E‑book do e‑materiału Eksploatacja maszyn i urządzeń do przygotowania mas formierskich i mas rdzeniowych
MTL.02. Eksploatacja maszyn i urządzeń odlewniczych - Operator maszyn i urządzeń odlewniczych 812107, Technik odlewnik 311705
Masy formierskie oraz maszyny do ich przygotowania
E‑BOOK
Spis treści
OsnowaOsnowa
Materiały wiążąceMateriały wiążące
Materiały dodatkoweMateriały dodatkowe
Przygotowanie masy formierskiejPrzygotowanie masy formierskiej
Regeneracja masy formierskiejRegeneracja masy formierskiej
Urządzenia wykorzystywane do przygotowania masy
Obsługa bieżąca maszyn i urządzeńObsługa bieżąca maszyn i urządzeń
Ocena stanu technicznego elementów maszyn i urządzeńOcena stanu technicznego elementów maszyn i urządzeń
Zasady bezpieczeństwa i higieny pracyZasady bezpieczeństwa i higieny pracy
Słownik pojęćSłownik pojęć
Netografia i bibliografiaNetografia i bibliografia
Urządzenia wykorzystywane do przygotowania masy
Przykłady urządzeń wykorzystywanych do przygotowania masy formierskiej świeżej i regenerowanej:
Suszenie i Chłodzenie
Piasek trafiający do odlewni może mieć różną zawartość wilgoci. Jeżeli transportowany jest odkrytymi wagonami lub samochodami jego wilgoć będzie zależeć od warunków atmosferycznych. Taki piasek może zawierać nawet wilgoci. W przypadku gdy wilgotność masy powinna wynosić piasek należy poddać suszeniu. W przypadku regeneracji masy odzyskany piasek może mieć zbyt wysoką temperaturę, wówczas należy poddać go chłodzeniu.
Zasadę działania oraz bilans cieplny suszarko – chłodziarki został przedstawiony na rysunku.
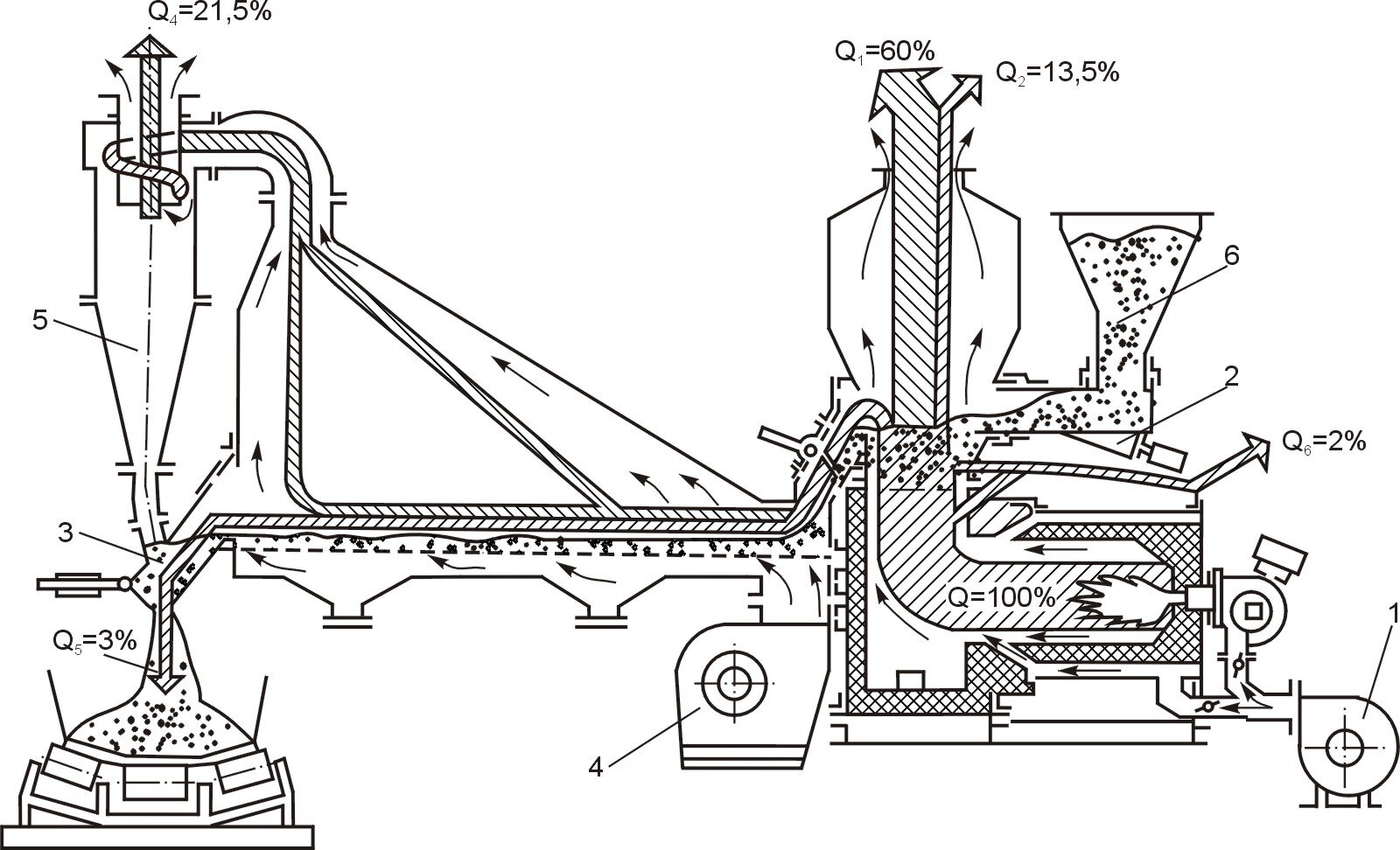
Na ilustracji przedstawiona została suszarko‑chłodziarka. Po prawej części urządzenia znajduję się zasobnik piasku wilgotnego w kształcie leja, do którego wsypywana jest masa. Następnie podajnikiem wibracyjnym masa przenoszona jest do miejsca w którym przez masę przepuszczone jest gorące powietrze. Pod podajnikiem wibracyjnym, na spodzie maszyny znajduję się wentylator suszarki, który produkuje obrót powietrza podczas całego procesu suszenia i chłodzenia. Obecne ciepło jest wyrażone w postaci Q i wynosi 100%. W początkowej fazie rozdmuchuje płomień przez co ciepłe powietrze idące w górę osusza masę. Nad osuszająca się masą znajduje się szeroki komin, przez które uchodzi powietrze oraz ciepło w wartościach 60% i 13,5%. Przez otwór znajdujący się w bocznej części urządzenia wydostaję się ciepło w wartości 2%.
Następnie masa wędruje podajnikiem i jednocześnie jest chłodzona przez wentylator znajdujący się pod kolejną częściom maszyny. Schłodzone powietrze jest częściowo odprowadzane przez pochyły komin na samym początku procesu chłodzenia. Komin doprowadza powietrze do ujścia znajdującego się nad cyklonem. Powstały suchy piasek zostaje umieszczony w zbiorniku specjalnie do tego przeznaczonym oraz którego ciepło wynosi 3%. Nad suchym już piaskiem jest umieszczony cyklon w kształcie wąskiego długiego leja, który kończy się ujściem ciepłego powietrza zakumulowanego w maszynie o wartości 21,5%. Na ilustracji zaznaczona jest droga jaką wprowadzony materiał przebywa przez całe urządzenie oraz zaznaczona jest też droga powietrza.
Odpylanie
Odpylacz to urządzenie umożliwiające wychwycenie pyłu z gazu lub powietrza i jego usunięcie. Podstawowym kryterium doboru odpylacza jest wielkość cząstek pyłu, które należy wychwycić.
Na sprawność pracy odpylaczyodpylaczy wpływa:
wielkość i masa właściwa ziarn pyłu,
wilgotność i zwilżalność (odpylacze mokre i tkaninowe),
własności elektrostatyczne pyłów,
zdolność do zlepiania się ziarn mniejszych w większe,
wybuchowość niektórych pyłów.
Rozdrabnianie
Rozdrabnianie stosuje się głównie przy regeneracji masy formierskiej. Wybitą z formy masę w celu regeneracji należy dokładnie rozkruszyć aby oddzielić materiał wiążący od osnowy piaskowej.
Najczęściej stosowanymi kruszarkami są kruszarki walcowe. Podstawową ich zaletą jest łatwość włączania w instalacje o ruchu ciągłym. Instaluje się je między przenośnikiem transportującym masę z krat do wybijania, a przesiewaczemprzesiewaczem.
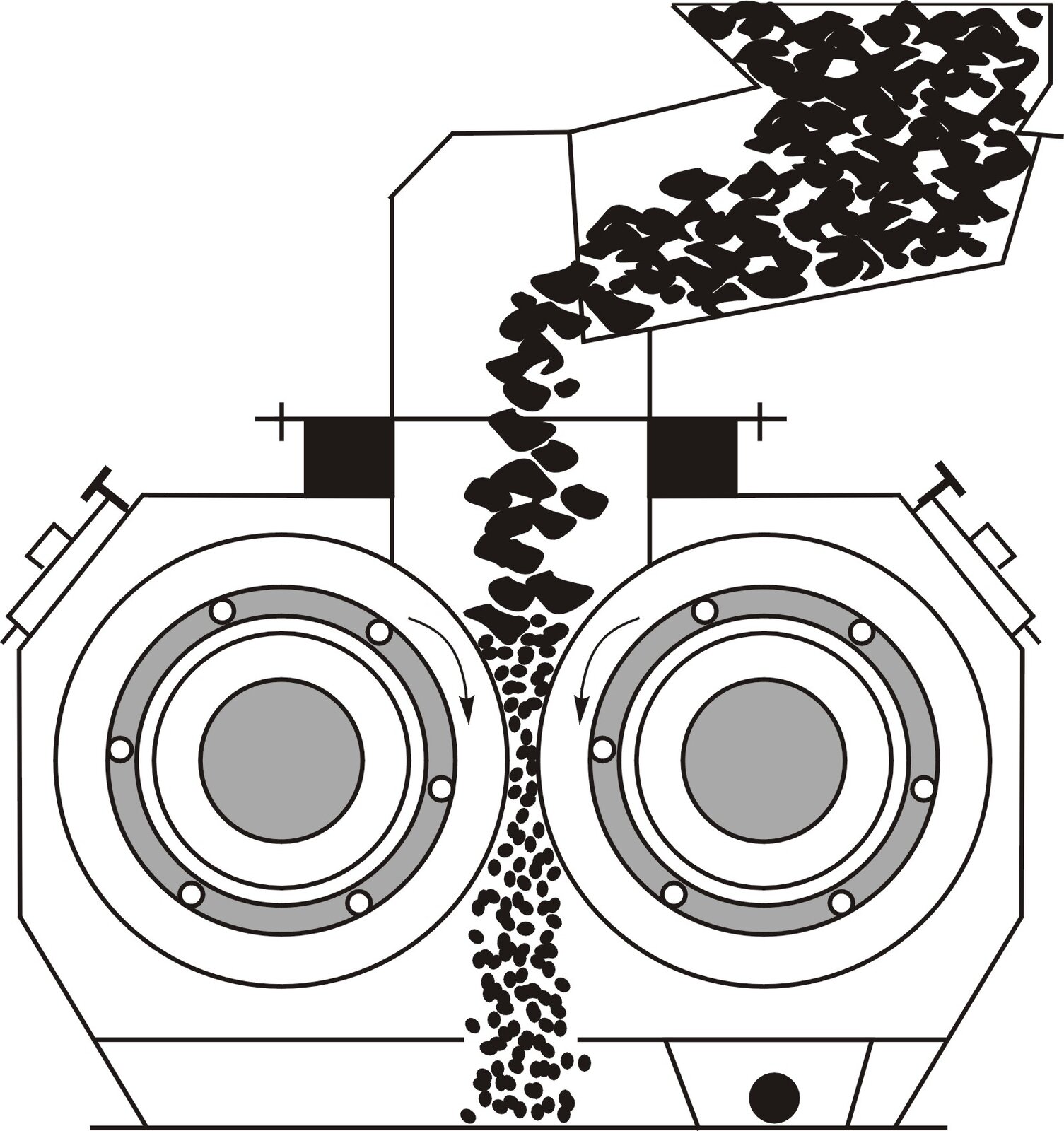
Kruszarka walcowa.
Na ilustracji przedstawiony jest schemat działania kruszarki walcowej. Główna część maszyny ma kształt prostokąta z poucinanymi rogami. Urządzenie posiada dwa walce, przedstawione na ilustracji jako koła o identycznych rozmiarach, które znajdują się w centralnej części korpusu maszyny. Koła te znajdują się na równej wysokości i oddalone są od siebie o niewielką odległość. Do górnej części maszyny przyłączony jest podajnik, zakończony częścią w kształcie leja. W podajniku znajduję się masa, w kształcie dużych kamieni, która następnie zostaje zsypana przez podajnik do części miedzy dwoma walcami, obracającymi się w swoją stronę. Na ilustracji zaznaczony jest kierunek obracania się walców. Masa zostaję rozkruszona miedzy kołami na drobniejsze elementy.
Kruszarki młotkowe stosuje się do bardzo twardych mas formierskich. Podawany od góry materiał jest wstępnie rozbijany przez przegubowo zawieszone młotki, spada następnie na ruszt gdzie jest kruszony do wymiarów otworów rusztu.
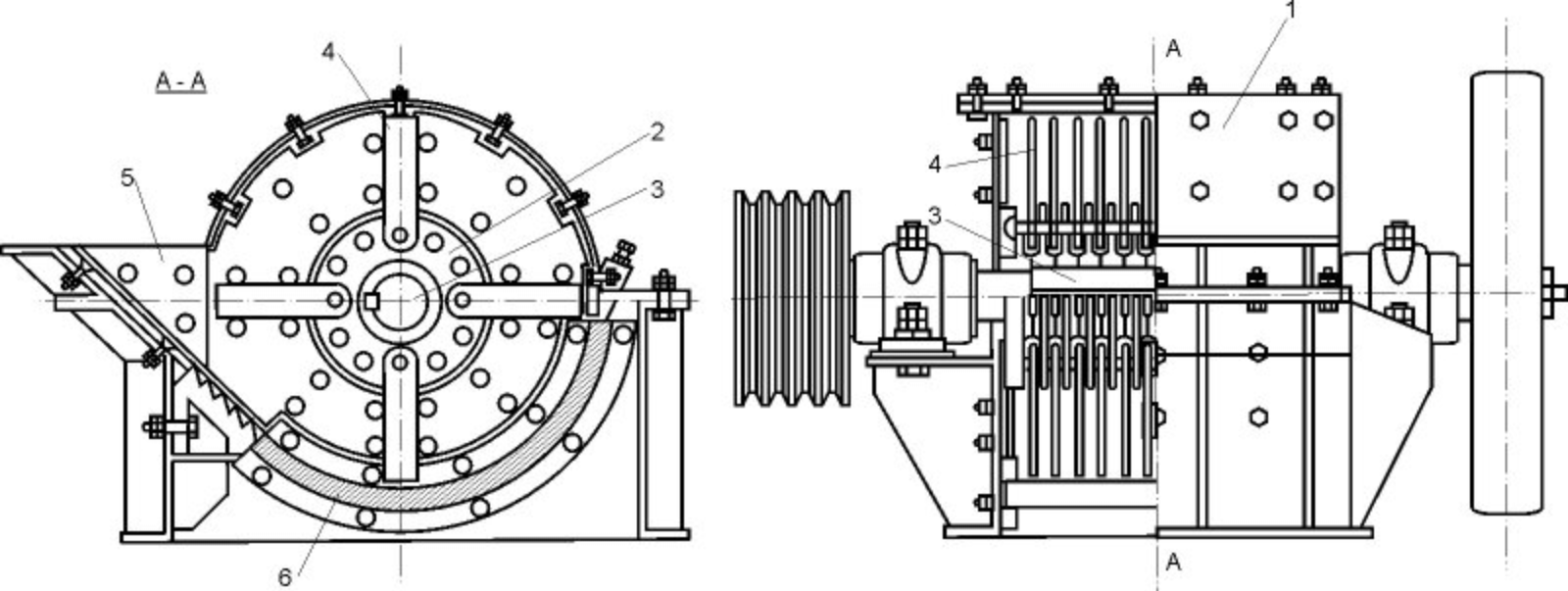
Na ilustracji przedstawione są dwa rysunki kruszarki młotkowej. Po lewej stronie znajduję się rysunek przekroju ozaznaczony symbolem A‑A. Kształt przekroju przypomina okrąg z wystającym trójkątem po lewej stronie. Całość umieszczona jest na dwóch słupach. Wyżej wymieniony trójkąt to lej załadunkowy, do którego wsypywana jest masa przeznaczona do rozdrobnienia. Wewnątrz maszyny znajduje się okrągła tarcz obrotowa, która obraca się po osi wału umieszczonego na środku. Do tarczy obrotowej zamontowane są młotki w kształcie prostokąta. Na spodzie wnętrza maszyny znajduję się półokrągły ruszt.
Po prawej stronie całej ilustracji znajduję się rysunek - pół widok‑pół przekrój kruszarki. Maszyna przedstawiona jest bokiem. Lewa strona maszyny stawowi jej przekrój, natomiast prawa strona przedstawia jej widok widziany z zewnątrz. Widoki te oddziela linia cienka przerywana, zakończona dużą literą A u dołu i góry. Po prawej stronie na widoku przedstawiony jest kadłub kruszarki, który przypomina kształtem prostokąt i jest zabezpieczeniem dla pracujących części maszyny. Po lewej stronie wewnątrz maszyny przedstawiony jest wał obrotowy znajdujący się w centralnej części maszyny. Od wału odchodzą wąskie prostokąty, które są młotkami. Całość maszyny przypomina kształt kwadratu z dwoma wypustami po bokach, przyczepionych do wału.
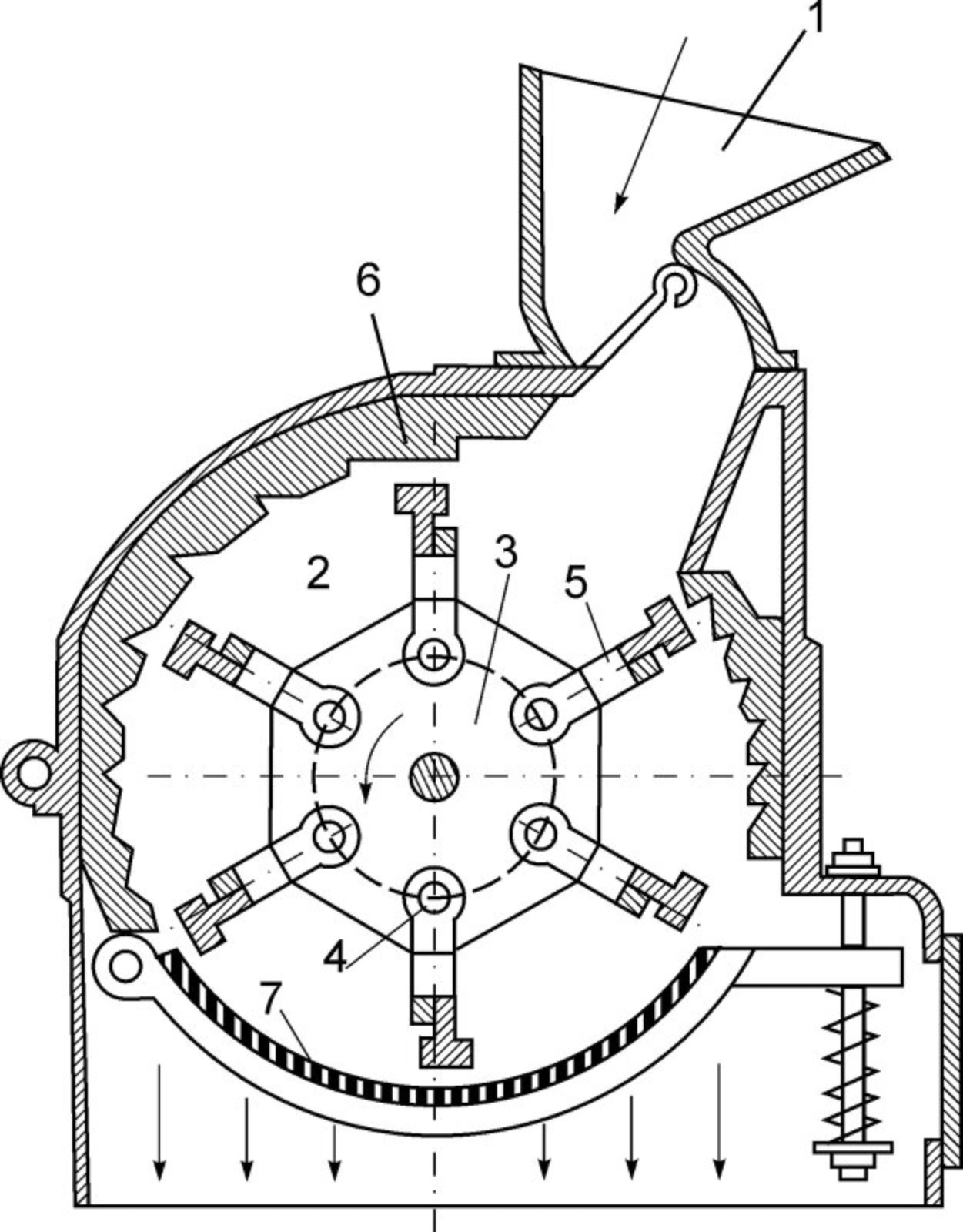
Ilustracja przedstawiony jest przekrój kruszarki młotkowej, która służy do rozdrabniania bardzo twardych mas formierskich. W prawym górnym rogu maszyny umieszczony jest lej załadunkowy, który służy do umieszczania masy do rozkruszenia. Wnętrze kruszarki ma kształtu podobny do koła, przy ściankach umieszczone są płyty odbojowe o nierównomiernym kształcie. W centralnej części wnętrza kruszarki znajduję się tarcza obrotowa w kształcie podobnym do koła , której obrót zaznaczony jest na ilustracji. Do tarczy zamontowanych jest sześć młotków, po obwodzie koła ramieniem montażowym. Młotki umieszczone są w równych odstępach pod kątem prostym do tarczy. Na spodzie wnętrza kruszarki znajduję się półokrągły ruszt, przez który spada rozdrobniona masa. Na schemacie zaznaczony jest kierunek spadania masy poniżej rusztu.
Kruszarki pneumatyczne stosuje się w instalacjach transportu pneumatycznego wybitej masy. Stosuje się je wtedy, gdy kawałki masy nie przekraczają średnicy rurociągu. Transportowana masa obija się o ścianki rurociągu oraz jednocześnie ziarna ocierają się o siebie pozbywając się materiału wiążącego.
Przykład takiego rozwiązania przedstawiono na poniższym rysunku.

Na ilustracji przedstawiona jest kruszarka pneumatyczna. Z lewej górnej strony urządzenia znajduję się wsyp przez który wpada masa przeznaczona do rozdrobnienia. Górna część wsypu ma kształt leja który zamienia się w korytarz, którym masa spada do komory. Następnie masa obsuwa się na dysze, którą podawane jest sprężone powietrze. Kierunek sprężonego powietrza jest przedstawiony na ilustracji. Piasek transportowany rurą strumieniową przez sprężone powietrze, a następnie z dużą siła uderza o górną część maszyny. Następnie piasek jest segregowany na wystarczająco oraz niewystraczająco rozdrobiony. Piasek gotowy spada na prawą stronę do wysypu, natomiast niewysączająco rozdrobniony na lewą stronę do komory, do ponownego przejścia procesu. Bardzo ważnym elementem jest instalacja odpylająca zamontowana nad urządzeniem w celu oczyszczenia powietrza.
Przesiewanie
Przesiewanie zachodzi, gdy występuje ruch surowca względem sita. Może być to związane z ruchem sita, lub grawitacyjnym przesuwaniem się surowca względem pochyłego sita.
Przesiewanie może być prowadzone przez jedno sito lub kilka sit w układach:
podsobnym,
nadsobnym,
mieszanym.
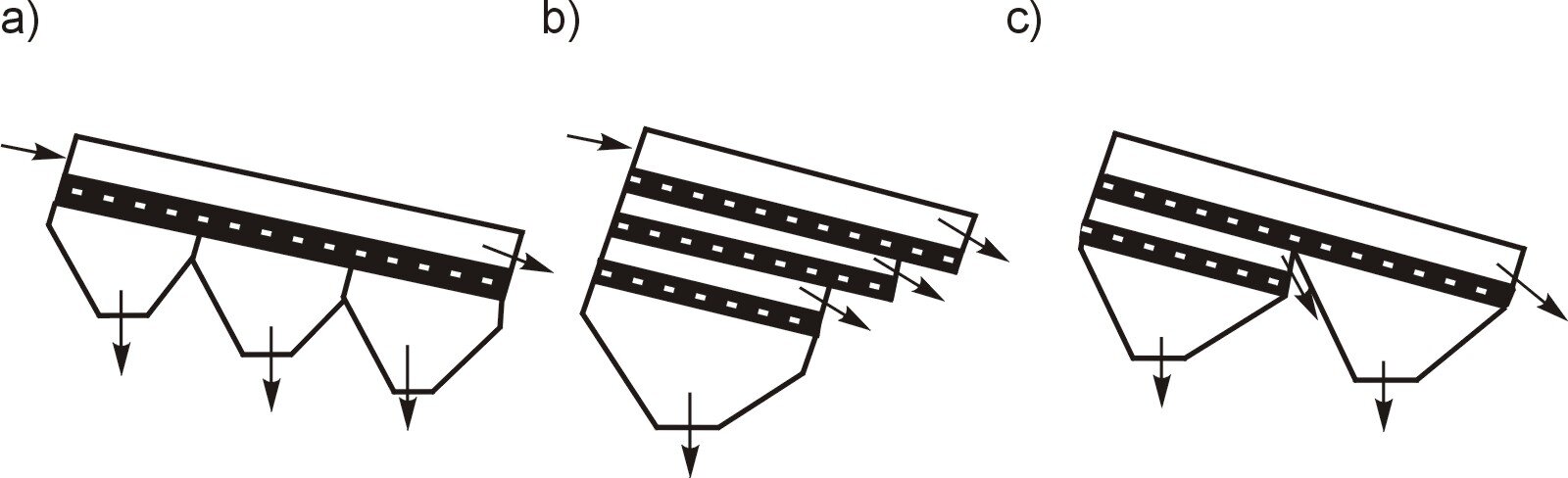
Na ilustracji przedstawione są trzy obrazki przedstawiające sita w różnych układach.
Sito przedstawione jest jako prostokątny, ciemniejszy element z jasnymi kreskami. Nas sitami zaznaczony jest prostokąt do którego wsypywany jest materiał do przesiania. Poniżej sit umieszczony jest element skupiający spadającą frakcję, przypomina kształt kanciastego leja. Strzałki zaznaczają kierunek przemieszczania masy na sitach oraz w dół poniżej nich.
Na pierwszym obrazku z lewej strony z podpunktem a) znajduję się sito w układzie podsobnym. Układ ten przedstawia trzy połączone ze sobą sita, które są pochylone w prawą stronę. Zakończone są trzema kanciastymi lejami. Strzałki zaznaczają kierunek przemieszczania masy na sitach oraz kierunek spadania masy przez kanciaste leje. Drugi obrazek b) przedstawia układ nadsobny, w którym trzy sita umieszczone są na sobie. Sita są pochylone na kąt około 30 stopni oraz każde z nich ma inną długość. Najdłuższe znajduję się najwyżej, a najkrótsze najniżej. Strzałki zaznaczają kierunek przemieszczania masy na sitach, tylko najniższe zakończone jest kanciastym lejem z którego wysypuje się przesiana frakcja.
Trzeci obrazek przedstawia układ c) mieszany w którym dwa sita są w jednej linii, natomiast trzecie znajduję się pod pierwszym sitem z lewej strony. Pod dwoma sitami oraz pod pojedynczym po prawej znajdują się kanciaste leje. Strzałki zaznaczają kierunek przemieszczania się masy na sitach oraz spadania przesianej frakcji w dół.
Rodzaje przesiewaczy wielokrotnych:
wahliwy,
wibracyjny,
bębnowy.
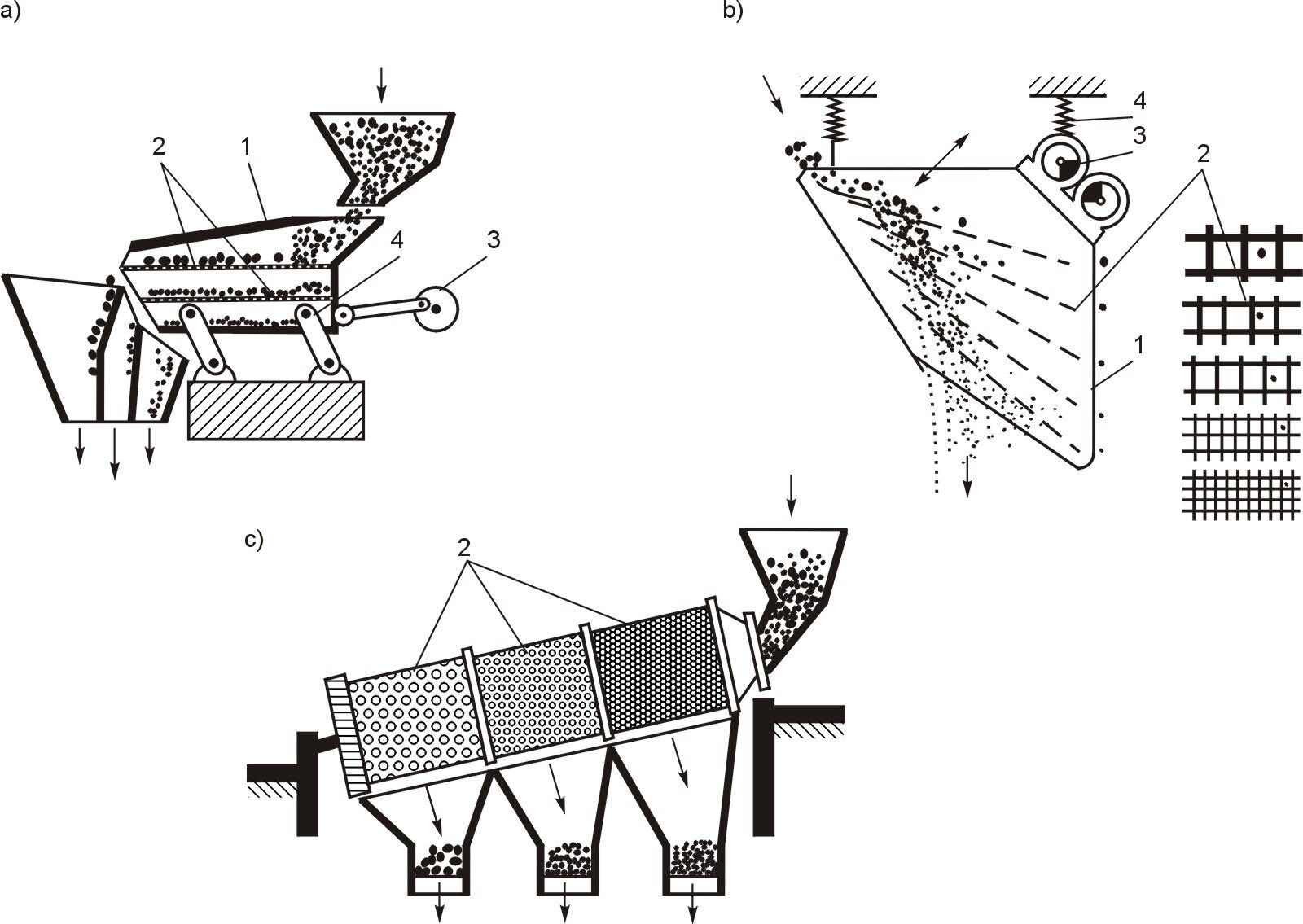
Na ilustracji przedstawione są trzy obrazki przedstawiające rodzaje przesiewaczy wielokrotnych. Na pierwszy obrazie a) widnieję przesiewacz wahliwy. Po prawej górnej stronie znajduję się lej, w którym umieszcza się masę do przesiania. W kolejnym kroku masa przedostaje się w dół - na pierwsze sito, gdzie zostaje przesiana, następnie drobniejsza frakcja trafia na kolejne (drugie) sito znajdujące się poniżej z drobniejszymi oczkami. Kolejny krok wygląda identycznie jak poprzedni – frakcja zostaje przesiana przez sito. Uzyskuję się frakcję odpowiedniej wielkości. Sita umieszczone są w wielokątnej obudowie. Pod obudową znajdują się elementy sprężyste dzięki którym, wszystkie sita mogą się poruszać, a masa zostaje przesiana. Po prawej stronie maszyny znajduję się napęd w kształcie koła z rączką. Po lewej stronie znajduję się zsyp podzielony na trzy części, w którym elementy które nie zostały przesiane przez poszczególne sita – zanieczyszczenia czy ciała obce znajdują ujście.
Kolejny obraz b) przedstawia przesiewacz wielokrotny wibracyjny. Od góry przesiewacz umieszczony jest na dwóch elementach sprężystych. Przy prawym elemencie sprężystym znajduję się napęd w postaci dwóch małych kółek. Wewnątrz obudowy umieszczonych jest pięć sit o różnej wielkości oczek, na które spada masa. W lewym górnym rogu masa wpada na pierwsze sito. Po prawej stronie znajduję się pięć kratek przedstawiających wielkość oczek w sitach. Na spodzie maszyny znajduję się zsyp dla przesianej już frakcji. Na obrazku przedstawiony jest kierunek przesiewania masy oraz kierunek drgań maszyny.
Na obrazku trzecim c) widnieję przesiewacz wielokrotny bębnowy. Po prawej stronie znajduję się wsyp do masy, którą należy przesiać. Wsyp jest w kształcie leja. Następnie masa trafia do bębnów, które są sitami. Frakcja trafia kolejno do sita o najmniejszych oczkach, następnie średnich i największych. Bębny pochylone są pod lekkim kątem w celu lepszego przesuwania się masy. Pod urządzeniem (dokładnie pod każdym z bębnów) zamontowane są trzy silosy dla posegregowanych frakcji.
Przesiewanie ma na celu usunięcie z przesiewanego materiału ciał obcych oraz jego podział na podziarno (przesiew) i nadziarno (odsiew). Przesiewanie przyczynia się także do ujednorodnienia ziarnistości piasków i mas formierskich co ułatwia ich dalszą przeróbkę zwłaszcza wymieszanie z materiałem wiążącym.
Przesiewacze wibracyjne charakteryzują się tym, że zamiast wahaczy stosuje się w nich zawieszenie sprężyste.
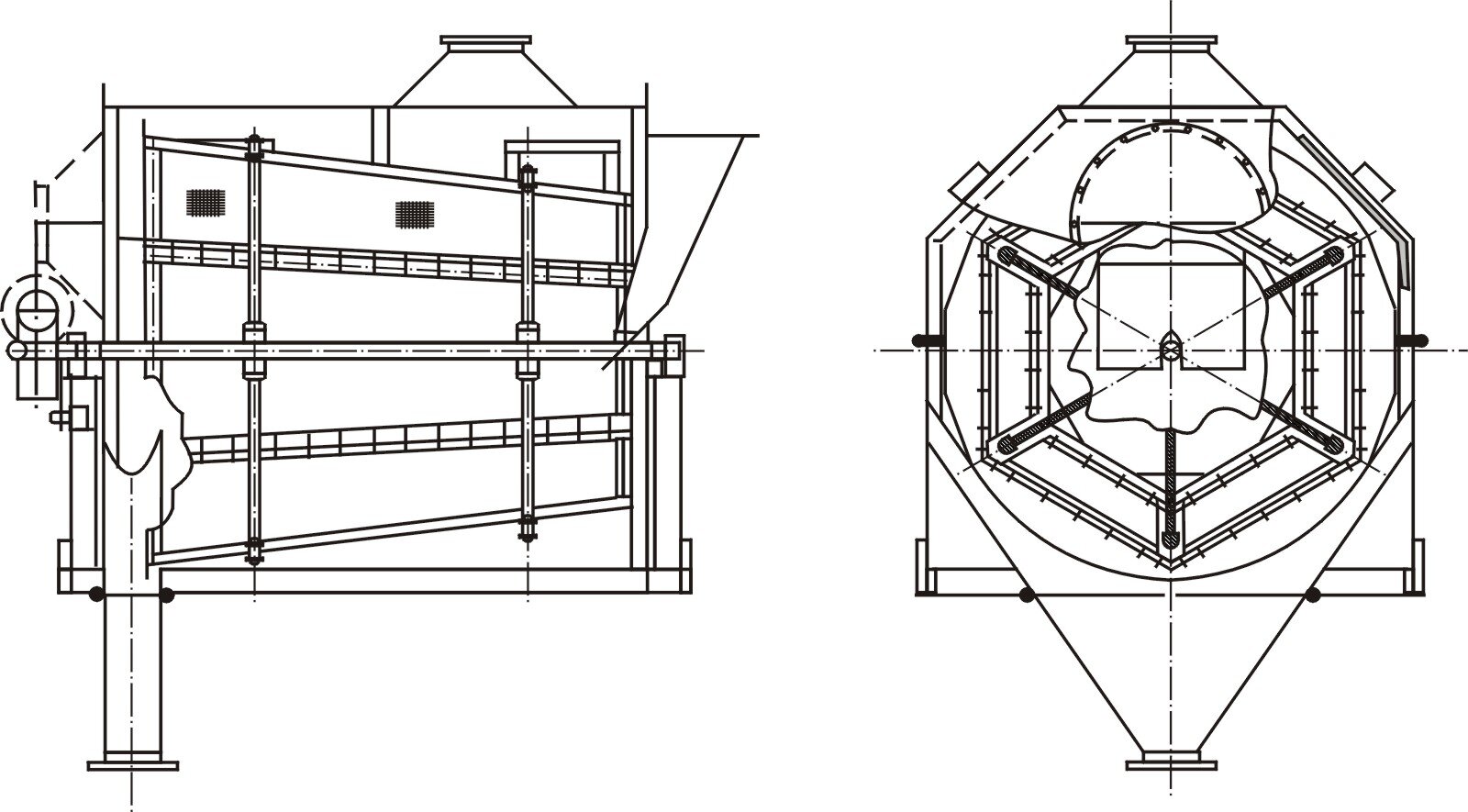
Na ilustracji przedstawiony jest przesiewacz obrotowy w dwóch widokach. Po lewej stronie rysunek ukazuję przekrój boczny maszyny. Do korpusu u dołu jest przymocowana rama nośna maszyny, która ciągnie się pod całym korpusem oraz po lewej stronie posiada kształt długiego prostokąta w stronę dołu, zakończonego stopką. Po prawej stronie na boku korpusu umieszczony jest zbiornik na zasyp materiału, w kształcie długiego leja. Do górnej części korpusu po prawej stronie jest zamontowany króciec odpylający oraz zasłona. Jest ona w kształcie odwróconego grubego leja. Taki sam króciec jest narysowany linią przerwana po lewej stronie na ścianie korpusu, oznacza to iż jest to korpus zamontowywany w zależności od trasy instalacji odpylającej. Pod spodem znajduję się zespół napędowy, który jest podwieszony na końcówce wału obrotowego. Ma kształt prostokąta zakończonego małym okręgiem. Wewnątrz maszyny umieszczony jest wał obrotowy, który umieszczony jest na samym środku przez cała długość maszyny. Wewnątrz maszyny znajduje się sito obrotowe, które stanowi ostrosłup ścięty o podstawie sześciokąta o pochyleniu ścian bocznych 7Indeks górny oo.
Miedzy stalową ramą sita, a wałem napędowym u góry i u dołu zamontowane są po dwa ścięgna. W górnej części korpusu przedstawione są dwie kratki, które są wziernikami.
Po prawej stronie obraz przedstawia przesiewacz obrotowy od przodu. Wewnątrz widnieje podstawa sita o podstawie sześciokąta. U dołu przedstawiona jest rama nośna, która ma kształt trójkąta stojącego na stopce. Natomiast u góry, ponad korpusem jest króciec opylający w tym samym kształcie co na rysunku poprzednim.
Mieszanie
Mieszanie ma na celu w jak najkrótszym czasie i przy minimalnym zużyciu energii otrzymanie z kilku różnych składników mieszaniny jednorodnej.
W mieszarkachmieszarkach mogą zachodzić trzy rodzaje procesów mieszania:
Mieszanie konwekcyjne – przenoszenie grup graniczących ze sobą cząstek z jednego miejsca mieszaniny do drugiego.
Mieszanie dyfuzyjne – rozkład cząstek powyżej świeżo rozwiniętej powierzchni.
Mieszanie przez ścinanie – ustawianie (kierowanie) ślizgających się strug odciętych od całości mieszaniny.
Procesy przerobu mas formierskich i rdzeniowych polegają na:
przerzucaniu,
ugniataniu,
rozcieraniu,
spulchnianiu.
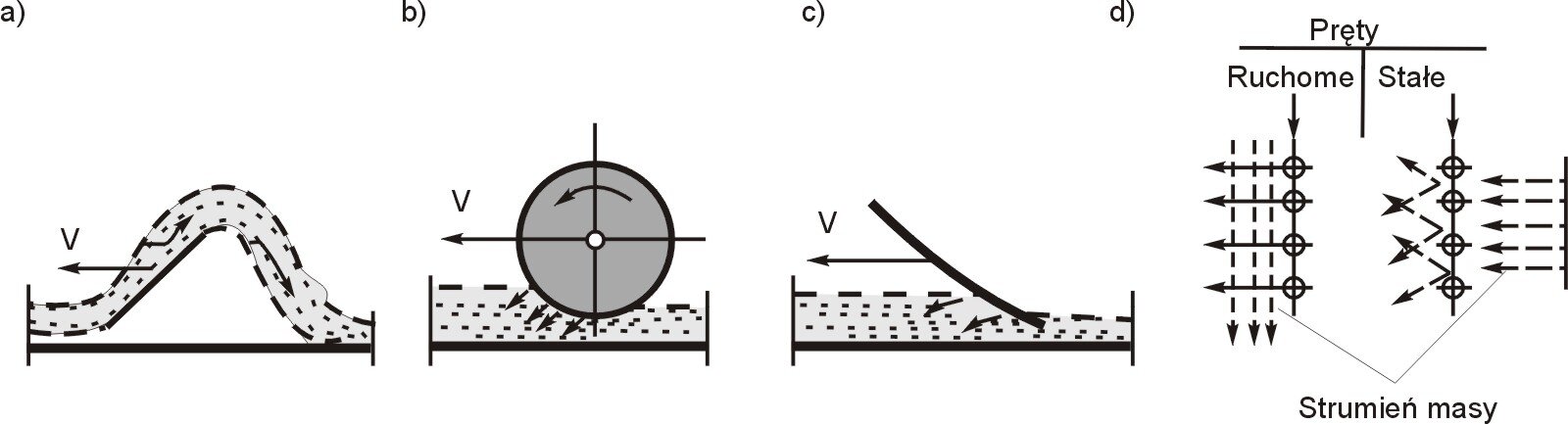
Na ilustracji widnieją są cztery rysunki przedstawiające procesy przerobu mas formierskich i rdzeniowych. Na rysunku pierwszym a) przedstawione jest przerzucanie masy. Masa przedstawiona jest jako zacienione pole, które przesypuję się nad jasnym wałem. Zaznaczony jest kierunek przesypywania się masy oraz kierunek prędkości wału poprzez listerę v. Na rysunku drugim b) przedstawione jest zgniatanie. Po ciemniejszej masie przesuwa się ciemna kula w celu jej ugniecenia. Przedstawiony jest kierunek obrotu kuli, kierunek prędkości v oraz proces ugniatania mas przez tą kulę. Wszystko następuję w tą samą stronę. Na rysunku trzecim c) przedstawione jest rozcieranie masy. Wcześniej ugnieciona masa zostaje przygładzona przez ciemną linię. Przedstawiony jest kierunek rozcierania masy z prędkością v. Na ostatnim, czwartym rysunku d) przedstawione jest spulchnianie. Po prawej stronie są cztery małe kółka, które przedstawiają pręty stałe oraz strzałki przedstawiające strumień masy który rozchodzi się na przemian. Natomiast po lewej stronie są przedstawione cztery koła, które przedstawiają pręty ruchome oraz strumień masy biegnący prostopadle do linii prętów.
W mieszarkach skrzydłowych występuje głównie mieszanie konwekcyjne. Elementem mieszającym są skrzydła osadzone na pionowym wale. Przemieszczanie masy przez łopatki powoduje jej spulchnianie.
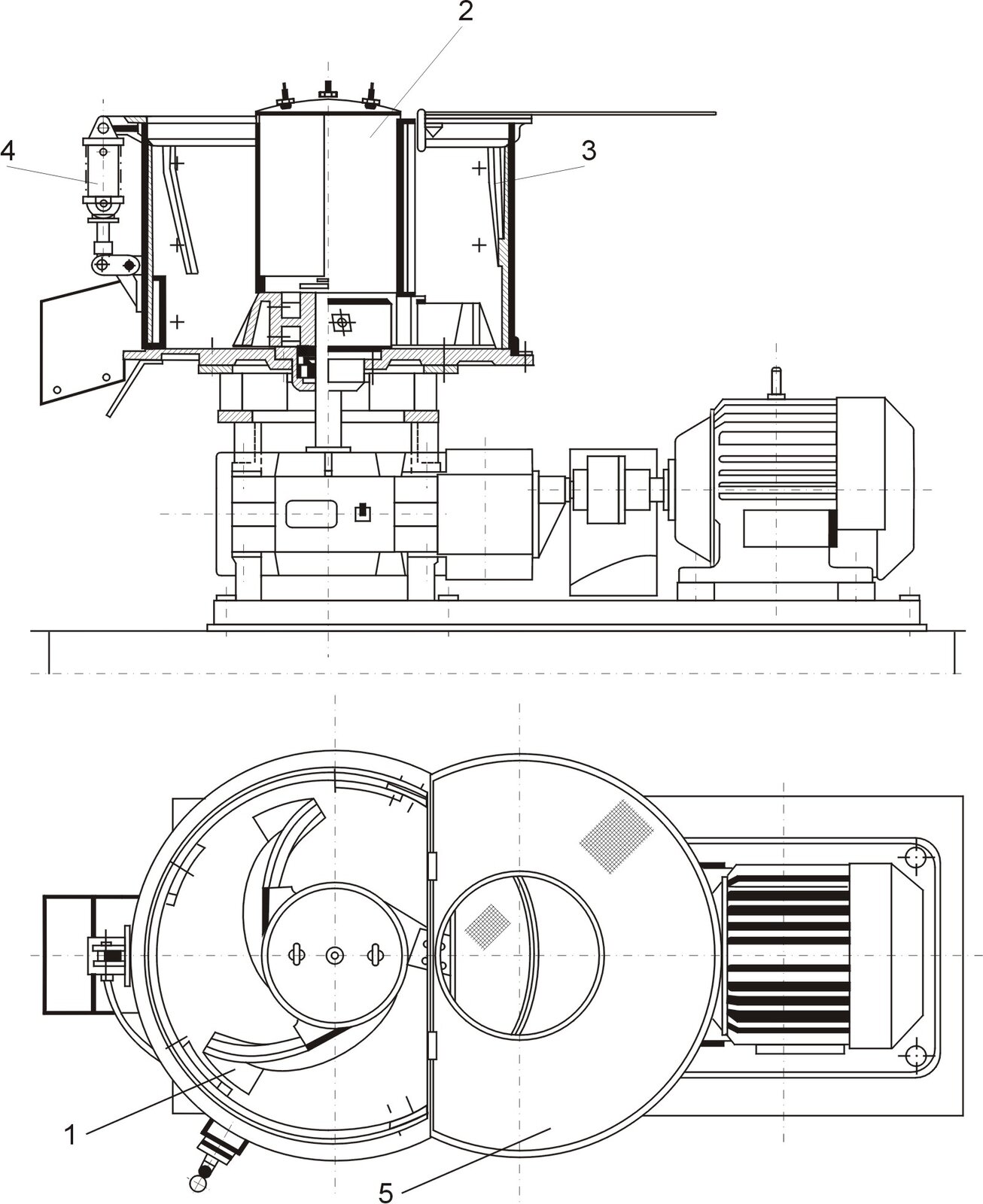
Na ilustracji przestawione są dwa widoki mieszarki skrzydłowej. Pierwszy widok ukazuję przekrój mieszarki z bocznej perspektywy. Dolną częścią maszyny jest silnik, nad którym po lewej stronie znajduję się jej główna część. Mieszarka ma kształt walca, natomiast w przekroju widoczny jest kształt prostokąta. W centralnej część znajduje się osłona, natomiast w środku na krawędziach są wkłady żeliwne. Na zewnątrz, po lewej stronie do mieszarki zamontowany jest siłownik pneumatyczny.
Drugi widok przedstawia mieszarkę skrzydłową od góry. Otworzona klapa uchylna daję dostęp do wnętrza mieszarki. Klapa oraz cała maszyna od góry ma kształt koła. Do osłony znajdującej się na samym środku zamontowane są trzy wymienne wkłady mieszadła, które mają zaokrąglony kształt. Mieszadła służą do spulchniania masy.
Mieszarki łopatkowe pracują zazwyczaj w ruchu ciągłym. Stosuje się je do transportu i chłodzenia wybitej masy formierskiej.
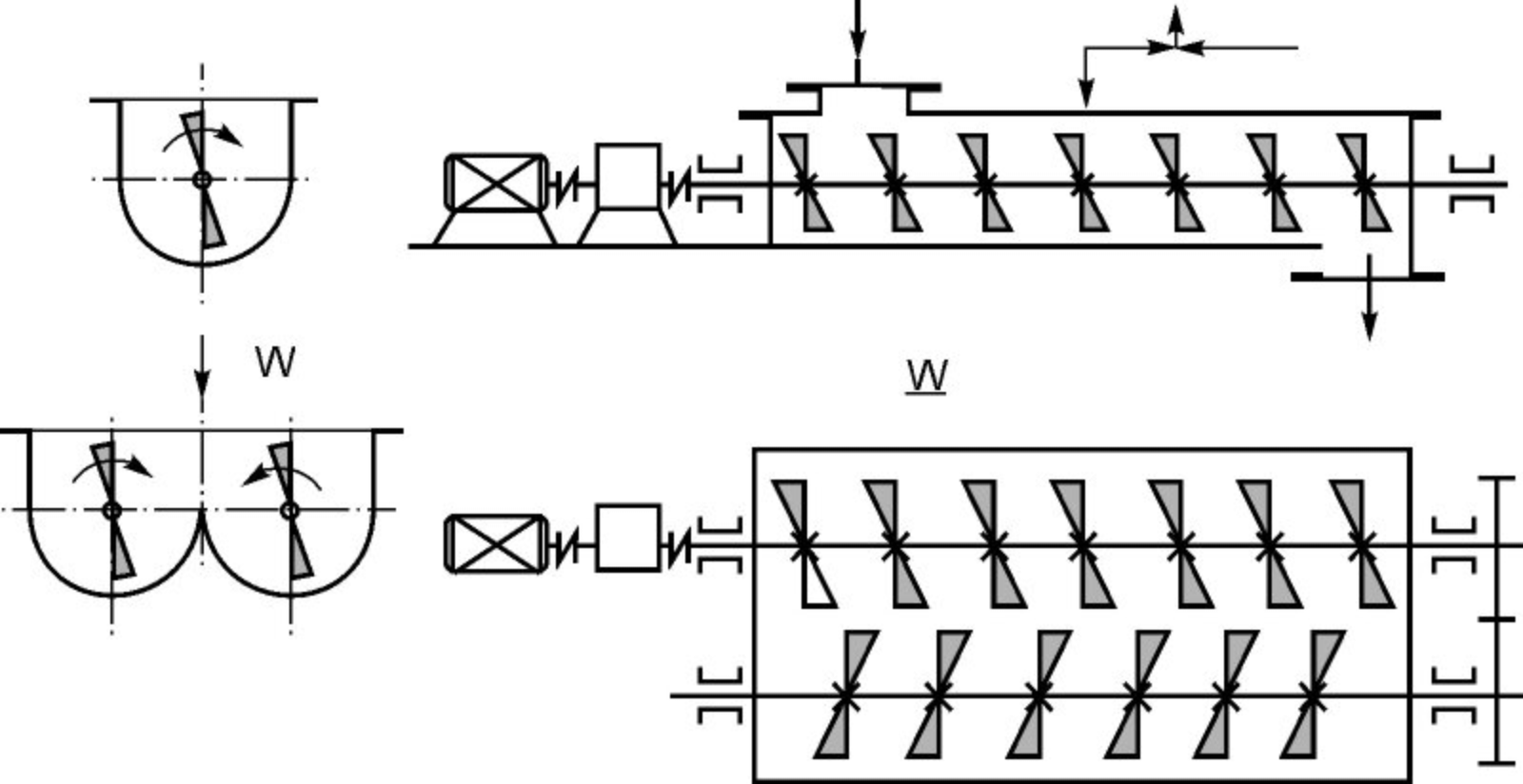
Na ilustracji przedstawiona jest mieszarka łopatowa o osi poziomej jednowałowa i dwuwałowa.
Na górze ilustracji przedstawiona jest mieszarka łopatkowa o osi poziomej jednowałowa z bocznej oraz górnej perspektywy. Z perspektywy bocznej mieszarka ma kształt półkola z wydłużonymi bokami, ustawionego półkolem do dołu. Wewnątrz znajduję się łopatka, która służy do mieszania masy znajdującej się wewnątrz urządzenia. W perspektywie górnej mieszarka ma kształt prostokąta, który z jednej strony zakończony jest silnikiem, a z drugiej wysypem. Wewnątrz znajduję się siedem łopatek do mieszania masy. Na dole ilustracji przedstawiona jest mieszarka łopatkowa o osi poziomej dwuwałowa również z bocznej i górnej perspektywy. Z perspektywy bocznej mieszarka ma kształt dwóch półkul z wydłużonymi bokami, połączonych ze sobą. Wewnątrz znajdują się dwie łopatki. Z perspektywy górnej ukazane dwa rzędy łopatek (w górnym rzędzie siedem, w dolnym sześć). Perspektywa ma kształt prostokąta zakończonego silnikiem oraz wsypami.
Mieszarki krążnikowe służą do sporządzania mas formierskich i rdzeniowych, ze składników świeżych i zwrotnych, naturalnych i syntetycznych. Mieszarki typu MK są przeznaczone do pracy w odlewniach, zmechanizowanych i zautomatyzowanych stacjach przerobu mas, w warunkach temperatuy dodatniej. W procesie mieszania następują intensywne procesy przerzucania masy, ugniatania i rozcierania, przez co mieszarki krążnikowe doskonale nadają się do sporządzania mas ze składników naturalnych i ze zbrylonej masy używanej. Proces mieszania odbywa się za pomocą obracającego się wewnątrz misy mieszarki zespołu mieszającego, złożonego z lemieszylemieszy i krążników. Wyładowanie gotowej masy odbywa się po otwarciu klapy wyładowczej znajdującej się w dnie mieszarki. Mieszarka jest przystosowana do pracy w cyklu automatycznym i ręcznym.
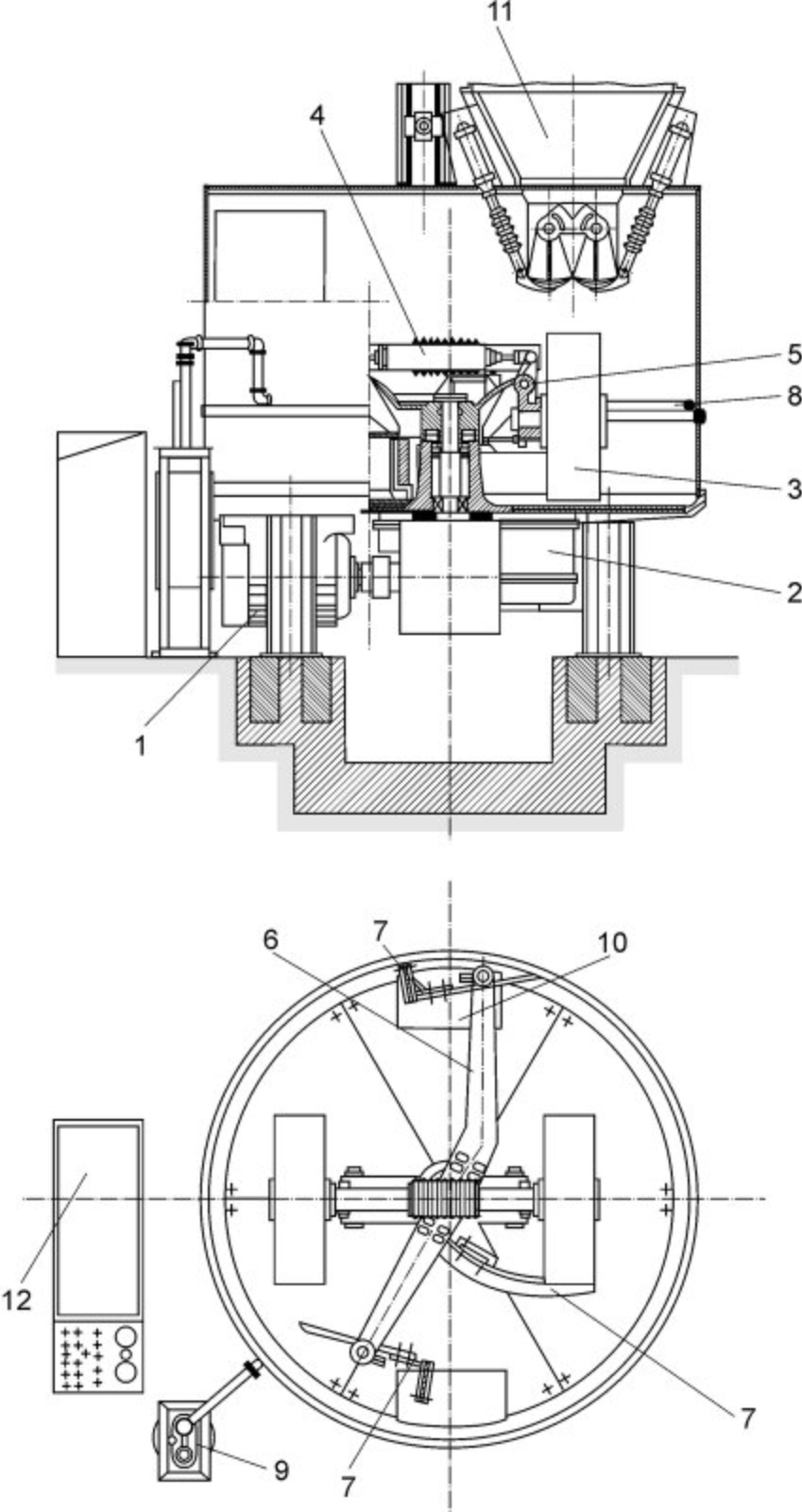
Na ilustracji przedstawiona jest mieszarka krążnikowa w dwóch widokach. Na górze ilustracji widnieje przekrój mieszarki z perspektyw bocznej.
Na samej górze mieszarki po prawej stronie jest dozownik, w którym umieszcza się piasek przeznaczony do zrobienia masy. Wewnątrz maszyny, na środku znajduje się mechanizm składający się ze sprężyny oraz wahacza połączonego z krążnikiem w kształcie prostokąta. Po lewej stronie od krążnika umieszczone są cienkie rurki – widoczne jako prostokąty, służące do doprowadzenia wody do maszyny. Pod opisanym mechanizmem znajduje się przekładnia, widoczna na obrazku jako prostokąt. Po lewej stronie obok mechanizmu ze sprężyną pokazany jest widok maszyny z zewnątrz w małym prostokącie, oddzielonym od wewnętrznej części linią ciągła przerywaną. Pod tym właśnie prostokątem widnieje mechanizm silnika, który napędza całą maszynę do pracy.
Na dolnym obrazku, mieszarka krążnikowa przedstawiona widokiem od góry ma kształt okręgu. Wewnątrz na samym środku widnieje sprężyna, pod którą od środka odchodzi ramię maszyny. Do ramienia na końcach umieszczone są rolki oraz lemiesze, służące do dokładnego wymieszania. Dodatkowy lemiesz jest przymocowany do środkowej części maszyny, jest on zaokrąglony. Na górze okręgu jest umieszczony otwór wysypowy, w kształcie prostokąta, przez który gotowa masa znajduję ujście. Po lewej dolnej stronie od maszyny znajduję się prostokąt, z dwoma małymi okręgami w środku. Jeden z okręgów jest połączony prostokątem z korpusem maszyny, jest to dozownik wody. Również po lewej stronie maszyny przedstawiona jest prostokątna szafa sterująca, z krzyżykami oraz kółkami na dole, które odzwierciedlają przyciski do sterowania.
Mieszarki pobocznicowe służą do sporządzania mas formierskich ze składników świeżych i zwrotnych naturalnych i syntetycznych. Mieszarki przeznaczone są do pracy w odlewniach, w zmechanizowanych i zautomatyzowanych stacjach przerobu mas w warunkach temperatur dodatnich. Odmierzone przy pomocy dozowników i załadowane do mieszarek składniki masy formierskiej podlegają procesowi mieszania za pomocą obracającego się wewnątrz mieszarki zespołu mieszającego złożonego z lemieszy i rolek. Powietrze z wentylatora wdmuchiwane w odpowiednim czasie do mieszarki chłodzi oraz spulchnia przerabianą masę. Wyładowanie gotowej masy odbywa się po otwarciu klapy wyładowczej znajdującej się na bocznej ścianie mieszarki. Mieszarki przystosowane są do pracy w cyklu automatycznym i ręcznym. Mieszarki wymagają podłączenia do instalacji odpylającej.
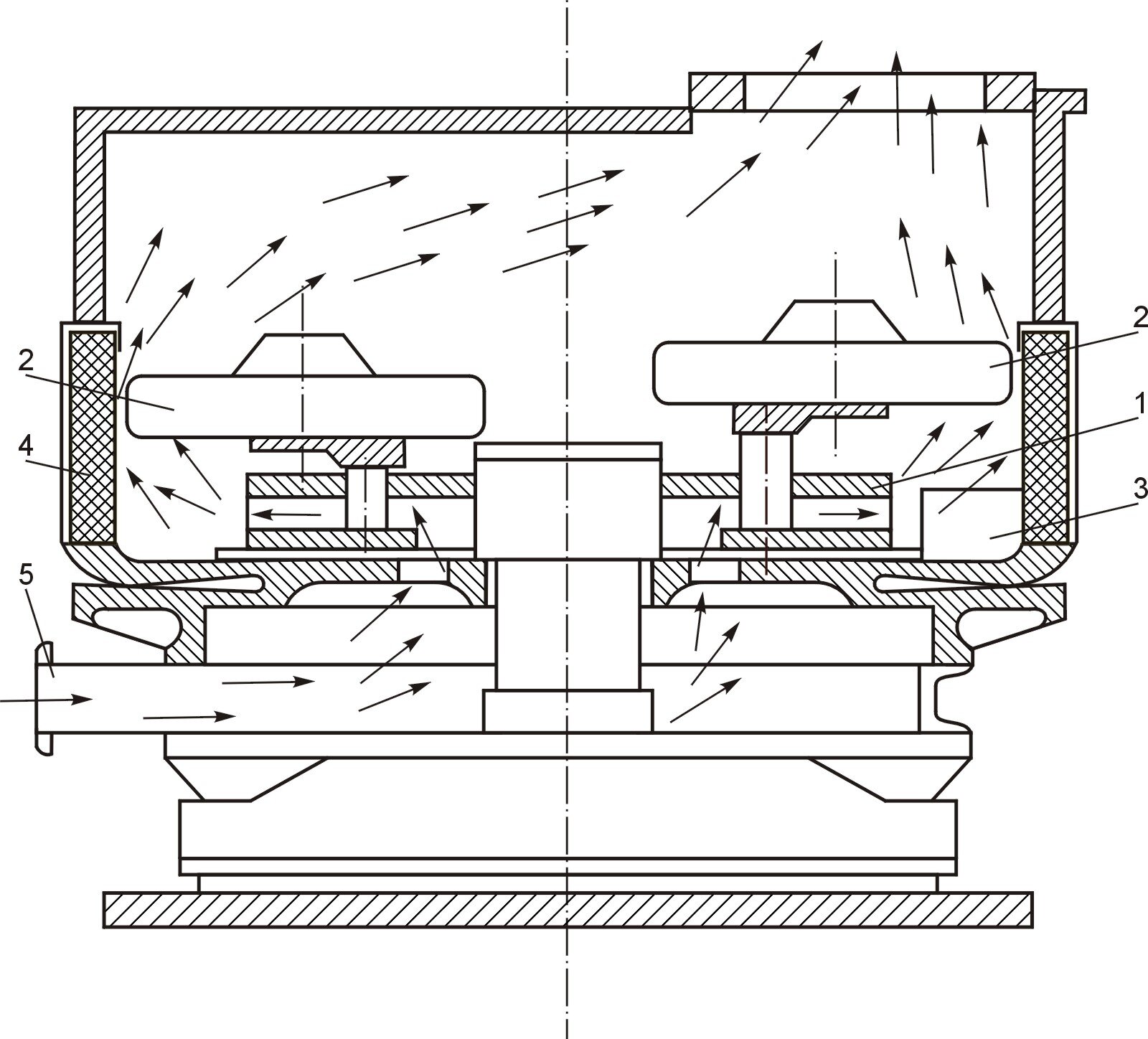
5 - dmuch, 6 - odciąg
Na ilustracji przedstawiony jest przekrój mieszarki pobocznicowej widzianej od boku. Mieszarka umieszczona jest na płaskim podłożu. U podstawy po lewej stronie urządzenie posiada miejsce przeznaczone na dmuch sprężonego powietrza. Powietrze przedostaję się w głąb maszyny wąskim i długim prostokątem. Na samym środku umieszczony jest prostokąt, od którego na dwie strony odchodzą małe elementy łączące z nim dwa krążniki. Krążnik po prawej stornie umieszczony jest nieco wyżej niż lewy. Krążniki od boku mają kształt długiego zaokrąglonego prostokąta, z odwróconym trapezem równoramiennym na górze. Pod krążnikami na całej długości umieszczona jest tarcza. Po obu stronach przedstawiona jest obudowa urządzenia zakrywająca cały środek maszyny. Po bokach dodatkowo zamontowane są gumowe wykładziny, będące zakreskowanym w dwie strony prostokątem. Z prawej dolnej strony przy tarczy znajduje się lemiesz. Obudowa urządzenia posiada ujście z prawej strony w dachu obudowy, jest to miejsce którym wydostaję się sprężone powietrze umieszczone na początku procesu w maszynie. Elementy obudowy oraz tarcza
zostały zakreskowane. Na ilustracji przedstawiony jest kierunek przemieszczania się sprężonego powietrza w mieszarce.
Mieszarki dynamiczne (turbinowe) można podzielić na grupy:
Grupa – posiada:
misę obrotową łącznie z obrotowym dnem,
turbinę stacjonarną – lub w zależności od wielkości maszyny,
mieszadło stacjonarne.
Grupa – posiada:
obrotowe dno,
misę stałą,
turbinę stacjonarną.
Grupa – posiada:
stałą misę,
stałe dno,
turbinę obracającą się ruchem planetarnym wokół osi misy.
Wyposażenie mieszarki dynamicznej w charakterystyczny dla tej techniki mieszania szybko obracający się wirnik (turbinę), którego napęd i konstrukcja umożliwia dostosowanie mieszarki do konsystencji i uziarnienia masy oraz dodatkowe narzędzie w postaci lemiesza kierującego otwierają cały szereg możliwości wpływania na proces:
prędkość wirnika można regulować w szerokim zakresie, aby umożliwić zmianę energii,
wprowadzanej do procesu mieszania,
kierunek działania narzędzia mieszającego – współbieżny lub przeciwbieżny,
indywidualne geometrie narzędzi dostosowane do danego zadania.
Mieszarki turbinowe pozwalają uzyskać masę o najlepszym stopniu spulchnienia i zadowalających parametrach wytrzymałościowych. W mieszarkach turbinowych uzyskujemy masę o bardzo dobrej przepuszczalności i wysokiej płynności. Duża wytrzymałość w strefie przewilżonej przy wystarczających pozostałych parametrach i stosunkowo krótkim czasie mieszania potwierdzają przydatność tego typu mieszarek do wykonywania mas formierskich bentonitowych.
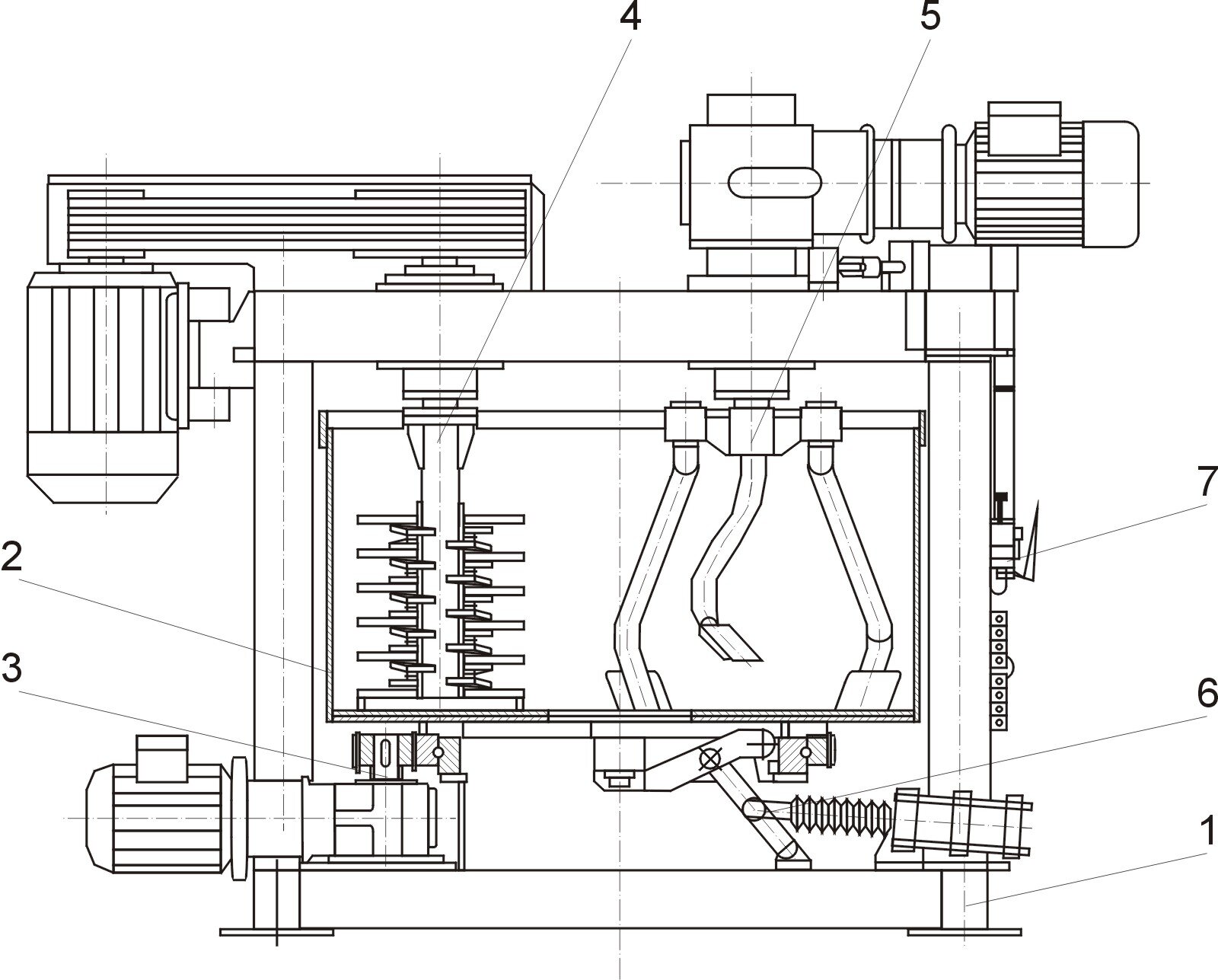
Na ilustracji przedstawiony jest przekrój mieszarki turbinowej widzianej od boku. Budowa mieszarki, która chroni wewnętrzne części maszyny ma kształt kwadratu i umieszczona jest na dwóch nóżkach stanowiących konstrukcję nośną. Po lewej stronie, u dołu znajduje się zespół napędu misy, którego część wystaję poza obudowę. Na przeciwko napędu misy znajduje się zespół klapy wysypowej. Następnie nad zespołem napędu misy oraz klapy wysypowej, wewnątrz urządzenia przedstawiony jest prostokąt, który jest misą obrotową. Wewnątrz tego właśnie prostokąta znajduję zespół turbiny z napędem po lewej stronie oraz zespół mieszadła z napędem po prawej. Oba napędy mają część zewnętrzną, która wystaję ponad obudowę, wewnątrz znajdują się tylko mieszadła oraz turbina. Zespół mieszadła posiada trzy długie zaokrąglone mieszadła sięgające do podstawy misy. Zespół turbiny z napędem posiada turbinę z wystającymi elementami, w celu spulchniania masy.
Dodatkowo po prawej stronie na obudowie po zewnętrznej części znajduję się zespół centralnego smarowania.
Spulchnianie
Spulchnianie stosuje się w celu ujednolicenia masy formierskiej, zwiększenia jej przepuszczalności oraz czasami obniżenia temperatury masy.
Spulchniarki palcowa i turbinowa zostały przedstawione w sekwencjach filmowych.
Spulchniarki nadtaśmowe instaluje się w ciągach przerobu mas za mieszarkami, nad typowymi przenośnikami taśmowymi rozprowadzającymi masę do zbiorników na stanowiskach formierskich.
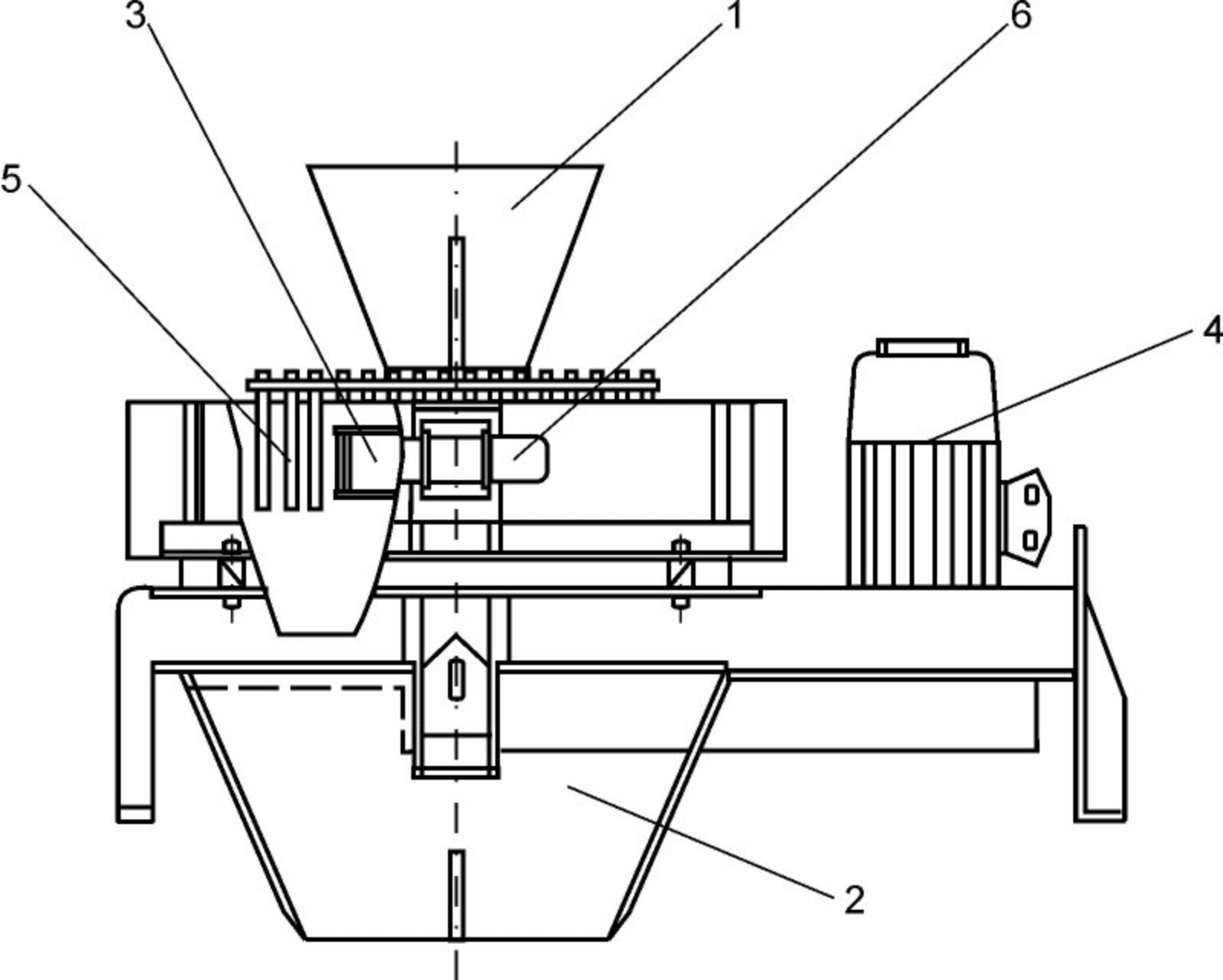
Na ilustracji przedstawiona jest spulchniarka nadtaśmowa. Na samym szczycie maszyny znajduję się wsyp masy w kształcie odwróconego trapezu równoramiennego. Zaraz pod wsypem jest przesłona prętowa wibracyjna, której trzy odsłonięte prostokątne pręty widnieją po lewej stornie. Natomiast reszta schowana jest za środkiem maszyny, w kształcie szerokiego i niskiego prostokąta. Obok prętów przedstawiony jest wirnik palcowy, natomiast na prawo od niego jest wibrator, który służy do wprawiania maszyny w ruch. Oba urządzenia mają kształt podobny do kwadratów. Po prawe stronie jako oddzielny element przyłączony do podstawy urządzenia znajduję się napęd wirnika, którzy przypomina kształtem kwadrat. Pod główną częścią maszyny przedstawiony jest wysyp masy w kształci dużego trapezu równoramiennego, odwróconego o 180Indeks górny oo.
Oddzielacze elektromagnetyczne bębnowe przeznaczone są do oddzielania w sposób ciągły zanieczyszczeń ferromagnetycznych zawartych w materiałach sypkich lub kawałkowatych przenoszonych na taśmie gumowej przenośnika stanowiąc równocześnie jego bęben napędowy.
Zostały przedstawione w sekwencjach filmowych ad.7
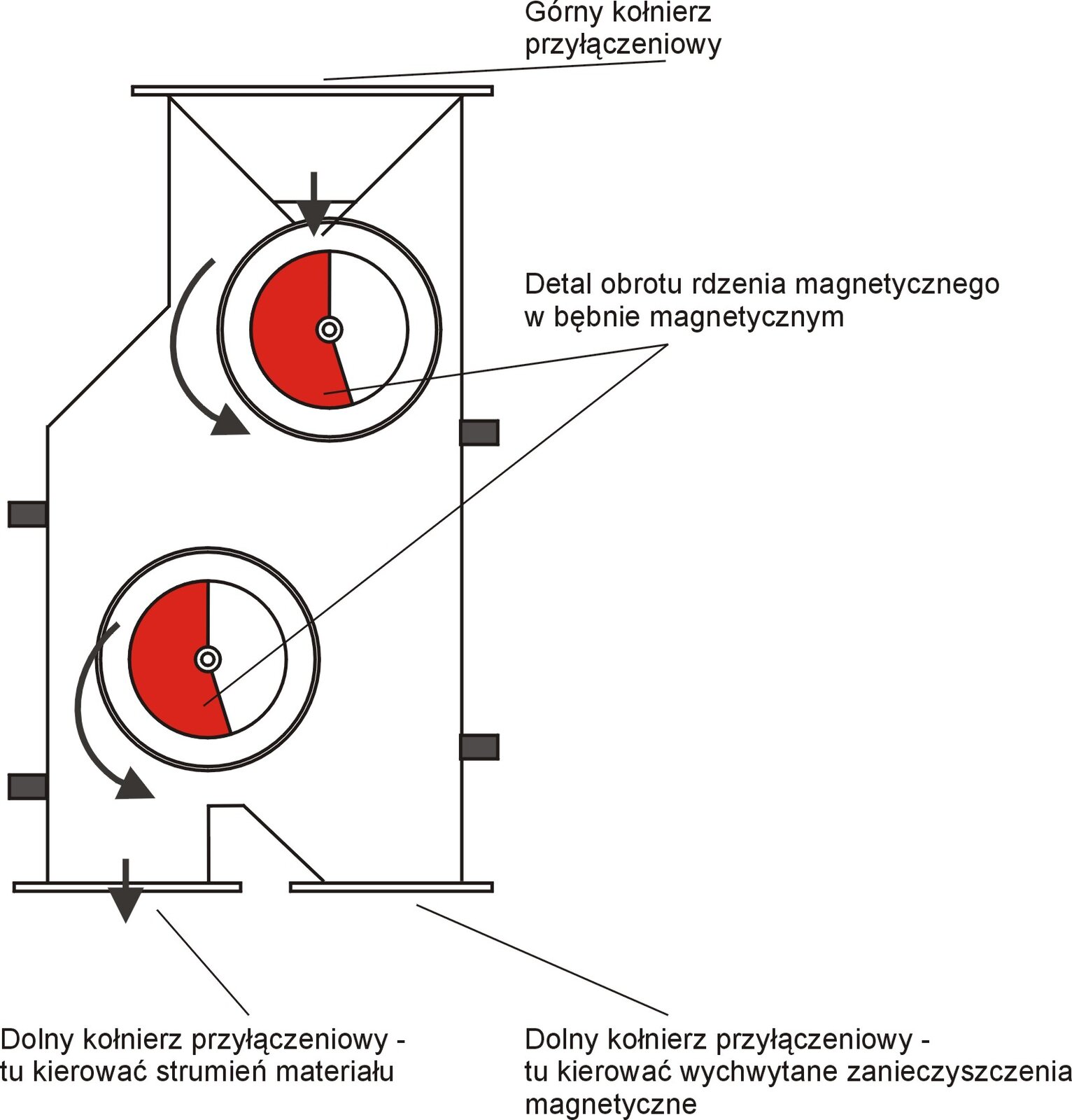
Na ilustracji przedstawiono oddzielacz elektromagnetyczny bębnowy. Urządzenie posiada trzy kołnierze, jeden znajduje się na górze i ma on większą średnicę niż dwa pozostałe kołnierze, które znajdują się dołu urządzenia. Górny kołnierz to kołnierz przyłączeniowy. Do dolnego kołnierza przyłączeniowego znajdującego się po lewej stronie urządzenia kierowany jest strumień materiału. Natomiast to dolnego kołnierza przyłączeniowego znajdującego się po prawej stronie kieruje się wychwytywane zanieczyszczenia magnetyczne. Urządzenie posiada dwa detale obrotu rdzenia magnetycznego w bębnie magnetycznym. Jeden znajduję się poniżej górnego kołnierza przyłączeniowego, natomiast drugi detal umieszczony jest powyżej dolnych kołnierzy przyłączeniowych, po lewej stronie względem osi urządzenia. na ilustracji zaznaczona jest droga jaką przebywa wprowadzony materiał przez urządzenie. Materiał dodawany jest do górnego kołnierza przyłączeniowego, następnie trafia na detal obrotu rdzenia magnetycznego obracającego się w prawą stronę, a kolejno na drugi taki detal również obracający się w prawą stronę. Następnie wprowadzony materiał kieruje się do dolnego kołnierza przyłączeniowego znajdującego się po lewej stronie.
Oddzielacze elektromagnetyczne taśmowe przeznaczone są do oddzielania w sposób ciągły zanieczyszczeń ferromagnetycznych zawartych w materiałach sypkich lub kawałkowatych, zwłaszcza w obiegowych masach formierskich przenoszonych na gumowych taśmach przenośników.
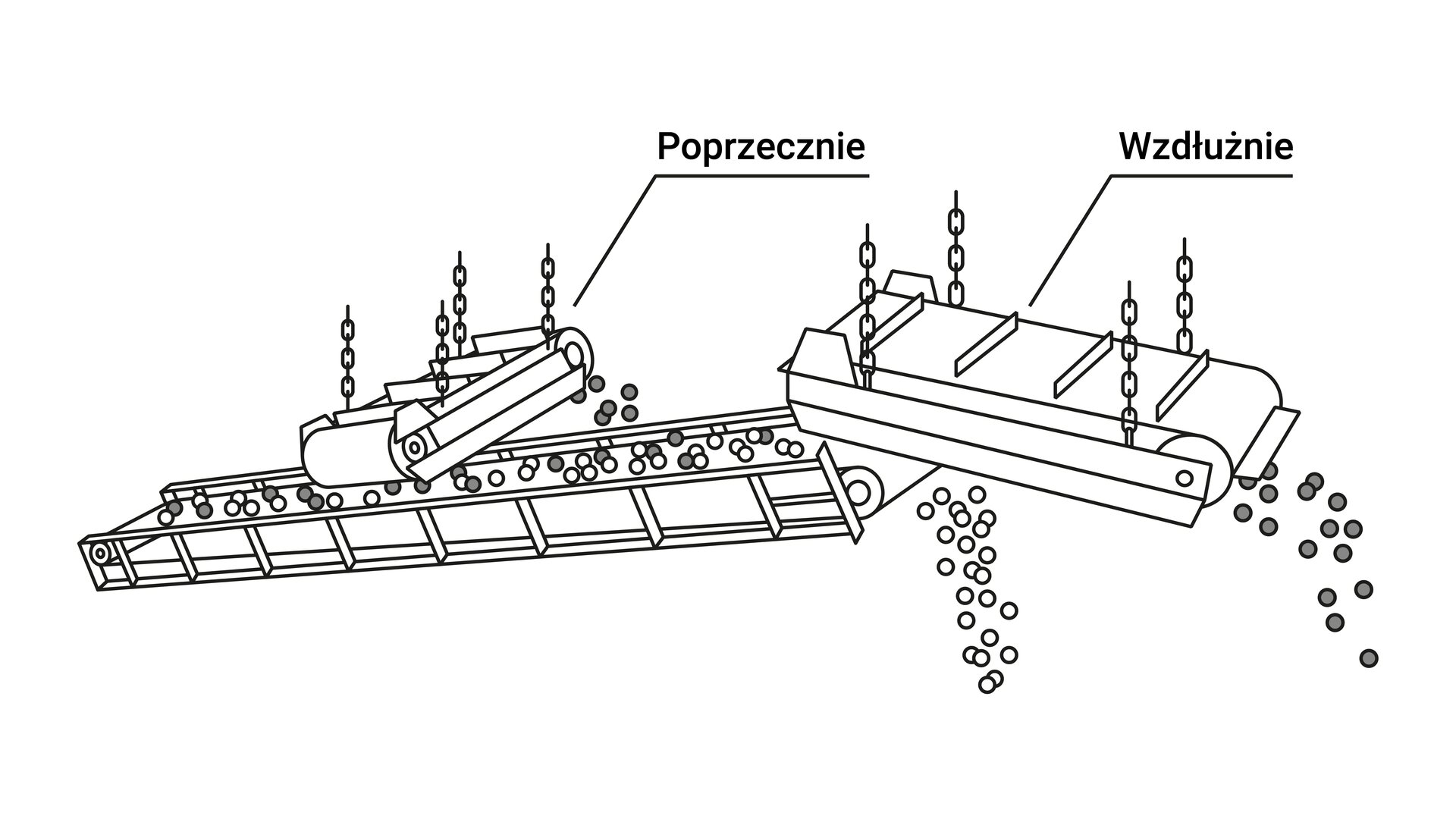
Na ilustracji przedstawione są dwa oddzielacze elekromagnetyczne taśmowe. Po lewej stronie ukazany jest podajnik taśmowy, na którym umieszczone są małe ciemne oraz jasne koła. Nad podajnikiem, w połowie długości wisi oddzielacz elektromagnetyczny zawieszony poprzecznie (prostopadle do podajnika). Oddzielacz jest w kształcie długiego i niskiego prostopadłościanu, z umieszczonymi rolkami na końcach. Do czterech rogów są przyczepione łańcuchy, które unoszą urządzenie. Na końcu podajnika przedstawiony jest kolejny oddzielacz elektromagnetyczny taśmowy, umieszczony wzdłużnie (równolegle do podajnika). Podajnik ma identyczny kształt i również jest zawieszony dzięki czterem łachom znajdujących się na rogach. Na obudowie oddzielacza z wierzchu widoczne są cztery wąskie prostokąty. Z jednej strony oddzielacza, tuż przy rolkach od spodu wysypują się posegregowane kulki w ciemnym kolorze, natomiast z drugiej strony widnieją kulki w kolorze jasnym.
Eksploatacja maszyn i urządzeń
Uszkodzenia maszyn i urządzeń odlewniczych są ściśle związane z ich trybem pracy.
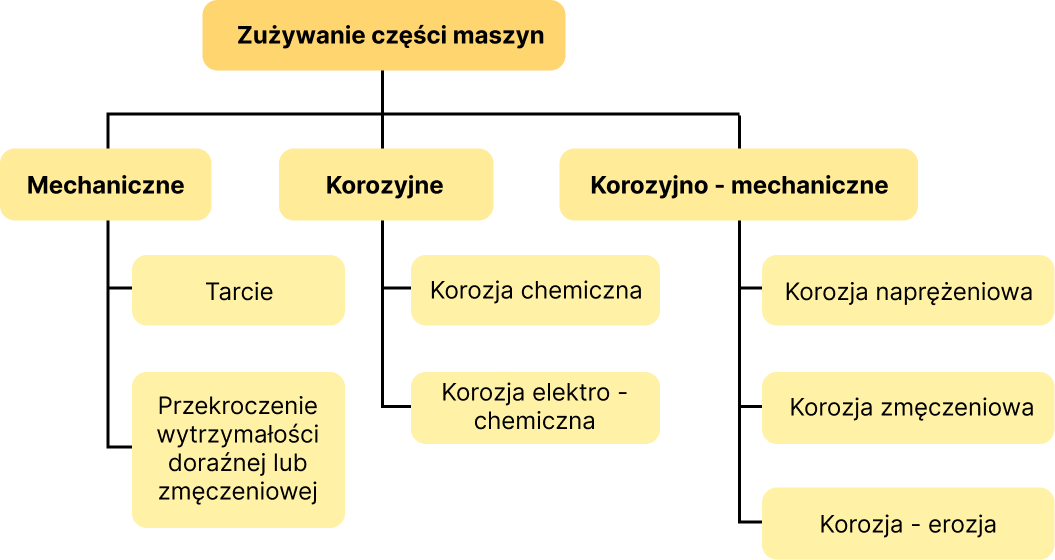
Ilustracja przedstawia schemat przyczyn zużywania części maszyn. Części maszyn zużywają się z powodów mechanicznych, korozyjnych i korozyjno‑mechanicznych. Wśród powodów mechanicznych wyróżniamy tarcie oraz przekroczenie wytrzymałości doraźnej lub zmęczeniowej. Natomiast wśród przyczyn korozyjnych wyróżniamy korozję chemiczną i korozję elektrochemiczną. Powodami zużycia korozyjno‑mechanicznego są korozja naprężeniowa, korozja zmęczeniowa i korozja, tak zwana erozja.
Głównymi przyczynami powstawania wad maszyn i urządzeń wykorzystywanych w przemyśle odlewniczym są:
oddziaływanie czynników zewnętrznych,
drgania,
zapylenie,
wilgoć,
błędy użytkowników,
błędy montażu,
błędy technologiczne powstałe w czasie jej projektowania,
przekroczenie normatywnego czasu pracy,
błędy konserwacji.
Każdy pracodawca ma obowiązek zapewnić okresową kontrolę maszyn i urządzeń narażonych na warunki mogące pogarszać ich stan techniczny. Poza kontrolą okresową przeprowadza się także badania prowadzone przez jednostki zewnętrzne, albo osoby upoważnione przez pracodawcę, które posiadają odpowiednie kwalifikacje. Wyniki kontroli są rejestrowane i przechowywane przez okres lat, są one do dyspozycji poszczególnych organów.
W przypadku gdy obsługa, naprawa, konserwacja urządzenia lub maszyny powoduje zagrożenie dla pracowników, pracodawca powinien zadbać, aby czynności te były wykonywane przez upoważnionych i odpowiednio wykwalifikowanych pracowników.
Powrót do spisu treściPowrót do spisu treści
Powiązane materiały multimedialne
Atlas interaktywny: Zasady obsługi bieżącej maszyn i urządzeń do przygotowania mas formierskich i mas rdzeniowychZasady obsługi bieżącej maszyn i urządzeń do przygotowania mas formierskich i mas rdzeniowych
Sekwencje filmowe: Rodzaje maszyn i urządzeń do przygotowania mas formierskich i mas rdzeniowychRodzaje maszyn i urządzeń do przygotowania mas formierskich i mas rdzeniowych
Animacja 3D: Proces przygotowania mas formierskich i mas rdzeniowychProces przygotowania mas formierskich i mas rdzeniowych
Schemat interaktywny: Zasady oceny stanu technicznego elementów maszyn i urządzeńZasady oceny stanu technicznego elementów maszyn i urządzeń