E‑book do e‑materiału Eksploatacja maszyn i urządzeń do przygotowania mas formierskich i mas rdzeniowych
MTL.02. Eksploatacja maszyn i urządzeń odlewniczych - Operator maszyn i urządzeń odlewniczych 812107, Technik odlewnik 311705
Masy formierskie oraz maszyny do ich przygotowania
E‑BOOK
Spis treści
OsnowaOsnowa
Materiały wiążąceMateriały wiążące
Materiały dodatkoweMateriały dodatkowe
Przygotowanie masy formierskiej
Regeneracja masy formierskiejRegeneracja masy formierskiej
Urządzenia wykorzystywane do przygotowania masyUrządzenia wykorzystywane do przygotowania masy
Obsługa bieżąca maszyn i urządzeńObsługa bieżąca maszyn i urządzeń
Ocena stanu technicznego elementów maszyn i urządzeńOcena stanu technicznego elementów maszyn i urządzeń
Zasady bezpieczeństwa i higieny pracyZasady bezpieczeństwa i higieny pracy
Słownik pojęćSłownik pojęć
Netografia i bibliografiaNetografia i bibliografia
Przygotowanie masy formierskiej
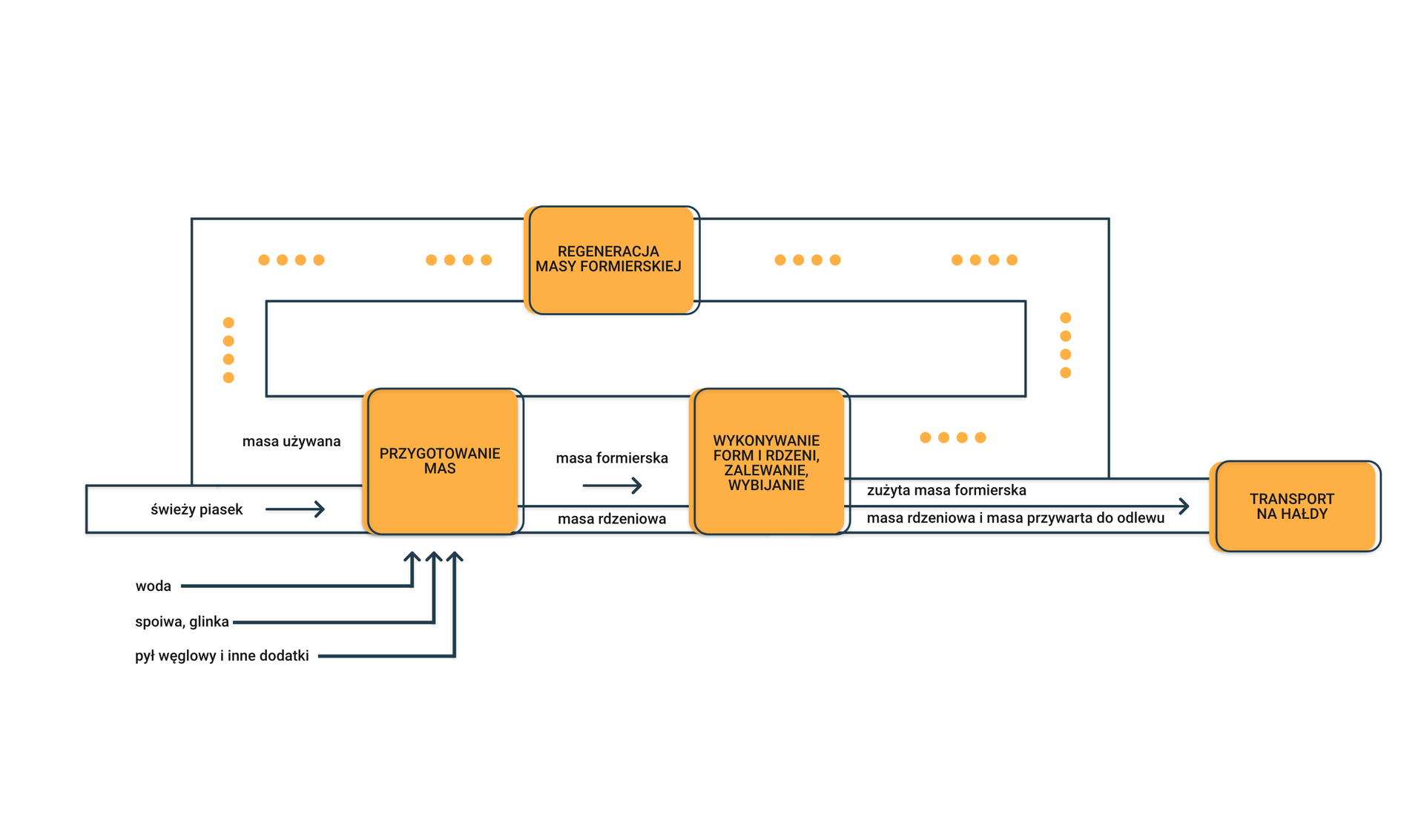
Ilustracja przedstawia schemat obiegu masy formierskiej w odlewni. Do miejsca gdzie przygotowywane są masy dostarczana jest woda, spoiwa glinki, pył węglowy i inne dodatki, a także świeży piasek i gotowa do ponownego wykorzystania masa używana. Kolejny etap to miejsce w którym znajduję się zarówno masa formierska jak i masa rdzeniowa. Kolejno wykonywane są formy i rdzenie, zalewanie oraz wybijanie. Z tego miejsca masa rozdzielana jest w trzech kierunkach. Masa rdzeniowa i masa przywarta do odlewu jest transportowana na hałdy. Zużyta masa formierska również transportowana jest na hołdy. Natomiast masa używana trafia do ponownego obiegu, ale zanim zostanie wykorzystana poddaje się ją regeneracji.
Suszenie | Chłodzenie | Odpylanie | Rozdrabnianie | Przesiewanie | Mieszanie | Spulchnianie i oddzielanie |
---|---|---|---|---|---|---|
1. Piece do suszenia:
2. Urządzenia fluidyzacyjne | 1. Chłodziarki:
| 1. Odpylacze:
| 1. Kruszarki:
2. Gniotowniki:
3. Młyny
| 1. Przesiewacze obrotowe:
2. Przesiewacze wstrząsowe:
| 1. Mieszarki do mas:
| 1. Spulchniarki:
2. Oddzielacze elektromagnetyczne
|
Kryteria doboru mas formierskich i rdzeniowych
Masa formierska jest to mieszanina różnych materiałów formierskich, dobranych w odpowiednim stosunku. Ilość i rodzaj poszczególnych składników mas są uzależnione od następujących czynników:
rodzaj stopu, masa i kształt odlewów,
wymagana dokładność wymiarowa odlewów oraz chropowatość,
wymiar produkcji,
ekonomika procesu,
względy ekologiczne,
temperatura zalewania formy,
skład ziarnowy masy,
oczekiwane właściwości mechaniczne i fizyczne mas np. płynność, zagęszczalność, przepuszczalność,
przeznaczenie,
wymagana konsystencja (sypka, ciekła),
stopień zużycia,
jakość.
Rodzaje mas formierskich i rdzeniowych
Masy formierskie z bentonitem
Należą do grupy mas syntetycznych. Taka masa jest mieszaniną osnowy piaskowej, bentonitu oraz wody. Istotny jest odpowiedni dobór proporcji poszczególnych składników. Obecność wody gwarantuje związanie ziaren osnowy przez glinę formierską. Odpowiednia ilość wody ma bezpośredni wpływ miedzy innymi na: wytrzymałość, przepuszczalność, zagęszczalność, osypliwość mas formierskich. Jeżeli masa jest zbyt sucha, powierzchnia styku między cząsteczką osnowy, a bentonitu jest punktem (zakładając kulisty kształt obu cząsteczek). Po dodaniu wody cząsteczki bentonitu pęcznieją, tym samym zwiększając powierzchnię styku. Zdolność przyłączania wody przez cząsteczki bentonitu jest ograniczona i po wprowadzeniu zbyt dużej ilości pozostaje ona jako woda niezwiązana i wpływa na spadek wytrzymałości. Powyższy opis mas z bentonitem dotyczy odlewów ze staliwa. W przypadku mas dla odlewów żeliwnych konieczny jest dodatek nośnika węgla błyszczącego.
Sypkie masy szybkoutwardzalne (szkło wodne przedmuchiwane )
Ten rodzaj masy jest zaliczany do technologii zimnej rdzennicy. Jako osnowę stosuje się głównie piasek kwarcowy, zawartość lepiszcza nie może przekraczać , zawartość frakcji pyłowej powinna wynosić mniej niż . W tej technologii spoiwem jest głównie szkło wodne. Na części masowych piasku dodaje się części masowych szkła wodnego, ilość szkła jest uzależniona od składu ziarnowego oraz modułu, lepkości i gęstości spoiwa. Mieszaninę piasku i szkła wodnego umieszcza się w rdzennicy lub skrzynce, a następnie w celu związania przedmuchuje się . Obecnie jednak szkło wodne zastępowane jest geopolimerami i innymi spoiwami krzemianowymi.
Masy cementowe
Mają zastosowanie w produkcji jednostkowej i seryjnej odlewów pośrednich i dużych wymiarach i nieskomplikowanym, lub średnioskomplikowanym kształcie.
Skład masy:
piasek kwarcowy,
cementu portlandzkiego,
wody.
W formie lub rdzennicy utwardza się na powietrzu godzin. Dodatek , w ilości skraca czas wiązania do godzin.
Do zalet tego rodzaju mas należy niski koszt cementu, mała ilość energii potrzebna do zagęszczenia masy, dobra dokładność wymiarowa, dobra wytrzymałość po utwardzeniu. Do wad możemy zaliczyć niezbyt dobrą jakość powierzchni oraz silne przywieranie masy do powierzchni modelu.
Ciekłe masy samoutwardzalne ()
Mają zastosowanie w produkcji jednostkowej i seryjnej odlewów o średnich i dużych wymiarach i nieskomplikowanym, lub średnioskomplikowanym kształcie. Masa składa się z mieszaniny piasku kwarcowego, szkła wodnego, żużla chromowego spełniającego rolę utwardzacza oraz dodatków spieniających w odpowiednich proporcjach. Mieszaninę o ciekłej konsystencji wylewa się na model. Po czasie następuje utwardzenie masy.
Ciekłe masy szybkoutwardzalne ()
Jako osnowę stosuje się głównie piasek kwarcowy. Wymagane są określona wielkość ziarna: oraz minimalna zawartość ziarn mniejszych od i frakcji pyłowych W tym przypadku spoiwem jest szkło wodne sodowe. Utwardzacze ciekłej masy są takie same jak sypkiej. Stosuje się środki powierzchniowo czynne. Sporządzenie masy rozpoczyna się od wymieszania ciekłych składników masy, następnie mieszaninę ciekłych składników dodaje się do osnowy. Masę wlewa się do rdzennicy lub skrzynki formierskiej bezpośrednio po zakończeniu mieszania. Masa powinna mieć ciekłość , nie wymaga ona zagęszczania.
Proces gorącej rdzennicy
Metoda ta ma zastosowanie przy seryjnej i masowej produkcji rdzeni o podwyższonych wymaganiach wymiarowych. Do procesu gorącej rdzennicy zalicza się masy wiążące w podwyższonej temperaturze, masy tego rodzaju zawierają także utwardzacz, który może spełniać rolę nośnika składników niezbędnych do szybkiego usieciowania żywicy lub katalizatora. Rdzennica podgrzana do temperatury (poza technologią Warm‑box, w której temperatury są poniżej podanego zakresu) zostaje napełniona za pomocą nadmuchiwarek lub strzelarek. Pod wpływem ciepła następuje polimeryzacja spoiwa powodująca utwardzenie masy rdzeniowej.
Wyróżniamy następujące procesy gorącej rdzennicy:
Croninga (formowanie skorupowe),
gorącej rdzennicy (Hot – box),
ciepłej rdzennicy (Warm – box),
skokowego utwardzania cieplnego (Thermoshock),
Z przedmuchaniem podgrzanym powietrzem (Warm air).
Proces zimnej rdzennicy wykorzystujący system przedmuchiwania gazem
W tym przypadku rolę utwardzacza mają substancje w stanie gazowym (aminy – , , , , utwardzacz estrowy – mrówczan metylu). Najkorzystaniejsze jest dostarczenie gazowego utwardzacza we wszystkie przestrzenie porowate rdzenia. Zatem, proces ten wymaga odpowiedniej przepuszczalnosći masy, punktowego doprowadzenia gazu.
Fenolowy proces Ashland
Proces tan zalicza się do technologii zimnej rdzennicy. Masy formierskie i rdzeniowe wykonane z udziałem żywicy są przedmuchiwane aminą (, , ), co powoduje natychmiastowe utwardzenie materiału w temperaturze otoczenia. Mała lepkość żywicy umożliwia wykorzystanie wszystkich rodzajów mieszarek do wytwarzania masy. Masę zagęszcza się za pomocą strzelarek lub nadmuchiwarek. Pary katalizatora , są wytwarzane w urządzeniach o konstrukcji umożliwiającej uzyskanie dużej prężności aminy w gazie obojętnym lub powietrzu. Nadmiar aminy jest usuwany przez przedmuchiwanie rdzenia powietrzem. Usunięta amina jest poddana procesowi odzysku i kierowana do następnego cyklu utwardzania. Rdzenie po utwardzeniu posiadają dużą wytrzymałość i mogą być transportowane, wykańczane, łączone ze sobą. Temperatura osnowy ziarnowej powinna wynosić . Niższa lub wyższa temperatura może stwarzać problemy z wykonaniem rdzeni. Zaleca się stosowanie wilgotności osnowy na poziomie . Wzrost wilgotności osnowy ziarnowej powyżej powoduje znaczny spadek wytrzymałości masy i skrócenie czasu jej przydatności do formowania. Jako oprzyrządowanie modelowe można stosować żeliwo, aluminium, żywice epoksydowe i uretanowe.
Metody wytwarzania odlewów | Zastosowanie: | Zastosowanie: | Rzeczywiste możliwe do uzyskania dokładności wymiarowe dla odlewów żeliwnych | Klasa chropowatości powierzchni |
---|---|---|---|---|
Formowanie w dołach, gruncie i wzornikami | F, R | Z, S | nieustalone | |
Formowanie ręczne w masach „na wilgotno” | F | Z, S, N | ||
Formowanie ręczne w masach „na sucho” | F, R | Z, S, N | ||
Formowanie maszynowe w masach „na wilgotno” zwykłych | F | Z, S, N |
Metody wytwarzania odlewów | Zastosowanie: | Zastosowanie: | Rzeczywiste możliwe do uzyskania dokładności wymiarowe dla odlewów żeliwnych | Klasa chropowatości powierzchni |
---|---|---|---|---|
Formowanie maszynowe w masach „na wilgotno” z materiałów kwalifikowanych | F | Z, N, S | ||
Proces | F, R | Z, S, N | ||
Formowanie w masach cementowych | F, R | Z | ||
Ciekłe masy samoutwardzalne (CMS) | F, R | Z, S | ||
Formowanie w masach furanowych samoutwardzalnych (proces zimnej rdzennicy) | F, R | Z, S, N | ||
Formowanie w masach żywicznycch termoutwardzalnych (proces gorącej rdzennicy) | R | Z, S, N | ||
Formowanie pod wysokimi naciskami | F | Z, S |
Metody wytwarzania odlewów | Zastosowanie: | Zastosowanie: | Rzeczywiste możliwe do uzyskania dokładności wymiarowe dla odlewów żeliwnych | Klasa chropowatości powierzchni |
---|---|---|---|---|
Formowanie skorupowe | F, R | Z, S, N | ||
Odlewanie kokilowe | F, R | Z, S, N | ||
Odlewanie odśrodkowe | F | Z, S, N | ||
Odlewanie ciągłe i półciągłe | F | Z, N | ||
Proces Shawa | F, R | Z, S |
Metody wytwarzania odlewów | Zastosowanie: | Zastosowanie: | Rzeczywiste możliwe do uzyskania dokładności wymiarowe dla odlewów żeliwnych | Klasa chropowatości powierzchni |
---|---|---|---|---|
Odlewanie ciśnieniowe | F, R | N | ||
Metoda wytapianych modeli | F | Z, S, N |
Szkodliwość mas formierskich i rdzeniowych
Na szkodliwość mas formierskich i rdzeniowych wpływają następujące czynniki:
szkodliwe i toksyczne świeże składniki mas,
zapylenie,
szkodliwe produkty destrukcji cieplnej (wydzielanie się gazów),
temperatura,
hałas, drgania,
pole magnetyczne,
trudne do utylizacji odpady.
Istotne jest zminimalizowanie oddziaływanie szkodliwych czynników występujących w przemyśle odlewniczym, zarówno w celu ochrony środowiska naturalnego, jak i ochrony zdrowia pracowników.
W tym celu odlewnie mogą podjąć następujące działania:
hermetyzacja szkodliwych procesów,
własna oczyszczalnie ścieków i chłodnia przemysłowa, dzięki czemu zrzut wód po etapie chłodzenia jest wstrzymany,
recykling i odpowiednia utylizacja odpadów produkcyjnych,
uruchomienie linii produkcyjnej pozbawionej przesypów masy - wówczas maleje emisja pyłów,
dach odlewni zmniejszający emisję hałasu,
maszyny i urządzenia wyposażone w program oszczędzania energii,
nowoczesne systemy wentylacji i odpylania,
wykorzystanie ogrzewania solarnego,
szkolenia podnoszące świadomość pracowników odnośnie ekologii.
Powrót do spisu treściPowrót do spisu treści
Powiązane materiały multimedialne
Atlas interaktywny: Zasady obsługi bieżącej maszyn i urządzeń do przygotowania mas formierskich i mas rdzeniowychZasady obsługi bieżącej maszyn i urządzeń do przygotowania mas formierskich i mas rdzeniowych
Sekwencje filmowe: Rodzaje maszyn i urządzeń do przygotowania mas formierskich i mas rdzeniowychRodzaje maszyn i urządzeń do przygotowania mas formierskich i mas rdzeniowych
Animacja 3D: Proces przygotowania mas formierskich i mas rdzeniowychProces przygotowania mas formierskich i mas rdzeniowych
Schemat interaktywny: Zasady oceny stanu technicznego elementów maszyn i urządzeńZasady oceny stanu technicznego elementów maszyn i urządzeń