Parametry technologiczne wiercenia
Wykonywanie prac wiertniczych - Wiertacz 811305, Technik wiertnik 311707
Przedstawienie pracy przewodu wiertniczego w trakcie wiercenia otworu
WIZUALIZACJA MODELU W GRAFICE 3D
Spis treści
Wizualizacja modeli 3DWizualizacja modeli 3D
Materiał pomocniczy: Optymalizacja parametru prędkości wiercenia przy założeniu trzech zmiennych parametrów wiercenia: nacisku na narzędzie, prędkości obrotowej narzędzia i strumienia objętości płuczki.Materiał pomocniczy: Optymalizacja parametru prędkości wiercenia przy założeniu trzech zmiennych parametrów wiercenia: nacisku na narzędzie, prędkości obrotowej narzędzia i strumienia objętości płuczki.
Wizualizacja modeli 3D
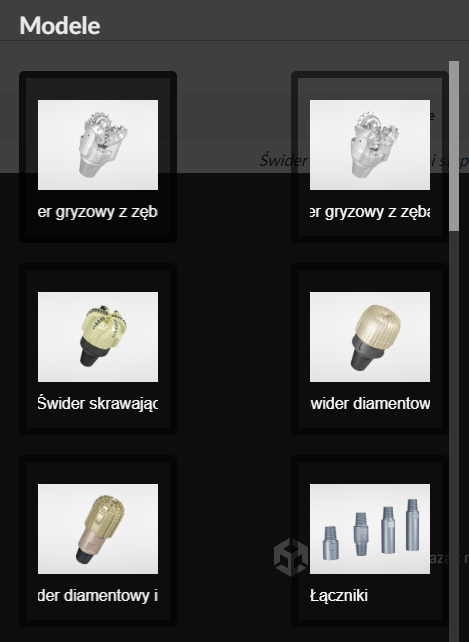
Zasób interaktywny dostępny pod adresem https://zpe.gov.pl/a/DgywnYG5R
Model . Świder gryzowy z zębami słupkowymi.
Na ekranie widać animowany interaktywny model przedstawiający świder gryzowy z zębami słupkowymi. Świder gryzowy jest to narzędzie wiercące pozwalające na zwiercanie powierzchni kołowej otworu wiertniczego. Wykonany jest jako korpus stalowy, wyposażony w rolki z nafrezowanymi zębami lub osadzonymi słupkami z węglika wolframu.
Na modelu zaznaczono kolejnymi cyframi poszczególne elementy urządzenia. Po naciśnięciu danej cyfry rozwija się szczegółowy opis danego elementu wraz z nagraniem audio. Nagranie audio odpowiada tekstowi znajdującemu się w opisie.
Cyfrą oznaczono świder gryzowy z zębami słupkowymi. Świdry gryzowe to najpowszechniej stosowany typ świdrów w wiertnictwie obrotowym. Składają się z zespawanych ze sobą segmentów (łap) wyposażonych w czopy, na których osadzone są obrotowe gryzy uzbrojone w zęby frezowane lub słupki. W segmentach umieszczane są kanały, doprowadzające płuczkę wiertniczą pod gryzy. Kanały zakończone są wymiennymi dyszami porcelanowymi, których zadaniem jest nadanie odpowiedniej prędkości wypływu płuczce wiertniczej. W zależności od konstrukcji świdra, ilość dysz może wynosić , lub . Charakterystyczną cechą świdrów gryzowych są łożyska, umieszczone na czopie, umożliwiające obracanie się gryzów podczas urabiania skały. Sposób, w jaki ułożyskowany jest czop, może się zmieniać w zależności od sił, jakie łożyska będą musiały przenieść. Głównym zadaniem obecności łożyska kulkowego w konstrukcji świdra jest zapobieganie spadnięciu gryza z czopa. W zależności od twardości skał stosuje się gryzy z zębami frezowanymi (do skał miękkich) lub z zębami słupkowymi (do skał twardych). Im skała bardziej miękka tym długość słupków lub zębów jest większa a im twardsza tym mniejsza. Rozmieszczone zęby lub słupki na obwodzie gryzów tworzą wieńce w taki sposób, że wieńce jednego gryza wchodzą między wieńce drugiego gryza. Takie ułożenie powoduje samoczyszczenie się gryzów z urobku. W celu zapobiegnięcia utraty średnicy zewnętrznej powierzchnie boczne segmentów są wzmacniane poprzez napawanie twardym materiałem lub zbrojąc je słupkami z węglików spiekanych. Wyróżniamy świdry jedno-, dwu-, trój- lub czterogryzowe jednak najczęściej stosowane są świdry trójgryzowe. Do danych warunków techniczno - geologicznych świdry gryzowe dobieramy według kodu IADC. Sposób w jaki świder gryzowy urabia zwiercaną skałę to kruszenie.
W rzucie głównym widać urządzenie mechaniczne, którego podstawę stanowi gwintowany czop w kształcie lejka. Na czopie osadzone są trzy łapy zakończone gryzem. Łapa, znajdująca się w centralnej części ekranu, widziana z tyłu ma kształt prostokąta o zaokrąglonych wierzchołach górnych. Łapa, która znajduje się z prawej strony ekranu, widziana z boku, jest w kształcie połowy prostopadłościanu utworzonego poprzez odcięcie jego części w linii przekątnej prostopadłościanu. Na utworzonej w ten sposób powierzchni bocznej łapy osadzone są gryzy. Gryz stanowi półkolistą tarczę, po obwodzie której w formie wieńców osadzone są słupki. Podstawa słupka jest w kształcie cylindra, na szczycie którego znajduje się zaokrąglenie w formie półkuli lub wierzchołka stożka. Widoczne rzędy wieńców na sąsiadujących gryzach wchodzą między siebie. Na szczycie gryza widocznego w centralnej części ekranu znajduje się cyfra .
Pomiędzy podstawami gryzów widać okrągły otwór czyli dyszę, którą doprowadzana jest płuczka.
Ze względu na to, że urządzenie składa się z takich samych segmentów, opis rzutu z prawej strony, z lewej strony oraz z tyłu urządzenia będzie tożsamy opisowi rzutu głównego.
W rzucie z góry widać, że urządzenie zbudowane jest z trzech takich samych segmentów. Osadzone słupki na tarczy gryza rozmieszczone są w formie czterech wieńców. Pomiędzy łapami widać okrągłe otwory, w których znajduje się dysza z płuczką. Na modelu znajdują się trzy takie otwory.
W rzucie dolnym w centralnej części podstawy czopa widać otwór. Na jego dnie widać stalowy element, na powierzchni którego po bo bokach widać wklęsłe stożkowe kształty w rozmieszczeniu trójkątnym. Zaokrąglone wierzchołki wklęsłych kształtów są skierowane w stronę środka podstawy.
Model . Świder gryzowy z zębami frezowymi.
Na ekranie widać animowany interaktywny model przedstawiający świder gryzowy z zębami frezowymi. Świder gryzowy jest to narzędzie wiercące pozwalające na zwiercanie powierzchni kołowej otworu wiertniczego. Wykonany jest jako korpus stalowy, wyposażony w rolki z nafrezowanymi zębami lub osadzonymi słupkami z węglika wolframu.
Na modelu zaznaczono kolejnymi cyframi poszczególne elementy urządzenia. Po naciśnięciu danej cyfry rozwija się szczegółowy opis danego elementu wraz z nagraniem audio. Nagranie audio odpowiada tekstowi znajdującemu się w opisie.
Cyfrą oznaczono świder gryzowy z zębami frezowymi. Świdry gryzowe to najpowszechniej stosowany typ świdrów w wiertnictwie obrotowym. Składają się z zespawanych ze sobą segmentów (łap) wyposażonych w czopy, na których osadzone są obrotowe gryzy uzbrojone w zęby frezowane lub słupki. W segmentach umieszczane są kanały, doprowadzające płuczkę wiertniczą pod gryzy. Kanały zakończone są wymiennymi dyszami porcelanowymi, których zadaniem jest nadanie odpowiedniej prędkości wypływu płuczce wiertniczej. W zależności od konstrukcji świdra, ilość dysz może wynosić , lub . Charakterystyczną cechą świdrów gryzowych są łożyska, umieszczone na czopie, umożliwiające obracanie się gryzów podczas urabiania skały. Sposób w jaki ułożyskowany jest czop może się zmnieniać w zależności od sił jakie łożyska będą musiały przenieść. Głównym zadaniem obecności łożyska kulkowego w konstrukcji świdra jest zapobieganie spadnięciu gryza z czopa. W zależności od twardości skał stosuje się gryzy z zębami frezowanymi (do skał miękkich) lub z zębami słupkowymi (do skał twardych). Im skała bardziej miękka tym długość słupków lub zębów jest większa a im twardsza tym mniejsza. Rozmieszczone zęby lub słupki na obwodzie gryzów tworzą wieńce w taki sposób, że wieńce jednego gryza wchodzą między wieńce drugiego gryza. Takie ułożenie powoduje samoczyszczenie się gryzów z urobku. W celu zapobiegnięcia utraty średnicy zewnętrznej powierzchnie boczne segmentów są wzmacniane poprzez napawanie twardym materiałem lub zbrojąc je słupkami z węglików spiekanych. Wyróżniamy świdry jedno-, dwu-, trój- lub czterogryzowe jednak najczęściej stosowane są świdry trójgryzowe. Do danych warunków techniczno - geologicznych świdry gryzowe dobieramy według kodu IADC. Sposób w jaki świder gryzowy urabia zwiercaną skałę to kruszenie.
W rzucie głównym widać urządzenie mechaniczne, którego podstawę stanowi gwintowany czop w kształcie lejka. Na czopie osadzone są trzy łapy zakończone gryzem. Łapa, znajdująca się w centralnej części ekranu, widziana z tyłu ma kształt prostokąta o zaokrąglonych wierzchołach górnych. Łapa, która znajduje się z prawej strony ekranu, widziana z boku, jest w kształcie połowy prostopadłościanu utworzonego poprzez odcięcie jego części w linii przekątnej prostopadłościanu. Na utworzonej w ten sposób powierzchni bocznej łapy osadzone są gryzy. Gryz stanowi półkolistą tarczę, po obwodzie której w formie wieńców osadzone są zęby frezowe. Ząb frezowy jest w kształcie graniastosłupa trójkątnego czyli graniastosłupa posiadającego w podstawie trójkąt. Graniastosłup jest osadzony na tarczy w sposób, w którym podstawy trójkątne bryły są widziane jako ściany boczne. Widoczne rzędy wieńców na sąsiadujących gryzach wchodzą między siebie. Na szczycie gryza widocznego w centralnej części ekranu znajduje się cyfra .
Pomiędzy podstawami gryzów widać okrągły otwór czyli dyszę, którą doprowadzana jest płuczka.
Ze względu na to, że urządzenie składa się z takich samych segmentów, opis rzutu z prawej strony, z lewej strony oraz z tyłu urządzenia będzie tożsamy opisowi rzutu głównego.
W rzucie z góry widać, że urządzenie zbudowane jest z trzech takich samych segmentów. Osadzone zęby frezowe na tarczy gryza rozmieszczone są w formie czterech wieńców. Pomiędzy łapami widać okrągłe otwory, w których znajduje się dysza z płuczką. Na modelu znajdują się trzy takie otwory.
W rzucie dolnym w centralnej części podstawy czopa widać otwór. Na jego dnie widać stalowy element, na powierzchni którego po bo bokach widać wklęsłe stożkowe kształty w rozmieszczeniu trójkątnym. Zaokrąglone wierzchołki wklęsłych kształtów są skierowane w stronę środka podstawy.
Model . Świder skrawający (PDC).
Na ekranie widać animowany interaktywny model przedstawiający świder skrawający (PDC). Świder PDC jest to narzędzie wiercące pozwalające na zwiercanie powierzchni kołowej otworu wiertniczego. Wykonany jest jako korpus stalowy, z naniesiona matrycą wraz z zamocowanymi ostrzami zakończonymi płytkami z polikrystalicznego diamentu (Polycrystalic diamond cutters). Świder ten urabia skałę przez skrawanie.
Na modelu zaznaczono kolejnymi cyframi poszczególne elementy urządzenia. Po naciśnięciu danej cyfry rozwija się szczegółowy opis danego elementu wraz z nagraniem audio. Nagranie audio odpowiada tekstowi znajdującemu się w opisie.
Cyfrą oznaczono świder skrawający (PDC). Są to świdry zaliczane do świdrów diamentowych wyposażone w ostrza z polikrystalicznych diamentów syntetycznych. Charakteryzują się stalowym lub matrycowym kadłubem z węglika wolframu, a także segmentowym, żebrowym lub skrzydłowym rozmieszczeniem ostrzy. Ostrza do kadłubów świdra PDC są przyspawane twardym spiekiem w specjalnych do tego przeznaczonych gniazdach. Wyróżnia się trzy główne kształty profilu roboczej powierzchni kadłuba świdrów: płaską lub lekko wygiętą, stożkową lub bardzo głęboko wygiętą oraz paraboliczną. Na jakość pracy świdra typu PDC ma wpływ wysokość wystawania ostrzy nad powierzchnię kadłuba. Im większa wysokość tym lepsze oczyszczanie dna otworu ze zwiercin jednak mniejsza wytrzymałość na nacisk osiowy. Tego typu świdry zwiercają urabianą skałę poprzez skrawanie.
W rzucie głównym widać urządzenie mechaniczne, którego podstawą jest czarny gwintowany czop w kształcie lejka. Przedłużenie czopa stanowi czarny cylindryczny element, na którym osadzony jest kadłub o powierzchni lekko wygiętej. Kadłub składa się z wypukłych segmentów o grubszej podstawie i zaokrąglonej lewej stronie. Po prawej stronie segmentów widać wypukłe półokrągłe gniazda, w których osadzone są stożkowe cylindryczne ostrza. W zależności od segmentu znajduje się w nim od sześciu do dziewięciu ostrzy. Przy podstawie każdego segmentu kadłuba znajduje się dziewięć nitów. Jest to zbrojenie wzmacniające. Nity są ułożone w dwóch pionowych rzędach. Pierwszy zawiera trzy elementy, drugi dziewięć elementów.
Na podstawie kadłuba pomiędzy segmentami z ostrzami widać okrągłe otwory z dyszą płuczkową. Dodatkowo pomiędzy widocznymi z przodu segmentami znajduje się cyfra .
Ze względu na to, że urządzenie składa się z takich samych segmentów, opis rzutu z prawej strony, z lewej strony oraz z tyłu urządzenia będzie tożsamy opisowi rzutu głównego.
W rzucie z góry widać, że urządzenie zbudowane jest z sześciu takich samych segmentów z ostrzami, które z góry przybierają kształt spirali. Na całej powierzchni kadłuba widać sześć okrągłych otworów, w których znajduje się dysza z płuczką. Otworu znajdują się w okrągłych zagłębieniach, w których wycięty jest kształt w formie znaku plus. W środka znaku znajduje się otwór z dyszą.
W rzucie dolnym w centralnej części podstawy czopa widać otwór. Przez otwór widać wnętrze świdra wraz z otworami, przez które dostarczana jest płuczka.
Model . Świder diamentowy ziarnisty.
Na ekranie widać animowany interaktywny model przedstawiający świder diamentowy ziarnisty. Świder diamentowy jest to narzędzie wiercące pozwalające na zwiercanie powierzchni kołowej otworu wiertniczego. Wykonany jest jako korpus stalowy, z naniesioną matrycą wraz diamentami.
Na modelu zaznaczono kolejnymi cyframi poszczególne elementy urządzenia. Po naciśnięciu danej cyfry rozwija się szczegółowy opis danego elementu wraz z nagraniem audio. Nagranie audio odpowiada tekstowi znajdującemu się w opisie.
Cyfrą oznaczono świder diamentowy ziarnisty. Świdry diamentowe ziarniste mają osadzone w powierzchniach roboczych i bocznych całe kryształy diamentów. Większość diamentów osadza się w powierzchni czołowej świdra, tak aby pokrywały one całkowicie dno otworu. Schemat ich rozmieszczenia jest różny dla różnych rozwiązań konstrukcyjnych i może być: promieniowy, spiralny lub koncentryczny. Ważnym parametrem opisującym świdry ziarniste jest stopień odkrycia opisujący jaka część diamentu znajduje się poza matrycą. Zazwyczaj jest to od jednej ósmej średnicy diamentu (skały twarde i spękane) do jednej trzeciej dla skał miękkich.
W rzucie głównym widać urządzenie mechaniczne, którego podstawą jest czarny gwintowany czop w kształcie lejka. Przedłużenie czopa stanowi czarny cylindryczny element w kształcie śruby, na którym osadzony złoty kadłub świdra. Na powierzchni kadłuba widać równomiernie rozmieszczone wypukłe półkoliste punkty, które stanowią kryształy diamentów. Diamenty osadzone są w segmentach składających się z trzech cienkich prostokątnych elementów, po których znajduje się kolejnych osiem podłużnych prostokątnych kształtów. W prostokątach diamenty osadzone są w dwóch rzędach, które ciągną się od podstawy korpusu po szczyt świdra w przypadku serii ośmiu prostokątów lub od połowy wysokości głowicy świdra do jej szczytu w przypadku serii trzech prostokątów. Pod serią trzech prostokątów na powierzchni korpusu znajduje się cyfra .
Ze względu na to, że urządzenie składa się z takich samych segmentów, opis rzutu z prawej strony, z lewej strony oraz z tyłu urządzenia będzie tożsamy opisowi rzutu głównego.
W rzucie z góry widać, że diamenty ulegają zagęszczeniu w obszarach korpusu znajdujących się coraz bliżej środka koronki świdra. W centralnej części koronki znajduje się otwór uformowany z trzech kształtów o formie strzałek, których grot zwrócony jest w stronę środka.
W rzucie dolnym w centralnej części podstawy czopa widać otwór. Przez otwór widać wnętrze świdra wraz z otworami, przez które dostarczana jest płuczka.
Model . Świder diamentowy impregnowany.
Na ekranie widać animowany interaktywny model przedstawiający świder diamentowy impregnowany. Świder diamentowy impregnowany jest narzędzie wiercące pozwalające na zwiercanie powierzchni kołowej otworu wiertniczego. Wykonany jest jako korpus stalowy, z naniesiona matrycą wraz z proszkiem diamentowym (powierzchnia sztuk na karat).
Na modelu zaznaczono kolejnymi cyframi poszczególne elementy urządzenia. Po naciśnięciu danej cyfry rozwija się szczegółowy opis danego elementu wraz z nagraniem audio. Nagranie audio odpowiada tekstowi znajdującemu się w opisie.
Cyfrą oznaczono świder diamentowy impregnowany. Świdry diamentowe impregnowane, w odróżnieniu od ziarnistych, posiadają pył diamentowy jako element skrawający. Warstwa robocza powstaje poprzez zmieszanie diamentów z proszkiem twardego metalu (stanowiącym ścieralną matrycę) i poddaniu mieszanki obróbce cieplnej. Uzyskuje się wówczas jednolicie rozmieszczone, drobne diamenty na pewnej długości części roboczej narzędzia. Podczas pracy zużyte diamenty wypadają, a matryca ściera się odsłaniając kolejne warstwy diamentów.
W rzucie głównym widać urządzenie mechaniczne, którego podstawą jest czarny gwintowany czop w kształcie lejka. Przedłużenie czopa stanowi miedziany cylindryczny element w kształcę śruby z dwoma kwadratowymi wycięciami przy podstawie od strony czopa. Na górze elementu osadzony jest złoty kadłub koronki świdra. Na powierzchni kadłuba widać równomiernie rozmieszczone żłobienia, które oddzielają prostokątne wypukłe elementy. Góra prostokątnego elementu ulega pofalowaniu oraz zwężaniu wraz ze zmniejszeniem odległości do szczytu koronki. Widoczny segment składa się z trzech prostokątnych wypukłych kształtów biegnących od podstawy koronki doi jej szczytu oraz jednego prostokątnego kształtu biegnącego od połowy wysokości koronki do jej szczytu. Pod krótszym elementem na kadłubie koronki jest cyfra .
Ze względu na to, że urządzenie składa się z takich samych segmentów, opis rzutu z prawej strony, z lewej strony oraz z tyłu urządzenia będzie tożsamy opisowi rzutu głównego.
W rzucie z góry widać, że koronka składa się z trzech segmentów. Trzy pofalowane wypukłe elementy łączą się ze sobą w środku koronki. Formują w ten sposób ułożenie trójkąta. Pomiędzy utworzonymi w ten sposób ramionami znajdują się trzy po trzy wypukłe pofalowane elementy, które biegną w stronę środka koronki, ale nie łączą się z nim ani ze sobą. Pomiędzy elementami widać żłobienia, a w górnej części w rejonie środka koronki są puste przestrzenie, przez które widać szare wnętrze świdra. W rzucie dolnym w centralnej części podstawy czopa widać otwór. Przez otwór widać wnętrze świdra wraz z otworami oraz górę koronki.
Model . Łączniki.
Na ekranie widać animowany interaktywny model przedstawiający cztery szare łączniki. Łącznik jest to element przewodu wiertniczego posiadający na dwóch końcach różnego typu i rozmiaru połączenia gwintowe. Dzięki niemu możliwe jest skręcenie na przykład: rur płuczkowych i rur HWDP posiadających inne połączenia gwintowe.
Na modelu zaznaczono kolejnymi cyframi poszczególne elementy łącznika. Po naciśnięciu danej cyfry rozwija się szczegółowy opis danego elementu wraz z nagraniem audio. Nagranie audio odpowiada tekstowi znajdującemu się w opisie.
Cyfrą oznaczono łączniki. Łączniki służą do łączenia ze sobą różnych elementów przewodu wiertniczego, które mogą mieć nie tylko różną średnicę wewnętrzną i zewnętrzną ale również różne połączenia gwintowe. Połączenia gwintowe łączników wykonywane są w trzech zasadniczych typach: Z wąskim przelotem WP (REG), z szerokim przelotem SP (FH), z jednakowym przelotem JP (IF). W przewodzie wiertniczym łączniki występują między graniatką a rurami płuczkowymi, rurami płuczkowymi a obciążnikami, między obciążnikami a narzędziem. Stosowane są także do łączenia takich elementów jak nożyc wiertniczych, amortyzatora drgań itp. Łączniki wykonywane są w trzech typach: czop – mufa, czop – czop, mufa – mufa.
Widoczne na ekranie cztery szare łączniki są w rzucie pionowym elementami symetrycznymi. Pierwszy łącznik znajdujący się po lewej stronie ekranu zbudowany jest z cylindrycznej podłużnej podstawy. Podstawa zakończona jest gwintowanym połączeniem w kształcie zwężającego się do góry lejka. Na górze korpusu podstawy znajduje się żłobienie o kształcie wklęsłego kwadratu. Nad żłobieniem znajduje się cyfra .
Drugi łącznik widoczny po lewej stronie ekranu jest niższy od wcześniej opisywanego łącznika. Łącznik zbudowany jest z cylindrycznej podłużnej podstawy. Podstawa zakończona jest gwintowanym połączeniem w kształcie zwężającego się do góry lejka. Na górze korpusu podstawy znajduje się żłobienie o kształcie wklęsłego kwadratu.
Trzeci łączni znajdujący się w centralnej części ekranu jest nieznacznie niższy od łącznika numer dwa. Łącznik zbudowany jest z cylindrycznej podłużnej podstawy. Podstawa po obu stronach zakończona jest gwintowanym połączeniem w kształcie zwężającego się lejka. Na górze korpusu podstawy znajduje się żłobienie o kształcie wklęsłego kwadratu.
Czwarty łącznik widoczny po prawej stronie ekranu jest najmniejszy ze wszystkich łączników. Łącznik zbudowany jest z cylindrycznej podłużnej podstawy. Podstawa zakończona jest gwintowanym połączeniem w kształcie zwężającego się do góry lejka. Na górze korpusu podstawy znajduje się żłobienie o kształcie wklęsłego kwadratu.
Ze względu na to, że urządzenie składa się z takich samych segmentów, opis rzutu z prawej strony, z lewej strony oraz z tyłu urządzenia będzie tożsamy opisowi rzutu głównego.
W rzucie górnym i dolnym widać, że łączniki są puste w środku to znaczy widać przelot łącznika.
Model . Koronka skrawająca.
Na ekranie widać animowany interaktywny model przedstawiający koronkę skrawającą. Koronka skrawająca jest to narzędzie wiercące urabiające na zasadzie skrawania skały. Zwyczajowo koronkami skrawającymi nazywa się koronki wiertnicze wyposażone w ostrza z węglika wolframu lub ze stali stopowych.
Na modelu zaznaczono kolejnymi cyframi poszczególne elementy koronki. Po naciśnięciu danej cyfry rozwija się szczegółowy opis danego elementu wraz z nagraniem audio. Nagranie audio odpowiada tekstowi znajdującemu się w opisie.
Cyfrą oznaczono koronkę skrawającą. Koronki typu PDC ze względu na możliwość formowania ostrzy różnej wielkości i konfiguracji występują w wielu formach, różniących się kształtem matrycy, ilością i wielkością ostrzy lub systemem płukania. Dodatkową zaletą koronek PDC jest brak łożysk i innych ruchomych elementów zmniejszających żywotność narzędzi oraz zwiększających prawdopodobieństwo awarii wiertniczej. Uzyskuje się również większe przewierty oraz większe uzyski w porównaniu z konwencjonalnymi narzędziami skrawającymi.
W rzucie głównym podstawę koronki stanowi szary element gwintowany w kształcie zwężającego się do dołu lejka. U góry podstawy koronki znajduje się niebieski element, na powierzchni którego widać żłobienia w kształcie cylindra o zaokrąglonym dnie od strony podstawy. Na żłobieniu znajduje się cyfra . Pomiędzy cylindrycznymi żłobieniami widać zęby o kształcie graniastosłupa z lekko ścięta powierzchnią górną. Zęby zamontowane są naprzemiennie po stronie wewnętrznej i zewnętrznej koronki. Podstawa zęba przymontowana do koronki ma zaokrąglone dno.
Ze względu na to, że urządzenie składa się z takich samych segmentów, opis rzutu z prawej strony, z lewej strony oraz z tyłu urządzenia będzie tożsamy opisowi rzutu głównego.
W rzucie górnym widać, że zęby osadzone na szczycie koronki mają podstawę ośmiokąta foremnego. Zęby zewnętrzne i wewnętrzne są umieszczone do połowy swojej szerokości w obudowie koronki. Góra koronki jest szersza od podstawy koronki. Zarówno w rzucie dolnym jak i górnym widać przelot koronki.
Model . Koronka skrawająca PDC
Na ekranie widać animowany interaktywny model przedstawiający koronkę skrawającą PDC. Koronka skrawająca z ostrzami PDC jest to narzędzie wiercące pozwalające na zwiercanie powierzchni pierścieniowej otworu wiertniczego. Wykonana jest jako korpus stalowy, z naniesiona matrycą wraz z zamocowanymi ostrzami zakończonymi płytkami z polikrystalicznego diamentu (Polycrystalic diamond cutters). Koronka ta urabia skałę przez skrawanie.
Na modelu zaznaczono kolejnymi cyframi poszczególne elementy koronki. Po naciśnięciu danej cyfry rozwija się szczegółowy opis danego elementu wraz z nagraniem audio. Nagranie audio odpowiada tekstowi znajdującemu się w opisie.
Cyfrą oznaczono koronkę skrawającą PDC. Koronki typu PDC ze względu na możliwość formowania ostrzy różnej wielkości i konfiguracji występują w wielu formach, różniących się kształtem matrycy, ilością i wielkością ostrzy lub systemem płukania. Dodatkową zaletą koronek PDC jest brak łożysk i innych ruchomych elementów zmniejszających żywotność narzędzi oraz zwiększających prawdopodobieństwo awarii wiertniczej. Uzyskuje się również większe przewierty oraz większe uzyski w porównaniu z konwencjonalnymi narzędziami skrawającymi.
W rzucie głównym podstawę koronki stanowi szary cylindryczny element o płaskiej powierzchni zewnętrznej. U góry podstawa łączy się jasno szarą koronką, na powierzchni której znajdują się wypukłe elementy w kształcie rombu. Góra rąbu ulega zaokrągleniu i biegnie po krawędzi górnej koronki do jej wnętrza. Na zaokrągleniu znajdują się szare stożkowe elementy, w których osadzone są czarne cylindryczne ostrza skrawające. Na górnej krawędzi koronki, po jej obwodzie biegną ostrza skierowane w sposób prostopadły do koronki. Po dwa takie ostrza znajdują się pomiędzy wypukłymi elementami.
Na ścianie bocznej koronki, pomiędzy wypukłymi elementami znajduje się cyfra .
Ze względu na to, że urządzenie składa się z takich samych segmentów, opis rzutu z prawej strony, z lewej strony oraz z tyłu urządzenia będzie tożsamy opisowi rzutu głównego.
W rzucie górnym widać, że urządzenie można podzielić na siedem segmentów, które przedzielają zaokrąglone kształty z ostrzami. Na zaokrągleniu widocznych jest siedem ostrzy skrawających. Zarówno w rzucie dolnym jak i górnym widać przelot koronki. Na podstawie wewnętrznej koronki widać żłobienia, które stanowią połączenie gwintowane.
Model . Koronka diamentowa ziarnista
Na ekranie widać animowany interaktywny model przedstawiający koronkę diamentową ziarnistą. Koronka diamentowa ziarnista jest to narzędzie wiercące pozwalające na zwiercanie powierzchni pierścieniowej otworu wiertniczego. Wykonana jest jako korpus stalowy, z naniesioną matrycą wraz diamentem.
Na modelu zaznaczono kolejnymi cyframi poszczególne elementy koronki. Po naciśnięciu danej cyfry rozwija się szczegółowy opis danego elementu wraz z nagraniem audio. Nagranie audio odpowiada tekstowi znajdującemu się w opisie.
Cyfrą oznaczono koronkę diamentową ziarnistą. Główne elementy konstrukcyjne koronek diamentowych to korpus zakończony gwintem umożliwiającym połączenie narzędzia z rdzeniówką oraz matryca, w której osadzone są diamenty. Podstawowym zadaniem matrycy jest utrzymanie diamentów w warunkach zmiennych naprężeń występujących podczas rdzeniowania. Matryce wykonywane są zazwyczaj z węglików spiekanych ze względu na twardość oraz współczynnik rozszerzalności cieplnej tego materiału, który powinien być zbliżony do rozszerzalności cieplnej diamentów. Przeciwdziała to przedwczesnemu wypadaniu diamentów z matrycy.
W rzucie głównym podstawę koronki stanowi czarny cylindryczny element o płaskiej powierzchni zewnętrznej. U góry podstawa łączy się ze złotą koronką, na powierzchni której znajdują się cienkie żłobienia pomiędzy wypukłymi elementami w kształcie prostokątnym. Prostokątne elementy ulegają zwężeniu w górnej części koronki. Dodatkowo nad krawędzią koronki ulegają zaokrągleniu. Na pojedynczym prostokątnym elemencie od jego podstawy do połowy jego wysokości biegną trzy wypukłe, równoległe względem siebie cienkie półcylindryczne kształty. Nad nimi w trzech rzędach pionowo do góry biegną małe wypukłe elementy o kształcie półkuli.
Koronkę można podzielić na cztery segmenty. Granicę stanowi powierzchnia płaska koronki, nad którą są dwa krótkie prostokątne elementy z trzema rzędami niewielkich wypukłych półkul. W segmencie znajduje się dziesięć pełnych prostokątnych kształtów. Na jednym z pełnych prostokątnych kształtów znajduje się cyfra .
W rzucie górnym widać, że prostokątne elementy zawężają się. Następnie zawężające sąsiadujące ze sobą prostokąty ulegają połączeniu w kształt przypominający trapez. Elementy widoczne u góry koronki biegną przez krawędź górną do wewnątrz. Koronka na środku ma otwór przelotowy.
W rzucie dolnym widać, że przy podstawie koronka ma połączenie gwintowane. Dodatkowo średnica podstawy jest większa od średnicy góry koronki.
W rzucie bocznym z lewej, prawej strony oraz z tyłu opis jest tożsamy do opisu rzutu głównego.
Model . Koronka diamentowa impregnowana
Na ekranie widać animowany interaktywny model przedstawiający koronkę diamentową impregnowaną. Koronka diamentowa impregnowana jest to narzędzie wiercące pozwalające na zwiercanie powierzchni pierścieniowej otworu wiertniczego. Wykonana jest jako korpus stalowy, z naniesiona matrycą wraz z proszkiem diamentowym (powierzchnia sztuk na karat).
Na modelu zaznaczono kolejnymi cyframi poszczególne elementy koronki. Po naciśnięciu danej cyfry rozwija się szczegółowy opis danego elementu wraz z nagraniem audio. Nagranie audio odpowiada tekstowi znajdującemu się w opisie.
Cyfrą oznaczono koronkę diamentową impregnowaną. Główne elementy konstrukcyjne koronek diamentowych to korpus zakończony gwintem umożliwiającym połączenie narzędzia z rdzeniówką oraz matryca, w której osadzone są diamenty. Podstawowym zadaniem matrycy jest utrzymanie diamentów w warunkach zmiennych naprężeń występujących podczas rdzeniowania. Matryce wykonywane są zazwyczaj z węglików spiekanych ze względu na twardość oraz współczynnik rozszerzalności cieplnej tego materiału, który powinien być zbliżony do rozszerzalności cieplnej diamentów. Przeciwdziała to przedwczesnemu wypadaniu diamentów z matrycy.
W rzucie głównym podstawę koronki stanowi czarny cylindryczny element o płaskiej powierzchni zewnętrznej. U góry korpus cylindra łączy się z jasnoszarą koronką o płaskiej powierzchni. Na górze koronki widać zęby w kształcie graniastosłupów o podstawie prostokąta. Na obu ścianach bocznych zęba od strony zewnętrznej koronki znajdują się dwa czarne równoległe względem siebie otwory. Otwory biegną pionowo w górę przez całą długość zęba. U góry koronki znajduje się cyfra .
W rzucie górnym widać, że koronka ma dziewięć zębów. Prostokątne czarne otwory widoczne są również na dolnej części ostrza to znaczy od strony zewnętrznej krawędzi oraz pomiędzy zębami. W środku koronka jest pusta i widać jej przelot.
W rzucie dolnym widać, że przy podstawie koronka ma połączenie gwintowane.
Model . Koronka gryzowa z zębami słupkowymi.
Na ekranie widać animowany interaktywny model przedstawiający koronkę gryzową z zębami słupkowymi. Koronka gryzowa jest to narzędzie wiercące pozwalające na zwiercanie powierzchni pierścieniowej otworu wiertniczego. Wykonana jest jako korpus stalowy, wyposażony w rolki z nafrezowanymi zębami lub osadzonymi słupkami z węglika wolframu. Koronka ta występuje pod zwyczajową nazwą koronka 'zębata'.
Na modelu zaznaczono kolejnymi cyframi poszczególne elementy koronki. Po naciśnięciu danej cyfry rozwija się szczegółowy opis danego elementu wraz z nagraniem audio. Nagranie audio odpowiada tekstowi znajdującemu się w opisie.
Cyfrą oznaczono koronkę gryzową słupkową. Koronki gryzowe niszczą strukturę skały poprzez jej kruszenie w wyniku przemiany momentu obrotowego przewodu na udary i poślizg zębów po dnie otworu. W tego typu rozwiązaniach konstrukcyjnych energia kinetyczna obrotu przemienia się w energię potencjalną o wartości niezbędnej do zniszczenia skały, przez co uzyskuje się efekt urabiania górotworu.
W rzucie głównym widać urządzenie mechaniczne, którego podstawę stanowi płaski czop w kształcie cylindra. Na czopie osadzonych jest sześć łap zakończonych gryzem. Łapa, znajdująca się w centralnej części ekranu, widziana z tyłu ma kształt prostokąta o zaokrąglonych wierzchołach górnych. Łapa, która znajduje się z prawej strony ekranu, widziana z boku, jest w kształcie połowy prostopadłościanu utworzonego poprzez odcięcie jego części w linii przekątnej prostopadłościanu. Na utworzonej w ten sposób powierzchni bocznej łapy osadzone są gryzy. Gryz stanowi półkolistą tarczę, po obwodzie której w formie wieńców osadzone są słupki. Podstawa słupka jest w kształcie cylindra, na szczycie którego znajduje się zaokrąglenie w formie półkuli lub wierzchołka stożka. Widoczne rzędy wieńców na sąsiadujących gryzach wchodzą między siebie. Na szczycie gryza widocznego w centralnej części ekranu znajduje się cyfra . Ze względu na to, że urządzenie składa się z takich samych segmentów, opis rzutu z prawej strony, z lewej strony oraz z tyłu urządzenia będzie tożsamy opisowi rzutu głównego.
W rzucie z góry widać, że urządzenie zbudowane jest z sześciu takich samych segmentów. Osadzone słupki na tarczy gryza rozmieszczone są w formie trzech wieńców. Pomiędzy łapami widać okrągłe otwory, w których znajduje się dysza z płuczką.
W rzucie dolnym w centralnej części podstawy czopa widać otwór. Wewnętrzna powierzchnia czopa przy jego podstawie jest żłobiona czyli posiada połączenie gwintowane.
Model . Rury HWDP
Na ekranie widać animowany interaktywny model przedstawiający rurę HWDP. Rura HWDP (Heavy Weight Drill Pipe) jest to grubościenna rura płuczkowe stanowiąca element zestawu przewodu wiertniczego. Rury te montowane są pomiędzy obciążnikami, a rurami płuczkowymi (w otworze pionowym i kierunkowym), a także między obciążnikami, a zestawem silnika wgłębnego (w otworze kierunkowym). Dzięki swojej budowie (znaczna grubość ścianki, długie zworniki, uzbrojenie zabezpieczające w części środkowej) mają większy ciężar od rur płuczkowych o takich samych wymiarach, są łatwe w marszowaniu, zapewniają stabilność oraz mniejszy kontakt ze ścianą otworu, zwiększają zdolność utrzymania kąta i kierunku przy wierceniu otworów.
Na modelu zaznaczono kolejnymi cyframi poszczególne elementy rury. Po naciśnięciu danej cyfry rozwija się szczegółowy opis danego elementu wraz z nagraniem audio. Nagranie audio odpowiada tekstowi znajdującemu się w opisie.
Cyfrą oznaczono rurę HWDP. Rury HWDP to rury płuczkowe o zwiększonej grubości ścianki, dłuższych zwornikach i uzbrojeniem zabezpieczającym przed wycieraniem w środkowej części. W zestawie przewodu wiertniczego, skręcane są między obciążnikami a właściwymi rurami płuczkowymi co zapewnia większą stabilność dolnej części przewodu wiertniczego.
W widoku głównym widać długi zielony cylindryczny kształt, który składa się z kilku sekcji o różnej średnicy. Podstawę rury stanowi cylindryczny kształt, który następnie ulega dwukrotnie nieznaczącemu zwężeniu. Zwężony cylinder ulega przyłączeniu do szerszego cylindra znajdującego się po środku rury. Środkowa cześć rury jest najprawdopodobniej o takiej samej średnicy jak podstawa. Do góry środkowej części rury przyłączone są takie same elementy cylindryczne jakie były od dolnej środkowej części rury do jej podstawy z tym, że górny element zakończony jest białym lejkowatym kształtem. Lejek zwęża się w kierunku góry. Na górze lejka znajduje się cyfra .
W rzucie bocznym z lewej, prawej strony oraz z tyłu opis jest tożsamy do opisu rzutu głównego.
W rzucie z góry i dołu przekrój rury ma kształt okrągły.
Model . Stabilizator
Na ekranie widać animowany interaktywny model przedstawiający stabilizator. Stabilizatory są elementami zestawu przewodu wiertniczego przeznaczone do utrzymywania dolnej części przewodu wiertniczego w osi otworu. Ze względu na rodzaj połączeń stosuje się dwa rodzaje stabilizatorów: stabilizatory nadświdrowe (z połączeniem mufa x mufa) oraz stabilizatory przewodowe (z połączeniem czop x mufa).
Na modelu zaznaczono kolejnymi cyframi poszczególne elementy stabilizatora. Po naciśnięciu danej cyfry rozwija się szczegółowy opis danego elementu wraz z nagraniem audio. Nagranie audio odpowiada tekstowi znajdującemu się w opisie.
Cyfrą oznaczono stabilizator. Stabilizatory to krótkie elementy rurowe o trzech zbrojnych spiralach, których średnica jest zbliżona do średnicy otworu. Ich rozmieszczenie w przewodzie wiertniczym powinno pokrywać się z punktami ugięcia obciążników podczas wywierania nacisku na narzędzie wiercące. Stabilizują one pracę świdra oraz zmniejszają tendencję narzędzia do krzywienia otworu. Rozmieszczając stabilizatory, w pierwszej kolejności stabilizuje się świder, umieszczając nad nim jeden lub kilka stabilizatorów (stabilizatory nadświdrowe). Rozmieszczenie i liczba pozostałych stabilizatorów zależy od schematu stabilizacji, który przygotowywany jest dla konkretnego otworu wiertniczego.
Na ekranie w widoku głównym widać niebieski cylindryczny element w formie rury. Środkowa cześć rury rozszerza się przybierając kształt gruszki. Na jej powierzchni widać żłobienia o profilu ślimakowym. U góry rury znajduje się cyfra .
W rzucie bocznym z lewej, prawej strony oraz z tyłu opis jest tożsamy do opisu rzutu głównego.
W rzucie z góry i dołu przekrój rury ma kształt okrągły. Z obu stron wewnętrzna strona rury ma żłobienia stanowiące połączenie gwintowane.
Model . Aparat rdzeniowy (standardowy, wrzutowy).
Na ekranie widać animowany interaktywny model przedstawiający aparat rdzeniowy. Aparat rdzeniowy służy do wykonywania wierceń rdzeniowych. Dzięki aparatowi rdzeniowemu możliwe jest pobieranie rdzenia, jego magazynowanie oraz urywanie od dna otworu.
Na modelu zaznaczono kolejnymi cyframi poszczególne elementy aparatu. Po naciśnięciu danej cyfry rozwija się szczegółowy opis danego elementu wraz z nagraniem audio. Nagranie audio odpowiada tekstowi znajdującemu się w opisie.
Cyfrą oznaczono aparat rdzeniowy. Służą one do wiercenia otworów geologicznych bez konieczności wyciągania przewodu wiertniczego w celu wydobycia rdzenia. Składają się z rury zewnętrznej, rury wewnętrznej oraz głowicy. Rurę wewnętrzną rdzeniówki wraz z rdzeniem wiertniczym wyciąga się wewnątrz rur płuczkowych za pomocą chwytaka zamocowanego do liny. Dzięki temu uzyskuje się zwiększenie postępu wierceń a co za tym idzie skrócenie czasu wykonania otworu.
Na ekranie w rzucie głównym widać dwa szare cylindryczne elementy. Elementy położone są równolegle obok siebie. Element na dole ekranu jest składa się czterech części. Góry element z lewej strony ekranu jest cienkim pierścieniem w kolorze miedzianym. Poniżej znajduje się szary podłużny cylinder, w środku którego po prawej stronie widać wewnętrzne żłobienia. Jest to połączenie gwintowane. Środkowy element stanowi szary podłużny cylinder, z którego lewej strony widać połączenie gwintowane w kolorze miedzianym. Czwarty element z prawej strony to podłużny cylinder, z którego lewej strony również widać połączenie gwintowane w kolorze miedzianym.
Drugie urządzenie znajdujące się powyżej jest w kształcie podłużnego szarego cylindra składającego się z różnych modułów. Po prawej stronie widać cienki szpic osadzony na cylindrycznym kształcie przyłączonym do szarego elementu w kształcie rury. Na rurze znajduje się cyfra . W punkcie stanowiącym środek długości rury, po obu jej stronach znajdują się stabilizatory o kształcie trapezów. Za rurą z lewej strony widać sześć pierścieni o różnej średnicy, które zakończone są białą sześciokątną nakrętką. Za nakrętką widać cylindryczny kształt z dwoma żłobieniami w centralnej jego części. Żłobienia są równolegle do siebie i biegną po obwodzie elementu. Całość zakończona jest szerszym cylindrem z otworem u góry.
W rzucie bocznym z lewej, prawej strony oraz z tyłu opis jest tożsamy do opisu rzutu głównego.
Model . Koronka gryzowa zębata
Na ekranie widać animowany interaktywny model koronki gryzowej zębatej. Koronka gryzowa zębata jest to narzędzie wiercące pozwalające na zwiercanie powierzchni pierścieniowej otworu wiertniczego. Wykonana jest jako korpus stalowy, wyposażony w rolki z nafrezowanymi zębami lub osadzonymi słupkami z węglika wolframu. Koronka ta występuje pod zwyczajową nazwą koronka 'zębata'.
Na modelu zaznaczono kolejnymi cyframi poszczególne elementy koronki. Po naciśnięciu danej cyfry rozwija się szczegółowy opis danego elementu wraz z nagraniem audio. Nagranie audio odpowiada tekstowi znajdującemu się w opisie.
Cyfrą oznaczono koronkę gryzową zębatą. Koronki gryzowe niszczą strukturę skały poprzez jej kruszenie w wyniku przemiany momentu obrotowego przewodu na udary i poślizg zębów po dnie otworu. W tego typu rozwiązaniach konstrukcyjnych energia kinetyczna obrotu przemienia się w energię potencjalną o wartości niezbędnej do zniszczenia skały, przez co uzyskuje się efekt urabiania górotworu.
W rzucie głównym w centralnej części ekranu widać urządzenie mechaniczne, którego podstawę stanowi czop w kształcie cylindra. Na czopie osadzony jest cylindryczny korpus, na końcu którego widać sześć łap. Na górze łapy widać okrągłą rolkę, na której znajdują się zęby. Element przypomina koło zębate. Na środku łapy widzianej w centralnej części ekranu znajduje się cyfra .
Ze względu na to, że urządzenie składa się z takich samych segmentów, opis rzutu z prawej strony, z lewej strony oraz z tyłu urządzenia będzie tożsamy opisowi rzutu głównego.
W rzucie z góry widać że centralną częścią urządzenia jest okrągły pierścień wpisany w sześcian, który zbliżony jest kształtem do struktury trójkąta. Pomiędzy łapą osadzoną na zewnętrznej ściany koronki a ścianą sześcianu osadzona jest rolka z organem roboczym wyposażonym w zęby
W rzucie dolnym w centralnej części podstawy czopa widać żłobienia, które stanowią połączenie gwintowane.
Model . Obciążniki
Na ekranie widać animowany interaktywny model trzech różnych obciążników. Obciążnik jest to elementy zestawu przewodu wiertniczego umieszczone bezpośrednio nad świdrem w przypadku wiercenia otworu pionowego lub w części pionowej otworu, szczególnie w przypadku wiercenia otworu horyzontalnego. Podstawowym zadaniem obciążników w otworze jest wywieranie swoim ciężarem nacisku na świder oraz utrzymywanie w napięciu rur płuczkowych. Obciążniki zakończone są połączeniami gwintowymi.
Na modelu zaznaczono kolejnymi cyframi poszczególne elementy koronki. Po naciśnięciu danej cyfry rozwija się szczegółowy opis danego elementu wraz z nagraniem audio. Nagranie audio odpowiada tekstowi znajdującemu się w opisie.
Cyfrą oznaczono obciążniki. Zadaniem obciążników jest wywieranie nacisku na narzędzie wiercące oraz usztywnienie dolnej części przewodu wiertniczego. Są to grubościenne rury bez szwu. Występują w trzech odmianach: gładkie na całej długości, z zatoczką na elewator oraz z zatoczką na kliny. Obecnie najczęściej stosuje się obciążniki spiralne, przez co zmniejsza się powierzchnię styku obciążnika ze ścianą otworu co zmniejsza ryzyko przychwycenia kolumny przewodu wiertniczego.
W rzucie głównym w centralnej części ekranu widać trzy różne obciążniki. Dwa obciążniki od strony góry ekranu są w kolorze niebieskim, trzeci obciążnik znajdujący się na dole ekranu jest w kolorze szarym. Obciążniki są w kształcie cienkich elementów cylindrycznych. Po lewy stronie każdego cylindra widać szare żłobienia. Jest to połączenie gwintowane.
Obciążniki pierwszy od góry i pierwszy od dołu są to obciążniki gładkie. Obciążniki te są w przekroju okrągłymi prętami, drążonymi wewnątrz, które zakończone są połączeniami gwintowymi. Po lewej stronie przy podstawie niebieskiego pręta widocznego u góry ekranu znajduje się cyfra . Niebieski obciążnik w środku jest obciążnikiem spiralnym czyli urządzeniem, które w przekroju jest okrągłym prętem z nafrezowaną na zewnątrz spiralna linią śrubową, drążonym wewnątrz, zakończonym połączeniami gwintowymi. Nafrezowana spirala ułatwia wynoszenie zwiercin.
W rzucie bocznym z lewej, prawej strony oraz z tyłu opis jest tożsamy do opisu rzutu głównego.
W rzucie z góry i dołu wszystkie pręty mają okrągły przekrój.
Model . Rura płuczkowa
Na ekranie widać animowany interaktywny model rury płuczkowej. Rury płuczkowe są podstawową częścią zestawu przewodu wiertniczego. Wykonane są jako stalowe rury bez szwu. Do każdego z końców rury przymocowany jest za pomocą zgrzewania tarciowego zwornik. Jest on częścią rury płuczkowej o zwiększonej średnicy zewnętrznej przez spęczenie. Na jednym końcu rury zgrzany jest zwornik zakończony gwintem narzędziowym wykonanym w postaci czopa zaś na drugim końcu w postaci mufy. Rury płuczkowe ze względu na bardzo trudne warunki w jakich pracują wykonywane są ze specjalnych gatunków stali o dużej wytrzymałości.
Na modelu zaznaczono kolejnymi cyframi poszczególne elementy rury. Po naciśnięciu danej cyfry rozwija się szczegółowy opis danego elementu wraz z nagraniem audio. Nagranie audio odpowiada tekstowi znajdującemu się w opisie.
Cyfrą oznaczono rurę płuczkową. Rury płuczkowe to podstawowa część przewodu wiertniczego. Wykonane są jako rury stalowe bez szwu. Ich cechą charakterystyczną są spęczenia znajdujące się na końcach każdej z rur. Ze względu na tę cechę rury płuczkowe dzieli się na wewnętrznie spęczane (WS), zewnętrznie spęczane (ZS) oraz rury wewnętrznie i zewnętrznie spęcznane (WZS). Połączenia między rurami mogą być wykonywane jako rury płuczkowe gwintowane lub rury płuczkowe z połączeniami zwornikowymi.
W rzucie głównym na ekranie widać szary cienki, podłużny cylinder. Na lewym końcu rury widać zewnętrzne połączenie gwintowane. Przy połączeniu gwintowanym znajduje się cyfra .
W rzucie bocznym z prawej strony widać, że rura ma żłobienia wewnętrzne, które stanowią połączenie gwintowane.
W rzucie z lewej strony widać, że wnętrze rury jest płaskie.
Opisy rzutów z góry, z dołu oraz z tyłu są tożsame z opisem rzutu głównego.
Model . Amortyzator drgań
Na ekranie widać animowany interaktywny model amortyzatora drgań czyli elementu przewodu wiertniczego odpowiedzialny za zmniejszenie natężenia drgań przenoszonych z narzędzia wiertniczego na górną część przewodu wiertniczego i urządzenie wiertnicze.
Na modelu zaznaczono kolejnymi cyframi poszczególne elementy amortyzatora. Po naciśnięciu danej cyfry rozwija się szczegółowy opis danego elementu wraz z nagraniem audio. Nagranie audio odpowiada tekstowi znajdującemu się w opisie.
Cyfrą oznaczono amortyzator drgań. Element montowany w kolumnie obciążników bezpośrednio nad świdrem lub nad stabilizatorami. Zadaniem amortyzatora drgań jest niedopuszczenie do przeniesienia drgań z narzędzia wiercącego na przewód wiertniczy oraz wyżej na urządzenie wiertnicze.
Na ekranie w rzucie głównym widać cienki podłużny cylinder. Korpus cylindra jest w kolorze niebieskim. Po prawej stronie cylindra widać zewnętrzne połączenie gwintowane, które odchodzi od szarego elementu w kształcie walca. Walec ten połączony jest z cieńszym szarym cylindrem, który wchodzi pod niebieski korpus amortyzatora. Na końcu szarego kształtu widoczny jest cienki niebieski pierścień oraz płaski cylinder, który łączy się z kolejnym szarym cylindrem o większej średnicy. Na całej długości elementu znajduje się dwadzieścia równomiernie rozmieszczonych pierścieni. Do lewego końca elementu przyłączony jest kolejny czarny podłużny cylinder oraz kolejne cztery elementy w tym samym kształcie.
Z prawej strony elementu przed połączeniem gwintowanym znajduje się cyfra .
W rzucie tylnym widać, że korpus urządzenia w dwóch trzecich jego długości jest w kolorze niebieskim, a w jednej trzeciej z prawej strony w kolorze szarym.
W rzucie z prawej i lewej strony widać, że urządzenie jest o przekroju kołowym.
Model . Nożyce wiertnicze (hydrauliczne)
Na ekranie widać animowany interaktywny model nożyc wiertniczych. Nożyce wiertnicze (fishing jar) służą do podbijania przychwyconego przewodu wiertniczego. Ich aktywacja przebiega przez powolne napinanie przewodu wiertniczego oraz kolejno jego energiczne zluzowanie. Energia hydrauliczna zmagazynowana w nożycach wytwarza udar na dolną część przewodu wiertniczego, powodując jego zbicie poniżej interwału przychwycenia
Na modelu zaznaczono kolejnymi cyframi poszczególne elementy nożyc. Po naciśnięciu danej cyfry rozwija się szczegółowy opis danego elementu wraz z nagraniem audio. Nagranie audio odpowiada tekstowi znajdującemu się w opisie.
Cyfrą oznaczono nożyce wiertnicze (hydrauliczne). Podstawowym zadaniem nożyc jest umożliwienie wywołania w przewodzie wiertniczym udarów (w górę lub w dół) w celu uwolnienia przychwyconego przewodu. Umieszczane w zestawie nad obciążnikami co ma zagwarantować, że wrazie przychwycenia przewodu, będą znajdować się nad miejscem przychwycenia co umożliwi ich użycie.
Na ekranie w rzucie głównym widać cienki cylindryczny element w kolorze szarym. Z prawej strony nożyc widać szary cylindryczny element, który osadzony jest na cienkim zielonym cylindrze, który wchodzi do wnętrza szarego korpusu. Zielony cylinder łączy się z kolejnym szarym cylindrem, który z lewej strony ma końcówkę w formie lejka o wydłużone szyjce. Pomiędzy końcówką elementu a zielonym cylindrem, na którego bokach znajdują się cienkie prostokątne nacięcia biegnące przez około dwie trzecie długości elementu znajduje się pustka. Nacięcia na zielonym cylindrze po lewej stronie zakończone są dodatkowo wyciętym elementem w kształcie koła. Cylinder ten łączy się z cienkim szarym elementem w kształcie podłużnego walca, który jest przyłączony do przeźroczystego cylindra znajdującego się w niewielkiej stalowej obejmie przypominającej stożek. Kolejnymi elementami są również cylindry, które nieznacznie trzykrotnie zmniejszają swoją średnicę. Na końcu elementu znajduje się cyfra . Za obudową z prawej strony widać kolejny cylindryczny element, którego prawy bok jest w kształcie lejka. Szyja lejka jest wydłużona i do niej przyłączony jest kolejny cienki szary cylinder.
W rzucie z tyłu widać, że nożyce są w kształcie cienkiej szarej rury, która składa się z kilku cylindrycznych segmentów o różnej średnicy.
Model . Silnik wgłębny
Na ekranie widać animowany interaktywny model silnika czyli elementu przewodu wiertniczego, odpowiedzialnego za przekazywanie momentu obrotowego na świder. W konstrukcji silników wgłębnych wykorzystano zasadę działania tak zwanej. 'pompy Moineau. Układ napędowy stanowi spiralny stalowy wał umieszczony wewnątrz elastomerowego, wykonanego w formie spirali statora. Obrót wału wymuszany jest przez płuczkę przepływającą pomiędzy obydwoma elementami. Prędkość obrotowa silnika zależy przede wszystkim od konfiguracji rotor - stator (ilości występów na przykład jedna druga, trzy czwarte, pięć szóstych i dziewięć dziesiątych). Im wyższa liczba 'występów' tym niższa prędkość obrotowa i tym wyższy moment.
Na modelu zaznaczono kolejnymi cyframi poszczególne elementy silnika. Po naciśnięciu danej cyfry rozwija się szczegółowy opis danego elementu wraz z nagraniem audio. Nagranie audio odpowiada tekstowi znajdującemu się w opisie.
Cyfrą oznaczono silnik wgłębny. Silniki wgłębne służą przekazywaniu napędu obrotowego bezpośrednio na narzędzie wiercące. Wiercenia ze względu na rodzaj silnika dzielą się na: z elektrowiertem, turbowiertem i wiercenia z silnikiem hydraulicznym. Wiercenie z silnikiem hydraulicznym wykorzystuje moc hydrauliczną przepływającej płuczki wiertniczej między rotorem a statorem. Jest to rozwiązanie bardzo często stosowane przy otworach kierunkowych.
Na ekranie w rzucie głównym widać cienki cylindryczny element wykonany ze stali. Główną część urządzenia stanowi stalowy korpus czyli stator. Wewnątrz stalowego korpusu widać wirnik o kształcie ślimakowym. Wirnik czyli rotor osadzony jest z lewej strony na szarym cylindrycznym elemencie znajdującym się wewnątrz obudowy. Na powierzchni cylindrycznego elementu widać cyfrę . Na końcu korpusu z prawej strony ekranu widać połączenie gwintowane.
W rzucie z tyłu widać podłużny cienki cylindryczny korpus. Korpus jest w kolorze szarym.
W przypadku rzutu z lewej strony widać, że w cylindrycznym elemencie znajduje się otwór. Na jego brzegach widać połączenie gwintowane.
W przypadku rzutu z prawej strony widać, że w rotorze znajduje się otwór, przez który widać przelot przez cały silnik.
Model . Kabina wiertacza z aparaturą kontrolno‑pomiarową
Na ekranie widać animowany model przedstawiającą kabinę operatora. Na modelu zaznaczono kolejnymi cyframi poszczególne elementy urządzenia. Po naciśnięciu danej cyfry rozwija się szczegółowy opis danego elementu wraz z nagraniem audio. Nagranie audio odpowiada tekstowi znajdującemu się w opisie.
Cyfrą oznaczono kabinę wiertacza. Kabina jest miejscem pracy wiertacza. Pozwala operować urządzeniem wiertniczym, oraz kontrolować proces wiercenia. Operowanie urządzeniem wiertniczym opiera się o wskazania kontrolne, których wartości chwilowe ukazują się na zegarach na pulpicie sterowania.
Cyfrą oznaczono ciężarowskaz.
Cyfrą oznaczono manometr ciśnienia płuczki na przewodzie wiertniczym.
Cyfrą oznaczono miernik momentu obrotowego w przewodzie wiertniczym.
Cyfrą oznaczono miernik liczby suwów pompy płuczkowej.
Cyfrą oznaczono manometr ciśnienia płuczki w przestrzeni pierścieniowej.
Cyfrą oznaczono miernik prędkości obrotowej przewodu wiertniczego.
Cyfrą oznaczono miernik siły w linie klucza maszynowego.
Cyfrą oznaczono wskaźnik chwilowej prędkości wiercenia.
Liczbą oznaczono wskaźnik wartości strumienia objętości tłoczonej płuczki wiertniczej do przewodu wiertniczego.
Cyfrą oznaczono wskaźnik bilansu ilości płuczki wpływającej i wypływającej z otworu wiertniczego.
Kabina operatora jest w kształcie pomarańczowego sześcianu. Wierzchołki znajdujące się po prawej stronie sześcianu są ścięte powodując, że podstawą bryły jest sześciokąt. W znajdujących się otworach w przedniej ścianie sześcianu oraz bocznych ścianach sześcianu znajdują się kraty. Otwory pełnią rolę okien. Góra sześcianu jest w kształcie graniastosłupa o podstawie sześciokąta. Ściany boczne graniastosłupa oraz ściana przednia jest wykonana w formie kratownicy która zapewnia lepszą widoczność. Na dachu kabiny znajduje się cyfra .
W środku kabiny widać animowany pulpit z siedmioma okrągłymi wskaźnikami znajdującymi się w centralnej części kabiny operatora. Szary pulpit znajduje się przed czarnym fotelem operatora który wyposażony jest w dwa dżojstiki. Po lewej stronie pulpitu znajdują się trzy wskaźniki rozmieszczone w układzie odwróconego trójkąta. Pierwszy wskaźnik u góry od lewej strony to miernik liczby suwów pompy płuczkowej oznaczony cyfrą . Drugi wskaźnik u góry od prawej strony to manometr ciśnienia płuczki na przewodzie wiertniczym oznaczony cyfrą , a wskaźnik u dołu to miernik momentu obrotowego w przewodzie wiertniczym oznaczony cyfrą . Po prawej stronie pulpitu znajdują się trzy kolejne wskaźniki rozmieszczone w układzie odwróconego trójkąta. Pierwszy wskaźnik od lewej oznaczony cyfrą jest to manometr ciśnienia płuczki w przestrzeni pierścieniowej drugi wskaźnik od lewej oznaczony cyfrą czyli miernik siły w linie klucza maszynowego a trzeci wskaźnik widoczny na dole pulpitu oznaczony jest cyfrą i jest to miernik prędkości obrotowej przewodu wiertniczego. Pomiędzy wskaźnikami znajduje się duży okrągły wskaźnik ciężarowskazu czyli przyrządu przeznaczonego do wskazywania ciężaru zawieszonego na haku wiertniczym oraz nacisku na narzędzie wiercące. Ciężarowskaz zajmuje całą wysokość szarego pulpitu w kabinie wiertacza. Ciężarowskaz jest oznaczony cyfrą .
Po prawej stronie operatora na szarym pulpicie w lewej jego części znajdują się trzy prostokątne wskaźniki oznaczone cyframi i liczbami , i . Wskaźniki są ułożone jeden pod drugim. W kolejności są to odpowiednio wskaźnik chwilowej prędkości wiercenia, wskaźnik wartości strumienia objętości tłoczonej płuczki wiertniczej do przewodu wiertniczego chwilowa prędkość przepływu oraz sskaźnik bilansu ilości płuczki wpływającej i wypływającej z otworu wiertniczego. Po prawej stronie pulpitu widać dwa pionowe wskaźniki o kształcie wąskich prostokątów, których wysokość odpowiada wysokości pulpitu. Wskaźniki są położone obok siebie i są równoległe względem siebie. Wskaźnik po lewej stronie ma niebieskie wypełnienie pokazujące daną wartość chwilową. Wskaźnik po prawej stronie ma zielone wypełnienie pokazujące daną wartość chwilową. Pod wskaźnikami znajdują się czarne prostokąty na których najprawdopodobniej w rzeczywistości są opisy.
W ostatniej części pulpitu widocznej z prawej strony fotela znajduje się niewielki prostokątny ekran ciekłokrystaliczny pod którym umieszczonych jest osiem czarnych przycisków. Przyciski rozmieszczone są w dwóch rzędach po cztery przyciski w każdym. Na końcu każdego rzędu przycisków znajduje się czarna gałka w kształcie dżojstika. Pod czarnym zestawem przycisków znajdują się cztery dodatkowe okrągłe przyciski.
W prawym górnym rogu kabiny operatora znajduje się czarny monitor.
W lewej części kabiny w pierwszym segmencie znajdują się trzy białe pokrętła. Pokrętła umieszczone są na czarnych elementach o kształcie prostokąta. Pod pokrętłami znajdują się trzy dźwignie. Dźwignie są w pozycji zero. Pod dźwigniami umieszczonych jest pięć okrągłych przycisków.
W drugim segmencie pulpitu znajduje się niebieski telefon z prostokątną słuchawką. Za telefonem umieszczonych jest piętnaście białych kwadratowych przycisków, które rozłożone są w trzech pionowych rzędach. W pierwszym rzędzie od lewej jest pięć przycisków, w drugim cztery przyciski i w trzecim pięć przycisków. Nad pierwszym i drugim rzędem znajduje się dodatkowo odpowiednio czerwony i zielony kwadratowy przycisk.
W trzecim segmencie za przyciskami widoczny jest czarny ekran na którym wyświetlane są zielone słupki. Dodatkowo w lewym górnym rogu kabiny znajduje się drugi ekran ciekłokrystaliczny.
Za fotelem operatora znajduje się szary prostopadłościan na którym zamontowane są zestawy dźwigienek oraz cztery okrągłe wskaźniki. Okrągłe wskaźniki, umieszczone są po dwa z każdej strony przy bocznych krawędziach w górnej części prostopadłościanu. Pomiędzy wskaźnikami na całej długości elementu znajdują się cztery dźwignie. Pomiędzy drugą i trzecią dźwignią, pod wskaźnikami znajdują się w sumie dwie dodatkowe dźwignie.
Po lewej stronie fotela operatora znajduje się dodatkowych sześć czarnych okrągłych przycisków, wspomniany wcześniej dżojstik oraz dźwignia. Po prawej stronie znajduje się analogicznie dżojstik oraz cztery duże okrągłe pokrętła oraz osiem mniejszych. Mniejsze pokrętła ułożone są w jednym rzędzie.
Powrót do spisu treściPowrót do spisu treści
Materiał pomocniczy: Optymalizacja parametru prędkości wiercenia przy założeniu trzech zmiennych parametrów wiercenia: nacisku na narzędzie, prędkości obrotowej narzędzia i strumienia objętości płuczki.
Przypadek | Nacisk | Prędkość obrotowa | Strumień płuczki | Prędkość wiercenia | Aby osiągnąć większą prędkość wiercenia: |
---|---|---|---|---|---|
Zwiększ nacisk, | |||||
Zwiększ nacisk, | |||||
| Zwiększ prędkość obrotową, | ||||
Zwiększ nacisk, | |||||
| Zwiększ nacisk, | ||||
| Zwiększ prędkość obrotową, | ||||
Zwiększ nacisk, | |||||
| Zwiększ nacisk, | ||||
| Zwiększ strumień płuczki | ||||
Zwiększ nacisk, | |||||
Zwiększ nacisk, | |||||
Zwiększ prędkość obrotową | |||||
Zwiększ nacisk, | |||||
Zwiększ nacisk, | |||||
| Zwiększ prędkość obrotową, | ||||
Zwiększ nacisk, | |||||
| Zwiększ nacisk, | ||||
| Zwiększ strumień płuczki | ||||
Zwiększ nacisk, | |||||
Zwiększ nacisk, | |||||
Zwiększ prędkość obrotową | |||||
Zwiększ nacisk, | |||||
Zwiększ nacisk, | |||||
Zwiększ prędkość obrotową | |||||
Zwiększ nacisk | |||||
Zwiększ nacisk | |||||
Parametry najlepsze dla osiągnięcia maksymalnej prędkości wiercenia |