Wykonywanie i naprawa elementów wyrobów oraz prostych części maszyn, urządzeń i narzędzi
MEC.07. Wykonywanie i naprawa elementów wyrobów oraz prostych części maszyn, urządzeń i narzędzi - Pracownik pomocniczy ślusarza 932917
Wykonywanie prostych połączeń elementów wyrobów, części maszyn, urządzeń i narzędzi
ATLAS INTERAKTYWNY
Spis treści
Połączenia rozłącznePołączenia rozłączne
Połączenia nierozłącznePołączenia nierozłączne
Elementy łącznikówElementy łączników
Grafiki maszyn i urządzeń z różnymi połączeniamiGrafiki maszyn i urządzeń z różnymi połączeniami
Narzędzia do wykonywania połączeń rozłącznych i nierozłącznychNarzędzia do wykonywania połączeń rozłącznych i nierozłącznych
Podział wpustów i wielowypustówPodział wpustów i wielowypustów
Podział nitów, spoin i zgrzeinPodział nitów, spoin i zgrzein
Podział kołków i sworzniPodział kołków i sworzni
Podział połączeń śrubowychPodział połączeń śrubowych
Podział gwintówPodział gwintów
Dźwięki maszyn i procesów technologicznychDźwięki maszyn i procesów technologicznych
Połączenia rozłączne
Połączenia śrubowe
Połączenia śrubowe (gwintowe) zalicza się do połączeń spoczynkowych rozłącznych, które w zależności od przeznaczenia, powinny spełniać poniższe warunki:
zapewnić właściwe położenie łączonych części,
zapewnić mocne połączenie sztywne, aby zapobiegać przesunięciu się względem siebie łączonych części,
zapewnić szczelność styku, aby zapobiegać wyciekaniu płynów i gazów,
zapewnić regulację wzajemnego położenia łączonych części.
Wyżej wymienione warunki nie zawsze muszą, a nawet nie zawsze mogą, być spełnione w każdym połączeniu śrubowym.
Rodzaje śrub i połączeń
Rodzaje śrub
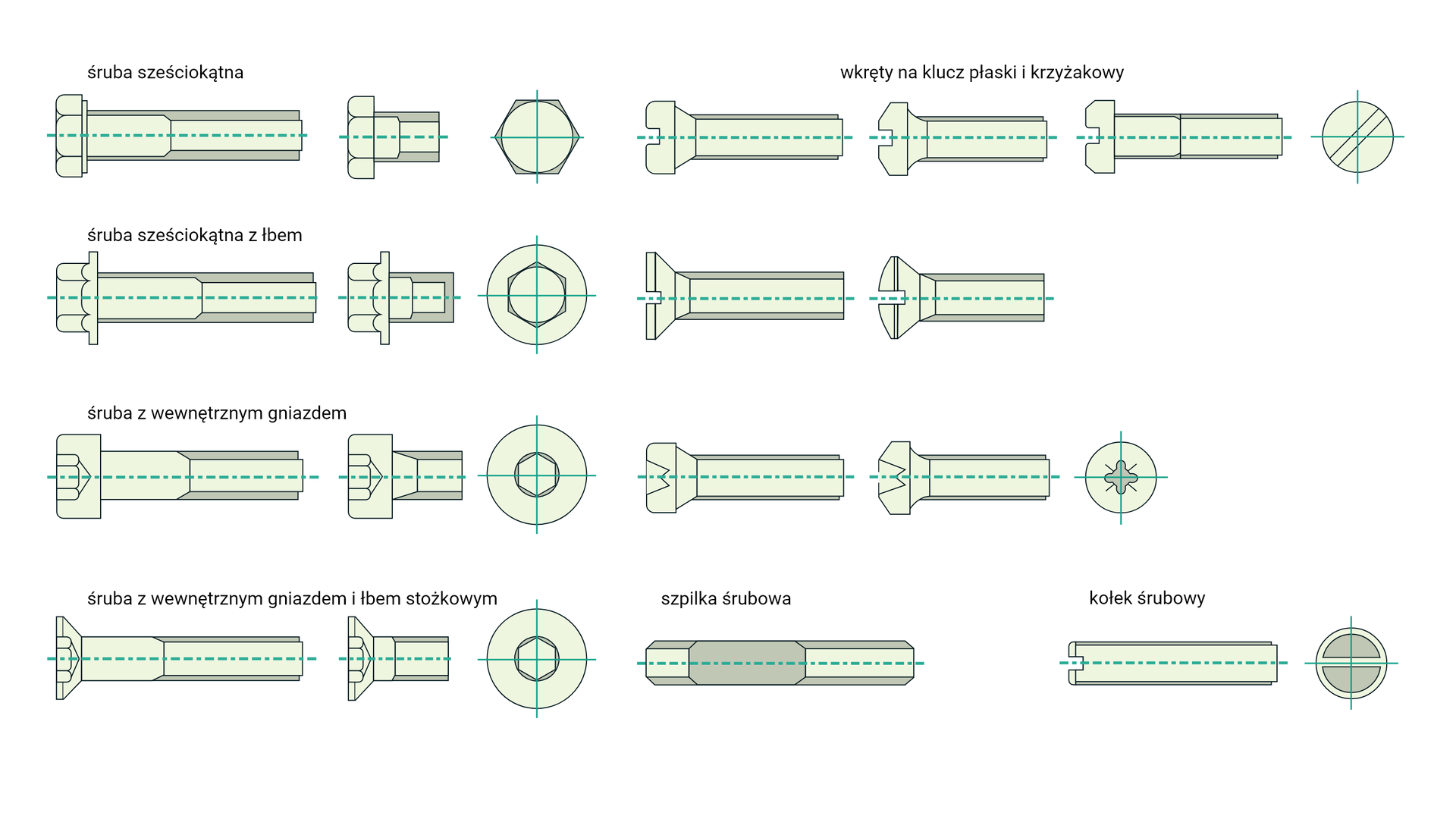
Śruby zbudowane są z łba/trzpienia oraz z gwintu. Podzielić je można na kilka kategorii:
Śruby z łbem
sześciokątnym,
czworokątnym,
trójkątnym,
grzybkowym,
kulistym,
młoteczkowym,
walcowym,
walcowym soczewkowym,
walcowym radełkowanym,
stożkowym,
stożkowym soczewkowym,
oczkowym,
skrzydełkowym,
z uchem,
bez łba.
Śruby z trzpieniem
równym średnicy gwintu,
zbliżonym do średnicy gwintu,
pasowanym.
Śruby z końcem
płaskim,
soczewkowym,
ściętym,
stożkowym,
wgłębionym,
z czopem (płaskim, walcowym, walcowym z otworem do zawleczki, soczewkowym, stożkowym).
Śruby z gniazdem
bez gniazda,
sześciokątnym,
rowkiem do wkrętaka,
wgłębieniem krzyżowym.
Śruby z gwintem
na całej długości,
z częściowym gwintem.
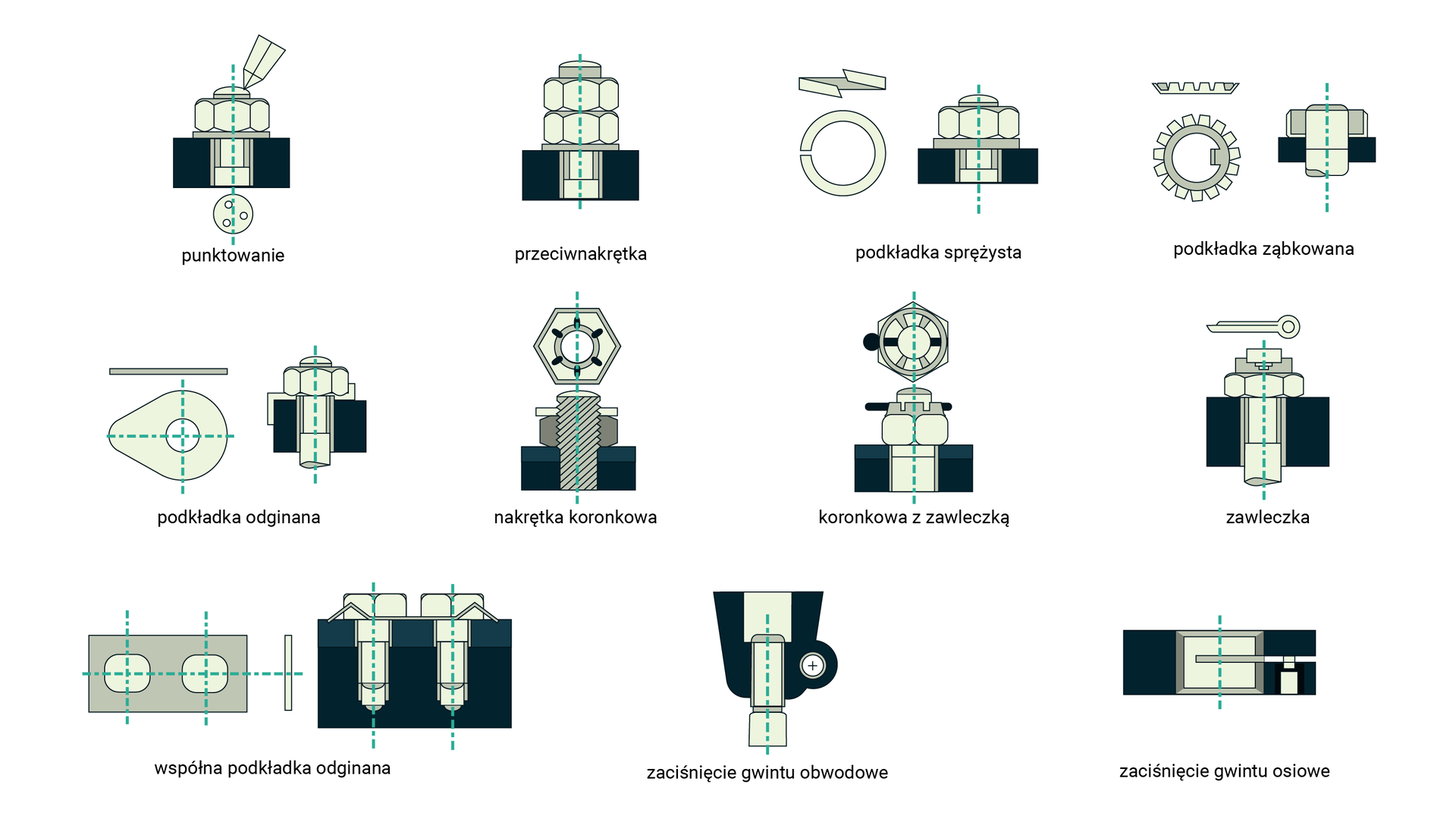
Nakrętki pozostają istotnym elementem używanym razem ze śrubami, zaś poprawny dobór nakrętek do śruby oraz danej sytuacji jest kluczowy. Podziału nakrętek dokonuje się przede wszystkim ze względu na ich kształt.
Do najczęściej wykorzystywanych nakrętek zalicza się:
sześciokątne,
czworokątne,
okrągłe,
skrzydełkowe (motylkowe),
radełkowane,
ślepe,
wieńcowe,
złączne,
kwadratowe,
z uchem.
Połączenia kołkowe
Połączenia kołkowe są rodzajem łączenia mechanicznego, w którym elementy są połączone za pomocą specjalnych elementów zwanych kołkami. Kołki są walcowatymi, cylindrycznymi lub stożkowymi elementami, które są wciskane w otwory w połączonych elementach w celu zapewnienia trwałego i stabilnego połączenia.
W zależności od zastosowania i wymagań konstrukcyjnych istnieje kilka rodzajów połączeń kołkowych:
Kołki rozporowe (kołki sprężynowe): Służą do wykonywania czasowego połączenia między dwoma elementami, które można łatwo rozłączyć i ponownie połączyć. Wykonane są z elastycznego materiału, który pozwala na ich elastyczne ugięcie podczas wprowadzania do otworu.
Kołki tulejowe: Wykonane z metalu lub tworzywa sztucznego, służą do poprawy wytrzymałości otworów w drewnianych elementach, na przykład w drewnianych meblach, aby zapobiec zużyciu i rozszerzeniu się otworu w wyniku częstego używania śruby lub śrubki.
Kołki stożkowe: Mają kształt stożka i służą do precyzyjnego i trwałego łączenia dwóch elementów. Wprowadza się je w dokładnie wywiercone otwory w obu elementach, co zapewnia stabilność i dokładne dopasowanie.
Kołki do łączenia elementów drewnianych: Wykorzystuje się je do łączenia drewnianych belek, desek lub płyt w konstrukcjach drewnianych, takich jak meble, ramy czy belki dachowe.
Połączenia kołkowe charakteryzują się prostotą, ekonomicznością i łatwością montażu, co czyni je popularnym wyborem w wielu aplikacjach, zwłaszcza tam, gdzie wymagane jest mocne, trwałe i precyzyjne połączenie.
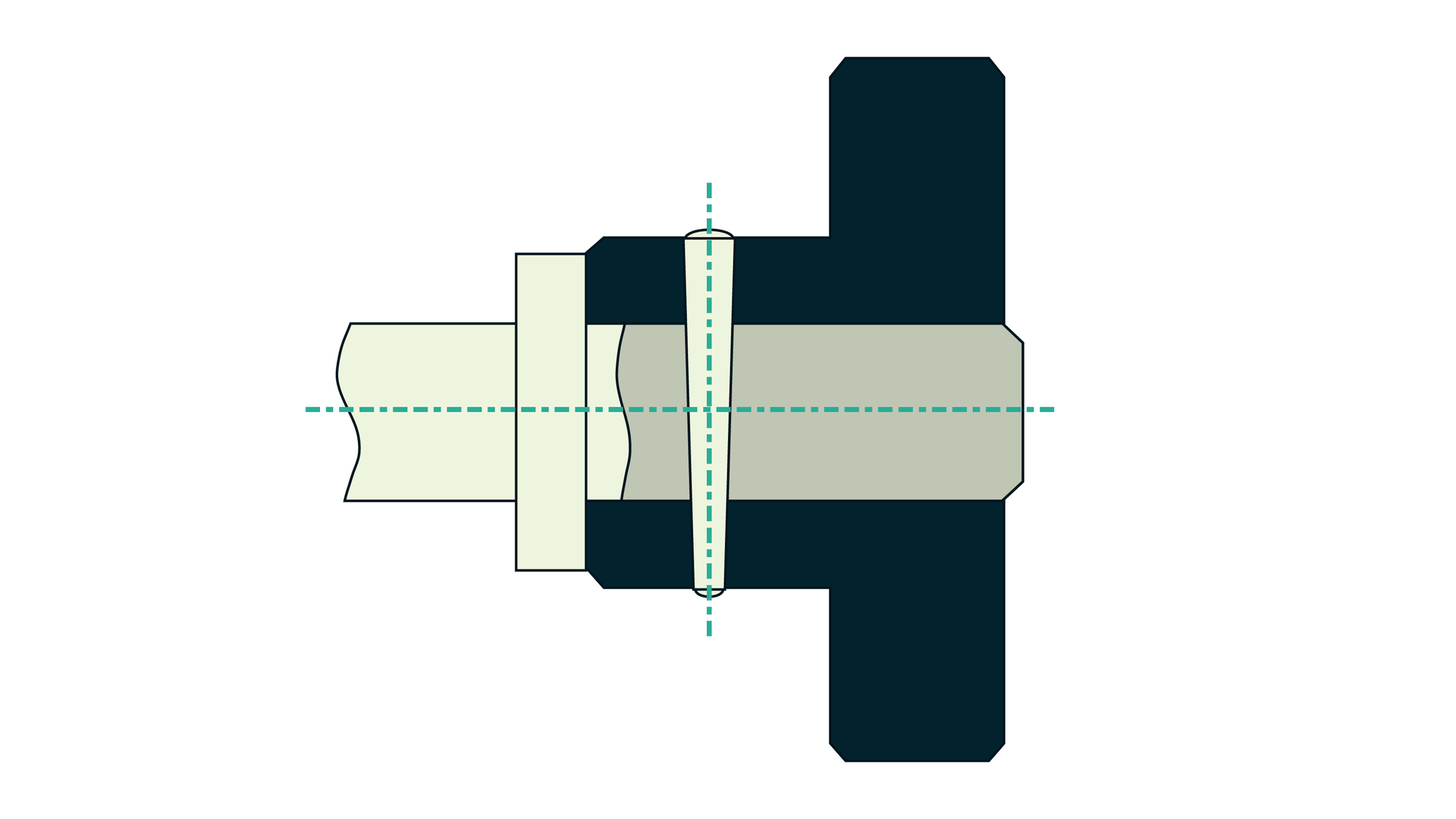
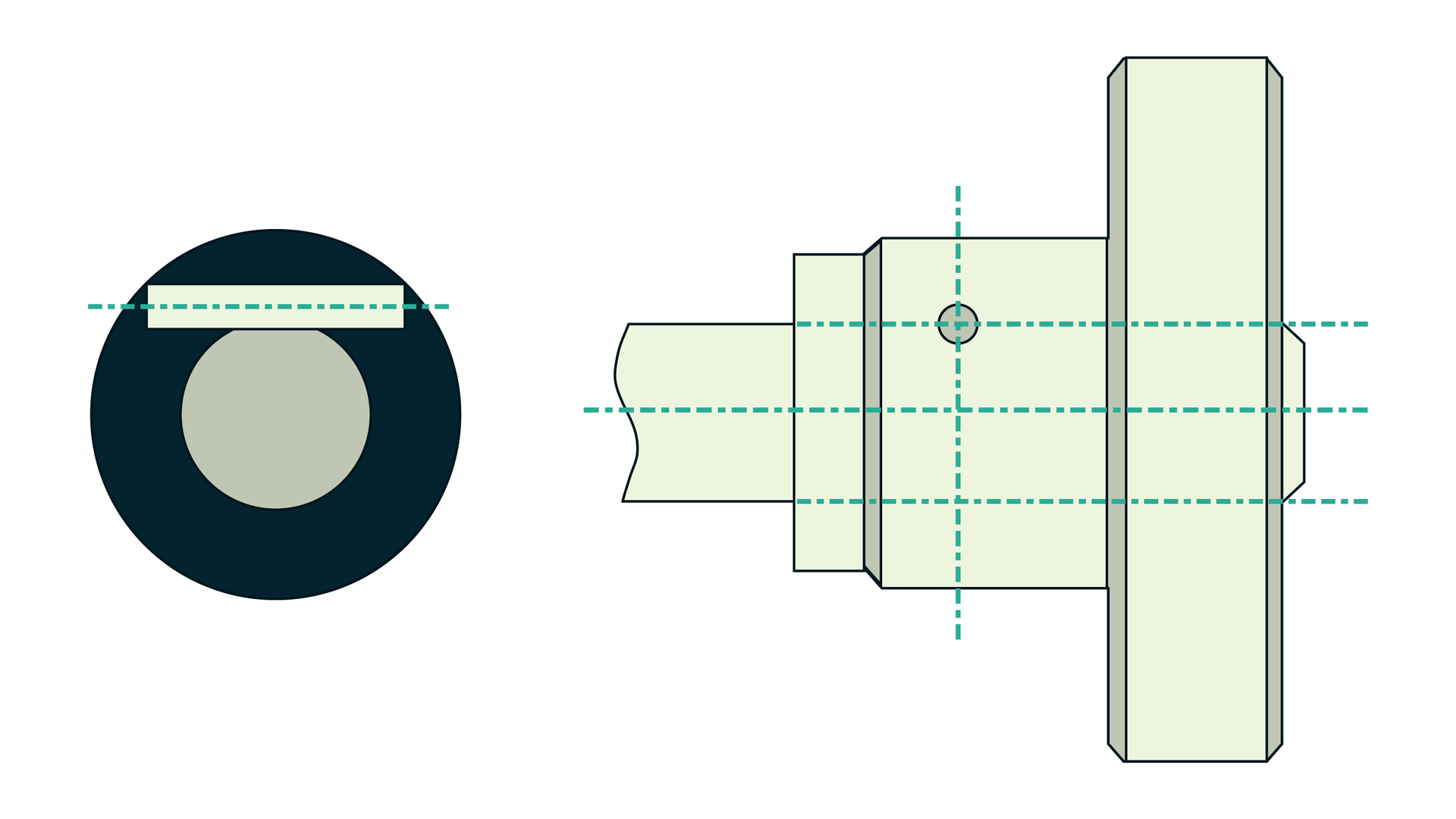
Połączenia sworzniowe
Połączenia sworzeniowe, nazywane również połączeniami sworzniami lub połączeniami osiowymi, są rodzajem łączenia mechanicznego stosowanego w celu zapewnienia ruchu obrotowego lub liniowego między dwoma elementami. Sworznie są elementami walcowatymi, cylindrycznymi lub stożkowymi, które umożliwiają względny ruch pomiędzy elementami, ale jednocześnie zapewniają im stabilność i trwałość.
Podstawowym elementem połączenia sworzeniowego jest sworzeń, który jest wprowadzany w dokładnie wywiercone otwory w obu łączonych elementach. Sworzeń może mieć różne rozmiary i kształty, a jego wybór zależy od wymagań konstrukcyjnych i obciążeń, jakim ma sprostać połączenie.
Przykłady zastosowań połączeń sworzeniowych:
Połączenia zawiasowe: Sworzeń jest stosowany jako element łączący dwie części, które muszą mieć możliwość obrotowego ruchu względem siebie, jak w przypadku zawiasów drzwi czy klap.
Połączenia dźwigniowe: Sworzeń jest używany w mechanizmach dźwigniowych, takich jak klucze, narzędzia ręczne czy maszynowe, aby zapewnić precyzyjny i płynny ruch dźwigni.
Połączenia w układach zawieszenia: Sworzenie stosuje się w pojazdach jako element łączący różne części układu zawieszenia, co pozwala na amortyzację drgań i zapewnia płynne poruszanie się kół.
Połączenia w maszynach i urządzeniach przemysłowych: Sworzenie znajduje zastosowanie w różnych maszynach i urządzeniach, gdzie wymagane jest zapewnienie ruchu osiowego lub obrotowego między częściami.
Podobnie jak w przypadku innych połączeń mechanicznych, wybór odpowiedniego rodzaju i rozmiaru sworznia oraz odpowiednie dopasowanie i montaż są kluczowe dla zapewnienia trwałego i bezpiecznego działania połączenia sworzeniowego.
Połączenia wpustowe
Połączenia wpustowe, nazywane również połączeniami wkładowymi lub wpustowo‑wkładkowymi, są rodzajem łączenia mechanicznego wykorzystywanego do połączenia dwóch elementów w taki sposób, że jeden element (wpust) jest wprowadzany do odpowiedniego otworu lub wyżłobienia w drugim elemencie (wpustowym). Połączenia wpustowe są używane do zapewnienia stabilności i trwałości między elementami, które mają względny ruch obrotowy lub liniowy.
Podstawowymi elementami połączenia wpustowego są:
Wpust: Jest to element, który jest wprowadzany do odpowiedniego wyżłobienia lub otworu w elemencie wpustowym. Wpust może mieć różne kształty, na przykład walcowy, prostokątny, stożkowy itp.
Element wpustowy: Jest to element, który posiada otwór lub wyżłobienie, w którym umieszczany jest wpust. Element wpustowy może być wykonany z bardziej odpornego materiału, takiego jak stal, w celu zwiększenia wytrzymałości połączenia.
Przykłady zastosowań połączeń wpustowych:
Połączenia w wałach i piastach: Połączenia wpustowe są często stosowane w wałach i piastach maszyn, gdzie wpust jest umieszczany w odpowiednio wyżłobionym otworze w piastach, co pozwala na przekazywanie momentu obrotowego między tymi elementami.
Połączenia w osiach i buławkach: Wpustowe połączenia są również używane w osiach i buławkach, które wymagają precyzyjnego i trwałego łączenia.
Połączenia w mechanizmach transmisyjnych: Wpustowe połączenia są często stosowane w mechanizmach transmisyjnych, które przenoszą ruch między różnymi częściami maszyn.
Połączenia w konstrukcjach drewnianych: Połączenia wpustowe są tradycyjnie wykorzystywane w stolarstwie i konstrukcjach drewnianych, gdzie zapewniają trwałe i estetyczne łączenia elementów drewnianych.
Wpustowe połączenia charakteryzują się wytrzymałością, dokładnym dopasowaniem i łatwością montażu, co sprawia, że są popularnym wyborem w wielu aplikacjach, gdzie wymagane jest precyzyjne i stabilne połączenie między elementami.
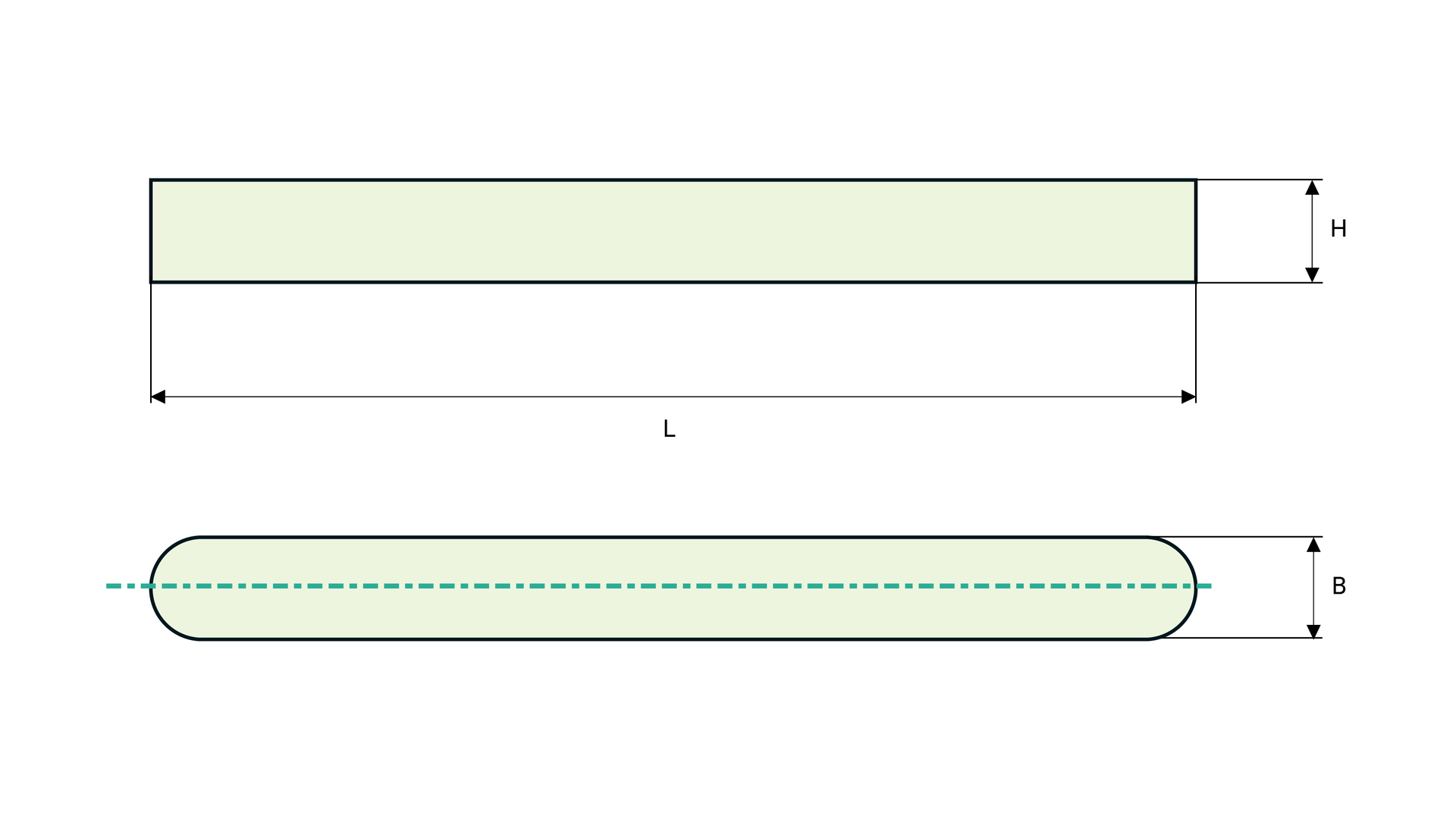
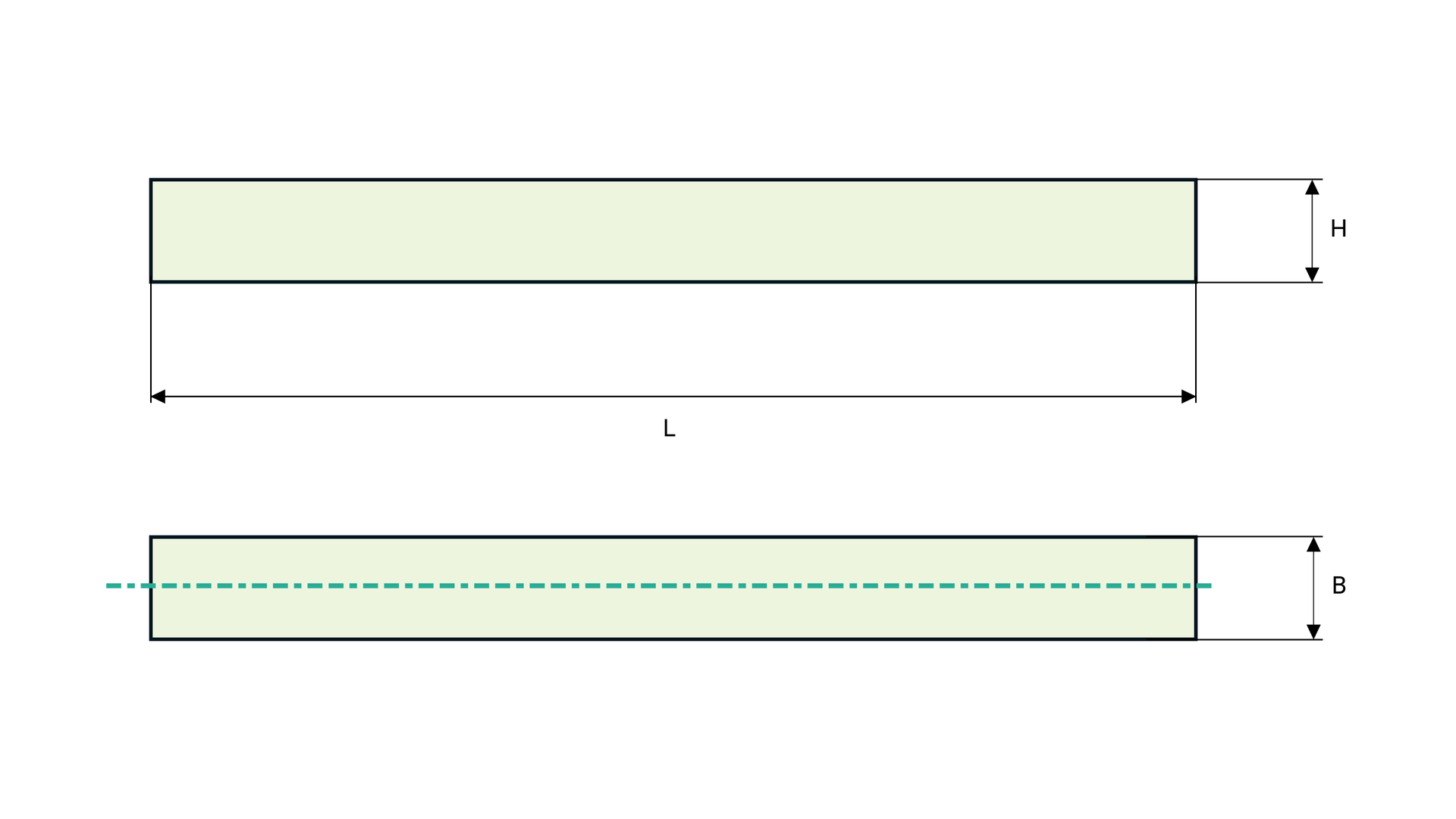
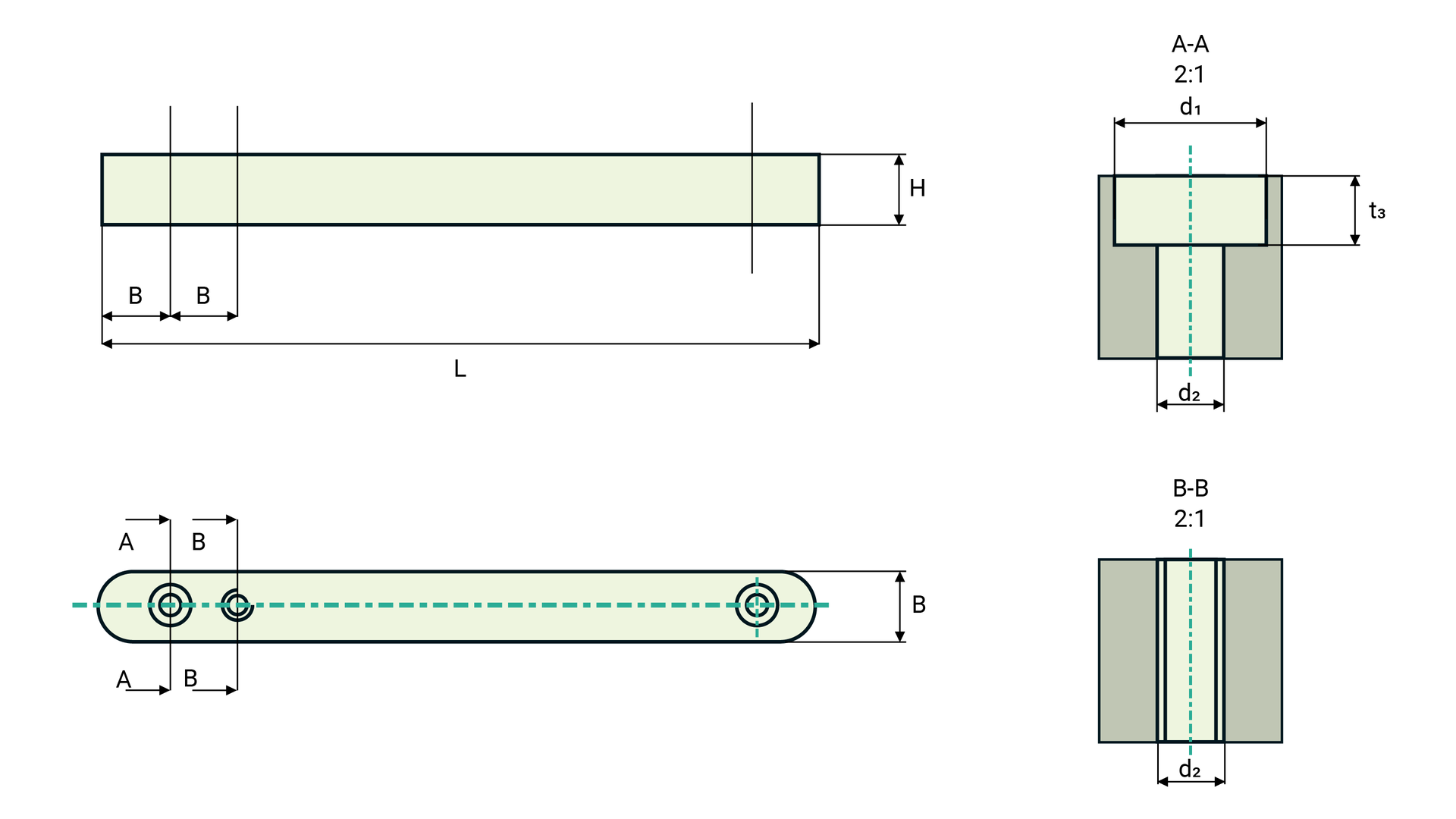
Połączenia wielowypustowe
Połączenia wielowypustowe są rodzajem łączenia mechanicznego, w którym używa się wielu wpustów i odpowiednich otworów wpustowych w celu połączenia dwóch elementów. Wielowypustowe połączenia są stosowane w celu zapewnienia większej trwałości i stabilności łączenia, zwłaszcza w przypadkach, gdy standardowe połączenia wpustowe nie zapewniają wystarczającej wytrzymałości lub dokładnego dopasowania.
Główne cechy połączeń wielowypustowych:
Większa wytrzymałość: Dzięki użyciu wielu wpustów i odpowiednich otworów wpustowych, połączenia wielowypustowe charakteryzują się większą wytrzymałością i zdolnością do przenoszenia większych obciążeń w porównaniu z pojedynczymi połączeniami wpustowymi.
Precyzyjne dopasowanie: Wielowypustowe połączenia pozwalają na dokładne dopasowanie elementów, co jest szczególnie ważne w przypadku maszyn i urządzeń wymagających wysokiej precyzji.
Względny ruch między elementami: Mimo większej liczby wpustów, połączenia wielowypustowe nadal pozwalają na względny ruch między łączonymi elementami, jeśli jest to wymagane.
Przykłady zastosowań połączeń wielowypustowych:
Połączenia w wałach: Wielowypustowe połączenia są często stosowane w wałach maszyn i urządzeń przemysłowych, gdzie wymagana jest wysoka wytrzymałość i precyzja.
Połączenia w łańcuchach przekładniowych: Wielowypustowe połączenia są używane w mechanizmach transmisyjnych, które przenoszą ruch między różnymi elementami przekładni.
Połączenia w osiach i wałach kół: Wielowypustowe połączenia są także stosowane w osiach i wałach kół pojazdów, które muszą przenosić obciążenia wynikające z ruchu i obrotu kół.
Połączenia wielowypustowe są zaprojektowane w taki sposób, aby dostosować się do konkretnych wymagań konstrukcyjnych i obciążeń łączonych elementów. Dzięki ich zaletom są one stosowane w różnorodnych aplikacjach, w których wymagane są trwałe, precyzyjne i wytrzymałe połączenia między elementami.
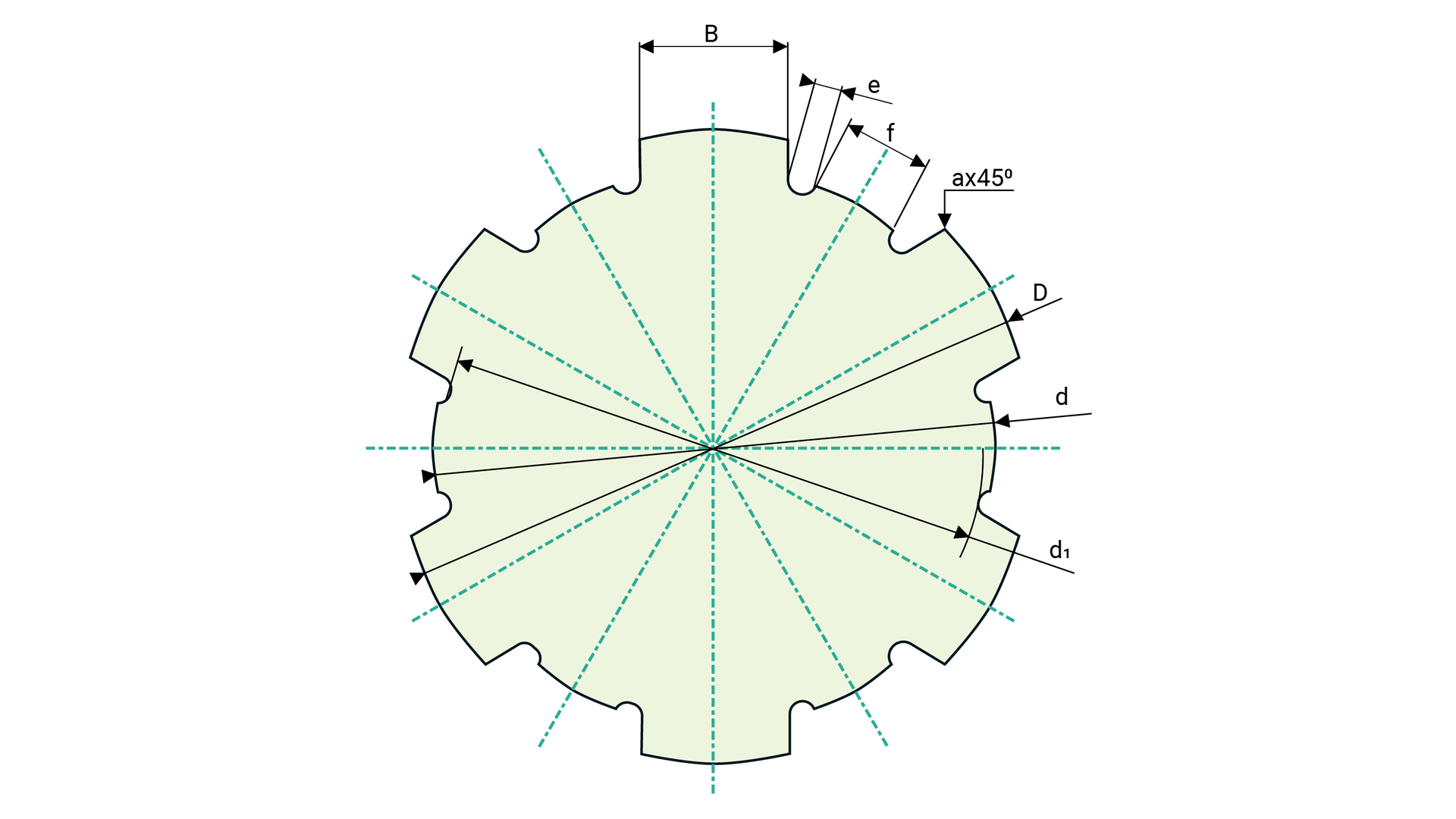
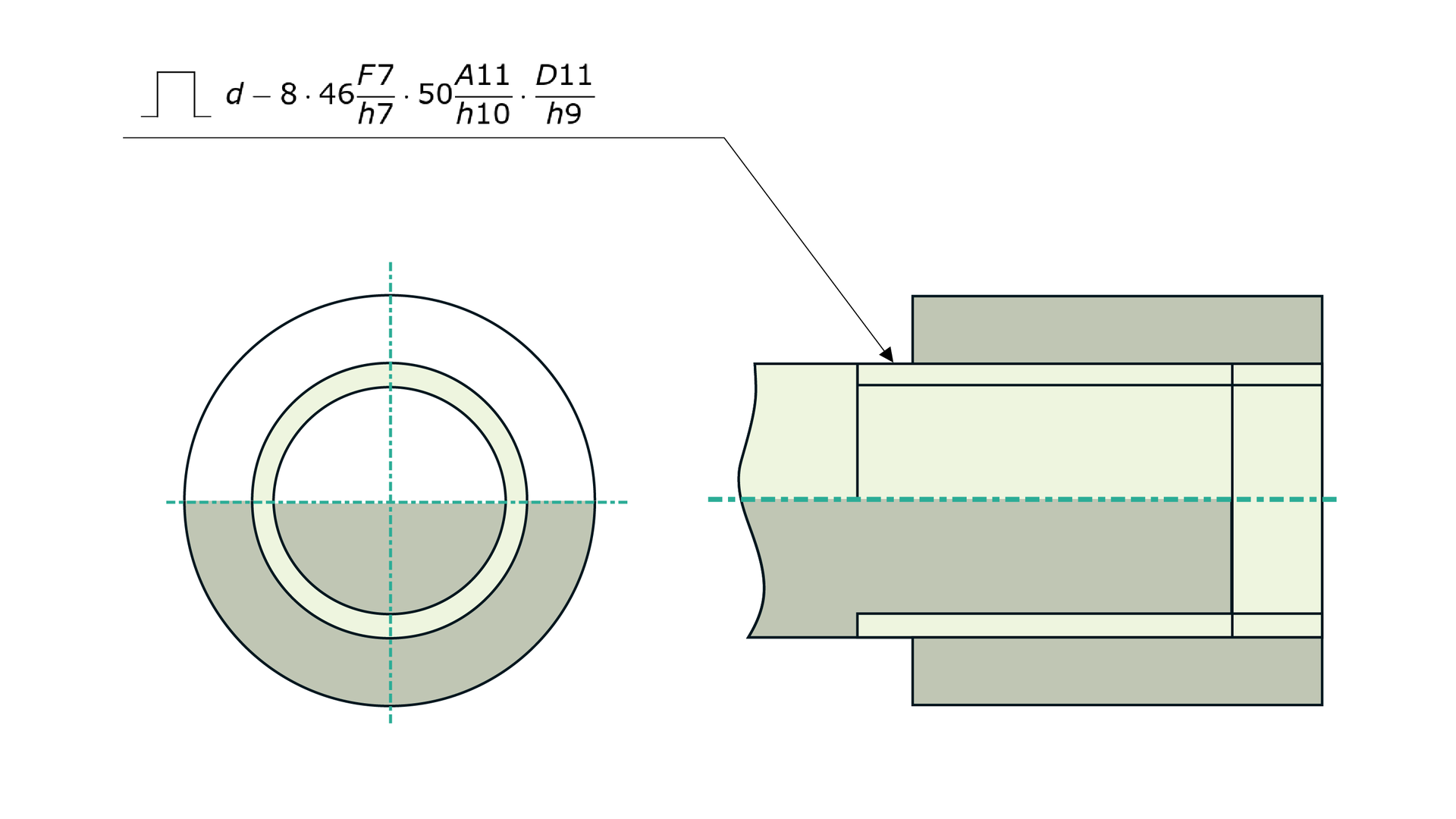
Powrót do spisu treściPowrót do spisu treści
Połączenia nierozłączne
Połączenia nitowane
Połączenia nitowane są rodzajem łączenia mechanicznego, w którym elementy są trwale łączone za pomocą nitów. Nity są metalowymi elementami walcowatymi, które są używane jako złączka do połączenia dwóch lub więcej elementów. Połączenia nitowane są szeroko stosowane w przemyśle i budownictwie ze względu na swoją wytrzymałość, trwałość i odporność na wibracje.
Proces nitowania polega na przeprowadzeniu następujących kroków:
Wywiercenie otworów: W łączonych elementach wywierca się otwory. Istnieją dwa rodzaje otworów: otwór główny, przez który wprowadza się nit, oraz otwór pomocniczy, który umożliwia formowanie główki nitu.
Wprowadzenie nitu: Następnie wprowadza się nit do otworu głównego, który jest odpowiednio dobrany pod względem rozmiaru i materiału w stosunku do materiałów łączonych.
Formowanie główki nitu: Na drugim końcu nitu wykonuje się odpowiednią operację, na przykład zgniatanie, aby utworzyć główkę, która utrzymuje elementy w połączeniu.
Spłaszczenie końcówki nitu: Czasami na końcu nitu wykonuje się spłaszczanie, które zapobiega jego wypadnięciu z połączenia.
Przykłady zastosowań połączeń nitowanych:
Przemysł motoryzacyjny: Połączenia nitowane są szeroko stosowane w produkcji pojazdów, zwłaszcza w konstrukcji nadwozia, zawieszenia i układów wydechowych.
Przemysł lotniczy: W lotnictwie połączenia nitowane są powszechnie wykorzystywane do łączenia różnych części kadłuba i skrzydeł.
Przemysł budowlany: W budownictwie połączenia nitowane są używane w konstrukcjach stalowych, mostach, konstrukcjach dachowych i innych elementach konstrukcyjnych.
Przemysł okrętowy: W konstrukcji statków i okrętów połączenia nitowane zapewniają trwałe połączenia nawet w trudnych warunkach morskich.
Połączenia nitowane są cenione ze względu na ich wytrzymałość, możliwość łączenia różnych materiałów oraz możliwość wykonywania połączeń w miejscach trudno dostępnych. Są one stosowane tam, gdzie wymagane jest solidne i trwałe połączenie, które jest odporne na oddziaływanie czynników zewnętrznych.
Połączenia spawane
Połączenia spawane są rodzajem łączenia trwałego, w którym dwa lub więcej elementów są połączone poprzez stopienie i złączenie ich za pomocą spoiny. Spoina jest materiałem pośredniczącym, który jest stosowany w stanie ciekłym lub plastycznym, a następnie stężałym w celu utworzenia trwałego połączenia między łączonymi elementami. Spawanie jest jedną z najczęściej stosowanych technik łączenia w różnych branżach, w tym w przemyśle metalowym, konstrukcyjnym, samochodowym, lotniczym, naftowym i wielu innych.
Proces spawania obejmuje następujące kroki:
Przygotowanie powierzchni: Przed przystąpieniem do spawania, elementy, które mają zostać połączone, muszą być odpowiednio przygotowane. Powierzchnie muszą być oczyszczone z rdzy, brudu i farb, aby zapewnić dobrą jakość spoiny.
Doprowadzenie do stopienia: W trakcie spawania, miejscami, które mają być połączone, jest doprowadzane do stopienia za pomocą odpowiedniej metody, takiej jak łuk elektryczny, płomień gazowy, laser lub wiązka elektronów.
Dodatkowy materiał spajający: W przypadku niektórych rodzajów spawania, jak np. spawanie metalu woskiem, dodatkowy materiał spajający jest używany do wypełnienia szczeliny między elementami w celu stworzenia spoiny.
Chłodzenie i stężenie: Po zakończeniu procesu spawania, stopiony materiał ochładza się, a spoina tężeje w celu utworzenia trwałego połączenia między elementami.
Przykłady zastosowań połączeń spawanych:
Spawanie metalu: Najczęściej stosowany rodzaj spawania, wykorzystywany w konstrukcjach stalowych, samochodowych, lotniczych, mostach i wielu innych aplikacjach.
Spawanie tworzyw sztucznych: Wykorzystywane w przemyśle plastikowym, wytwarzanie elementów z tworzyw sztucznych, rur i zbiorników.
Spawanie aluminium: Często stosowane w przemyśle lotniczym i motoryzacyjnym ze względu na lekkość i wytrzymałość aluminium.
Spawanie punktowe: Wykorzystywane w produkcji samochodów do połączenia różnych elementów nadwozia.
Spawanie jest popularną metodą łączenia, ponieważ pozwala na tworzenie trwałych i wytrzymałych połączeń między elementami. W zależności od materiałów, które mają być połączone, oraz wymagań konstrukcyjnych, istnieje wiele różnych technik spawania, z których każda ma swoje zastosowanie i charakterystyczne cechy.
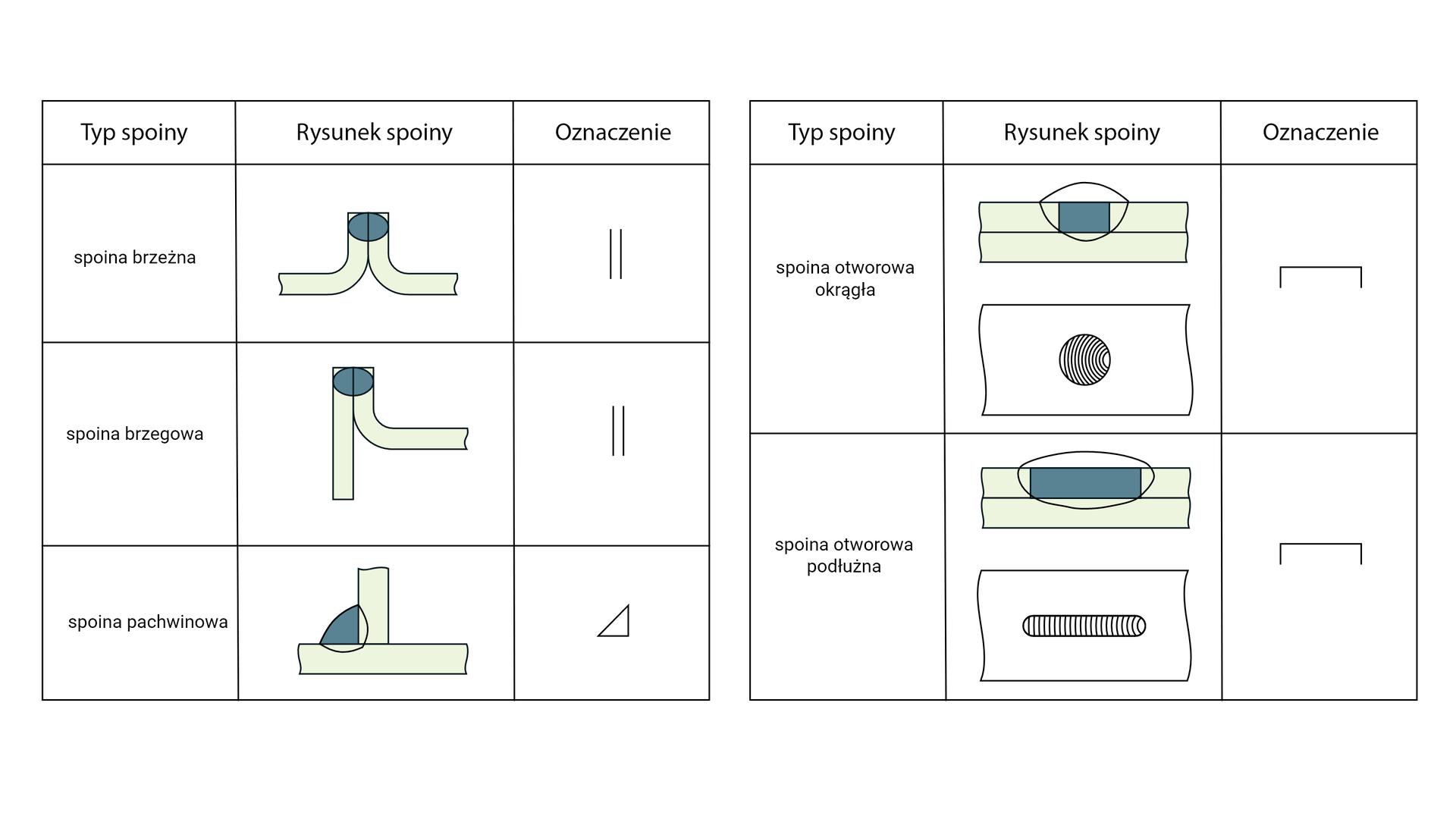
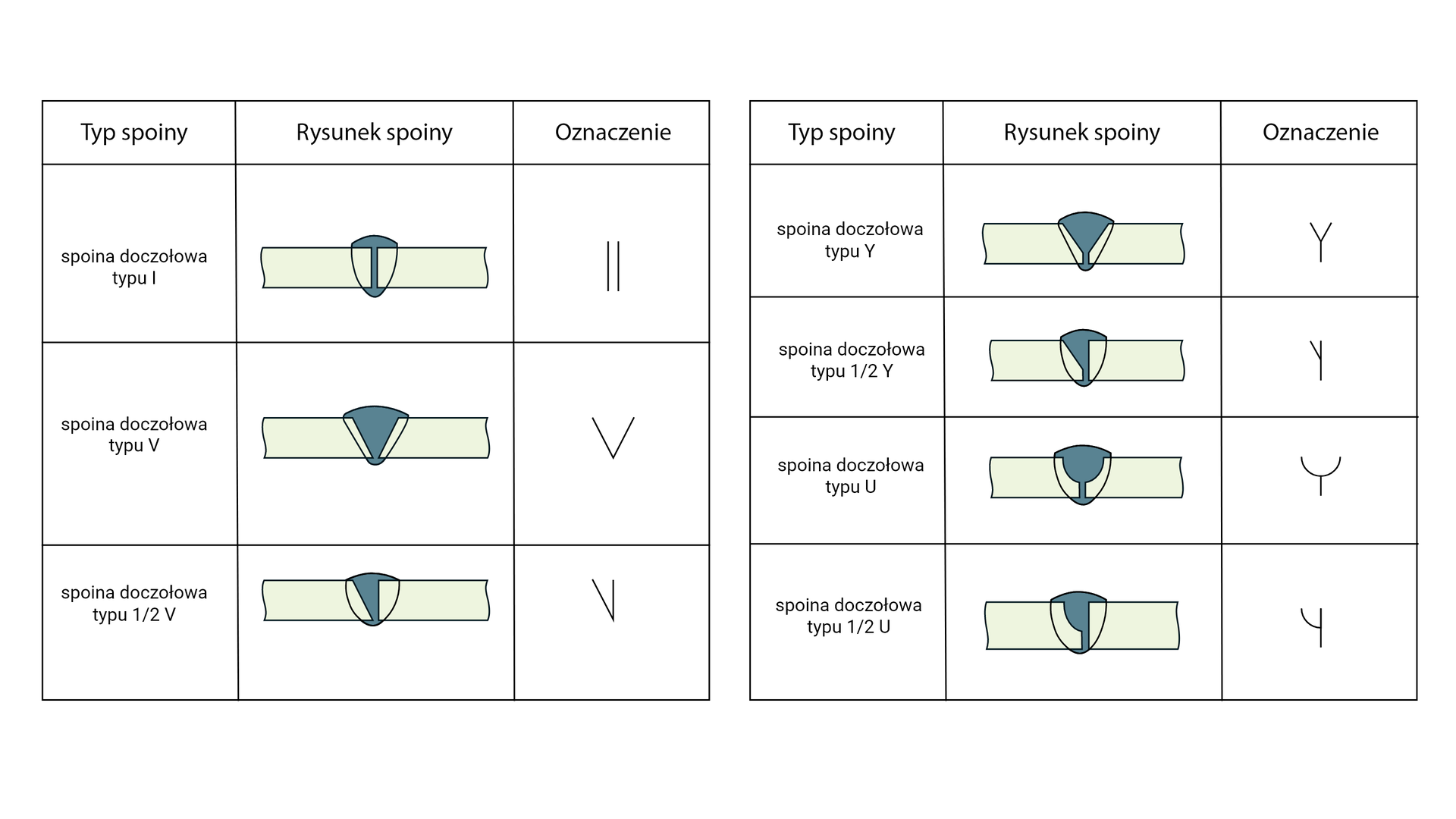
Połączenia lutowane
Połączenia lutowane są rodzajem łączenia trwałego, w którym dwa lub więcej elementy są połączone za pomocą stopu lutowania. Lutowanie to proces, w którym stop lutowny (nazywany również lutem) jest używany jako materiał pośredniczący do połączenia elementów. Lut jest metalowym stopem o niższym punkcie topnienia niż same łączone elementy, co pozwala na spoinowanie elementów bez ich stopienia.
Proces lutowania obejmuje następujące kroki:
Przygotowanie powierzchni: Przed przystąpieniem do lutowania, elementy, które mają zostać połączone, muszą być odpowiednio oczyszczone z tłuszczu, oleju, rdzy i brudu, aby zapewnić dobre przyleganie lutu.
Podgrzanie elementów: Elementy, które mają zostać połączone, są podgrzewane do odpowiedniej temperatury, która jest niższa od temperatury topnienia lutu.
Wprowadzenie lutu: Gdy elementy są odpowiednio podgrzane, lut jest stosowany na miejsce połączenia, gdzie topi się i wypełnia szczeliny między elementami.
Chłodzenie i stężenie: Po zakończeniu procesu lutowania lut tężeje, tworząc trwałą i wytrzymałą spoinę między elementami.
Istnieją różne techniki lutowania, w tym lutowanie miękkie, lutowanie twarde, które różnią się rodzajem stosowanego lutu i temperaturą procesu lutowania. Wybór odpowiedniej techniki lutowania zależy od materiałów, które mają zostać połączone i wymagań konstrukcyjnych.
Przykłady zastosowań połączeń lutowanych:
Elektronika: Lutowanie jest szeroko stosowane w przemyśle elektronicznym do łączenia elementów elektronicznych, takich jak płytki drukowane, kondensatory, rezystory i przewody.
Przemysł motoryzacyjny: Lutowanie jest również używane w produkcji pojazdów, szczególnie w układach chłodzenia, klimatyzacji i układach wydechowych.
Przemysł metalowy: Lutowanie jest stosowane do łączenia różnych elementów metalowych, takich jak rury, przewody, złącza i rury.
Przemysł złotniczy i jubilerski: Lutowanie jest używane do łączenia elementów biżuterii i drobnych przedmiotów złotniczych.
Połączenia lutowane są popularne ze względu na swoją trwałość, estetykę i możliwość łączenia różnych materiałów, takich jak metale, miedź, stal, srebro, złoto ii inne. Ponadto lutowanie jest stosunkowo łatwe do wykonania i nie wymaga dużej ilości wyposażenia, co sprawia, że jest szeroko stosowane w różnych dziedzinach.
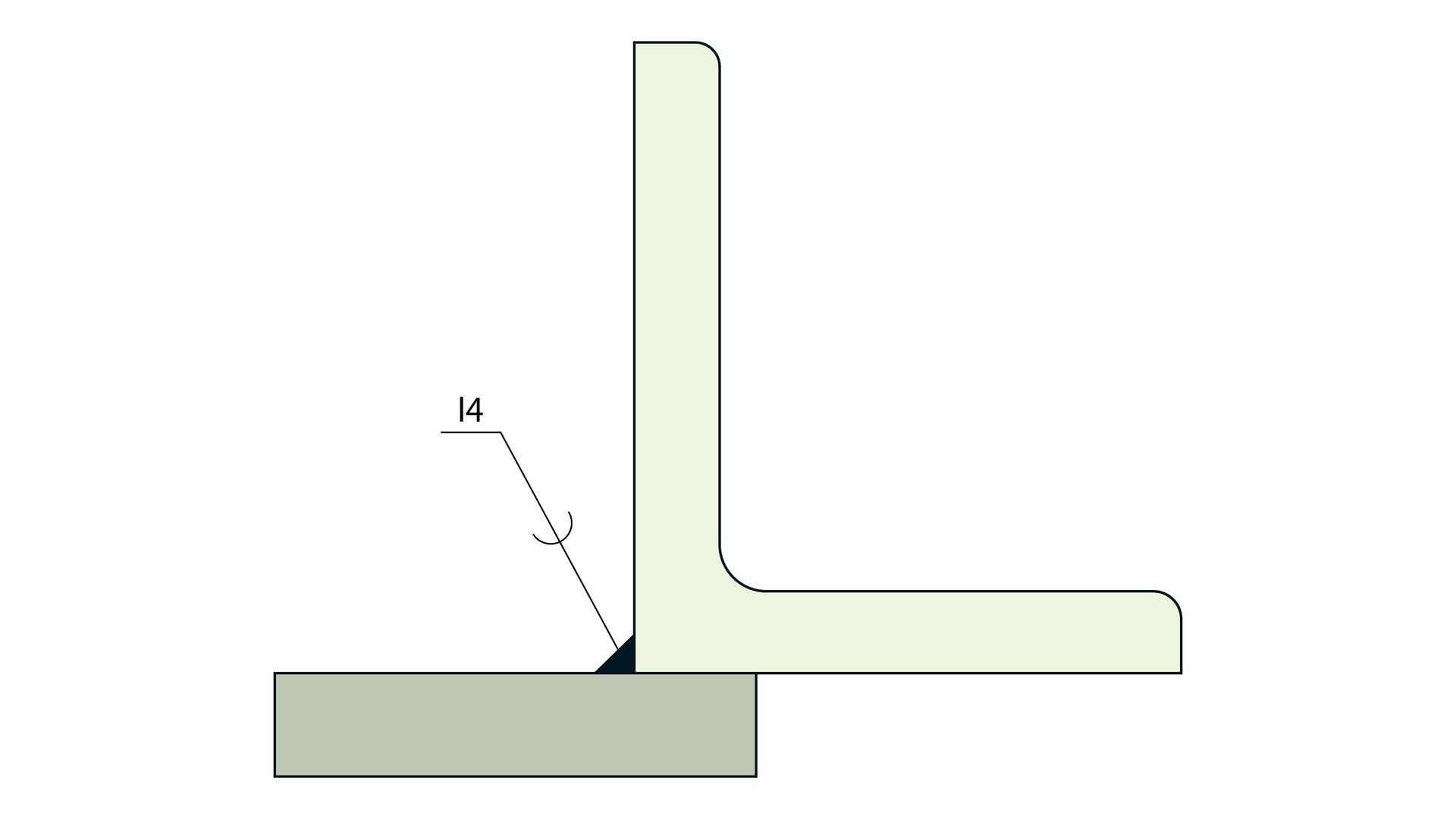
Połączenia zgrzewane
Połączenia zgrzewane są rodzajem łączenia trwałego, w którym dwa lub więcej elementów jest łączonych poprzez stopienie i złączenie ich za pomocą odpowiedniego źródła ciepła, bez dodatkowych materiałów spajających. Proces zgrzewania polega na podgrzewaniu elementów do odpowiedniej temperatury, a następnie łączeniu ich, aby powstało trwałe połączenie.
Istnieje kilka różnych technik zgrzewania, z których każda ma swoje zastosowanie w zależności od rodzaju materiałów, grubości elementów i wymagań konstrukcyjnych. Najczęściej stosowanymi technikami zgrzewania są:
Zgrzewanie oporowe: Jest to technika zgrzewania, w której elementy są podgrzewane przez prąd elektryczny przepływający przez miejsce łączenia. Prąd elektryczny powoduje lokalne nagrzanie elementów, a następnie łączenie ich.
Zgrzewanie tarczowe: Technika ta wykorzystuje ciśnienie i tarcze obrotowe do nagrzewania i połączenia elementów.
Zgrzewanie indukcyjne: W tej technice elementy są podgrzewane przez indukcyjne pole magnetyczne, co powoduje stopienie i połączenie ich.
Zgrzewanie laserowe: Wykorzystuje wiązkę lasera do podgrzewania i połączenia elementów w precyzyjny sposób.
Przykłady zastosowań połączeń zgrzewanych:
Przemysł motoryzacyjny: Zgrzewanie jest szeroko stosowane w przemyśle motoryzacyjnym do łączenia elementów w konstrukcji pojazdów, takich jak nadwozia, rury i inne elementy.
Przemysł metalowy: Zgrzewanie jest powszechnie używane do łączenia różnych elementów metalowych, takich jak blachy, rury, druty i inne elementy.
Przemysł elektrotechniczny: Zgrzewanie jest stosowane w produkcji przewodów elektrycznych, złączy, elementów grzewczych i innych komponentów elektrotechnicznych.
Przemysł naftowy i gazowy: Zgrzewanie jest używane w przemyśle naftowym i gazowym do łączenia rur w infrastrukturze wydobywczej i przesyłowej.
Połączenia zgrzewane charakteryzują się wytrzymałością, odpornością na wibracje i korozję oraz brakiem konieczności stosowania dodatkowych materiałów spajających. Są one szeroko stosowane w przemyśle, zwłaszcza tam, gdzie wymagane są trwałe i wytrzymałe połączenia między elementami, które są poddawane dużej eksploatacji i obciążeniom mechanicznym.
Połączenia klejone
Połączenia klejone są rodzajem łączenia trwałego, w którym dwa lub więcej elementy są połączone za pomocą kleju lub adhezji. Klejony połączenia są tworzone przez złączenie powierzchni łączonych elementów za pomocą odpowiedniego kleju lub klejów, które następnie utwardzają się, tworząc trwałą i wytrzymałą spoinę.
Proces klejenia obejmuje następujące kroki:
Przygotowanie powierzchni: Przed przystąpieniem do klejenia, elementy, które mają zostać połączone, muszą być odpowiednio oczyszczone z tłuszczu, oleju, kurzu i brudu, aby zapewnić dobrą przyczepność kleju.
Nakładanie kleju: Klej jest nakładany na jedną lub obie powierzchnie łączonych elementów. Klej może być stosowany w płynnej, pastowej lub w postaci taśmy.
Sklejenie elementów: Po nałożeniu kleju, elementy są sklejane razem w odpowiedniej pozycji, a następnie zaciśnięte lub przytrzymane, aby zapewnić prawidłowe dopasowanie i kontakt powierzchni.
Utwardzenie kleju: Klej utwardza się w określonym czasie, tworząc trwałą i wytrzymałą spoinę między elementami.
Przykłady zastosowań połączeń klejonych:
Przemysł meblarski: Klejenie jest szeroko stosowane w produkcji mebli do łączenia różnych elementów drewnianych i płytowych.
Przemysł motoryzacyjny: Połączenia klejone są również używane w przemyśle motoryzacyjnym do produkcji samochodów, gdzie klejonych jest wiele elementów, takich jak szyby, panele karoserii, elementy wnętrza itp.
Przemysł elektroniczny: Klejenie jest stosowane w produkcji urządzeń elektronicznych, gdzie łączy się różne komponenty elektroniczne.
Przemysł konstrukcyjny: Połączenia klejone są używane w konstrukcjach budowlanych, zwłaszcza tam, gdzie tradycyjne metody łączenia, takie jak spawanie lub nitowanie, są niewskazane.
Połączenia klejone charakteryzują się równomiernym rozkładem obciążeń, estetycznym wyglądem, brakiem widocznych złączy czy spoin oraz możliwością łączenia różnych materiałów, takich jak drewno, metal, tworzywa sztuczne, szkło i inne. Są one stosowane w różnych branżach ze względu na swoją wszechstronność i trwałość połączeń.
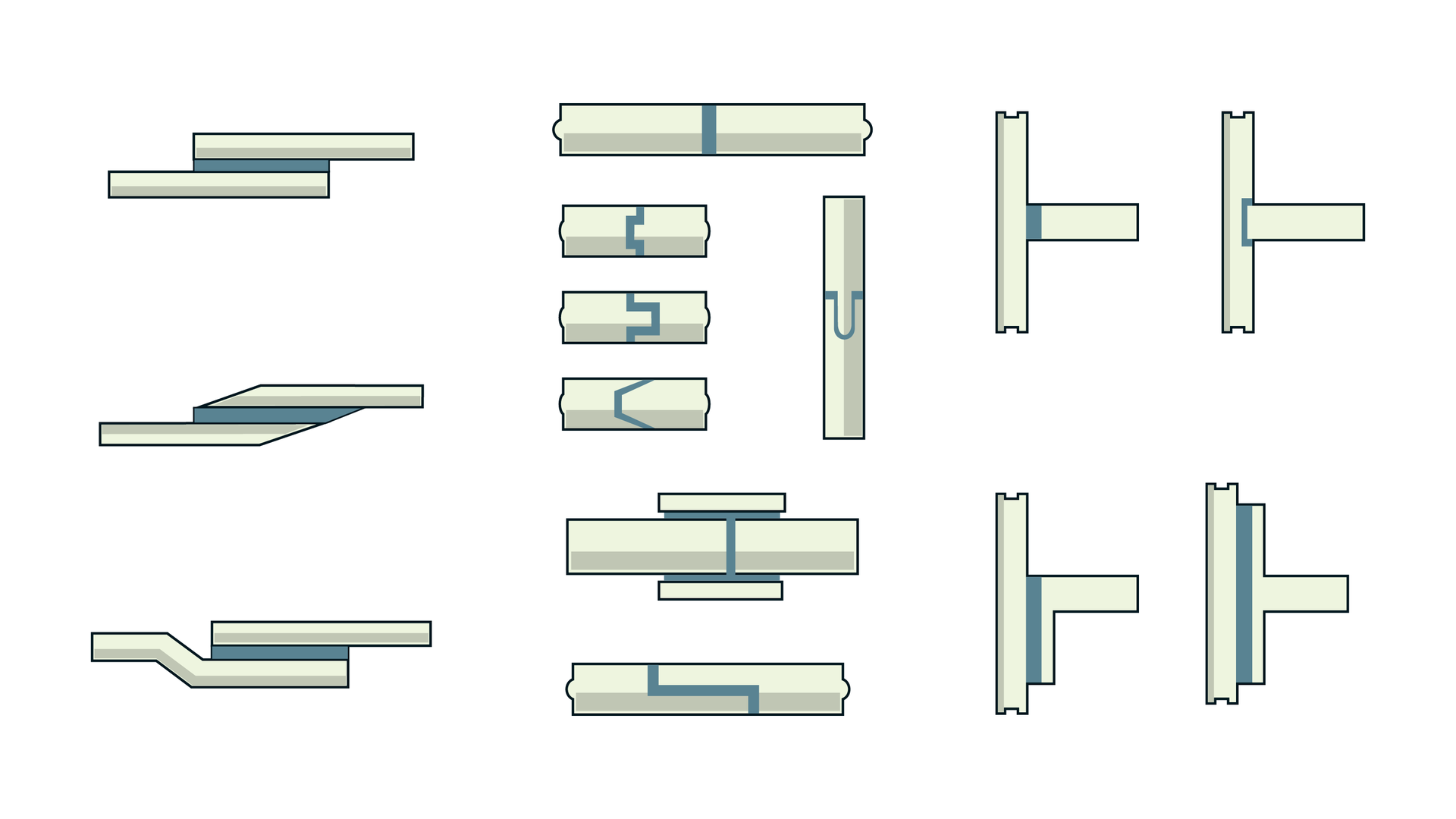
Połączenia wciskowe
Połączenia wciskowe, nazywane również połączeniami na wcisk lub połączeniami tłocznymi, to rodzaj łączenia mechanicznego, w którym jeden element jest wciskany lub wciśnięty w otwór drugiego elementu w celu utworzenia trwałego i bezpiecznego połączenia. Wciskanie odbywa się za pomocą odpowiedniej siły lub narzędzi, które umożliwiają osadzenie elementu wciskanego w ściśle dopasowanym otworze.
Połączenia wciskowe są używane w wielu zastosowaniach, a ich zaletami są szybki montaż, brak potrzeby stosowania dodatkowych elementów spajających (jak np. śruby, nity czy kleje), a także możliwość demontażu połączenia w razie potrzeby.
Przykłady zastosowań połączeń wciskowych:
Łożyska: Wciskanie łożysk to powszechna metoda łączenia wałów z obudową, umożliwiająca swobodny obrót łożyska.
Osłony i obudowy: Wciskane połączenia są używane do montażu osłon i obudów w maszynach i urządzeniach.
Elementy metalowe i plastikowe: Połączenia wciskowe są wykorzystywane do łączenia różnych elementów metalowych i plastikowych w różnych branżach.
Przemysł samochodowy: Wciskane połączenia są często stosowane w przemyśle samochodowym, w montażu różnych elementów, takich jak panele karoserii czy elementy wnętrza.
Wciskanie wymaga precyzyjnego wykonania otworów i odpowiedniego doboru siły, aby zapewnić trwałe i bezpieczne połączenie. W celu ułatwienia wciskania stosuje się różne narzędzia, takie jak prasy, młoty hydrauliczne czy prasy mechaniczne. Dzięki zaletom, jakie oferują, połączenia wciskowe są popularnym rozwiązaniem w wielu branżach, gdzie wymagane są szybkie, trwałe i precyzyjne połączenia między elementami.
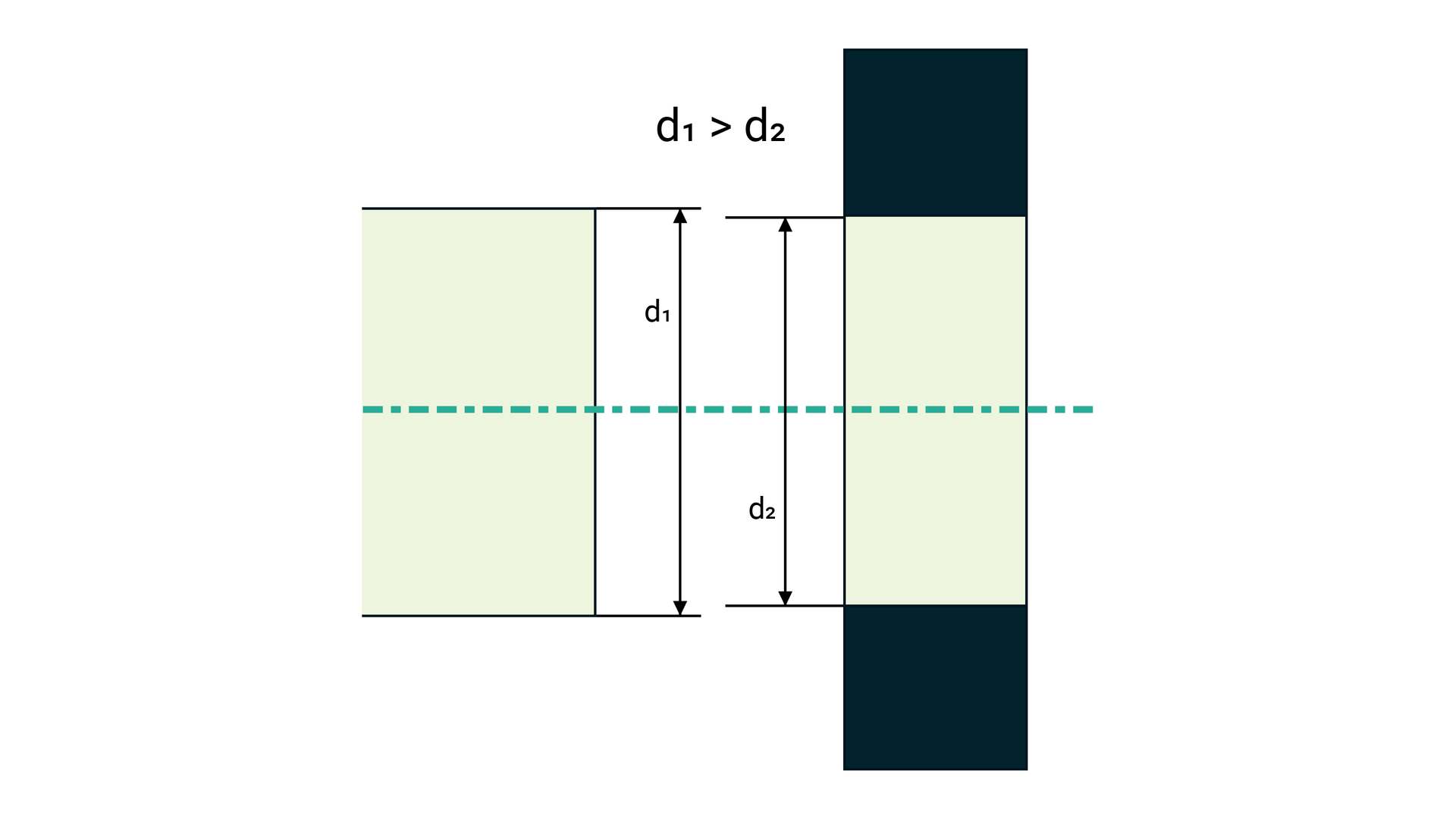
Powrót do spisu treściPowrót do spisu treści
Elementy łączników
Śruby
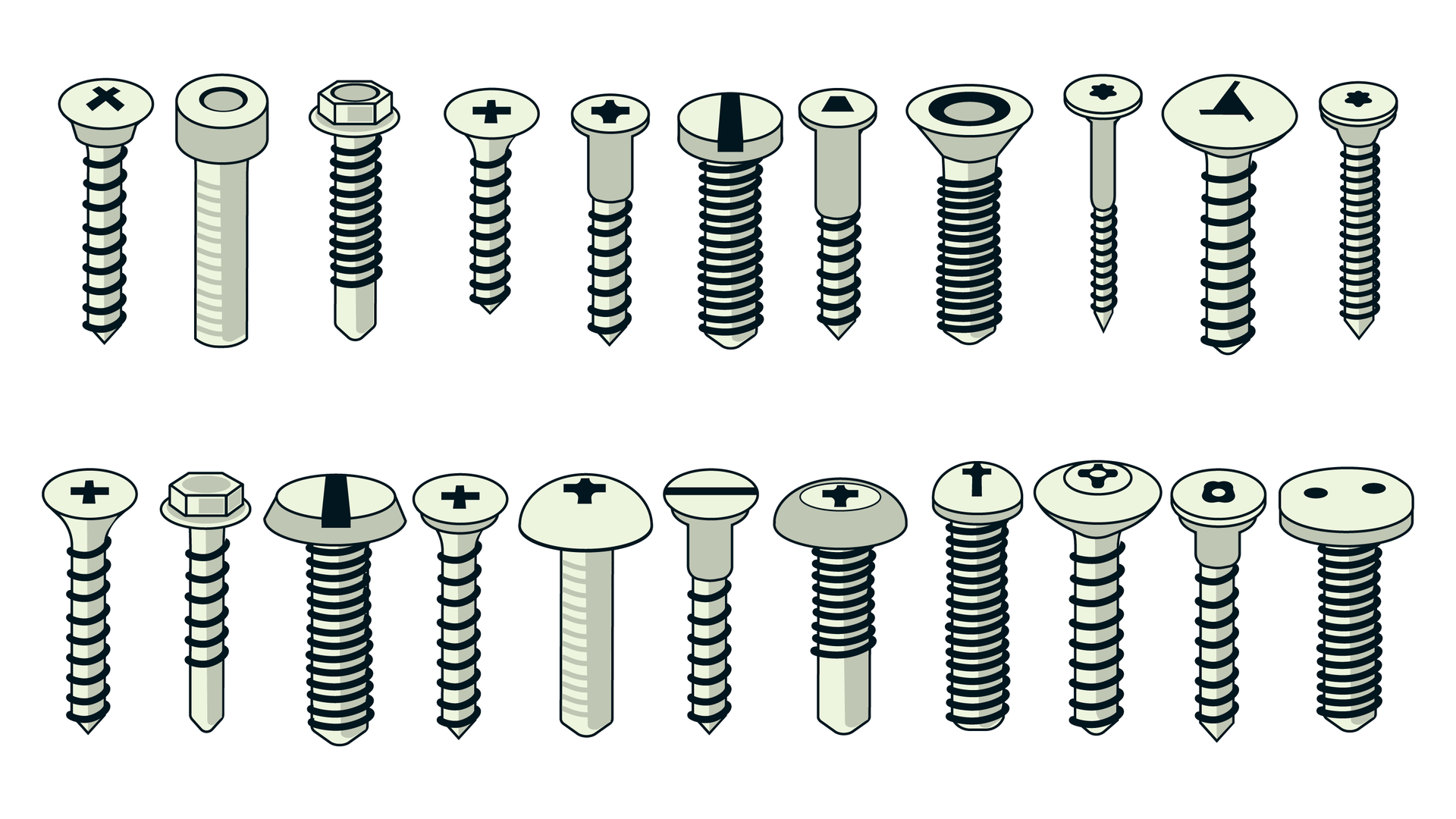
Śruba jest jednym z najbardziej powszechnie używanych elementów łączących w dziedzinie inżynierii i konstrukcji. Jest to element o kształcie walcowym zewnętrznym gwintem, który pasuje do wewnętrznego gwintu otworu w innym elemencie. Śruby składają się z kilku charakterystycznych części, które obejmują:
Gwint: Gwint to zewnętrzna, spiralna rzeźba na powierzchni trzonka śruby. W zależności od rodzaju śruby, gwint może mieć różne kształty, takie jak gwint metryczny, calowy, trapezowy, czy specjalny (np. gwint samoregulujący). Gwinty pozwalają na precyzyjne i stabilne łączenie śruby z elementem.
Trzonek: Trzonek to długi walec, który stanowi główną część śruby. Jego długość może się różnić w zależności od zastosowania i wymagań konstrukcyjnych. Trzonek może być zakończony łbem, który ułatwia manipulację śrubą za pomocą narzędzi.
Głowica: Głowica śruby to element znajdujący się na jednym z jej końców. Głowica może mieć różne kształty, takie jak sześciokątna (nakrętka) lub okrągła (w przypadku śrub imbusowych). Służy ona do wywierania odpowiedniej siły rotacyjnej podczas montażu i demontażu.
Nakrętka: Nakrętka to element łączący się z gwintem na trzonku śruby. Jest to element, który pozwala na dokręcanie lub odkręcanie śruby, umożliwiając łączenie lub rozłączanie elementów konstrukcji.
Śruby występują w różnych rodzajach, które są dostosowane do różnych zastosowań i wymagań technicznych:
Śruby metryczne: Najbardziej popularny rodzaj śrub o jednolitym profilu gwintu, stosowany powszechnie na całym świecie. Obejmuje różne klasy wytrzymałości, takie jak 4.6, 8.8, 10.9, 12.9, które określają ich wytrzymałość.
Śruby calowe: Często stosowane w Stanach Zjednoczonych i innych krajach, gdzie system jednostek calowych jest używany.
Śruby trapezowe: Wykorzystywane w mechanizmach przesuwu i prowadzeniu, gdzie wymagane jest precyzyjne przenoszenie ruchu.
Śruby samogwintujące: Specjalne śruby, które posiadają na swoim trzonku nacięcia, umożliwiające samoosadzanie w materiałach, takich jak drewno czy plastik.
Śruby różnią się także w zależności od rodzaju zakończenia głowicy i nakrętki, takie jak śruby z łbem sześciokątnym, śruby z łbem walcowym, śruby imbusowe, śruby z łbem stożkowym itp.
Ważnym elementem w konstrukcji i łączeniu śrub są odpowiednie gwinty w otworach, które muszą być dokładnie dopasowane do gwintu śruby, aby zapewnić trwałe i stabilne połączenie. Gwinty można również podzielić na różne typy, takie jak gwinty metryczne, calowe, trapezowe, rury, czy specjalne typy gwintów stosowane w przemyśle.
Podsumowując, śruby są niezwykle istotnym elementem łączącym w dziedzinie inżynierii i konstrukcji. Ich różnorodność pozwala na dostosowanie do różnych zastosowań, a precyzyjne połączenie i konstrukcja gwintów stanowią kluczowe czynniki dla wydajności i bezpieczeństwa w wielu aplikacjach inżynierskich.
Kołki
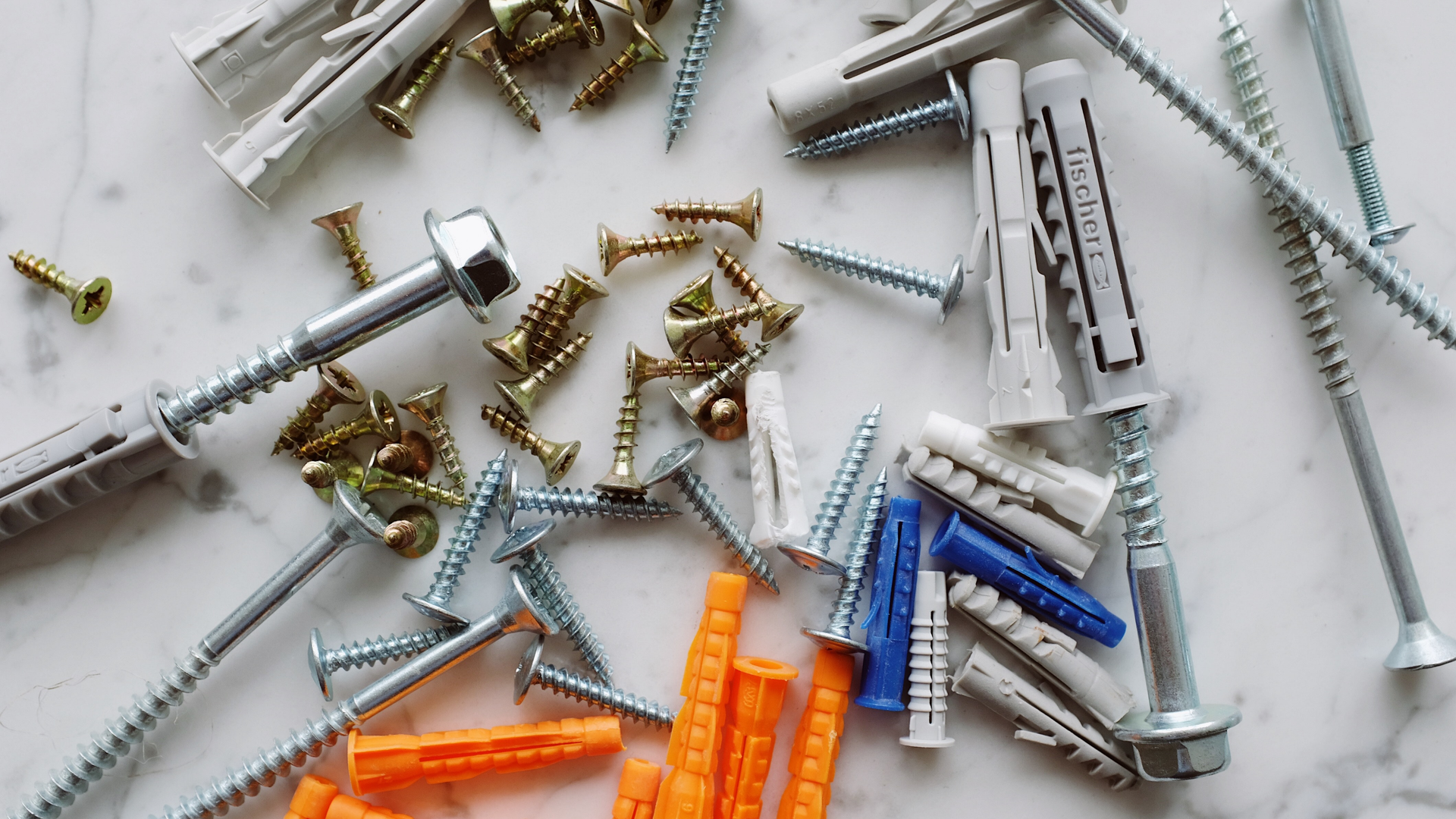
Rodzaje kołków:
Kołki rozporowe: Są to kołki stosowane do utrzymania obiektów w jednym miejscu. Składają się z ciała z rozszerzającym się zakończeniem. Po umieszczeniu kołka w otworze i odpowiednim nacisku na jego ciało, rozszerzenie pozwala na pewne przytrzymanie kołka w miejscu. Kołki rozporowe są używane do mocowania elementów w betonie, murach i innych twardych powierzchniach.
Kołki gwintowane: Te kołki są zaprojektowane z zewnętrznym gwintem, który umożliwia ich wkręcanie w materiał. Są idealne do mocowania elementów w drewnie, płytach gipsowo‑kartonowych, a także w miękkich materiałach. Kołki gwintowane cechuje łatwy montaż i demontaż.
Kołki do drewna: Przeznaczone do mocowania elementów drewnianych. Zwykle posiadają ostrzejsze zakończenie, które ułatwia ich wbijanie w drewno. W zależności od wymagań mogą mieć różne kształty i rozmiary.
Kołki do izolacji: Wykorzystywane w przemyśle elektrycznym do mocowania izolacji na elementach elektrycznych, takich jak transformatorach i silnikach. Są zazwyczaj wykonane z tworzyw sztucznych, które mają doskonałe właściwości izolacyjne.
Kołki stalowe: Charakteryzują się wyjątkową wytrzymałością na rozciąganie i skręcanie. Są powszechnie stosowane w budownictwie, w miejscach wymagających mocnych połączeń.
Kołki ekspansywne: Te kołki są podobne do kołków rozporowych, ale posiadają również wewnętrzny mechanizm ekspansji. Po włożeniu w otwór mechanizm ten pozwala na jeszcze większe rozszerzenie kołka, zapewniając jeszcze silniejsze i trwalsze połączenie.
Sworznie
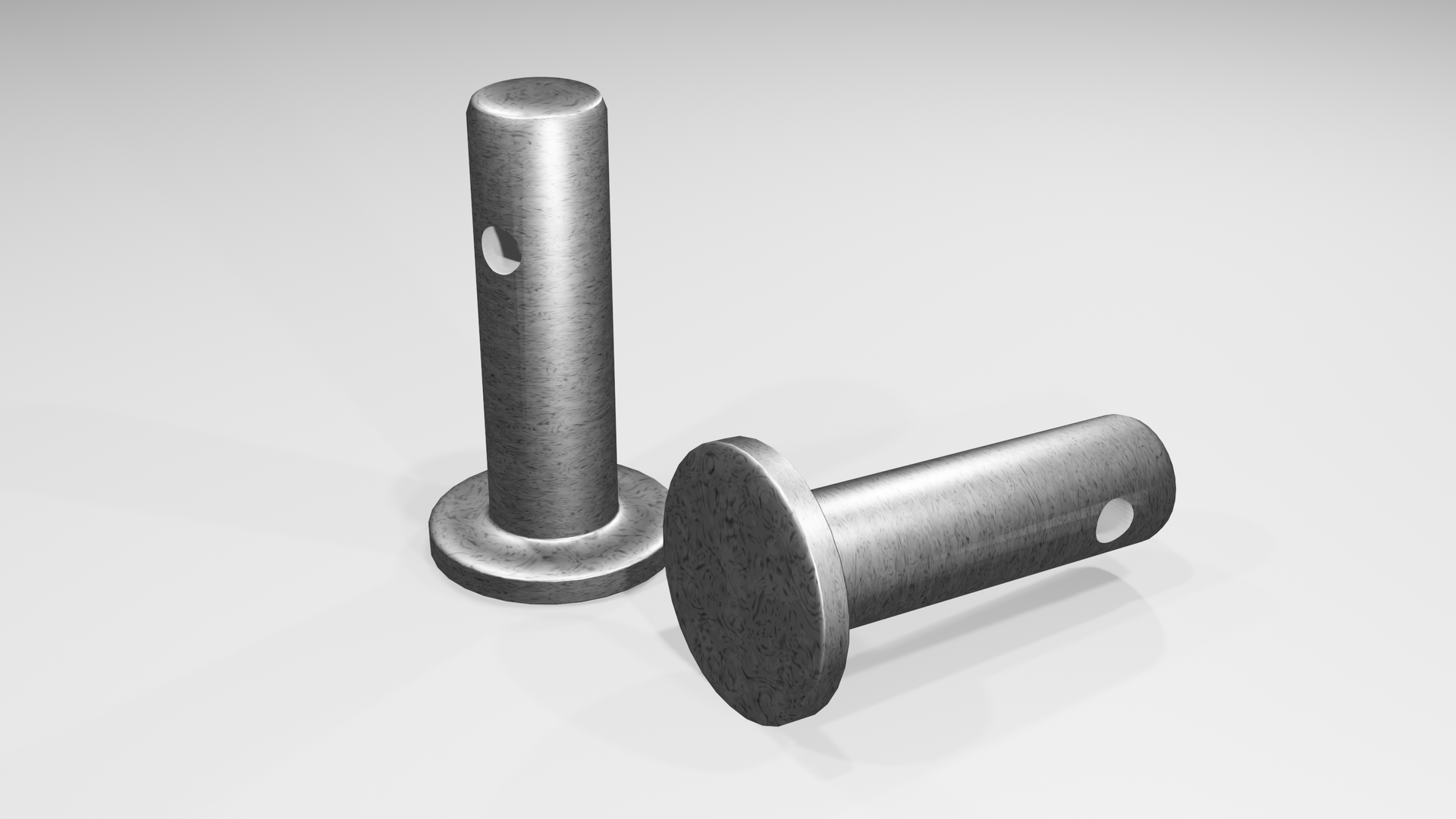
Sworznie są elementami mechanicznymi, które służą do łączenia i zapewnienia ruchu pomiędzy różnymi częściami maszyn, urządzeń oraz konstrukcji. Ich podstawową funkcją jest utrzymywanie odpowiedniej relacji pomiędzy elementami, umożliwiając jednocześnie ich swobodne przemieszczanie względem siebie w określonych kierunkach. Sworznie są powszechnie używane w przemyśle mechanicznym, motoryzacyjnym, lotniczym, a także w wielu innych dziedzinach techniki.
Budowa i rodzaje:
Sworznie cylindryczne: To najbardziej popularny rodzaj sworzni, które mają cylindryczny kształt. Składają się z trzonu (najczęściej o stałym przekroju) oraz zakończeń o różnych kształtach, np. stożkowym lub kulistym. Sworznie cylindryczne są stosunkowo proste w konstrukcji i znakomicie sprawdzają się w wielu zastosowaniach.
Sworznie stożkowe: Te sworznie posiadają stożkowe zakończenia na obu końcach. Są używane głównie w miejscach wymagających dokładniejszego wycentrowania i wyrównania elementów.
Sworznie kuliste: Sworznie kuliste mają zakończenia w postaci półkulek, co umożliwia swobodny ruch w różnych kierunkach. Są stosowane, gdy wymagana jest większa swoboda ruchu w danym połączeniu.
Sworznie tulejowe: Sworznie tulejowe składają się z trzonu i tulei, która otacza trzon sworznia. Są używane w celu zmniejszenia tarcia między elementami połączonymi przez sworzeń oraz zapewnienia wytrzymałości połączenia.
Wpusty
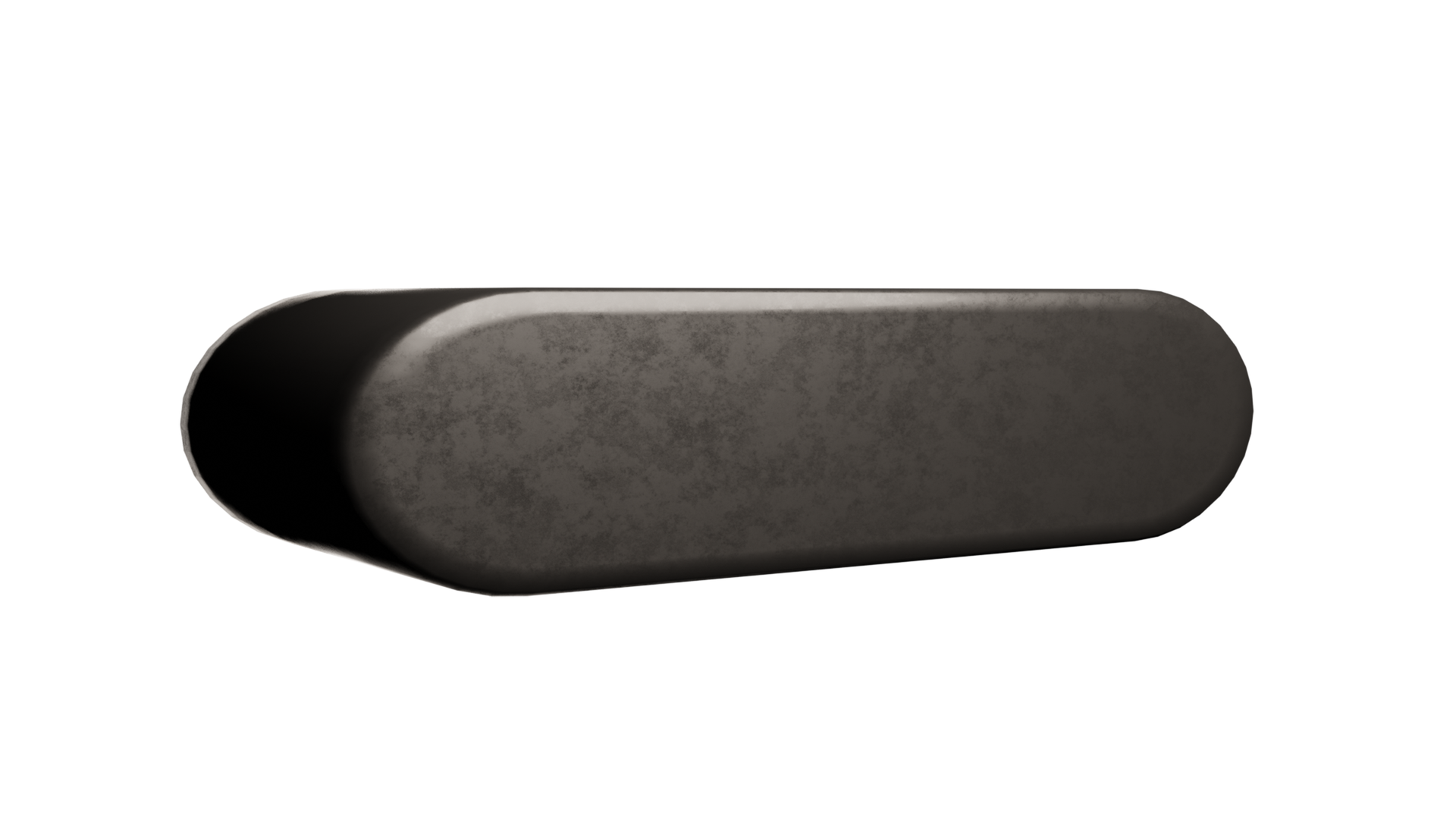
Wpusty pryzmatyczne to popularne połączenia piasty z wałem, zapewniające współpracę i zabezpieczenie przed obrotem względnym. Muszą być ciasno dopasowane do otaczających je powierzchni bocznych. Dzielą się na typy o różnych kształtach, takie jak zaokrąglone, ścięte, pełne i jedno- lub dwuotworowe. Wpusty pryzmatyczne służą głównie do zapewnienia ruchu obrotowego między elementami napędowymi w maszynach i urządzeniach.
Nity
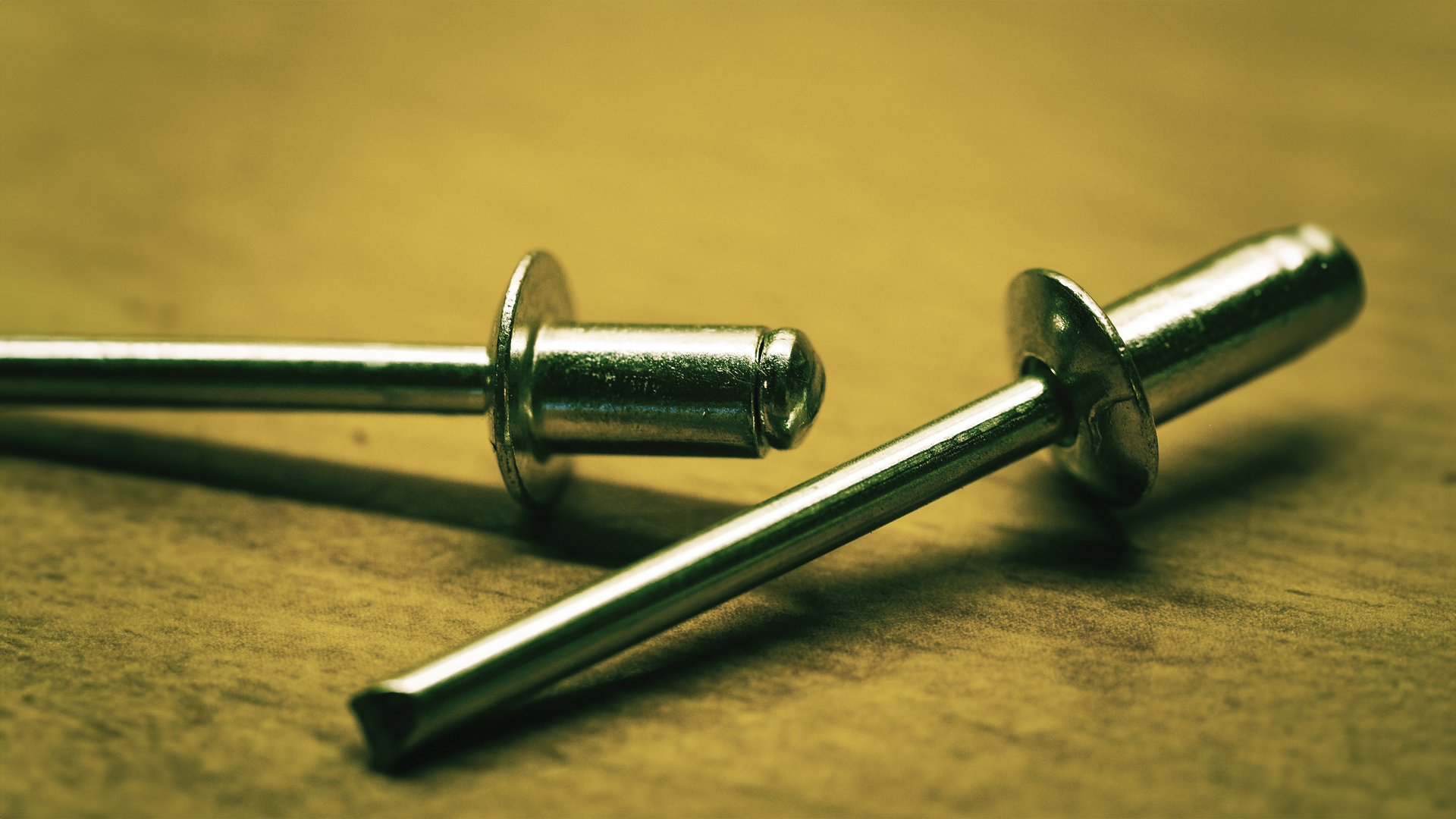
Nity to metalowe elementy łączące płaskie części. Współcześnie popularne są nity zrywalne w postaci rurek z łebkiem i pręcika z drutu, który zostaje wyciągnięty po nitowaniu. Przy wyborze odpowiednich nitów należy kierować się materiałem wykonania. Dostępne są nity aluminiowe, stalowe, ze stali nierdzewnej, miedzi, stopów miedziano‑niklowych. Wyróżnia się różne kształty główki, np. kuliste, płaskie, grzybkowe, a także różny przekrój trzonka, np. pełne, drążone i rurkowe. Nity ślepe są jednostronnie zamykane. Wybór odpowiedniego typu nitów jest istotny dla trwałości i właściwości połączenia.
Spoiny
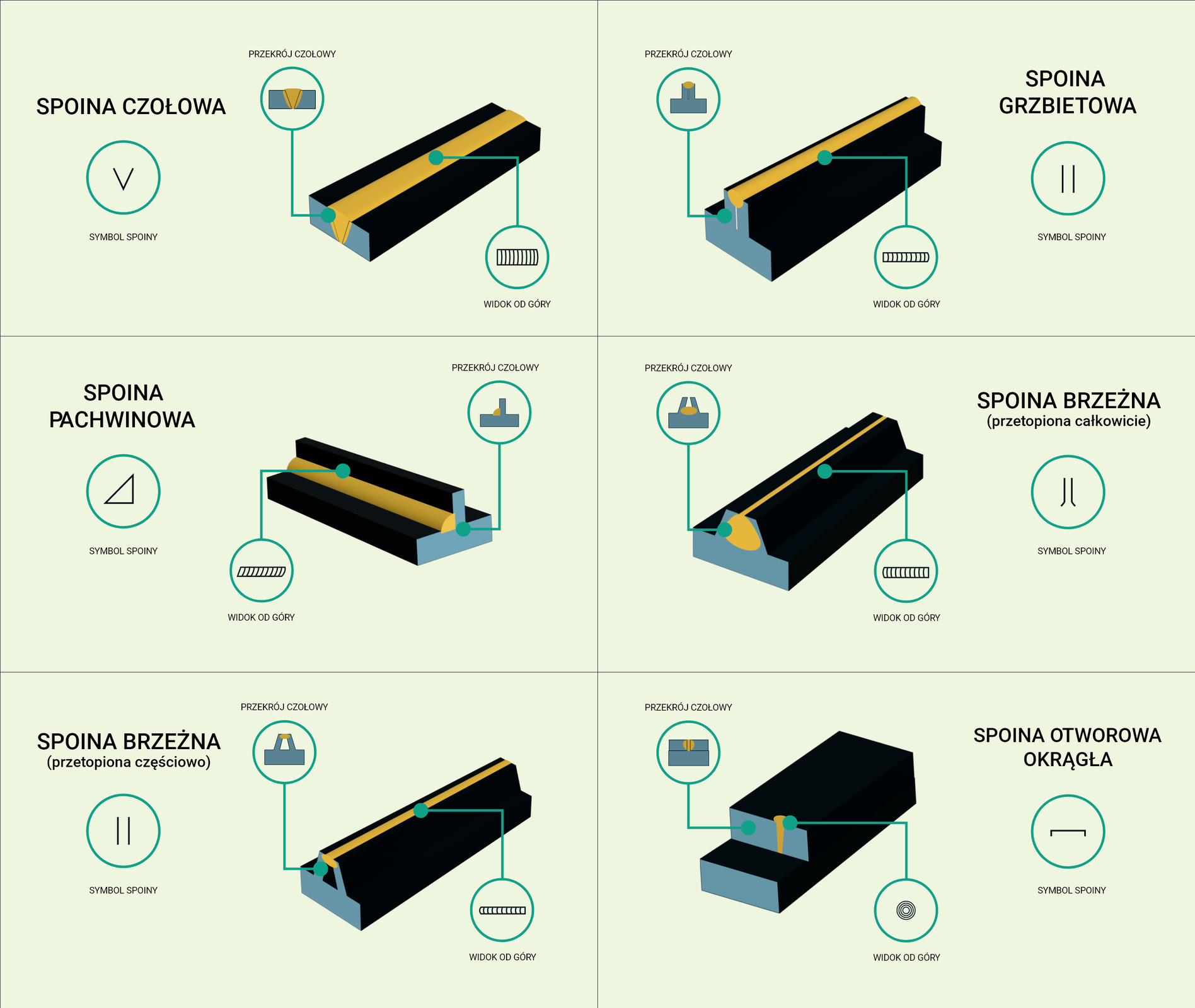
Spoiny to połączenia dwóch lub więcej elementów, które są sklejane, spawane, lutowane lub klejone ze sobą w celu utworzenia trwałego i wytrzymałego połączenia.
Rodzaje spoin:
Spoiny sklejane: Wykonuje się je poprzez zastosowanie specjalnych klejów, które łączą elementy. Spoiny sklejane są używane w wielu zastosowaniach, zarówno w konstrukcjach lekkich, jak i ciężkich.
Spoiny spawane: Wykonywane przez stopienie materiału bazowego przy użyciu odpowiedniego źródła ciepła, takiego jak płomień, łuk elektryczny lub laser. Spawanie umożliwia utworzenie bardzo mocnego połączenia, które jest szeroko stosowane w przemyśle i budownictwie.
Spoiny lutowane: Spoiny te są wykonane poprzez stopienie stopu lutowniczego, który wypełnia przestrzeń między elementami, a po ochłodzeniu utwardza się, łącząc elementy razem. Spoiny lutowane są stosowane w elektronice, w branży jubilerskiej i w niektórych zastosowaniach przemysłowych.
Spoiny klejone: W tym rodzaju spoin stosuje się kleje, które utwardzają się po złączeniu elementów. Spoiny klejone są używane w różnych zastosowaniach, w tym w produkcji pojazdów, mebli, a także w budownictwie.
Funkcje spoin:
Łączenie elementów: Główną funkcją spoin jest połączenie dwóch lub więcej elementów, aby utworzyć jednolitą i trwałą strukturę.
Przenoszenie obciążeń: Poprzez spoiny, obciążenia i siły działające na połączonych elementach są przekazywane w sposób ciągły, zapewniając stabilność i wytrzymałość połączenia.
Zabezpieczenie przed wnikaniem środków zewnętrznych: Wiele rodzajów spoin, takich jak spoiny klejone i lutowane, może także zapewniać uszczelnienie i ochronę przed wilgocią, pyłem lub innymi środkami zewnętrznymi.
Luty
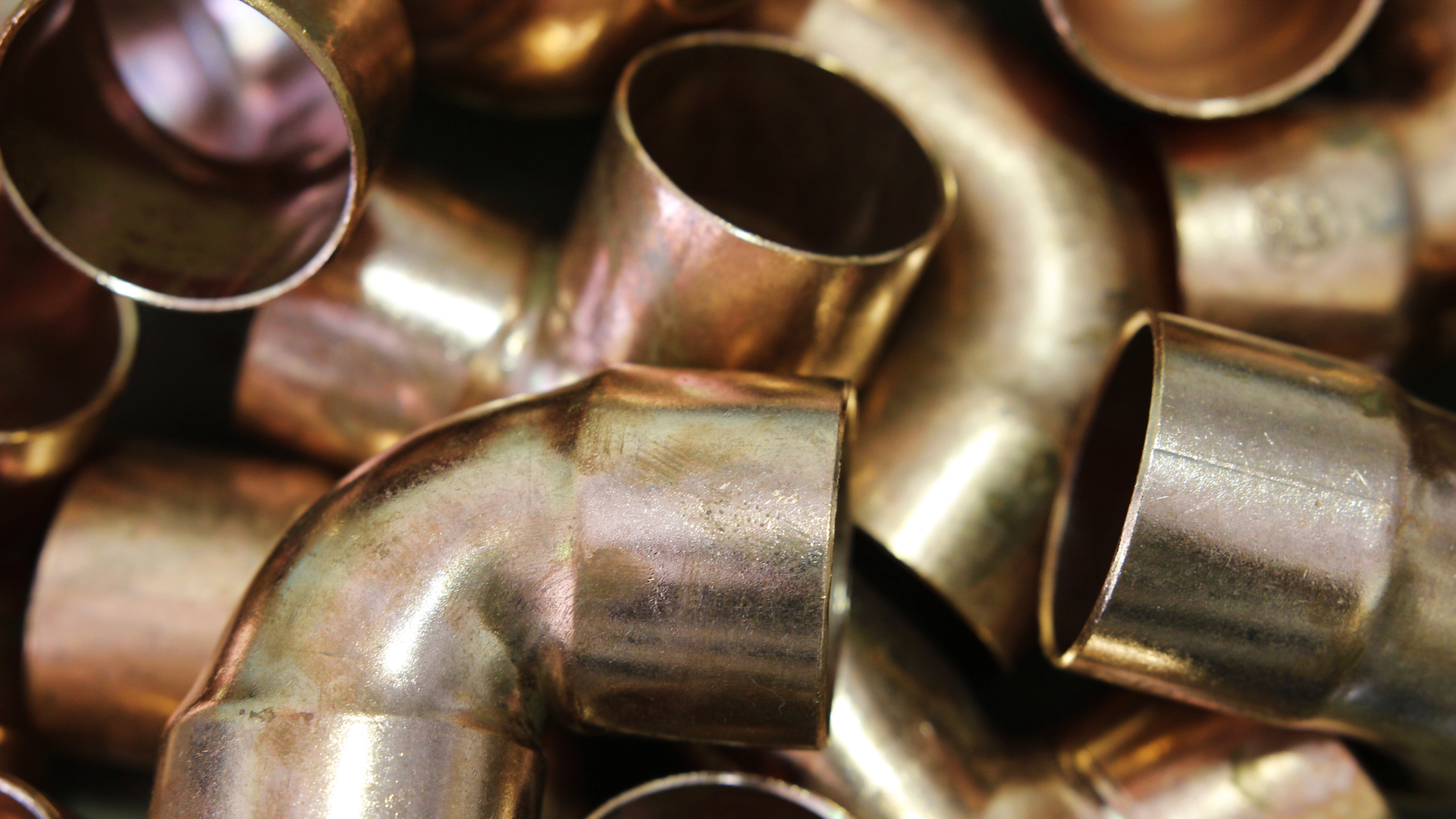
Lutowanie to proces łączenia metalowych przedmiotów za pomocą spoiwa lutowniczego. Spoiwo lutownicze jest stopem metali lub metalem, który ma niższą temperaturę topnienia od przedmiotów, które mają być połączone. Podział spoiw lutowniczych uwzględnia temperaturę topnienia, wyróżnia się luty twarde (powyżej 450°C) i miękkie (poniżej 450°C). Luty twarde stosuje się przy łączeniu stali węglowej, chromowej, złota i mosiądzu, natomiast luty miękkie topią się w temperaturach 180°C - 280°C i najczęściej zawierają cynę. Spoiwa lutownicze można wykonać z różnych metali, takich jak miedź, srebro, mosiądz czy cyna, w zależności od zastosowania. Lutowanie jest powszechnie używane w przemyśle, warsztatach oraz w domowym użytku do łączenia i naprawy różnych metalowych przedmiotów, elementów elektroniki czy rur.
Powrót do spisu treściPowrót do spisu treści
Grafiki maszyn i urządzeń z różnymi połączeniami
Przykłady maszyn z połączeniami rozłącznymi
Prasa mechaniczna: Prasy mechaniczne są wykorzystywane w przemyśle metalowym do wytłaczania, cięcia, gięcia lub formowania blachy. W maszynach tych często stosuje się połączenia śrubowe i nakrętki, które pozwalają na łatwe demontowanie narzędzi i wymianę matryc.
R39GBhaAeiGxH Prasa mechanicznaŹródło: Englishsquare.pl Sp. z o.o., licencja: CC BY-SA 3.0.Wiertarki: Wiertarki przemysłowe służą do wykonywania otworów w różnych materiałach. Często stosuje się połączenia rozłączne, takie jak chwytaki (wrzeciono z wrzeciona), które umożliwiają szybką wymianę wiertła.
RFESUdm9W0LgW WiertarkiŹródło: Englishsquare.pl Sp. z o.o., licencja: CC BY-SA 3.0.Tokarki: Tokarki są wykorzystywane do obróbki skrawaniem, w celu uzyskania cylindrycznych kształtów. W tokarkach można stosować połączenia śrubowe do montażu narzędzi i osłon.
RjDbBdwjHEoKO TokarkaŹródło: Englishsquare.pl Sp. z o.o., licencja: CC BY-SA 3.0.Spawarki: Spawarki są wykorzystywane do łączenia elementów metalowych za pomocą spawania. Choć spawanie jest połączeniem trwałym, spawarki same są często składane i montowane z różnych elementów, które są połączone na przykład za pomocą śrubowych połączeń rozłącznych.
R51fNu1n86FSm SpawarkaŹródło: dostępny w internecie: https://pixabay.com/pl/, domena publiczna.
Powiązane połączenia rozłączne są często stosowane w przemyśle, aby zapewnić elastyczność, wygodę obsługi, wymianę części czy narzędzi, a także ułatwić konserwację i naprawy maszyn przemysłowych.
Przykłady maszyn z połączeniami nierozłącznymi
Samoloty: W przemyśle lotniczym używa się połączeń nierozłącznych, takich jak nitowanie czy klejenie, do łączenia różnych części skrzydeł, kadłubów, usterzeń i innych elementów konstrukcyjnych samolotów. Połączenia te zapewniają trwałość i wytrzymałość, a jednocześnie zmniejszają masę konstrukcji.
R1DVsp6kaFIgf SamolotŹródło: dostępny w internecie: https://pixabay.com/pl/, domena publiczna.Pociągi: W przemyśle kolejowym połączenia nierozłączne, takie jak spawanie, są szeroko stosowane do łączenia elementów taboru.
R1MihwG5hviru PociągŹródło: dostępny w internecie: https://pixabay.com/pl/, domena publiczna.Statki i jednostki pływające: W przemyśle morskim używa się połączeń nierozłącznych, takich jak spawanie czy klejenie, do łączenia różnych elementów konstrukcyjnych statków i jednostek pływających.
R19uhaIkVcMbM StatekŹródło: dostępny w internecie: https://pixabay.com/pl/, domena publiczna.Maszyny wydobywcze: W przemyśle górniczym i wydobywczym stosuje się połączenia nierozłączne, takie jak spawanie, do łączenia różnych elementów maszyn wydobywczych, takich jak koparki, wiertnice czy ładowarki.
R1Pl9aGRuVrdM Maszyny wydobywczeŹródło: dostępny w internecie: https://pixabay.com/pl/, domena publiczna.
W przypadku maszyn przemysłowych połączenia nierozłączne są często wykorzystywane w celu zapewnienia trwałości, wytrzymałości i bezpieczeństwa konstrukcji. W takich maszynach, gdzie wymagane są trwałe połączenia, stosuje się różne techniki łączenia, takie jak spawanie, klejenie, nitowanie czy zgrzewanie.
Powrót do spisu treściPowrót do spisu treści
Narzędzia do wykonywania połączeń rozłącznych i nierozłącznych
Śrubokręty: Śrubokręty to ręczne narzędzia, które służą do dokręcania i odkręcania śrub. Składają się z długiego trzonka zakończonego ostrzem (bitą) o odpowiednim kształcie, który pasuje do śruby. Śrubokręty występują w różnych rozmiarach i kształtach, aby pasować do różnych rodzajów śrub. W przypadku połączeń rozłącznych śrubokręty pozwalają na montaż i demontaż elementów, co ułatwia naprawy i konserwację.
RF3qa1TECCVii ŚrubokrętyŹródło: dostępny w internecie: https://pixabay.com/pl/, domena publiczna.Klucze: Klucze to narzędzia służące do dokręcania i odkręcania nakrętek. W zależności od rodzaju nakrętek dostępne są różne rodzaje kluczy, takie jak klucze płaskie, klucze nasadowe, klucze imbusowe, klucze oczkowe itp. Klucze pozwalają na precyzyjne wykonanie połączeń śrubowych i umożliwiają dostęp do miejsc trudno dostępnych.
R1Kk5r9PHDBG7 Klucze płaskieŹródło: dostępny w internecie: https://pixabay.com/pl/, domena publiczna.Rx1jMFM5UHxvO KluczeŹródło: dostępny w internecie: https://pixabay.com/pl/, domena publiczna.R1QFCCOM2ZBMb Zestaw kluczyŹródło: dostępny w internecie: https://pixabay.com/pl/, domena publiczna.Klucze dynamometryczne: Klucze dynamometryczne są specjalnymi kluczami, które pozwalają na dokładne określenie momentu obrotowego podczas dokręcania śrub. Dzięki temu można precyzyjnie kontrolować siłę dokręcania śruby, co jest szczególnie istotne w przypadku delikatnych elementów i precyzyjnych montaży, gdzie zbyt duży moment może uszkodzić elementy lub spowodować ich odkształcenie.
R1FAyHYYpsPMZ Klucz dynamometrycznyŹródło: Englishsquare.pl Sp. z o.o., licencja: CC BY-SA 3.0.Młotki: Młotki to narzędzia wykorzystywane do wbijania kołków, sworzni czy innych elementów w połączenia wciskane. Młotki mogą mieć różne wagi i kształty, aby pasować do różnych zastosowań.
R1HppuqSojQZ6 MłotkiŹródło: dostępny w internecie: https://pixabay.com/pl/, domena publiczna.Prasy: Prasy to urządzenia, które służą do wykonywania połączeń wciskanych. W prasach można wciskać łożyska, sworznie, wpusty i inne elementy w odpowiednie otwory. Prasy są używane w różnych branżach przemysłu, w tym w produkcji maszyn, pojazdów czy elementów konstrukcyjnych.
ROB2gMLBIco8J PrasaŹródło: Englishsquare.pl Sp. z o.o., licencja: CC BY-SA 3.0.Wkrętarki: Wkrętarki to narzędzia elektryczne do wkręcania i wykręcania śrub, które pozwala na szybkie i wygodne łączenie elementów.
R1CNQ2NEVc0GJ WkrętarkaŹródło: dostępny w internecie: https://pixabay.com/pl/, domena publiczna.Narzędzia do lutowania: Lutowanie to proces łączenia metalowych elementów przy użyciu stopów lutowniczych. Narzędzia do lutowania obejmują różne rodzaje lutownic, palników lutowniczych i stacji lutowniczych, które pozwalają na precyzyjne i trwałe połączenia metalowe.
R1XV7YG6yMjhM LutownicaŹródło: dostępny w internecie: https://pixabay.com/pl/, domena publiczna.Narzędzia do klejenia: Narzędzia do klejenia, takie jak pistolety do kleju, służą do nakładania kleju na połączone elementy. Klejenie jest popularnym sposobem łączenia różnych materiałów, takich jak plastik, drewno, metal czy szkło.
R1TLoOTUeMhap Narzędzie do klejeniaŹródło: dostępny w internecie: https://pixabay.com/pl/, domena publiczna.Narzędzia do nitowania: Narzędzia do nitowania, takie jak oprawki do nitów i nitownice, pozwalają na wykonywanie połączeń nitowanych. Nitowanie jest metodą stosowaną w wielu branżach do łączenia różnych materiałów, takich jak metal, plastik czy drewno.
RNcvQcZKWv92L NitownicaŹródło: Englishsquare.pl Sp. z o.o., licencja: CC BY-SA 3.0.Narzędzia do frezowania i toczenia: Narzędzia do frezowania i toczenia są wykorzystywane do obróbki skrawaniem i tworzenia różnych rodzajów połączeń, takich jak rowki, wpusty czy gwinty. Są to kluczowe narzędzia w obróbce metali i tworzyw sztucznych w przemyśle produkcyjnym.
R1HtDew03uwR1 FrezarkaŹródło: Englishsquare.pl Sp. z o.o., licencja: CC BY-SA 3.0.
Każde z tych narzędzi spełnia określoną funkcję i jest używane w zależności od rodzaju połączenia, materiałów, jakie mają zostać połączone, oraz wymagań dotyczących precyzji i wytrzymałości łączenia. Dzięki nim możliwe jest wykonywanie różnorodnych połączeń i konstrukcji, które są niezbędne w przemyśle produkcyjnym.
Powrót do spisu treściPowrót do spisu treści
Podział wpustów i wielowypustów
Połączenia wpustowe zaliczają się do kategorii połączeń nierozłącznych. Ich głównym celem jest łączenie piasty z wałem oraz zapewnienie ochrony przed ewentualnym obrotem spowodowanym działaniem momentu skręcającego. Wpust jest elementem pryzmatycznym, który jest ciasno pasowany na swoich powierzchniach bocznych.
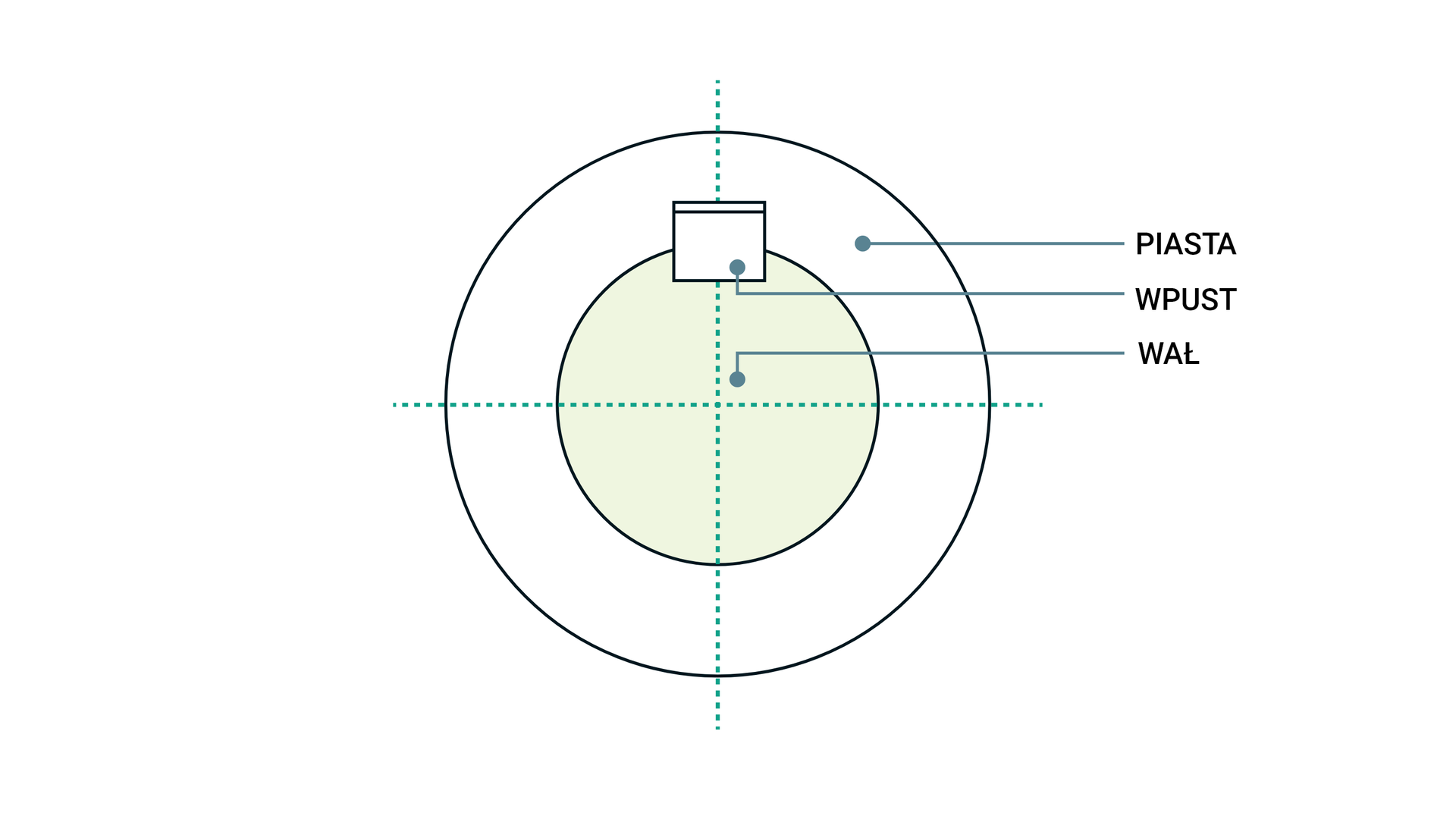
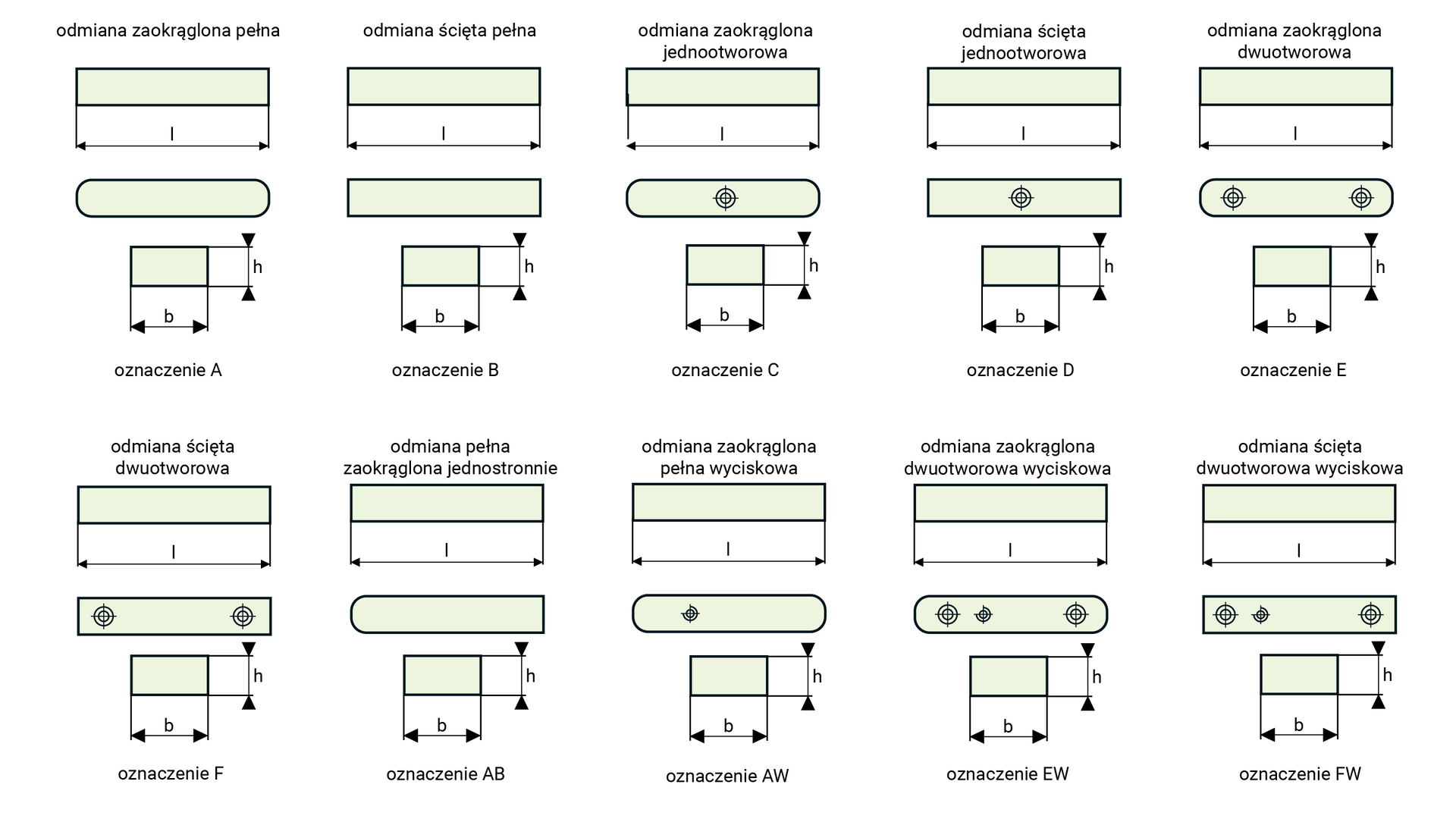
Połączenie wielowypustowe ma na celu zestawienie piasty z wałem oraz ochronę przed relatywnym obracaniem się spowodowanym działaniem momentu skręcającego. Kluczowym elementem przenoszącym ten moment jest wielowypust wycięty na wale. W zestawieniu z połączeniami wpustowymi połączenia wielowypustowe mogą przenosić większe obciążenia. Dodatkowo umożliwiają one dokładne wycentrowanie połączonych elementów, lecz są kosztowniejsze w realizacji.
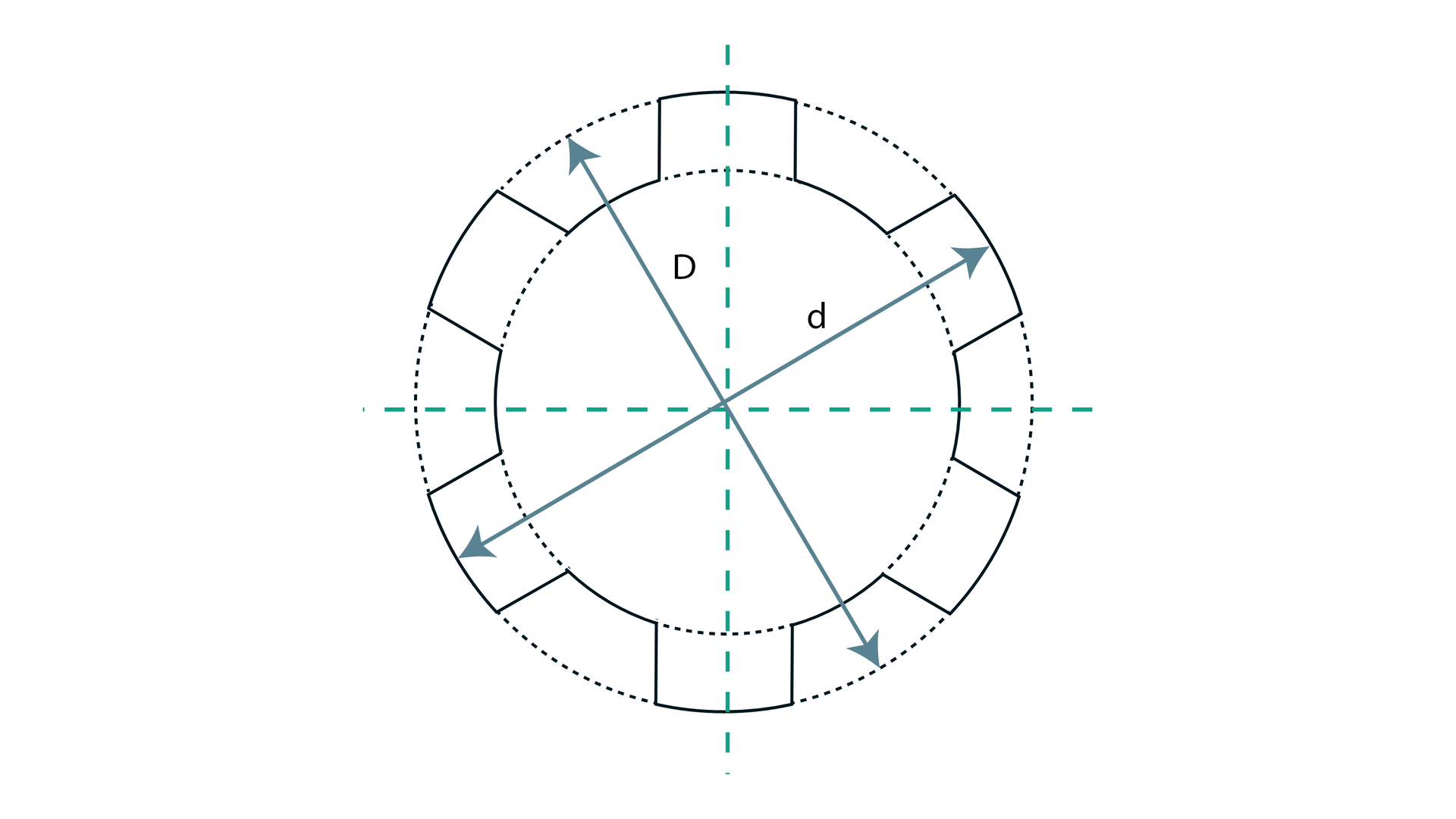
Najczęściej spotykane są połączenia wielowypustowe o zarysie:
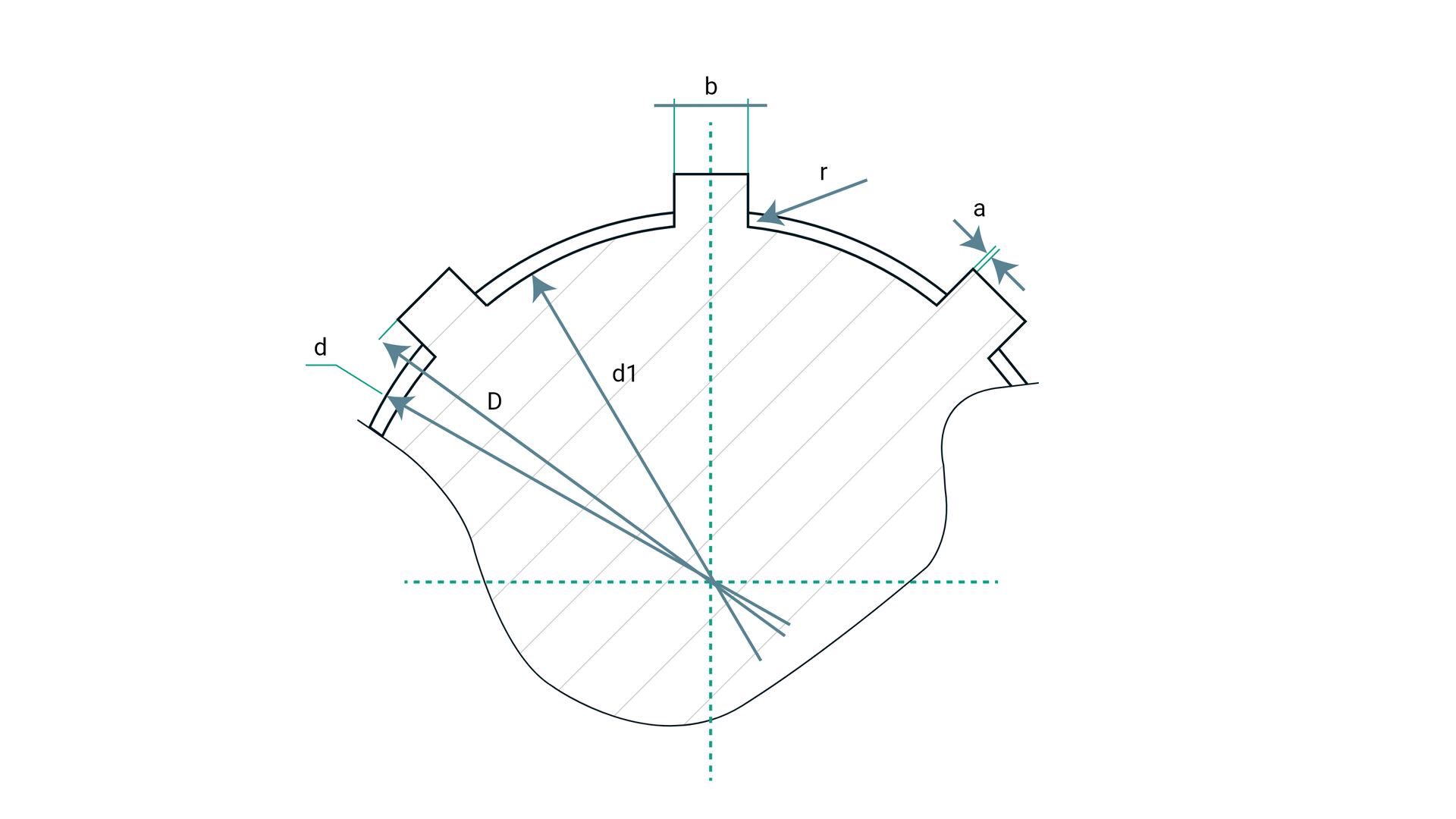
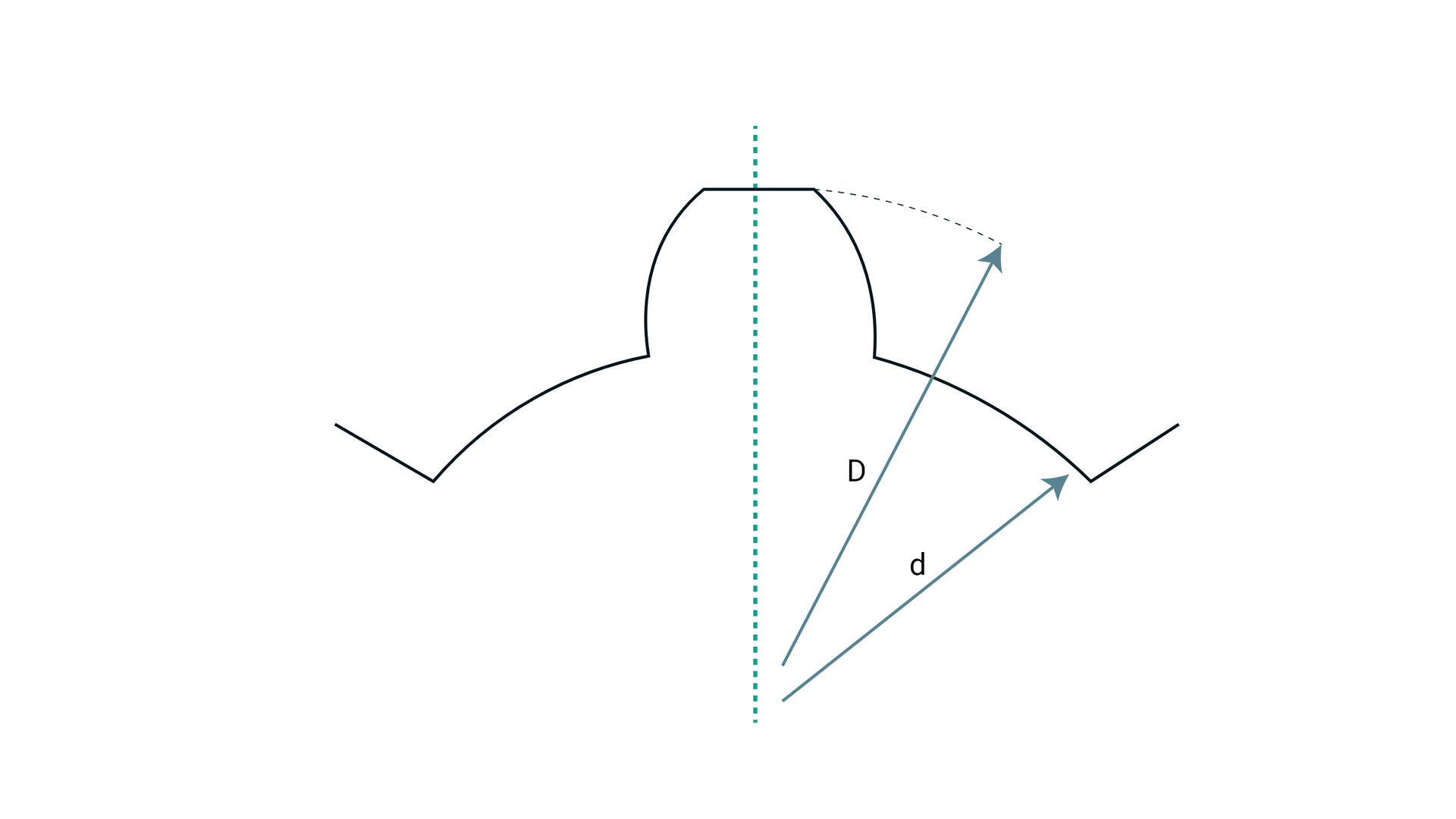
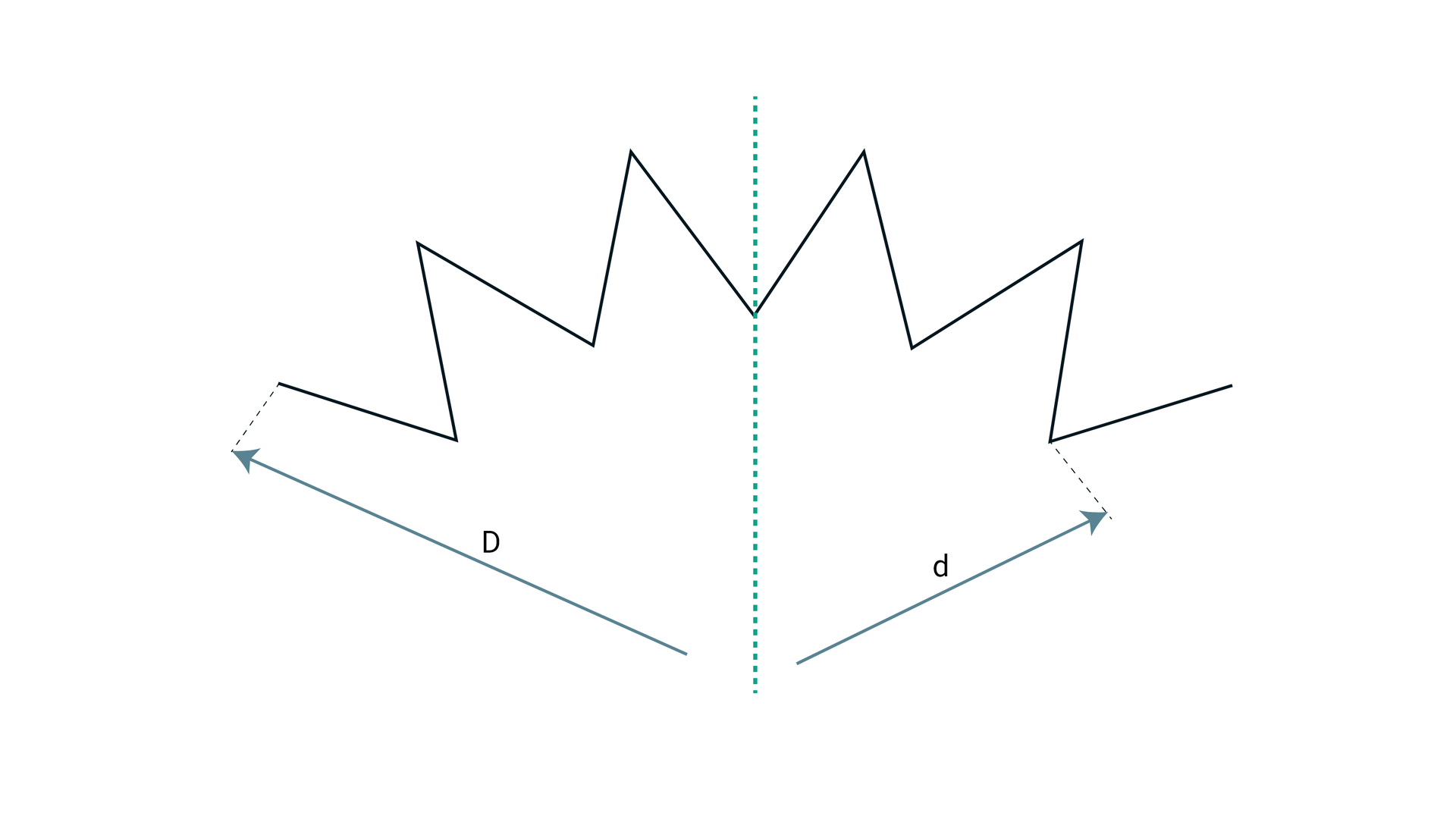
Powrót do spisu treściPowrót do spisu treści
Podział nitów, spoin i zgrzein
Nity
Spoiny
Spoiny spawalnicze podlegają klasyfikacji na podstawie ich kształtu oraz wyglądu, uwzględniając zarówno aspekty zewnętrzne, jak i widok w przekroju.
Jak już wcześniej wspomniano, istnieje kilka podstawowych rodzajów spoin:
Istnieją również spoiny bezotworowe, które można wyróżnić:
Punktowe: Tworzone są bez wcześniejszego przygotowywania otworu w materiale. Takie połączenia powstają w wyniku przetopienia jednej blachy i wtopienia jej w drugą (znajdującą się poniżej).
Liniowe: Formują się poprzez skumulowanie spoin punktowych.
Warto zaznaczyć, że istnieje szereg podkategorii spoin, w tym m.in. spoiny brzeżne z krawędziami podwiniętymi, spoiny przetopione całkowicie lub częściowo, a także spoiny doczołowe typu I, V, 1/2 V, Y, 1/2 Y, U, 1/2 U, V o stromych brzegach oraz 1/2 V ze stromym brzegiem. Ponadto, w niektórych przypadkach można dodatkowo mówić o spoinach prawostronnych lub lewostronnych.
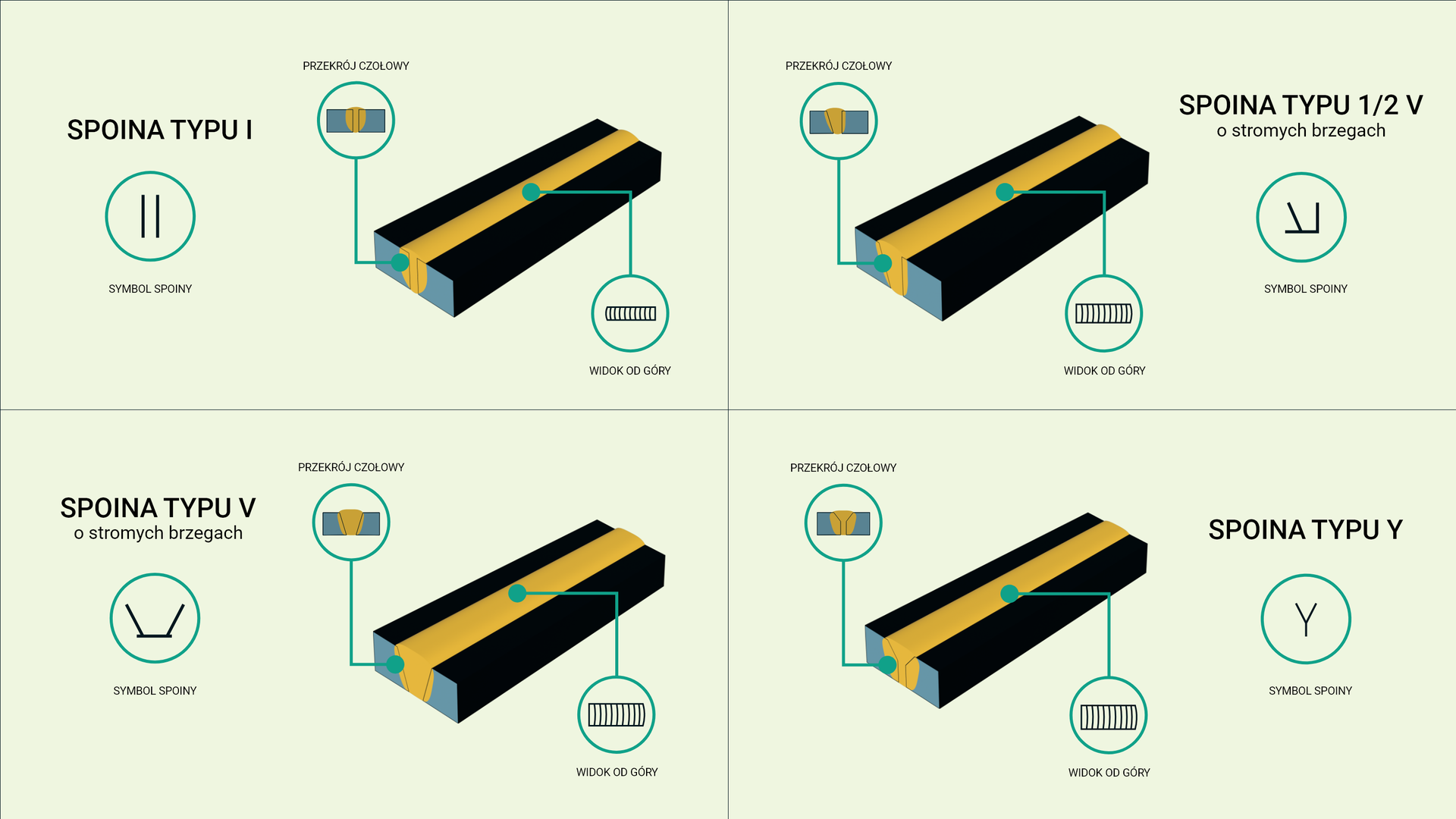
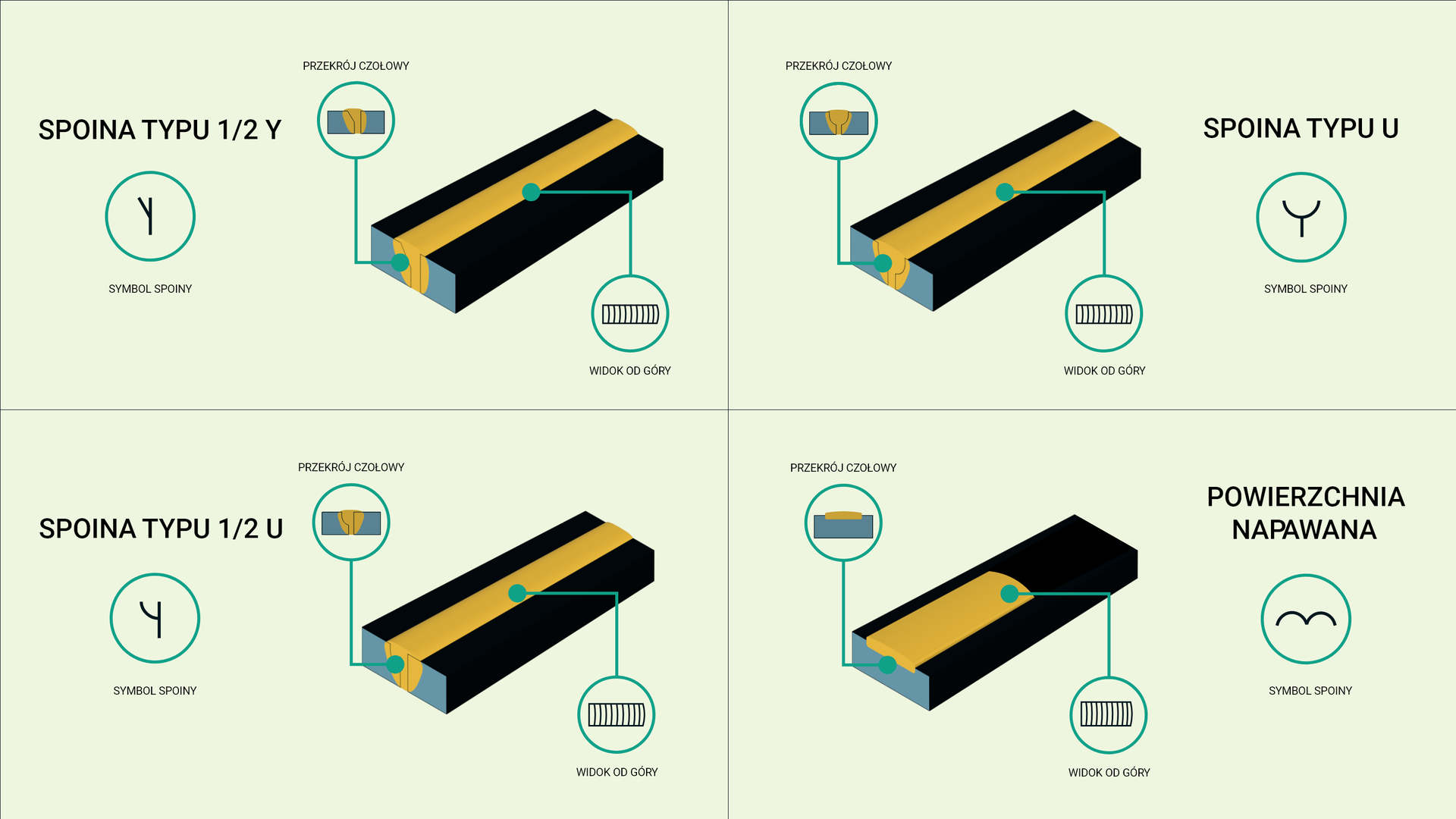
Zgrzeiny
Powrót do spisu treściPowrót do spisu treści
Podział kołków i sworzni
Powrót do spisu treściPowrót do spisu treści
Podział połączeń śrubowych
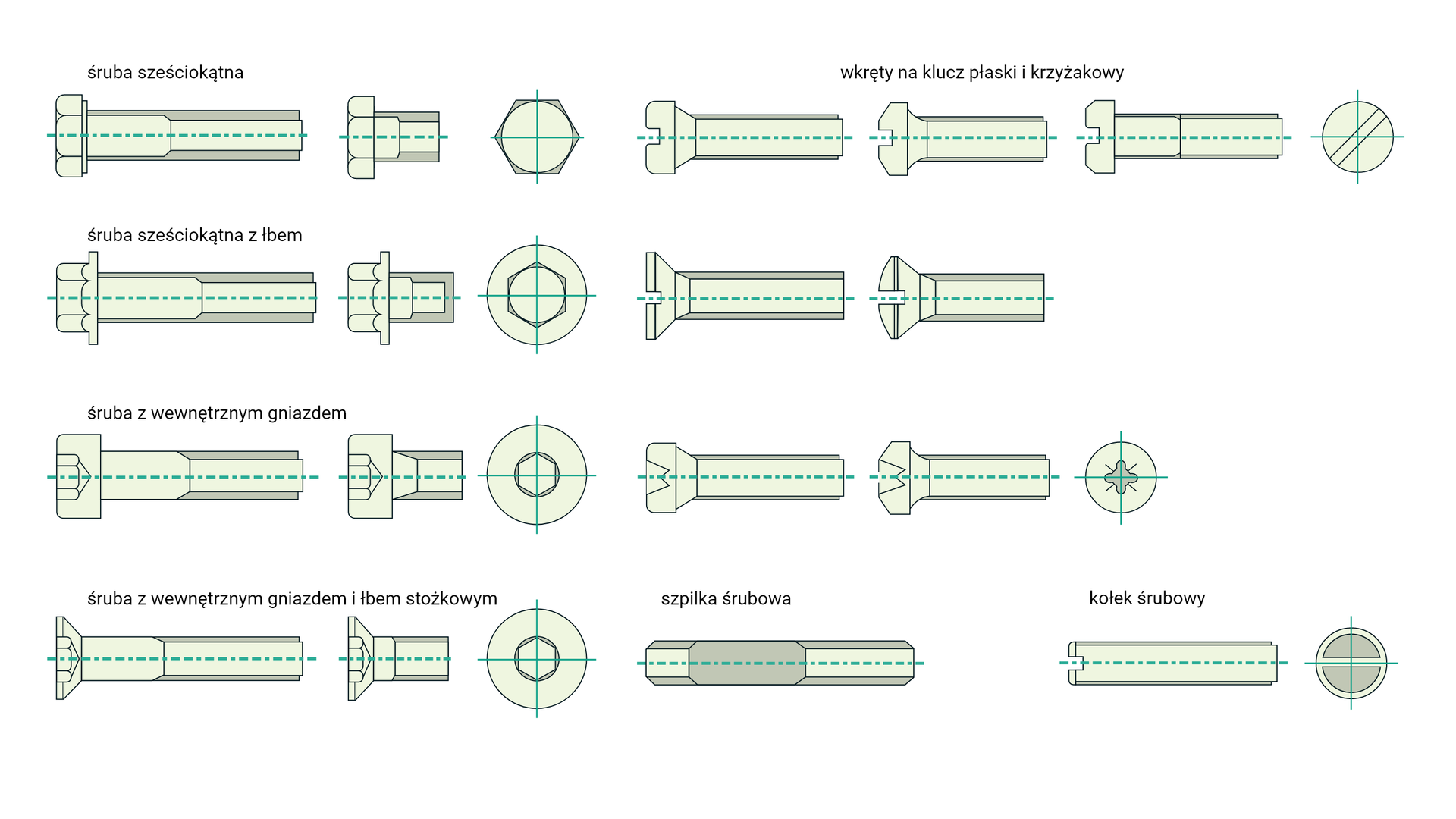
Połączenia śrubowe dzielimy na zakładkowe i czołowe.
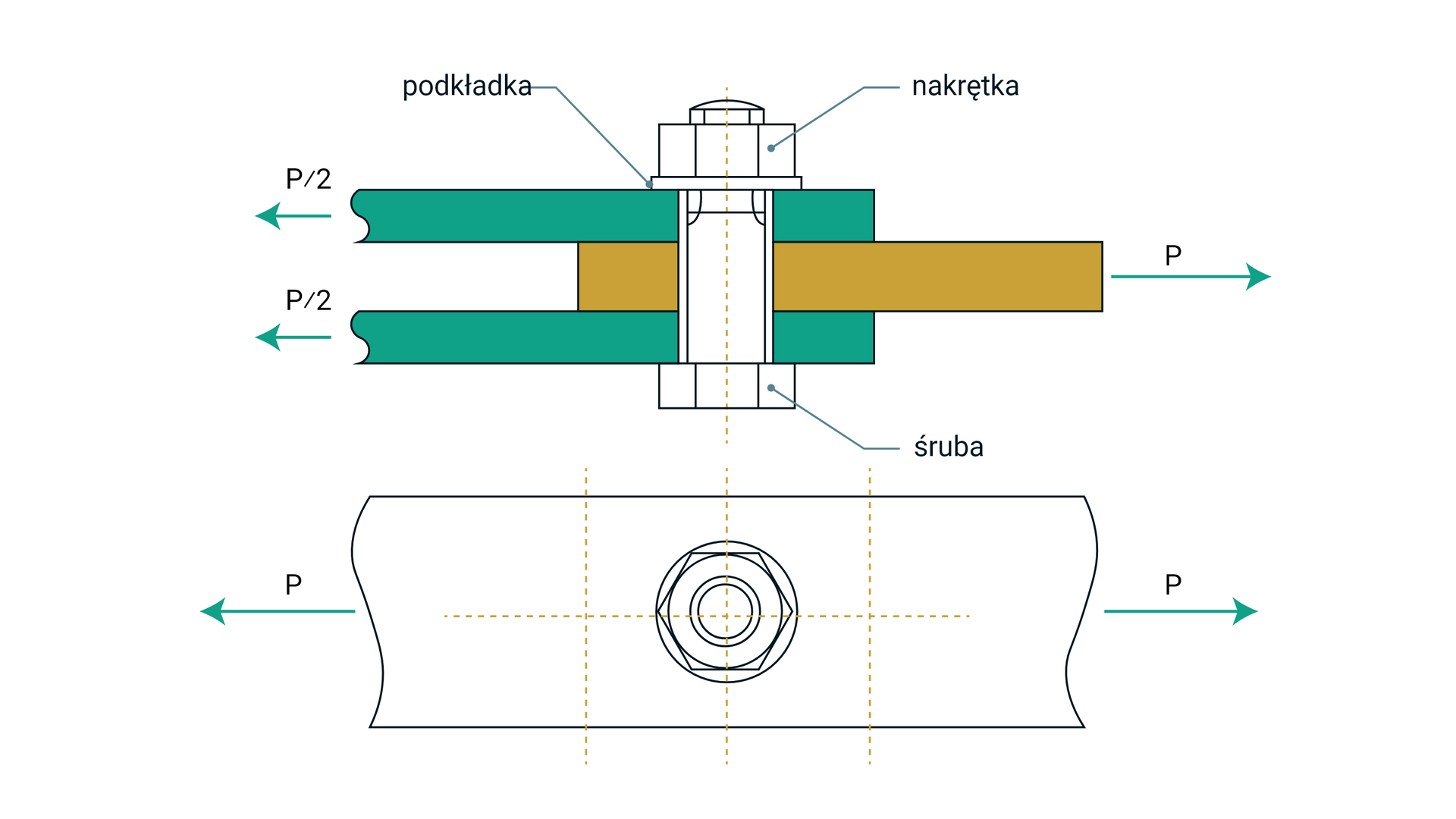
Powrót do spisu treściPowrót do spisu treści
Podział gwintów
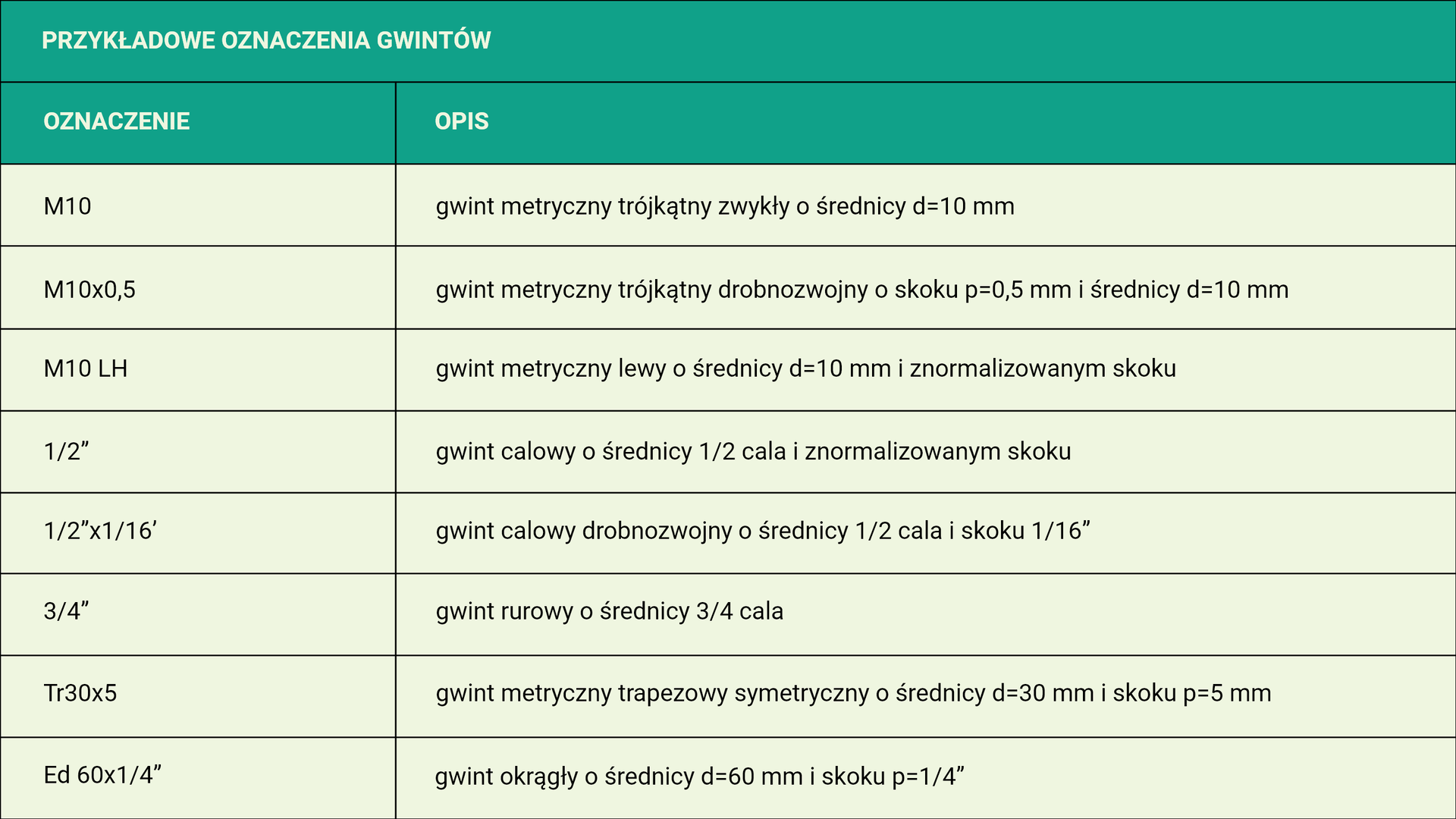
Powrót do spisu treściPowrót do spisu treści
Dźwięki maszyn i procesów technologicznych
Nagranie dostępne pod adresem https://zpe.gov.pl/a/DtgEmkUpw
Nagranie
Powrót do spisu treściPowrót do spisu treści