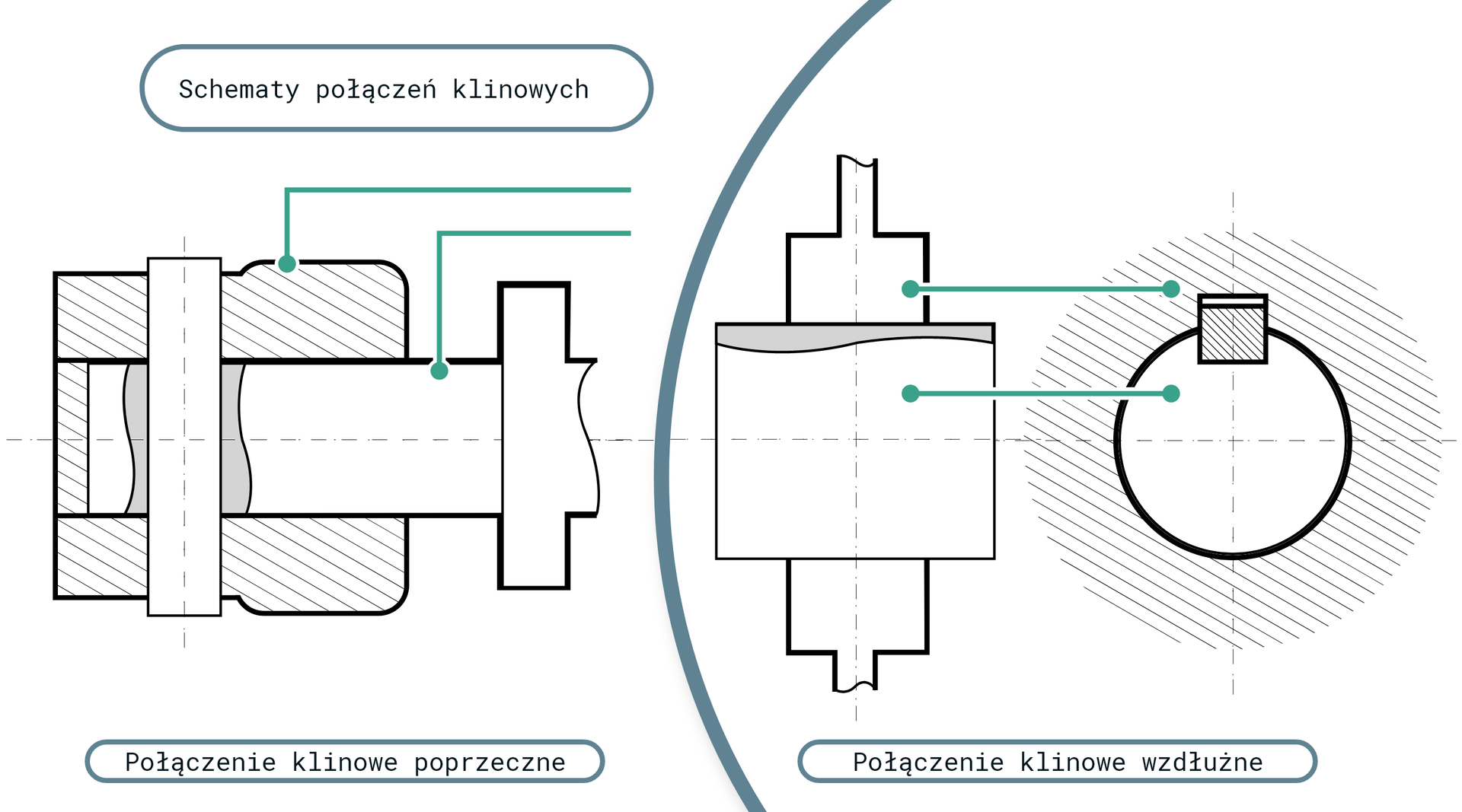
Kołki i sworznie pełnią różne funkcje w konstrukcjach mechanicznych, a ich zastosowanie zależy od wymagań danego systemu. Stosunek średnicy do długości kołka jest zazwyczaj niski, co oznacza, że są one stosunkowo krótkie w porównaniu do swojej średnicy. Sworznie są zazwyczaj dłuższe niż kołki, co pozwala na większy zakres ruchu liniowego. Stosunek średnicy do długości sworznia jest wyższy niż w przypadku kołka, co oznacza, że są one stosunkowo dłuższe w porównaniu do swojej średnicy.
Połączenia kołkowe
służy do ustalania wzajemnego położenia dwóch lub więcej elementów. Wykorzystuje kołki o kształcie stożkowym lub walcowym, gładkie lub karbowane. Jest to połączenie spoczynkowe, pośrednie i rozłączne, zapewniające ustabilizowane położenie elementów bez ich względnego ruchu podczas obciążenia. Rodzaje kołków:Kołki stożkowe niehartowane,
Kołki stożkowe z wewnętrznym gwintem,
Kołki stożkowe z dodatkowym wewnętrznym gwintem,
Kołki stożkowe z gwintowanym czopem niehartowane,
Kołki stożkowe zakończone gwintowanym czopem na jednym końcu,
Kołki walcowe ze stali niehartowanej lub z austenitycznej stali nierdzewnej,
Kołki walcowe,
Kołki karbowane na całej długości,
Kołki z nacięciami lub rowkami na całej długości,
Kołki sprężyste rozcięte lekkie,
Kołki sprężyste z nacięciami,
Kołki sprężyste zwijane lekkie,
Kołki sprężyste wykonane w formie spirali.
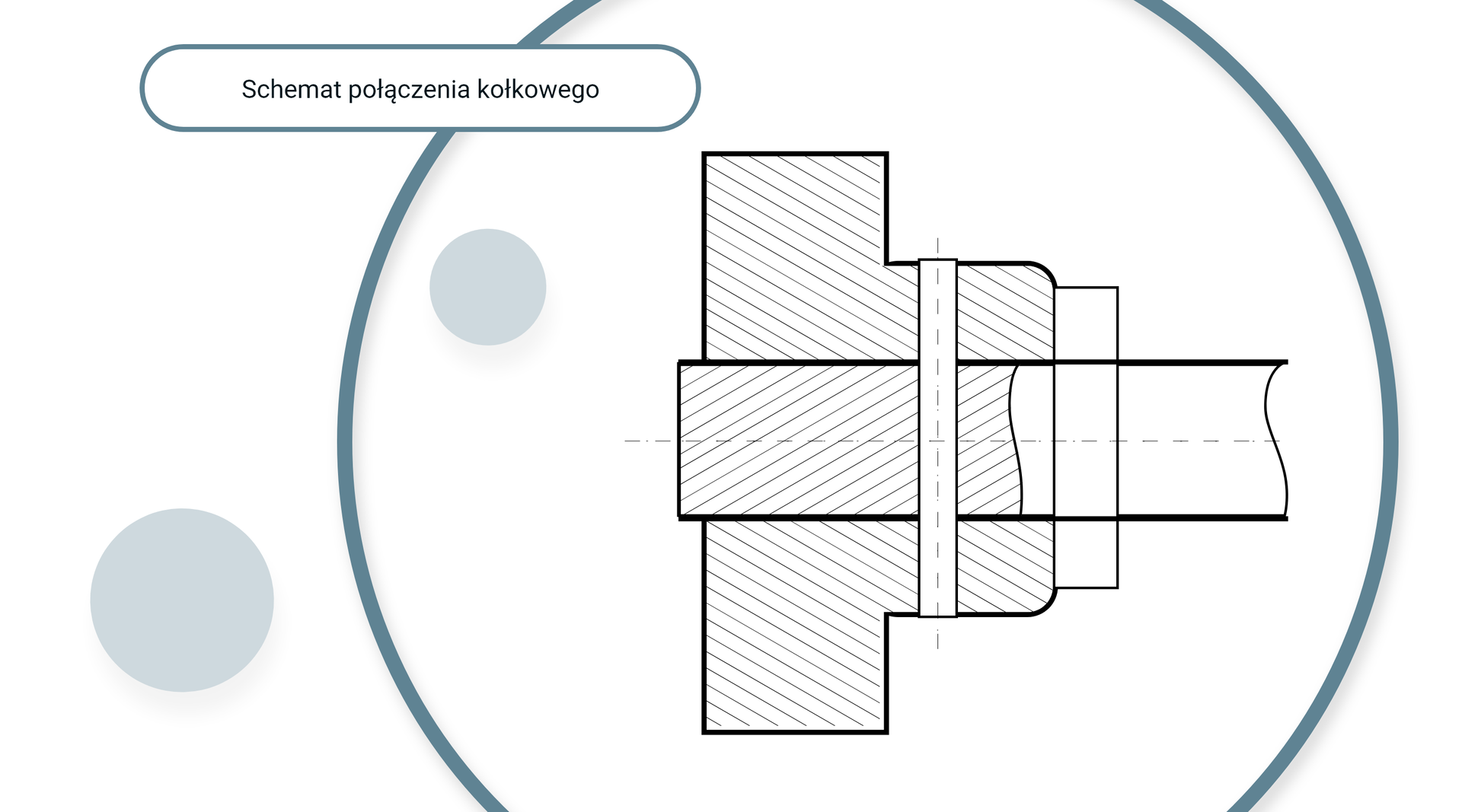
Połączenia sworzniowe — rodzaj połączenia rozłącznego ruchowego, w którym centralnym elementem łączącym jest walcowy sworzeń. Jest on wykorzystywany głównie w przegubach do łączenia elementów, umożliwiając ruch obrotowy jednego elementu względem osi sworznia przy jednoczesnym zachowaniu stabilności i przenoszeniu obciążeń. Wyróżniamy:
sworznie bez łba,
sworznie z czopem gwintowym,
sworznie z dużym łbem walcowym,
sworznie z łbem czworokątnym,
sworznie z łbem soczewkowym,
sworznie z małym łbem walcowym.
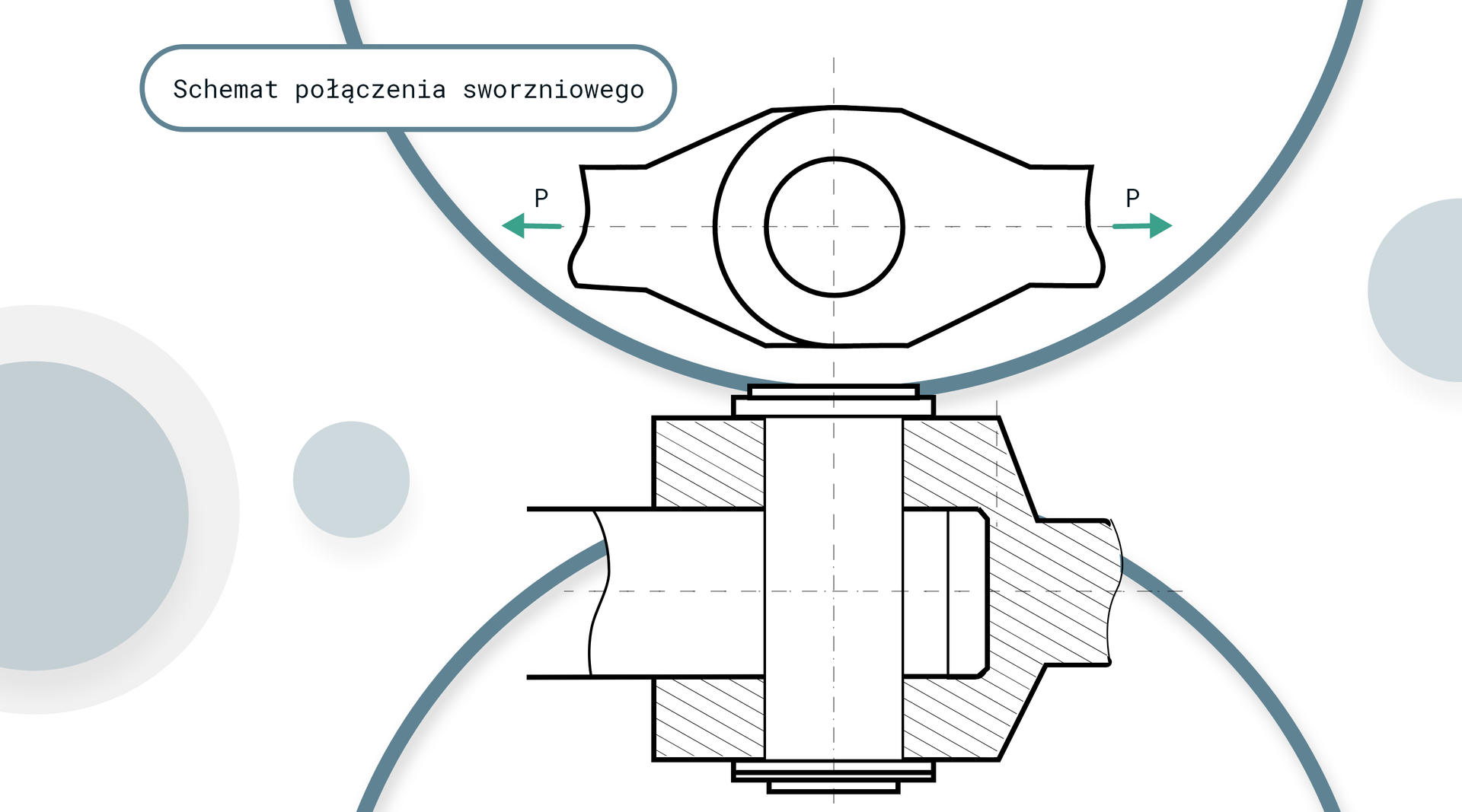
Połączenia gwintowe — rodzaj połączenia mechanicznego, w którym elementy łączące, takie jak śruba i nakrętka, posiadają odpowiednio ukształtowane względem siebie występy i wgłębienia w postaci gwintów. Te występy i wgłębienia, zwane również zwojami, współpracują ze sobą, umożliwiając ruch obrotowy jednego elementu względem drugiego oraz utrzymanie ich połączenia poprzez siłę tarcia między gwintami. Podział gwintów ze względu na zarys:
Trapezowe symetryczne (przenoszą duże obciążenia w obu kierunkach),
Trapezowe niesymetryczne (pracują przy jednym kierunku obciążeń),
Trójkątne,
Okrągłe (duża wytrzymałość zmęczeniowa),
Prostokątne.
Podział gwintów ze względu na rodzaj wymiaru:
Gwint wewnętrzny,
Gwint zewnętrzny.
Podział gwintów ze względu na jednostkę miary:
Gwint calowy,
Gwint metryczny.
Podział gwintów ze względu na wielkość:
Gwinty różnią się od siebie rozmiarem, który jest określany liczbą zwoi na długość.
Podział gwintów ze względu na ilość linii śrubowej:
Gwint walcowany,
Gwint stożkowy.
Podział gwintów ze względu na zastosowanie:
Gwint pociągowy,
Gwint złączny.
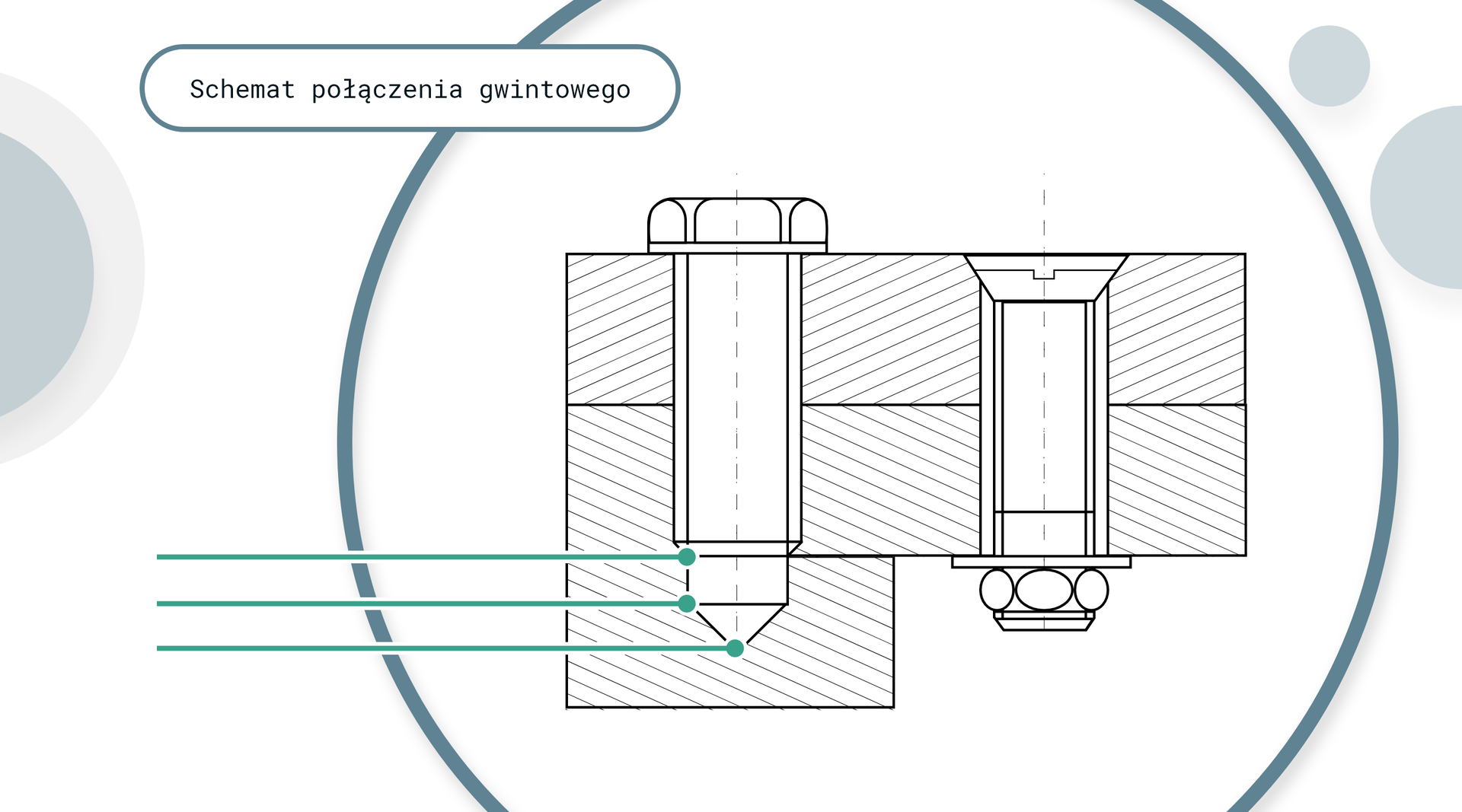
Połączenie śrubowe — rodzaj rozłącznego połączenia kształtowego, w którym elementy są ze sobą łączone za pomocą dodatkowych elementów złącznych, takich jak śruby, nakrętki i podkładki. W tym rodzaju połączenia, elementy konstrukcyjne są zestawione i utrzymywane razem przy pomocy śrub, które działają jako łączniki.
Podział połączeń śrubowych:Połączenie śrubowe śrubą zwykłą — w tym typie połączenia, nakrętka i łeb śruby wywierają nacisk na łączone elementy. Aby zapobiec odkręcaniu się, można używać różnych dodatkowych elementów, takich jak podkładki, zawleczki czy dodatkowe wkręty. Wytrzymałość takiego połączenia opiera się na zdolności śruby do wytrzymywania sił rozciągających oraz tarcia pomiędzy elementami, kiedy to jest konstrukcyjnie uzasadnione. Śruba w stosunku do otworu jest dopasowana luźno zgodnie z normą PN‑75/M‑02046.
Połączenia śrubowe pasowane — w tym rodzaju połączenia, śruba ma dostosowaną dokładność pasowania do otworu. Nakrętka jest używana w celu zabezpieczenia śruby przed wypadnięciem. To połączenie jest przystosowane do przenoszenia sił poprzecznych. Wytrzymałość opiera się na siłach ścinających i naciskach powierzchniowych działających na powierzchnię trzpienia śruby. Śruba w stosunku do otworu jest dopasowana wciskowo.
Połączenia śrubowe dociskowe — w tego typu połączeniach, śruba służy do dociskania jednego elementu złącza do drugiego. Jeden z elementów ma nacięty gwint i działa jako swoista nakrętka.
Przykładem połączenia śrubowego jest złącze kołnierzowe z uszczelnieniem skręcone kilkoma śrubami na obwodzie koła. Połączenie dwóch elementów poprzez kołnierz i uszczelnienie. Kołnierz, zazwyczaj wykonany z wytrzymałego materiału, jest płaskim lub lekko wypukłym pierścieniem. Uszczelnienie ma za zadanie zapewnić szczelność między kołnierzem a przylegającą powierzchnią. Należy przygotować oba elementy, dbając o ich czystość i suchą powierzchnię. Jeśli konieczne, uszczelnienie należy równomiernie rozmieścić wokół kołnierza. Kołnierz należy umieścić na drugim elemencie, tak aby uszczelnienie było dokładnie w miejscu połączenia. Śruby należy włożyć w otwory kołnierza, równomiernie je rozkładając. Dokręcanie śrub zaczynamy od jednej strony, przestrzegając określonego momentu dokręcania. Po dokręceniu sprawdzamy równomierne mocowanie kołnierza i dopasowanie uszczelnienia. W razie potrzeby można przeprowadzić test szczelności. Gdy złącze jest gotowe, można zabezpieczyć śruby, aby uniknąć poluzowania. Demontaż złącza kołnierzowego, polega na odłączeniu dwóch połączonych elementów. W przypadku złącza kołnierzowego z uszczelnieniem należy najpierw wykręcić śruby z otworów w kołnierzu, zaczynając od jednej strony i równomiernie się przemieszczając. Po usunięciu wszystkich śrub można delikatnie oddzielić kołnierz od drugiego elementu. Jeśli uszczelnienie było używane, należy również je usunąć. Ważne jest zachowanie ostrożności, aby nie uszkodzić ani nie zanieczyścić powierzchni elementów.
Powrót do spisu treściPowrót do spisu treści
Na grafice przedstawiono połączenia śrubowe. Kolejne typy połączeń to: za pomocą śruby i nakrętki, za pomocą śruby, za pomocą śruby dwustronnej, za pomocą wkręta, za pomocą śruby fundamentowej.
Połączenia nierozłączne
Połączenia nierozłączne to rodzaj połączeń konstrukcyjnych, w których elementy są trwale złączone i nie można ich rozdzielić bez zniszczenia lub naruszenia co najmniej jednego z elementów. Rodzaje połączeń nierozłącznych:
Spawanie — proces tworzenia połączenia nierozłącznego między elementami poprzez ich miejscowe stopienie, przy pomocy odpowiedniego źródła ciepła i zestalenie. W trakcie spawania dodatkowo może być stosowane spoiwo spawalnicze, które wypełnia spoinę. Rodzaje powstałych spoin w zależności od ich kształtu:
Spoiny czołowe: Powstają zespawaniem dwóch elementów wzdłuż ich czoła.
Spoiny pachwinowe: Wykonuje się w rowku między dwoma ściankami spoiny, mogą być równoboczne lub nierównoboczne. Lico spoiny może być wypukłe, wklęsłe lub płaskie.
Spoiny brzeżne: Wykonywane przez przetopienie i podgięcie brzegów blachy.
Spoiny grzbietowe: Powstają na blachach cienkich, na ich części równoległych lub podwiniętych brzegach. Grubość spoiny równa sumie wysokości spawu i głębokości linii wtopienia.
Spoiny otworowe: Powstają w obecności otworu w jednej z blach, który zostaje wypełniony spoiwem. Otwór może mieć ścianki ukośne ułatwiające wtopienie.
Spoiny bezotworowe punktowe: Wykonywane bez wcześniejszego otworu, poprzez przetopienie jednej blachy i wtopienie w drugą, umiejscowioną pod nią.
Spoiny bezotworowe liniowe: Powstają poprzez akumulację spoin punktowych. Stykają się ze sobą lub zachodzą na siebie, tworząc zgrzeiny liniowe.
Lutowanie: to sposób trwałego łączenia metalowych elementów za pomocą stopu o niższym punkcie topnienia niż same elementy. To połączenie nie wymaga stopienia samych elementów, co sprawia, że jest bezpieczne i idealne do precyzyjnych zastosowań. Stop lutu działa jako spoiwo, tworząc stałe i trwałe połączenie między elementami. Do tego celu wykorzystuje się lutownicę lub palnik gazowy, aby podgrzać elementy i stop lutu, który następnie wypełnia przestrzeń między nimi, tworząc trwałe połączenie.
Na ekranie przedstawiono schemat procesu lutowania. Po kliknięciu każdego z numerów pojawia się jego nazwa odczytywana przez lektora w nagraniu dźwiękowym.
Numer jeden. Lutownica.
Numer dwa. Stop lutowniczy.
Numer trzy. Drut pomiędzy stopem lutowniczym, a lutownicą
Klejenie: Trwałe łączenie mechaniczne, w którym używa się specjalnych substancji klejowych, wykorzystujących adhezyjne właściwości do penetracji powierzchni materiałów i tworzenia stabilnego połączenia po stwardnieniu. W procesie połączenia klejowego używa się klejów lub klejów konstrukcyjnych.
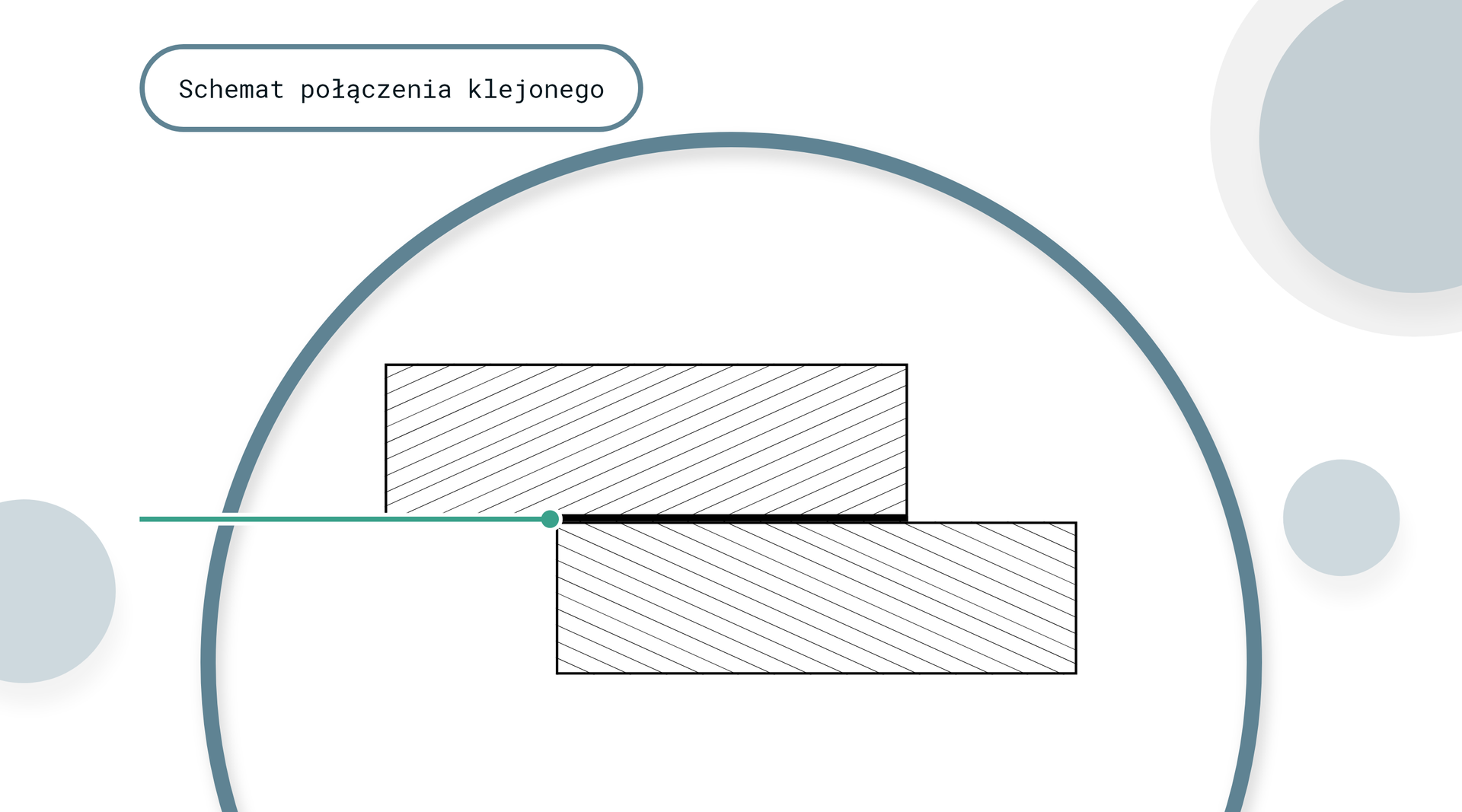
Nitowanie: Stałe połączenie elementów poprzez zastosowanie metalowych nitów, które składają się z trzpieni walcowych z łbami. Proces nitowania polega na przekształceniu trzpienia nita, co prowadzi do rozszerzenia lub zakuwania łbów nita. To z kolei tworzy trwałe i nierozłączne połączenie. Warianty nitów obejmują różne rodzaje:
Standardowe: Zwykłe nity o powszechnym zastosowaniu, w których łby wystają ponad powierzchnię łączonych części.
Szczelne: Stosowane, aby zapewnić szczelność połączenia.
Rozwidlone: Pozwalają na łączenie w miękkich materiałach jak drewno czy plastik.
Rozprężne: Używane w konstrukcjach nośnych.
Wpuszczane: Wpuszczane obustronnie w otwór, tworząc płaską powierzchnię.
Otwarte: Przeznaczone do zastosowań nisko obciążeniowych.
Zamknięte: Łby nitów są schowane wewnątrz materiałów łączonych.
Rowkowane: Stosowane w otworach nieprzelotowych.
Połączenie nitowe to nierozłączne i pośrednie połączenie mechaniczne elementów za pomocą nitów zwykle w postaci trzpieni walcowych z łbami.
Zgrzewanie: Polega na połączeniu materiałów poprzez ich podgrzewanie i łączenie za pomocą docisku lub tarcia. Może to obejmować docisk przed podgrzaniem lub po nim. Istnieją różne metody zgrzewania, a popularna opcja to zgrzewanie elektryczne oporowe, wykorzystujące oporność elektryczną do generowania ciepła i połączenia. Dla tworzyw termoplastycznych uplastycznienie następuje poprzez ciepło, prąd elektryczny lub energię mechaniczną, tworząc trwałe połączenie po ochłodzeniu i docisku. Rozróżniamy cztery kształty zgrzein:
Punktowa — małe, wypukłe, okrągłe obszary stopionej tkanki na powierzchniach elementów.
Liniowa — równa wąska spoina wzdłuż linii styku elementów. Może mieć lekko wypukły lub płaski kształt w zależności od parametrów procesu zgrzewania i właściwości materiałów.
Doczołowa — zgrzewaniu doczołowym powstaje prostokątna lub owalna spoina pomiędzy powierzchniami elementów. Ta spoina jest zwykle płaska lub lekko wypukła i równomiernie przylega do powierzchni łączonych elementów.
Garbowa — wypukłe wypiętrzenie na powierzchni złącza.
Na grafice przedstawiono schemat zgrzewania zespołów łożyskowych. Po kliknięciu każdego z numerów pojawia się nazwa odczytywana przez lektora w nagraniu dźwiękowym.
Numer jeden. Siła docisku.
Numer dwa. Prędkość obrotowa.
Numer trzy. Prędkość zgrzewania.
Numer cztery. Strona natarcia.
Numer pięć. Kołnierz.
Numer sześć. Trzpień.
Numer siedem. Strona spływu.
Numer osiem. Kierunek zgrzewania.
Powrót do spisu treściPowrót do spisu treści
Pasowanie mieszane
W pasowaniu mieszanych, elementy łączące mają minimalne dopuszczalne odchylenie od wymiarów nominalnych, co pozwala na pewien luz montażowy, ale nie jest to tak obszerne, jak w przypadku pasowania luzem. Dzięki temu, po zmontowaniu, elementy nadal pozostają trwale w miejscu i spełniają określone wymagania funkcjonalne, bez zbyt dużego luzy lub luzu, które mogłyby wpłynąć negatywnie na działanie połączenia.
Przykładowo w tulei osadzanej na wale prostym za pomocą pasowania mieszanego, montaż można przeprowadzić poprzez umieszczenie tulei na wale w taki sposób, aby minimalny wymiar tulei pasował do maksymalnego wymiaru wału. Następnie tuleję delikatnie uderza się, zapewniając precyzyjne osadzenie. W przypadku demontażu należy starannie zdjąć tuleję z wału, korzystając z narzędzi lub metod umożliwiających kontrolowane oddzielenie tulei od wału. Dbałość o dokładne dopasowanie minimalnych i maksymalnych wymiarów jest kluczowa, aby zapewnić stabilność połączenia i jego prawidłowe działanie.
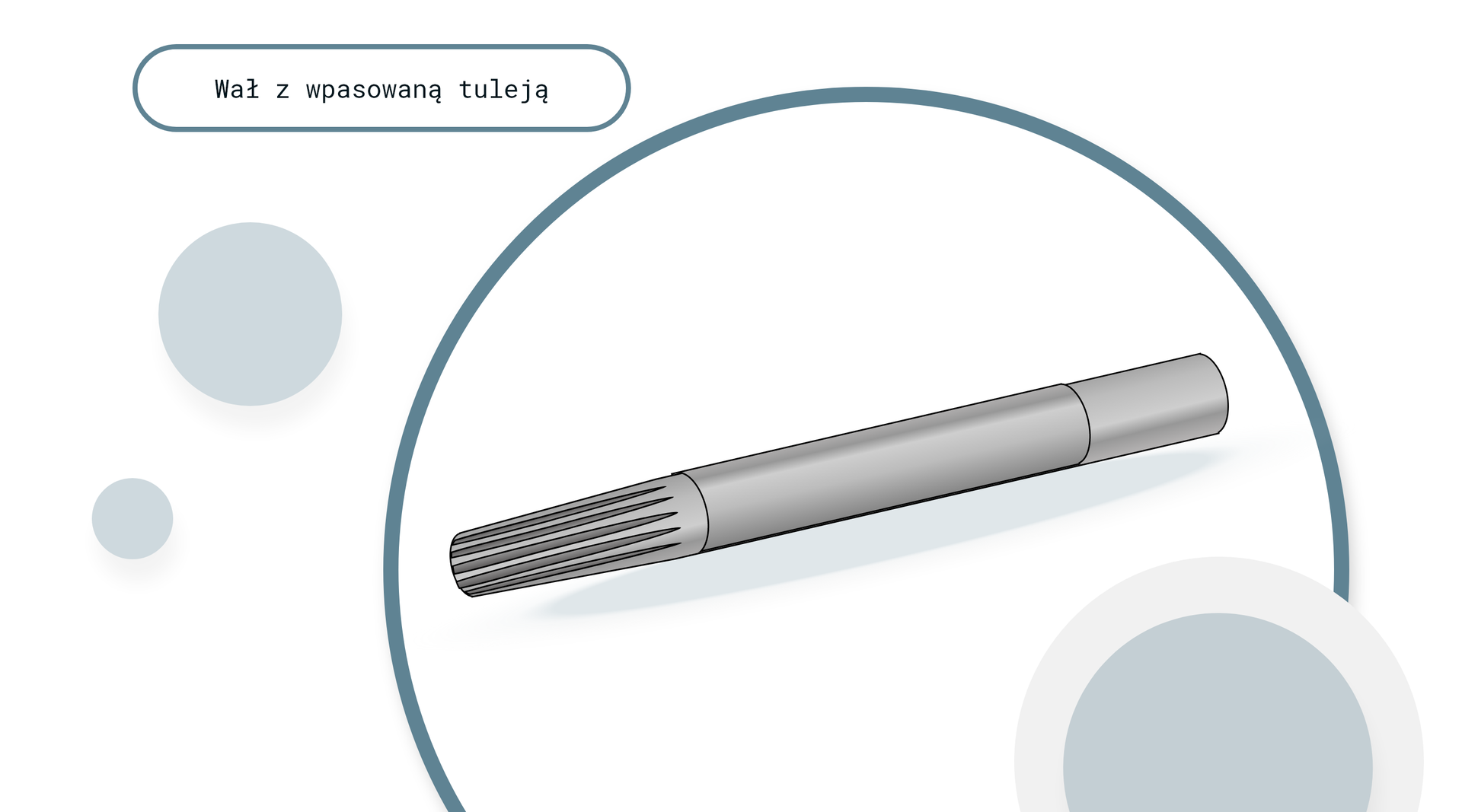
Powrót do spisu treściPowrót do spisu treści
Napędy sterujące
Napęd sterujący odnosi się do układu lub mechanizmu, który ma na celu generowanie ruchu lub zmiany położenia w odpowiedzi na sygnały sterujące. Tego rodzaju napędy są używane w różnych zastosowaniach, takich jak automatyka, robotyka, maszyny przemysłowe i wiele innych, aby umożliwić precyzyjne sterowanie i regulację. Podział napędów sterujących ze względu na rodzaj napędu obejmuje trzy główne kategorie:
Napędy hydrauliczne: wykorzystują płyn hydrauliczny (zazwyczaj olej) do przekazywania energii i generowania ruchu. Są stosowane tam, gdzie wymagane jest duża siła i precyzyjne sterowanie. Przykłady zastosowań to wciągarki, prasy hydrauliczne, maszyny budowlane, a także systemy podnoszenia i składania w różnych branżach.
Napędy pneumatyczne: opierają się na zasadzie sprężonego powietrza do generowania ruchu. Są stosowane w sytuacjach, gdzie potrzebna jest szybka reakcja i ruchy o średniej sile. Przykłady zastosowań obejmują pneumatyczne narzędzia, automatyczne systemy sortujące, układy podawania i transportu.
Napędy elektryczne: wykorzystują energię elektryczną do generowania ruchu. Są bardzo wszechstronne i znajdują zastosowanie w wielu dziedzinach. W zależności od rodzaju silnika elektrycznego i układu sterowania mogą zapewniać wysoką precyzję i łatwe dostosowanie. Przykłady obejmują silniki krokowe używane w drukarkach i układach pozycjonowania, serwomotory w robotyce, oraz silniki prądu stałego lub przemiennego w różnych maszynach przemysłowych.