Ocena surowców i półproduktów do sporządzania mas ceramicznych
CES.01. Eksploatacja maszyn i urządzeń przemysłu ceramicznego - Technik ceramik 311944,
Operator urządzeń przemysłu ceramicznego 818115
Sporządzanie mas ceramicznych
WIZUALIZACJA MODELI W GRAFICE 3D
Spis treści
1. Animacja1. Animacja
2. Wizualizacja2. Wizualizacja
Animacja
Przeanalizuj poniższą animację i dowiedz się, w jaki sposób sporządzać masy ceramiczne oraz jaka aparatura jest do tego procesu niezbędna.
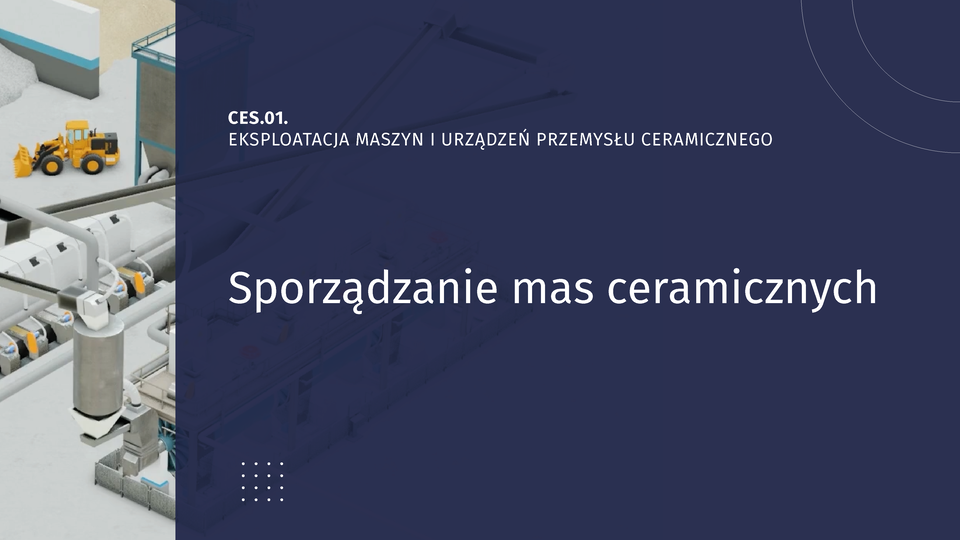
Film dostępny pod adresem /preview/resource/RP9oodXHvtDMn
Film dotyczący tematyki sporządzania mas ceramicznych.
Powrót do spisu treściPowrót do spisu treści
Wizualizacja
Aby zapoznać się z wyglądem i budową urządzeń stosowanych do sporządzenia mas ceramicznych oraz magazynem surowców, wciśnij panel „Pokaż modele”, a następnie wybierz interesujące Cię urządzenie, klikając w jego miniaturę.
Zapoznaj się z opisem wyglądu i budowy urządzeń stosowanych do sporządzenia mas ceramicznych oraz magazynem surowców.
Poniżej w wizualizacji znajdują się urządzenia stosowane do sporządzenia mas ceramicznych wraz z opisami.
Poniżej znajdują się opisy urządzeń stosowanych do sporządzenia mas ceramicznych.
Magazyn podzielony został na siedem równych części. W każdej z tych części znajdują się różne rodzaje surowców używanych w przemyśle ceramicznym:
1. Kaolin – klasyfikowany jest do surowców ilastych powstających ze skał osadowych zawierających w swym składzie głównie kaolinit, a także m.in. kwarc i mikę. Jest to surowiec o właściwościach plastycznych, stosowany między innymi w masie ceramicznej jako składnik spajający i umożliwiający kształtowanie wyrobów.
2. Piasek kwarcowy – klasyfikowany jest do grupy surowców krzemionkowych. Składa się w przeważającej części z kwarcu. Wielkość ziaren waha się od 0.02 do 4.0 mm. Jest to surowiec o właściwościach nieplastycznych. Stosowany w masie ceramicznej jako składnik schudzający (zmniejszający skurczliwość masy podczas jej suszenia, wypalania i spiekania) oraz w celu obniżenia temperatury spiekania (jako topnik). Podstawowy składnik piasku kwarcowego ditlenek krzemu (SiO2) ma właściwości szkłotwórcze.
3. Dolomit – główny składnik skały osadowej o tej samej nazwie, która składa się z minerału dolomitu (węglanu wapnia i magnezu – ponad 90%) i minerału kalcytu (węglanu wapnia), minerałów ilastych, kwarcu, markasytu, pirytu, i substancji bitumicznej. Znajduje zastosowanie jako topnik w masach ceramicznych oraz przy wytwarzaniu materiałów ogniotrwałych.
4. Gliny – są skałą osadową złożoną z minerałów ilastych, kwarcu, skaleni, substancji koloidalnych, może zawierać okruchy innych skał oraz substancje organiczne. Stanowią one cenny surowiec do produkcji wyrobów ceramicznych. Są to surowce o właściwościach plastycznych, stosowane w masie ceramicznej jako składnik spajający i umożliwiający kształtowanie wyrobów. Barwa gliny zależy od zawartości i stopnia utlenienia koloidalnych cząsteczek uwodnionych tlenków żelaza i manganu. W warunkach utleniających przeważają barwy od żółtej poprzez czerwoną do brunatnej, w warunkach redukcyjnych glina może być jasnoszara, szara, szarozielona. Gliny czerwone wykorzystuje się do sporządzania zestawów mas do produkcji wyrobów ceramicznych np. płytek klinkierowych.
5. Gliny – są skałą osadową złożoną z minerałów ilastych, kwarcu, skaleni, substancji koloidalnych, może zawierać okruchy innych skał oraz substancje organiczne. Stanowią one cenny surowiec do produkcji wyrobów ceramicznych. Są to surowce o właściwościach plastycznych, stosowane w masie ceramicznej jako składnik spajający i umożliwiający kształtowanie wyrobów. Barwa gliny zależy od zawartości i stopnia utlenienia koloidalnych cząsteczek uwodnionych tlenków żelaza i manganu. W warunkach utleniających przeważają barwy od żółtej poprzez czerwoną do brunatnej, w warunkach redukcyjnych glina może być jasnoszara, szara, szarozielona. Gliny szare wykorzystuje się do sporządzania zestawów mas do produkcji wyrobów ceramicznych np. płytek gresowych.
6. Skalenie – obok kwarcu są to najpospolitsze minerały w skorupie ziemskiej (objętościowo budują ponad połowę skorupy ziemskiej). Skalenie krystalizują w głębi Ziemi z gorącego stopu skalnego, nazywanego magmą. Występują więc one pospolicie w skałach magmowych. Są też częste w skałach metamorficznych, czyli powstających w wyniku działania wysokich temperatur lub ciśnień, zazwyczaj głęboko pod powierzchnią Ziemi. Skalenie są glinokrzemianami przestrzennymi potasu, sodu, wapnia, rzadziej baru. Zawierają izomorficzne domieszki litu, rubidu, cezu, strontu i żelaza. Jest to surowiec o właściwościach nieplastycznych. Stosowany w masie ceramicznej jako składnik schudzający (zmniejszający skurczliwość masy podczas jej suszenia, wypalania i spiekania) oraz w celu obniżenia temperatury spiekania (jako topnik). Skalenie mają wpływ na zwiększenie wytrzymałości mechanicznej i odporności chemicznej wyrobów ceramicznych.
Wybrakowane wyroby ceramiczne – są to odpady powstające podczas produkcji wyrobów ceramicznych (od przygotowania masy ceramicznej do jej wypalania). Odpady takie ponownie są zawracane do procesu przygotowania i przemiału masy ceramicznej. Wybrakowane niewypalone oraz wypalone wyroby ceramiczne są dodatkiem schudzającym masę ceramiczną. Nazwa stosowana w przemyśle to złom biskwitowy.
Podczas przygotowywania mas ceramicznych używany jest wagozasilacz.
Jego budowę oraz zastosowania przedstawiono poniżej:
1. Zbiornik metalowy (szyb zasypowy)
Szyb zasypowy (tzw. kosz zasypowy), przystosowany jest do przyjmowania materiałów ilastych oraz materiałów twardszych. Montowany jest on bezpośrednio na jednostce wagowej. Dolna część leja jest specjalnie ukształtowana, aby ułatwić wypływ produktu przy jednoczesnym ograniczeniu obciążenia jednostki napędowej. Poszczególne surowce są umieszczane przez operatora ładowarki bezpośrednio w górnej części odpowiedniego zbiornika, przeznaczonego do danego surowca wg ustalonej receptury. W dolnej części urządzenia znajduje się tzw. rozdrabniacz, który służy do kruszenia surowców ceramicznych. Rozdrabniacz składa się z wału z ostrzami nożowymi i niezależnym sterowaniem silnikiem, który zapewnia jednorodny wyładunek materiału z kosza zasypowego.
2. Pas transmisyjny (gumowa taśma wyciągowa)
Instalacja pośrednia, składająca się z kilku skrzynek, po jednym na każdy surowiec, z taśmą wyciągową–ważącą. Urządzenie ważące wyposażone jest w czujniki tensometryczne służące do pomiaru nacisku. W ten sposób uzyskuje się system ciągłego ważenia z jednoczesnym dozowaniem poszczególnych składników receptury. System jest zarządzany automatycznie przez ważenie elektroniczne na poszczególnych taśmach.
3. Napęd taśmy wyciągowej oraz urządzenia ważące.
Napęd taśmy wyciągowej składa się z silnika i motoreduktora. Surowiec podawany na taśmę wyciągową, z każdego szybu zasypowego, jest ważony przy użyciu wagi przenośnikowej wyposażonej w czujniki tensometryczne.
4. Rozdrabniacz wraz z przesypem
Surowce po ich naważeniu, zgodnie z recepturą, zostają przesypane na przenośnik taśmowy transportujący je do rozdrabniacza (kruszarki zębatej dwuwalcowej). Kruszarki tego typu mogą być montowane bezpośrednio pod zasypem oraz mogą być stosowane do rozdrabniania materiałów gliniastych, mokrych, suchych i twardych. Mieszanka surowców następnie transportowana jest za pomocą przenośników taśmowych do kolejnego procesu przemiału ich w młynach kulowych. System przenośników transportowych, wraz z przesypami, pracuje w trybie ciągłym i może transportować surowce w poziomie, w pionie, a także pod kątem.
5. Instalacja odciągowa
Instalacja odciągowa (system rur i elastycznych węży) stanowi element systemu odpylania. Odciągi miejscowe są połączone w jeden system z urządzaniami filtrowentylacyjnymi służącymi do oczyszczania powietrza i odpylania pyłów ceramicznych.
Młyny kulowe od wielu lat są wykorzystywane do produkcji wysokiej jakości proszków mineralnych. Nadają się do mielenia materiałów średnio twardych do ekstremalnie twardych, kruchych i włóknistych.
Poniżej przedstawiono elementy wchodzące w skład młyna kulowego:
1. Młyn modułowy
Młyn modułowy składa się z niezależnych (dwóch lub trzech) korpusów (bębnów) cylindrycznych połączonych szeregowo. Materiał wyprodukowany przez pierwszy młyn podczas obrotu przechodzi do kolejnego cylindra, za pomocą łączących się rur teleskopowych. Korpus cylindryczny wykonany jest z grubej blachy wyłożony od wewnętrznej strony gumową okładziną (która pełni funkcję tłumiącą hałas w wyniku uderzeń kul‑mielników). Na wierzchniej stronie gumowej okładziny znajduje się warstwa odporna na ścieranie (np. tlenek glinu). Każdy korpus cylindryczny posiada niezależny napęd.
2. Jednostka napędowa
Wszystkie poszczególne jednostki napędowe składają się z: silnika elektrycznego, reduktora osi ortogonalnej, zwolnica (przekładnia zębata stosowana przy kołach napędzanych w celu zwiększenia przełożenia końcowego) z pasem pasowym przenoszenie oraz układu chłodzenia i recyrkulacji oleju. Każdy napęd jest wyposażony również w falownik, pozwalający na ustawienie różnych prędkości obrotowych (oddzielnie dla każdego cylindra). W ten sposób możemy uzyskać optymalne parametry związane z przemiałem masy ceramicznej.
3. Panel sterowania
Panel sterowania umożliwia kompleksowe zarządzanie systemem przemiału masy ceramicznej (wejścia/wyjścia surowców ceramicznych w procesie ich mielenia). Wyposażony jest w klawiaturę sterującą oraz monitor do ustawiania danych obsługi maszyny (czasy, temperatury, dane produkcyjne itp.) oraz do wyświetlania komunikatów dla operatora i komunikaty alarmowe. Główne funkcje programu sterowania to: - zarządzanie modułem rozpoczęcia i zakończenia przemiału, - kontrola i monitoring systemu smarowania, - kontrola łożyska głównego i elementu napędowego oraz ich temperatury, - diagnostyka eksploatacyjna dla części mechaniczny i elektrycznych.
4. Silos (zbiornik) dozowania surowców
Surowce po ich naważeniu (zgodnie z recepturą) podawane są przenośnikami transportującymi do systemu dozowania młyna tzw. silosu (zbiornika). Następnie mieszanka surowców, wody i dodatków, przygotowana zgodnie z recepturą technologiczną, dozowana jest (za pomocą urządzenia podającego–ślimak) do pierwszego modułu (cylindra) młyna.
5. Przenośnik ślimakowy
Przenośnik ślimakowy – urządzenie służące do wprowadzania surowców ceramicznych (zasyp młyna) w sposób kontrolowany i ciągły. Przenośnik ślimakowy przenosi ładunek za pomocą wału z piórami w kształcie ślimaka, który obraca się w nieruchomym korycie. Transportowany materiał obraca się razem ze ślimakiem i zgodnie ze zwojami linii śrubowej przesuwa się wzdłuż jego osi.
6. Sito wibracyjne
Przesiewacz wibracyjny do eliminacji gruboziarnistych odpadów.
7. Szafa elektryczna (zasilająca)
Szafa elektryczna dedykowana jest oddzielnie do zasilania dla każdego modułu młyna. Szafy zasilające sterują napędami silników głównych i pomocniczych. Elektroniczna automatyka jest kontrolowana przez automatykę PC. Poprzez użycie odpowiedniego terminala pozwala: - ustawić cykle pracy (nawet podczas pracy maszyny), - zapamiętać i przywołać wszystkie parametry każdego cyklu, - przeglądać komunikaty blokujące, alarmowe i informacyjne dla operatora.
MAGAZYN SUROWCÓW
Przeznaczony jest do składowania kopalnych surowców, wykorzystywanych do przygotowania mas ceramicznych.
WAGOZASILACZE
Przeznaczone są do przygotowania oraz ważenia surowców ceramicznych, w odpowiednich proporcjach, w celu zasypu ich do młynów.
MŁYN KULOWY DO PRACY CIĄGŁEJ
Przeznaczony jest do mielenia dużych partii surowców ceramicznych na mokro, w trybie pracy ciągłej.
MŁYN KULOWY DO PRACY OKRESOWEJ
Przeznaczony jest do mielenia małych partii surowców ceramicznych na mokro, zgodnie z zapotrzebowaniem przerobowni mas ceramicznych.
Powrót do spisu treściPowrót do spisu treści