Maszyny i urządzenia- obsługa
MEC.03. Montaż i obsługa maszyn i urządzeń - Mechanik‑Monter maszyn i urządzeń, Technik mechanik
Użytkowanie maszyn i urządzeń
ATLAS INTERAKTYWNY
opisy prezentowanych na grafikach obiektów są załączone w treści
Spis treści
Fazy istnienia obiektu technicznegoFazy istnienia obiektu technicznego
EksploatacjaEksploatacja
Wymagania eksploatacyjneWymagania eksploatacyjne
Charakterystyka i podział eksploatacyjny maszyn i urządzeńCharakterystyka i podział eksploatacyjny maszyn i urządzeń
Fizykochemiczne podstawy eksploatacji maszynFizykochemiczne podstawy eksploatacji maszyn
Zużywanie części maszynZużywanie części maszyn
SmarowanieSmarowanie
Stan techniczny i eksploatacja maszyn i urządzeń – pojęcia podstawoweStan techniczny i eksploatacja maszyn i urządzeń – pojęcia podstawowe
Uszkodzenia obiektu eksploatacjiUszkodzenia obiektu eksploatacji
Podstawy diagnostyki technicznejPodstawy diagnostyki technicznej
Diagnostyka technicznaDiagnostyka techniczna
Rodzaje badań diagnostycznychRodzaje badań diagnostycznych
Użytkowanie maszyn i urządzeńUżytkowanie maszyn i urządzeń
Właściwości użytkowe maszynWłaściwości użytkowe maszyn
Miary użytkowania i ich zastosowanieMiary użytkowania i ich zastosowanie
Dobór podstawowych parametrów użytkowaniaDobór podstawowych parametrów użytkowania
Wdrażanie urządzeń do użytkowaniaWdrażanie urządzeń do użytkowania
Dokumentacja techniczno‑ruchowa maszyn i urządzeńDokumentacja techniczno‑ruchowa maszyn i urządzeń
Zasady bezpieczeństwa użytkowania maszynZasady bezpieczeństwa użytkowania maszyn
Obsługa maszyn i urządzeńObsługa maszyn i urządzeń
Rodzaje obsługiRodzaje obsługi
Utrzymanie maszyn i urządzeńUtrzymanie maszyn i urządzeń
Obsługa codziennaObsługa codzienna
Obsługa sezonowaObsługa sezonowa
Obsługa zabezpieczającaObsługa zabezpieczająca
Obsługa diagnostycznaObsługa diagnostyczna
Obsługa gwarancyjnaObsługa gwarancyjna
Obsługa okresowaObsługa okresowa
Remont bieżącyRemont bieżący
Remont średniRemont średni
Remont kapitalnyRemont kapitalny
Modernizacja i adaptacjaModernizacja i adaptacja
Cykl remontowyCykl remontowy
Obsługiwanie przechowywanych maszyn i urządzeńObsługiwanie przechowywanych maszyn i urządzeń
Zasady ogólneZasady ogólne
Kryteria wyboru metody przechowywaniaKryteria wyboru metody przechowywania
Obsługiwanie przed przechowywaniemObsługiwanie przed przechowywaniem
Obsługiwanie w czasie przechowywaniaObsługiwanie w czasie przechowywania
Obsługiwanie po przechowywaniuObsługiwanie po przechowywaniu
Fazy istnienia obiektu technicznego
Eksploatacja
Pojęcie eksploatacji maszyn i urządzeń obejmuje:
wykonywanie operacji na tych urządzeniach,
zachowanie urządzeń w odpowiednim stanie technicznym.
W ramach działań związanych z prowadzeniem urządzeń należy wymienić:
uruchamianie urządzenia,
obsługę podczas pracy,
planowane zatrzymywanie urządzenia w normalnych warunkach, jak i w przypadku awarii,
dokumentowanie zdarzeń związanych z ruchem maszyn.
Do działań związanych z utrzymywaniem urządzeń w odpowiednim stanie technicznym zalicza się: przeglądy, konserwację, naprawy oraz działania kontrolno‑pomiarowe, które pozwalają na ocenę stanu technicznego.
Eksploatacja to ciąg działań, procesów i zjawisk związanych z wykorzystaniem obiektów technicznych przez człowieka. W procesie eksploatacji wyodrębnia się rodzaje (obszary) działań:
użytkowanie - to wykorzystywanie obiektu zgodnie z jego przeznaczeniem i właściwościami;
obsługiwanie - to utrzymywanie obiektu w stanie sprawności technicznej oraz przywracanie wymaganych właściwości dzięki przeglądom, naprawom, konserwacji, regulacji;
zasilanie - to dostarczanie do obiektu materiałów, energii, informacji;
zarządzanie - to planowanie i podejmowanie decyzji, organizowanie, analizowanie.
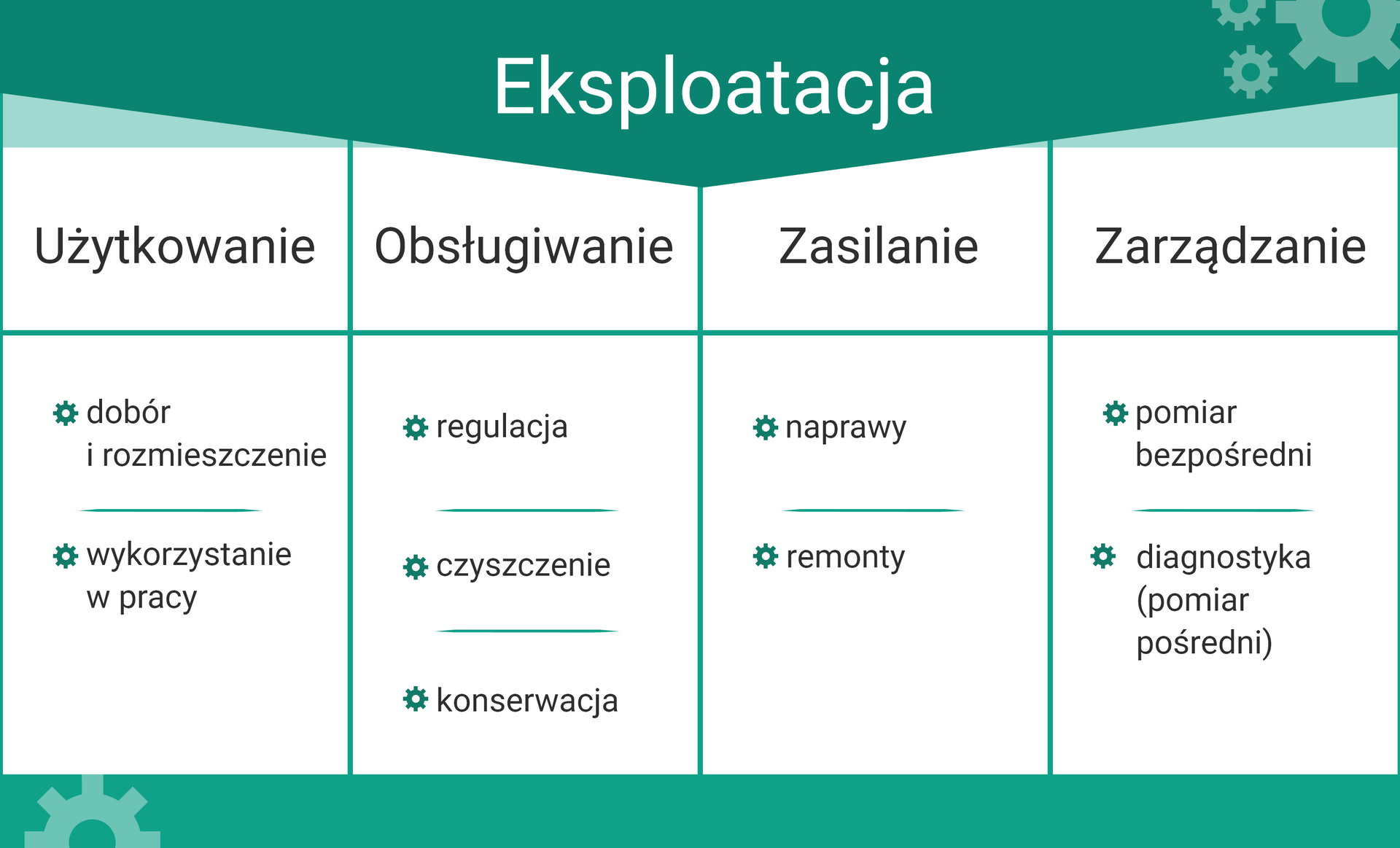
Wymagania eksploatacyjne
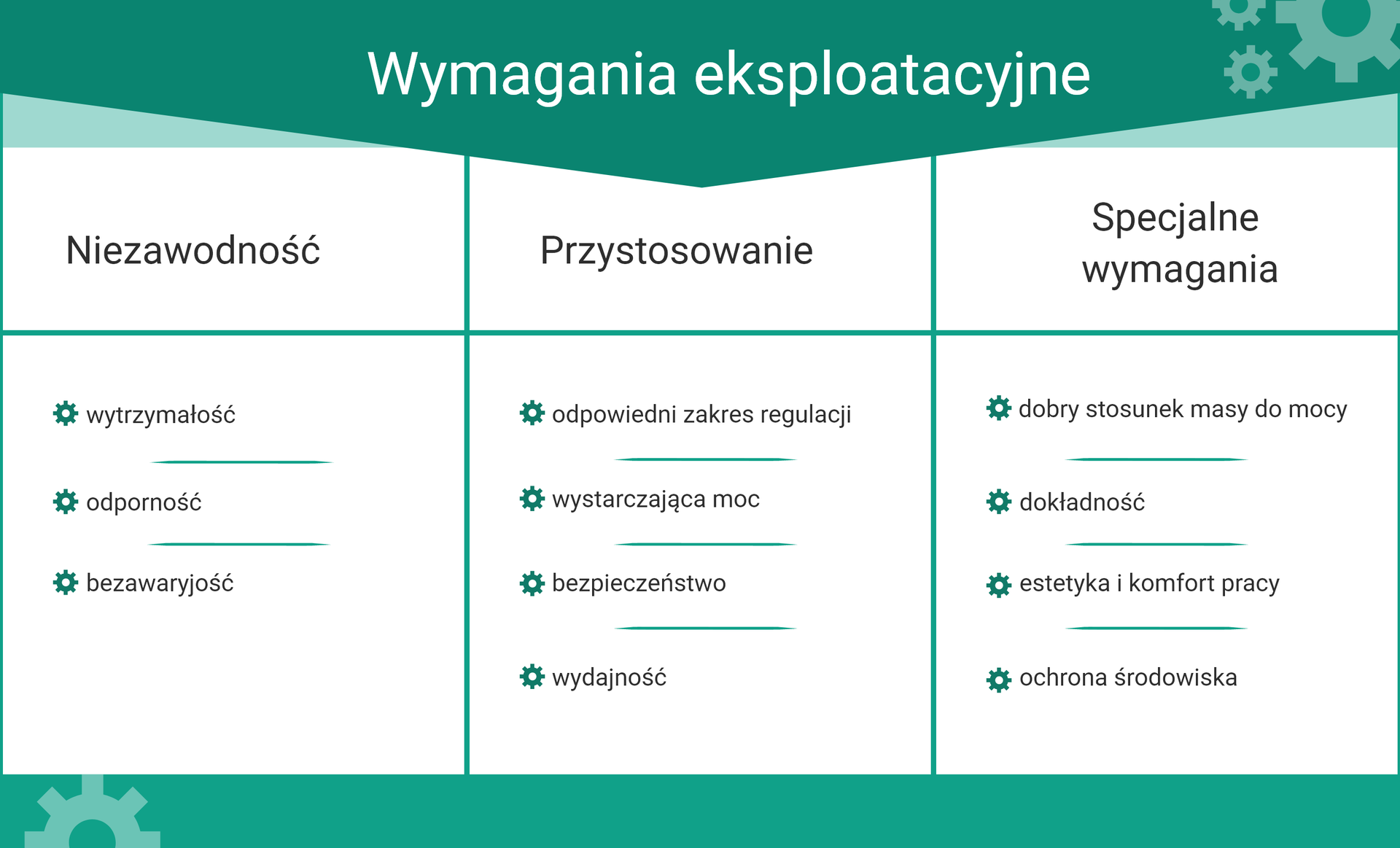
Charakterystyka i podział eksploatacyjny maszyn i urządzeń
Charakterystyka i podział eksploatacyjny maszyn i urządzeń to istotne koncepcje w dziedzinie inżynierii i zarządzania technicznego. Obejmuje to zrozumienie właściwości, funkcji, zastosowań oraz cyklu życia maszyn i urządzeń w kontekście ich użytkowania i konserwacji.
W skład charakterystyki eksploatacyjnej obiektu technicznego wchodzą różne elementy:
Podział eksploatacyjny maszyn i urządzeń może mieć różne kryteria, zależnie od kontekstu.
Oto przykłady:
Podział według zastosowania:
maszyny produkcyjne wykorzystywane w procesach produkcyjnych takie jak tokarki, frezarki, wtryskarki itp.,
urządzenia transportowe takie jak: ciężarówki, dźwigi, wózki widłowe,
urządzenia medyczne takie jak: aparatura diagnostyczna i terapeutyczna,
urządzenia domowe takie jak: pralki, lodówki, odkurzacze.
Podział według branży:
maszyny rolnicze: traktory, kombajny, prasy,
maszyny budowlane: koparki, wiertnice, spychacze,
maszyny przemysłowe: tokarki, wtryskarki, piece przemysłowe,
maszyny spożywcze: młyny, piece piekarnicze, linie produkcyjne.
Podział według złożoności:
maszyny prostych zastosowań o niewielkiej złożoności technicznej i niewielkim stopniu automatyzacji,
maszyny zaawansowane wymagające zaawansowanej automatyki, sterowania i monitorowania.
Podział według źródła napędu:
maszyny elektryczne napędzane energią elektryczną,
maszyny mechaniczne wykorzystujące ruch mechaniczny do przekazywania energii,
maszyny pneumatyczne i hydrauliczne napędzane sprężonym powietrzem lub płynami.
Podział eksploatacyjny maszyn i urządzeń może być dostosowany do konkretnego sektora przemysłu lub zastosowania. Ostatecznie celem jest efektywne zarządzanie i utrzymanie tych urządzeń w celu zapewnienia wydajności, bezpieczeństwa i zgodności z wymaganiami technicznymi.
Fizykochemiczne podstawy eksploatacji maszyn
Tarcie to opór, który występuje między dwiema powierzchniami, poruszającymi się względem siebie. Jest to zjawisko fizyczne wynikające z oddziaływań między atomami i cząstkami wewnętrznymi struktur ciała stałego. Tarcie przeciwdziała ruchowi i jest przyczyną straty energii mechanicznej na skutek przekształcenia jej w ciepło. W kontekście obsługi maszyn i urządzeń, tarcie może mieć zarówno pozytywne, jak i negatywne skutki.
Opis alternatywny dotyczy grafiki interaktywnej z pozytywnymi i negatywnymi skutkami tarcia.
Przenoszenie energii. W przypadku pasów napędowych tarcie jest wykorzystywane do przenoszenia energii – od napędzającej jednostki do napędzanego mechanizmu, na przykład w pasach transmisyjnych.
Hamowanie. Układy hamulcowe wykorzystują tarcie do spowolnienia lub zatrzymania ruchu pojazdów lub maszyn.
Uszkodzenia i zużycie. Tarcie prowadzi do zużywania powierzchni materiałów, co może powodować uszkodzenia i zużycie części maszyn, a także generować opiłki metalu lub inne odpady.
Wytwarzanie ciepła. Tarcie generuje ciepło, co może prowadzić do przegrzewania się elementów maszyn i utraty wydajności.
Energia potrzebna do pokonania tarcia. Wymagane jest dostarczenie dodatkowej energii, aby pokonać opór tarcia, co może prowadzić do większego zużycia energii i spadku wydajności.
Zużywanie części maszyn
Zużywanie to proces polegający na wyczerpywaniu się pewnego zasobu oraz niszczeniu go poprzez długotrwałe użytkowanie lub funkcjonowanie.
Proces zmniejszania masy lub trwałe deformacje powierzchni elementów maszyn nazywane są zużywaniem tych elementów. Efektem tego procesu jest pojawienie się zużycia.
Aby opisać proces zużywania, często posługujemy się pojęciem szybkości zużywania, co oznacza zmianę w ilości zasobu na jednostkę czasu.
Smarowanie
Smarowanie to proces stosowania środków smarnych w celu zminimalizowania tarcia i zużycia oraz zapewnienia odpowiedniej ochrony powierzchni metalowych. Środki smarne mają za zadanie utrzymywać odpowiedni poślizg pomiędzy powierzchniami ruchomymi oraz redukować procesy korozyjne. Smarowanie odgrywa kluczową rolę w zapewnieniu trwałości i efektywności maszyn, urządzeń i pojazdów.
Stan techniczny i eksploatacja maszyn i urządzeń – pojęcia podstawowe
Uszkodzenia obiektu eksploatacji
Uszkodzenie obiektu eksploatacji odnosi się do sytuacji, w której dany przedmiot, urządzenie lub struktura przestaje funkcjonować zgodnie z pierwotnym przeznaczeniem z powodu uszkodzenia, awarii lub innych nieprawidłowości. Obiektem eksploatacji może być cokolwiek, od maszyn przemysłowych, urządzeń elektronicznych, budynków, po środki transportu, a nawet infrastrukturę publiczną.
Opisując uszkodzenie obiektu eksploatacji, należy uwzględnić kilka kluczowych aspektów:
Rodzaj uszkodzenia
Uszkodzenia mogą mieć różny charakter, np. mechaniczny, elektryczny, termiczny, chemiczny, korozję itp. W zależności od rodzaju uszkodzenie może prowadzić do różnych konsekwencji dla działania obiektu.Podział uszkodzeń:
usuwalne (czasowe, chwilowe),
nieusuwalne (stałe),
krytyczne – brak możliwości dalszego używania obiektu,
ważne – wymagana natychmiastowa interwencja w celu przywrócenia użyteczności obiektu,
mało ważne – interwencja w celu przywrócenia użyteczności może być odłożona w czasie,
nieistotne – pomijający wpływ na działanie obiektu.
Przyczyna uszkodzenia
Warto zrozumieć, co spowodowało uszkodzenie. Może to być wada konstrukcyjna, niewłaściwa lub nadmierna eksploatacja, brak konserwacji w obsłudze lub uszkodzenie wynikające z zewnętrznych czynników, takich jak wypadek, warunki atmosferyczne itp.Skutki uszkodzenia
Uszkodzenie może prowadzić do różnych skutków, takich jak przerwanie produkcji, straty finansowe, zagrożenie bezpieczeństwa, opóźnienia w dostawach lub usługi, a także wpływać na reputację firmy lub organizacji.Skala uszkodzenia
Uszkodzenia mogą mieć różną skalę, od niewielkich problemów, które można szybko naprawić, po poważne awarie, które mogą wymagać długotrwałej naprawy lub nawet zastąpienia obiektu nowym.
Podział skali uszkodzenia:usterka (najmniej rozległa),
uszkodzenie,
awaria,
zniszczenie (najbardziej rozległe).
Naprawa i przywrócenie funkcjonalności
W przypadku uszkodzenia istotne jest, aby przeprowadzić odpowiednie działania naprawcze. Może to obejmować diagnozę problemu, zamianę uszkodzonych części, konserwację, regenerację lub całkowitą wymianę uszkodzonego obiektu.Zapobieganie przyszłym uszkodzeniom
Po naprawie istotne jest podjęcie działań w celu minimalizacji ryzyka przyszłych uszkodzeń, takich jak: lepsza konserwacja, wdrożenie środków bezpieczeństwa, monitorowanie stanu obiektu i przeprowadzanie regularnych przeglądów.
Powrót do spisu treściPowrót do spisu treści
Podstawy diagnostyki technicznej
Diagnostyka techniczna
Diagnostyka
To proces identyfikowania, analizowania i rozwiązywania problemów lub chorób w różnych dziedzinach, takich jak medycyna, psychologia, technologia czy mechanika. Diagnostyka polega na zbieraniu informacji, badaniu objawów, analizie danych i wnioskowaniu w celu określenia przyczyn problemów lub stanów nieprawidłowych oraz opracowania odpowiednich rozwiązań lub terapii.
Diagnostyka techniczna
Zwana również diagnostyką maszynową lub diagnostyką inżynierską, koncentruje się na identyfikowaniu problemów, awarii lub uszkodzeń w urządzeniach, maszynach, pojazdach czy systemach technicznych. Jej celem jest zrozumienie, dlaczego dana maszyna lub urządzenie nie działa poprawnie i określenie, jakie kroki należy podjąć, aby je naprawić lub przywrócić do pełnej sprawności.
Rodzaje badań diagnostycznych
Powrót do spisu treściPowrót do spisu treści
Użytkowanie maszyn i urządzeń
Właściwości użytkowe maszyn
W trakcie eksploatacji maszyn różne ich elementy oddziałują na siebie, co generuje obciążenia, szczególnie w sytuacjach, gdy muszą pokonywać chwilowe opory, np. podczas obróbki, hamowania czy uruchamiania pod obciążeniem. Wzmocnienie jednej z sił działających na urządzenie w określonym czasie występuje w momentach, gdy maszyna konfrontowana jest z dodatkowymi oporami ruchu, które pojawiają się w trakcie całego okresu użytkowania, np. podczas obciążenia własnym ciężarem, siłami napędowymi lub kontynuowaną obróbką materiału.
Obciążenia mogą być podzielone na trzy rodzaje: chwilowe, krótkotrwałe i długotrwałe. W trakcie użytkowania maszyny może być ona normalnie obciążona, niedociążona lub przeciążona. Przeciążenia zwykle wynikają z błędów popełnianych w trakcie obsługi maszyn.
W trakcie użytkowania urządzeń mechanicznych wiele parametrów podlega zmianom. Są to m.in.: prędkość mechanizmów, cykle technologiczne, godziny pracy, właściwości otoczenia oraz parametry techniczne. Właściwości urządzeń i maszyn obejmują takie parametry, jak: długość, masa, temperatura, wytrzymałość na obciążenia, odporność na odkształcenia, trwałość, zużycie energii i wiele innych. Wartości tych parametrów powinny mieścić się w określonym zakresie tolerancji. Znamionowe wartości maszyn określa konstruktor i umieszcza je na tabliczce znamionowej przy maszynie.
Właściwości maszyn i urządzeń związane z użytkowaniem obejmują:
W trakcie eksploatacji urządzeń ich poszczególne części i zespoły ulegają zużyciu. Aby zapewnić im prawidłowe funkcjonowanie, konieczne jest przeprowadzanie prac konserwacyjnych i remontowych. W celu określenia odpowiednich terminów tych działań wykorzystuje się mierniki wykonywanej pracy, takie jak intensywność pracy, intensywność użytkowania i resurs.
Kryteria oceny poprawności użytkowania urządzeń obejmują aspekty techniczne, ekonomiczne i bezpieczeństwa, uwzględniając zarówno wydajność, jak i warunki ochrony środowiska oraz higieny pracy.
Miary użytkowania i ich zastosowanie
Parametry użytkowania rejestrowane są za pośrednictwem liczników, które oddają obraz intensywności eksploatacji urządzenia lub maszyny:
długość – liczba pokonanych kilometrów;
czas – liczba przepracowanych godzin;
masa – łączny tonaż przewiezionego ładunku;
liczebność – liczba przeprowadzonych cykli operacyjnych;
koszt – wartość wytwarzanych produktów w jednostce czasu.
Dobór podstawowych parametrów użytkowania
W trakcie przygotowywania oraz prowadzenia procesu użytkowania urządzeń technicznych istotne jest uwzględnienie odpowiednich parametrów pracy maszyn. Wśród tych parametrów kluczową rolę odgrywają wskaźniki związane z obciążeniem urządzeń oraz prędkością roboczą. Te dwie cechy mają znaczący wpływ na zdolności użytkowe, wydajność i koszty generowane w trakcie eksploatacji. Wartości te istotnie wpływają na skuteczność funkcjonowania maszyn.
Opis procesu użytkowania i jego ocena opierają się na podziale parametrów obiektów technicznych według ich znaczenia.
Wdrażanie urządzeń do użytkowania
Zakres działań objętych planem rozruchowym jest uzależniony od gotowości operacyjnej urządzenia do pracy. Gotowość operacyjna (nazywana także gotowością techniczną lub przygotowawczą) oznacza zdolność urządzenia do wykonywania swoich funkcji w momencie, gdy użytkownik tego oczekuje. Wyraża ona prawdopodobieństwo rozpoczęcia pracy w określonym czasie. Wyższy stopień gotowości operacyjnej przekłada się na mniejszy zakres działań rozruchowych oraz krótszy czas, jaki jest potrzebny do rozpoczęcia pracy.
Istnieją różne rodzaje gotowości operacyjnej, a mianowicie:
dla nowych urządzeń, które nie zostały jeszcze zainstalowane ani używane;
dla nowych urządzeń po wykonaniu procesu ustawiania, odkonserwowania i połączenia z pozostałym systemem technicznym;
dla urządzeń po pierwszym uruchomieniu w fazie wdrożenia;
dla urządzeń znajdujących się w długotrwałym stanie postoju;
dla urządzeń znajdujących się w krótkotrwałym stanie postoju;
dla urządzeń, które zostały częściowo uruchomione.
Proces rozruchu polega na usunięciu blokad oraz dostarczeniu energii i surowców niezbędnych do podtrzymania pracy urządzenia. Ze względu na trwałość samego urządzenia proces rozruchu powinien być przeprowadzany stopniowo. Rozruch związany jest z pewnymi stratami energii i surowców, dlatego konieczne jest określenie czasu, jaki jest potrzebny do jego zakończenia. W sytuacjach uzasadnionych, gdy wymagany jest szybki rozruch, urządzenie powinno być utrzymywane w wyższym stopniu gotowości operacyjnej.
Z uwagi na ograniczone zakresy ustawień regulatorów, które nie obejmują obszarów poza zakresem zmienności ruchowej, często niemożliwa jest automatyczna regulacja tych obszarów. W związku z tym stosuje się regulację ręczną, która po zakończeniu procesu rozruchu może być przełączona na tryb automatyczny.
Podczas procesu rozruchu zachodzą pewne zjawiska, które mają wpływ na zużycie oraz trwałość urządzeń. Są to m.in.:
zwiększone zużycie energii w celu przezwyciężenia sił bezwładności, pokonania oporów tarcia spoczynkowego, pokonania większej lepkości zimnych środków smarnych itp.;
zmiany i różnice w temperaturze poszczególnych części urządzenia w wyniku przepływu ciepła, co wpływa na opory, jakie napotykane są przez ten przepływ;
możliwość poślizgu części współpracujących ze sobą przez tarcie;
występowanie zjawisk elektrycznych podczas rozruchu, takich jak początkowe przeciążenia prądowe w silnikach elektrycznych;
dodatkowe utrudnienia spowodowane nieprawidłową pracą urządzeń pomocniczych lub nieprawidłowym stanem mediów roboczych w czasie rozruchu. Może to obejmować niewłaściwe początkowe luzowanie, uszczelnienia mechaniczne i hydrauliczne, zakłócenia wynikłe z nagromadzonych zanieczyszczeń w niewłaściwych miejscach urządzeń podczas postoju, a także ogólnie złe stany urządzeń.
Aby złagodzić niekorzystne efekty procesów rozruchowych, warto dążyć do opracowania optymalnych procedur (programów) rozruchu, które zapewnią płynne i stopniowe obciążenie urządzeń. Przyspieszenie procesu rozruchu można osiągnąć poprzez utrzymanie urządzenia w odpowiedniej gotowości operacyjnej.
Etapy realizacji programu rozruchowego:
sprawdzenie stanu urządzenia w celu upewnienia się, że wszystkie prace naprawcze, konserwacyjne oraz usuwanie ciał obcych, blokad i zanieczyszczeń zostały zakończone;
przygotowanie urządzenia do działania poprzez:
odpowiednie dostosowanie urządzeń sterujących i współpracujących,
zapełnienie zbiorników surowcami, substancjami roboczymi, paliwem itp.;
prowadzenie właściwego procesu rozruchu poprzez:
zachowanie optymalnej prędkości rozruchu,
skoordynowane uruchamianie poszczególnych mechanizmów, obiegów i zasilania,
nadzór i monitoring zwiększonych wskazań przyrządów pomiarowych itp.
Podczas zatrzymywania urządzeń konieczne jest uwzględnienie:
utrzymania trwałości urządzenia podczas okresów bezczynności,
czyszczenia i suszenia urządzenia,
unikania:
wyładowań elektrycznych,
uderzeń hydraulicznych (w systemach przepływowych),
przerzutów substancji (w systemach próżniowych).
Rozruch nowych urządzeń w fazach:
W tym okresie dokładnie badane są właściwości ruchowe urządzenia, a personel obsługujący jest szkolony.
Uważa się, że urządzenie jest gotowe do eksploatacji:
po osiągnięciu trwałej zdolności użytkowej, przy zachowaniu pozostałych parametrów użytkowych (wydajność, jakość produktu itp.),
po dostrojeniu i zoptymalizowaniu pracy urządzenia pod względem określonych kryteriów,
po zrozumieniu jego charakterystyki i ustanowieniu szczegółowych zasad eksploatacji.
Dokumentacja techniczno‑ruchowa maszyn i urządzeń
Dokumentacja techniczno‑ruchowa (DTR) maszyn i urządzeń zawiera:
charakterystykę techniczną i dane ewidencyjne,
rysunek złożeniowy,
wykaz wyposażenia normalnego i specjalnego,
schematy kinematyczne, elektryczne i pneumatyczne,
schemat funkcjonowania,
instrukcję użytkowania,
instrukcję obsługi,
instrukcję konserwacji i smarowania,
instrukcję BHP,
normy remontowe,
wykaz części zamiennych,
wykaz wyposażenia,
wykaz rysunków złożeniowych,
wykaz części zapasowych.
W firmie, która nabywa nowe urządzenie lub maszynę, dokumentację techniczną i ruchową otrzymuje dział głównego mechanika. W przypadku braku instrukcji smarowania i obsługi dział ten opracowuje je na podstawie Dokumentacji Techniczno‑Ruchowej (DTR) i umieszcza je na stanowisku pracy. Dodatkowo dział głównego mechanika tworzy Kartę maszynową na bazie DTR. Karta ta zawiera następujące informacje:
dane ewidencyjne (nazwa maszyny, typ, numer fabryczny, numer inwentarzowy, rok produkcji, rok ustawienia, miejsce ustawienia),
charakterystyki fizyczne maszyny,
rysunek lub zdjęcie maszyny,
wymiary zewnętrzne maszyny oraz jej wagę,
informacje dotyczące napędu,
dane na temat standardowego i specjalnego wyposażenia,
dane eksploatacyjne maszyny.
Na podstawie Dokumentacji techniczno‑ruchowej i Karty maszynowej dział głównego mechanika tworzy również Kartę remontów maszyn. W ramach tej karty określa się cykl remontowy oraz opracowuje plan przeglądów i napraw. W niektórych przedsiębiorstwach wykorzystywana jest jedna karta, która zawiera zarówno informacje dotyczące maszyny, jak i dane związane z przeprowadzanymi remontami.
Zasady użytkowania bezpieczeństwa maszyn
Wpływ na jakość oraz wydajność pracy stanowi istotny czynnik, jakim jest bezpieczeństwo oraz higiena pracy. Pracodawca ponosi obowiązek stworzenia odpowiednich i higienicznych warunków pracy. Operator, czyli bezpośredni użytkownik maszyny, ma obowiązek w pełni przestrzegać obowiązujących przepisów w tym zakresie. Tego rodzaju przepisy zwykle są formułowane w sposób zwięzły poprzez wydawanie instrukcji. W tym kontekście ważne są instrukcje dotyczące bezpieczeństwa i higieny pracy (BHP), zwłaszcza te dotyczące użytkowania określonych urządzeń i maszyn, znane jako instrukcje stanowiskowe, dedykowane operatorom.
Kluczowym elementem w ocenie bezpiecznego użytkowania maszyn jest analiza ryzyka zawodowego związanego z danym stanowiskiem pracy. W związku z tym dla każdego stanowiska przygotowywana jest dokumentacja oceny ryzyka.
Typowy schemat oceny ryzyka zawodowego obejmuje trzy główne etapy:
Wszystkie te etapy mają na celu zapewnienie bezpiecznych warunków pracy oraz minimalizację potencjalnych zagrożeń zawodowych.
Przykładowe znaki:
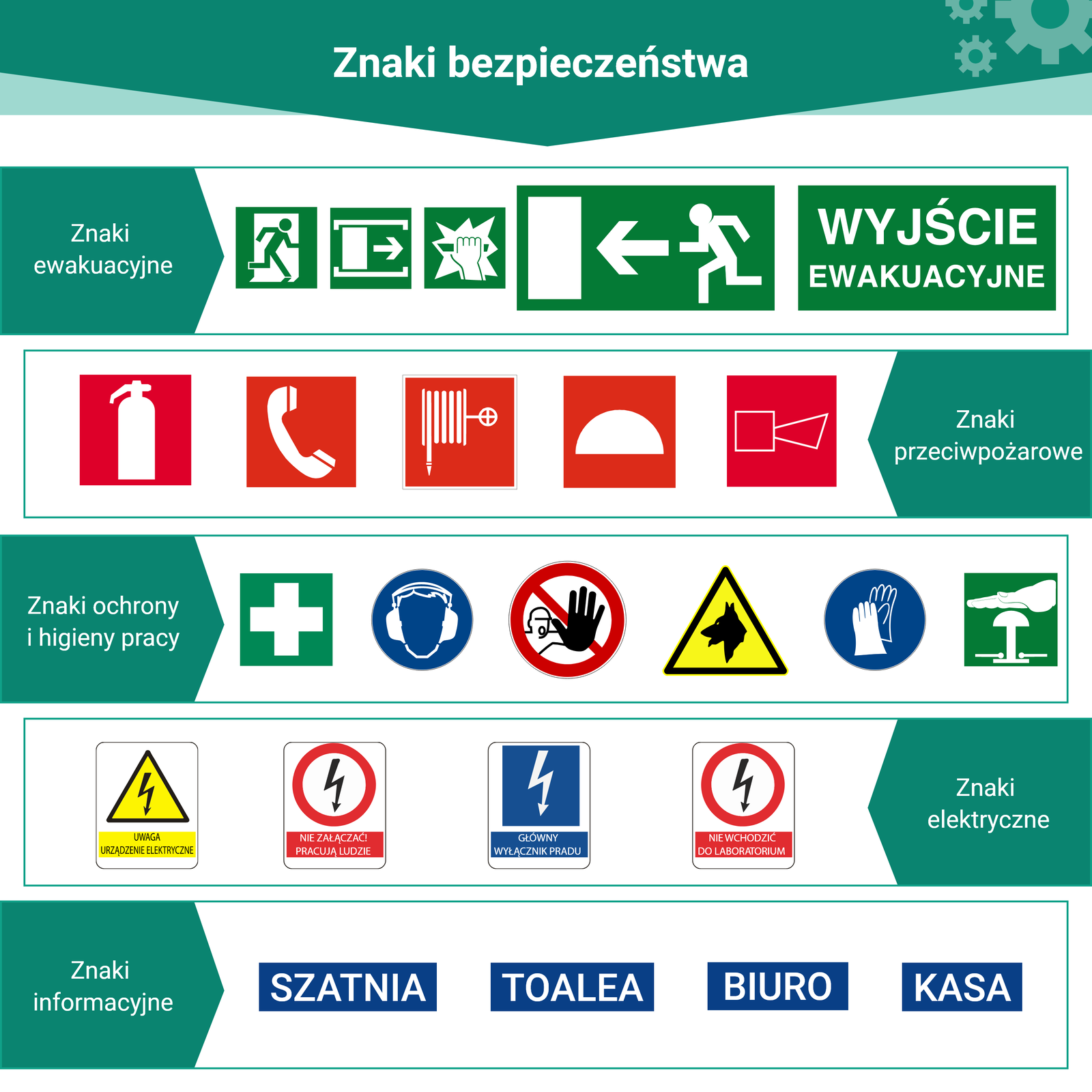
Powrót do spisu treściPowrót do spisu treści
Obsługa maszyn i urządzeń
Rodzaje obsługi
Obsługa maszyn i urządzeń to proces związany z utrzymaniem lub przywracaniem obiektom technicznym ich zdolności do użytku w określonym czasie. W zależności od celu obsługi można wyróżnić obsługę:
jednokrotną i wielokrotną,
techniczną,
organizacyjną.
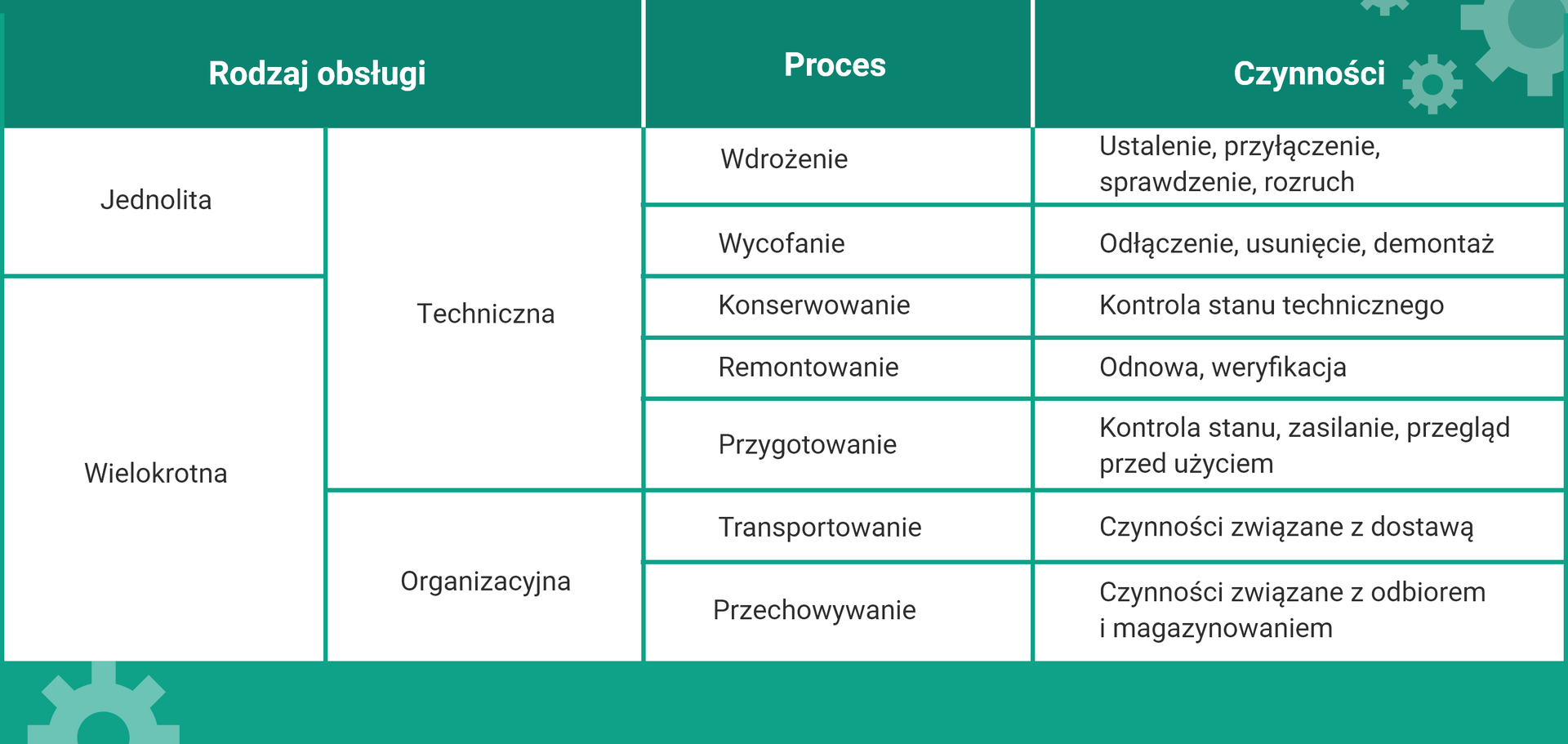
Utrzymanie maszyn w ruchu
Użytkowanie maszyn powoduje ich zużywanie. Czas pracy zależy od sprawności maszyny, co wiąże się z ich przeglądami technicznymi oraz naprawami. W trakcie napraw następują przestoje, które można podzielić na:
przestój planowany – planowane przerwanie pracy wynikające z planów naprawczych maszyn i urządzeń;
przestój nieplanowany – okres, w którym dany obiekt techniczny nie funkcjonuje z powodu awarii, uszkodzenia lub innego nieoczekiwanego problemu. Jest to sytuacja, która może powodować znaczne straty finansowe, spowolnienie produkcji, zmniejszenie wydajności i niekorzystny wpływ na działanie całego procesu produkcyjnego lub operacyjnego. Przestoje nieplanowane zazwyczaj występują wtedy, gdy maszyny lub urządzenia ulegają awariom, wymagają naprawy lub konserwacji, co prowadzi do nieplanowanego przerywania normalnego procesu pracy.
Aby zapobiec przestojom nieplanowanym w obsłudze maszyn i urządzeń, można zastosować kilka strategii:
W skrócie – przestoje nieplanowane w obsłudze maszyn i urządzeń są kosztowne i mogą zakłócić działalność firmy. Zapobieganie im wymaga regularnej konserwacji, monitorowania, szkolenia personelu i właściwego planowania działań, aby utrzymać maszyny w optymalnym stanie pracy.
Obsługa codzienna
Taka obsługa obejmuje następujące czynności:
czystość maszyn,
smarowanie mechanizmów i połączeń oraz regulacji,
działanie mechanizmów jezdnych,
ogólne bezpieczeństwo pracy.
Obsługa sezonowa
Taka obsługa dotyczy maszyn pracujących w różnych środowiskach. Obejmuje następujące aspekty:
sprawdzenie stanu gotowości technicznej,
sprawdzenie stanu placów,
odnowienie uszkodzonych elementów,
odnowienie uszkodzonych elementów,
sprawdzenie pomieszczeń służących do przechowywania obiektów.
Obsługa zabezpieczająca
Taka obsługa to inaczej konserwacja. Zapewnia przydatność użytkową maszyn przez planowane jej zabezpieczenie przed oddziaływaniem czynników zewnętrznych, takich jak korozja.
Obsługa diagnostyczna
Taka obsługa polega na określeniu aktualnego stanu technicznego maszyny. Wyniki pozwalają przewidzieć dalszy proces użytkowania, a zatem zaplanować przyszłe naprawy.
Obsługa gwarancyjna
Obsługa ta w czasie, w którym producent gwarantuje działanie maszyny, pozwala na utrzymanie przydatności maszyny do działania. Taka obsługą zajmuje się autoryzowany serwis.
Obsługa okresowa
Do takiej obsługi należą procesy wykonywane zgodnie z zaplanowanym harmonogramem. Obejmuje ona następujące czynności:
częściowy demontaż,
czyszczenie oraz mycie,
przeprowadzanie pomiarów zespołów i podzespołów,
przegląd techniczny elementów maszyny,
regulowanie pracy maszyny,
określenie zużycia,
usuwanie drobnych uszkodzeń,
wykonywanie czynności związanych z obsługą codzienną.
Remont bieżący
Proces polegający na usunięciu zużycia i przywróceniu maszynie jej stuprocentowej sprawności.
Remont bieżący obejmuje:
czynności wykonywane podczas obsługi,
wymianę lub naprawę często zużywających się elementów.
Zakres czynności podczas remontu bieżącego zależy od:
skomplikowania budowy maszyny,
warunków eksploatacyjnych,
metod remontów,
przeprowadzonych przeglądów.
Remont średni
Ma większy wymiar niż remont bieżący, a podczas jego wykonywania następuje wymiana ważniejszych elementów maszyny. Koszt takiego remontu nie powinien przekraczać 50% wartości odtworzeniowej maszyny.
Remont średni obejmuje:
wymianę zużytych łożysk tocznych,
szlifowanie czopów wałków,
skrobanie i pasowanie łożysk ślizgowych,
regenerację powierzchni ciernych, śrub itd.,
naprawę pompek, napędów itd.,
regenerację elementów napędów hydraulicznych,
wymianę zużytych części,
sprawdzenie skuteczności ochrony przed porażeniem,
kontrolę urządzeń BHP,
montaż oraz próby.
Remont średni
Jest to tak zwany remont główny polegający na naprawie oraz wymianie elementów, które obniżyły swoją zdolność użytkową przez długotrwałe używanie maszyny.
Remont kapitalny obejmuje trzy główne rodzaje prac:
Rodzaj 1 – przygotowawcze:
przegląd,
demontaż,
sporządzenie protokołu.
Rodzaj 2 – remontowy:
szlifowanie i podszlifowanie odpowiednich elementów, np. powierzchni prowadnic,
regenerację elementów,
wymianę uszkodzonych elementów,
remont urządzeń sterujących, instalacji chłodzenia,
remont wyposażenia normalnego,
wymianę elementów elektrycznych,
przegląd i sprawdzenie aparatury kontrolno‑pomiarowej,
montaż oraz próby.
Rodzaj 3 – odbiorowy:
zlecenie,
protokół przeglądu,
rysunki i szkice,
wyniki kontroli.
Modernizacja i adaptacja
Modernizacja – jest to proces odnowy, który ma spowodować przywrócenie lub zwiększenie zdolności produkcyjnej danej maszyny. Głównymi celami modernizacji są:
zwiększenie zdolności produkcyjnej,
zwiększenie wydajności pracy,
obniżenie kosztów eksploatacji,
polepszenie warunków pracy.
Rozróżnia się dwie typy modernizacji:,
cząstkową (niepełną),
kompleksową.
Adaptacja – jest to modernizacja, która jest wykonywana na podstawie planu usprawnień technologii aktualnie produkowanych elementów.
Modernizacja oraz adaptacja mają zapewnić wysoki poziom techniczny produkcji.
Cykl remontowy
Jest to okres czasu między dwoma remontami kapitalnymi, w którym przeprowadza się określoną liczbę zabiegów. Jeżeli nie przewiduje się prac związanych z remontem kapitalnym, to cykl remontowy to czas między dwoma największymi remontami.
Wyróżnia się dwa rodzaje struktur cyklu remontowego:
struktura cyklu 9‑remontowego,
struktura cyklu 6‑remontowego.
Obsługiwanie przechowywanych maszyn i urządzeń
Obsługa przechowywanych maszyn i urządzeń jest kluczowym aspektem zapewnienia ich trwałości, bezpieczeństwa oraz właściwego funkcjonowania. Poniżej przedstawione są szczegóły dotyczące różnych etapów obsługi.
Zasady ogólne
Kryteria wyboru metody przechowywania
Obsługiwanie przed przechowywaniem
Przygotowanie
Przed przechowaniem urządzenia należy je dokładnie oczyścić z zanieczyszczeń, usunąć pozostałości substancji chemicznych oraz sprawdzić, czy nie ma uszkodzeń mechanicznych.Konserwacja
Jeśli istnieją wytyczne producenta dotyczące konserwacji przed przechowywaniem, warto je zastosować. Może to obejmować na przykład smarowanie, wymianę filtrów lub inne czynności mające na celu zachowanie prawidłowego stanu urządzenia.
Obsługiwanie w czasie przechowywania
Monitorowanie stanu
Okresowo należy sprawdzać stan przechowywanych urządzeń. Pozwoli to wykryć ewentualne zmiany, uszkodzenia lub degradację stanu urządzenia.Ochrona przed czynnikami zewnętrznymi
Upewnij się, że przechowywane urządzenia są odpowiednio zabezpieczone przed wilgocią, kurzem, promieniowaniem słonecznym lub innymi czynnikami, które mogą wpłynąć na ich stan.
Obsługiwanie po przechowywaniu
Podsumowując, obsługa przechowywanych maszyn i urządzeń obejmuje serię etapów, które mają na celu zachowanie ich trwałości, bezpieczeństwa i funkcjonalności. Ważne jest, aby przestrzegać wytycznych producenta oraz monitorować stan urządzeń w trakcie przechowywania i po nim, aby zapewnić ich poprawne działanie.
Powrót do spisu treściPowrót do spisu treści