Obrabiarki numeryczne
MEC.05. Użytkowanie obrabiarek skrawających - Operator obrabiarek skrawających 722307, Technik mechanik 311504
Maszyny CNC
ATLAS INTERAKTYWNY
Spis treści
Budowa i charakterystyka obrabiarekBudowa i charakterystyka obrabiarek
SterowanieSterowanie
Odmiany konstrukcyjneOdmiany konstrukcyjne
Technologia obróbkiTechnologia obróbki
Podstawowe metody obróbki skrawaniemPodstawowe metody obróbki skrawaniem
Podstawy programowania obrabiarek CNCPodstawy programowania obrabiarek CNC
Cykle obróbkiCykle obróbki
Przygotowanie do obróbki oraz diagnostyka procesu skrawaniaPrzygotowanie do obróbki oraz diagnostyka procesu skrawania
Metody pomiaru przedmiotu obrabianegoMetody pomiaru przedmiotu obrabianego
Budowa i charakterystyka obrabiarek
Budowa i charakterystyka obrabiarek sterowanych numerycznie
Obrabiarki to maszyny robocze wykorzystywane do produkowania elementów części maszyn i urządzeń. Można je podzielić na obrabiarki do obróbki:
bezwiórowej (np. do obróbki plastycznej czy odlewnictwa),
skrawaniem i erozyjnej.
Obrabiarki sterowane numerycznie (CNC ang. Computerized Numerical Control) charakteryzują się dużym zakresem parametrów skrawania, zamkniętą przestrzenią obróbkową, układem samosmarowania, a dodatkowo – możliwościami wykonania symulacji obróbki, wyboru trybu programu i trybu chłodzenia detalu. Głównym celem konstrukcyjnym maszyn CNC jest zwiększenie wydajności produkcji przy jednoczesnym zmniejszeniu kosztów wytwarzania i poprawie dokładności obróbki.
Obrabiarka, np. frezarka, składa się z napędu głównego wrzeciona, napędu posuwu, układu pomiaru położenia, śruby kulkowej napędu posuwu i pulpitu sterującego. Wykonuje ona wiele prac w sposób automatyczny, dlatego też brak jest elementów obsługi ręcznej do np. napędu posuwów. Sanie obrabiarek NC napędzane są w sposób niezależny. Za napęd sani odpowiadają układy napędowe i przekładnie śrubowe ruchów posuwowych.
Na grafice przedstawiona została sterowana numerycznie frezarka. Jej części to:
Numer jeden. Napęd głównego wrzeciona.
Numer dwa. Napęd posuwu.
Numer trzy. Pulpit sterujący z ekranem.
Numer cztery. Układ pomiaru położenia.
Numer pięć. Śruba kulkowa napędu posuwu.
Szczegółowa budowa obrabiarki NC
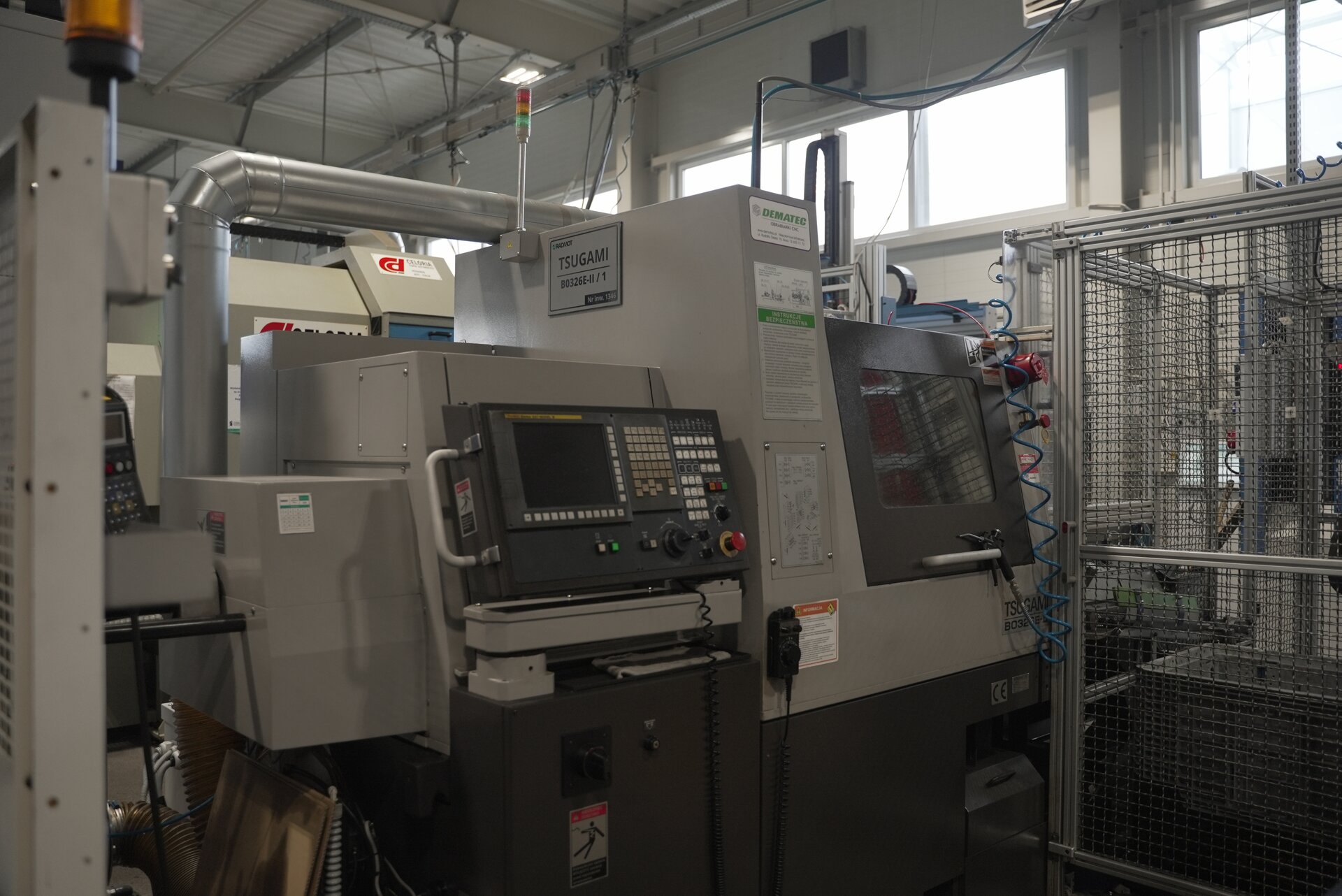
Elementy budowy obrabiarki NC przedstawionej na grafice to:
Numer jeden. Zespoły obrabiarki.
Numer dwa. Osłony z blachy.
Numer trzy. Drzwi przesuwane z dostępem do przestrzeni roboczej.
Numer cztery. Chwytacz części.
Numer pięć. Pulpit sterowniczy.
Numer sześć. Szafa sterująca.
Numer siedem. Stabilizator temperatury wrzeciona.
Numer osiem. Wylot przenośnika wiórów.
Numer dziewięć. Układ chłodzenia.
Numer dziesięć. Zasilacz hydrauliczny.
Numer jedenaście. Urządzenia sprężonego powietrza.
Numer dwanaście. Układ centralnego sterowania (łożyska, wrzeciona, prowadnice).
Numer trzynaście. Kolektor chłodziwa.
Punkty charakterystyczne obrabiarki
Obrabiarki posiadają układy współrzędnych: sterowania, związane z przedmiotem obrabianym, związane z osiami maszyny. Do układu współrzędnych należą punkty charakterystyczne:
zerowe,
odniesienia.
Punkty zerowe:
Punkt zerowy maszyny - przy jego pomocy ustalany jest układ współrzędnych maszyny. Do tego punktu odnoszą się pozostałe punkty odniesienia.
RntKwvf1GObeT Punkt zerowy maszynyŹródło: Englishsquare.pl Sp. z o.o., licencja: CC BY-SA 3.0.Punkt zerowy obrabianego przedmiotu (programu) - układ współrzędnych przedmiotu względem punktu zerowego maszyny; jest on określany przez producenta i nie może być zmieniony; znajduje się poza obszarem obróbki.
RdGi4DJtry53S Punkt zerowy obrabianego przedmiotuŹródło: Englishsquare.pl Sp. z o.o., licencja: CC BY-SA 3.0.Punkt zerowy zamocowania - w przypadku tokarek może pokrywać się z punktem zerowym przedmiotu.
R8xmKJE4cxFRT Punkt zerowy zamocowaniaŹródło: Englishsquare.pl Sp. z o.o., licencja: CC BY-SA 3.0.

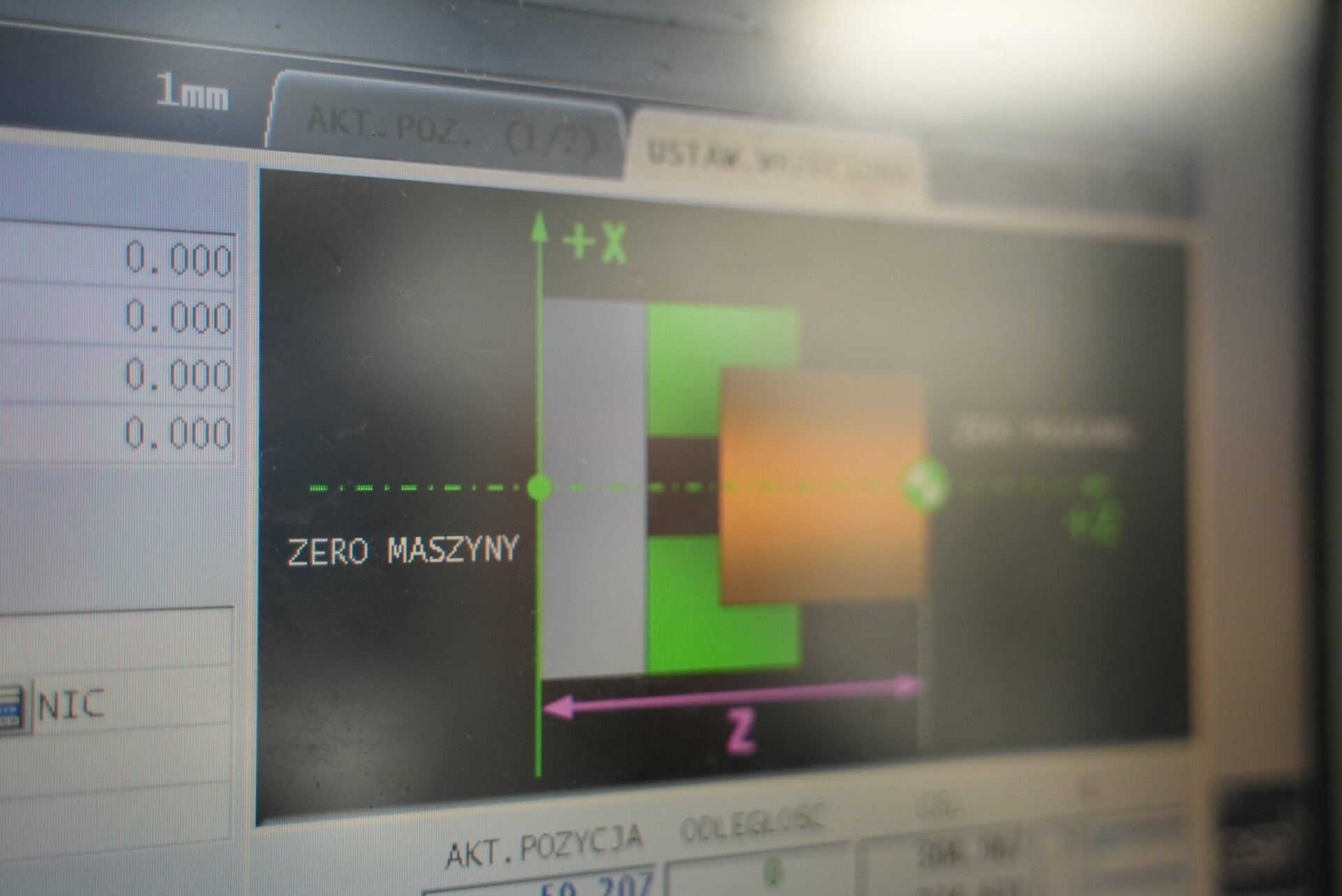
Grafiki przedstawiają oznaczenia punktów zerowych maszyny w programach komputerowych. Oznaczenia wyświetlają się na monitorze komputera.
Punkty odniesienia:
Punkt odniesienia - pozycja ustalona przez zderzak i system pomiarowy. Odstęp między punktem odniesienia R a punktem zerowym M musi być znany. Umożliwia to ustawienie pozycji osi na dokładnie tę samą wartość.
RAclo24NiOfeM Punkt odniesieniaŹródło: Englishsquare.pl Sp. z o.o., licencja: CC BY-SA 3.0.Punkt startowy - punkt ustalany przez program, znajduje się w obszarze roboczym; w tym miejscu pierwsze narzędzie rozpoczyna obróbkę.
RYOpqiyVvi2Du Punkt startowyŹródło: Englishsquare.pl Sp. z o.o., licencja: CC BY-SA 3.0.Punkt odniesienia nośnika narzędzi - posiadając informacje o długości zastosowanego narzędzia, sterowanie oblicza odstęp wierzchołka narzędzia od punktu odniesienia nośnika narzędzia.
R1P61dsG1MZMv Punkt odniesienia nośnika narzędziŹródło: Englishsquare.pl Sp. z o.o., licencja: CC BY-SA 3.0.Punkt wymiany narzędzia - punkt, w którym następuje zmiana narzędzia wykorzystywanego do obróbki.
R1ZC4LCz209ZW Punkt wymiany narzędziaŹródło: Englishsquare.pl Sp. z o.o., licencja: CC BY-SA 3.0.
Korpusy i prowadnice
Korpusy obrabiarek są częściami łączącymi w jedną całość elementy obrabiarki. Wyróżnić można korpus główny, będący podstawą konstrukcji obrabiarki, oraz korpusy zespołów, do których mocuje się przedmiot obrabiany lub odpowiednie narzędzie (np. głowice rewolwerowe).
Korpusy muszą spełniać wymagania niezmienności kształtu (także w trakcie obróbki), sztywności, tłumienia drgań, ukształtowania zapewniającego bezpieczeństwo i ergonomię obsługi oraz relatywnie niedużych kosztów konstrukcyjnych. Najczęściej produkuje się je z maszynowego żeliwa szarego, żeliwa sferoidalnego, materiałów polimero‑betonowych, czy też z kompozytów.
Prowadnice są to współpracujące części większych mechanizmów; ich zadanie polega na zmianie położenia części prowadzonych. Połączenie prowadnicowe składa się z prowadnicy oraz prowadnika. Elementy te na ogół wykonują ruch prostoliniowy. Siły oraz momenty (czyli nośność prowadnicy), jakie będą na nie działały, uważa się za podstawowy parametr doboru prowadnic.
Ze względu na rodzaj występującego tarcia wyróżnia się następujące prowadnice:
ślizgowe:
walcowe
pryzmatyczne.
toczne:
rolkowe,
ze swobodnymi elementami tocznymi.
z tarciem wewnętrznym:
pneumatyczne,
hydrauliczne,
sprężyste.
Ze względu na zastosowanie prowadnic w maszynach i obrabiarkach, wyróżnia się:
prowadnice ślizgowe (połączenia obrotowe oraz prostoliniowe):
hydrostatyczne,
aerostatyczne,
magnetyczne,
o styku bezpośrednim,
z nakładkami stalowymi.
prowadnice toczne (połączenia prostoliniowe i obrotowe):
szynowe zestawy prowadnicowe,
bloki prowadnicowe,
z otwartym obiegiem elementów tocznych.
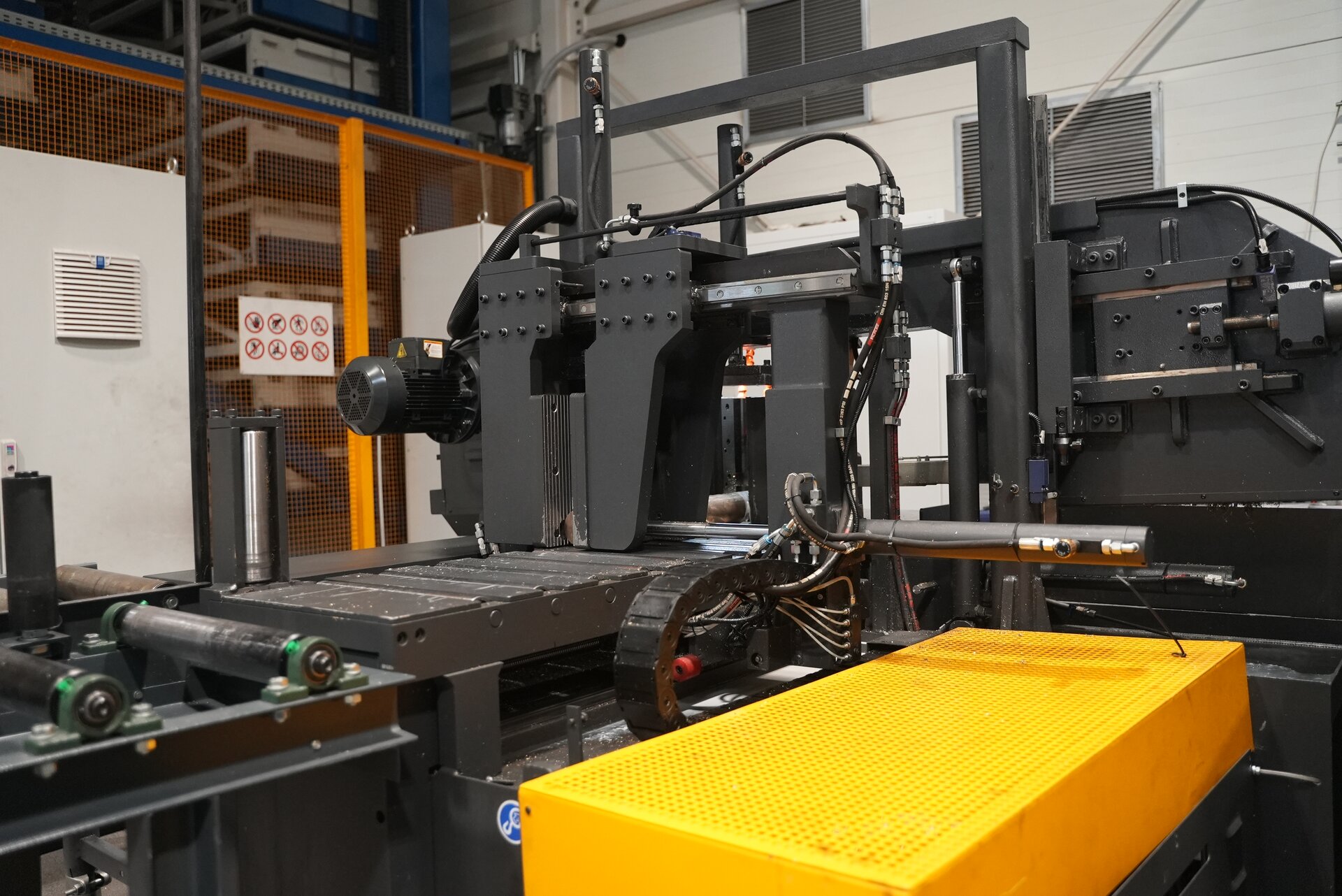
Zespoły napędowe
Zespoły napędowe są to zespoły, które przenoszą energię z sieci elektrycznej do zespołu roboczego maszyny.
Zespoły napędowe obrabiarek NC dzielą się na:
napędy główne,
napędy posuwów,
napędy pomocnicze.
Napęd główny służy do przekazywania mocy potrzebnej do obróbki skrawaniem poprzez wrzeciono. Najważniejszymi cechami napędu głównego jest jego wysoka sztywność (moment obrotowy musi utrzymać pozycję pomimo oddziałujących sił skrawania) oraz zdolność do sprawnej i płynnej zmiany prędkości skrawania (nie mogą być generowane dodatkowe drgania).
Najczęściej stosowane rodzaje napędów głównych to:
hydrauliczne,
elektromechaniczne z przekładnią stopniową lub bezstopniową,
elektryczne z:
silnikiem prądu przemiennego synchronicznym lub asynchronicznym,
silnikiem prądu stałego i przekładnią stopniową.
Napędy posuwów można podzielić na trzy grupy
napęd tradycyjny – silnik obrotowy napędza śrubę toczną; odbywać się to może bezpośrednio lub z wykorzystaniem rzekładni pasowej lub zębatej;
napęd z elektronakrętką – silnik współpracuje z nakrętką toczną, śruba pozostaje nieruchoma;
bezpośredni napęd liniowy z silnikiem elektrycznym.
Układy pomiaru położenia i przemieszczenia
Układy pomiaru położenia i przemieszczenia pozwalają zrealizować pętlę sprzężenia zwrotnego położeniowego. Są to jedne z części składowych układów regulacji automatycznej położenia, to znaczy – serwomechanizmów, które stosuje się w napędach pozycjonujących.
Ze względu na sposób pomiaru wyróżnia się układy do pomiarów bezpośrednich i pośrednich.
Pomiar bezpośredni charakteryzuje czujnik pomiarowy, który odczytuje położenie ze skali zamontowanej do stołu obrabiarki.
Pomiar pośredni może polegać np. na pomiarze przez przetwornik pomiarowy obrotowo‑impulsowy, który mierzy liniowe przemieszczenie stołu poprzez odczytanie kąta obrotu śruby pociągowej.
W układach pomiarowych należy wyróżnić bloki funkcjonalne, do których należą:
czujnik pomiarowy, który przekształca wielkość przemieszczenia lub położenia w inną fizyczną wielkość,
przetwornik umożliwiający uzyskanie pomiarowego sygnału elektrycznego.
Wymagania, jakie stawia się układom pomiarowym:
szeroki zakres pomiarowy,
wysoka precyzja pomiarowa,
dostosowanie do pracy w przemysłowych warunkach (drgania, zmienna temperatura, przyspieszenia),
sygnał wyjściowy mający postać przebiegu elektrycznego.
Urządzenia do wymiany narzędzi
Magazyny narzędzi są urządzeniami, z których narzędzia są pobierane i do których są odkładane w przypadku zajścia potrzeby wymiany narzędzia.
Magazyny narzędzi dzieli się ze względu na sposób budowy: gwiazdowe, łańcuchowe, bębnowe.
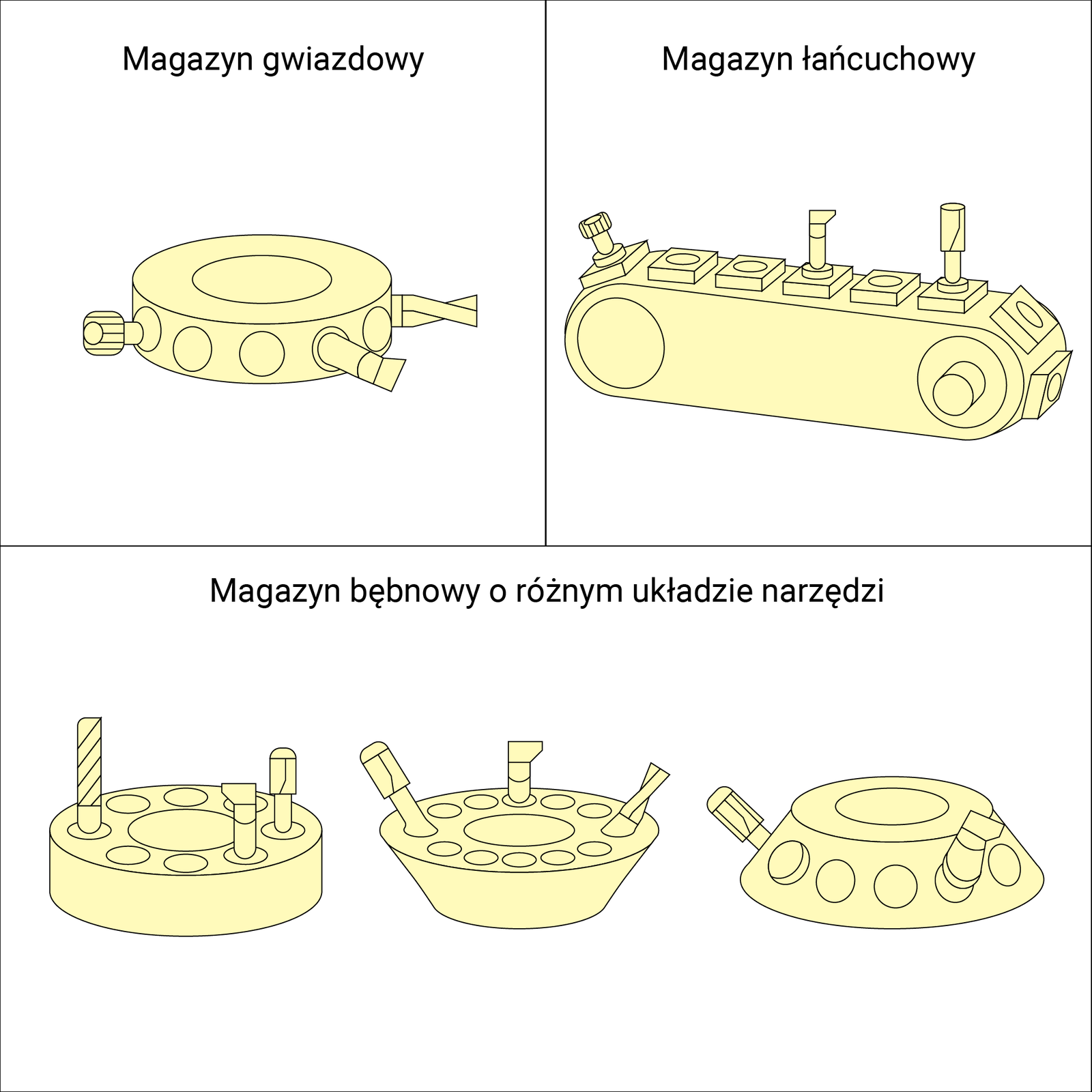
Narzędziowa głowica rewolwerowa jest magazynem z zamocowanymi, wymiennymi narzędziami.
Wykorzystywana jest do toczenia małych części, z użyciem niewielkich rozmiarów narzędzi.
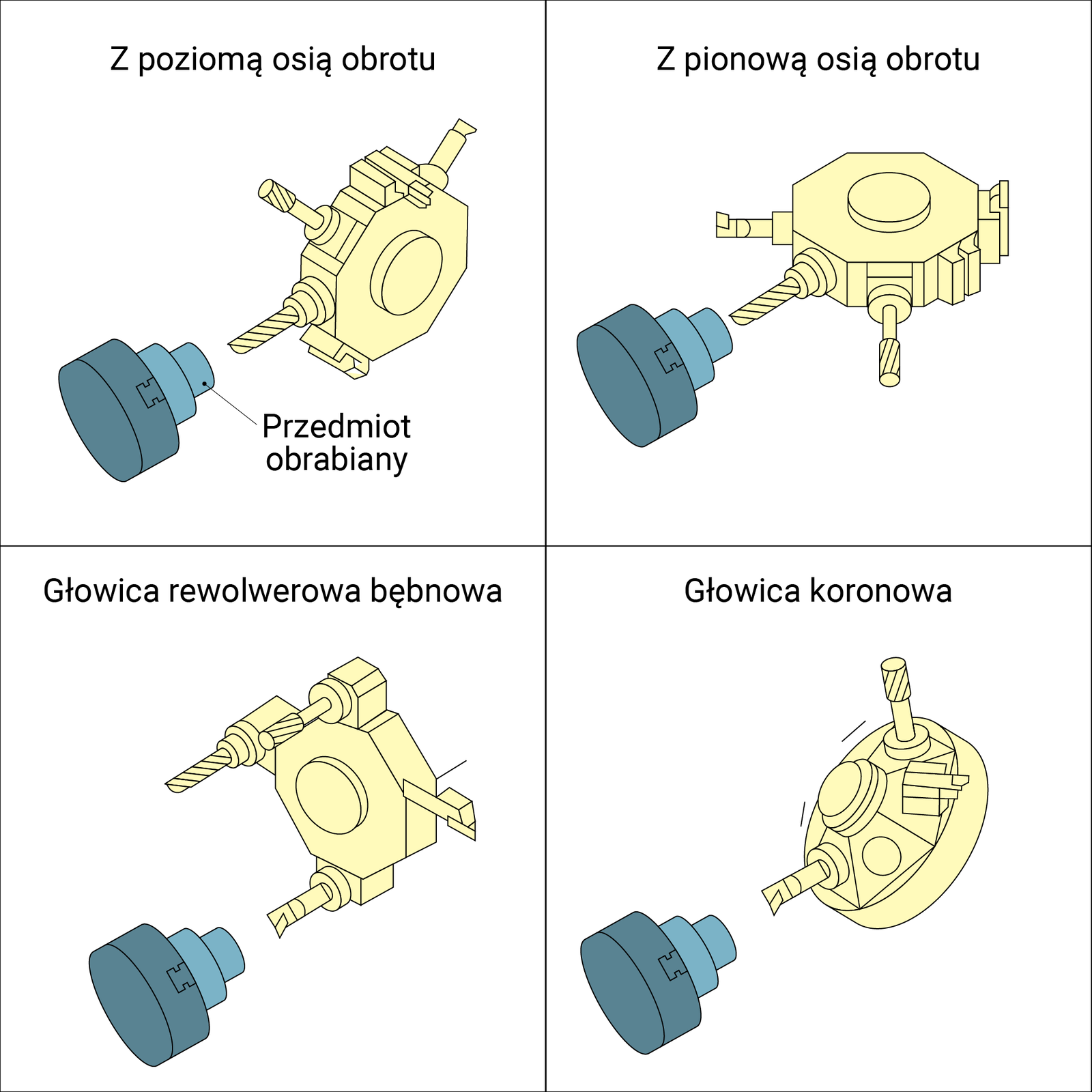
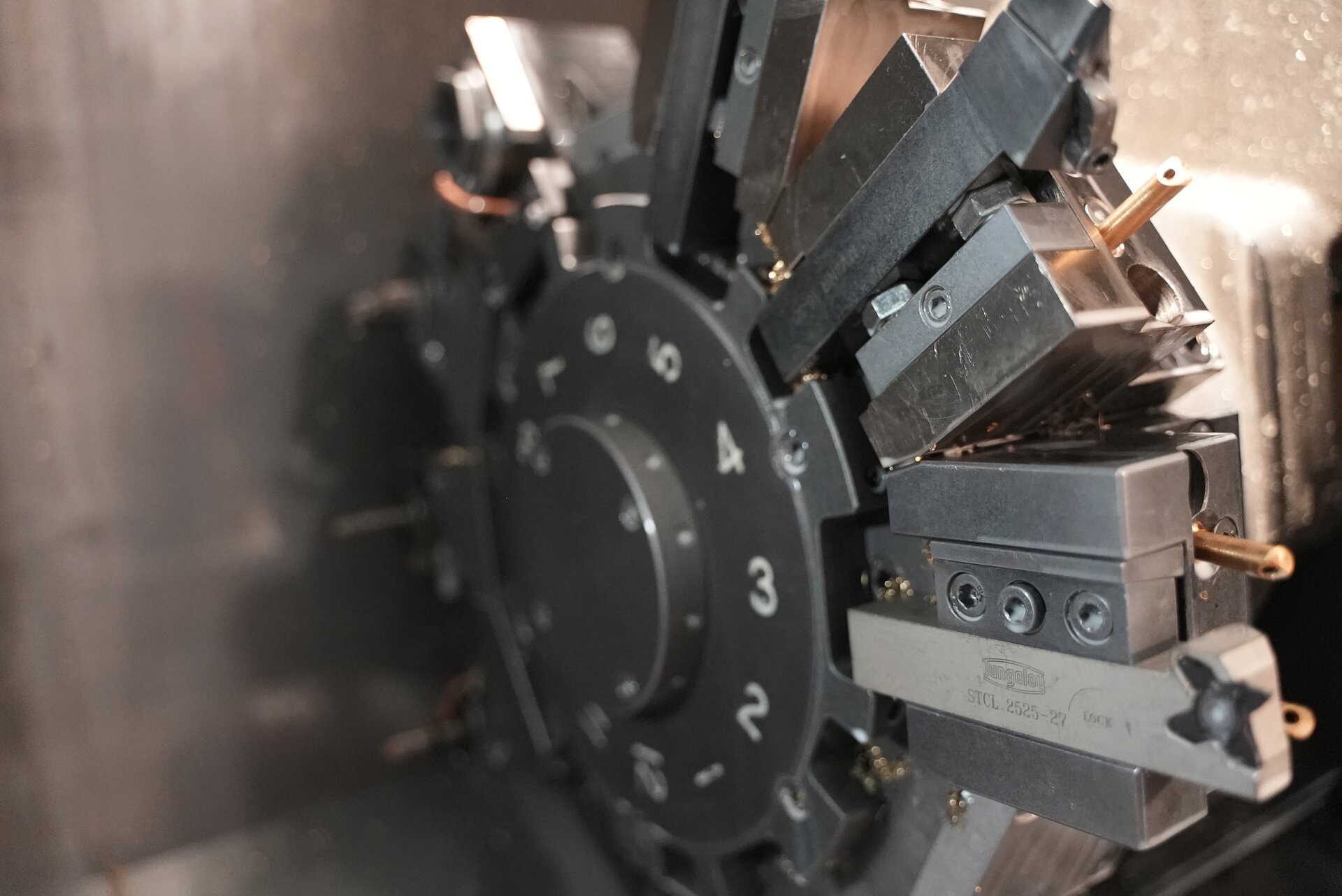
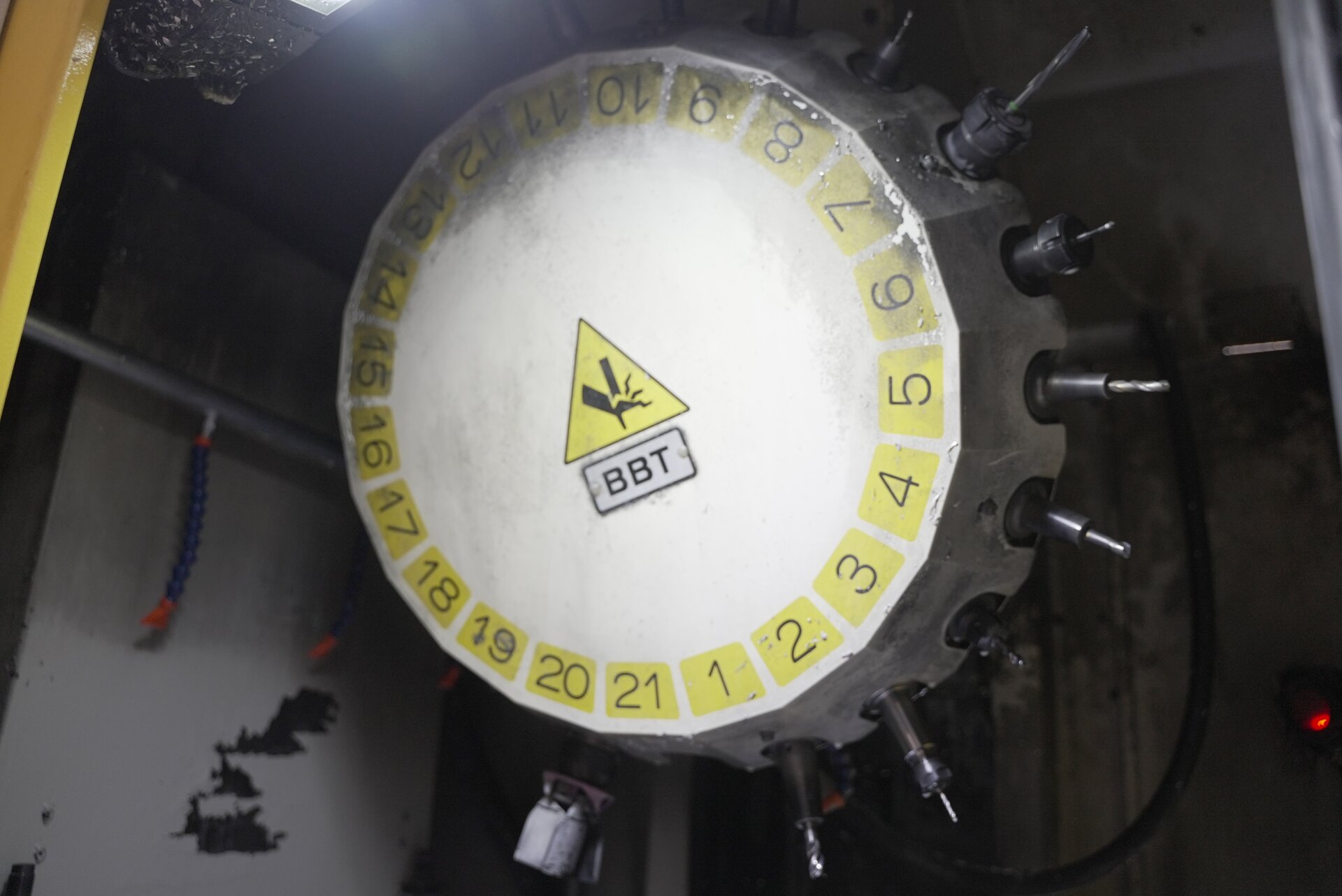
Na grafice przedstawiona została wieżyczka narzędziowa (magazyn gwiazdowy) wraz z narzędziami tnącymi. Na okręgu ponumerowanym od jeden do dwanaście znajdują się kolejne ostrza.
Zlokalizowane obok wrzeciona, wieżyczka zawiera wiele stacji, gdzie można umieszczać różnorodne narzędzia tokarskie. Wieżyczka narzędziowa automatycznie przechowuje i wymienia narzędzia tnące w trakcie procesu obróbki.
Budowa narzędzi skrawających
Narzędzia skrawające zbudowane są z dwóch głównych części składowych:
części roboczej – w której zawierają się elementy biorące udział w procesie skrawania,
części chwytowej – która służy do ustalenia położenia narzędzia.
Część robocza i część chwytowa wykonywane są z różnych materiałów, w związku z czym muszą być ze sobą łączone. Łączenie wykonuje się na kilka sposobów:
zgrzewanie elektryczne lub tarciowe,
lutowanie płytek,
klejenie,
mocowanie mechaniczne.
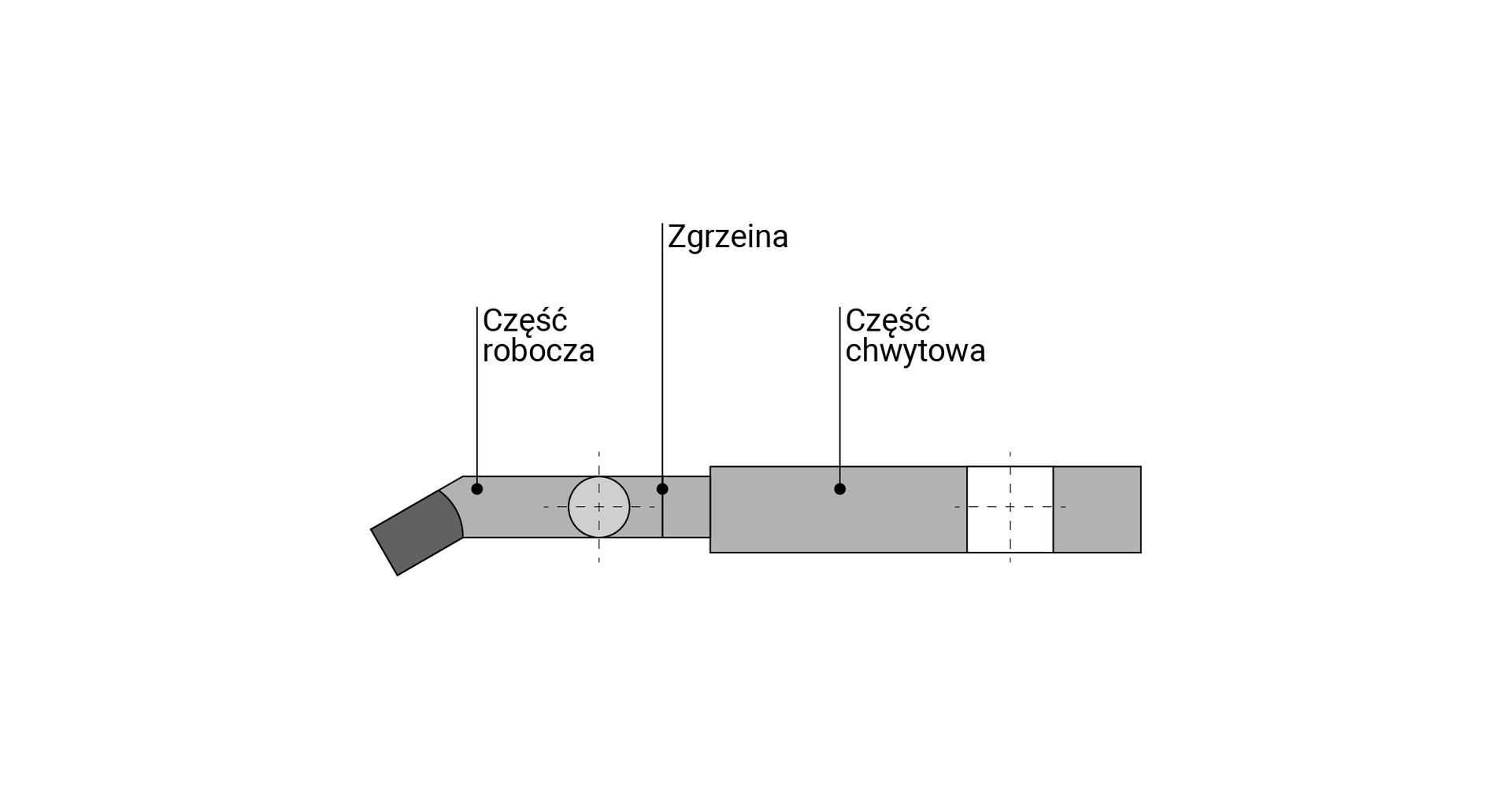
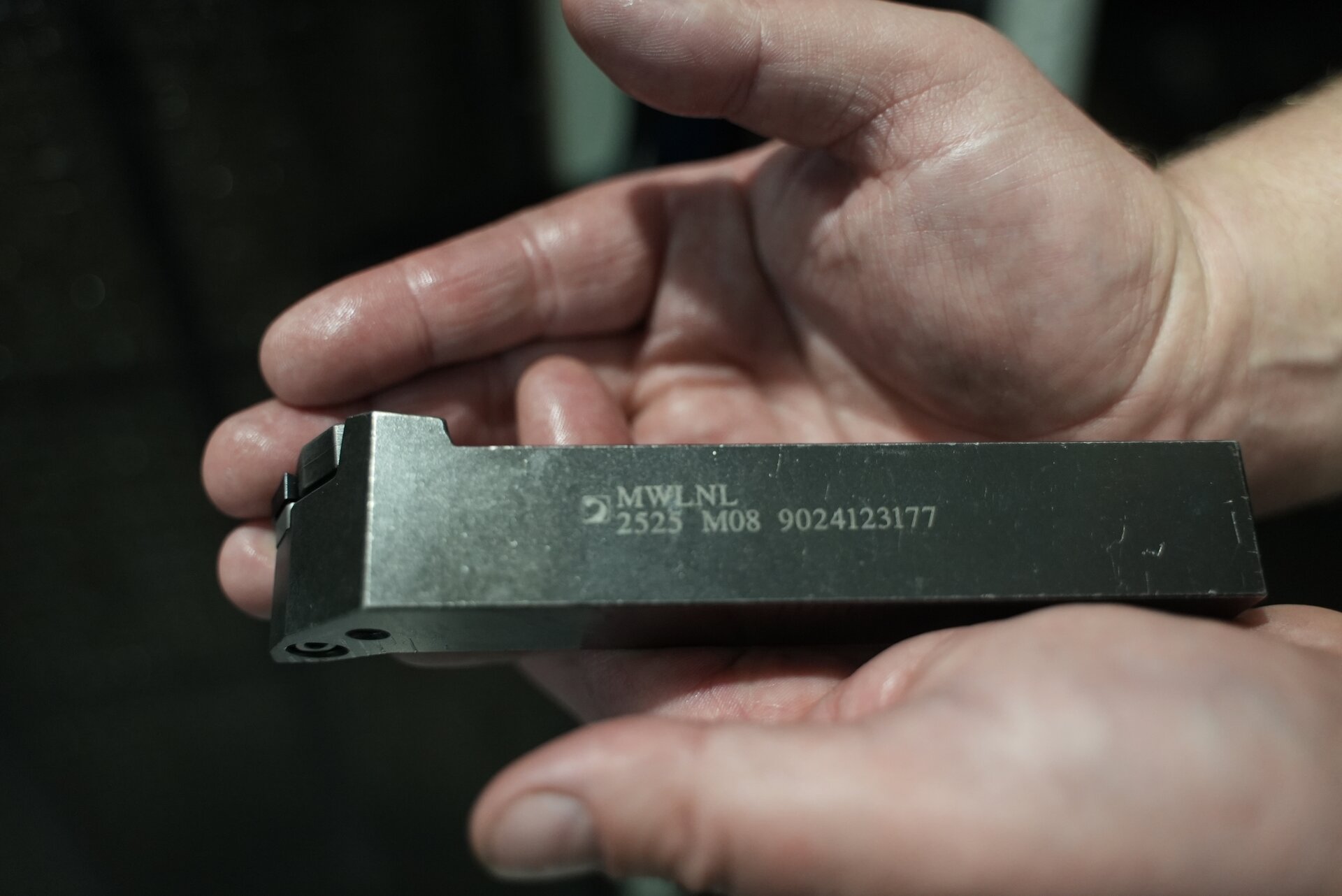
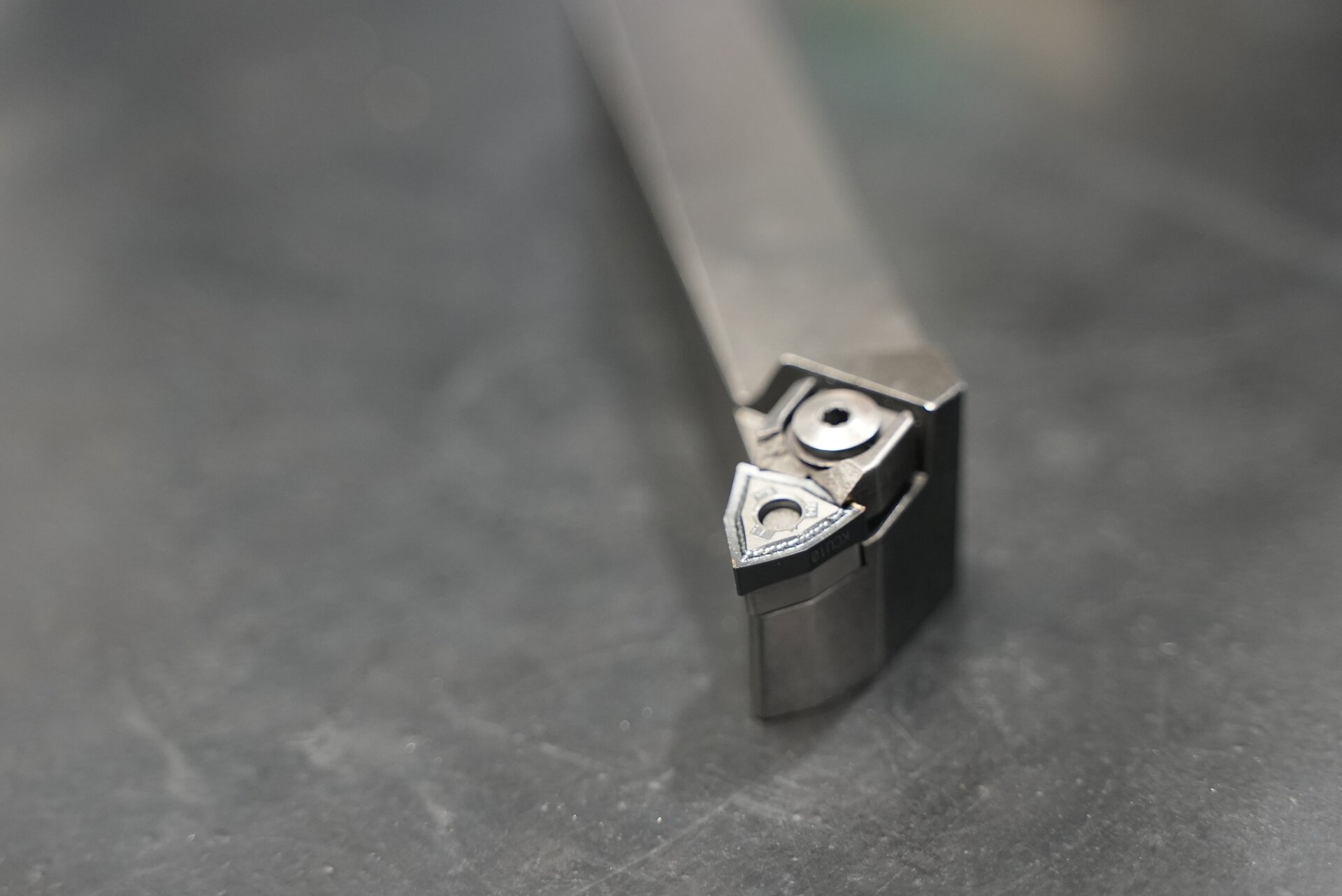
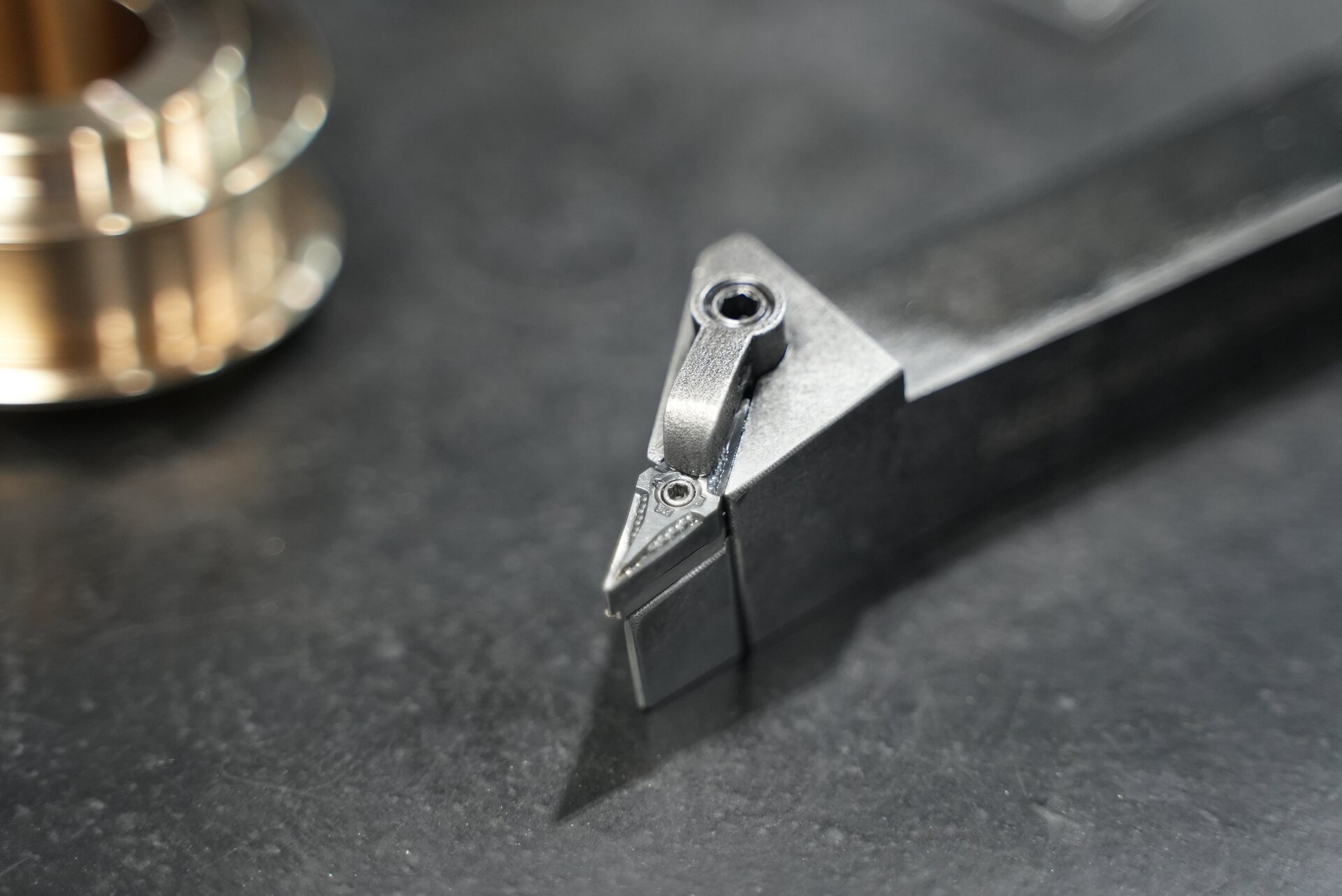
Na grafikach przedstawiono przykładowe narzędzie skrawające składające się z części roboczej, zgrzeiny (zwanej również złączem lutowanym) oraz części chwytowej. Na końcu części roboczej znajduje się ostrze.
Geometria ostrza i jej wpływ na obróbkę
Geometria ostrza tokarskiego ma zasadniczy wpływ na proces obróbki materiału. Kąt ostrza ma znaczenie nie tylko dla samej jakości powierzchni przedmiotu poddanego procesowi obróbki, ale także dla trwałości ostrza i ekonomii procesu toczenia.
Schemat przedstawia geometrię ostrza tokarskiego. Pod kolejnymi numerami znajdują się:
Numer jeden. Kąt przyłożenia.
Numer dwa. Pomocniczy kąt przyłożenia.
Numer trzy. Przejściowy kąt przyłożenia.
Numer cztery. Kąt natarcia.
Numer pięć. Przejściowy kąt przystawienia.
Kąt przystawienia – przy dużych wartościach tego kąta po obróbce otrzymuje się dużą chropowatość; kiedy zmniejsza się wartość tego kąta, poprawia się powierzchnia, jednakże wzrastają również opory skrawania i drgania. Zalecany zakres .
Pomocniczy kąt przystawienia – kąt ten zmniejsza chropowatość powierzchni. Zalecany zakres do . Kąt przyłożenia – kąt ten zmniejsza tarcie pomiędzy przedmiotem obrabianym a powierzchnią przyłożenia noża; zwiększa również trwałość ostrza. Wraz ze zwiększeniem tego kąta, na skutek zmniejszenia tarcia, zużycie noża zmniejsza się; trwałość ostrza się zwiększa, ale jednocześnie zmniejsza wytrzymałość (zmniejszenie pola przekroju ostrza). Zalecany zakres do .
Uwaga: kąt nie może mieć wartości ujemnej.
Kąt natarcia – wartość tego kąta jest odpowiedzialna za wielkość odkształceń, jakim podlega wiór. Im kąt jest większy, tym mniejsze jest odkształcenia wióra oraz odkształcenia i obciążenia cieplne noża. Duże wartości kąta osłabiają jednakże jego wytrzymałość. Zalecany zakres do , zalecany zakres do . Uwaga: kąt nie może mieć wartości ujemnej.
Kąt pochylenia głównej krawędzi skrawającej – od wartości tego kąta zależą dwie rzeczy: kierunek spływu wiórów i stopniowe wcinanie się ostrza w obrabiany materiał podczas toczenia przerywanego. Zalecany zakres do . W trakcie toczenia przerywanego zaleca się kąty o mniejszej wartości.
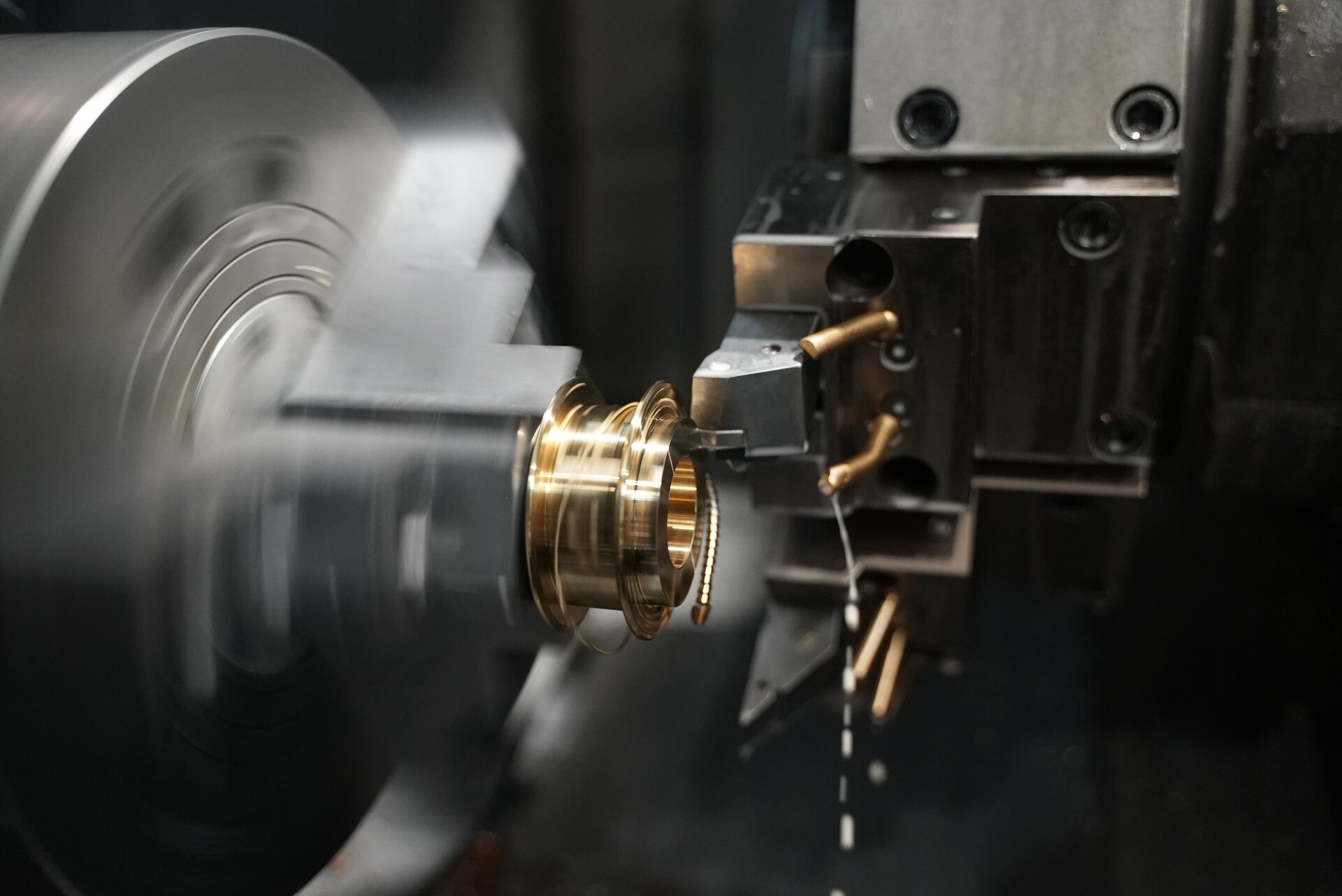
Materiały narzędziowe
Materiały stosowane do produkcji narzędzi wykorzystywanych przy obróbce skrawaniem muszą charakteryzować się między innymi dużą twardością i udarnością, wytrzymałością na ściskanie, skręcanie, zginanie czy rozciąganie. W związku z tym do produkcji narzędzi wykorzystuje się materiały takie jak HSS, HSS‑E, HSSE‑PM, oraz VHM.
Stal szybkotnąca HSS, z dodatkiem kobaltu HSS‑E, proszkowa HSSE‑PM – stal wysokostopowa, w której skład wchodzi około chromu, od do wanadu, do wolframu oraz opcjonalnie kobaltu. Stal ta jest ciągliwa, odporna na ścieranie i na obciążenia dynamiczne.
VHM węglik spiekany – materiał wytwarzany w wyniku spiekania węglików metali trudnotopliwych, w skład którego wchodzi tantal, niob, cyrkon, chrom i nikiel lub wanad. Węgliki dzieli się na dwie grupy: WC+Co oraz WC+(Ti, Ta, Nb) C+Co. Pierwsza z nich charakteryzuje się dużą twardością i ciągliwością, zaś druga odpornością na ścieranie w wysokiej temperaturze, mniejszą skłonnością do zgrzewania się z materiałem poddawanym obróbce i mniejszą erozją materiału ostrza.
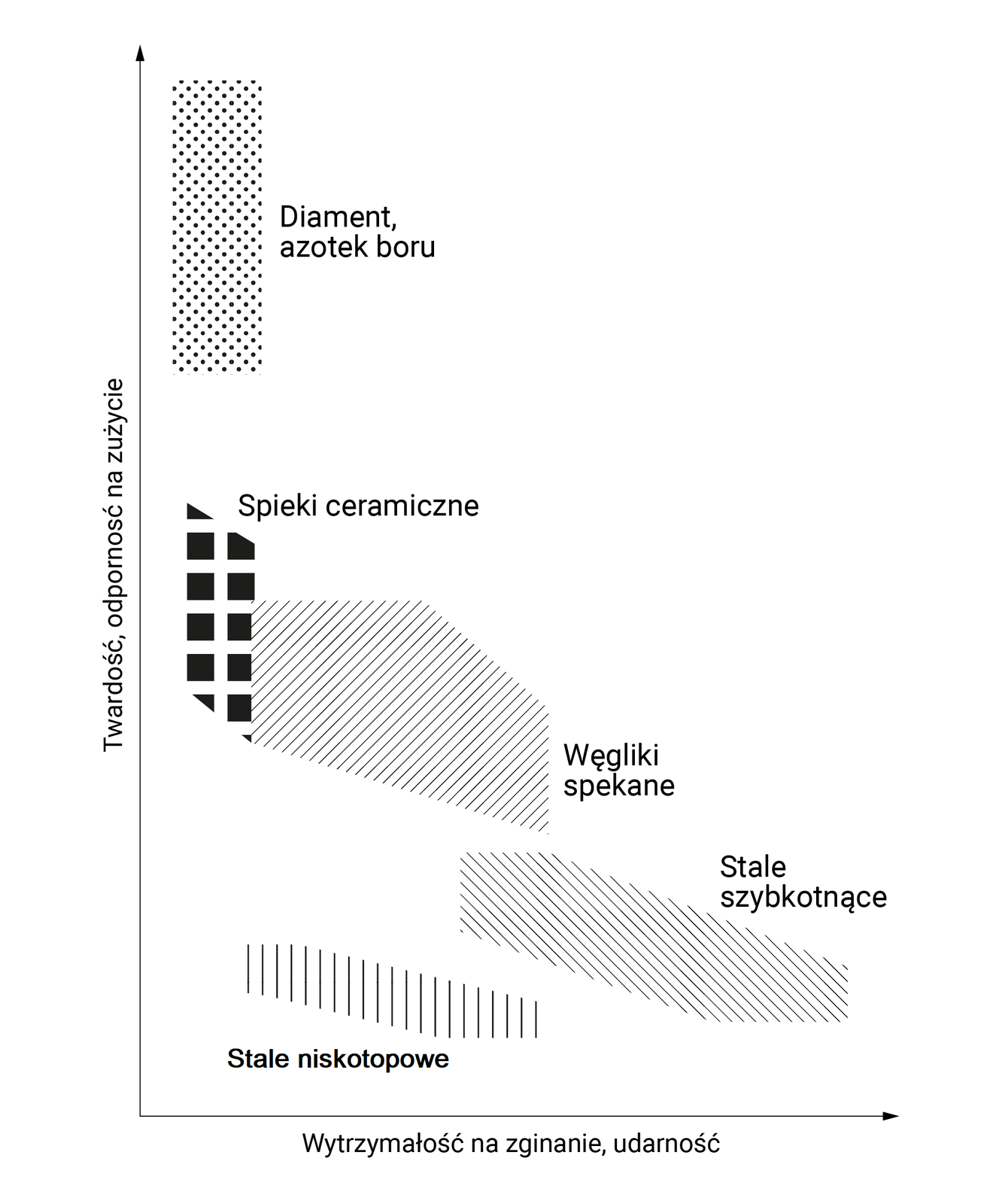
Oznaczenia kodowe narzędzi skrawających wg ISO
Oznaczenia narzędzi skrawających zbudowane są z szeregu znaków, w których każdy z nich odpowiada konkretnemu parametrowi tego narzędzia. Poniżej widoczna jest przynależność symbolu do parametru oraz różnice w charakterystykach dla narzędzia skrawającego na przykładzie płytki.
Kształt płytki i kąt naroża
Kąt przyłożenia normalny
Dokładność płytki
Kształt powierzchni natarcia i sposób mocowania płytki
Długość boku płytki
Grubość płytki
Promień naroża
Symbole dodatkowe
Postać krawędzi skrawającej
Kierunek skrawania
Symbol ustalony przez producenta (np. geometria łamacza wiórów)
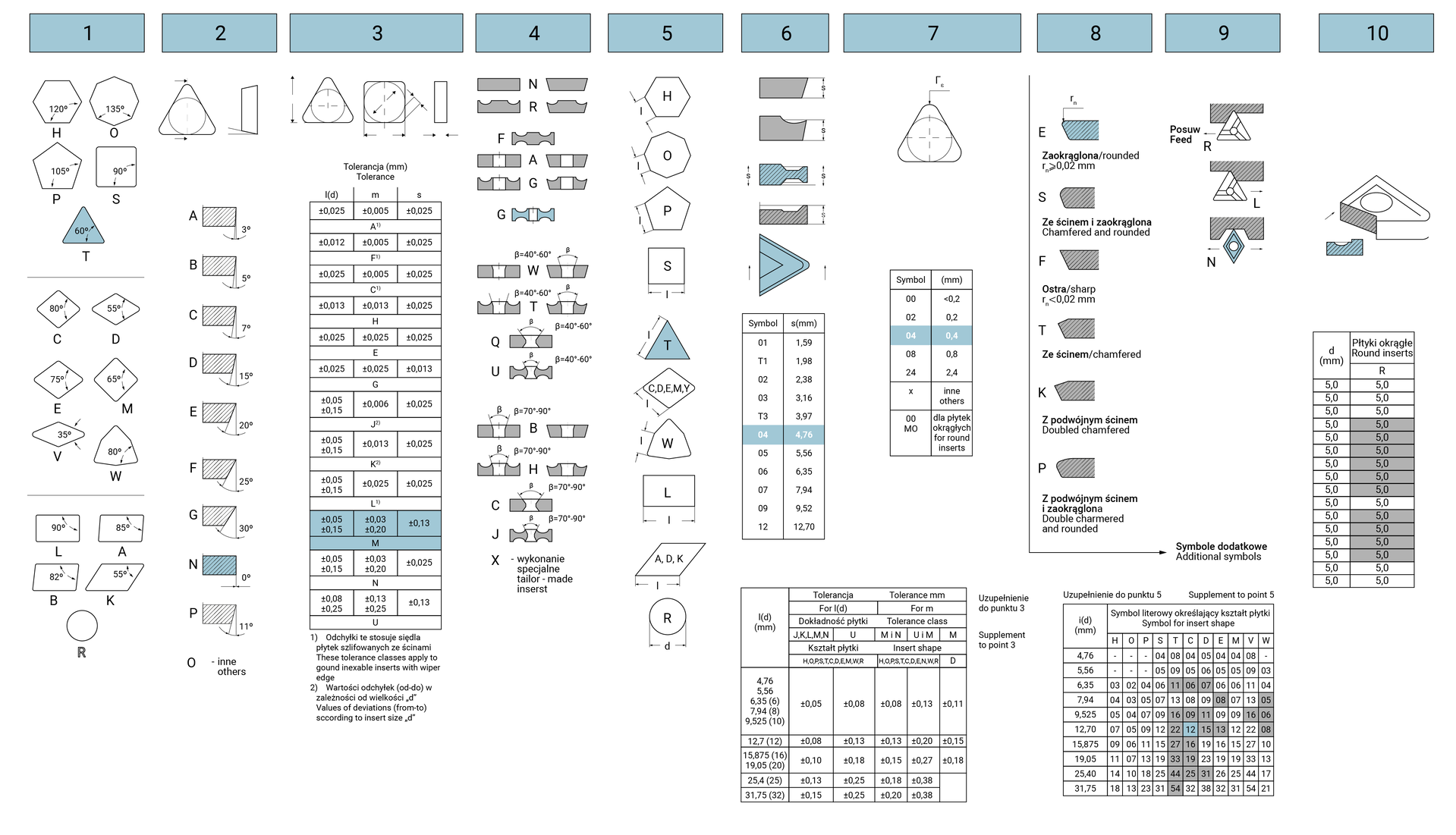
Powrót do spisu treściPowrót do spisu treści
Sterowanie
Struktura sterowania numerycznego obrabiarek
Sterowanie numeryczne NC (ang. Numerical Control) w wyniku przetwarzania informacji cyfrowych generuje sygnały sterujące ruchem maszyn lub urządzeń. W celu podkreślenia komputerowego charakteru sterowania stosuje się nazwę „sterowanie CNC” (ang. Computerized Numerical Control). Obecnie stosowane układy sterowania numerycznego są wieloprocesorowe, a do ich zadań należy nie tylko sterowanie numeryczne, ale także programowalne sterowanie maszynami i urządzeniami peryferyjnymi, komunikacja sieciowa systemu CIM (ang. Computer Integrated Manufacturing), czy teleserwis i teleprogramowanie.
Główną istotą sterowania numerycznego jest cyfrowa regulacja położenia zespołów ruchu, czyli osi maszyny.
Osie sterowane numerycznie
Osie sterowane numerycznie to każdy ruch, który jest sterowany w sposób ciągły. Należą do nich osie ruchów posuwowych oraz napędy bezstopniowe i napędy wrzecion. W układzie prostokątnym należy wyróżnić 3 prostoliniowe ruchy wzdłuż osi X, Y, Z a także 3 obrotowe ruchy wokół tych osi – A, B, C.
Pozycjonowanie jest istotne w wielu procesach produkcyjnych, w których zarówno narzędzia, jak i obrabiane przedmioty muszą być umieszczone w określonym położeniu. Takie położenie może być określone przy użyciu zderzaka mechanicznego podczas cięcia pręta o określonej długości. Możliwe jest także zastosowanie pojedynczej osi ruchu, która wówczas pozycjonuje się przy pomocy techniki sterowania numerycznego. W maszynach instaluje się wiele takich osi NC. Sterowanie osiami pojedynczymi prowadzone jest przy pomocy modułów sterowania numerycznego w sterowniku programowalnym.
Do najbardziej istotnych zadań numerycznego sterowania pozycyjnego należą:
przemieszczenia wolne i szybkie zespołów napędowych,
przemieszczenia na zadane absolutnie położenie,
przemieszczenia względem danego położenia,
przemieszczenia do punktu odniesienia lub punktu synchronizacji.
Obrabiarki CNC charakteryzują się co najmniej dwoma osiami sterowanymi jednocześnie. Sterowanie to odbywa się na zasadzie ruchu narzędzia po matematycznie określonym torze. Tokarki posiadają co najmniej dwie osie NC, frezarki co najmniej trzy (dla specjalnych zastosowań pięć), natomiast roboty zazwyczaj posiadają sześć osi NC.
Układy sterowania numerycznego CNC
W zależności od sposobu realizacji ruchów posuwowych poszczególnych osi obrabiarki wyróżnia się sterowanie punktowe, sterowanie odcinkowe i sterowanie kształtowe.
Sterowanie punktowe
Głównym celem sterowania punktowego jest precyzyjne pozycjonowanie narzędzia w określonym punkcie względem przedmiotu, niezależnie od ścieżki poruszania się narzędzia. Prędkość przemieszczania narzędzia z jednego punktu do drugiego nie ma istotnego znaczenia, jednak w celu skrócenia czasu operacji i zapewnienia bezkolizyjności ruchu narzędzia zaleca się przemieszczanie się z maksymalną prędkością po linii prostej.
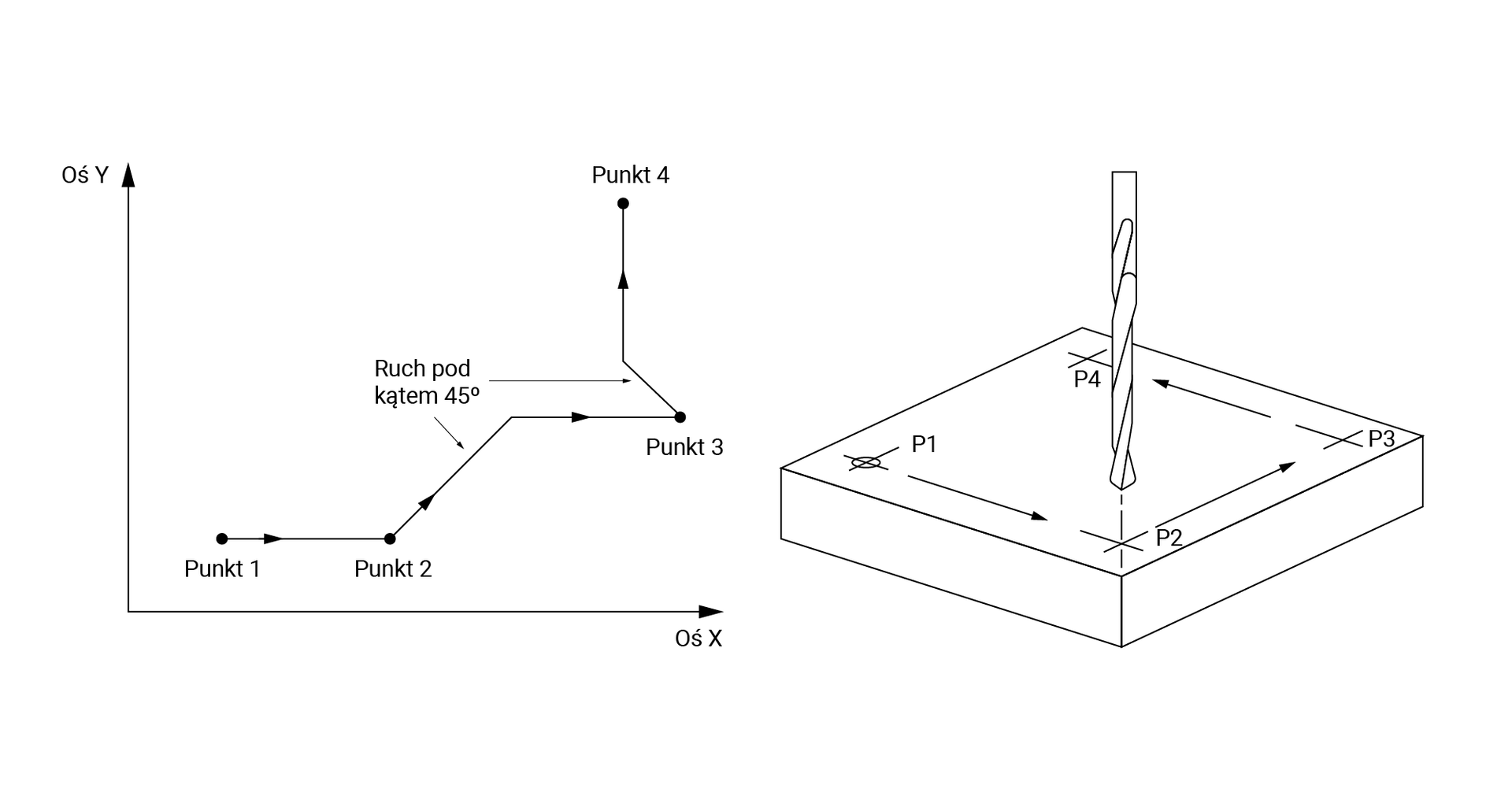
Sterowanie odcinkowe
Sterowanie odcinkowe wyróżnia się tym, że narzędzie porusza się po zdefiniowanej ścieżce i określonej prędkości. Odcinki trasy narzędzia muszą być równoległe do osi układu współrzędnych w określonej płaszczyźnie, dlatego kontury przedmiotu obrabianego mogą być równoległe do osi sterowanych.
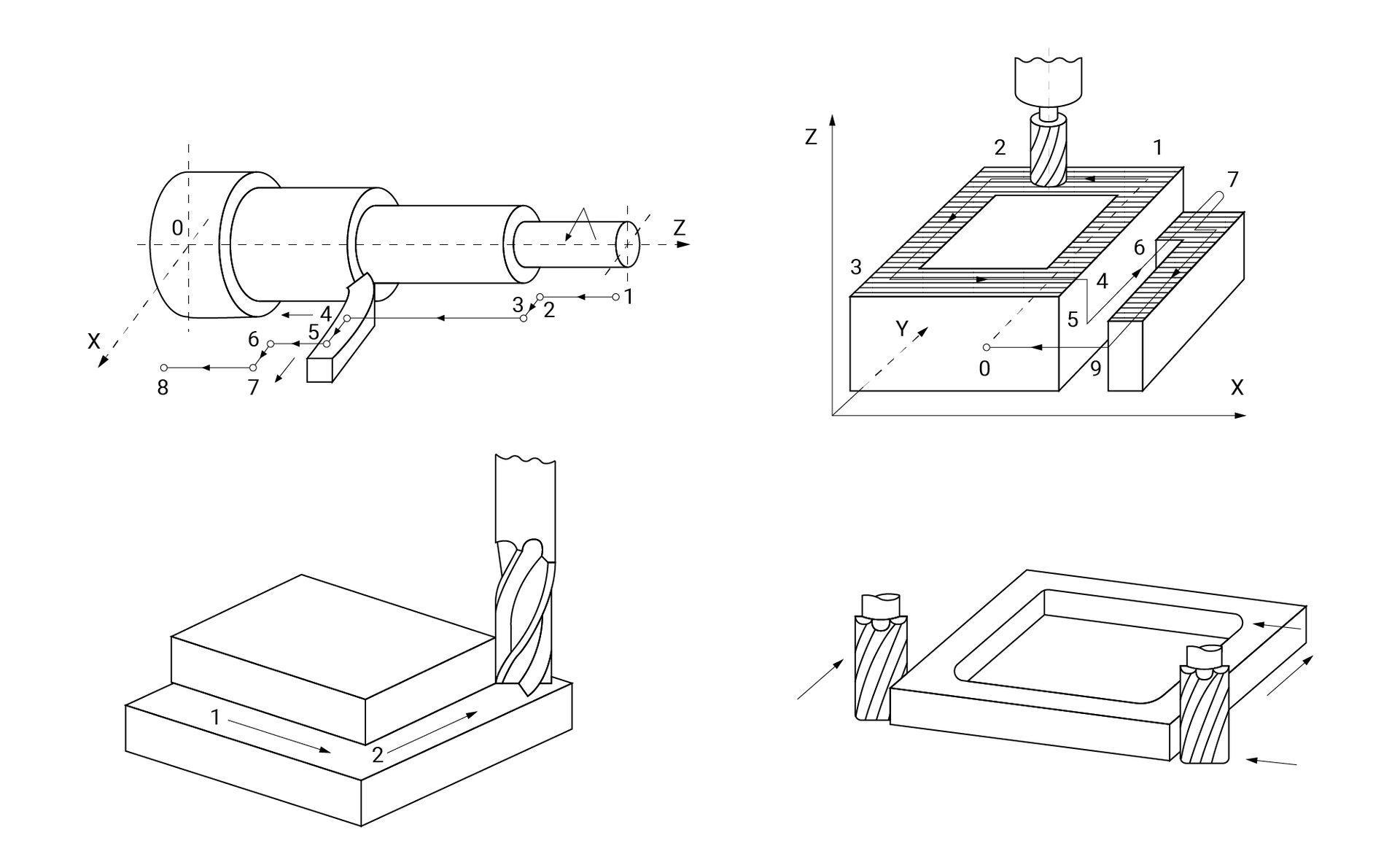
Sterowanie kształtowe
Narzędzie może poruszać się po powierzchni i w przestrzeni, umożliwiając wykonywanie skosów i łuków. Za pomocą dwóch silników napędowych można uzyskać różne kształty. Przed wykonaniem takiego ruchu układ sterowania musi określić punkty pośrednie i końcowy.
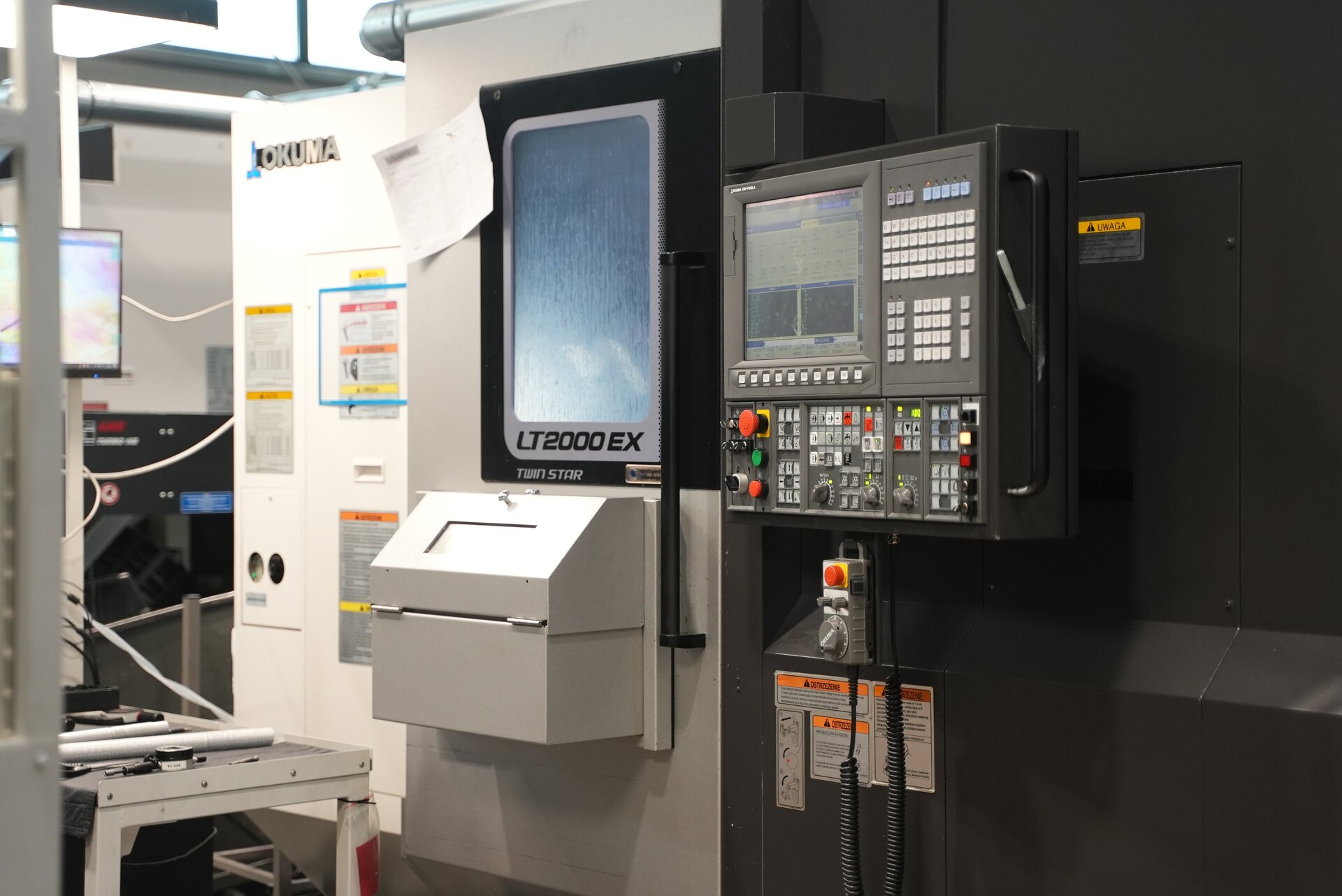
Powrót do spisu treściPowrót do spisu treści
Odmiany konstrukcyjne
Różnica pomiędzy sterowaniem obrabiarek NC i CNC
Główną różnicę między sterowaniem obrabiarek NC a CNC stanowi stopień automatyzacji, a także poziom zaawansowania technologicznego. Obrabiarka NC wykonuje określone ruchy, korzystając z wprowadzonych ręcznie liczb i instrukcji. Z kolei sterowanie obrabiarką CNC jest bardziej zaawansowane, wykorzystuje komputery do bardziej elastycznego programowania, korzystając dzięki temu z nowoczesnych technologii.
Do organizacji pracy maszyn służy sterowanie DNC (Distributed Numerical Control), które pomaga w zarządzaniu oraz kontroli obrabiarek numerycznych, stosując rozproszoną infrastrukturę komunikacyjną. Programy sterowania oraz dane numeryczne mogą być przechowywane na wielu urządzeniach. Operatorzy, za pomocą sterowania DNC, zarządzają produkcją z centralnego punktu, co przekłada się na szybsze przekazywanie danych do obrabiarek, co za tym idzie zwiększenie efektywności produkcji.
Odmiany konstrukcyjne obrabiarek sterowanych numerycznie
Obrabiarki sterowane numerycznie, tak samo jak tradycyjne, mogą być podzielone na różne kategorie, przy uwzględnieniu różnych kryteriów. Przedstawione zostaną jedynie wybrane, powszechnie stosowane rodzaje.
Najbardziej ogólną klasyfikacją jest podział według przeprowadzanego procesu obróbkowego:
frezarki sterowane numerycznie,
tokarki sterowane numerycznie,
szlifierki sterowane numerycznie,
wiertarki sterowane numerycznie,
piły taśmowe sterowane numerycznie.
Inna kategoryzacja dotyczy liczby sterowanych osi. Nowoczesne obrabiarki CNC mogą mieć sterowanie od trzech do dziewięciu osi. Dodatkowe osie są osiągane przez różne sposoby, takie jak:
dla tokarek: poprzez dodatkowe wrzeciona narzędziowe, narzędzia obrotowe lub pozycjonowanie kątowe wrzeciona, a także sterowany programowo konik lub podtrzymka,
dla frezarek: poprzez dodatkowe wrzeciona i wrzeciona narzędziowe oraz stół obrotowy.
Nagranie dostępne pod adresem https://zpe.gov.pl/a/DSHvSSylD
Nagranie
Nagranie dźwiękowe przedstawiające dźwięk obrabiarki.
Tokarki NC
Tokarki są grupą obrabiarek skrawających, zaprojektowanych przede wszystkim do obróbki przedmiotów o kształcie obrotowym (toczenie). Oprócz toczenia pozwalają wykonywać również inne czynności, takie jak: wiercenie, rozwiercanie, przecinanie, radełkowanie, gwintowanie, a także frezowanie i szlifowanie przy użyciu dodatkowych narzędzi.
W kategorii tokarek istnieje wiele różnych konstrukcji, do których należą m.in.:
tokarki poziome i pionowe (karuzelowe), które różnią się położeniem wrzeciona,
tokarki prętowe, uchwytowe i kłowe, które różnią się rodzajem obrabianego przedmiotu,
tokarki jedno- i wielowrzecionowe.
Tokarki można również podzielić na tokarki przedosiowe i zaosiowe, w których toczenie odbywa się przed osią (od dołu) lub głowica narzędziowa porusza się za osią (od góry).
Nagranie dostępne pod adresem https://zpe.gov.pl/a/DSHvSSylD
Nagranie
Nagranie dźwiękowe przedstawiające dźwięk tokarki.
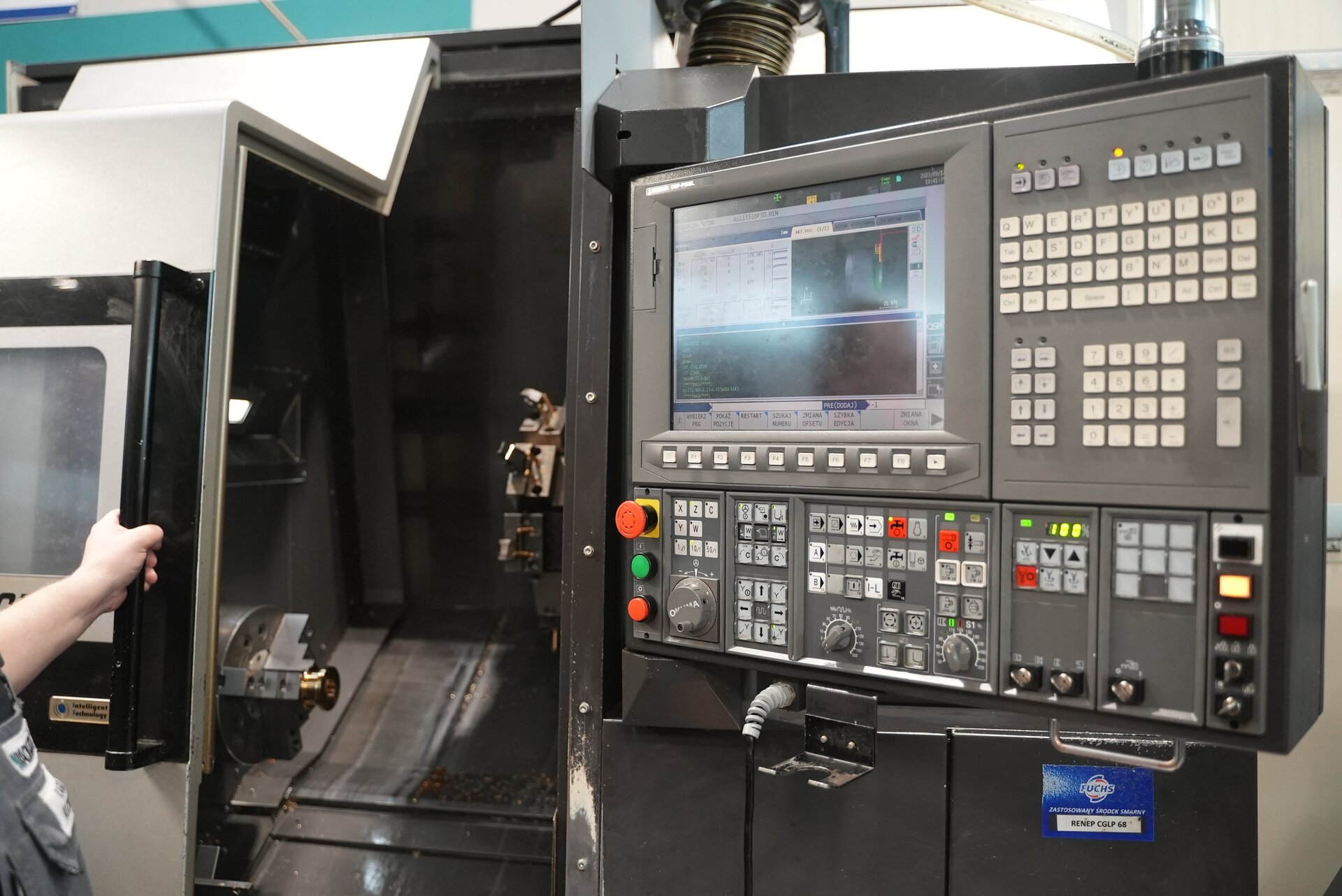
Frezarki NC
Frezarki stanowią grupę obrabiarek skrawających, wykorzystywanych do obróbki płaszczyzn, powierzchni kształtowych, rowków itp. za pośrednictwem frezów (narzędzi frezujących). Obrabiarki te cechuje wszechstronność technologiczna.
Ze względu na usytuowanie osi wrzeciona można wyróżnić:
frezarki horyzontalne,
frezarki pionowe.
W przypadku frezarek główny ruch wykonywany jest przez narzędzie umieszczone we wrzecionie. Ruchy posuwowe najczęściej wykonuje się poprzez przesuwanie przedmiotu zamocowanego na poruszającym się stole, choć istnieją również rozwiązania, w których cały wrzeciennik jest przemieszczany. Dążenie do udoskonalenia konstrukcji tych obrabiarek skupia się na możliwości realizacji kompleksowej obróbki przy jednym zamocowaniu poprzez zwiększenie liczby sterowanych osi. Ruchy w osiach obrotowych mogą być realizowane za pomocą obrotowego wrzeciennika, obracania stołu lub jego odchylania.
Nagranie dostępne pod adresem https://zpe.gov.pl/a/DSHvSSylD
Nagranie
Nagranie dźwiękowe przedstawiające dźwięk frezarki NC.
Centra obróbkowe
Centra obróbkowe są nowoczesnymi maszynami umożliwiającymi precyzyjne wykonanie skomplikowanych elementów za pomocą wielu narzędzi. Mają szerokie możliwości obróbki, takie jak: wiercenie, gwintowanie i frezowanie – dostosowane do wymagań procesu. Są wydajnymi narzędziami w procesie produkcyjnym, jednak ich wadą jest wyższy koszt zakupu w porównaniu do tradycyjnych obrabiarek CNC.
Nagranie dostępne pod adresem https://zpe.gov.pl/a/DSHvSSylD
Nagranie
Nagranie dźwiękowe przedstawiające dźwięk centrum obróbkowego.
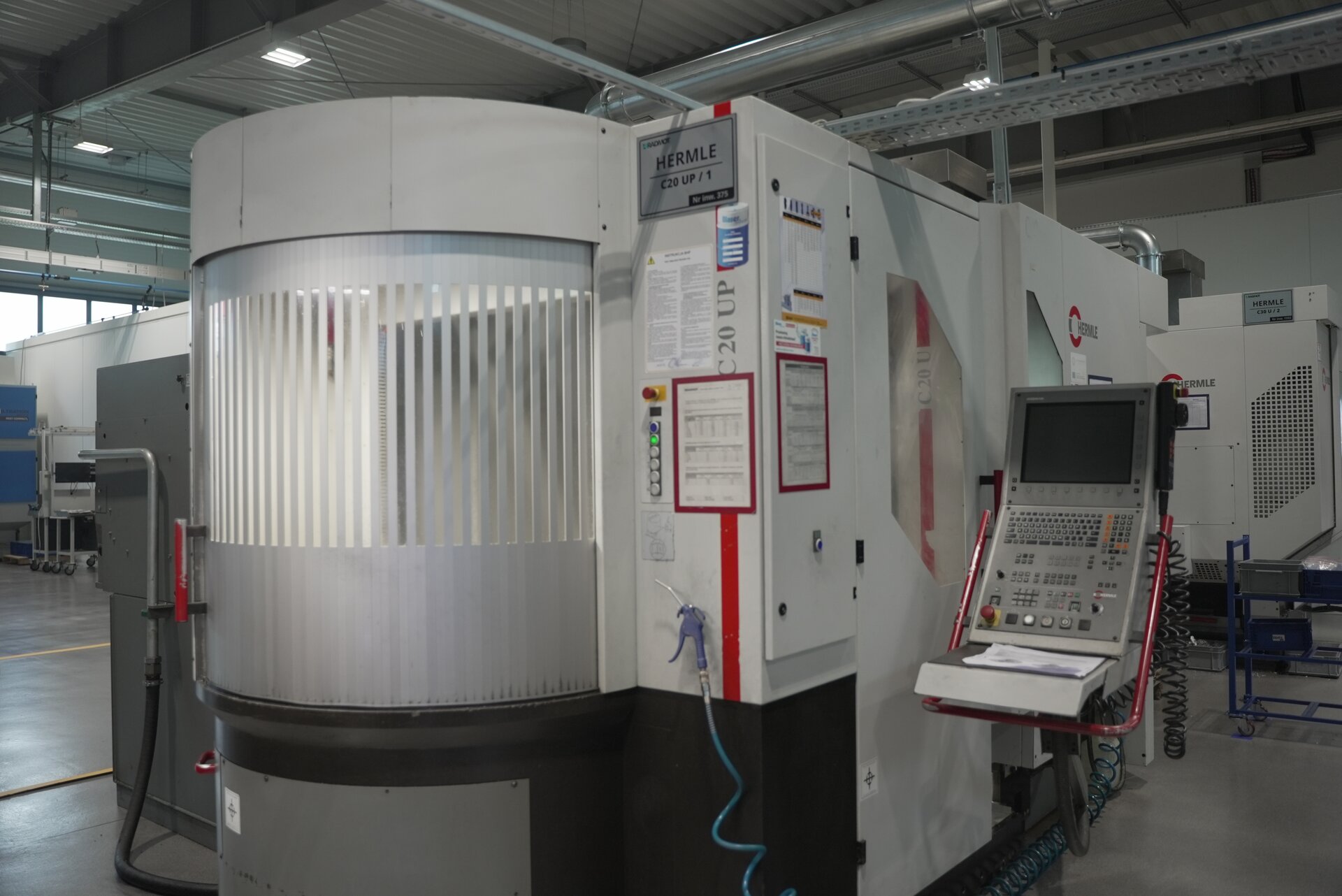
Szlifierki NC
Szlifierki NC są używane do precyzyjnej regeneracji narzędzi i utwardzonych powierzchni. Ułatwiają i przyspieszają ten proces lepiej niż tradycyjne szlifierki. Programy obróbkowe są przechowywane w pamięci urządzenia, co pozwala wyeliminować błędy popełniane często przy ręcznym sterowaniu. Maszyny szlifierskie CNC są kontrolowane przez komputer nadzorujący pracę narzędzia i położenie przedmiotu, co zapewnia wysoką precyzję obróbki, dzięki możliwości sterowania zarówno osiami prostoliniowymi, jak i osiami obrotowymi. Szybkość i efektywność pracy na tych szlifierkach przekłada się na dokładność wymiarową i gładkość powierzchni.
Nagranie dostępne pod adresem https://zpe.gov.pl/a/DSHvSSylD
Nagranie
Nagranie dźwiękowe przedstawiające dźwięk centrum obróbkowego.
Rekonfigurowalność obrabiarek
Rekonfigurowalność obrabiarek jest istotnym aspektem elastyczności wytwarzania. W przeszłości skupiano się na częściowych rozwiązaniach, takich jak elastyczne urządzenia mocujące czy przyspieszenie przezbrojenia obrabiarki, obecnie ważna jest również zdolność obrabiarek do zmian. Rekonfigurowalność oznacza, że obrabiarka może być dostosowana do różnych technologii, niezależnie od rodzaju wyrobów. Multitechnologiczne centrum obróbkowe jest przykładem takiej rekonfigurowalnej obrabiarki, która umożliwia różne sposoby obróbki (np. toczenie, frezowanie, wiercenie, szlifowanie). Obrabiarka może również pracować na sucho lub na mokro oraz obrabiać materiały w stanie utwardzonym. Dzięki rekonfigurowalności obrabiarka może być optymalnie dostosowana do aktualnych potrzeb produkcyjnych, co ma duże znaczenie techniczno‑ekonomiczne.
Inne obrabiarki sterowane numerycznie
Równolegle z rozwojem układów CNC rośnie liczba obrabiarek sterowanych numerycznie, spośród których wyróżnić można:
obrabiarki laserowe,
obrabiarki do obróbki erozyjnej.
Powrót do spisu treściPowrót do spisu treści
Technologia obróbki
Podstawy rysunku technicznego
Rzutowanie
Rysunek techniczny przedstawia trójwymiarowy przedmiot w postaci płaskich rzutów, co pozwala go określić w sposób jednoznaczny.
Rzutowanie metodą europejską
Rzutowanie metodą europejską to technika, która polega na wyznaczaniu rzutów prostokątnych przedmiotu na wzajemnie prostopadłych rzutniach. Rzuty są rozmieszczane na arkuszu rysunkowym zgodnie z rozwinięciem prostopadłościanu tworzącego rzutnię. Celem jest umieszczenie wystarczającej liczby rzutów, aby jednoznacznie przedstawić rysowany przedmiot. Metoda europejska jest stosowana w Polsce.
Rzutowanie metodą amerykańską
Rzutowanie prostokątne metodą amerykańską polega na umiejscowieniu rzutni pomiędzy obserwatorem a przedmiotem, w przeciwieństwie do wcześniej opisanego rzutowania. Ta różnica powoduje inne rezultaty i rozmieszczenie rzutów dla poszczególnych metod.
Rzutowanie z dowolnym rozmieszczeniem rzutów
Podczas rzutowania istnieje możliwość dowolnego rozmieszczenia rzutów na arkuszu, co wymaga oznaczenia kierunku rzutowania za pomocą liter. Te same litery powtarza się nad odpowiednimi rzutami.
Rzut ukośny
Rzutowanie ukośne umożliwia wykonywanie rzutów na płaszczyznę, która jest nachylona pod określonym kątem do rzutni. Rzuty mogą przedstawiać widoki zewnętrzne przedmiotów oraz przekroje, które ukazują ich wewnętrzną strukturę. Przekrój powstaje poprzez przecięcie przedmiotu wyimaginowaną płaszczyzną.
Zasady wymiarowania
Wymiary na rysunkach technicznych są umieszczone w taki sposób, aby jak najwięcej można było z nich odczytać, patrząc od dołu lub z prawej strony. Zgodnie z zasadą podaje się tylko tyle wymiarów, ile jest niezbędne do dokładnego określenia przedmiotu mierzonego.
Na obrabiarce sterowanej numerycznie układ wymiarowania jest niezbędny. Istnieją trzy rodzaje układów: równoległy, szeregowy i mieszany. W układach równoległych wymiary są podawane od jednej bazy (powierzchni lub linii). W tym przypadku programowanie absolutne jest lepsze do obróbki. W układach szeregowych wymiary są umieszczane jeden po drugim. W tym przypadku programowanie przyrostowe jest lepsze do obróbki. Wymiarowanie w układzie mieszanym to połączenie metod wymienionych wyżej.
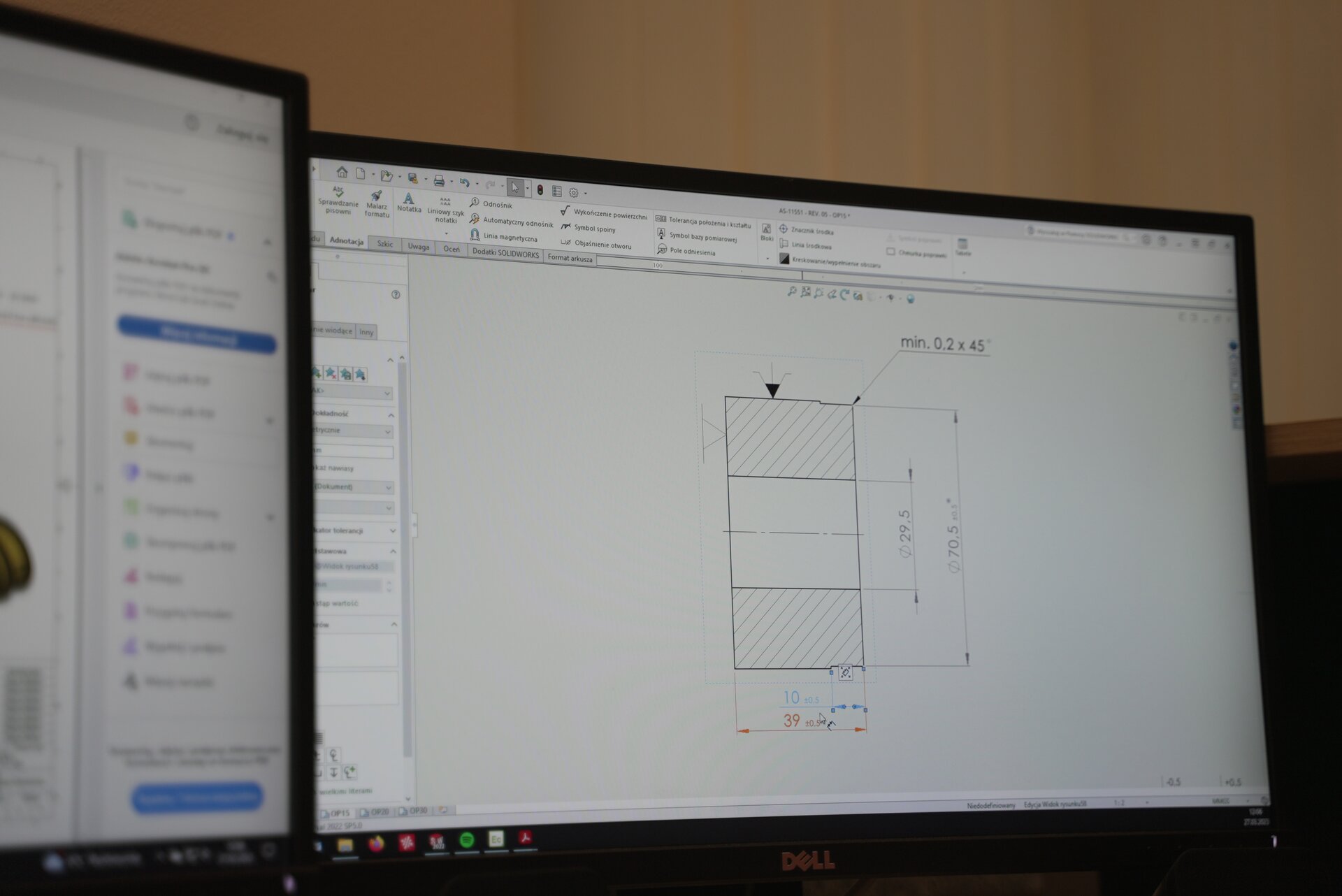
Tolerancje wymiarów
W wyniku różnic w dokładności wykonania i pomiaru rzeczywiste wymiary przedmiotów mogą odbiegać od nominalnych wymiarów podanych na rysunkach. Dlatego określa się tolerancję, czyli dopuszczalny zakres zmienności wymiaru. Tolerancja jest różnicą pomiędzy odchyłkami górną i dolną. Jest reprezentowana graficznie jako pole tolerancji, które tworzone jest przez proste przedstawiające te granice.
Tolerowanie może być realizowane w sposób liczbowy, symbolowy lub mieszany. Tolerowanie symbolowe jest stosowane dla otworów (duże litery – cyfry) i wałków (małe litery – cyfry). Litera określa położenie pola tolerancji względem wymiaru nominalnego, natomiast cyfra określa dokładność i szerokość pola tolerancji.
Oznaczanie chropowatości
Chropowatość może zostać oznaczona poprzez:
znak chropowatości,
oznaczenie i wartość liczbową parametru Ra [µm] (a),
oznaczenie sposobu obróbki powierzchni (b),
wartość odcinka elementarnego (c),
oznaczenie kierunkowości struktury powierzchni (d),
parametr chropowatości innych niż Ra (f).
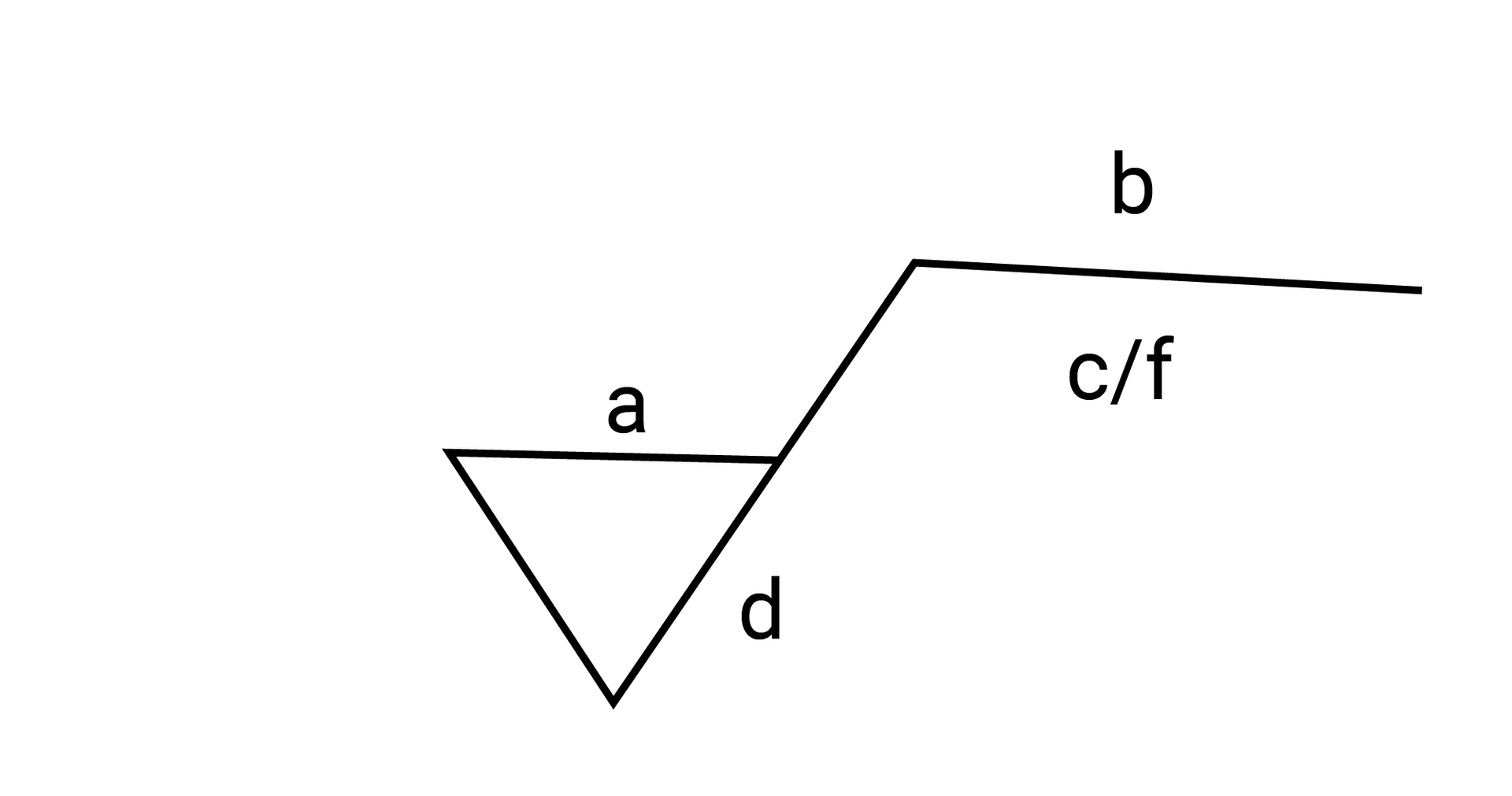
Oznaczenia tolerancji kształtu i położenia
Tolerancję kształtu i położenia oznacza się przy pomocy znaku tolerancji i jej wartości wyrażonej w milimetrach. Można spotkać dodatkowy symbol odpowiadający elementowi odniesienia, względem którego tolerancja została zdefiniowana.
Zdarza się, że przed wartością tolerancji występują dodatkowe symbole:
Ø – wtedy, gdy wartość tolerancji jest średnicą,
R – w przypadku, gdy wartość tolerancji jest promieniem,
T – wtedy, gdy wartość tolerancji jest odległością między dwiema równoległymi prostymi lub płaszczyznami, które ograniczają obszar tolerancji,
T/2 — wtedy, gdy wartość tolerancji to odległość pomiędzy jedną z dwóch prostych lub płaszczyzn równoległych, które ograniczają obszar tolerancji i ich odpowiednio prostą lub też płaszczyzną symetrii,
O (znak w postaci okręgu) — gdy obszar tolerancji jest kulisty. Stosuje się również następujące znaki:
M – w przypadku tolerancji zależnej,
P – gdy pole tolerancji jest zewnętrzne.
Matematyczne podstawy opisu geometrycznego
Opis elementów geometrii na płaszczyźnie lub w przestrzeni oparty jest na układach współrzędnych. Praktycznie stosowane układy to układy współrzędnych prostokątnych (kartezjańskich) oraz układy współrzędnych biegunowych.
Układ współrzędnych prostokątnych składa się z dwóch lub trzech wzajemnie prostopadłych osi, które przecinają się w początku układu nazywanym „punktem zerowym”. Pozycja punktu jest określana poprzez odległość od początku układu do rzutów prostopadłych punktu na poszczególne osie. Te odległości stanowią współrzędne punktu, które mogą przyjmować wartości dodatnie lub ujemne, w zależności od kierunku pomiaru.
Układ współrzędnych biegunowych przypomina płaski układ współrzędnych prostokątnych, ale różni się od niego tym, że położenie punktu jest określane za pomocą pary liczb (r, theta). Liczba r reprezentuje długość promienia łączącego punkt z wyróżnionym punktem układu zwanym „biegunem”, natomiast liczba theta reprezentuje kąt pomiędzy promieniem a wyróżnionym kierunkiem nazywanym „prostą biegunową”.
Dokumentacja techniczna
Dokumentację techniczną można podzielić na dokumentację konstrukcyjną i technologiczną.
Dokumentacja konstrukcyjna obejmuje różne elementy, takie jak: rysunki, schematy, warunki techniczne i dokumentację ruchową. Rysunki wykonawcze są szczególnie istotne w technologii obróbki.
Dokumentacja technologiczna, oparta na dokumentacji konstrukcyjnej, składa się: z kart technologicznych, instrukcji obróbki, instrukcji uzbrojenia obrabiarki i innych dokumentów dotyczących technologii wykonania wyrobu. W instrukcjach wyróżnia się m.in.: stanowisko robocze, liczbę i kolejność zabiegów czy warunki obróbki i informacje dodatkowe do wykonania danej operacji. Zakres i szczegółowość dokumentacji zależy od kwalifikacji personelu i wielkości produkcji w danym zakładzie.
Ustalanie baz obróbkowych
Właściwe ustalenie i mocowanie przedmiotu jest kluczowe dla jego poprawnego wykonania. Przedmiot posiada 6 stopni swobody, które mogą być ograniczone poprzez jego ustalenie. Przykładowo, umieszczenie przedmiotu na stole obrabiarki odbiera mu 3 stopnie swobody, pozwalając na obrót wokół osi prostopadłej do stołu (Z) oraz ruch wzdłuż osi równoległych do stołu (X, Y). Po ustaleniu przedmiotu konieczne jest jego zamocowanie, np. poprzez pola elektromagnetyczne. Wybierając powierzchnię bazową, należy kierować się zasadą, aby była obrobiona i pokrywała się z bazą przyjętą przez konstruktora. W przypadku surowych powierzchni bazowa powinna być stosunkowo równa i duża, zapewniając tym samym pewniejsze podparcie. Wykorzystanie przyjętej powierzchni bazowej we wszystkich operacjach przyczynia się do osiągnięcia wyższej dokładności wymiarowo‑kształtowej.
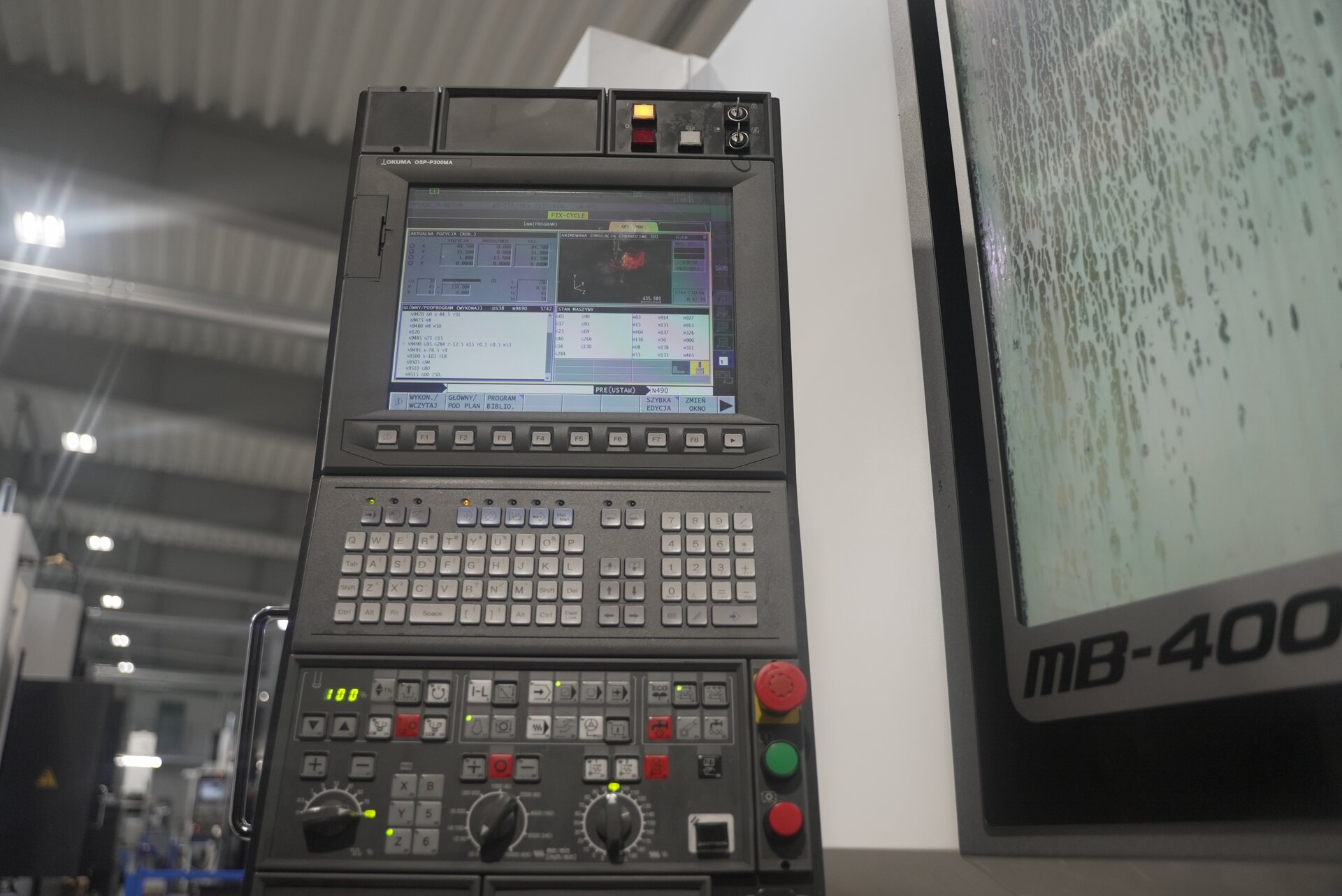
Bazy obróbkowe są konieczne do określenia ustalenia i zamocowania przedmiotu obrabianego w uchwycie obróbkowym.
Powrót do spisu treściPowrót do spisu treści
Podstawowe metody obróbki skrawaniem
Toczenie
Toczenie tokarkami to metoda obróbki skrawaniem używana do wykonywania przedmiotów o kształtach brył obrotowych. Toczenie polega na ruchu obrotowym przedmiotu obrabianego i ruchu posuwowym narzędzia skrawającego. Istnieje wiele odmian toczenia, zależnie od kształtu i rodzaju powierzchni obrabianego przedmiotu, rodzaju obrabiarki i warunków procesu. Przytoczone odmiany obejmują toczenie powierzchni zewnętrznych i wewnętrznych oraz toczenie powierzchni walcowych, stożkowych i kształtowych. Toczenie może być wykonywane na tokarkach poziomych i pionowych, a także w różnych kierunkach ruchu posuwowego, takich jak toczenie wzdłużne, poprzeczne, wgłębne i profilowe. W toczeniu prędkość skrawania zależy od prędkości obrotowej wrzeciona i średnicy przedmiotu obrabianego. Parametr posuwu określa odległość, jaką narzędzie przemieszcza się podczas jednego pełnego obrotu przedmiotu obrabianego. Głębokość skrawania to odległość między powierzchnią, która ma być skrawana, a już obrobioną powierzchnią. Czas skrawania zależy od długości skrawania, posuwu, prędkości obrotowej wrzeciona i liczby przejść narzędzia.
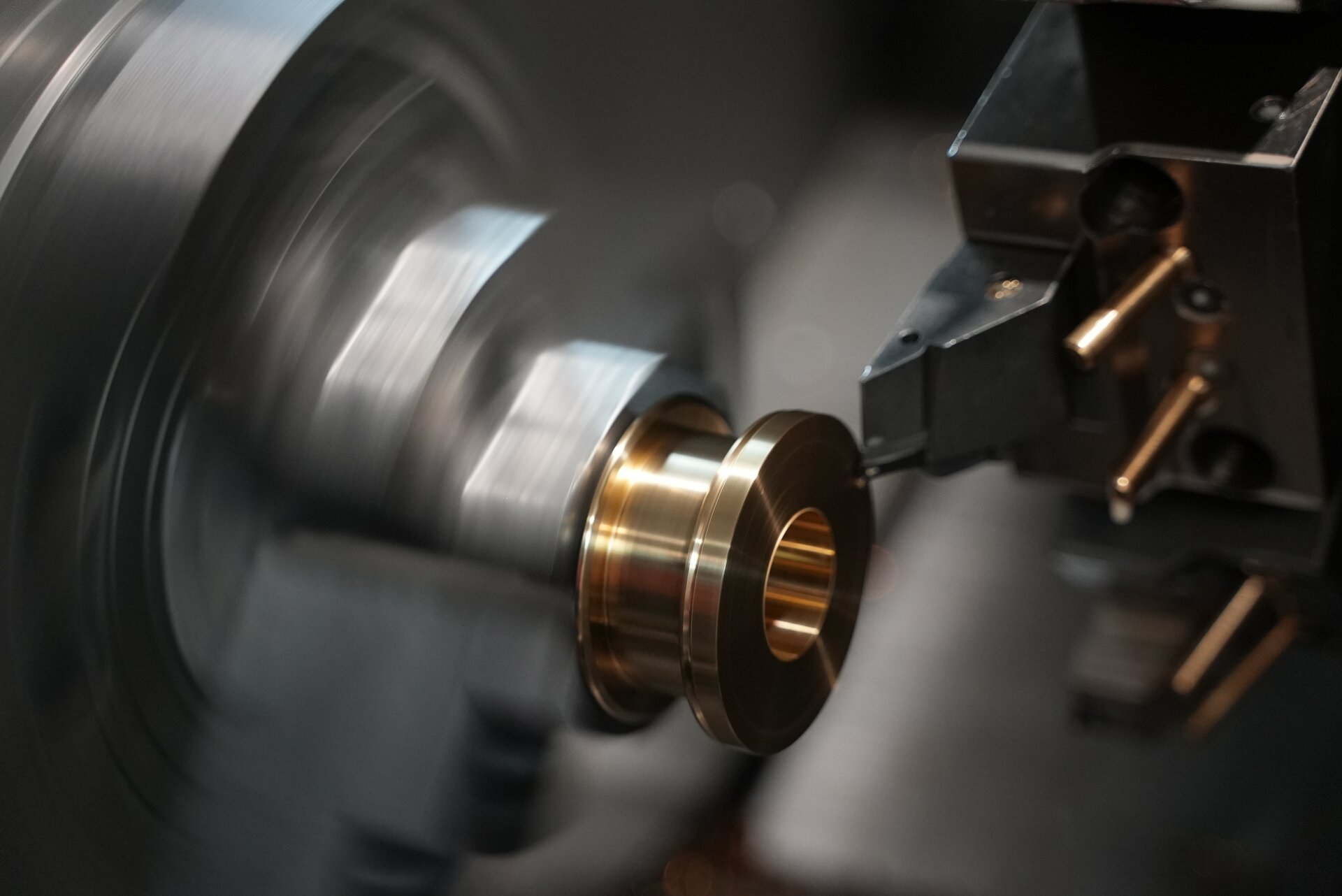
Frezowanie
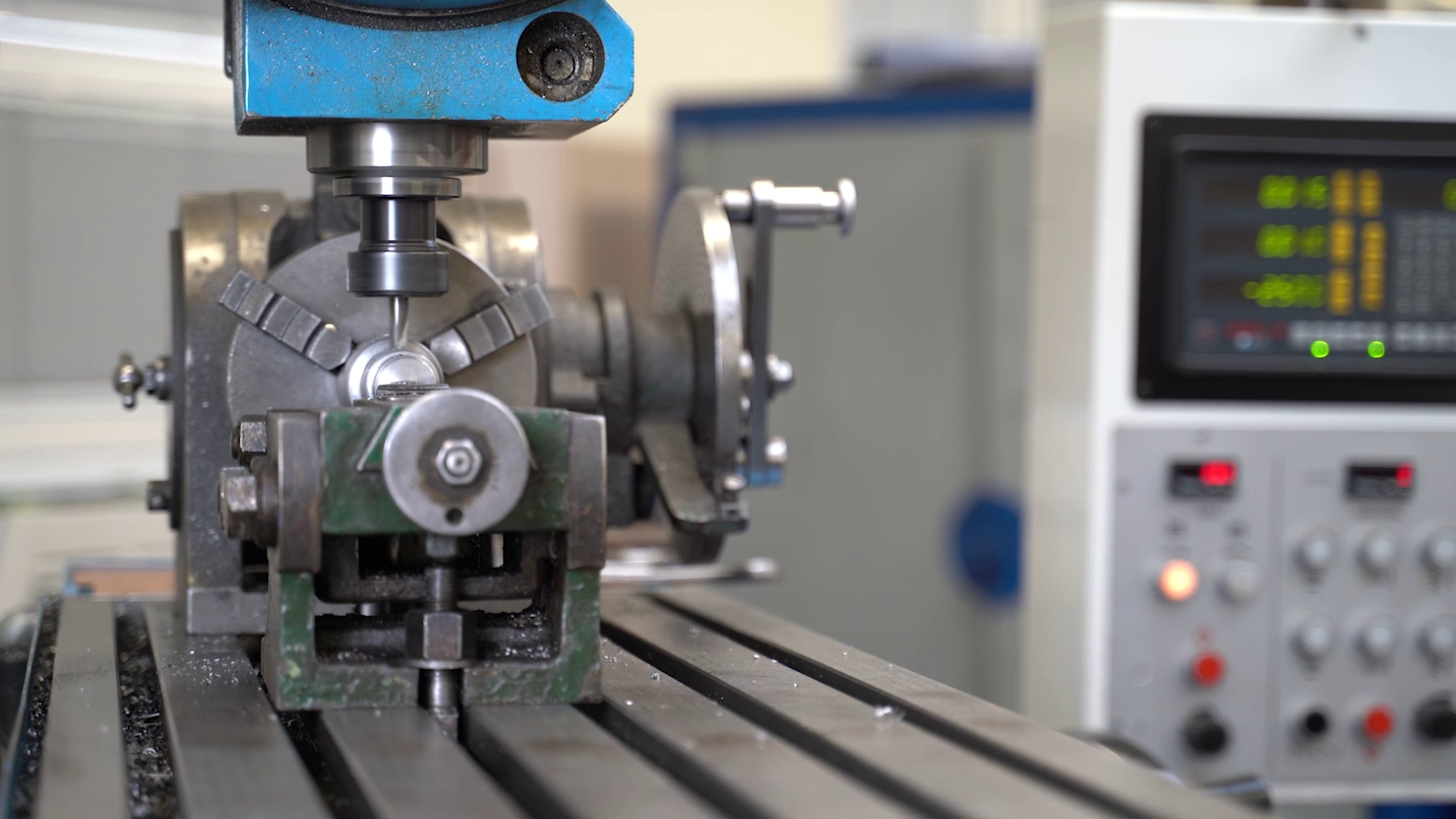
Frezowanie to metoda obróbki skrawaniem, która umożliwia tworzenie płaszczyzn, rowków, kanałków, powierzchni kształtowych, gwintów i uzębień. W frezowaniu narzędzie wykonuje ruch obrotowy, a przedmiot obrabiany wykonuje ruchy posuwowe. Frezowanie jest efektywne, ponieważ materiał zbędny jest usuwany jednocześnie przez wiele ostrzy. Wyróżnia się frezowanie czołowe, w którym ostrza są rozmieszczone na powierzchni czatowej i obwodowej, oraz frezowanie obwodowe, w którym ostrza znajdują się tylko na powierzchni obwodowej. Proces frezowania może obejmować takie operacje jak frezowanie płaszczyzn, frezowanie profilowe powierzchni, frezowanie rowków oraz frezo‑toczenie.
Wiercenie, rozwiercanie, pogłębianie
Wiercenie, rozwiercanie i pogłębianie to procesy obróbki skrawaniem stosowane do tworzenia otworów. Wiercenie jest najczęściej używaną metodą, która polega na tworzeniu otworów w pełnym materiale. Rozwiercanie jest wykorzystywane do wykończenia istniejących otworów, co zapewnia wysoką jakość powierzchni. Pogłębianie polega na powiększaniu otworów przy użyciu specjalnego narzędzia, poprzez usuwanie materiału na obwodzie otworu. Wyróżnia się pogłębianie walcowe i stożkowe. Prędkość wiercenia jest określana jako prędkość obwodowa narzędzia, a posuw na obrót wykorzystuje się do obliczania prędkości zagłębiania. Podstawowe parametry charakteryzujące otwory to średnica, głębokość, sposób wykonania i materiał obrabiany.
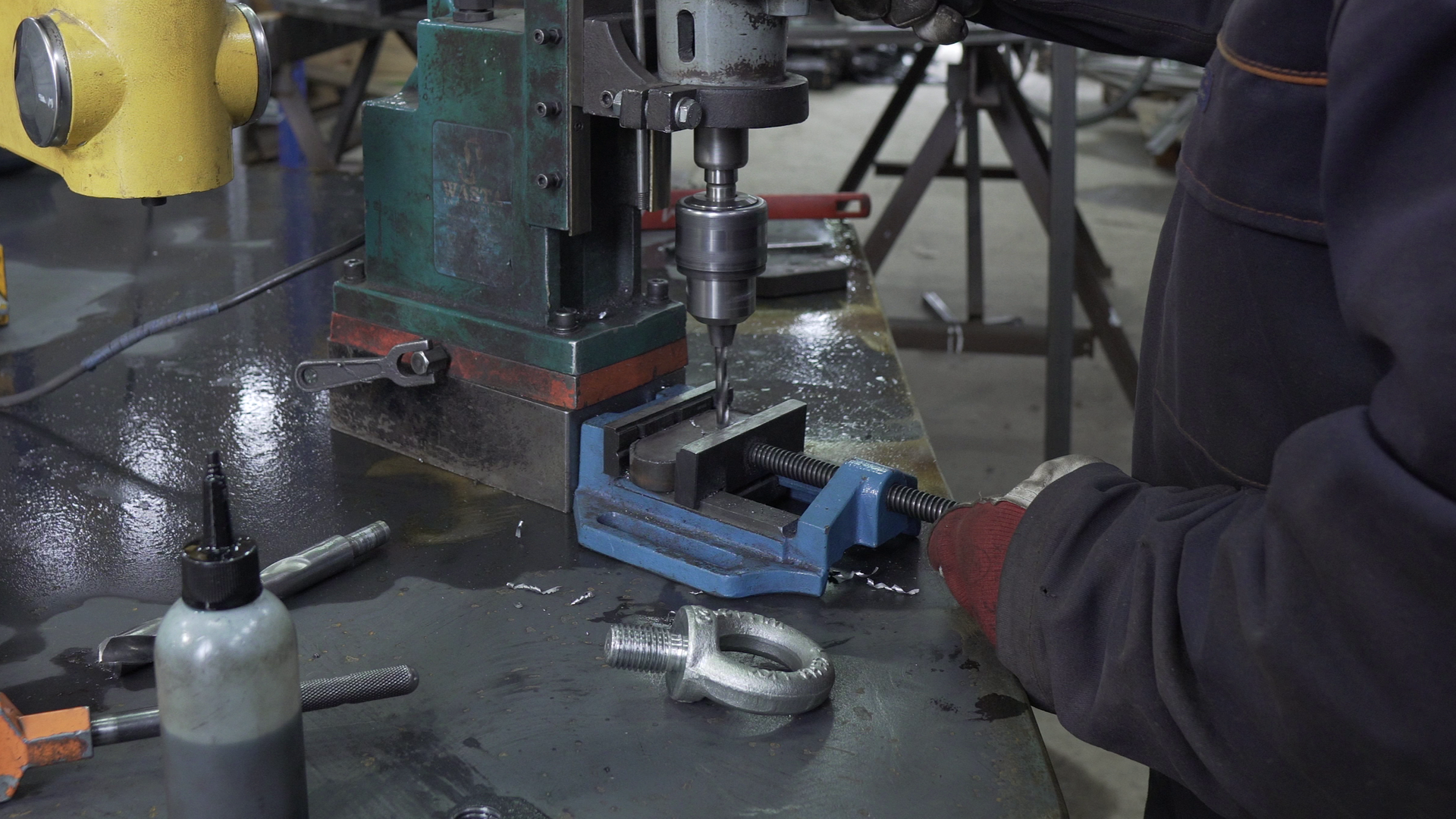
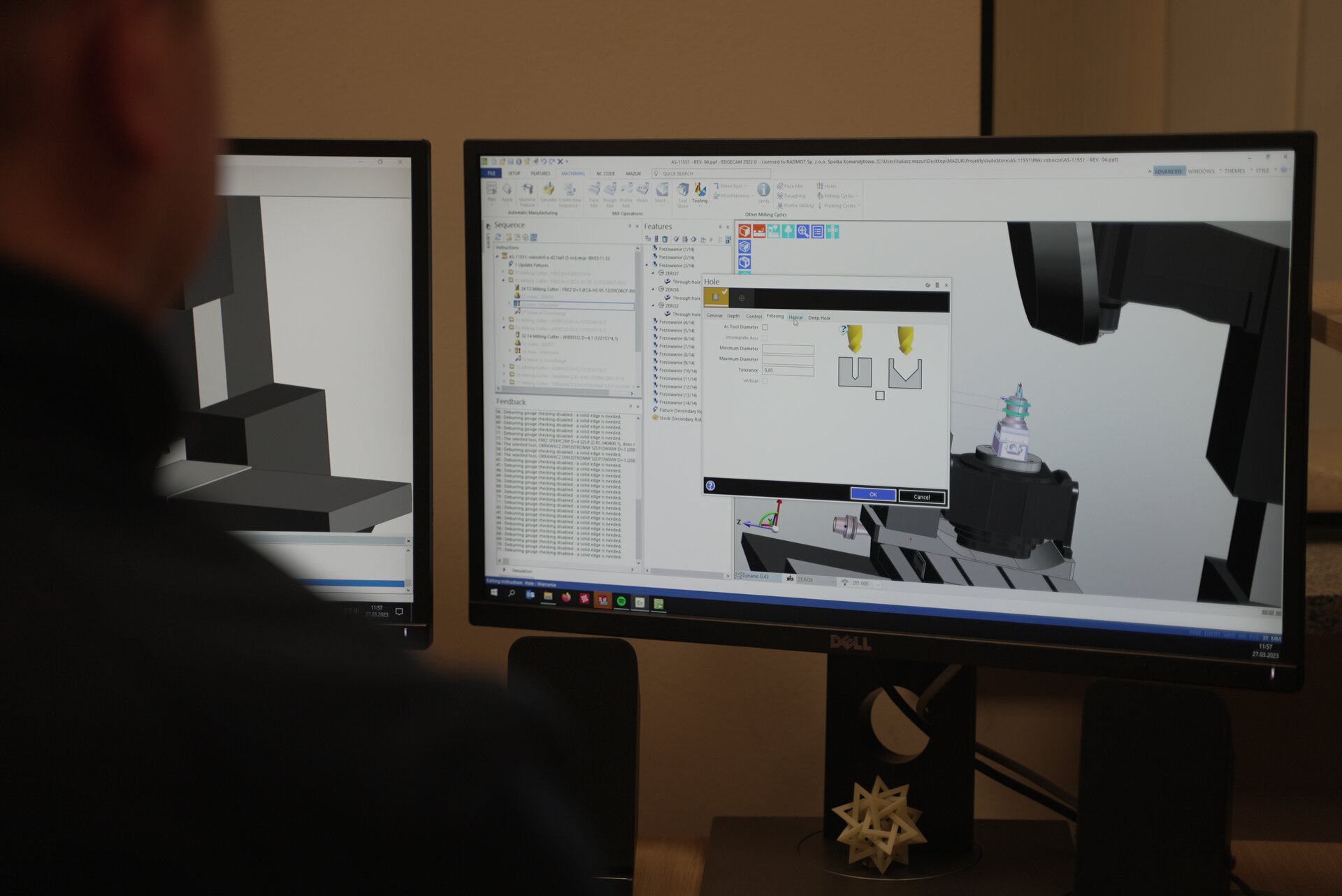
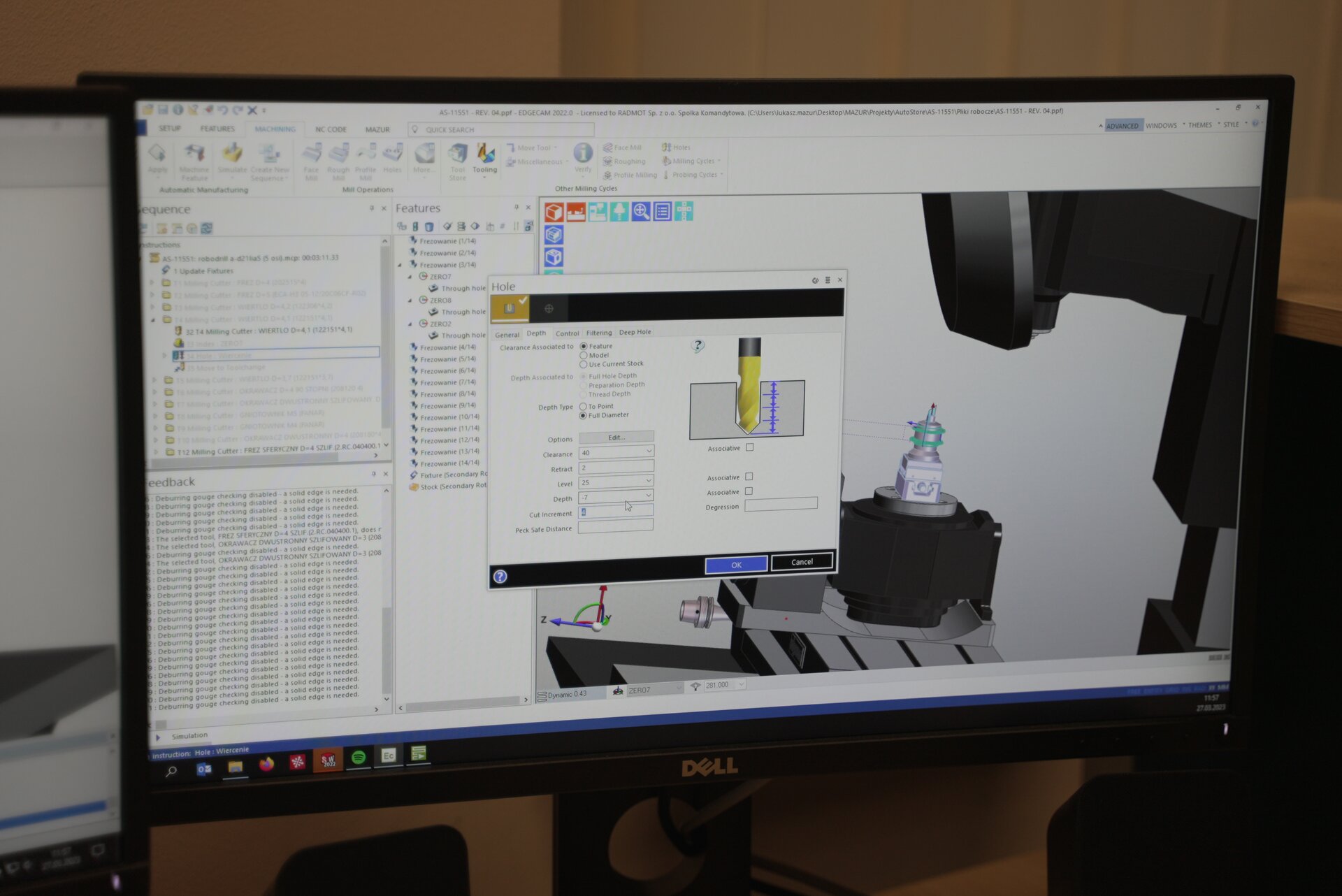
Grafiki przedstawiają procesy wiercenia, rozwiercania i pogłębiania w programie komputerowym.
Narzędzia skrawające
Narzędzia skrawające składają się z dwóch głównych części: części roboczej, która odpowiada za proces skrawania, oraz części chwytowej służącej do ustalenia położenia i mocowania narzędzia. Te dwie części są zwykle wykonane z różnych materiałów i mogą być łączone poprzez zgrzewanie, lutowanie, klejenie lub mocowanie mechaniczne. Mocowanie mechaniczne, zwłaszcza przy użyciu płytek z węglików spiekanych lub ceramiki, zapewnia wysoką niezawodność narzędzi. W przypadku zużycia lub uszkodzenia krawędzi skrawającej narzędzia wymiana lub przestawienie części roboczej (płytki) jest wystarczające, bez konieczności ponownego ustawiania narzędzia na maszynie.
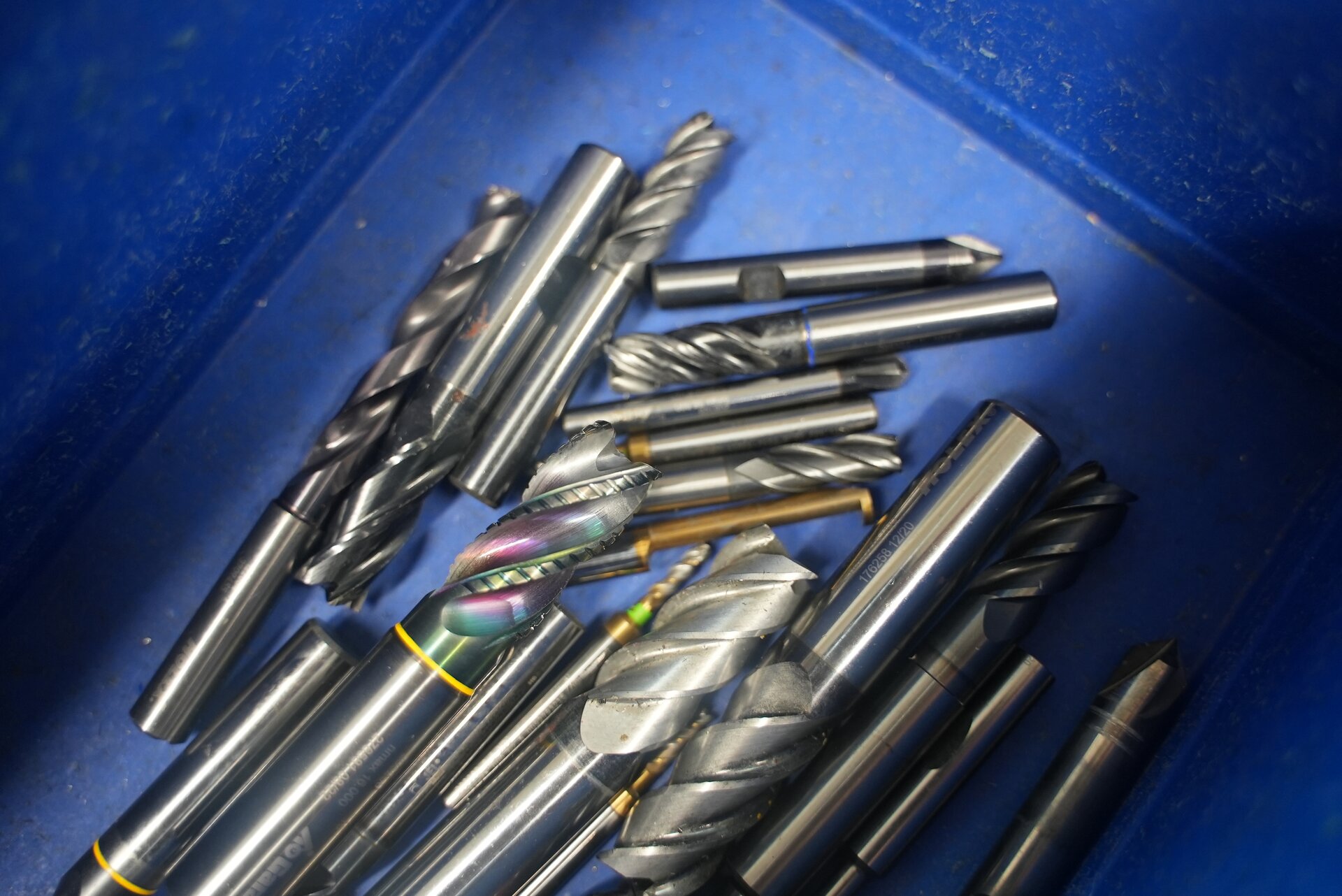
Grafika przedstawia narzędzia skrawające o różnych średnicach i wymiarach leżące w pudełku.
Fizykalne podstawy skrawania
Narzędzia skrawające wykorzystują działanie klina do rozdzielania warstw materiału. Siła F działająca na klin pokonuje opór materiału i siły tarcia na powierzchniach bocznych. Zmniejszenie kąta klina prowadzi do większych składowych sił prostopadłych FN i większego tarcia zależnego od kształtu i jakości powierzchni klina. Nachylenie jednej z powierzchni klina pod kątem alfa do powierzchni obrobionej zmniejsza siłę tarcia. Kąt gamma między prostopadłą do kierunku ruchu a powierzchnią Ay klina wpływa na odkształcenie warstwy skrawanej, gdzie mniejszy kąt gamma wymaga większej siły F do pokonania oporu odkształcenia.
Powrót do spisu treściPowrót do spisu treści
Podstawy programowania obrabiarek CNC
Komputerowe sterowanie numeryczne
Komputerowe sterowanie numeryczne (CNC) dekoduje program sterujący i przetwarza instrukcje geometryczne i technologiczne na sygnały elektryczne. Impulsy sterujące są przekazywane do zespołów sterowanych obrabiarki, takich jak silniki napędu głównego i ruchu posuwowego. Układy pomiarowe dostarczają informacje o aktualnej pozycji. CNC wykorzystuje układy mikroprocesorowe do przetwarzania informacji, umożliwiając większą automatyzację obróbki i kompensację błędów. W budowie układu CNC wyróżnia się mikroprocesor, monitor programowania i diagnozowania, pamięć RAM, interfejs komunikacyjny oraz programowalny sterownik logiczny PLC. Układy CNC oferują szybkie obliczenia, elastyczne programowanie przemieszczeń i graficzne wspomaganie programowania.
Czynności składające się na tworzenie programu sterującego
W procesie programowania obróbki wykonuje się kilka istotnych czynności. Na początku programista powinien zapoznać się z rysunkiem wykonawczym, który zawiera niezbędne informacje geometryczne i technologiczne dotyczące obrabianego przedmiotu. Następnie, przy współpracy z technologiem, należy utworzyć plan obróbki, uwzględniając proces technologiczny. Określenie oprzyrządowania takiego jak uchwyty obróbkowe jest istotne dla programisty, aby mógł uwzględnić zamocowanie przedmiotu w programie obróbki. Ponadto programista musi posiadać wiedzę na temat narzędzi skrawających i ich parametrów technologicznych.
Kolejnym krokiem jest ustalenie poszczególnych etapów obróbki, takich jak punkty dosuwu narzędzi, ruchy robocze, wymiana narzędzi, włączanie/wyłączanie obrotów wrzeciona, chłodziwa, korekcja toru ruchu narzędzi, parametry technologiczne itp. Na koniec zapisuje się te etapy obróbki w odpowiednim języku programowania i formacie dostosowanym do danego układu sterowania CNC.
Metody programowania obrabiarek CNC
Programowanie obrabiarek CNC polega na tworzeniu programu sterującego w odpowiednim języku i formacie na odpowiednim nośniku. Ten program zawiera niezbędne informacje dotyczące operacji technologicznych i przejść w procesie obróbki. Istnieją różne metody programowania obrabiarek CNC zależne od sposobu przetwarzania danych. Są nimi programowanie ręczne, programowanie automatyczne oraz programowanie dialogowe, które stanowi pewne wyjątki od tradycyjnej klasyfikacji metod.
Programowanie ręczne
Programowanie ręczne to bezpośrednie tworzenie programu sterującego w języku i formacie odpowiednim dla konkretnej obrabiarki i jej układu sterowania, podczas którego programista lub technolog korzysta z dostępnych informacji zawartych w technologicznych bazach wiedzy, takich jak: poradniki, tablice materiałowe, dokumentacje techniczno‑ruchowe obrabiarek, katalogi narzędzi, elektroniczne bazy narzędzi itp. W ten sposób realizowane są czynności potrzebne do stworzenia programu sterującego.
Programowanie automatyczne
Programowanie automatyczne obejmuje dwuetapowe przetwarzanie danych, które składa się z procesora i postprocesora. W procesorze tworzone są dane pośrednie na podstawie programu źródłowego lub modelu CAD przedmiotu obrabianego. W tym etapie dokonuje się obliczeń geometrycznych i technologicznych, wykorzystując bazy danych i automatyczny dobór parametrów skrawania. Programy źródłowe są zapisywane w określonym języku programowania, takim jak APT, EXAPT, GTJ i zawierają instrukcje geometryczne i technologiczne. Następnie dane pośrednie są adaptowane do konkretnej obrabiarki w postprocesorze, gdzie tworzony jest program sterujący. Programowanie automatyczne CAD/CAM wymaga utworzenia modelu przedmiotu obrabianego w systemie CAD. Importuje się ten model do systemu CAM, gdzie następuje automatyczne tworzenie torów ruchu narzędzi na podstawie geometrii obróbki. Systemy CAM oferują elastyczność w wyborze cykli obróbkowych, definicji oraz obsługę wieloosiowej obróbki. Weryfikacja obróbki na wirtualnej maszynie zapewnia większe bezpieczeństwo przed uruchomieniem programu na rzeczywistej obrabiarce CNC.
Programowanie dialogowe
Programowanie dialogowe to proces tworzenia kompletnych cykli obróbkowych bezpośrednio na układzie sterowania przez określanie parametrów przy użyciu grafiki pomocniczej. Układ sterowania umożliwia pełną kontrolę wprowadzanych danych, sprawdzając ich poprawność, zakres wartości i zależności logiczne.
Podstawy programowania ręcznego układów CNC Sinumerik na bazie kodu ISO
Podstawy programowania ręcznego układów CNC Sinumerik na bazie kodu ISO opierają się na zgodności języka i formatu instrukcji programu sterującego z normami ISO. Pomimo że te normy definiują podstawowy zestaw poleceń, nie obejmują one wszystkich zasad programowania, co prowadzi do różnic pomiędzy układami sterowania różnych producentów.
Struktura programu sterującego
Struktura programu sterującego w układach CNC jest określona przez Polską Normę (PN) i składa się z programu operacji technologicznej. Program ten zawiera zapisane w odpowiednim języku i formacie na nośniku instrukcje, które sterują automatycznym układem. Instrukcje determinują przesunięcia i prędkości. Programy są podzielone na bloki danych, z których każdy opisuje sekwencję procesu obróbki i składa się z kolejnych słów. Pierwszy blok to blok nagłówkowy, a ostatni to blok końcowy zawierający funkcję kończącą program lub podprogram. Słowa składają się z adresu i wartości liczbowej, definiując funkcje w bloku danych. Słowa mogą być modalne (zachowujące swoją aktywność między blokami) lub niemodalne (aktywne tylko w danym bloku) i mogą być przedblokowe (wykonywane przed innymi słowami w bloku) lub poblokowe (wykonywane po pozostałych słowach w bloku). Układy CNC Sinumerik umożliwiają również stosowanie adresów rozszerzonych z wykorzystaniem rozszerzeń numerycznych lub liter łacińskich w formie wyrażeń arytmetycznych.
Podprogramy
Podprogramy są fragmentami programu sterującego, które można wywołać do realizacji określonych zadań. Ich wykorzystanie pozwala na tworzenie bardziej czytelnych programów i ograniczenie objętości poprzez wielokrotne wywoływanie tych samych podprogramów. Dzięki temu unika się powtarzania grup bloków danych w programie sterującym. Programowanie z podprogramami pozwala również na tworzenie struktury programu z ciągiem bloków danych zapisanych w różnych plikach, co ułatwia edycję i wykorzystanie w innych programach. Można także wywoływać podprogramy z poziomu innych podprogramów, tworząc zagnieżdżone podprogramy. Struktura podprogramu jest podobna do struktury głównego programu, z różnicą polegającą na specjalnym bloku nagłówkowym (np. %_N_PODPROG_SPF) i funkcji końca podprogramu (M17) w bloku końcowym.
Deklaracja sposobu wymiarowania
Funkcje Systemu Miar
G70/G71/G700/G710
Dotyczy obróbki: toczenie, frezowanie
G70 Ujęcie podstawowych danych wymiarowych w calach, funkcja modalna;
G71 Ujęcie podstawowych danych wymiarowych w milimetrach, funkcja modalna;
G700 Podanie w calach wszystkich danych wymiarowych; posuwy – w cal/obr. (dla G95) lub cal/min (dla G94), funkcja modalna;
G710 Podanie wszystkich danych wymiarowych w milimetrach; posuwy – w mm/obr. (dla G95) lub mm/min (dla G94), funkcja modalna;
Pod terminem „podstawowe informacje wymiarowe” rozumie się dane dotyczące przemieszczenia (X, Y, Z), parametry interpolacji (I, J, K), wartości promienia okręgów (CR=), promienie biegunowe (RP=) oraz przesunięcie punktu zerowego. W przypadku funkcji G700 i G710 oprócz podstawowych danych wymiarowych istnieje również możliwość zmiany jednostek posuwu.
Funkcja G71, która umożliwia wymiarowanie metryczne, jest najczęściej aktywowana bezpośrednio po uruchomieniu sterownika. Natomiast programowanie w jednostkach calowych wymaga deklaracji funkcji G70 na początku programu lub w bloku, w którym chcemy zmienić sposób wymiarowania na ten.
Programowanie funkcji ruchu
Funkcje Ruchu Ustawczego
Dotyczy obróbki: toczenie, frezowanie
G0 Programowanie ruchu ustawczego (ruch szybki) po prostej linii, funkcja modalna;
Funkcja ruchu ustawczego (G0) służy do przemieszczania narzędzia po linii prostej do określonego punktu docelowego z maksymalną prędkością posuwu. Jest wykorzystywana głównie do pozycjonowania narzędzia. Programowanie tej funkcji może odbywać się we współrzędnych prostokątnych lub biegunowych, zarówno przy użyciu programowania absolutnego (G90), jak i przyrostowego (G91).
Programowanie obróbki gwintów
Dotyczy obróbki: toczenie
G33 Programowanie nacinania gwintu – synchronicznego (toczenie); funkcja modalna;
Programowanie obróbki gwintów umożliwia realizację gwintowania synchronicznego na tokarce z przetwornikiem kątowym na wrzecionie, gdzie istotne jest zachowanie odpowiedniego stosunku prędkości posuwu do obrotów wrzeciona.
Programowanie funkcji związanych z układami współrzędnych i ich transformacjami
Funkcje Ruchu we Współrzędnych Maszynowych
G53/G500
Dotyczy obróbki: toczenie, frezowanie
G53 i G500 Programowanie we współrzędnych maszynowych; funkcja niemodalna;
Funkcje ruchu G53, G500 oraz G54‑G599 pozwalają na programowanie przemieszczeń w układach współrzędnych maszynowych, umożliwiając wyłączenie aktualnego przesunięcia punktu zerowego i programowalnych przesunięć. Dzięki temu można dokonać precyzyjnych przemieszczeń względem punktu zerowego maszyny, co przydaje się na przykład przy bezpiecznej wymianie narzędzi.
Inne funkcje przygotowawcze
Funkcja Czasowego Postoju
Dotyczy obróbki: toczenie, frezowanie
G4 Programowanie postoju czasowego; funkcja niemodalna
Funkcja G4, którą należy programować w oddzielnym bloku, sprawia, że proces sterowania zatrzymuje się na dany czas.
Programowanie funkcji związanych z narzędziem i jego wymiarami
Podczas definiowania narzędzia w programie sterującym programista musi określić punkt charakterystyczny, względem którego będą mierzone jego wymiary. W przypadku narzędzi tokarskich często dostępne są dwa punkty charakterystyczne do wyboru:
punkt ostrza narzędzia P – jest to punkt przecięcia prostych stycznych do krzywizny ostrza noża i równoległych odpowiednio do osi X oraz Z,
punkt środka krzywizny ostrza narzędzia S — umieszczony jest w środku promienia zaokrąglenia naroża (przyjęcie tego punktu charakterystycznego jest zalecane).
Programowanie parametryczne
Układy CNC umożliwiają programowanie parametryczne, które pozwala na przypisywanie wartości R‑parametrów oraz wykonywanie skomplikowanych obliczeń, instrukcji warunkowych i skoków w programie. Ten rodzaj programowania jest przeznaczony do bardziej złożonych zadań technologicznych, dając programiście większą swobodę w kształtowaniu procesu obróbki.
Programowanie funkcji technologicznych
Dotyczy obróbki: toczenie, frezowanie
Programowanie prędkości obrotowej wrzeciona; funkcja modalna Prędkość obrotowa wrzeciona nie jest wymagana przy programowaniu przemieszczeń, ponieważ nie ma bezpośredniego wpływu na otrzymywany tor ruchu narzędzia. Funkcja prędkości obrotowej S to funkcja przedblokowa.
Dotyczy obróbki: toczenie, frezowanie
Programowanie prędkości posuwu; funkcja modalna
Adres F w programowaniu sterowania obrabiarek pełni podstawową funkcję, umożliwiając programowanie prędkości posuwu. Prędkość ta jest istotna przy programowaniu ruchu roboczego, a jej jednostki wyrażenia różnią się w zależności od rodzaju obrabiarki: mm/obr dla tokarek i mm/min dla tokarek oraz frezarek.
Programowanie funkcji pomocniczych
Dotyczy obróbki: toczenie, frezowanie
M0 Bezwarunkowe zatrzymanie programu
M1 Warunkowe zatrzymanie programu (wykonywana przy ustawionym w sterowniku warunku wykonania tej funkcji)
M2 Koniec programu
M3 Załączenie obrotów w kierunku zgodnym z ruchem wskazówek zegara (CW)
M4 Załączenie obrotów w kierunku przeciwnym do ruchu wskazówek zegara (CCW)
M5 Zatrzymanie obrotów wrzeciona
M6 Wymiana narzędzia — dla obrabiarek z magazynem narzędzi
M8 Załączenie chłodziwa
M9 Wyłączenie chłodziwa
M17 Koniec podprogramu
M19 Zorientowane zatrzymanie wrzeciona
M30 Koniec programu
Programowanie cykli obróbkowych
Cykle obróbkowe są zdefiniowanymi subprogramami wbudowanymi w pamięć sterownika, umożliwiającymi automatyzację programowania. Umożliwiają szybkie programowanie typowych operacji wiertarskich, frezarskich, tokarskich i szlifierskich w niektórych układach CNC. Programowanie cykli obróbkowych polega na wywołaniu odpowiedniej funkcji cyklu i określeniu parametrów obróbki. W niektórych układach CNC SINUMERIK możliwe jest także programowanie przy użyciu modułu programowania dialogowego. Wywołanie cyklu wymaga zastosowania określonej struktury bloku programu sterującego oraz deklaracji parametrów cyklu. Parametry mogą być wartościami zmiennymi lub stałymi, a wywołanie cyklu może być modalne lub niemodalne.
Skrócony opis podstawowych funkcji programowania układów CNC FANUC
% NAZWA : | Początek programu |
O0001 | Numer programu |
N... | |
N... | |
(KOMENTARZ) | Sekcja komentarza |
N... | |
N... | |
M30 | |
% | Koniec programu |
O0001 | Numer podprogramu |
N... | |
N... | |
N... | |
N... | |
M99 | Koniec podprogramu |
Wywołanie podprogramu:
N... M98 P...
gdzie
P – numer podprogramu
Deklaracja sposobu wymiarowania
G20 | Określanie podstawowych danych wymiarowych w calach |
G21 | Określanie podstawowych danych wymiarowych w milimetrach |
G17 | Płaszczyzna robocza X/Y |
G18 | Płaszczyzna robocza Z/X |
G19 | Płaszczyzna robocza Y/Z |
G90 | Programowanie absolutne |
G91 | Programowanie przyrostowe |
G94 | Programowanie prędkości posuwu w mm/min (cal/min); prędkość posuwu programowana jest słowem F |
G95 | Programowanie prędkości posuwu w mm/obr (cal/obr); prędkość posuwu programowana jest słowem F |
G96 | Włączenie stałej prędkości skrawania |
G97 | Odwołanie stałej prędkości skrawania |
G92 | Ograniczenie maksymalnej wartości prędkości obrotowej wrzeciona |
Programowanie podstawowych funkcji ruchu
Funkcja ruchu ustawczego
G00
Określanie podstawowych danych wymiarowych w calach
N... G00 X... Y... Z...
gdzie X, Y, Z – współrzędne końca ruchu
Funkcja ruchu roboczego
G01
Programowanie ruchu roboczego po linii prostej
N... G01 X... Y... Z... F...
gdzie
F – prędkość posuwuFunkcje łuku okręgu
G02
Programowanie ruchu po łuku okręgu w kierunku dodatnim (zgodnie z ruchem wskazówek zegara)
G03
Programowanie ruchu po łuku okręgu w kierunku ujemnym (przeciwnie do ruchu wskazówek zegara)
N... G17(G18, G19) G02(G03) X... Y... (Z...) I... J... (K...) F...
N... G17(G18, G19) G02(G03) X... Y... (Z...) R... F...
gdzie
I, J, K – parametry interpolacji
R – promień łuku okręguInterpolacja helikalna
G12
Programowanie ruchu po linii śrubowej w kierunku dodatnim (zgodnie z ruchem wskazówek zegara)
G13
Programowanie ruchu po linii śrubowej w kierunku ujemnym (przeciwnie do ruchu wskazówek zegara)
N... G17 G02 (G03) X... Y... I... J... alfa... F...
N... G17 G02 (G03) X... Y... R... alfa... F...
alfa – dowolna oś (np. Z), w której nie zastosowano interpolacji
Programowanie obróbki gwintów
Funkcja gwintowania synchronicznego
G33
Programowanie synchronicznego nacinania gwintu (toczenie), funkcja modalna
N... Z... (X... Y...) F...
gdzie
F – skok gwintuFunkcja gwintowania otworów
G63
Funkcja gwintowania otworów
Programowanie funkcji związanych z układami współrzędnych i ich transformacjami
Funkcje ruchu we współrzędnych maszynowych
G53
Programowanie we współrzędnych maszynowych
N... G53 X... Y... Z...
Funkcje zera programu
G54 ÷ G59
Programowanie podstawowych przesunięć punktu zerowego
N... G54(G55÷G59) X... Y... Z...
Funkcje programowych transformacji układu współrzędnych
G68
Obrót aktualnie obowiązującego układu współrzędnych przedmiotu obrabianego
G69
Anulowanie obrotu układu współrzędnych
N... G68 X... Y... (Z...) R...
gdzie
X, Y, Z – współrzędne środka obrotu
R – kąt obrotuG51.1
Odbicie lustrzane wykonane względem zaprogramowanej osi
G50.1
Anulowanie lustrzanego odbicia
N... G51.1 X... (Y..., Z...)
gdzie
X, Y, Z – współrzędna osi symetrii dla lustrzanego odbicia (określana dla osi układu współrzędnych prostopadłej do osi symetrii)G51
Skalowanie wymiarowania w odniesieniu do aktualnie obowiązującego układu współrzędnych przedmiotu obrabianego
G50
Anulowanie skalowania
N... G51 X... Y... Z... P...
N... G51 X... Y... Z... I... J... K...
gdzie
X, Y, Z – położenie punktu środkowego skalowania
P – współczynnik skalowania
I, J, K – współczynnik skalowania w poszczególnych osiach
Inne funkcje przygotowawcze
Funkcja czasowego postoju
G04
Programowanie czasowego postoju
N... G04 X...
N... G04 P...
gdzie
X, P – czas lub liczba obrotów wrzeciona przewidziane na postójFunkcje przestrzeni obróbki
G22
Ograniczenie obszaru roboczego
G23
Anulowanie ograniczenia obszaru roboczego
N... G22 X... Y... Z... I... J... K...
gdzie
X, Y, Z – współrzędne ograniczenia górnego
I, J, K – współrzędne ograniczenia dolnegoFunkcje sposobu zatrzymania
G9
Zatrzymanie dokładne
G60
Pozycjonowanie w jednym kierunku
G61
Zatrzymanie dokładne
G64
Programowanie płynnego przejścia między kolejnymi blokami – tryb obróbki skrawaniem
Programowanie funkcji związanych z narzędziem i jego wymiarami
Funkcja wyboru narzędzia
T
Programowanie wyboru określonego narzędzia obróbki
Funkcja korekcji promieniowej
G40
Kasowanie korekcji promieniowej wprowadzonej funkcjami G41 i G42
G41
Wprowadzanie korekcji promieniowej na lewo od konturu
G42
Wprowadzanie korekcji promieniowej na prawo od konturu
Programowanie funkcji technologicznych
Funkcja prędkości obrotowej wrzeciona
S
Programowanie prędkości obrotowej wrzeciona
Funkcja prędkości posuwu
F
Programowanie prędkości posuwu
Programowanie funkcji pomocniczych
M0
Bezwarunkowe zatrzymanie programu
M1
Warunkowe zatrzymanie programu
M2
Koniec programu
M3
Załączenie obrotów w kierunku zgodnym z ruchem wskazówek zegara (CW)
M4
Załączenie obrotów w kierunku przeciwnym do ruchu wskazówek zegara (CCW)
M5
Zatrzymanie wrzeciona
M6
Wymiana narzędzia
M8
Załączenie chłodziwa
M9
Wyłączenie chłodziwa
M30
Koniec programu
M98
Wywołanie podprogramu
M99
Koniec podprogramu
Cykle stałe
G73
Szybki cykl wiercenia głębokich otworów
N... G73 X... Y... R... Q... F... K...
G74
Cykl gwintowania lewostronnych otworów
N... G74 X... Y... Z... R... P... F... K...
G76
Cykl wiercenia dokładnego
N... G76 X... Y... R... Q... P... F... K...
G81
Cykl wiercenia/nawiercania
N... G81 X... Y... Z... R... F... K...
G82
Cykl wiercenia i pogłębiania walcowego
N... G82 X... Y... Z... R... P... F... K...
G83
Cykl wiercenia głębokich otworów
N... G83 X... Y... Z... R... Q... F... K...
G84
Cykl gwintowania otworów
N... G84 X... Y... Z... R... P... F... K...
G85
Cykl rozwiercania 1
N... G85 X... Y... Z... R... F... K...
G86
Cykl rozwiercania 2 z zatrzymaniem wrzeciona
N... G86 X... Y... Z... R... F... K...
G87
Cykl rozwiercania 3 narzędziem jednoostrzowym (kątowe zorientowanie wrzeciona z odsunięciem o wartość Q)
N... G87 X... Y... Z... R... Q... P... F... K...
G88
Cykl rozwiercania 4 (ręczne wycofanie narzędzia)
N... G88 X... Y... Z... R... P... F... K...
G89
Cykl rozwiercania 5 (jak G85 + przerwa na dnie otworu)
N... G89 X... Y... Z... R... P... F... K...
G80
Zakończenie cyklu stałego
Parametry przedstawionych cykli: X, Y – współrzędne położenia otworu na płaszczyźnie roboczej (dla aktywnej G17),
Z – odległość od płaszczyzny bezpiecznej do dna otworu,
R – odstęp od płaszczyzny wycofania do płaszczyzny bezpiecznej,
Q – cząstkowa głębokość skrawania (G73, G83) / wartość odsunięcia na dnie otworu (G76, G87),
P – czas postoju na dnie otworu,
F – prędkość posuwu,
K – liczba powtórzeń.
Skrócony opis podstawowych funkcji programowania układów CNC HEIDENHAIN
%NAZWA G71* | Początek programu, nazwa, określenie systemu miar |
N10 G30 G17 X+0 Y+0 Z‑30* | Określenie dolnego narożnika półfabrykatu oraz określenie płaszczyzny obróbki |
N20 G31 G90 X+90 Y+90 Z+0* | |
N... | Określenie górnego narożnika półfabrykatu |
N...* | |
* ;KOMENTARZ | Komentarz |
N...* | |
N...* | |
N9999999 %NAZWA G71* | Koniec programu |
Podprogramy
%NAZWA G71* | Początek programu |
N...* | |
N120 L1,0 | Wywołanie podprogramu, przeskok do bloku N300 |
N... | |
N300 G98 L1* | Początek podprogramu |
N... | Bloki wykonania podprogramu |
N380 G98 L0* | Koniec podprogramu – powrót do bloku wywołania N120 |
N... | |
N... | |
N9999999 %NAZWA G71* | Koniec podprogramu |
Wywołanie podprogramu:
N... G98 Ln,m
gdzie
n – numer podprogramu
m – liczba powtórzeń
Deklaracja sposobu wymiarowania
Funkcje systemu miar
G70
Określanie podstawowych danych wymiarowych w calach, określić na początku programu
G71
Określanie podstawowych danych wymiarowych w milimetrach, określić na początku programu
Określanie płaszczyzny roboczej
G17
Płaszczyzna robocza X/Y
G18
Płaszczyzna robocza Z/X
G19
Płaszczyzna robocza Y/Z
G20
Oś narzędzia IV
Funkcje wymiarowania współrzędnych
G90
Programowanie absolutne
G91
Programowanie przyrostowe
Programowanie podstawowych funkcji ruchu
Funkcje ruchu ustawczego
G00
Programowanie ruchu ustawczego (szybkiego) po linii prostej
N... G00 X... Y... Z... *
gdzie
X, Y, Z – współrzędne końca ruchuG10
Programowanie ruchu ustawczego (szybkiego) po linii prostej we współrzędnych biegunowych
N... I... J...
N... G10 R... H... *
gdzie
I, J – współrzędne określające biegun
R – promień biegunowy
H – kąt biegunowyFunkcje ruchu roboczego
G01
Programowanie ruchu roboczego po linii prostej
N... G01 X... Y... Z... F... *
gdzie
F – prędkość posuwuG11
Programowanie ruchu roboczego po linii prostej we współrzędnych biegunowych
N... I... J...
N... G11 R... H... F... *
Funkcje łuku okręgu
G02
Programowanie ruchu po łuku okręgu w kierunku dodatnim
G03
Programowanie ruchu po łuku okręgu w kierunku ujemnym
G05
Programowanie ruchu po łuku okręgu bez informacji o kierunku, przemieszczenie w ostatnio zaprogramowanym kierunku
N... I... J...
N... G02(G03, G05) X... Y... F... *
N... G02(G03, G05) R... F... *
Interpolacja helikalna
G12
Programowanie ruchu po linii śrubowej w kierunku dodatnim
G13
Programowanie ruchu po linii śrubowej w kierunku ujemnym
N... I... J... *
N... G12(G13) H... Z... *
gdzie
H – kąt obrotu określany jako liczba pełnych zwojów x 360 + kąt dobiegu/wybiegu
Z – współrzędne końca linii śrubowej w osi równoległej do płaszczyzny obrabiarkiWykonanie sfazowania
G24
Programowanie wykonania fazy pomiędzy dwoma elementami prostymi
N... G24 R... F... *
gdzie
R – długość fazy
F – prędkość posuwu aktywna tylko w danym blokuWykonanie zaokrąglenia
G25
Programowanie wykonania zaokrąglenia naroża konturu
N... G25 R... F... *
gdzie
R – promień zaokrąglenia
F – prędkość posuwu aktywna tylko w danym bloku
Programowanie funkcji związanych z układami współrzędnych i ich transformacjami
Funkcja przesunięcia punktu zerowego
G53
Przesunięcie punktu zerowego przy pomocy tabeli punktów zerowych
N... G53 P... *
gdzie
P – numer punktu zerowego z tabeli punktów zerowychG54
Przesunięcie punktu zerowego
N... G54 X... Y... Z... *
gdzie
X, Y, Z – współrzędne nowego punktu zerowego w układzie współrzędnych przedmiotu obrabianego, który jest określany poprzez wyznaczenie punktu odniesieniaFunkcje programowych transformacji układu współrzędnych
G73
Obrót aktualnie obowiązującego układu współrzędnych przedmiotu obrabianego
N... G73 G90(G91) H... *
gdzie
H – kąt obrotuG28
Odbicie lustrzane wykonane względem zaprogramowanej osi
N... G28 X Y *
gdzie
X, Y – osie lustrzanego odbiciaG72
Skalowanie wymiarowania
N... G72 F... *
gdzie
F – współczynnik skalowania
Inne funkcje przygotowawcze
Funkcja czasowego postoju
G04
Programowanie czasowego postoju
N... G04 F... *
gdzie
F – czas przewidziany na postój w sekundachFunkcje definicji półfabrykatu
G30
Ograniczenie dolne (minimalne współrzędne) obszaru półfabrykatu we współrzędnych absolutnych (G90)
G31
Ograniczenie górne (minimalne współrzędne) obszaru półfabrykatu we współrzędnych absolutnych (G91)
N... G30 G17 X... Y... Z... *
N... G31 G90 X... Y... Z... *
gdzie
X, Y, Z – współrzędne ograniczające obszar półfabrykatu
Funkcja definicji narzędzia
G99 | Wprowadzenie danych o narzędziu |
N... G99 T... L... R... ... *
gdzie
T – numer narzędzia
L – długość narzędzia
R – promień narzędzia
… - inne funkcje zależne od rodzaju narzędzia
Programowanie funkcji związanych z narzędziem i jego wymiarami
Funkcja wyboru narzędzia
T
Programowanie wyboru określonego narzędzia obróbki
Funkcja korekcji promieniowej
G40
Kasowanie korekcji promieniowej wprowadzonej funkcjami G41 i G42
G41
Wprowadzanie korekcji promieniowej na lewo od konturu
G42
Wprowadzanie korekcji promieniowej na prawo od konturu
Programowanie funkcji technologicznych
Funkcja prędkości obrotowej wrzeciona
S
Programowanie prędkości obrotowej wrzeciona
Funkcja prędkości posuwu
F
Programowanie prędkości posuwu
Programowanie funkcji pomocniczych
M0
Bezwarunkowe zatrzymanie programu
M1
Warunkowe zatrzymanie programu
M2
Koniec programu
M3
Załączenie obrotów w kierunku zgodnym z ruchem wskazówek zegara (CW)
M4
Załączenie obrotów w kierunku przeciwnym do ruchu wskazówek zegara (CCW)
M5
Zatrzymanie wrzeciona
M6
Wymiana narzędzia
M8
Załączenie chłodziwa
M9
Wyłączenie chłodziwa
M13
Działanie jak M3+M8
M14
Działanie jak M4+M8
M30
Koniec programu
M89
Stała prędkość posuwu na narożach
M90
Programowanie we współrzędnych maszynowych
M109
Stała prędkość skrawania
M134
Zatrzymanie dokładne
M135
Anulowanie M134
M136
Posuw w mm/obr
Cykle dla wiercenia i gwintowania
G240
Nawiercanie
G200
Wiercenie
G201
Rozwiercanie
G202
Wytaczanie
G203
Wiercenie uniwersalne
G204
Pogłębianie wsteczne
G205
Wiercenie uniwersalne 2
G206
Gwintowanie z oprawką kompensacyjną
G207
Gwintowanie bez oprawki kompensacyjnej
G208
Frezowanie gwintów
G209
Gwintowanie z łamaniem wióra
G262 G267
Frezowanie gwintów
Cykle dla frezowania kieszeni, stempli i rowków wpustowych
G210
Frezowanie rowków z wahadłowym zagłębianiem
G211
Frezowanie rowków rozmieszczonych na okręgu z wahadłowym zagłębianiem
G212
Obróbka wykończeniowa kieszeni prostokątnej
G213
Obróbka wykończeniowa stempla prostokątnego
G214
Obróbka wykończeniowa kieszeni okrągłej
G215
Obróbka wykończeniowa stempla okrągłego
G251
Kieszeń prostokątna
G252
Kieszeń okrągła
G253
Frezowanie rowka wpustowego
G254
Frezowanie rowka rozmieszczonego na okręgu
Cykle dla wytwarzania wzorów
G220
Wzory punktowe na okręgu
G221
Wzory punktowe na liniach
Skrócony opis podstawowych funkcji programowania układów CNC PRONUM
%MPF920 | Początek programu |
N... | |
N... | |
(KOMENTARZ) | Komentarz |
N... | |
N... | |
M30 | Koniec programu |
Podprogramy
%SPF101 | Początek programu |
N... | |
N... | |
N... | |
N... | |
M17 | Koniec podprogramu |
Wywołanie podprogramu:
N... L... P...
gdzie
L – numer podprogramu
P – liczba powtórzeń
aaaaaaaaaa
Deklaracja sposobu wymiarowania
Funkcje systemu miar
G70
Określanie podstawowych danych wymiarowych w calach
G71
Określanie podstawowych danych wymiarowych w milimetrach
Określanie płaszczyzny roboczej
G17
Płaszczyzna robocza X/Y
G18
Płaszczyzna robocza Z/X
G19
Płaszczyzna robocza Y/Z
Funkcje wymiarowania współrzędnych
G90
Programowanie absolutne
G91
Programowanie przyrostowe
Funkcje wymiarowania współrzędnych
G94
Programowanie prędkości posuwu w mm/min (cal/min); prędkość posuwu programowana jest słowem F
G95
Programowanie prędkości posuwu w mm/obr (cal/obr); prędkość posuwu programowana jest słowem F
Funkcje prędkości skrawania
G96
Włączenie stałej prędkości skrawania
G97
Odwołanie stałej prędkości skrawania
G92
Ograniczenie maksymalnej wartości prędkości obrotowej wrzeciona
Programowanie podstawowych funkcji ruchu
Funkcja ruchu ustawczego
G0
Programowanie ruchu ustawczego (szybkiego) po linii prostej
N... G0 X... Y... Z... *
gdzie
X, Y, Z – współrzędne końca ruchuFunkcje ruchu roboczego
G1
Programowanie ruchu roboczego po linii prostej
N... G1 X... Y... Z... F...
gdzie
F – prędkość posuwuFunkcje łuku okręgu
G2
Programowanie ruchu po łuku okręgu w kierunku dodatnim
G3
Programowanie ruchu po łuku okręgu w kierunku ujemnym
N... G17(G18, G019) G2(G3) X... Y... (Z...) I... J... (K...) F...
N... G17(G18, G019) G2(G3) X... Y... (Z...) U... F...
gdzie
X, Y, Z – współrzędne końca ruchu
I, J, K – parametry interpolacji
U – promień łuku okręguInterpolacja helikalna
G2
Programowanie ruchu po linii śrubowej w kierunku dodatnim
G3
Programowanie ruchu po linii śrubowej w kierunku ujemnym
N... G17 G2 (G3) X... Y... Z... I... J... F...
Programowanie obróbki gwintów
Funkcja gwintowania synchronicznego
G33
Programowanie synchronicznego nacinania gwintu (toczenie)
N... Z... (x... Y...) K... (I... J...)
gdzie
I, J, K – skok gwintuFunkcja gwintowania otworów
G63
Funkcja gwintowania niesynchronicznego otworów
Programowanie funkcji związanych z układami współrzędnych i ich transformacjami
Funkcje ruchu we współrzędnych maszynowych
G53
Programowanie ruchu we współrzędnych maszynowych
N... G53 X... Y... Z...
N... G53 D... X0 Y0 Z0
gdzie
D – rejestr zawierający współrzędne końca ruchu (D400÷D409)Funkcje zera programu
G54
Przesunięcie punktu zerowego przedmiotu obrabianego o wektor przesunięcia określony w odpowiednim rejestrze
N... G54 D... X... Y... Z...
G55
Korekcja przesunięcia punktu zerowego przedmiotu obrabianego
N... G55 D... X... Y... Z...
Funkcje programowych transformacji układu współrzędnych
G74
Programowanie lustrzanego odbicia w kierunku osi X
G75
Odwołanie lustrzanego odbicia w kierunku osi X
G76
Programowanie lustrzanego odbicia w kierunku osi Y
G77
Odwołanie lustrzanego odbicia w kierunku osi Y
G78
Programowanie lustrzanego odbicia w kierunku osi Z
G79
Odwołanie lustrzanego odbicia w kierunku osi Z
Inne funkcje przygotowawcze
Funkcja czasowego postoju
G4
Programowanie czasowego postoju
N... G4 F... *
gdzie
F – czas przewidziany na postój w sekundachFunkcje przestrzeni obróbki
G25
Ograniczenie dolne obszaru roboczego
G26
Ograniczenie górne obszaru roboczego
G27
Anulowanie ograniczenia obszaru roboczego
N... G25(G26) X... (Y...) Z...
N...
N... G27
gdzie
X, Y, Z – współrzędne ograniczające obszar
Funkcja sposobu zatrzymania
G9 | Ruch z wyhamowaniem na końcu odcinka linii prostej |
G60 | Wywołanie dojazdu jednokierunkowego |
G61 | Zatrzymanie dokładne |
G64 | Programowanie płynnego przejścia między kolejnymi blokami – tryb obróbki skrawaniem |
Programowanie funkcji związanych z narzędziem i jego wymiarami
Funkcja wyboru narzędzia
T
Programowanie wyboru określonego narzędzia obróbki
N... T... D...
T – po adresie T określany jest numer narzędzia w głowicy narzędziowej lub magazynie narzędzi D – numer rejestru narzędziowego, w którym umieszczone są dane dotyczące narzędzia
Funkcja korekcji promieniowej
G40
Kasowanie korekcji promieniowej wprowadzonej funkcjami G41 i G42
G41
Wprowadzanie korekcji promieniowej na lewo od konturu
G42
Wprowadzanie korekcji promieniowej na prawo od konturu
Programowanie funkcji technologicznych
Funkcja prędkości obrotowej wrzeciona
S
Programowanie prędkości obrotowej wrzeciona
Funkcja prędkości posuwu
F
Programowanie prędkości posuwu
Programowanie funkcji pomocniczych
M0 | Bezwarunkowe zatrzymanie programu |
M1 | Warunkowe zatrzymanie programu |
M2 | Koniec programu |
M3 | Załączenie obrotów w kierunku zgodnym z ruchem wskazówek zegara (CW) |
M4 | Załączenie obrotów w kierunku przeciwnym do ruchu wskazówek zegara (CCW) |
M5 | Zatrzymanie wrzeciona |
M6 | Wymiana narzędzia |
M8 | Załączenie chłodziwa |
M9 | Wyłączenie chłodziwa |
M13 | Działanie jak M3+M8 |
M14 | Działanie jak M4+M8 |
M17 | Koniec podprogramu |
M19 | Zorientowane zatrzymanie wrzeciona |
M30 | Koniec programu |
Cykle stałe dla toczenia
L95
Cykl toczenia warstwowego
Parametry cyklu
R20 — numer podprogramu opisującego kontur przedmiotu obrabianego,
R29=34 — obróbka zgrubna wzdłuż osi X wewnątrz konturu; po niej następuje jedno przejście wzdłuż konturu z zaprogramowanym naddatkiem,
R29=41 — jak 31+ jedno przejście wzdłuż konturu bez pozostawienia naddatku,
R29=42 — jak 32+ jedno przejście wzdłuż konturu bez pozostawienia naddatku,
R29=43 — jak 33+ jedno przejście wzdłuż konturu bez pozostawienia naddatku,
R29=44 — jak 34+ jedno przejście wzdłuż konturu bez pozostawienia naddatku.L97
Cykl gwintowania
Parametry cyklu
R20 — skok gwintu,
R21 — współrzędna X początku gwintu,
R22 — współrzędna Z początku gwintu,
R24 — głębokość gwintowania (dla gwintów zewnętrznych R24<0; dla gwintów wewnętrznych R24>0),
R25 — naddatek na obróbkę wykończeniową,
R26 — długość dobiegu,
R27 — długość wybiegu,
R28 — liczba nacięć zgrubnych,
R29 — kąt dosuwu w stopniach (dla gwintów wzdłużnych i płaskich) — w przypadku nacinania gwintu metodą wcinania po stycznej; w przypadku gwintów na stożku należy zadeklarować R29=0,
R31 — współrzędna X końca gwintu,
R32 — współrzędna Z końca gwintu.L98
Cykl wiercenia głębokich otworów
Parametry cyklu
R22 — współrzędna absolutna punktu odniesienia,
R24 — przyrost głębokości wiercenia,
R25 — pierwsza głębokość wiercenia,
R26 — końcowa głębokość wiercenia,
R27 — czas postoju przed otworem (po kolejnym wycofaniu),
R28 — czas postoju na dnie otworu.
Cykle stałe dla frezowania
Parametry cykli dla frezowania
R0 — czas postoju nad otworem przed rozpoczęciem posuwu roboczego,
R1 — pierwsza głębokość wiercenia,
R2 — współrzędna absolutna płaszczyzny odniesienia (płaszczyzny, na poziomie której pozycjonowane jest narzędzie),
R3 — głębokość wiercenia, gwintowania lub wytaczania,
R4 — czas postoju na dnie otworu,
R5 — zmniejszenie przyrostu głębokości wiercenia,
R7 — kierunek obrotów wrzeciona (R7=3 dla M3; R7=4 dla M9),
R10 — współrzędna absolutna płaszczyzny wycofania (płaszczyzny, do poziomu której następuje wycofanie narzędzia po wykonaniu operacji określonej przez cykl),
R11 — wybór płaszczyzny.
Deklaracja R11 | Płaszczyzna obróbki | Oś wrzeciona |
---|---|---|
R11=0 | X Y | Z |
R11=1 | Y Z | X |
R11=2 | Z X | Y |
G81 (L81)
Cykl wiercenia
Parametry cyklu
R2, R3, R11
G82 (L82)
Cykl pogłębiania
Parametry cyklu
R2, R3, R4, R10, R11
G83 (L83)
Cykl wiercenia głębokich otworów
Parametry cyklu
R0, R1, R2, R3, R4, R5, R10, R11
G85 (L85)
Cykl wytaczania (wersja 1)
Parametry cyklu
R2, R3, R10, R11
G86 (L86)
Cykl wytaczania (wersja 2)
Parametry cyklu
R2, R3, R4, R7, R10, R11
G87 (L87)
Cykl wytaczania (wersja 3)
Parametry cyklu
R2, R3, R7, R11
G88 (L88)
Cykl wytaczania (wersja 4)
Parametry cyklu
R2, R3, R4, R7, R11
G89 (L89)
Cykl wytaczania (wersja 5)
Parametry cyklu
R2, R3, R4, R11
Powrót do spisu treściPowrót do spisu treści
Cykle obróbki
Cykle obróbki wiertarskiej
CYCLE81 - wiercenie, nawiercanie
Blok programu sterującego
CYCLE81 (RTP, RFP, SDIS, DP, DPR)
Parametry
RTP — płaszczyzna wycofania (we współrzędnych absolutnych)
RFP — płaszczyzna odniesienia (we współrzędnych absolutnych)
SDIS — odsunięcie płaszczyzny bezpiecznej (wartość przyrostowa bez znaku)
DP — głębokość wiercenia (we współrzędnych absolutnych)
DPR — głębokość wiercenia w stosunku do płaszczyzny odniesienia (wartość przyrostowa bez znaku)
Cykl wiertarski CYCLE81 umożliwia wiercenie z zaprogramowaną prędkością obrotową wrzeciona i prędkością posuwu do określonej głębokości wiercenia. Jest to najprostszy spośród cykli wiertarskich stosowany do wiercenia otworów o małej głębokości oraz nawiercania.
CYCLE82 – wiercenie, pogłębianie
Blok programu sterującego
CYCLE82 (RTP, RFP, SDIS, DP, DPR, DTB)
Parametry
RTP — płaszczyzna wycofania (we współrzędnych absolutnych),
RFP — płaszczyzna odniesienia (we współrzędnych absolutnych),
SIDIS — odsunięcie płaszczymy bezpiecznej (wartość przyrostowa bez znaku),
DP — głębokość wiercenia (we współrzędnych absolutnych),
DPR — głębokość wiercenia w stosunku do płaszczyzny odniesienia (wartość przyrostowa bez znaku), DTB — czas postoju na głębokości wiercenia.
Działanie cyklu CYCLE82 zbliżone jest do CYCLE81, z tym że na głębokości wiercenia możliwe jest zaprogramowanie czasu postoju na złamanie wióra. Cykl ten może być wykorzystywany do operacji wiercenia lub pogłębiania.
CYCLE83 - wiercenie głębokich otworów
Blok programu sterującego
CYCLE83 (RTP, RFP, SDIS, DP, DPR, FDEP, FDPR, DAM, DTB, DTS, FRF, VARI, _AXN, _MDEP, _VRT, _DTD, _DIS1)
Parametry
RTP — płaszczyzna wycofania (we współrzędnych absolutnych),
RFP — płaszczyzna odniesienia (we współrzędnych absolutnych),
SDIS — odsunięcie płaszczyzny bezpiecznej (wartość przyrostowa bez znaku),
DP — głębokość wiercenia (we współrzędnych absolutnych),
DPR — głębokość wiercenia w stosunku do płaszczyzny odniesienia (wartość przyrostowa bez znaku),
FDEP — pierwsza głębokość wiercenia (we współrzędnych absolutnych),
FDPR — pierwsza głębokość wiercenia w stosunku do płaszczyzny odniesienia (wartość przyrostowa bez znaku),
DAM — degresja głębokości wiercenia (wartość przyrostowa bez znaku),
DTB — czas postoju na głębokości wiercenia (łamanie wiórów); wartości: > 0 (w sekundach), < 0 (w obrotach),
DTS — czas postoju na poziomie początkowym dla usunięcia wiórów; wartości: > 0 (w sekundach), < 0 (w obrotach),
FRF — współczynnik posuwu dla pierwszej głębokości wiercenia (zakres: 0.001÷1),
VARI — rodzaj obróbki; wartości: 0 (łamanie wiórów), 1 (usuwanie wiórów),
_AXN — oś narzędzia: 1, 2 lub 3 oś geometrii (lub zadana w programie funkcjami G17/G18/G19),
_MDEP — minimalna głębokość wiercenia,
_VRT — zmienna wielkość wycofania (dla VARIA); wartości: > 0 (jest wielkością wycofania), 0 (nastawiona 1 mm),
_DTD — czas oczekiwania na końcowej głębokości wiercenia, wartości: > 0 (w sekundach), < 0 (w obrotach), = 0 (wartość jak DTB),
_DIS1 — odstęp od materiału przy ponownym zagłębieniu do otworu (przy usuwaniu wiórów VARI=1); wartości: > 0 (zaprogramowana wartość), = 0 (obliczany automatycznie).
Cykl CYCLE83 przeznaczony jest do wiercenia głębokich otworów, przy czym otwór taki jest wykonywany przez wielokrotny dosuw na częściową głębokość wiercenia. Po osiągnięciu każdej częściowej głębokości wiercenia wiertło może zostać cofnięte do płaszczyzny odniesienia w celu usunięcia wiórów lub, po zatrzymaniu na częściowej głębokości wiercenia w celu złamania wiórów, może zostać cofnięte o zaprogramowaną drogę wycofania.
CYCLE84 – gwintowanie otworu bez oprawki kompensacyjnej
Blok programu sterującego
CYCLE84 (RTP, RFP, SDIS, DP, DPR, DTB, SDAC, MPIT, PIT, POSS, SST, SST1, _AXN, _PTAB, _TECHNO, _VARI, _DAM, _VRT)
Parametry
RTP — płaszczyzna wycofania (we współrzędnych absolutnych),
RFP — płaszczyzna odniesienia (we współrzędnych absolutnych),
SDIS — odsunięcie płaszczyzny bezpiecznej (wartość przyrostowa bez znaku),
DP — głębokość gwintowania (we współrzędnych absolutnych),
DPR — głębokość gwintowania w stosunku do płaszczyzny odniesienia (wartość przyrostowa bez znaku),
DTB — czas oczekiwania na głębokości gwintowania,
SDAC — kierunek obrotów po zakończeniu cyklu, wartości: 3 (dla M3), 4 (dla M4) albo 5 (dla M51),
MPIT — skok gwintu jako wielkość gwintu (ze znakiem liczby), zakres wartości: 3 (dla gwintu M3) ÷ 48 (dla gwintu M48), znak liczby określa rodzaj gwintu: + gwint prawy, - gwint lewy,
PIT — skok gwintu jako wartość (ze znakiem liczby), zakres wartości: 0.001÷2000.000 mm, znak liczby określa rodzaj gwintu: + gwint prawy, - gwint lewy,
POSS — pozycja wrzeciona dla zorientowanego zatrzymania (w stopniach),
SST — prędkość obrotowa dla gwintowania otworu,
SST1 — prędkość obrotowa dla wycofania,
_AXN — oś narzędzia: 1, 2 lub 3 oś geometrii (lub zadana w programie funkcjami G17/G18/G19),
Za pomocą cyklu CYCLE84 można gwintować otwory bez oprawki kompensacyjnej. Cykl ten można stosować, gdy wrzeciono ma możliwość kątowego pozycjonowania. Działanie cyklu wynika z dokładnego sprzężenia ruchu obrotowego i posuwowego narzędzia (funkcje G331 i G332).
CYCLE840 – gwintowanie otworu z użyciem oprawki kompensacyjnej
Blok programu sterującego
CYCLE840 (RTP, RFP, SDIS, DP, DPR, DTB, SDR, SDAC, ENC, MPIT, PIT- AXN, _PTAB)
Parametry
RTP — płaszczyzna wycofania (we współrzędnych absolutnych),
RFP — płaszczyzna odniesienia (we współrzędnych absolutnych),
SDIS — odsunięcie płaszczyzny bezpiecznej (wartość przyrostowa bez znaku),
DP — głębokość gwintowania (we współrzędnych absolutnych),
DPR — głębokość gwintowania w stosunku do płaszczyzny odniesienia (wartość przyrostowa bez znaku),
DTB — czas oczekiwania na głębokości gwintowania,
SDR — kierunek obrotów dla wycofania, wartości: 0 (automatyczne odwrócenie obrotów), 3 (dla M3), 4 (dla M4),
SDAC — kierunek obrotów po zakończeniu cyklu, wartości: 3 (dla M3), 4 (dla M4), 5 (dla M5),
ENC — gwintowanie otworu z przetwornikiem kątowym (sprzężenie ruchu posuwowego i ruchu obrotowego wrzeciona) / bez przetwornika, wartości: 0 (z przetwornikiem, bez czasu oczekiwania), 1 (bez przetwornika, posuw zaprogramować przed cyklem),
MPIT — skok gwintu jako wielkość gwintu (ze znakiem liczby), zakres wartości: 3 (dla gwintu M3) ÷ 48 (dla gwintu M48),
PIT — skok gwintu jako wartość (ze znakiem liczby), zakres wartości: 0.001÷2000.000 mm,
_AXN — oś narzędzia: 1, 2 lub 3 oś geometrii (lub zadana w programie funkcjami G17/G18/G19),
_PTAB — system miar dla skoku gwintu PIT, wartości: 0 (zgodnie z zaprogramowanym systemem miar calowy/metryczny), 1 (skok w mm), 2 (skok w zwojach gwintu na cal), 3 (skok w calach/obrót).
Przy pomocy cyklu CYCLE840 można wykonywać gwintowanie otworów z użyciem oprawki kompensacyjnej. Gwintowanie takie może odbywać się z przetwornikiem kątowym (funkcja G33) zapewniającym sprzężenie ruchu posuwowego narzędzia z jego ruchem obrotowym lub bez takiego przetwornika (funkcja G1 ÷ G63).
CYCLE85 – rozwiercanie 1
Blok programu sterującego
CYCLE85 (RTP, RFP, SDIS, DP, DPR, DTB, FFR, RFF)
Parametry
RTP — płaszczyzna wycofania (we współrzędnych absolutnych),
RFP — płaszczyzna odniesienia (we współrzędnych absolutnych),
SDIS — odsunięcie płaszczyzny bezpiecznej (wartość przyrostowa bez znaku),
DP — głębokość rozwiercania (we współrzędnych absolutnych),
DPR — głębokość rozwiercania w stosunku do płaszczyzny odniesienia (wartość przyrostowa bez znaku),
DTB — czas oczekiwania na głębokości rozwiercania,
FFR — posuw,
RFF — posuw wycofania.
Cykl wiertarski CYCLE85 może być stosowany do rozwiercania otworów. Wykonanie tego cyklu polega na osiowym przemieszczeniu narzędzia z zadaną prędkością obrotową aż do końcowej głębokości rozwiercania. Prędkość posuwu zagłębiania i wycofania narzędzia może być programowana niezależnie.
CYCLE86 — rozwiercanie 2
Blok programu sterującego CYCLE86 (RTP, RFP, SDIS, DP, DPR, DTB, SDIR, RPA, RPO, RPAP, POSS)
Parametry
RTP — płaszczyzna wycofania (we współrzędnych absolutnych),
RFP — płaszczyzna odniesienia (we współrzędnych absolutnych),
SDIS — odsunięcie płaszczymy bezpiecznej (wartość przyrostowa bez maku),
DP — głębokość rozwiercania (we współrzędnych absolutnych),
DPR — głębokość rozwiercania w stosunku do płaszczyzny odniesienia (wartość przyrostowa bez maku),
DTB — czas oczekiwania na głębokości,
SDIR — kierunek obrotów, wartości: 3 (dla M3), 4 (dla M4),
RPA — droga wycofania w odciętej płaszczyzny roboczej (wartość przyrostowa),
RPO — droga wycofania w rzędnej płaszczymy roboczej (wartość przyrostowa),
RPAP — droga wycofania (wartość przyrostowa),
POSS — pozycja wrzeciona dla zorientowanego zatrzymania (w stopniach).
Cykl CYCLE86 wykorzystuje się do obróbki otworów narzędziami niesymetrycznymi (wytaczaki jednoostrzowe). Po osiągnięciu głębokości otworu następuje zorientowane zatrzymanie wrzeciona, a następnie ruch szybki kolejno do pozycji wycofania oraz płaszczyzny wycofania.
CYCLE87 – rozwiercanie 3
BIok programu sterującego
CYCLE87 (RTP, RFP, SDIS, DP, DPR, SDIR)
Parametry
RTP — płaszczyzna wycofania (we współrzędnych absolutnych),
RFP — płaszczyzna odniesienia (we współrzędnych absolutnych),
SDIS — odsunięcie płaszczyzny bezpiecznej (wartość przyrostowa bez znaku),
DP — głębokość rozwiercania (we współrzędnych absolutnych),
DPR — głębokość rozwiercania w stosunku do płaszczyzny odniesienia (wartość przyrostowa bez znaku),
SDIR — kierunek obrotów, wartości: 3 (dla M3), 4 (dla M4).
Wykonanie cyklu CYCLE87 wymaga obecności operatora, gdyż po osiągnięciu przez narzędzie końcowej głębokości rozwiercania następuje zatrzymanie wrzeciona bez kątowego zorientowania (funkcja M5) oraz zatrzymanie wykonania programu (funkcja M0). Dopiero po naciśnięciu przez operatora przycisku NC‑START następuje przemieszczenie narzędzia ruchem szybkim do płaszczyzny wycofania.
CYCLE88 — rozwiercanie 4
Blok programu sterującego
CYCLE88 (RTP, RFP, SDIS, DP, DPR, DTB, SDIR)
Parametry
RTP — płaszczyzna wycofania (we współrzędnych absolutnych),
RFP — płaszczyzna odniesienia (we współrzędnych absolutnych),
SDIS — odsunięcie płaszczyzny bezpiecznej (wartość przyrostowa bez znaku),
DP — głębokość rozwiercania (we współrzędnych absolutnych),
DPR — głębokość rozwiercania w stosunku do płaszczyzny odniesienia (wartość przyrostowa bez znaku),
DTB — czas oczekiwania na głębokości,
SDIR — kierunek obrotów, wartości: 3 (dla M3), 4 (dla M4).
Różnica pomiędzy działaniem cyklu CYCLE88 a CYCLE87 polega na możliwości zaprogramowania postoju czasowego na głębokości rozwiercania oraz opcjonalnym zatrzymaniu wykonania programu (funkcja M0).
CYCLE89 — rozwiercanie 5
Blok programu sterującego
CYCLE89 (RTP, RFP, SDIS, DP, DPR, DTB)
Parametry
RTP — płaszczyzna wycofania (we współrzędnych absolutnych),
RFP — płaszczyzna odniesienia (we współrzędnych absolutnych),
SDIS — odsunięcie płaszczyzny bezpiecznej (wartość przyrostowa bez znaku),
DP — głębokość rozwiercania (we współrzędnych absolutnych),
DPR— głębokość rozwiercania w stosunku do płaszczyzny odniesienia (wartość przyrostowa bez znaku),
DTB — czas oczekiwania na głębokości.
Cykl CYCLE89 stosuje się do rozwiercania otworów. Działanie tego cyklu polega na osiowym przemieszczaniu narzędzia z zadaną prędkością wrzeciona i posuwu aż do osiągnięcia końcowej głębokości rozwiercania. Gdy głębokość ta zostanie osiągnięta, można zaprogramować określony czas postoju.
HOLES1 — wiercenie otworów rozmieszczonych wzdłuż linii prostej
Blok programu sterującego
HOLESI (SPCA, SPCO, STAI, FDIS, DBH, NUM)
Parametry
SPCA — odcięta punktu odniesienia (we współrzędnych absolutnych),
SPCO — rzędna punktu odniesienia (we współrzędnych absolutnych),
STA1 — kąt względem osi poziomej, wartości: -180<STA1≤180 stopni,
FDIS — odległość pierwszego otworu od punktu odniesienia (wartość przyrostowa bez znaku),
DBH — odległość między otworami (wartość przyrostowa bez znaku),
NUM — liczba otworów.
Przy pomocy cyklu HOLES1 można wykonywać szereg otworów rozmieszczonych wzdłuż linii prostej. Cykl ten wymaga uprzedniego modalnego wywołania jednego z przedstawionych cykli wiertarskich (CYCLE81÷CYCLE89).
HOLES2 — wiercenie otworów rozmieszczonych na okręgu
Blok programu sterującego
HOLES2 (CPA, CPO, RAD, STAI, INDA, NUM)
Parametry
CPA — odcięta punktu środkowego okręgu, na którym rozmieszczone są otwory (we współrzędnych absolutnych),
CPO — rzędna punktu środkowego okręgu, na którym rozmieszczone są otwory (we współrzędnych absolutnych),
RAD — promień okręgu, na którym rozmieszczone są otwory (wartość przyrostowa bez znaku),
STAI — kąt początkowy, wartości: -180<STA1≤180 stopni,
INDA — kąt rozmieszczenia otworów,
NUM — liczba otworów.
Cykl HOLES2 umożliwia wykonanie grupy otworów rozmieszczonych na okręgu. Cykl ten, podobnie jak HOLES1, wymaga uprzedniego modalnego wywołania jednego z przedstawionych cykli wiertarskich (CYCLE81÷CYCLE89).
Cykle obróbki frezarskiej
LONGHOLE — frezowanie otworów podłużnych rozmieszczonych na okręgu
Blok programu sterującego
LONGHOLE (RTP, RFP, SDIS, DP, DPR, NUM, LENG, CPA, CPO, RAD, STA1, INDA, FFD, FFP1, MID)
Parametry
RTP — płaszczyzna wycofania (we współrzędnych absolutnych),
RFP — płaszczyzna odniesienia (we współrzędnych absolutnych),
SDIS — odsunięcie płaszczyzny bezpiecznej (wartość przyrostowa bez znaku),
DP — głębokość otworu podłużnego (we współrzędnych absolutnych),
DPR — głębokość otworu podłużnego w stosunku do płaszczyzny odniesienia (wartość przyrostowa bez znaku),
NUM — liczba otworów podłużnych,
LENG — długość otworu podłużnego (wartość przyrostowa bez znaku),
CPA — odcięta punktu środkowego okręgu, na którym rozmieszczone są otwory (we współrzędnych absolutnych),
CPO — rzędna punktu środkowego okręgu, na którym rozmieszczone są otwory (we współrzędnych absolutnych),
RAD — promień okręgu, na którym rozmieszczone są otwory (wartość przyrostowa bez znaku),
STA1 — kąt początkowy,
INDA — kąt rozmieszczenia otworów,
FFD — posuw dla dosuwu wgłębnego,
FFP1 — posuw dla obróbki powierzchni,
MID — maksymalna głębokość pojedynczego dosuwu (wartość przy‑rostowa bez znaku).
Przy pomocy cyklu LONGHOLE można obrabiać otwory podłużne rozmieszczone na okręgu, przy czym osie podłużne tych otworów są ustawione promieniowo. Szerokość takiego otworu podłużnego określana jest przez średnicę narzędzia.
SLOT1— frezowanie rowków podłużnych rozmieszczonych na okręgu
Blok programu sterującego
SLOT1 (RTP, RFP, SDIS, DP, DPR, NUM, LENG, WID, CPA, CPO, RAD, STA1, INDA, FFD, FFP1, MID, CDIR, FAL, VARI, MIDF, FFP2, SSF, _FALD, STA2)
Parametry
RTP — płaszczyzna wycofania (we współrzędnych absolutnych),
RFP — płaszczyzna odniesienia (we współrzędnych absolutnych),
SDIS — odsunięcie płaszczyzny bezpiecznej (wartość przyrostowa bez znaku),
DP — głębokość rowka (we współrzędnych absolutnych),
DPR — głębokość rowka w stosunku do płaszczyzny odniesienia (wartość przyrostowa bez znaku),
NUM — liczba rowków,
LENG — długość rowka (wartość przyrostowa bez znaku),
WID — szerokość rowka (wartość przyrostowa bez znaku),
CPA — odcięta punktu środkowego okręgu, na którym rozmieszczone są rowki (we współrzędnych absolutnych),
CPO — rzędna punktu środkowego okręgu, na którym rozmieszczone są rowki (we współrzędnych absolutnych), RAD — promień okręgu, na którym rozmieszczone są rowki (wartość przyrostowa bez znaku),
STA1 — kąt początkowy,
INDA — kąt rozmieszczenia rowków,
FFD — posuw dla dosuwu wgłębnego,
FFP1 — posuw dla obróbki powierzchni,
MID — maksymalna głębokość pojedynczego dosuwu (wartość I przyrostowa bez znaku),
CDIR — kierunek frezowania dla obróbki rowka, wartości: 0 (frezowanie współbieżne), 1 (frezowanie przeciwbieżne), 2 (G2), 3 (G3),
FAL — naddatek na obrzeżu rowka (wartość przyrostowa bez znaku),
VARI — rodzaj obróbki (wartość przyrostowa bez znaku), wartości (miejsce jednostek): 0 (obróbka kompletna), 1 (obróbka zgrubna), 2 (obróbka wykończeniowa), wartości (miejsce dziesiątek): 0x (prostopadle z G0), 1x (prostopadle z G1), 3x (ruch wahliwy G1),
MIDF — maksymalna głębokość dosuwu dla obróbki wykończeniowej,
FFP2 — posuw dla obróbki wykończeniowej,
SSF — prędkość obrotowa dla obróbki wykończeniowej,
_FALD — naddatek na dnie rowka,
_STA2 — maksymalny kąt zagłębiania się narzędzia.
Cykl SLOT1 umożliwia frezowanie rowków podłużnych rozmieszczonych na okręgu. Osie podłużne tych rowków ustawione są promieniowo. W odróżnieniu od cyklu LONGHOLE, dla cyklu SLOT1 można określić szerokość rowka niezależnie od średnicy freza.
SLOT2 — frezowanie rowków kołowych
Blok programu sterującego
SLOT2 (RTP, RFP, SDIS, DP, DPR, NUM, AFSL, WID, CPA, CPO, RAD, STA1, INDA, FFD, FFP1, CDIR, FAL, VARI, MIDF, FFP2, SSF)
Parametry
RTP — płaszczyzna wycofania (we współrzędnych absolutnych),
RFP — płaszczyzna odniesienia (we współrzędnych absolutnych),
SDIS — odsunięcie płaszczyzny bezpiecznej (wartość przyrostowa bez znaku),
DP — głębokość rowka (we współrzędnych absolutnych),
DPR — głębokość rowka w stosunku do płaszczyzny odniesienia (wartość przyrostowa bez znaku),
NUM — liczba rowków,
AFSL — kąt wyznaczający długość rowka (wartość przyrostowa bez znaku),
WID — szerokość rowka kołowego (wartość przyrostowa bez znaku),
CPA — odcięta punktu środkowego okręgu, na którym rozmieszczone są rowki (we współrzędnych absolutnych),
CPO — rzędna punktu środkowego okręgu, na którym rozmieszczone są rowki (we współrzędnych absolutnych),
RAD — promień okręgu, na którym rozmieszczone są rowki (wartość przyrostowa bez znaku),
STA1 — kąt początkowy,
INDA — kąt rozmieszczenia rowków,
FFD — posuw dla dosuwu wgłębnego,
FFP1 — posuw dla obróbki powierzchni,
MID — maksymalna głębokość pojedynczego dosuwu (wartość przyrostowa bez znaku),
CDIR — kierunek frezowania przy obróbce rowka kołowego wartości: 2 (dla G2), 3 (dla G3),
FAL — naddatek na obrzeżu rowka (wartość przyrostowa bez ma‑ku),
VARI — rodzaj obróbki,
wartości (miejsce jednostek): 0 (obróbka kompletna), 1 (obróbka zgrubna), 2 (obróbka wykończeniowa),
wartości (miejsce dziesiątek): 0x (pozycjonowanie od rowka do rowka po prostej z GO), 1x (pozycjonowanie od rowka do rowka po torze kołowym z posuwem),
MIDF — maksymalna głębokość dosuwu dla obróbki wykończeniowej,
FFP2 — posuw dla obróbki wykończeniowej,
SSF — prędkość obrotowa przy obróbce wykończeniowej.
Cykl SLOT2 umożliwia obróbkę rowków kołowych rozmieszczonych na okręgu.
POCKET1 – Frezowanie kieszeni prostokątnej
Blok programu sterującego
POCKET1 (RTP, RFP, SDIS, DP, DPR, LENG, WID, CRAD, CPA, CPD, STA1, FFD, FFP1, MID, CDIR, FAL, VARI, MIDF, FFP2, SSF)
Parametry
RTP — płaszczyzna wycofania (we współrzędnych absolutnych),
RFP — płaszczyzna odniesienia (we współrzędnych absolutnych),
SDIS – odsunięcie płaszczyzny bezpiecznej (wartość przyrostowa bez znaku),
DP — głębokość kieszeni (we współrzędnych absolutnych),
DPR — głębokość kieszeni w stosunku do płaszczymy odniesienia (wartość przyrostowa bez znaku),
LENG — długość kieszeni (wartość przyrostowa bez znaku),
WID — szerokość kieszeni (wartość przyrostowa bez znaku),
CRAD — promień naroża (wartość przyrostowa bez znaku),
CPA — odcięta punktu środkowego kieszeni (we współrzędnych absolutnych),
COP — rzędna punktu środkowego kieszeni (we współrzędnych absolutnych),
STA1 — kąt pomiędzy osią wzdłużną kieszeni i osią odciętą, wartości: 0≤STA1<180 stopni,
FFD — posuw dla dosuwu wgłębnego,
FFP1 — posuw dla obróbki powierzchni,
MID — maksymalna głębokość pojedynczego dosuwu (wartość przyrostowa bez maku),
CDIR — kierunek frezowania przy obróbce wnęki, wartości: 2 (dla G2), 3 (dla G3),
FAL — naddatek na obrzeżu kieszeni (wartość przyrostowa bez znaku),
VARI — rodzaj obróbki, wartości: 0 (obróbka kompletna), 1 (obróbka zgrubna), 2 (obróbka wykończeniowa),
MIDF — maksymalna głębokość dosuwu dla obróbki wykończeniowej,
FFP2 — posuw dla obróbki wykończeniowej,
SSF — prędkość obrotowa przy obróbce wykończeniowej.
Działanie cyklu POCKET1 umożliwia frezowanie kieszeni o zarysie prostokątnym przy pomocy freza walcowego. Kieszeń taka może być ustawiona dowolnie na płaszczyźnie obróbki.
POCKET2 – frezowanie kieszeni kołowej
Blok programu sterującego
POCKET2 (RTP, RFP, SDIS, DP, DPR, PRAD, CPA, CPO, FFD, FFP1, MID, CDIR, FAL, VARI, MIDF, FFP2, SSF)
Parametry
RTP — płaszczyzna wycofania (we współrzędnych absolutnych),
RFP — płaszczyzna odniesienia (we współrzędnych absolutnych),
SDIS — odsunięcie płaszczyzny bezpiecznej (wartość przyrostowa bez znaku),
DP — głębokość kieszeni (we współrzędnych absolutnych),
DPR — głębokość kieszeni w stosunku do płaszczyzny odniesienia (wartość przyrostowa bez znaku),
PRAD — promień kieszeni (wartość przyrostowa bez znaku),
CPA — odcięta punktu środkowego kieszeni (we współrzędnych absolutnych),
CPO — rzędna punktu środkowego kieszeni (we współrzędnych absolutnych),
FFD — posuw dla dosuwu wgłębnego,
FFP1 — posuw dla obróbki powierzchni,
MID — maksymalna głębokość pojedynczego dosuwu (wartość przyrostowa bez znaku),
CDIR — kierunek frezowania przy obróbce wnęki, wartości: 2 (dla G2), 3 (dla G3),
FAL — naddatek na obrzeżu kieszeni (wartość przyrostowa bez znaku),
VARI — rodzaj obróbki, wartości: 0 (obróbka kompletna), 1 (obróbka zgrubna), 2 (obróbka wykończeniowa),
MIDF — maksymalna głębokość dosuwu dla obróbki wykończeniowej,
FFP2 — posuw dla obróbki wykończeniowej,
SSF — prędkość obrotowa przy obróbce wykończeniowej.
Cykl POCKET2 służy do wykonywania kieszeni o zarysie kołowym przy pomocy freza walcowego.
CYCLE71 – Frezowanie płaszczyzny
Blok programu sterującego
CYCLE71 (_RTP, _RFP, _SDIS, _DP, _PA, _PO, _LENG, _WID, _STA, _MID, _MIDA, _FDP, _FALD, _FFP1, _VARI, _FDP1)
Parametry
_RTP — płaszczyzna wycofania (we współrzędnych absolutnych),
_RFP — płaszczyzna odniesienia (we współrzędnych absolutnych),
_SDIS — odsunięcie płaszczyzny bezpiecznej (wartość przyrostowa bez znaku),
_DP — głębokość (we współrzędnych absolutnych),
_PA — odcięta punktu początkowego (we współrzędnych absolutnych),
_PO — rzędna punktu początkowego (we współrzędnych absolutnych),
_ LENG — długość obszaru obróbki w osi odciętych (wartość przyrostowa),
_WID — długość obszaru obróbki w osi rzędnych (wartość przyrostowa),
_STA — kąt pomiędzy osią wzdłużną obszaru obróbki i osią odciętą, wartości: 0 ≤ _STA < 180 stopni,
_MID — maksymalna głębokość dosuwu (wartość przyrostowa bez znaku),
_MIDA — szerokość dosuwu (wartość przyrostowa bez znaku),
_FDP — droga dobiegu narzędzia (wartość przyrostowa bez znaku),
_FALD — naddatek na obróbkę wykończeniową na głębokości (wartość przyrostowa bez znaku),
_FFP1 — posuw dla obróbki płaszczyzny,
_VARI — rodzaj obróbki: (wartość przyrostowa bez znaku), wartości (miejsce jednostek): 1 (obróbka zgrubna), 2 (obróbka wykończeniowa), wartości (miejsce dziesiątek): 1x (równolegle do odciętej, w jednym kierunku), 2x (równolegle do rzędnej, w jednym kierunku), 3x (równolegle do odciętej, z kierunkiem zmiennym), 4x (równolegle do rzędnej, z kierunkiem zmiennym), _FDP1 — droga wyjścia narzędzia w kierunku dosuwu w płaszczyźnie (wartość przyrostowa bez znaku).
Przy pomocy cyklu CYCLE71 można dokonywać frezowania dowolnie rozmieszczonej płaskiej powierzchni prostokątnej. Cykl ten nie uwzględnia korekty promienia narzędzia, a dosuw na kolejną głębokość obróbki wykonywany jest poza określonym obszarem frezowania.
CYCLE72 — Frezowanie konturu
Blok programu sterującego
CYCLE72 (_KNAME, _RTP, _RFP, _SDIS, _DP, _MID, _FAL, _FALD, _FFP1 , _FFD, _VARI, _RL, _AS1, _LP1, _FF3, _AS2, _LP2)
Parametry
_KNAME— nazwa podprogramu konturu,
_RTP — płaszczyzna wycofania (we współrzędnych absolutnych),
_RFP — płaszczyzna odniesienia (we współrzędnych absolutnych),
_SDIS— odsunięcie płaszczyzny bezpiecznej (wartość przyrostowa bez znaku),
_DP — głębokość (we współrzędnych absolutnych),
_MID — maksymalna głębokość dosuwu (wartość przyrostowa bez znaku),
_FAL — naddatek na powierzchni bocznej (wartość przyrostowa bez znaku),
_FALD — naddatek na dnie (wartość przyrostowa bez znaku), _FFP1 — posuw dla obróbki płaszczyzny,
_FFD — posuw dla dosuwu wgłębnego,
_VARI — rodzaj obróbki, wartości (miejsce jednostek): 1 (obróbka zgrubna), 2 (obróbka wykończeniowa), wartości (miejsce dziesiątek): 0x (drogi pośrednie z GO), 1x (drogi pośrednie z G1), wartości (miejsce setek): 0xx (wycofanie na końcu konturu do _RTP), 1xx (wycofanie na końcu konturu do _RFP + _SDIS), 2xx (wycofanie na końcu konturu o _SDIS), 3xx (bez wycofania na końcu konturu),
_RL — kierunek korekcji promieniowej, wartości: 40 (dla G40), 41 (dla G41), 42 (dla G42), _AS1 — sposób wprowadzenia narzędzia do obróbki, wartości (miejsce jednostek): 1 (prosta stycznie), 2 (ćwierć‑okrąg), 3 (półokrąg), wartości (miejsce dziesiątek): 0x (dosunięcie do konturu w płaszczyźnie), 1x dosunięcie do konturu po torze przestrzennym,
_LP1 — długość drogi odsunięcia (w przypadku prostej) lub promień łuku dosunięcia (w przypadku okręgu),
_FF3 — posuw wycofania i posuw dla ustawień pośrednich narzędzia w płaszczyźnie,
_AS2 — sposób wprowadzenia narzędzia do obróbki, wartości (miejsce jednostek): 1 (prosta stycznie), 2 (ćwierć okrąg), 3 (półokrąg), wartości (miejsce dziesiątek): 0x (dosunięcie do konturu w płaszczyźnie), 1x dosunięcie do konturu po torze przestrzennym,
_LP2 – długość drogi odsunięcia (w przypadku prostej) lub promień łuku dosunięcia (w przypadku okręgu).
Cykl CYCLE72 pozwala na programowanie obróbki wzdłuż dowolnego konturu zdefiniowanego w podprogramie. Obrabiany kontur nie musi być zamknięty, lecz kierunek jego programowania musi być zgodny z kierunkiem obróbki.
CYCLE76 — Frezowanie stempla prostokątnego
Blok programu sterującego
CYCLE76 (_RTP, _RFP, _SDIS, _DP, _DPR, _LENG, _WID, _CRAD, _PA, _PO, _STA, _MID, _FAL, _FALD, _FFP1, _FFD, _CDIR, _VARI, _AP1, _AP2)
Parametry
_RTP — płaszczyzna wycofania (we współrzędnych absolutnych),
_RFP — płaszczyzna odniesienia (we współrzędnych absolutnych),
_SDIS — odsunięcie płaszczyzny bezpiecznej (wartość przyrostowa bez znaku),
_DP — głębokość stempla (we współrzędnych absolutnych),
_DPR — głębokość stempla w stosunku do płaszczyzny odniesienia (wartość przyrostowa bez znaku),
_LENG — długość stempla,
_WID — szerokość stempla,
_CRAD — promień naroża stempla,
_PA — odcięta punktu odniesienia stempla (we współrzędnych absolutnych),
_PO — rzędna punktu odniesienia stempla (we współrzędnych absolutnych),
_STA — kąt pomiędzy osią wzdłużną i osią odciętych,
_MID — maksymalny dosuw na głębokość (wartość przyrostowa bez znaku),
_FAL — naddatek na powierzchni bocznej (wartość przyrostowa bez znaku),
_FALD — naddatek na dnie (wartość przyrostowa bez znaku),
_FFP1 — posuw wzdłuż konturu,
_FFD — posuw dla dosuwu wgłębnego,
_CDIR — kierunek frezowania, wartości: 0 (frezowanie współbieżne), 1 (frezowanie przeciwbieżne), 2 (G2), 3 (G3),
_VARI — rodzaj obróbki, wartości: 1 (obróbka zgrubna z pozostawieniem naddatku), 2 (obróbka wykończeniowa),
_AP1 — długość półfabrykatu,
_AP2 — szerokość półfabrykatu.
Cykl CYCLE76 umożliwia wykonanie stempla o zarysie prostokątnym ustawionego dowolnie na płaszczyźnie obróbki.
CYCLE77 — Frezowanie stempla kołowego
Blok programu sterującego
CYCLE77 (_RTP, _RFP, _SDIS, _DP, _DPR, _PRAD, _PA, _PO, _MID, _FAL, _FALD, _FFP1, _FFD, _CDIR, _VARI, _AP1)
Parametry
_RTP — płaszczyzna wycofania (we współrzędnych absolutnych),
_RFP — płaszczyzna odniesienia (we współrzędnych absolutnych),
_SDIS — odsunięcie płaszczyzny bezpiecznej (wartość przyrostowa bez znaku),
_DP — głębokość stempla (we współrzędnych absolutnych),
_DPR — głębokość stempla w stosunku do płaszczyzny odniesienia (wartość przyrostowa bez znaku),
_PRAD — średnica stempla,
_PA — odcięta punktu środkowego stempla (we współrzędnych absolutnych),
_PO — rzędna punktu środkowego stempla (we współrzędnych absolutnych),
_MID — maksymalny dosuw na głębokość (wartość przyrostowa bez znaku),
_FAL — naddatek na powierzchni bocznej (wartość przyrostowa bez znaku),
_FALD — naddatek na dnie (wartość przyrostowa bez znaku),
_FFP1 — posuw wzdłuż konturu,
_FFD — posuw dla dosuwu wgłębnego,
_CDIR — kierunek frezowania, wartości: 0 (frezowanie współbieżne), 1 (frezowanie przeciwbieżne), 2 (G2), 3 (G3),
_VARI — rodzaj obróbki, wartości: 1 (obróbka zgrubna z pozostawieniem naddatku), 2 (obróbka wykończeniowa),
_AP1 — średnica półfabrykatu.
Cykl CYCLE77 służy do wykonania stempla o zarysie kołowym, a jego działanie jest zbliżone do CYCLE76.
Cykle obróbki tokarskiej
CYCLE93 — Toczenie rowków
Blok programu sterującego
CYCLE93 (SPD, SPL, WIDG, DIAG, STA1, ANG1, ANG2, RCO1, RCO2, RCI1, RCl2, FAL1, FAL2, IDEP, DTB, VARI)
Parametry
SPD — punkt początkowy w osi poprzecznej,
SPL — punkt początkowy w osi wzdłużnej,
WIDG — szerokość rowka (wartość przyrostowa bez znaku),
DIAG — głębokość rowka (wartość przyrostowa bez znaku),
STA1 — kąt między konturem i osią odciętych, wartości: 0 ≤ STA1 ≤ 180 stopni,
ANG1 — kąt ściany rowka po stronie punktu początkowego (bez znaku liczby), wartości: : 0 ≤ ANGI1 < 90 stopni,
ANG2 — kąt ściany rowka po przeciwnej stronie punktu początkowego (bez znaku liczby), wartości: 0 ≤ ANGI2 < 90 stopni,
RCO1 — promień/faza 1 na zewnątrz po stronie punktu początkowego,
RCO2 — promień/faza 2 na zewnątrz po przeciwnej stronie punktu początkowego,
RCI1 — promień/faza 1 wewnątrz po stronie punktu początkowego,
RCl2 — promień/faza 2 wewnątrz po przeciwnej stronie punktu początkowego,
FAL1 — naddatek na dnie rowka,
FAL2 — naddatek na ściankach,
IDEP — głębokość dosuwu (wartość przyrostowa bez znaku),
DTB — czas oczekiwania na dnie rowka,
VARI — rodzaj obróbki, wartości: 1÷8 i 11÷18.
Cykl toczenia CYCLE93 umożliwia wykonanie asymetrycznych i symetrycznych rowków osiowych i promieniowych. Jednym z warunków poprawnej definicji obróbki za pomocą CYCLE93 jest odpowiednia deklaracja rejestrów narzędziowych (niezbędne jest zdefiniowanie dwóch rejestrów narzędziowych opisujących kolejne dwa punkty charakterystyczne narzędzia). Na ich podstawie obliczana jest szerokość narzędzia przy obróbce zgrubnej jak również korekcja promieniowa przy obróbce wykończeniowej.
CYCLE94 — Toczenie podcięcia
Blok programu sterującego CYCLE94 (SPD, SPL, FORM, _VARI)
Parametry
SPD — punkt początkowy w osi poprzecznej,
SPL — punkt początkowy konturu w osi wzdłużnej,
FORM — definicja kształtu, wartości: E (dla kształtu E), F (dla kształtu F),
_VARI — określenie położenia podcięcia, wartości: 0 (odpowiednio do położenia ostrza narzędzia), 1‑4 (zdefiniować położenie).
Za pomocą cyklu CYCLE94 można wykonać podcięcie odpowiadające oznaczeniom i wymiarom według normy DIN509. Zgodnie z polską normą PN‑58/M‑02043 podcięciu typu E (według normy DIN) odpowiada typ A, a podcięciu typu F — typ B.
CYCLE95 — Cykl skrawania warstwowego
Blok programu sterującego CYCLE95 (NPP, MID, FALZ, FALX, FAL, FF1, FF2, FF3, VARI, DT, DAM)
Parametry
NPP — nazwa podprogramu opisującego kontur,
MID — głębokość dosuwu (wartość przyrostowa bez znaku),
FALZ — naddatek w osi wzdłużnej (wartość przyrostowa bez znaku),
FALX — naddatek w osi poprzecznej (wartość przyrostowa bez znaku),
FAL — naddatek od konturu (wartość przyrostowa bez znaku),
FF1 — posuw dla obróbki zgrubnej bez podcięcia,
FF2 — posuw do zagłębiania się w elementy podcięcia,
FF3 — posuw dla obróbki wykończeniowej,
VARI — rodzaj obróbki, wartości: 1÷12,
DT — czas oczekiwania przy łamaniu wiórów przy obróbce zgrubnej,
DAM — długość drogi, po przebyciu której następuje zatrzymanie w celu złamania wióra.
Cykl tokarski CYCLE95 umożliwia wykonanie z półfabrykatu o kształcie walca przedmiotu o konturze określonym w podprogramie poprzez skrawanie warstwowe równolegle lub prostopadle do osi. Przy pomocy tego cyklu można obrabiać kontury zarówno za pomocą obróbki zgrubnej, jak i wykończeniowej. Jest to jeden z najpowszechniej stosowanych a zarazem złożonych cykli obróbkowych.
CYCLE96 — Toczenie podcięcia gwintu
Blok programu sterującego
CYCLE96 (DIATH, SPL, FORM, _VARI)
Parametry
DIATH — średnica nominalna gwintu,
SPL — punkt początkowy konturu w osi podłużnej,
FORM — definicja kształtu podcięcia, wartości: A (dla kształtu A), B (dla kształtu B), C (dla kształtu C), D (dla kształtu D); podcięcia kształtów A i B są zdefiniowane dla gwintu zewnętrznego, podcięcia gwintu kształtów C i D są stosowane dla gwintu wewnętrznego, kształt A i C dla normalnych wyjść gwintu, kształt B i D stosowany jest dla krótkich wyjść gwintu,
_VARI — określenie położenia podcięcia, wartości: 0 (odpowiednio do położenia ostrza narzędzia), 1‑4 (definicja położenia).
Cykl CYCLE96 służy do wykonywania podcięć gwintu zgodnie z normą DIN76. Działanie tego cyklu jest podobne do CYC‑LE94.
CYCLE97 — Cykl nacinania gwintu
Blok programu sterującego
CYCLE97 (PIT, MPIT, SPL, FPL, DM1, DM2, APP, ROP, TDEP, FAL, IANG, NSP, NRC, NID, VARI, NUMT)
Parametry
PIT — skok gwintu jako wartość,
MPIT — skok gwintu jako wielkość gwintu, wartości: 3 (dla M3) + 60 (dla M60),
SPL — punkt początkowy gwintu w osi wzdłużnej,
FPL — punkt końcowy gwintu w osi wzdłużnej,
DM1 — średnica gwintu w punkcie początkowym,
DM2 — średnica gwintu w punkcie końcowym,
APP — dobieg narzędzia (wartość przyrostowa bez znaku),
ROP — wybieg narzędzia (wartość przyrostowa bez znaku),
TDEP — głębokość gwintu (wartość przyrostowa bez znaku),
FAL — naddatek (wartość przyrostowa bez znaku),
IANG — kąt dosuwu, wartości: + (dla dosuwu po jednej powierzchni nośnej), — (dla dosuwu naprzemiennego),
NSP — przesunięcie kątowe startu dla następnego zwoju gwintu,
NRC — liczba przejść zgrubnych,
NID — liczba przejść wykończeniowych,
VARI — określenie rodzaju obróbki gwintu, wartości: 1+4,
NUMT — liczba zwojów gwintu.
Przy pomocy cyklu nacinania gwintów można wykonywać walcowe i stożkowe gwinty zewnętrzne i wewnętrzne o stałym skoku, jak również zarysy spiralne na powierzchniach czołowych. Gwinty mogą być jedno- lub wielozwojne, a ich obróbka może uwzględniać różne sposoby wcinania narzędzia.
CYCLE98 — Toczenie łańcuchów gwintów
Blok programu sterującego
CYCLE98 (PO1, DM1, PO2, DM2, PO3, DM3, PO4, DM4, APP, ROP, TDEP, FAL, IANG, NSP, NRC, NID, PP1, PP2, PP3, VARI, NUMT)
Parametry
PO1 — współrzędna punktu początkowego gwintu w osi wzdłużnej,
DM1 — średnica gwintu w punkcie początkowym,
PO2 — współrzędna pierwszego punktu pośredniego w osi wzdłużnej,
DM2 — średnica w pierwszym punkcie pośrednim,
PO3 — współrzędna drugiego punktu pośredniego w osi wzdłużnej,
DM3 — średnica w drugim punkcie pośrednim,
PO4 — współrzędna punktu końcowego gwintu w osi wzdłużnej,
DM4 — średnica w punkcie końcowym,
APP — dobieg narzędzia (wartość przyrostowa bez znaku),
ROP — wybieg narzędzia (wartość przyrostowa bez znaku),
TDEP — głębokość gwintu (wartość przyrostowa bez znaku),
FAL — naddatek (wartość przyrostowa bez znaku),
IANG — kąt dosuwu, wartości: + (dla dosuwu po jednej powierzchni nośnej), — (dla dosuwu naprzemiennego),
NSP — przesunięcie kątowe punktu startowego dla pierwszego zwoju gwintu,
NRC — liczba skrawów zgrubnych,
NID — liczba skrawów wykończeniowych,
PP1 — skok gwintu na pierwszym odcinku jako wartość,
PP2 — skok gwintu na drugim odcinku jako wartość,
PP3 — skok gwintu na trzecim odcinku jako wartość,
VARI — określenie rodzaju obróbki gwintu, wartości: 1÷4,
NUMT — liczba zwojów gwintu.
Cykl CYCLE98 umożliwia wykonanie maksymalnie trzech odcinków (kolejno jeden po drugim) gwintów walcowych albo stożkowych o różnych parametrach i wymiarach. Sposób obróbki i znaczenie parametrów jest podobne jak dla CYCLE97.
Powrót do spisu treściPowrót do spisu treści
Przygotowanie do obróbki oraz diagnostyka procesu skrawania
Podstawowe czynności obsługowe układu sterowania
Charakterystyka pulpitu układu sterowania

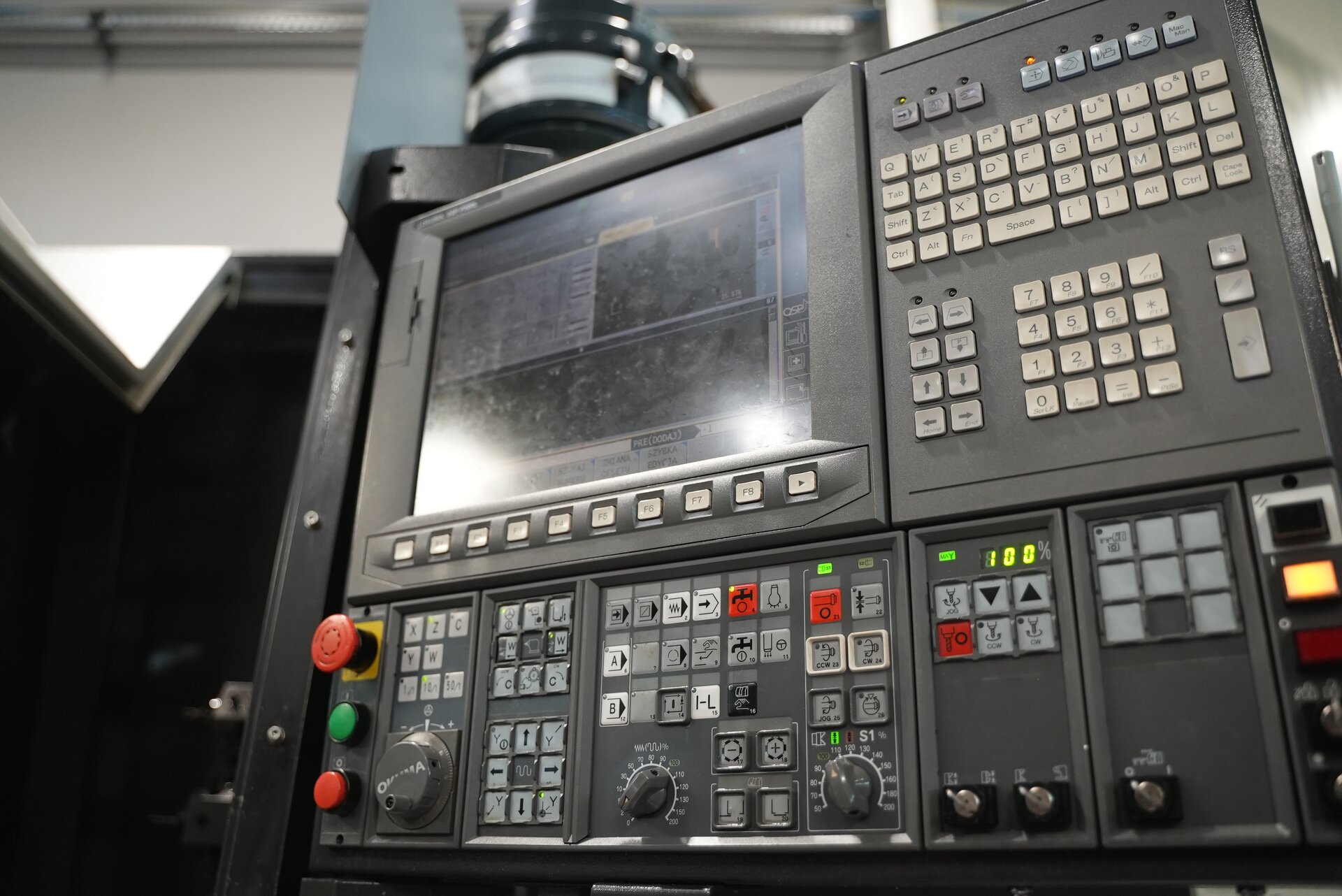
Wprowadzanie i wyprowadzanie danych w układach CNC
Układy CNC są wyposażone w pamięć (RAM, wbudowane dyski twarde); umożliwiającą zarówno zapisywanie, jak i odczytywanie danych. W zależności od możliwości układu sterowania dane można zapisywać i odczytywać z pamięci na różne sposoby:
bezpośrednio, używając klawiatury alfanumerycznej na pulpicie sterowniczym oraz na ekranie;
za pomocą złącza RS 232: z przystawek pamięciowych, z pamięci komputera zewnętrznego;
wykorzystując złącze USB;
z użyciem stacji dyskietek;
przez transmisję danych w połączonym do sieci układzie.
Do układów CNC można wprowadzać m.in.:
podprogramy;
programy obróbki;
wartości korekcyjne wymiarów narzędzia;
dane, które określają położenie charakterystycznych punktów obrabiarki (np. współrzędne punktów wymiany narzędzia, współrzędne przesunięcia początku układu współrzędnych);
parametry użytkownika,
dane, które określają parametry;
dane, które określają parametry maszynowe osi, wrzeciona, interpolacji;
programy interfejsowe;
dane, które określają parametry interfejsu (PLC).
Operator ma kompetencje do edycji tylko pięciu z wymienionych rodzajów danych. Za edycję pozostałych danych odpowiedzialna jest obsługa serwisowa obrabiarki. Dane wprowadzane bezpośrednio z klawiatury są zapisywane w odpowiednich rejestrach pamięci przypisanych do konkretnych typów danych, natomiast dane wprowadzane pośrednio (np. przez złącze RS 232) wymagają podania identyfikatora (etykiety), który umożliwia rozpoznanie typu danych przez układ CNC i ich zapisanie w odpowiednim miejscu.
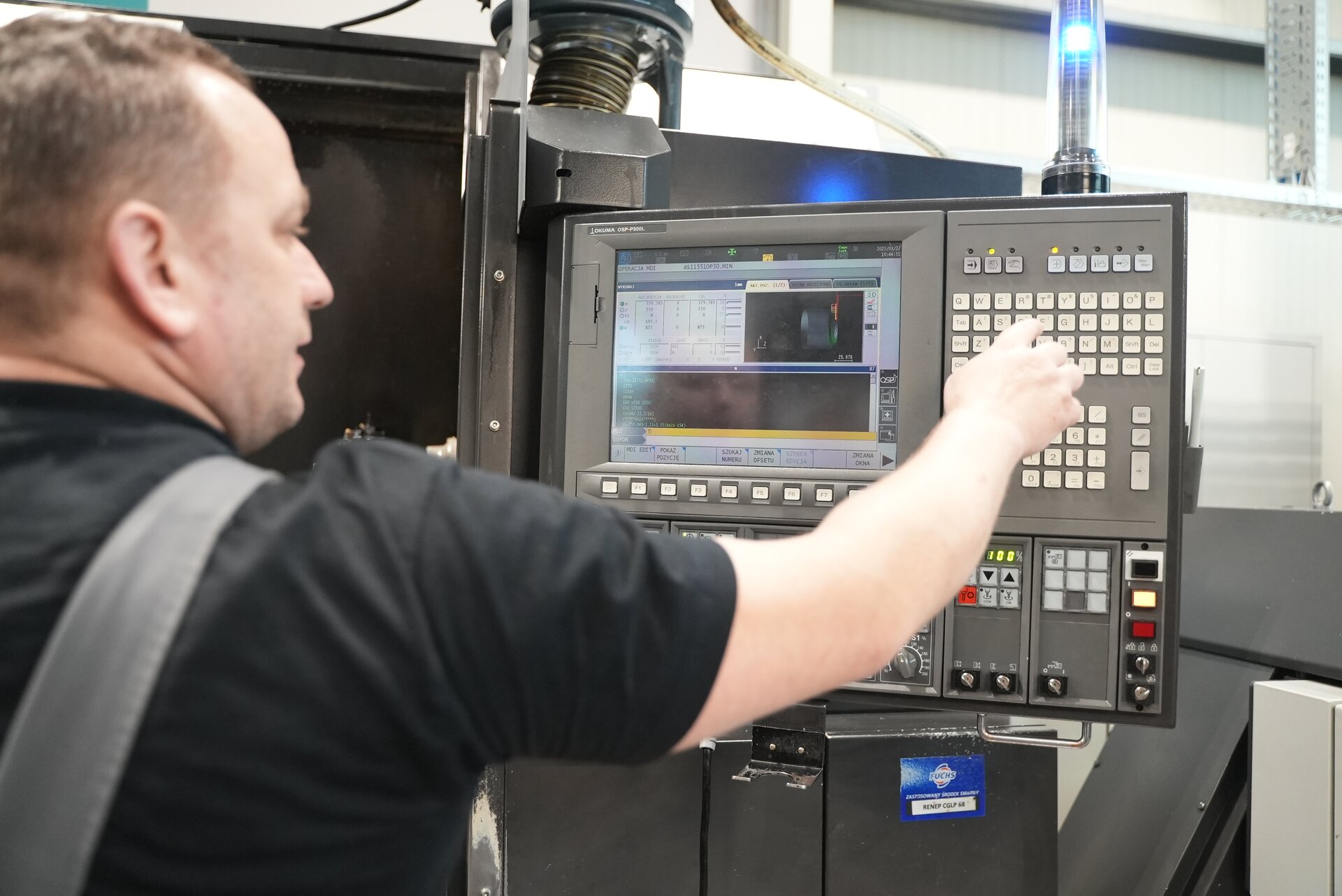
Symulacja obróbki
Symulacja obróbki pozwala na monitorowanie działania programu sterującego na ekranie układu sterowania. Jest to istotne do sprawdzenia poprawności programu przed jego wykonaniem. Możliwa jest symulacja na poziomie programowania przy użyciu systemów CAM, jednak wciąż konieczne jest sprawdzenie programu bezpośrednio na układzie CNC. Podczas symulacji obróbki kontroluje się poprawność torów ruchu narzędzi, zgodność formalnego zapisu programu oraz parametry technologiczne. Układy CNC umożliwiają przeprowadzenie symulacji w trybie automatycznym i blokowym, a także wyświetlanie szczegółów w powiększeniu. Zaawansowane układy CNC umożliwiają również symulację obróbki w przestrzeni 3D.
Uzbrojenie obrabiarki
Uchwyty narzędziowe
Tokarki sterowane numerycznie często posiadają głowice narzędziowe rewolwerowe, które umożliwiają mocowanie narzędzi za pomocą uchwytów. Istnieją dwa główne rodzaje uchwytów narzędziowych: uchwyty przykręcane śrubami do głowicy i uchwyty typu VDI. Obecnie coraz popularniejsze są głowice rewolwerowe VDI, które umożliwiają szybką wymianę uchwytów. Uchwyty narzędziowe można podzielić na uchwyty do noży tokarskich oraz uchwyty do narzędzi trzpieniowych. Uchwyty do noży tokarskich mogą być poprzeczne, wzdłużne lub wzdłużno‑poprzeczne, w zależności od zastosowania. Uchwyty do narzędzi trzpieniowych najczęściej wykorzystują tuleje zaciskowe do mocowania narzędzi. Istnieją także uchwyty do mocowania wytaczadeł, które umożliwiają mocowanie narzędzi za pomocą śrub rozmieszczonych promieniowo. Głowice narzędziowe są zaawansowanym oprzyrządowaniem narzędziowym umożliwiającym obróbkę frezarską na tokarkach. W celu skrócenia czasów mocowania narzędzi stosuje się modułowe systemy narzędziowe, które pozwalają na wymianę tylko części mocujących narzędzia, a nie całego zespołu narzędziowego.
Uchwyty przedmiotowe
Uchwyty przedmiotowe, wykorzystywane głównie w tokarkach konwencjonalnych, mogą być szczękowe z zamocowaniem ręcznym lub mechanicznym. W przypadku obrabiarek sterowanych numerycznie często stosuje się uchwyty mechaniczne, które dzielą się na uchwyty dźwigniowe i klinowe.
Uchwyty szczękowe z zamocowaniem mechanicznym są napędzane siłownikiem hydraulicznym lub pneumatycznym umieszczonym w tylnej części wrzeciennika tokarki. W uchwycie dźwigniowym ruch osiowy cięgna powoduje przesunięcie tulei, co powoduje obrót dźwigni, a ramiona dźwigni wykonują ruch promieniowy. Natomiast w uchwycie klinowym tuleja działa bezpośrednio na szczęki za pomocą skośnych ścięć, co powoduje ruch promieniowy.
W przypadku obróbki prętów stosuje się uchwyty z otworem, a do obróbki zewnętrznych powierzchni walcowych stosuje się trzpienie tokarskie, takie jak trzpienie tokarskie stale, rozprężne, z tuleją rozprężną, ze sprężynami krążkowymi, z wleją cienkościenną lub z wkładkami płytkowymi. Uchwyty z tulejami zaciskowymi są wykorzystywane do mocowania prętów lub krótkich wałków, jednak, ze względu na ograniczony zakres regulacji średnicy wewnętrznej tulei podczas mocowania, uchwyty tego rodzaju dostępne są jako zestawy z określonymi grupami tulei.
W obróbce powierzchni czołowych cienkich tarcz stosuje się uchwyty obrotowe elektromagnetyczne, magnetyczne lub oparte na mocowaniu za pomocą próżni. Uchwyty do mocowania za pomocą próżni znajdują zastosowanie w przypadku materiałów niemagnetycznych.
W grupie uniwersalnych uchwytów frezarskich wyróżnia się imadła maszynowe, uchwyty magnetyczne oraz uchwyty z zamocowaniem za pomocą podciśnienia. Imadła maszynowe są popularne w obróbce frezarskiej ze względu na swoją wszechstronność. Istnieje wiele różnych konstrukcji imadeł maszynowych, takich jak: imadła maszynowe stale, obrotowe, uchylne w trzech osiach oraz do wałków. Kolejną grupę stanowią stoły obrotowe i podziałowe, które umożliwiają ruch obrotowy realizowany za pomocą napędu mechanicznego.
Uchwyty przedmiotowe specjalne są projektowane i przygotowywane do obróbki seryjnej i wielkoseryjnej, często przez dedykowane komórki zakładowe. Natomiast w skład uchwytów składanych wchodzą różne elementy i zespoły służące do ustalenia i zamocowania przedmiotu obrabianego oraz prowadzenia narzędzi. Zestawy uchwytów składanych zawierają podstawy, elementy ustalające, elementy zamocowujące, elementy złączne oraz podzespoły.
Stoły obrotowe i urządzenia podziałowe sterowane numerycznie
Stoły obrotowe są używane w celu przeprowadzania frezowania obwodowego, wykonywania rowków obwodowych oraz obróbki ciągłej. Natomiast urządzenia podziałowe umożliwiają dokonywanie obróbki frezarskiej przy zdefiniowanym podziale kątowym. Obecnie, oprócz różnorodnych rozwiązań konstrukcyjnych, coraz powszechniejsze jest stosowanie sterowania numerycznego w stołach obrotowych i urządzeniach podziałowych. Dzięki temu uzyskuje się dodatkowe osie sterowane, co znacznie zwiększa możliwości technologiczne obrabiarek wykorzystujących tego rodzaju urządzenia.
Przykład określania punktu zerowego przedmiotu obrabianego
Określanie punktu zerowego na czole przedmiotu obrabianego.
Jeśli punkt zerowy nie znajduje się na powierzchni czołowej, należy uwzględnić tę różnicę podczas wyznaczania bazy pomiarowej. Bez wywoływania korekcyjnych wielkości, takich jak przesunięcie punktu zerowego czy wymiary narzędzia, najczęściej sterowanym punktem jest punkt odniesienia narzędzia. Wprowadzenie korekcyjnych wielkości ZB (przesunięcie zera przedmiotu obrabianego w osi Z) i ZN (wymiar narzędzia w osi Z) oraz ich wywołanie w programie sterującym powoduje przemieszczenie się zespołu sterowanego do pozycji P2. Dodatkowo określenie wymiaru narzędzia w osi X (XN) pozwala na przemieszczenie się zespołu sterowanego do pozycji P3. Te zależności umożliwiają bezpośrednie określenie przesunięcia punktu zerowego w osi Z na obrabiarce. Pierwszym krokiem jest zamocowanie przedmiotu obrabianego, a następnie wprowadzenie narzędzia wzorcowego o znanym wymiarze. Następnie, za pomocą ruchów ręcznych, narzędzie jest przybliżane do powierzchni czołowej przedmiotu obrabianego. Odczytując współrzędną osi Z z układu CNC, można określić całkowitą korekcję w tej osi (ZK). Poprzez korektę wielkości ZK o wymiar narzędzia w osi Z (ZN) można obliczyć przesunięcie punktu zerowego w osi Z (ZB).
Metody określania wymiarów narzędzia
Przy określaniu wymiarów narzędzi na obrabiarce postępuje się podobnie jak przy bazowaniu obrabiarki. W przypadku wymiaru narzędzia przy toczeniu w osi Z (Zw) narzędzie jest doprowadzane do kontaktu z powierzchnią czołową przedmiotu obrabianego. Wymiar narzędzia wynika z wartości współrzędnej Z odczytanej z układu CNC i odległości powierzchni czołowej od punktu zerowego przedmiotu obrabianego (ZL). Przy określaniu wymiaru narzędzia w osi X narzędzie jest przetaczane po powierzchni walcowej przedmiotu obrabianego, a wymiar wynika z wartości współrzędnej X, odczytanej z układu sterowania i promienia przedmiotu obrabianego. W przypadku frezowania długość narzędzi jest głównym wymiarem do określenia. Najczęściej stosuje się narzędzie zerowe jako odniesienie, a pozostałe narzędzia określa się względem niego. Możliwe jest również określanie wymiarów narzędzi przy użyciu sondy impulsowej, która umożliwia pomiar długości, promienia, ustawienia i zużycia ostrzy. Istnieją także nowoczesne systemy bezdotykowego pomiaru narzędzi, które są szybkie, umożliwiają weryfikację przed obróbką i są bezpieczne dla narzędzi. Do pomiarów narzędzi poza obrabiarką stosuje się specjalne urządzenia nastawcze, które zapewniają dokładne pomiary i dokumentację.
Zużycie i uszkodzenie narzędzi
Problem | Powód | Zalecenia |
---|---|---|
Starcie na powierzchni przyłożenia i karby | a – prędkość skrawania za wysoka lub niewystarczająca odporność na ścieranie | a) Zmniejszyć prędkość skrawania. Zastosować gatunek o większej odporności na ścieranie. |
Odkształcenie plastyczne | Zbyt duża temperatura skrawania w połączeniu z dużymi naciskami. | Należy wybrać twardszy gatunek o większej odporności na odkształcenie plastyczne |
Narost | Obrabiany materiał zespawany z płytką z powodu:
| Zwiększyć prędkość skrawania |
Uderzenia wióra | Wióry odwijają się na ostrze. | Zmienić posuw. Wybrać płytkę o geometrii alternatywnej. |
Zużycie w formie krateru | Zużycie dyfuzyjne z powodu zbyt wysokich temperatur na powierzchni natarcia. | Należy zastosować gatunek powlekany Al2O3. |
Wykruszenia | Zbyt kruchy gatunek | Zastosować gatunek o większej udarności. |
Pęknięcia cieplne | Zmiany temperaturowe wywołane:
| Zastosować gatunek o większej odporności na wstrząsy termiczne. |
Złamanie płytki | Zbyt kruchy gatunek | Wybrać gatunek o większej udarności. |
Odłamanie – ceramika | Za duże naciski | Zmniejszyć posuw. |
Diagnostyka obrabiarki
Zapewnienie dokładności obróbki wymaga oceny stanu obrabiarek przed rozpoczęciem skrawania. Badania geometryczne obejmują prostoliniowość, płaskość, równoległość, prostopadłość i obroty. Obrabiarki CNC podlegają dodatkowemu badaniu dokładności i powtarzalności pozycjonowania osi sterowanych numerycznie oraz badaniu okrągłości. Pomiar dokładności dotyczy osi liniowych i obrotowych. Obrabiarka jest programowana do ruchu zespołu sterowanego wzdłuż osi z pozycjonowaniem w punktach pomiarowych. Metody wykorzystujące urządzenia laserowe są przydatne do tych badań, umożliwiają szybką diagnostykę i automatyczną kompensację błędów. Badanie okrągłości jest powszechnie akceptowane jako test dokładności obrabiarek CNC. Polega ono na ocenie odchyłki promienia okręgu podczas ruchów w dwóch osiach. Wykorzystuje się próbniki jedno- lub dwuwymiarowe oraz urządzenia pomiarowe. Odchyłki geometryczne, sterowanie numeryczne i działanie serwonapędów mają wpływ na dokładność konturów okrągłości na obrabiarkach CNC.
Powrót do spisu treściPowrót do spisu treści
Metody pomiaru przedmiotu obrabianego
Pomiary w trakcie obróbki
W trakcie procesu skrawania stosuje się stykowe elektroniczne urządzenia pomiarowe do mierzenia przedmiotu obrabianego i osiągnięcia wysokiej dokładności obróbki. Te urządzenia posiadają szczęki pomiarowe, które stykają się z przedmiotem podczas obróbki. Aktualny wymiar przedmiotu jest ustalany na podstawie położenia szczęk.
Pomiary z wykorzystaniem sondy pomiarowej
Sondy pomiarowe znajdują coraz szersze zastosowanie w obrabiarkach CNC i często są ich standardowym wyposażeniem. Pozwalają na pomiar przed i po obróbce przedmiotu oraz określanie współrzędnych wybranych punktów, takich jak bazowanie obrabiarki. Pomiar z sondą pomiarową polega na zbliżeniu końcówki pomiarowej do przedmiotu obrabianego, odczytaniu współrzędnych i na tej podstawie określeniu mierzonej wielkości. Sondę pomiarową można stosować zarówno w trybie ręcznym, jak i automatycznym na obrabiarkach CNC. Tryb automatyczny obejmuje typowe cykle pomiarowe, takie jak pomiary pozycji w osiach X, Y, Z, określanie średnic otworów/wałków, wymiarów stempli/kieszeni oraz pomiary kątów. Uzyskane wyniki pomiarów są najczęściej zapisywane w postaci R‑parametrów, które mogą być wykorzystane w obliczeniach arytmetycznych lub bezpośrednio w programach sterujących, na przykład do ustawienia punktu zerowego przedmiotu obrabianego.
Pomiary z wykorzystaniem czujnika krawędziowego
Do pomiaru przedmiotu obrabianego na obrabiarkach można również wykorzystać czujnik krawędziowy, który umożliwia pomiary w trzech kierunkach (X, Y, Z). Końcówkę pomiarową zbliża się do określonej powierzchni przedmiotu obrabianego, a precyzyjny punkt styku jest określany dzięki wysokiej rozdzielczości tego czujnika. Współrzędną punktu styku odczytuje się bezpośrednio z układu sterowania, co umożliwia obliczenie wybranych punktów i wymiarów przedmiotu obrabianego. Ten sposób pomiaru przypomina pomiar z sondy, ale odbywa się wyłącznie w trybie ręcznym na obrabiarkach. Pomiary z wykorzystaniem czujnika krawędziowego na obrabiarkach CNC pozwalają m.in. na ustalenie punktu zerowego na przedmiocie obrabianym, określenie współrzędnych środka otworu, identyfikację błędów ustawienia przedmiotu obrabianego oraz pomiary długości na przedmiocie obrabianym.
Podstawowe przyrządy miernictwa warsztatowego
Przyrządy pomiarowe stosowane w warsztatach można podzielić na trzy grupy: suwmiarki, przyrządy mikrometryczne i przyrządy czujnikowe. Suwmiarki są najprostszymi przyrządami i posiadają prowadnicę z wzorcem długości oraz suwak z urządzeniem do odczytywania położenia. Przyrządy mikrometryczne, takie jak mikrometry zewnętrzne, wewnętrzne, głębokościomierze, średnicówki i głowice mikrometryczne, oferują większą dokładność pomiaru. Przyrządy czujnikowe umożliwiają pomiary różnicowe, mają mały zakres pomiarowy i wysoką dokładność. W tej grupie można wyróżnić czujniki mechaniczne, zębate, dźwigniowo‑zębate, dźwigniowo‑śrubowe, sprężynowe, optyczno‑mechaniczne, elektryczne, pneumatyczne i inkrementalne, z różnicami w zasadzie działania.
Powrót do spisu treściPowrót do spisu treści