Przeczytaj
Dlaczego ochrona przed korozja jest konieczna?
Z powodu korozji elektrochemicznejkorozji elektrochemicznej, każdego roku ulega zniszczeniu nawet jedna trzecia światowej produkcji stali. Przynosi to olbrzymie straty gospodarcze w wielu gałęziach przemysłu, które wykorzystują metalowe elementy. W związku z powyższym, ochrona materiałów metalowych jest konieczna, aby zredukować straty związane z procesem korozji. W jaki sposób możemy zabezpieczyć wyroby przemysłu metalurgicznego przed tym zjawiskiem?
Korozja i pasywacja
Korozja atmosferyczna i pasywacjapasywacja mają podobne podłoże chemiczne. Oba procesy mogą zachodzić pod wpływem warunków atmosferycznych. Korozja jest zjawiskiem negatywnym, pogłębiającym się i niszczącym coraz więcej materiału, którego dotyka. Z kolei pasywacja (z punktu widzenia ochrony przed niszczeniem metalu) jest zjawiskiem pozytywnym – w reakcji z tlenem lub innym składnikiem atmosfery i wodą, materiał metalowy wytwarza warstwę obojętnego (pasywnego), regenerującego się, nierozpuszczalnego w wodzie związku nieorganicznego, który tworzy szczelną warstwę ochronną przed dostępem wody i tlenu. Przykładami tego typu powłok są tlenek cynku i patyna, czyli węglan diwodorotlenek miedzi().
Metal znajduje się w stanie pasywnym wtedy, kiedy ma znacznie większą odporność na korozję, niż odporność wskazana przez jego położenie w szeregu napięciowym. Przykładem są stale odporne na korozję, zawierające więcej niż .
Metale aktywne, a więc metale łatwo ulegające utlenieniu, są bardziej podatne na korozję. Natomiast metale o dodatnich potencjałach elektrochemicznych (metale szlachetne) zdecydowanie trudniej ulegają utlenieniu, a tym samym są mniej podatne na uleganie procesom korozyjnym. Podatność danego metalu na korozję możemy zatem sprawdzić, posługując się szeregiem elektrochemicznym metali. Im niższa jest wartość potencjału elektrochemicznego, tym bardziej dany metal podatny jest na korozję. W związku z tym, magnez jest metalem podatnym na korozję, a już srebro pozostaje na niego odporne. Ta wiedza potrzebna jest do przeciwdziałania temu zjawisku.
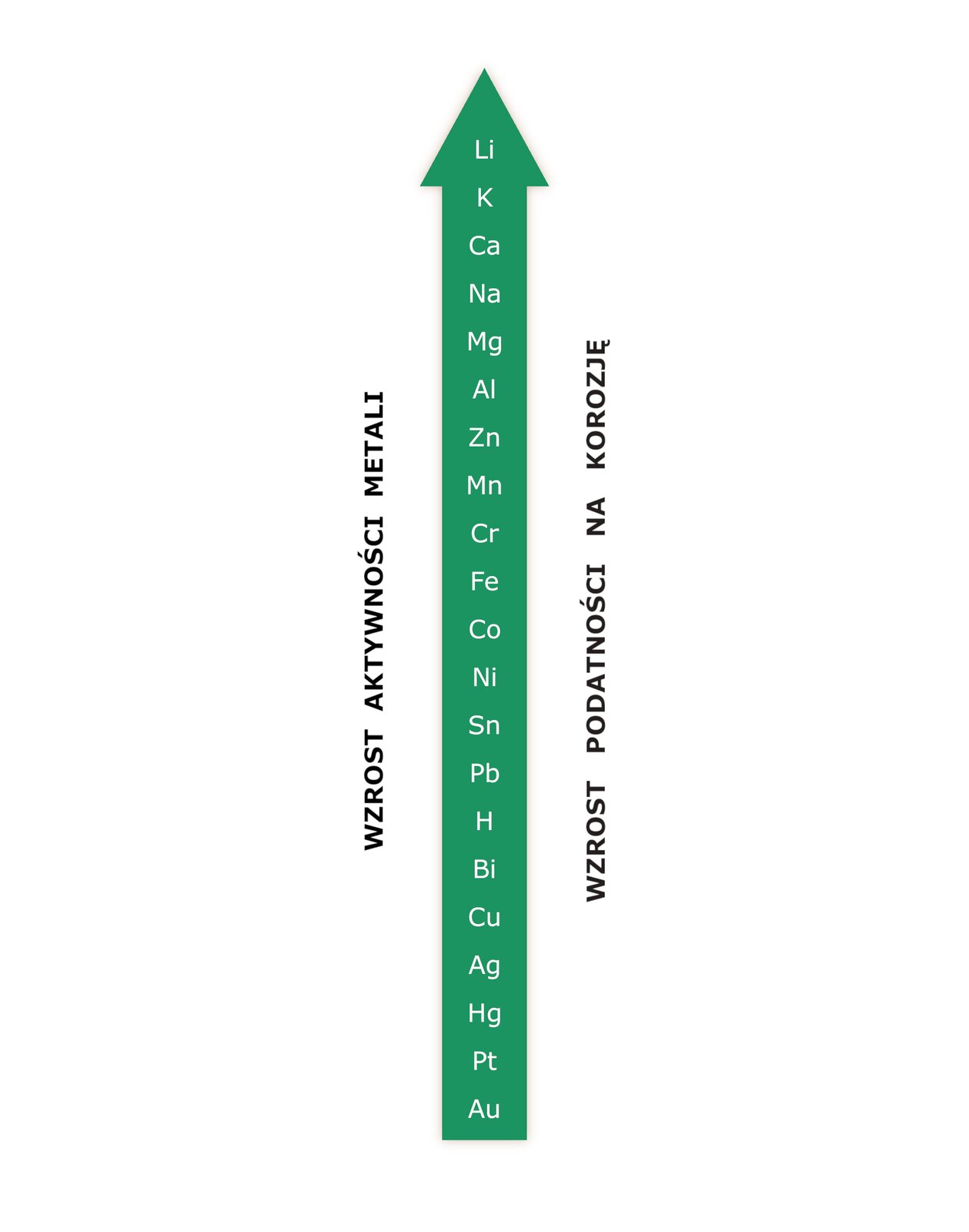
Sposoby zapobiegania korozji
Korozji można zapobiegać na wiele różnych sposobów, zarówno już na etapie produkcji wyrobu, jak i przy jego montażu. W pierwszym przypadku zastosować można następujące zabiegi:
oczyszczanie metalu z fosforu i siarki, które, utleniając się, przyspieszają proces korozji;
stosowanie dodatków stopowychstopowych, które zwiększają odporność na korozję, np. w przypadku stali wprowadza się do niej molibden lub chrom.
W przypadku ochrony poprodukcyjnej zastosować można powłoki ochronne lub inhibitory korozji. Przyjrzyjmy się bliżej tym metodom ochrony przed korozją.
Powłoka anodowa
Powłoki ochronne mogą być wykonane z różnych materiałów, które szczegółowo opiszemy w dalszej części tekstu. Niezależnie jednak od rodzaju powłoki, każda chroni dany element przed korozją w momencie, kiedy pozostaje szczelna. Ta cecha powłoki ochronnej zapewnia bowiem brak kontaktu metalu chronionego z czynnikami środowiskowymi. Poszczególne powłoki zaczynają jednak zachowywać się różnie w sytuacji ich zarysowania lub uszkodzenia.
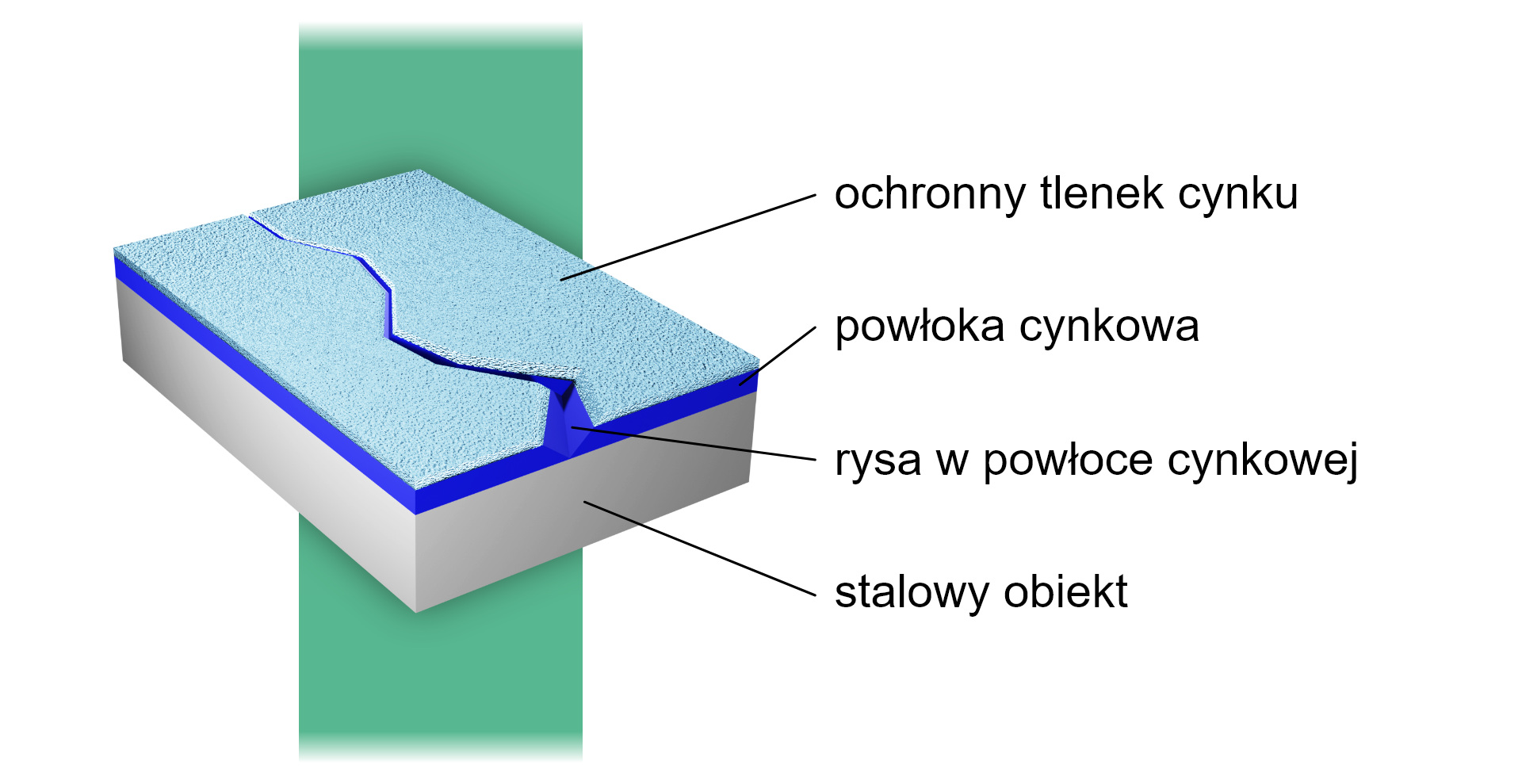
Powłoka anodowa wykonana jest z metalu bardziej aktywnego od metalu, który jest chroniony. Przyjrzyjmy się przykładowi przedstawionemu na rysunku. Stalowy obiekt, który składa się w głównej mierze z żelaza (), został pokryty warstwą cynku (). Ta dodatkowo uległa procesowi pasywacji, co zwiększyło ochronę. Jak wspomniano, w przypadku szczelności warstwy ochronnej, brak korozji jest związany przede wszystkim z brakiem kontaktu stali z otoczeniem. Kiedy jednak warstwa cynku ulegnie uszkodzeniu, to czynniki środowiskowe uzyskują dostęp do elementu stalowego. W takiej sytuacji jednak to cynk, jako aktywniejszy, zaczyna ulegać utlenieniu – pełni rolę anody. Stalowa powierzchnia z kolei pełni rolę katody, na której zachodzą procesy redukcji, np. tlenu cząsteczkowego:
Zatem cynk chroni stal przed korozją nawet w momencie zarysowania lub uszkodzenia powierzchni ochronnej – jest to cecha charakterystyczna wszystkich powłok anodowych.
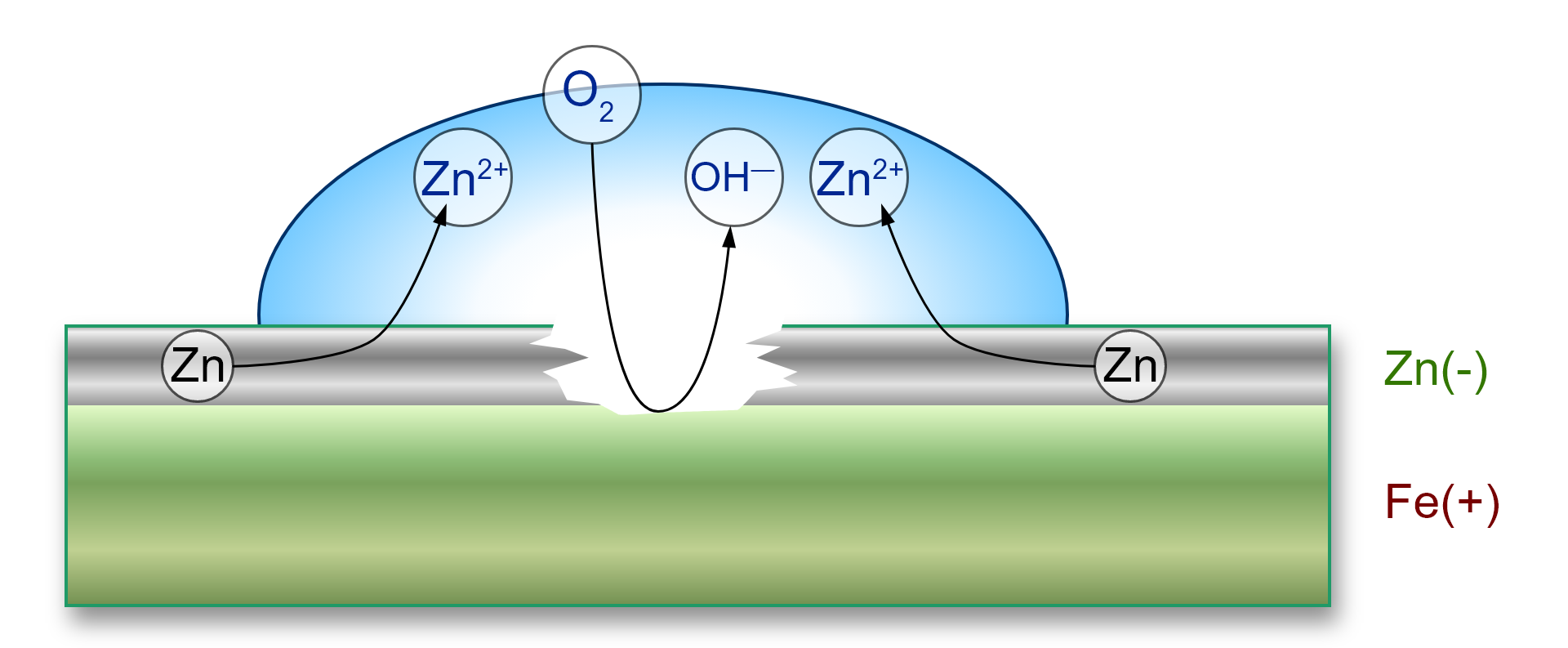
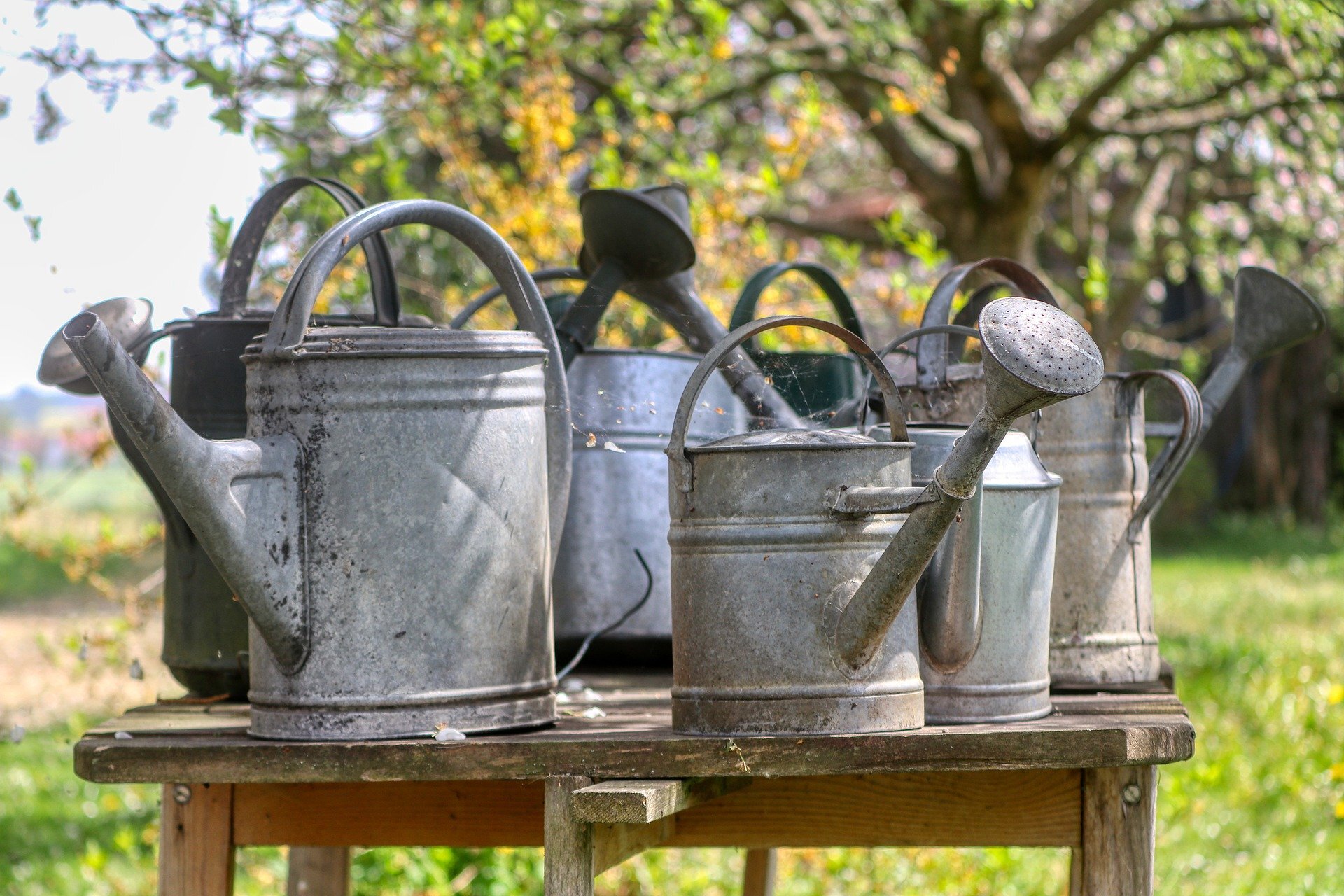
Powłoka katodowa
Powłoka katodowa wykonana jest z metalu mniej aktywnego niż metal, który jest chroniony. Przeanalizujmy przykład pokrycia elementu stalowego (w przypadku ) warstwą niklu (). Niezmienna pozostaje ochrona elementu stalowego w sytuacji szczelności powłoki ochronnej. Niemniej, po zarysowaniu tejże powłoki, nikiel, jako metal mniej aktywny, przyjmuje rolę katody, natomiast żelazo, jako bardziej aktywne, przyjmuje rolę anody i zaczyna ulegać utlenieniu:
Na katodzie niklowej może dochodzić do redukcji tlenu atmosferycznego:
Zatem powłoki katodowe tworzą skuteczną ochronę tylko do momentu, kiedy szczelnie odcinają element od środowiska zewnętrznego. Wydawać by się więc mogło, że stosowanie powłok katodowych nie ma większego sensu. Należy jednak pamiętać, że ze spadkiem aktywności metali rośnie ich odporność na działanie środowiska. Powłoki wykonane z metali mniej aktywnych są zatem bardziej odporne na działanie choćby kwaśnych opadów i pozostają na elemencie chronionym znacznie dłużej niż powłoki z metali aktywnych.
Podsumowując, można zatem wskazać, że powłoki anodowe wykazują większą uniwersalność – nie jest wymagana ich szczelność dla prawidłowego działania. Niemniej same tego typu powłoki łatwiej ulegają działaniom czynników środowiskowych, ponieważ są wykonane z metali zwykle o znacznej aktywności. Powłoki katodowe muszą pozostać szczelne celem ochrony elementu metalowego, niemniej zwykle ich odporność na działanie czynników środowiska jest znacznie większa niż odporność powłoki anodowej z metalu aktywnego, stosowane w miejscach, w których element chroniony jest narażony na zarysowania. Powłoki katodowe stosuje się za to dla elementów, które – z racji swojego umiejscowienia lub zamocowania – z dużym prawdopodobieństwem nie ulegną zarysowaniu.
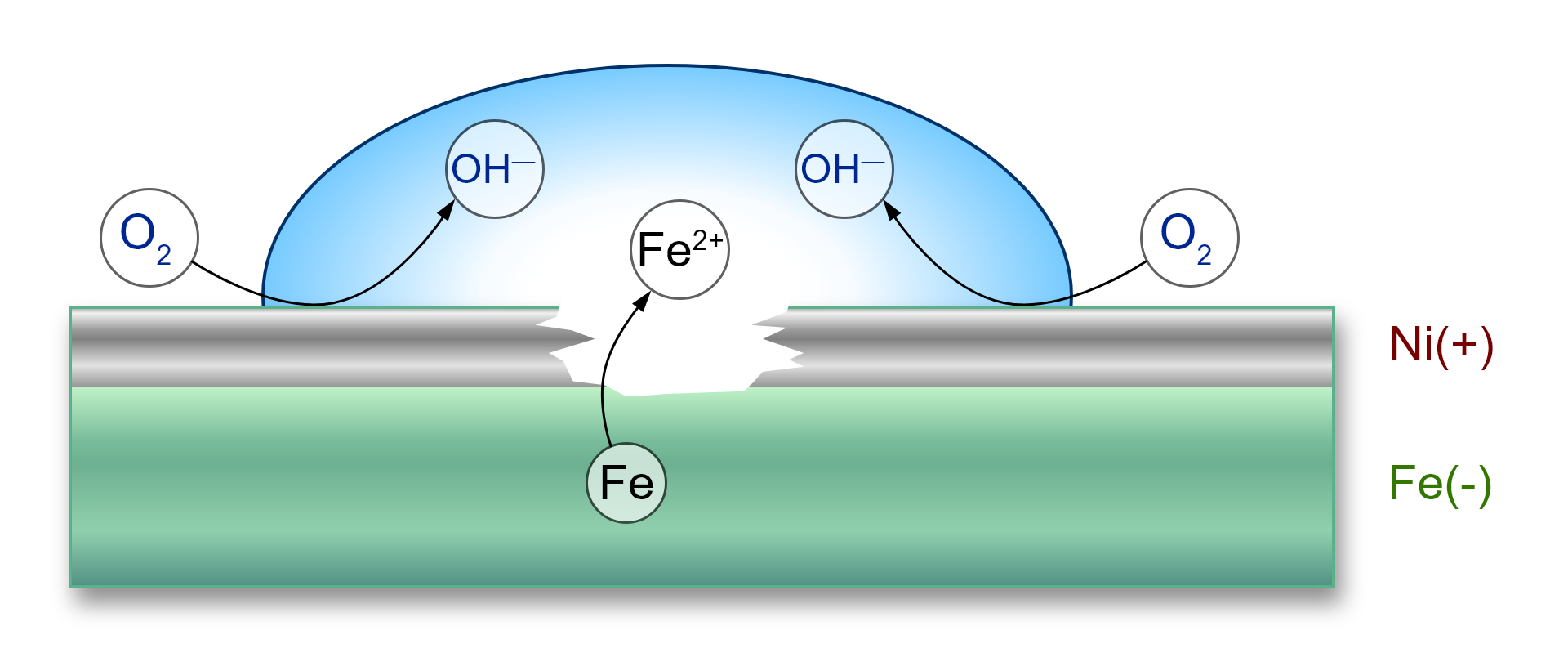
Ochrona katodowa – zastosowanie protektorów
Ponieważ, jak już wspomnieliśmy, w przypadku ochrony anodowej warstwa ochronna nie musi pozostawać szczelna, to taką cechę wykorzystuje się w tzw. ochronie protektorowej. Protektor to np. płytka z metalu bardziej aktywnego od metalu chronionego, którą przyczepia się od rurociągu lub kadłuba statku. Z ochroną protektorową mamy do czynienia w przypadku przyłączenia do stalowego rurociągu płytki z magnezu. Zachodzące procesy powodują utlenienie metalu tworzącego protektor – magnezu:
chroniąc tym samy rurociąg. Płytka protektora z czasem zużywa się i musi zostać zastąpiona nową płytką.
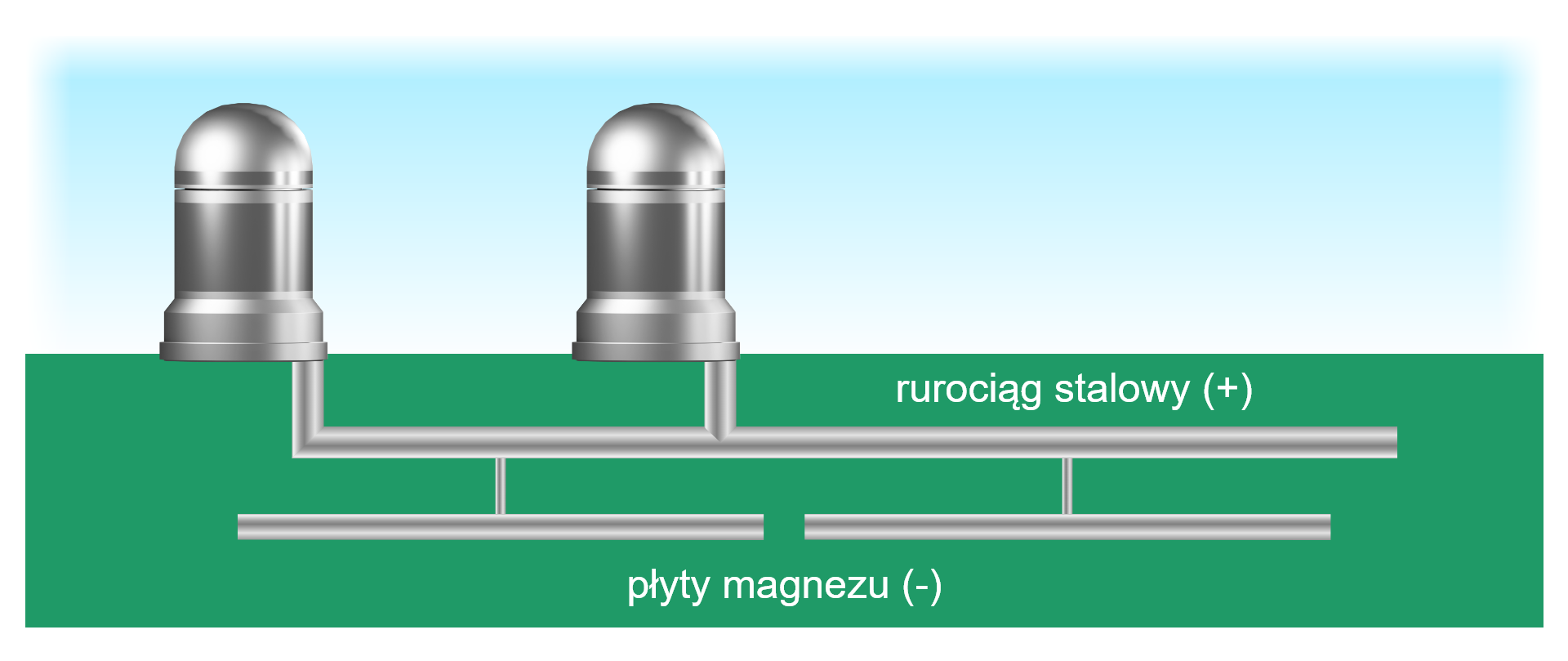
Stosowanie niemetalicznych powłok ochronnych
Zadaniem niemetalicznych powłok ochronnych jest izolowanie powierzchni metali od dostępu tlenu i wilgoci. Niemetaliczne powłoki ochronne uzyskiwane są na powierzchni metali poprzez:
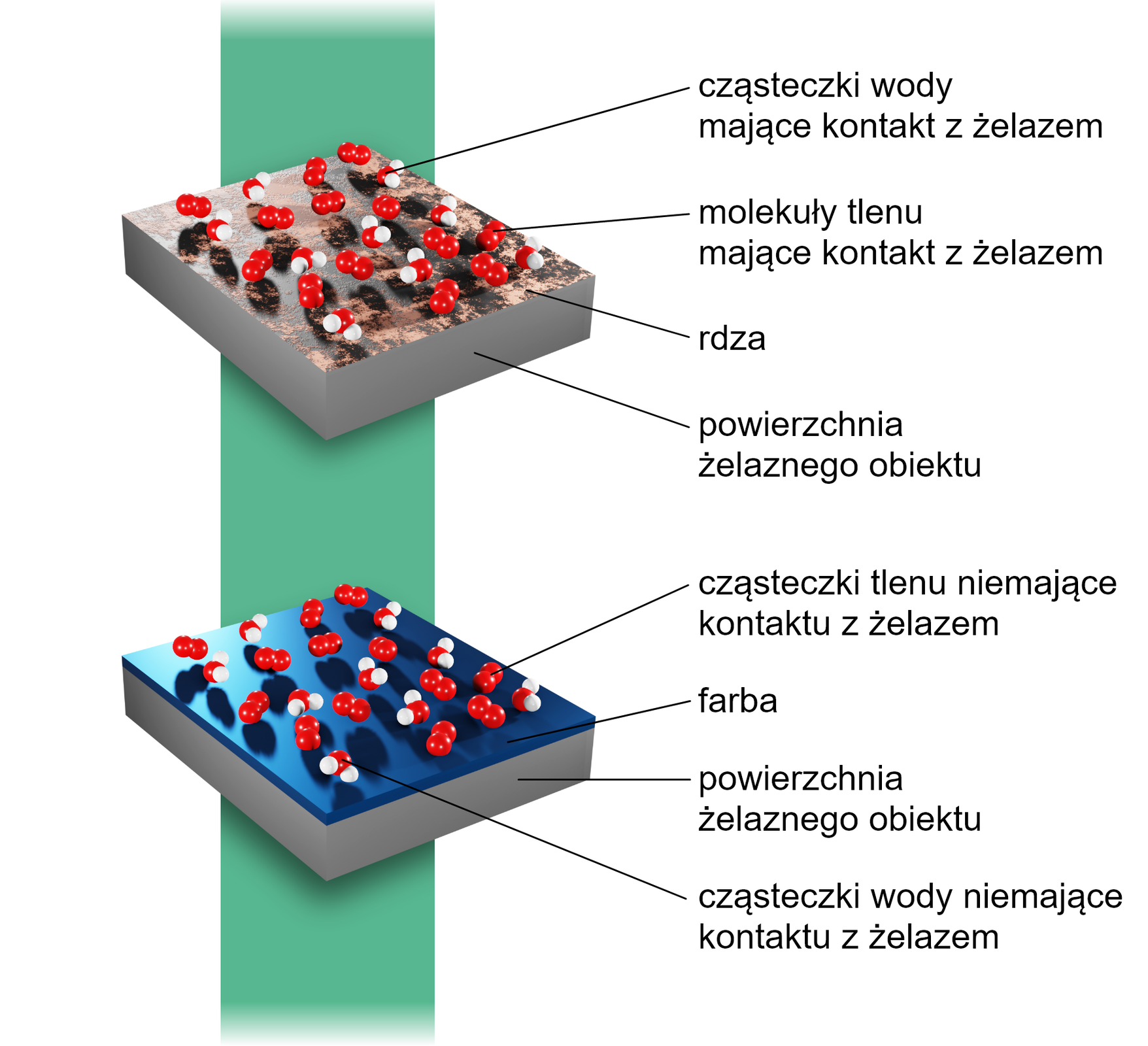
Stosowanie inhibitorów korozjiinhibitorów korozji
Jest to metoda stosowana do ochrony elementów metalowych, w których znajdują się sprzyjające korozji roztwory wodne w obiegu zamkniętym. Przykładami są kotły parowe (np. centralnego ogrzewania) i instalacje chłodnicze (na przykład samochodowe). Dodawanie niewielkich ilości substancji silnie absorbujących się na powierzchni metalu i blokujących dostęp jonów oksoniowych opóźnia znacznie procesy korozyjne.
Słownik
mieszanina składająca się z dwóch lub więcej pierwiastków chemicznych, z których co najmniej jeden, ale występujący w przeważającej ilości, jest metalem
stopy, których głównym składnikiem jest żelazo, a dodatkami stopowymi są różne pierwiastki metaliczne i niemetaliczne
pokrywanie się niektórych metali (miedź, cynk, glin, ołów) cienką warstwą ich związków (np. tlenków) pod wpływem czynników środowiska (na przykład tlenu), jak pokrywanie się cynku nalotem z jego tlenku
po wprowadzeniu ich do elektrolitu, w którym zanurzony jest chroniony wyrób metalowy, związki te opóźniają proces utlenienia poprzez absorbowanie się na powierzchni metalu i izolowanie dostępu do niego czynników korozyjnych; inhibitory tworzą zwykle na powierzchni metalu warstewki ochronne hamujące szybkość korozji; dla korozji w środowisku alkalicznym, jako inhibitory korozji, stosowane są sole: cyny, arsenu, niklu i magnezu, zaś w środowisku kwasowym: krochmal, klej lub białko
produkt korozji atmosferycznej miedzi i jej stopów w wilgotnym powietrzu; powierzchniowa warstwa patyny tworzy powłokę koloru od jasnozielonego do szarozielonego; głównym składnikiem (przy powstawaniu w niezanieczyszczonej atmosferze) jest węglan diwodorotlenek miedzi() – ; powłoka trwała, powstająca jako ostatni etap procesu pasywacji; cały proces pokrywania się powierzchni metalu nalotem patyny trwa kilkadziesiąt lat, chociaż pierwsze objawy mogą zacząć pojawiać się już po kilku miesiącach
korozja metali spowodowana procesami elektrochemicznymi, zachodząca wskutek występowania różnicy potencjałów na powierzchni metalowego obiektu, który znajduje się w środowisku elektrolitu; korozja atmosferyczna, zachodząca pod wpływem czynników atmosferycznych, jest typem korozji elektrochemicznej
Bibliografia
Bielański A., Podstawy chemii nieorganicznej, Warszawa 1987.
Bogdańska Zarembina A., Matusewicz E. I., Matusewicz J., Chemia dla szkół średnich, Warszawa 1995.
Dudek K., Płotek M., Ostatni dzwonek przed maturą. Elektrochemia. Repetytorium maturzysty.
Kaczyński J., Czaplicki A., Chemia ogólna, Warszawa 1974.
Litwin M., Styka‑Wlazło S., Szymońska J., Chemia ogólna i nieorganiczna, Warszawa 2002.
Pazdro K. M., Chemia. Podręcznik do kształcenia rozszerzonego w liceach, Warszawa 2009.