E‑book do e‑materiału Eksploatacja maszyn i urządzeń do przygotowania mas formierskich i mas rdzeniowych
MTL.02. Eksploatacja maszyn i urządzeń odlewniczych - Operator maszyn i urządzeń odlewniczych 812107, Technik odlewnik 311705
Masy formierskie oraz maszyny do ich przygotowania
E‑BOOK
Spis treści
OsnowaOsnowa
Materiały wiążąceMateriały wiążące
Materiały dodatkowe
Przygotowanie masy formierskiejPrzygotowanie masy formierskiej
Regeneracja masy formierskiejRegeneracja masy formierskiej
Urządzenia wykorzystywane do przygotowania masyUrządzenia wykorzystywane do przygotowania masy
Obsługa bieżąca maszyn i urządzeńObsługa bieżąca maszyn i urządzeń
Ocena stanu technicznego elementów maszyn i urządzeńOcena stanu technicznego elementów maszyn i urządzeń
Zasady bezpieczeństwa i higieny pracyZasady bezpieczeństwa i higieny pracy
Słownik pojęćSłownik pojęć
Netografia i bibliografiaNetografia i bibliografia
Materiały dodatkowe
Materiały zawierające węgiel:
pył węglowy, grafitowy
pył węgla brunatnego
żywice węglowodorowe
mieszanki bentonitowe (nośnik węgla błyszczącego)
Dodatki zawierajace węgiel są stosowane do mas z bentonitem, ponieważ:
poprawiają jakość powierzchni odlewów,
powodują mniejszy nakład pracy przeznaczony na oczyszczanie odlewów (mniejsza adhezja masy do powierzchni odlewu),
pozwalają uzyskać lepszą płynność i wybijalność masy,
ograniczone zostaje występowanie niektórych wad w odlewach (zmniejszenie adsorpcji ),
łatwo się je dozuje i mają niską cenę.
Wadami dodatków zawierających węgiel są:
zmniejszenie wytrzymałości formy,
większy stopień dezaktywacji bentonitu (większe zużycie),
emisja , , benzenu, toluenu, etylobenzenu, ksylenów (), wielopierścieniowych węglowodorów aromatycznych () itp.,
zanieczyszczenie masy formierskiej (benzenem, kondensatami itp.),
po ich dodaniu konieczne jest dodanie wody do masy (a większa wilgotność sprzyja powstaniu wad w odlewach).
Materiały zluźniające:
trociny, torf, mączka drewna,
dodawane są w celu polepszenia wybijalnośći mas formierskich. Są dodatkiem stosowanym w masach o małej zdolności do odkształcania w miarę postępującego skurczu odlewniczego.
Parafina, wosk, stearyna:
ich dodatek wpływa na polepszenie płynności piasku, ułatwiają oddzielenie skrzynek formierskich od płyty modelowej.
odlewnie odchodzą jednak od wprowadzania dodatków organicznych z uwagi na ich szkodliwą emisję do atmosfery, zatem ogranicza się ich ilość do niezbędnego minimum.
Dodatki skrobiowe:
głównie skrobia roslinna lub dekstryna,
zmniejszają skłonność klasycznych mas syntetycznych do powodowania wad takich jak strupy lub żyłki, zmniejszają także osypliwość masy.
Oznaczenia tabeli „Możliwość użycia osnowy, w zależności od przeznaczenia powłoki ochronnej”:
„” odpowiedni,
„” nieodpowiedni,
„” możliwe zastosowanie
Stop odlewniczy | Grafit | Koks | Kwarc | Cyrkon | Magnezyt spieczony | Talk | Szamot | Glinokrzemiany | Łyszczyki |
---|---|---|---|---|---|---|---|---|---|
Staliwo węglowe | |||||||||
Staliwo stopowe | |||||||||
Żeliwo szare | |||||||||
Żeliwo sferoidalne | |||||||||
Żeliwo ciągliwe | |||||||||
Stopy miedzi | |||||||||
Stopy aluminium | |||||||||
Stopy magnezu | |||||||||
Powłoki ochronne
W odlewnictwie zastosowanie mają powłoki ochronne na formy i rdzenie, składające się z osnowy z materiałów ogniotrwałych, wysokotemperaturowego materiału wiążącego, odpowiedniego rozpuszczalnika oraz dodatków. Najczęściej są to materiały wieloskładnikowe występujące w konsystencji: stałej, pasty, ciekłej.
Celem nanoszenia powłok jest:
zmniejszenie chropowatości powierzchni odlewów,
zapobieganie przypaleniu materiałów formierskich do odlewu,
ułatwienie usunięcia odlewu z formy.
Efekt ochrony uzyskuje się przez:
zakrycie porów masy formierskiej, co zapobiega penetracji ciekłego metalu w głąb masy,
zapobieganie powstawaniu fałd i pęknięć.
Powłoki ochronne muszą posiadać następujące cechy:
ogniotrwałość powłoki musi być wyższa niż temperatura ciekłego metalu,
odpowiednie właściwości wytrzymałościowe,
odporność na pękanie podczas suszenia lub utwardzania,
powłoka musi być niereaktywna z tlenkami metali w podwyższonej temperaturze,
zdolność do przeciwstawiania się erozji metalu wypełniającego formę.
Nazwa materiału | Wzór chemiczny | Gęstość | Temperatura topnienia |
---|---|---|---|
Grafit | powyżej | ||
Koks | |||
Kwarc | |||
Cyrkon | |||
Magnezyt spieczony | |||
Talk | |||
Szamot | |||
Glinokrzemiany | |||
Korund | |||
Łyszczyki (muskowit) |
Objaśnienie dotyczące tabeli „Rodzaje rozcieńczalników”:
– najwyższe dopuszczalne stężenie
– Najwyższe dopuszczalne stężenie chwilowe
Wartości te określają maksymalne stężenie czynników szkodliwych dla zdrowia.
Substancja | Wzór chemiczny | Temperatura wrzenia | Gęstość | Temperatura zapłonu | |
---|---|---|---|---|---|
Alkohol etylowy | |||||
Alkohol izopropylowy | |||||
Alkohol metylowy | |||||
Alkohol butylowy | |||||
Chlorek metylenu | |||||
Benzyna |
Oznaczenia tabeli „Sposoby nanoszenia bezwodnych powłok ochronnych na formy i rdzenie piaskowe”:
„” sposób odpowiedni,
„” sposób nieodpowiedni,
„m” możliwe do zastosowania pod określonymi warunkami
W poniższej tabeli „Sposoby nanoszenia bezwodnych powłok ochronnych na formy i rdzenie piaskowe” użyto znaków w następującym znaczeniu: plus to sposób odpowiedni, minus nieodpowiedni, a literą możliwe zastosowanie pod określonymi warunkami
Zastosowanie | Zanurzenie | Malowanie pędzlem | Polewanie | Natryskiwanie |
---|---|---|---|---|
Rdzenie małe (produkcja jednostkowa i małoseryjna) | ||||
Rdzenie średnie (produkcja jednostkowa i małoseryjna) | ||||
Rdzenie duże (produkcja jednostkowa i małoseryjna) | m | |||
Rdzenie małe (produkcja seryjna) | m | |||
Rdzenie średnie (produkcja seryjna) | ||||
Rdzenie duże (produkcja seryjna) | m | m | ||
Formy małe (produkcja jednostkowa i małoseryjna) | ||||
Formy średnie (produkcja jednostkowa i małoseryjna) | m | |||
Formy duże (produkcja jednostkowa i małoseryjna) | m | |||
Formy małe (produkcja seryjna) | ||||
Formy średnie (produkcja seryjna) | m | m | ||
Formy duże (produkcja seryjna) | m |
Oznaczenia tabeli „Sposoby nanoszenia wodnych powłok ochronnych na formy i rdzenie piaskowe”:
„” sposób odpowiedni,
„” sposób nieodpowiedni,
„m” możliwe do zastosowania pod określonymi warunkami
W poniższej tabeli „Sposoby nanoszenia wodnych powłok ochronnych na formy i rdzenie piaskowe” użyto znaków w następującym znaczeniu: plus to sposób odpowiedni, minus nieodpowiedni, a literą możliwe zastosowanie pod określonymi warunkami
Zastosowanie | Zanurzenie | Malowanie pędzlem | Polewanie | Natryskiwanie |
---|---|---|---|---|
Rdzenie małe (produkcja jednostkowa i małoseryjna) | ||||
Rdzenie średnie (produkcja jednostkowa i małoseryjna) | ||||
Rdzenie duże (produkcja jednostkowa i małoseryjna) | ||||
Rdzenie małe (produkcja seryjna) | m | |||
Rdzenie średnie (produkcja seryjna) | ||||
Rdzenie duże (produkcja seryjna) | m | |||
Formy małe (produkcja jednostkowa i małoseryjna) | ||||
Formy średnie (produkcja jednostkowa i małoseryjna) | m | |||
Formy duże (produkcja jednostkowa i małoseryjna) | m | |||
Formy małe (produkcja seryjna) | ||||
Formy średnie (produkcja seryjna) | m | m | ||
Formy duże (produkcja seryjna) | m |
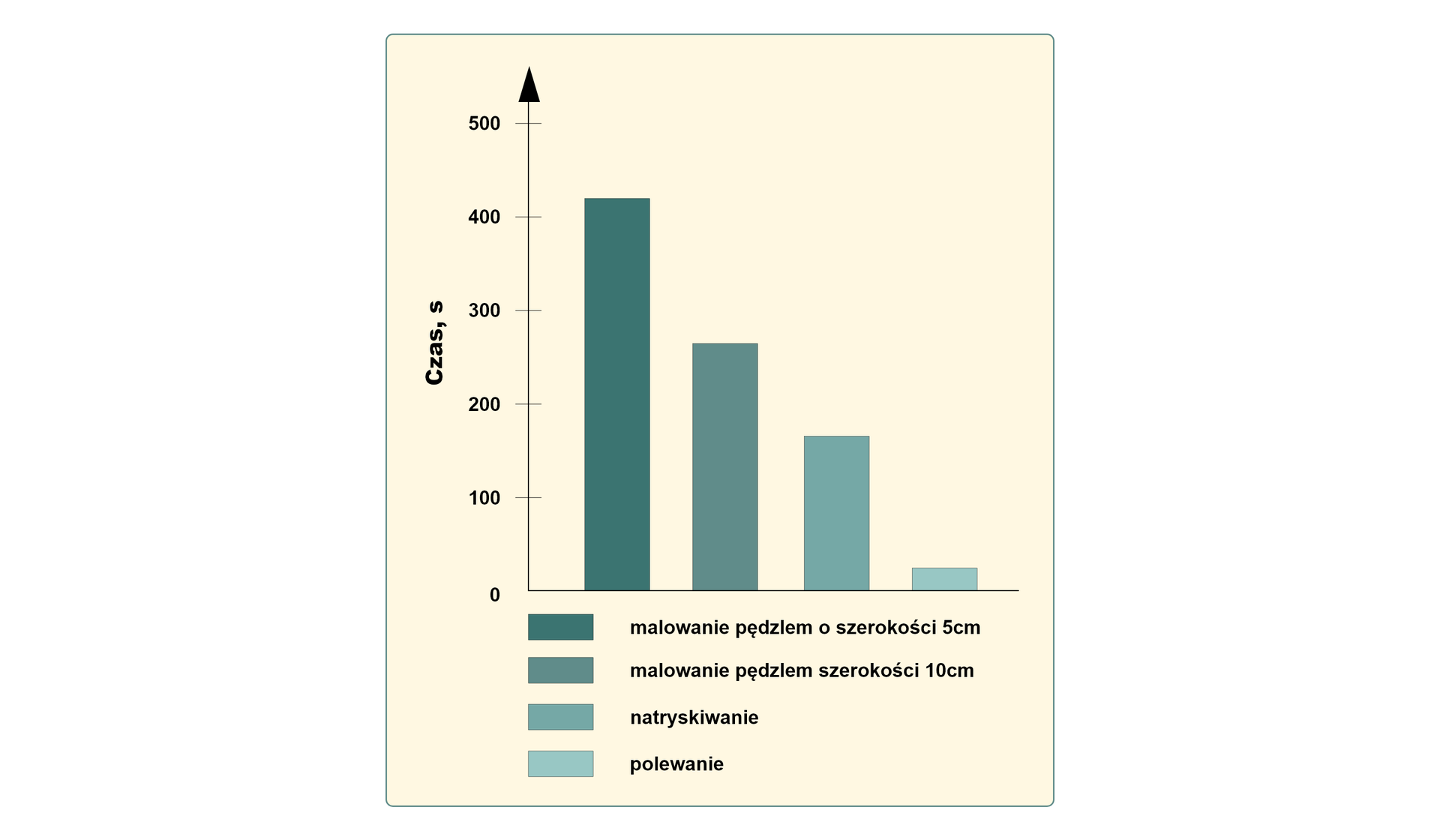
Wykres słupkowy przedstawia zależność czasu podanego w sekundach, od sposobu nanoszenia powłoki ochronnej na jeden metr kwadratowy rdzenia. Zestawiono wyniki dla czterech różnych sposobów pokrywania rdzeni: malowanie pędzlem o szerokości centymetrów, malowanie pędzlem o szerokości centymetrów, natryskiwanie oraz polewanie. Podczas malowania pędzlem o szerokości centymetrów czas wyniósł sekund. Gdy malowano pędzlem o szerokości centymetrów czas wyniósł sekund. Natryskiwanie zajęło sekund. Natomiast czas dla metody, podczas której polewano rdzeń, wyniósł sekund.

Wykres słupkowy przedstawia zależność zużycia powłoki ochronnej, podanej w gramach, od metody jej nanoszenia na jeden metr kwadratowy rdzenia. Zestawiono wyniki dla trzech metod: natryskiwanie, polewanie oraz malowanie. Dla natryskiwania zużycie wynosiło gram, dla polewania gram, a dla malowania wynosiło gram.
Otuliny egzotermiczne i termoizolacyjne
W celu wydłużenia czasu krzepnięcia zasilaczy stosuje się otuliny termoizolacyjne i egzotermiczne. Dzięki ich zastosowaniu nadlew ma mniejszą objętość, a metal zawarty w jego wnętrzu dłużej pozostaje w stanie ciekłym, zapewniając czas na wypełnienie niedoboru objętościowego w odlewanym elemencie. Końcowa faza krzepnięcia przebiega w zasilaczu. Zastosowanie tego typu otulin zmniejsza straty cieplne w odlewie, co zwiększa uzysk metalu.
Rodzaj masy | Gęstość pozorna, | Wyrzymałość na ściskanie, | Współczynnik przewodzenia ciepła w temperaturze | Współczynnik przewodzenia ciepła w temperaturze | Współczynnik przewodzenia ciepła w temperaturze | Współczynnik przewodzenia ciepła w temperaturze | Temperatura klasyfikacyjna, |
---|---|---|---|---|---|---|---|
Szamotowe | |||||||
Wysokoglinowe | |||||||
Krzemionkowe | |||||||
Ziemia okrzemkowa | |||||||
Wełna mineralna (płyty) | |||||||
Włókna glinokrzemianowe (płyty) | |||||||
Włókna z |
Im niższy współczynnik przewodzenia ciepła
Składniki i właściwości masy | |||
---|---|---|---|
Symbol masy: | Symbol masy: | Symbol masy: | |
Aluminium | |||
Gęstość pozorna | |||
Ciepło właściwe |
Powrót do spisu treściPowrót do spisu treści
Powiązane materiały multimedialne
Atlas interaktywny: Zasady obsługi bieżącej maszyn i urządzeń do przygotowania mas formierskich i mas rdzeniowychZasady obsługi bieżącej maszyn i urządzeń do przygotowania mas formierskich i mas rdzeniowych
Sekwencje filmowe: Rodzaje maszyn i urządzeń do przygotowania mas formierskich i mas rdzeniowychRodzaje maszyn i urządzeń do przygotowania mas formierskich i mas rdzeniowych
Animacja 3D: Proces przygotowania mas formierskich i mas rdzeniowychProces przygotowania mas formierskich i mas rdzeniowych
Schemat interaktywny: Zasady oceny stanu technicznego elementów maszyn i urządzeńZasady oceny stanu technicznego elementów maszyn i urządzeń