E‑book do e‑materiału Eksploatacja maszyn i urządzeń do przygotowania mas formierskich i mas rdzeniowych
MTL.02. Eksploatacja maszyn i urządzeń odlewniczych - Operator maszyn i urządzeń odlewniczych 812107, Technik odlewnik 311705
Masy formierskie oraz maszyny do ich przygotowania
E‑BOOK
Spis treści
OsnowaOsnowa
Materiały wiążąceMateriały wiążące
Materiały dodatkoweMateriały dodatkowe
Przygotowanie masy formierskiejPrzygotowanie masy formierskiej
Regeneracja masy formierskiejRegeneracja masy formierskiej
Urządzenia wykorzystywane do przygotowania masyUrządzenia wykorzystywane do przygotowania masy
Obsługa bieżąca maszyn i urządzeńObsługa bieżąca maszyn i urządzeń
Ocena stanu technicznego elementów maszyn i urządzeń
Zasady bezpieczeństwa i higieny pracyZasady bezpieczeństwa i higieny pracy
Słownik pojęćSłownik pojęć
Netografia i bibliografiaNetografia i bibliografia
Ocena stanu technicznego elementów maszyn i urządzeń
Maszyny oraz urządzenia techniczne ulegają procesowi zużycia. Jest to złożone zjawisko obejmujące przede wszystkim naturalne zużywania się elementów w sposób, który jest zależny od intensywności i typu eksploatacji. Oceny stanu technicznego elementów maszyn i urządzeń można dokonać na kilka sposobów. Do podstawowych metod należą: obserwacja prosta, przegląd techniczny oraz klasyfikacja stanu technicznego urządzeń.
Obserwacja prosta
To metoda podczas której wykorzystywane są zmysły człowieka, takie jak: wzrok, dotyk, węch i słuch. Koniecznym przy tych obserwacjach jest doświadczenie pracownika i jego znajomość danego urządzenia. Wśród metod obserwacji prostej wyróżniane są:
kontrola wzrokowa:
wskazania przyrządów kontrolno‑pomiarowych, na przykład: termometru, amperomierza lub obrotomierza,
przecieki zewnętrzne,
wibracje, czyli drgania lub wstrząsy,
kontrola dotykowa:
temperatura,
wibracje,
przecieki,
kontrola słuchowa:
wewnętrzne hałasy mechaniczne,
zewnętrzne hałasy mechaniczne.
Diagnozowanie za pomocą obserwacji prostej jest metodą mało kosztowną oraz najczęściej stosowaną w przypadku układów hydraulicznych i pneumatycznych maszyn roboczych.
Przegląd techniczny
Przegląd techniczny to zbiór czynności obejmujący między innymi konserwację, diagnostykę i profilaktykę. Celem tych czynności jest wykrycie oraz usunięcie powstałych w urządzeniu uszkodzeń.
W maszynach i urządzeniach uszkodzenia lub zniszczenia powstają pod wpływem przenoszonej energii. Ze względu na rodzaj pracy jaka maszyna wykonuje w danych warunkach przyczyny powstawania uszkodzeń można podzielić na:
mechaniczne – naprężenia, zmęczenie materiału, zużycie cierne,,
chemiczne – korozja metali, starzenie się gum oraz farb, butwienie drewna,
cieplne – przyspieszenie zużywania się elementów, nadtapianie,
elektryczne – elektro–korozja.
Główne przyczyny powstawania uszkodzeń maszyn i urządzeń można podzielić na:
konstrukcyjne – uszkodzenia pojawiające się w wyniku błędów projektowych i konstruowania urządzenia; najczęściej wskutek nie uwzględnienia obciążeń ekstremalnych, czyli wartości istotnie przekraczających obciążenie w jakim maszyna pracuje na co dzień,
technologiczne, inaczej nazywane produkcyjnymi – uszkodzenia powstałe w wyniku błędów i niedokładności procesów technologicznych (np. nie wystarczająca gładkość powierzchni, brak tolerancji),
eksploatacyjne – uszkodzenia powstałe na skutek nie przestrzegania zasad eksploatacji lub eksploatacji w warunkach nieprzewidzianych dla danego urządzenia, w których czynniki zewnętrzne wpływają na osłabienie i przedwczesne zużycie elementów maszyny,
Sposobami na usunięcie uszkodzeń, które wyróżniamy są:
wyłączenie i naprawa uszkodzonego elementu urządzenia,
wyłączenie i zastąpienie uszkodzonego elementu jego odpowiednikiem. W przypadku, gdy uszkodzony element nie może być wyłączony z eksploatacji, istnieje możliwość wyłączenia urządzenia z eksploatacji lub używania urządzenia z ograniczoną wydajnością.
Na poniższej ilustracji przedstawiono schematyczne kroki działania względem zmiany stanu technicznego maszyny i upływającego czasu.
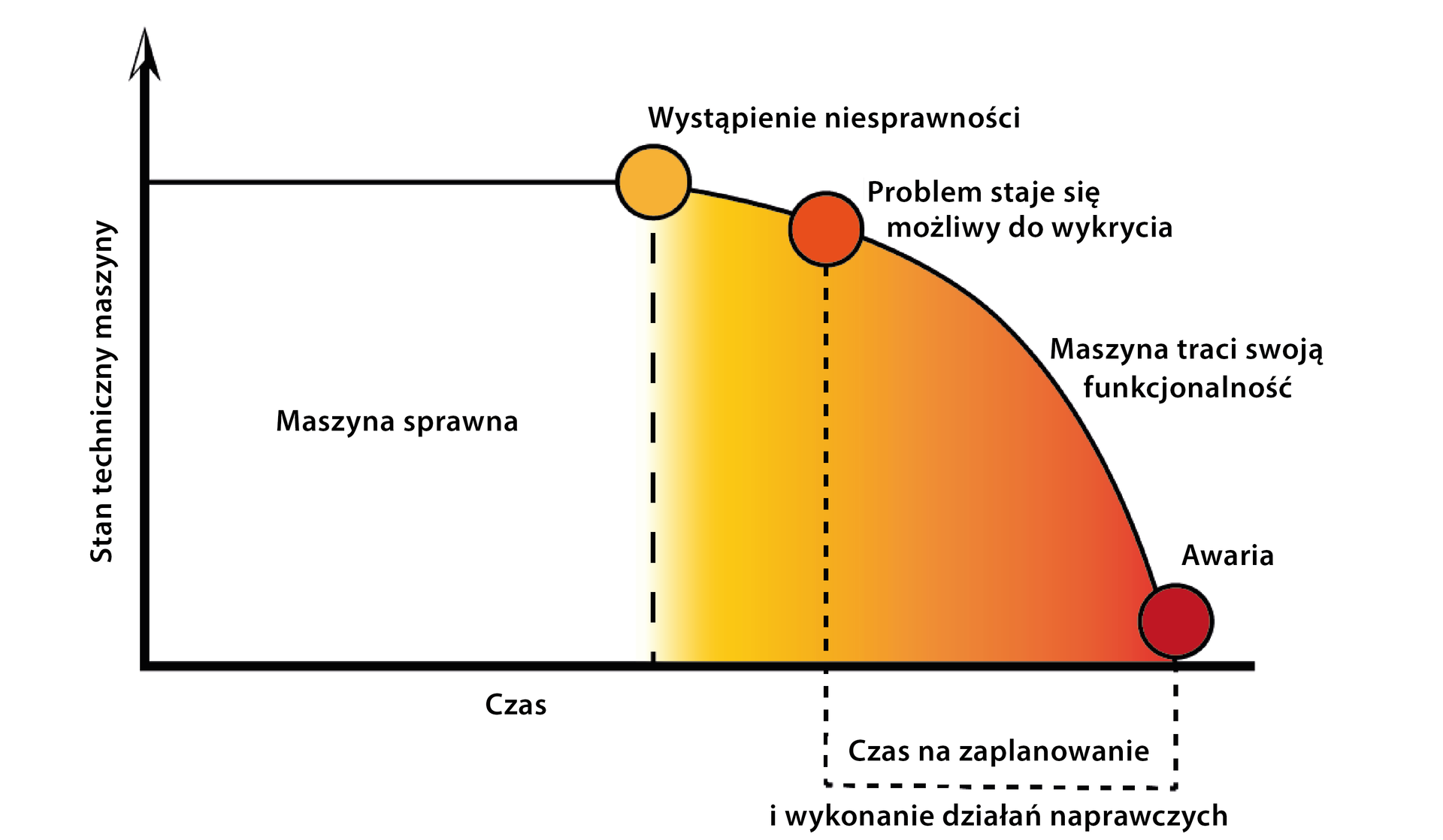
Wykres przedstawia zależność stanu technicznego maszyny od czasu. Na osi opisano czas, natomiast na osi stan techniczny maszyny. Na obu osiach nie zaznaczono wartości liczbowych, wykres ma charakter poglądowy i ukazuje poszczególne etapy przejścia od pełnej sprawności maszyny do jej awarii. Fragment wykresu, który opisuje maszynę sprawną przebiega równolegle do osi , aż do punktu w którym zaznaczono wystąpienie niesprawności. Po przekroczeniu punktu wykres przebiega malejąco, na kształt łuku. Na łuku zaznaczone są 2 punkty: problem staje się możliwy do wykrycia oraz awaria. Podczas pojawienia się problemu spadek stanu technicznego maszyny staje się gwałtowniejszy, jest to etap kiedy maszyna traci swoją funkcjonalność. Kończy się on awarią maszyny, kiedy to urządzenie traci całkowicie swoją sprawność. Czas pomiędzy pojawieniem się problemu, a awarią to czas na zaplanowanie i wykonanie działań naprawczych.
Podczas przeglądu technicznego można wyróżnić kluczowe elementy, takie jak:
określanie stopnia zużycia i czasów pracy zespołów i części,
sprawdzanie i pomiar zespołów styków i uszczelnień,
wyważenie urządzeń napędowych maszyny lub urządzenia,
czyszczenie i mycie poszczególnych elementów maszyny lub urządzenia,
przegląd i badanie danych elementów,
sprawdzanie i wyregulowanie dokładności pracy maszyny,
wykonanie pomiarów luzów,
częściowy demontaż maszyny i urządzenia,
sprawdzanie działania przyrządów pomiarowo kontrolnych i urządzeń regulacyjnych,
usuwanie drobnych uszkodzeń,
wykonywanie wszystkich czynności wchodzących w zakres codziennej obsługi.
Klasy stanu technicznego urządzeń
Podczas badań diagnostycznych wyróżniane są następujące klasy stanów technicznych urządzeń:
sprawności technicznej,
niesprawności technicznej,
zdatności,
niezdatności.
Ze stanem sprawności technicznej mamy styczność, gdy żaden z parametrów struktury urządzenia nie przekracza wartości dopuszczalnej. W tym stanie urządzenie w bezpieczny sposób spełnia wszystkie założone przy konstruowaniu funkcje.
Natomiast stan zdatności występuje gdy urządzenie nie wypełnia swoich zasadniczych funkcji, jednak zauważalne jest działanie urządzenia ze zmienionymi właściwościami techniczno–eksploatacyjnymi. Przykładem takiej zmiany może być zwiększone zużycie paliwa w samochodzie, co jest spowodowane zużyciem pierścieni tłokowych. Diagnozowane urządzenie będzie wtedy w stanie niepełnej sprawności, czyli niesprawności technicznej.
W sytuacji, gdy któryś z parametrów struktury przekroczy wartość graniczną i urządzenie utraci właściwości techniczno–eksploatacyjne, wskutek czego nie będzie spełniać założonych funkcji, to występuje stan niezdatności. Jest to stan, w którym urządzenie uległo uszkodzeniu i nie spełnia żadnej założonej przy konstruowaniu funkcji.
Dodatkowo wyróżniamy jeszcze dwa stany techniczne urządzeń:
dopuszczalny,
częściowej zdatności.
Stan dopuszczalny definiowany jest jako stan zagrożenia uszkodzenia urządzenia. Natomiast, stan częściowej zdatności występuje, wtedy gdy urządzenie może spełniać swoje założone zadanie w ograniczonym zakresie, czyli na przykład z mniejszą prędkością.
Remonty
Maszyny i urządzenia (jeżeli zajdzie taka potrzeba) są poddawane remontom. Wyróżniamy ich następujące rodzaje:
obsługa okresowa , to przegląd techniczny obejmujący czynności związane z: regulacją zespołów i mechanizmów, usunięciem usterek i uszkodzeń, ustaleniem stopnia zużycia poszczególnych części i zespołów dla określenia szczegółowo zakresu naprawy oraz myciem i czyszczeniem urządzeń,
remont bieżący , obejmuje on naprawę lub wymianę szybko zużywających się części. W jego zakres wchodzą również wszystkie czynności przeglądu technicznego,
remont średni , obejmuje naprawę lub wymianę szybciej zużywających się części zespołów w celu zapewnienia prawidłowej eksploatacji maszyny lub urządzenia do następnego remontu średniego i kapitalnego. Remont średni obejmuje również wszystkie czynności remontu bieżącego,
remont kapitalny , to remont obejmujący naprawę lub wymianę wszystkich części, a nawet całych zespołów ulegających zużyciu.
Powrót do spisu treściPowrót do spisu treści
Powiązane materiały multimedialne
Atlas interaktywny: Zasady obsługi bieżącej maszyn i urządzeń do przygotowania mas formierskich i mas rdzeniowychZasady obsługi bieżącej maszyn i urządzeń do przygotowania mas formierskich i mas rdzeniowych
Sekwencje filmowe: Rodzaje maszyn i urządzeń do przygotowania mas formierskich i mas rdzeniowychRodzaje maszyn i urządzeń do przygotowania mas formierskich i mas rdzeniowych
Animacja 3D: Proces przygotowania mas formierskich i mas rdzeniowychProces przygotowania mas formierskich i mas rdzeniowych
Schemat interaktywny: Zasady oceny stanu technicznego elementów maszyn i urządzeńZasady oceny stanu technicznego elementów maszyn i urządzeń